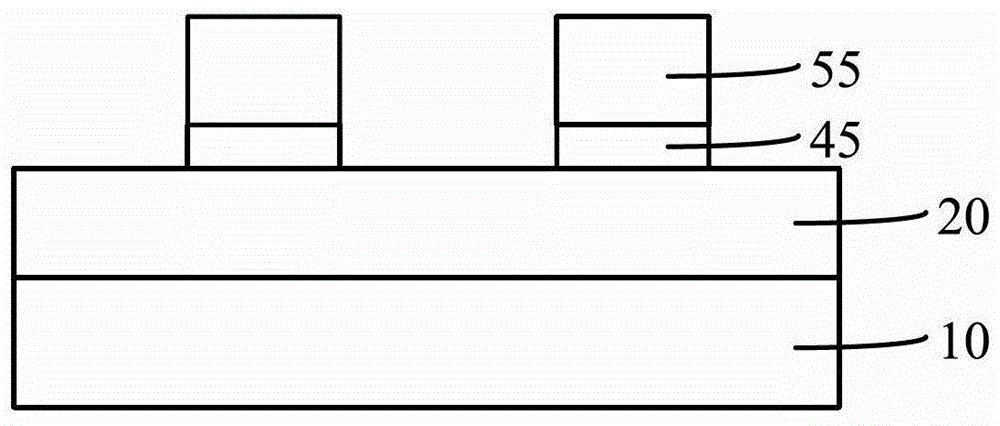
本发明涉及半导体技术,特别涉及一种自对准双重图形的形成方法。
背景技术:在半导体制造领域,光刻胶材料用于将掩膜图像转印到一层或多层的材料层中,例如将掩膜图像转印到金属层、介质层或半导体衬底上。但随着半导体工艺的特征尺寸的不断缩小,利用光刻工艺在材料层中形成小特征尺寸的掩膜图形变得越来越困难。为了提高半导体器件的集成度,业界已提出了多种双重图形工艺,其中,自对准双重图形(Self-AlignedDoublePatterning,SADP)工艺即为其中的一种。图1至图6为现有技术的一种利用自对准双重图形为掩膜对半导体结构进行刻蚀的方法,具体包括:请参考图1,提供半导体衬底10,在半导体衬底10表面形成待刻蚀材料层20,在所述待刻蚀材料层20表面形成底部抗反射层40,在所述底部抗反射层40表面形成光刻胶层50;请参考图2,对所述光刻胶层进行曝光显影,形成牺牲光刻胶层55,以所述牺牲光刻胶层55为掩膜,对底部抗反射层进行刻蚀,形成牺牲底部抗反射层45;请参考图3,在所述待刻蚀材料层20和牺牲光刻胶层55表面形成硬掩膜层60;请参考图4,对所述硬掩膜层进行回刻蚀,直到暴露出所述待刻蚀材料层20表面和牺牲光刻胶层55的顶部表面,在所述牺牲光刻胶层55、牺牲底部抗反射层45侧壁表面形成侧墙65;请参考图5,去除所述牺牲光刻胶层和牺牲底部抗反射层;请参考图6,以所述侧墙65作为掩膜,对所述待刻蚀材料层20(请参考图5)进行刻蚀。更多关于自对准双重图形工艺请参考公开号为US2009/0146322A1的美国专利文献。但是发明人发现,利用上述方法刻蚀待刻蚀材料层形成的刻蚀图形的侧壁形貌较差。
技术实现要素:本发明解决的问题是提供一种自对准双重图形的形成方法,最终形成的待刻蚀材料层的侧壁形貌较佳。为解决上述问题,本发明提供了一种自对准双重图形的形成方法,包括:提供待刻蚀材料层;在所述待刻蚀材料层上形成牺牲光刻胶层;在所述牺牲光刻胶层的顶部和侧壁表面形成聚合物层;在所述聚合物层表面形成第一掩膜材料层;对所述第一掩膜材料层进行回刻蚀,直到暴露出所述牺牲光刻胶层顶部表面的聚合物层,位于所述牺牲光刻胶层两侧的第一掩膜材料层形成第一掩膜图形;去除所述牺牲光刻胶层和聚合物层。可选的,形成所述聚合物层的工艺包括:在所述牺牲光刻胶层的顶部和侧壁表面利用沉积工艺形成聚合物层;对所述聚合物层进行刻蚀工艺,去除部分厚度的聚合物层。可选的,重复若干次上述的沉积工艺和刻蚀工艺,使得形成的聚合物层的转角为直角。可选的,所述重复的次数为1~5。可选的,所述沉积工艺为等离子体沉积工艺,具体包括:利用至少包括CH3F、CH2F2、HBr、CH4其中一种或几种的反应气体在所述牺牲光刻胶层顶部和侧壁表面形成聚合物层,其中,射频功率的范围为100瓦~1000瓦,反应温度的范围为30摄氏度~60摄氏度,反应腔压强范围为100毫托~200毫托。可选的,所述刻蚀工艺为等离子体刻蚀工艺,具体包括:利用至少含有CF4、CHF3、CH2F2、O2、Ar其中一种的刻蚀气体对聚合物层进行刻蚀,射频功率的范围为50瓦~1000瓦,反应温度的范围为30摄氏度~60摄氏度,反应腔压强范围为5毫托~200毫托。可选的,所述第一掩膜材料层的材料为氧化硅、氮化硅、氮氧化硅、氮化钛、氮化钽其中的一种或几种。可选的,形成所述第一掩膜材料层的工艺为原子层沉积工艺、低压化学气相沉积工艺或亚常压化学气相沉积工艺。可选的,还包括,在所述待刻蚀材料层表面形成第二掩膜材料层,在所述第二掩膜材料层表面形成牺牲光刻胶层。