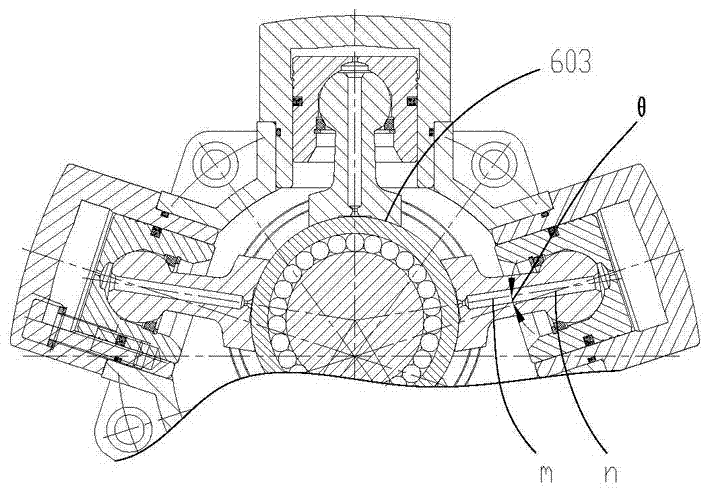
本发明涉及液压元件技术领域,具体是一种中速大扭矩径向柱塞液压马达。
背景技术:径向柱塞液压马达典型构造为柱塞沿驱动轴呈星形放射状分布,柱塞运动平面与驱动轴垂直,其显著优点是排量大,扭矩大,可直接带动负载启动,特别适合低速大扭矩的应用场合。然而,现今市场上实际使用表明,常见的径向柱塞液压马达使用转速低于300r/min。按液压马达行业以500r/min为界,将高于500r/min归为高速马达,低于500r/min归为低速马达的约定俗成的观点来看,现今市场上出售的径向柱塞液压马达大部分应归为低速大扭矩径向柱塞液压马达,高于500r/min的高速马达大多是扭矩偏小的轴向柱塞液压马达,一般需要通过减速环节才能带动负载启动。随着科技的进步,市场出现了对转速达300~1000r/min,对应排量4000~200mL/r,能直接带负载启动的中速大扭矩液压马达的旺盛需求。由上述对液压马达简单分析可知,能满足中速大扭矩直接带负载启动的只能是径向柱塞结构,而现今各类低速大扭矩径向柱塞液压马达随着使用转速的提高,都会出现各种各样的问题,不能满足使用要求,即便有个别能称得上中速大扭矩的液压马达也存在各种缺陷。图1和图2为现有技术的一种曲轴连杆式低速大扭矩径向柱塞液压马达的结构示意图,其结构示意图可见之于相关厂家的产品样本。包括壳体1,前盖2,曲轴3,滚柱4,轴承座5,连杆6,保持环7,活塞8,缸盖9,配油机构10。曲轴3,滚柱4,轴承座5构成一滚子轴承结构,连杆6通过两边各一个保持环7刚性连接于轴承座5外圆柱面501上,连杆6的球头602设置于活塞8的球窝801内,活塞8设置于缸盖9的圆柱内孔901内。工作时,配油机构将液压油(图中未注)依次配至由活塞8与缸盖9内腔902所包围的各个容腔,液压油推动活塞8在缸盖9的圆柱内孔901内向下滑动,向下滑动的活塞8推动连杆6向下运动,连杆6向下运动的同时绕其球头602的球心沿垂直于曲轴3的轴线x方向摆动并经过轴承座5、滚柱4推动曲轴3旋转。曲轴连杆式低速大扭矩径向柱塞液压马达价格便宜,在低速工况领域获得了广泛应用,是世界上产量最大的低速大扭矩液压马达之一,但随着转速的提高,该结构形式的液压马达存在下述缺点:1、轴承座5的外表面501为一圆柱面,与轴承座5圆柱面501配合的连杆6的内凹面603仍为圆柱面,圆柱面之间贴合不能约束沿圆柱轴线方向,即轴y方向的自由度。因此,随着工作转速的提高,连杆6的定位能力差,稳定性差。2、连杆6与保持环7完全是机械构件的刚性连接,连杆6的沟槽601与保持环内孔701之间存在间隙,随着转速的提高,离心力增加,连杆6与保持环7之间存在机械撞击,产生噪音。3、如图2所示,随着连杆6绕其球头602的球心沿垂直于曲轴3的轴线x方向摆动,连杆6的轴线m与活塞8的轴线n存在周期变化的交角θ,活塞8存在周期性的侧向力,该侧向力使缸盖9的圆柱内孔901产生不规则的磨损,磨损后,圆形变成椭圆形,如图3所示,转速越高,压力越高椭圆磨损越严重。4、由上述连杆6的运动规律可知,连杆6对曲轴3的推动力有按余弦规律变化的波动,即推动力等于Fcosθ,其中F由活塞8直径和液压油压强大小共同决定,由此可知,曲轴3输出扭矩存在波动。5、除上述结构原理上的缺陷外,该结构形式的马达还存在工艺上的不足。曲轴3上设置两个用于约束滚柱4沿轴y方向自由度的台阶301,302,两台阶301和302之间的距离尺寸公差及表面光洁度均有较高的要求,给加工带来了不便,同理,轴承座5的台阶502,503也给加工带来了不便。图4为意大利Calzoni公司发明,佛山顺德中意液压有限公司获得其生产许可的现有技术的一种套筒伸缩摆缸式低速大扭矩径向柱塞液压马达的结构示意图,包括壳体1,前盖2,曲轴3,油缸4,活塞5,弹簧6,缸盖7,弹簧盖8,弹簧座9、配油机构10。曲轴3,缸盖7分别设有外球面301,701,油缸4,活塞5分别设有内球面401,501。弹簧6通过弹簧座9,弹簧盖8分别将油缸4的内球面401与曲轴3的外球面301和活塞5的内球面501与缸盖7的外球面701贴紧。油缸4和活塞5同轴配合,配合轴线为y,构成一仅能沿轴线y做伸缩滑动和在与轴线x垂直平面内绕缸盖7球面701的球心O1摆动的伸缩摆动套筒结构。缸盖7,活塞5,油缸4,曲轴3构成一密封容腔,工作时,由配油机构10依次配至的液压油进入该密封容腔,容腔包围的液压油柱直接推动曲轴3旋转。曲轴3旋转一周,油缸4与活塞5之间伸缩一次,弹簧6也跟随伸缩一次。与上述曲轴连杆式低速大扭矩径向柱塞液压马达相比,套筒伸缩摆缸式低速大扭矩径向柱塞液压马达具有明显的优势:1、油缸4与活塞5之间只有沿轴线y的伸缩和在与轴线x垂直平面内绕缸盖7球面701的球心O1摆动的伸缩摆动运动,油缸4与活塞5始终保持同轴,两者之间不存在侧向力,这意味着不存在椭圆磨损。2、液压油直接推动曲轴3旋转,推力大小由活塞5直径和液压油压强共同决定,不存在曲轴连杆式低速大扭矩径向柱塞液压马达因机构转化原理的固有特性引起的力和扭矩的波动。但随着转速的提高,图4所示现有技术的套筒伸缩摆缸式低速大扭矩径向柱塞液压马达仍存在下述缺点:1、由上述分析可知,曲轴3旋转一周,弹簧6伸缩一次,转速越高,弹簧6伸缩频率越高,越容易疲劳断裂,因此,弹簧6成了提高马达转速的瓶颈之一。2、随着弹簧6的伸缩,油缸4与曲轴3之间,活塞5与缸盖7之间的接触应力发生周期性变化,由接触力学知识可知,交变接触应力比静态接触应力更容易使接触表面产生疲劳破坏。3、油缸内球面401与曲轴外球面301之间组成一滑动摩擦副,由摩擦学原理可知,材料耐磨极限受摩擦副之间PV值的制约,其中P为摩擦副之间的正压力,V为摩擦副之间的相对滑动速度。随着转速的提高,V随之增大,磨损加剧,因此摩擦副磨损是提高该结构形式马达转速最严重的瓶颈。针对上述套筒伸缩摆缸式低速大扭矩径向柱塞液压马达的缺点,相关厂家进行了各种改进:2015年2月4日公布的申请公布号为CN104329217A公开了一种伸缩摆缸式液压马达及其偏心轴球面加工方法,该发明通过工艺手段,在曲轴球面上加工出细小的储液孔以提高其自润滑性能,虽能一定程度地减少摩擦,提高转速,但油缸与曲轴球面之间滑动摩擦的物理事实没有改变,依然受摩擦副PV值的制约。2013年4月3日公布的申请公布号为CN103014587A公开了一种在曲轴轴面热喷涂钼涂层的方法,该发明通过在曲轴球面上喷涂一层金属涂层,以增加其自润滑性和耐磨性,该方法在大排量(3600ml/r及以上)液压马达上取得良好的效果,但和上述CN104329217A公布的发明方法一样,油缸与曲轴球面之间滑动摩擦的物理事实没有改变,依然受摩擦副PV值的制约,仍无法胜任中速工况。美国专利文献US5967018公开了一种解决方案,如图5。