可选的,去除所述牺牲底部抗反射层和牺牲光刻胶层后,以所述第一掩膜图形为掩膜,对所述第二掩膜材料层进行刻蚀,形成第二掩膜图形。可选的,去除所述第一掩膜图形,以所述第二掩膜图形为掩膜,对所述待刻蚀材料层进行刻蚀。可选的,所述第二掩膜材料层的材料为氧化硅、氮化硅、碳化硅、氮氧化硅、无定形碳、多晶硅、氧化铪、氧化钛、氧化锆、氮化钛、氮化钽、钛其中的一种或几种。可选的,还包括,以所述第一掩膜图形为掩膜,对所述待刻蚀材料层进行刻蚀。可选的,去除所述牺牲光刻胶层和聚合物层的工艺为灰化工艺。可选的,所述聚合物层的厚度范围为1纳米~30纳米。与现有技术相比,本发明具有以下优点:本发明实施例在所述待刻蚀材料层上形成牺牲光刻胶层,在所述牺牲光刻胶层的顶部和侧壁表面利用沉积工艺和刻蚀工艺形成聚合物层,在所述待刻蚀材料层、聚合物层表面形成第一掩膜材料层,对所述第一掩膜材料层进行回刻蚀,直到暴露出所述牺牲光刻胶层顶部表面的聚合物层,位于所述牺牲光刻胶层两侧的第一掩膜材料层形成第一掩膜图形。由于在所述牺牲光刻胶层的顶部和侧壁表面形成了聚合物层,所述聚合物层的硬度远远大于牺牲光刻胶层的硬度,聚合物层的形状不容易变形,使得牺牲光刻胶层的形状不会因为第一掩膜材料层产生的应力发生形变,利用沉积工艺和刻蚀工艺形成的聚合物层的转角为直角,使得最终的刻蚀图形的侧壁形貌较佳,且通过控制所述聚合物层的厚度,可以控制最终的刻蚀图形的间距。附图说明图1至图6是现有技术的自对准双重图形工艺的剖面结构示意图;图7至图16是本发明实施例的自对准双重图形的形成过程的剖面结构示意图。具体实施方式由于利用上述技术刻蚀待刻蚀材料层形成的刻蚀图形的侧壁形貌较差,发明人经过研究发现,当在所述牺牲材料层和牺牲光刻胶层表面形成硬掩膜层时,所述硬掩膜层会对牺牲光刻胶层产生应力作用。由于光刻胶层的硬度不大,即使经过曝光后烘烤后牺牲光刻胶层也较为柔软,所述硬掩膜层产生的应力会使得牺牲光刻胶层变形,形成剖面为类梯形的牺牲光刻胶层,使得牺牲光刻胶层的侧壁不垂直于待刻蚀材料层表面,使得后续形成于所述牺牲光刻胶层侧壁表面的侧墙不垂直于待刻蚀材料层表面,影响最终对待刻蚀材料层进行刻蚀形成的刻蚀图形的侧壁形貌。为此,本发明提出了一种自对准双重图形的形成方法,在所述待刻蚀材料层上形成牺牲光刻胶层,在所述牺牲光刻胶层的顶部和侧壁表面利用沉积工艺和刻蚀工艺形成聚合物层,在所述待刻蚀材料层、聚合物层表面形成第一掩膜材料层,对所述第一掩膜材料层进行回刻蚀,直到暴露出所述牺牲光刻胶层顶部表面的聚合物层,位于所述牺牲光刻胶层两侧的第一掩膜材料层形成第一掩膜图形。由于在所述牺牲光刻胶层的顶部和侧壁表面形成了聚合物层,所述聚合物层的硬度远远大于牺牲光刻胶层的硬度,聚合物层的形状不容易变形,使得牺牲光刻胶层的形状不会因为第一掩膜材料层产生的应力发生形变,且利用沉积工艺和刻蚀工艺形成的聚合物层的转角为直角,不会影响最终的刻蚀图形的侧壁形貌。为使本发明的上述目的、特征和优点能够更为明显易懂,下面结合附图对本发明的具体实施方式做详细的说明。在以下描述中阐述了具体细节以便于充分理解本发明。但是本发明能够以多种不同于在此描述的其它方式来实施,本领域技术人员可以在不违背本发明内涵的情况下做类似推广。因此本发明不受下面公开的具体实施的限制。请参考图7至图16,为本发明实施例的自对准双重图形的形成过程的结构示意图。请参考图7,提供半导体衬底100,在所述半导体衬底100表面形成待刻蚀材料层110。所述半导体衬底100为硅衬底、锗衬底、硅锗衬底、绝缘体上硅衬底(SOI)、绝缘体上锗(GOI)衬底、玻璃衬底等其中的一种。