在缸盖1与曲轴2之间设置一套径向伸缩套筒3,伸缩套筒3含油缸4.和活塞5,油缸4和活塞5各设置一内球面,缸盖1和曲轴2各设置一外球面;弹簧6对油缸4施加弹力,使油缸4内球面与曲轴2外球面贴紧;弹簧7对活塞5施加弹力,使活塞5内球面与缸盖1外球面贴紧;弹簧6和弹簧7不随曲轴2的旋转而改变压缩量,因此对接触面的预紧力不变,改善了接触面相关零件的受力状况,避免了随着转速的提高弹簧出现疲劳断裂及加剧球面磨损现象。但该方案仍存在下述缺点:1、弹簧6和弹簧7均设置在伸缩套筒3的外围,增加了马达尺寸,尤其显著地增加了缸盖1的尺寸。2、和前述方案一样,油缸4与曲轴2球面之间滑动摩擦的物理事实没有改变,依然受摩擦副PV值的制约,仍无法胜任中速工况。美国专利文献US7267042B2是继美国专利文献5967018之后公开的另一种解决方案,如图6。该方案将美国专利文献5967018设置于活塞外面的弹簧移至活塞内部,通过挂杆、挂杆环等构件对弹簧进行预紧,减少了马达尺寸,但马达运转时,油缸与曲轴接触面所组成的摩擦副仍是滑动摩擦副,无法胜任中速工况。图7为意大利Sai公司生产的一种摆缸式大扭矩径向柱塞液压马达的结构示意图,包括曲轴1、滚柱2、轴承套3、摆缸4、活塞5、保持环6、蝶形弹簧7,前壳体8、后壳体9、配油机构10等。摆缸4通过两耳轴401,402支撑于前壳体8和后壳体9孔内,工作时,摆缸4绕耳轴401,402摆动,活塞5与摆缸4只做相对的伸缩运动,从而消除了活塞5对摆缸4的侧向压力,减少摩擦,消除椭圆磨损现象,提高机械效率。活塞5与曲轴1之间采用滚柱轴承结构变上述连杆式和套筒伸缩摆缸式马达的滑动摩擦为滚动摩擦,大大降低摩擦力和发热量。轴承套3两端各设置一个蝶形弹簧7,蝶形弹簧7对保持环6施加弹力,将保持环6扣紧在活塞5的沟槽上,防止活塞5与轴承套3脱离。活塞5与轴承套3为球面接触,改善了对中性和稳定性。该结构形式马达在中速领域获得较好的应用效果,但仍然存在下述缺点:1、摆缸绕支撑于前、后壳体内的耳轴摆动,摆动中心在壳体内部,摆动半径小,据陈卓如教授在其专著《低速大扭矩液压马达理论设计与计算》分析,摆动半径越小,马达扭矩和转速脉动越大。2、耳轴是悬臂梁结构,存在弯曲应力,受力特性不好。3、为较少摆缸耳轴的接触应力,耳轴直径较大,重量大,增加了摆缸运动惯量,转速越高,其负面影响越大。4、活塞内部设置一阻尼孔,活塞并非完全中空的薄壁结构,重量大,其缺点如上述缺点3。5、在圆柱型摆缸上设置两个悬臂耳轴,两耳轴的同轴度、光洁度、表面硬度均有较高的要求,因此加工工艺性不好。6、给保持环提供弹力的弹簧是蝶形弹簧,虽比螺旋弹簧紧凑,但仍有改进的空间,可将马达尺寸做得更紧凑。美国专利文献US8206130B2公开了一种具有高转速能力的径向柱塞液压马达,其总体结构和工作原理与上述Sai公司生产的摆缸式大扭矩径向柱塞液压马达相似,在耳轴上开设若干油槽,对耳轴进行强制润滑,同时在配油盘上也开设了润滑槽,所述两项措施改善了摩擦副润滑特性。但如上述图7所示结构,耳轴结构固有缺点没有改变,且配油机构不具备自动补偿能力。
技术实现要素:本发明要解决的技术问题在于:针对现有技术的缺陷,提供一种中速大扭矩径向柱塞液压马达。本发明的技术方案是这样实现的:一种中速大扭矩径向柱塞液压马达,包括壳体、对外输出转速和扭矩的曲轴,外套于曲轴的偏心轴段的滚柱、滚柱内套于轴承套的内孔内、径向星形均布紧固于壳体的缸盖、沿轴承座径向分布且上下端分别与缸盖的外球面和轴承套的外球面相抵的伸缩套筒、将伸缩套筒的下端始终紧贴于轴承套之外球面的保持环、将伸缩套筒的上端始终紧贴于缸盖外球面的挂杆、两端分别与曲轴和配油机构连接的传动轴。所述伸缩套筒包含油缸和活塞,所述油缸和所述活塞同轴配合,轴线z始终通过缸盖之外球面的球心O1和轴承套之外球面的球心O2,工作时,油缸和活塞沿z轴伸缩运动和绕缸盖之球面的球心O1摆动。所述曲轴、滚柱、轴承套构成一滚动轴承结构。还包括保持环、保持环压板、设置于保持环与保持环压板之间的弹性橡胶圈,与保持环压板紧贴并卡套在所述轴承套沟槽里的弹性挡圈,所述弹性挡圈将油缸之内球面与轴承套之外球面贴紧;还包括托盘、自锁螺母、挂杆、挂杆环、蝶形弹簧、弹簧座、弹性挡圈,所述托盘、自锁螺母、挂杆、挂杆环、蝶形弹簧、弹簧座、弹性挡圈将活塞内球面与缸盖外球面贴紧;还包括配油机构,所述配油机构包括配油板、配油盘、浮动环、蝶形弹簧、后盖,一端与曲轴铰接的传动轴穿过壳体及配油板另一端与配油盘铰接,工作时,曲轴、传动轴、配油盘同步绕轴x正向或反向旋转,一端与后盖相抵另一端与浮动环相抵的蝶形弹簧将浮动环直接压紧在配油盘上,进而间接将配油盘压紧在配油板上,起到初始密封及磨损补偿作用,即当浮动环与配油盘之间或配油盘与配油板之间出现磨损后,在蝶形弹簧的弹力作用下,浮动环与配油盘之间、配油盘与配油板之间仍然保持贴紧。所述轴承套左右两端分别与壳体的台阶面和前盖左端面间隙相抵,即轴承套沿轴y方向的自由度为所述台阶面和所述左端面所约束,但轴承套又可和曲轴一起绕轴x自由旋转。进一步地,所述油缸靠近内球面一端的外径设置一沟槽,所述沟槽的直径A比油缸内径B略小。进一步地,所述沟槽的直径A与油缸内径B之比约等于0.8~0.85,油缸的截球面尺寸C与沟槽的直径A之比不小于0.5。进一步地,所述油缸的截球面尺寸C与沟槽的直径A之比为0.7~0.8。进一步地,所述活塞设置为中空薄壁圆柱结构。进一步地,所述曲轴的偏心轴段左端设置一绕轴y的环形凸台阶。进一步地,所述曲轴的偏心轴段设置2-4道卸荷槽。进一步地,所述轴承套之内孔设置为一不带凸台阶的光孔。进一步地,所述轴承套之内孔设置2道卸荷槽。进一步地,所述保持环与保持环压板之间设置一弹性橡胶圈及放置弹性橡胶圈的沟槽,沟槽既可设置于保持环上,也可设置于保持环压板上。进一步地,设置于保持环与保持环压板之间的弹性橡胶圈材质为丁腈橡胶,弹性橡胶圈横截面可以是圆形、方形、星形或是其它形状。进一步地,所述保持环设置一内孔,保持环压板设置一凸台,保持环的内孔与保持环压板的凸台配合,配合轴线为轴y。进一步地,所述油缸下端的外围,即与球形座相抵一端的外围设置一沟槽,保持环扣合在油缸下端外围的沟槽上,通过保持环、设置于保持环与保持环压板之间的弹性橡胶圈,保持环压板,与保持环压板紧贴并卡套在轴承套沟槽里的弹性挡圈将油缸之内球面与轴承套之外球面贴紧。进一步地,所述活塞内孔设置一环形台阶,通过与环形台阶相抵的托盘,与挂杆的螺纹配合的自锁螺母,挂杆,挂杆环、蝶形弹簧、弹簧座、弹性挡圈将活塞内球面与缸盖外球面贴紧。进一步地,所述挂杆及挂杆环分别设置一外球面和内球面,两球面相抵,可做相对滑动。进一步地,所述挂杆设置2-4个通油孔,孔的大小及数量依据马达排量大小而定。进一步地,所述缸盖之外球面的球心O1设置在缸盖实体的外部。