所述待刻蚀材料层110为氧化硅层、氮化硅层、多晶硅层、低K介质材料、无定形碳、金属层等其中的一种或几种。在本实施例中,所述待刻蚀材料层110为金属层,所述金属层的材料为铝,利用自对准双重图形为掩膜对所述金属层进行刻蚀形成金属互连线。在其他实施例中,所述待刻蚀材料层还可以为半导体衬底,利用自对准双重图形作为掩膜对所述半导体衬底进行刻蚀。请参考图8,在所述待刻蚀材料层110表面形成第二掩膜材料层120。所述第二掩膜材料层120为单层结构或多层堆叠结构,所述第二掩膜材料层120的材料为氧化硅、氮化硅、碳化硅、氮氧化硅、无定形碳、多晶硅、氧化铪、氧化钛、氧化锆、氮化钛、氮化钽、钛中的一种或几种。在其它实施例中,所述第二掩膜材料层还可以为底部抗反射层。所述形成第二掩膜材料层120的工艺为化学气相沉积工艺或物理气相沉积工艺。所述第二掩膜材料层120的材料与待刻蚀材料层110的材料不同,两者具有高的刻蚀选择比,使得后续利用所述第二掩膜材料层120形成的第二掩膜图形对待刻蚀材料层110进行刻蚀时第二掩膜图形的损耗较小,有利于控制最终形成的刻蚀图形的形貌和大小。且由于后续回刻蚀形成的第一掩膜图形的上端往往不是规则的长方形,具有一定的弧度,直接利用所述第一掩膜图形为掩膜对待刻蚀材料层进行刻蚀会影响最终形成的刻蚀图形的侧壁形貌,因此,在本实施例中,在所述待刻蚀材料层110表面形成第二掩膜材料层120,后续利用第二掩膜材料层120形成第二掩膜图形后,去除位于其表面的第一掩膜图形,以所述上端形状为规则长方形的第二掩膜图形为掩膜,刻蚀所述待刻蚀材料层,有利于控制最终形成的刻蚀图形的形貌。且在本实施例中,所述第二掩膜材料层120包括无定形碳层和位于所述无定形碳层表面的氧化硅层,由于干法刻蚀工艺对无定形碳层进行刻蚀时无定形碳层侧壁形貌较佳,且所述氧化硅层与金属层的刻蚀选择比较大,有利于刻蚀厚度较大的金属层。请参考图9,在所述待刻蚀材料层120表面形成底部抗反射层130和位于底部抗反射层130表面的牺牲光刻胶层145。在本实施例中,形成所述底部抗反射层130和牺牲光刻胶层145的工艺为:利用旋转涂胶工艺在所述第二掩膜材料层120表面形成底部抗反射层130,在所述底部抗反射层130表面形成光刻胶层(未图示),对所述光刻胶层进行曝光显影形成牺牲光刻胶层145。在本实施例中,形成牺牲光刻胶层145后不直接刻蚀底部抗反射层130,等到后续形成第一掩膜图形后,以所述第一掩膜图形为掩膜,再对所述底部抗反射层130、第二掩膜材料层120、待刻蚀材料层110进行刻蚀。在其它实施例中,形成牺牲光刻胶层后,以所述牺牲光刻胶层为掩膜,刻蚀底部抗反射层形成牺牲底部抗反射层,后续形成的聚合物和第一掩膜图形位于所述牺牲底部抗反射层和牺牲光刻胶层的侧壁。在其他实施例中,所述底部抗反射层还可以为溶于显影液的底部抗反射层,当所述光刻胶层进行曝光显影时,同时也对底部抗反射层进行曝光显影,使得形成牺牲底部抗反射层和牺牲光刻胶层可以一步形成,节省了工艺步骤。在其他实施例中,也可以不形成所述底部抗反射层,在所述第二掩膜材料层表面形成光刻胶层,并对所述光刻胶层进行曝光显影,形成牺牲光刻胶层。在其他实施例中,也可以不在所述待刻蚀材料层表面形成第二掩膜材料层,直接在所述待刻蚀材料层表面形成底部抗反射层和光刻胶层,并后续以形成于待刻蚀材料层上的第一掩膜图形为掩膜,对所述待刻蚀材料层进行刻蚀。请参考图10,在所述牺牲光刻胶层145的顶部和侧壁表面利用沉积工艺形成聚合物层155。