进一步地,所述缸盖、挂杆、挂杆环、活塞四个零件之球面的球心同心。进一步地,所述配油盘与所述配油板相抵平面上设有同心的三环密封带,分别是外环密封带、中环密封带、内环密封带,所述外环密封带上外内交错设有两排润滑油孔和,每排润滑油孔数量是2个或2个以上,所述内排润滑油孔的外包络圆半径比所述外环润滑油孔的内包络圆半径大,即R1>R2。进一步地,所述中环密封带上外内交错设有两排润滑油孔,每排润滑油孔数量是2个或2个以上,所述内排润滑油孔的外包络圆半径比所述外环润滑油孔的内包络圆半径大,即R3>R4。进一步地,所述内环密封带上外内交错设有两排润滑油孔,每排润滑油孔数量是2个或2个以上,所述内排润滑油孔的外包络圆半径比所述外环润滑油孔的内包络圆半径大,即R5>R6。本发明与现有技术相比,具有以下优点和有益效果:1、本发明采用伸缩套筒结构,组成伸缩套筒的油缸活塞同轴配合,做相对伸缩运动的油缸和活塞其轴线始终重合,消除了连杆式马达因伴随着活塞与连杆的相对运动轴线有交角而产生的侧向力和椭圆形磨损的现象。2、由轴承座、油缸、活塞、缸盖包围而成的液压油柱直接推动轴承座和曲轴旋转,与现有技术的连杆式及意大利Sai公司的摆缸式马达相比,提高了机械效率和可靠性。3、油缸,活塞均为薄壁圆筒结构,与现有技术相比,质量更轻,运动惯量更小,因此更适合中高速工况,同时,其加工工艺更简单。4、油缸与轴承座之间,活塞与缸盖之间为球面接触,与连杆式结构的圆柱面配合相比,对中性和稳定性更好,与耳轴结构相比,受力特性更好。5、油缸与曲轴之间采用滚柱轴承结构变意大利Calzoni公司及佛山顺德中意有限公司现有技术的套筒伸缩摆缸式马达的滑动摩擦为滚动摩擦,大大降低摩擦力和发热量,但具体实施细节上又和意大利Sai公司和曲轴连杆式的现有技术方案不同。6、采用弹性橡胶圈代替蝶形弹簧对保持环施加预紧,与现有技术相比,减少了马达轴向尺寸,马达更紧凑,同时,橡胶圈具有吸收能量的阻尼作用,能起到吸收振动和噪音的积极效果。7、将伸缩套筒的摆动中心设置在缸盖实体的外部,增加伸缩套筒的摆动半径,与现有技术相比,减少了马达转速及扭矩脉动。8、曲轴与轴承座在轴向上无相对的位置约束关系,曲轴的轴向和径向自由度由设置于壳体与前盖的两轴承约束,轴承座轴向自由度由壳体凸台面和前盖左端面约束,因此可以去掉曲轴偏心轴段上约束滚柱和轴承座的凸台阶,曲轴偏心轴段的一个凸台阶仅为装配拆卸时临时定位而设置,工作时不起功能性的作用,尺寸精度及表面光洁度要求不高,因此曲轴加工方便。9、配油盘上开设有强制润滑油孔及补偿弹簧,润滑性能更好,可靠性更高。附图说明下面结合附图对本发明做进一步详述。图1是现有技术的一种曲轴连杆式低速大扭矩径向柱塞液压马达结构示意图。图2是图1的A-A剖视图。图3是曲轴连杆式低速大扭矩径向柱塞液压马达椭圆形磨损示意图。图4是现有技术的一种套筒伸缩摆缸式低速大扭矩径向柱塞液压马达结构示意图。图5是美国专利文献US5967018公开的一种解决方案结构示意图。图6是美国专利文献US7267042B2公开的一种解决方案结构示意图。图7是意大利Sai公司生产的一种摆缸式大扭矩液压马达的结构示意图。图8是本发明一种中速大扭矩径向柱塞液压马达的结构示意图。图9是本发明油缸结构示意图。图10是本发明挂杆结构示意图。图11是本发明曲轴结构示意图。图12是图8的局部放大图Ⅰ。图13是本发明配油盘结构示意图。图14是图13的A-A剖视图。图15是图14的局部放大图Ⅱ。图16是本发明配油盘润滑油孔布置示意图。其中图中:1.壳体101.壳体台阶面2.曲轴201.偏心轴段202.环形凸台阶203.台阶端面204.卸荷槽3.滚柱4.轴承套401.内孔402.轴承套外球面5.缸盖501.缸盖外球面6.伸缩套筒7.保持环8.挂杆801.螺纹802.外球面803.通油孔9.配油机构10.传动轴11.油缸1101.油缸内球面1102.沟槽12.活塞1201.活塞内球面1202.环形台阶13.保持环压板14.弹性橡胶圈15.轴承套沟槽里的弹性挡圈16.托盘17.自锁螺母18.挂杆环1801.内球面19.蝶形弹簧20.弹簧座21弹性挡圈22.配油板23.配油盘2301.外环密封带2302.中环密封带2303.内环密封带2304.润滑油孔2305.润滑油孔2306.润滑油孔2307.润滑油孔2308.润滑油孔2308润滑油孔2310.导流槽2311.配油盘外围2312.润滑油孔缺口24.浮动环25配油机构蝶形弹簧26.后盖27.前盖2701.前盖左端面O1.缸盖外球面球心O2.轴承套外球面球心x.轴线y.轴线z.轴线e.偏距。具体实施方式为了使本发明的技术特征、目的和有益效果更加清晰明了,下面结合附图对本发明的具体实施方式进行详细说明。如图8所示,一种中速大扭矩径向柱塞液压马达,包括壳体1、对外输出转速和扭矩的曲轴2,设置于壳体1和前盖27内孔的轴承29、外套于曲轴2偏心轴段201的滚柱3、滚柱3内套于轴承套4的内孔401内、径向星形均布紧固于壳体1的缸盖5、沿轴承座4径向分布且上下端分别与缸盖5的外球面501和轴承套4的外球面402相抵的伸缩套筒6、将伸缩套筒6的下端始终紧贴于轴承套4之外球面402的保持环7、将伸缩套筒6的上端始终紧贴于缸盖外球面501的挂杆8、两端分别与曲轴2左端和配油机构9连接的传动轴10。伸缩套筒6包含油缸11和活塞12两个零件,油缸11和活塞12同轴配合,轴线为z,轴线z始终通过缸盖5之外球面501的球心O1和轴承套4之外球面402的球心O2,工作时,油缸11和活塞12沿z轴伸缩运动和绕缸盖5之球面501的球心O1摆动。曲轴2、滚柱3、轴承套4构成一滚动轴承结构,工作时,将油缸11与轴承套4之间的滑动转化为轴承套4与曲轴2之间的相对滚动,根据摩擦学滚动摩擦力远远小于滑动摩擦力的基本原理,所述方案大大改善所述中速大扭矩径向柱塞液压马达的摩擦特性。通过保持环7、保持环压板13、设置于保持环7与保持环压板13之间的弹性橡胶圈14、与保持环压板13紧贴并卡套在轴承套4沟槽里的弹性挡圈15将油缸11之内球面1101与轴承套4之外球面402贴紧,贴紧面起密封作用。通过托盘16、自锁螺母17、挂杆8、挂杆环18、蝶形弹簧19、弹簧座20、弹性挡圈21将活塞内球面1201与缸盖外球面501贴紧,贴紧面起到滑动密封作用。配油机构9包括配油板22、配油盘23、浮动环24、蝶形弹簧25、后盖26,一端与曲轴3铰接的传动轴10穿过壳体1及配油板22另一端与配油盘23铰接,工作时,曲轴2、传动轴10、配油盘23同步绕轴x正向或反向旋转,一端与后盖26相抵另一端与浮动环24相抵的蝶形弹簧25将浮动环24直接压紧在配油盘23上,进而间接将配油盘23压紧在配油板22上,起到初始密封及磨损补偿作用,即当浮动环24与配油盘23之间或配油盘23与配油板22之间出现磨损后,在蝶形弹簧25的弹力作用下,浮动环24与配油盘23之间、配油盘23与配油板22之间仍然保持贴紧。所述轴承座4左右两端分别与壳体1的台阶面101和前盖27左端面2701间隙相抵,即轴承座4沿轴y方向的自由度为所述台阶面101和所述左端面2701所约束,但轴承座4又可和曲轴2一起绕轴x自由旋转。工作时,液压油经过配油结构9依次配至壳体1及缸盖5流道,进入由缸盖5、油缸11、活塞12、球形座4所包围的容腔,所述容腔包围的液压油柱对球形座4产生推力,所述推力作用线始终通过O2,因O2与曲轴2的轴线x有一偏距e,所以所述推力对曲轴2产生转矩,致使曲轴2绕轴线x旋转,对外输出转速和扭矩,球形座4绕轴x公转的同时绕轴y自转。作为本实施例更具体的技术方案:如图9,油缸11设置为中空薄壁圆柱结构,下端(即靠近内球面1101一端)外径设置一沟槽1102,为减少马达轴向尺寸,沟槽1102的直径A比油缸内径B略小,A/B约等于0.8~0.85;同时考虑油缸11的机械强度及油缸11的外球面1101与轴承座4的外球面402的接触应力,油缸11的尺寸C不应过小,C/A不应小于0.5,较佳的是0.7~0.8。上述油缸11的设计目的是在保证材料机械强度的前提下获得最小的结构尺寸,减少运动惯量,这对提高马达转速尤为重要。因挂杆8外球面802与挂杆环18内球面1801紧贴,为避免液压油对挂杆8产生冲击,如图10所示,挂杆8上开若干泄油孔803,泄油孔803的数量及直径大小取决于马达排量大小。如图11所示,曲轴2的偏心轴段201左端设置一绕轴y的环形凸台阶202,为装配和拆卸时临时定位用,工作时并不起功能性的作用。因此,尺寸L精度及台阶端面203光洁度均无过高的要求,因此曲轴加工方便;为减少或消除应力集中,在偏心轴段201上设置若干道卸荷槽204。如局部放大图12所示,保持环7扣合在油缸11外径的沟槽1102上,设置于保持环7与保持环压板13之间的弹性橡胶圈14对保持环7施加弹力,始终将保持环7扣紧在油缸11的沟槽1102上,使油缸11的内球面1101始终与球形座4的外球面402贴紧,贴紧面对油缸11中空内腔的液压油施加密封。所述弹性橡胶圈14材质为耐油的丁腈橡胶,横截面可以是圆形、方形、星形或是其它形状。与现有技术的蝶形弹簧设计相比,因弹性橡胶圈14可埋设于保持环压板13或保持环7沟槽内,节省了安装空间,尺寸更为紧凑,另外,弹性橡胶圈还具有吸收能量的阻尼作用,一定程度上能减少振动和噪音。参考图8、13、14,配油盘23与配油板22相抵平面上设有同心的外环密封带2301、中环密封带2302、内环密封带2303。所述外环密封带2301上外内交错设有两排润滑油孔2304和2305,每排润滑油孔数量可以是2个、3个、4个…,具体视马达排量大小和使用工况而定,配油盘23导流槽2310及其外围2311上的液压油通过所述的各个润滑油孔的缺口2312进入各个润滑油孔,对摩擦副进行强制润滑。所述内排润滑油孔2305的外包络圆半径比所述外环润滑油孔2304的内包络圆半径大,即R1>R2,其目的在于浮动环22与配油盘23外环密封带2301接触面上都能得到润滑。中环密封带2302和内环密封带2303上的润滑油口设置方法及其目的与外环密封带2301上的润滑油孔设置方法和目的相同,此不再详述。以上所述的具体实施例,仅为本发明较佳的实施例而已,举凡依本发明申请专利范围所做的同等设计,均应为本发明的技术所涵盖。