在本实施例中,形成所述聚合物层155的工艺为等离子体沉积工艺,由于所述牺牲光刻胶层主要的元素包含有C,因此利用等离子体可以在所述牺牲光刻胶层145表面形成聚合物层155,所述聚合物层155具有高度交联的网状结构,热稳定性、化学稳定性和力学强度、硬度优良。由于所述牺牲光刻胶层145表面具有机械强度高、硬度高的聚合物,使得后续形成的第一掩膜材料层产生的应力不会让牺牲光刻胶层发生形变,后续形成的第一掩膜图形与半导体衬底表面垂直,不会影响最终形成的刻蚀图形的侧壁形貌。所述等离子体沉积工艺具体包括:反应气体至少包括CH3F、CH2F2、HBr、CH4其中一种或几种,通过射频功率源将所述反应气体等离子体化后,所述反应气体的等离子体与牺牲光刻胶层表面的光刻胶发生反应,在所述牺牲光刻胶层顶部和侧壁表面形成聚合物层,射频功率的范围为100瓦~1000瓦,反应温度的范围为30摄氏度~60摄氏度,反应腔压强范围为100毫托~200毫托。请参考图11,对所形成的聚合物层155进行刻蚀工艺,去除部分厚度的聚合物层。由于利用一次等离子体沉积工艺形成的聚合物层155可能厚薄不均,且聚合物层155转角处也可能较为圆滑,使得后续形成的第一掩膜图形的侧壁形貌不佳。因此,在形成了一层聚合物层155之后,利用刻蚀工艺对部分厚度的聚合物层155进行刻蚀,使得刻蚀后的聚合物层155表面光滑,所述聚合物层155转角处变为直角。在本实施例中,所述刻蚀工艺为等离子体刻蚀工艺,具体包括:通过射频功率源将至少含有CF4、CHF3、CH2F2、O2、Ar其中一种的刻蚀气体等离子体化后,利用所述刻蚀气体的等离子体对聚合物层进行刻蚀,射频功率的范围为50瓦~1000瓦,反应温度的范围为30摄氏度~60摄氏度,反应腔压强范围为5毫托~200毫托。在现有技术中,由于第一掩膜材料层的厚度(即第一掩膜图形的宽度)对应于待刻蚀材料层的刻蚀图形的宽度,所述待刻蚀材料层的刻蚀图形的宽度是确定的,即第一掩膜材料层的厚度是确定的,相邻的牺牲光刻胶层之间的两个第一掩膜图形之间的间距取决于牺牲光刻胶层之间的间距。而受到现有光刻工艺的限制,相邻的牺牲光刻胶层之间的间距较大,因此,在本发明实施例中,还可以重复若干次所述沉积聚合物层工艺和刻蚀聚合物层工艺,由于先前形成的聚合物层中也含有碳元素,利用至少包括CH3F、CH2F2、HBr、CH4其中一种或几种的反应气体的等离子体会与先前形成的聚合物层进一步反应形成更厚的聚合物层,从而控制最终形成的聚合物层的厚度,进而控制相邻的牺牲光刻胶层之间的两个第一掩膜图形之间的间距,控制最终形成的刻蚀图形之间的间距。在本实施例中,重复沉积工艺和刻蚀工艺的次数为1~5,最终形成的聚合物层155的厚度范围为1纳米~30纳米。请参考图12,在所述底部抗反射层130表面和聚合物层155的顶部表面、侧壁表面形成第一掩膜材料层160。所述第一掩膜材料层160的材料为氧化硅、氮化硅、氮氧化硅、氮化钛、氮化钽其中的一种或几种。所述第一掩膜材料层160的材料与第二掩膜材料层120、底部抗反射层130的材料不同,具有高的刻蚀选择比,使得后续利用所述第一掩膜材料层160形成的第一掩膜图形对底部抗反射层130、第二掩膜材料层120进行刻蚀时第一掩膜图形的损耗较小,有利于控制最终形成的刻蚀图形的形貌和大小。在其他实施例中,当所述底部抗反射层直接形成在所述待刻蚀材料层表面时,所述第一掩膜材料层的材料与待刻蚀材料层的材料不同,两者具有高的刻蚀选择比,使得后续利用所述第一掩膜材料层形成的第一掩膜图形对待刻蚀材料层进行刻蚀时第一掩膜图形的损耗较小,有利于控制最终形成的刻蚀图形的形貌和大小。由于所述第一掩膜材料层160用于形成自对准双重图形的第一掩膜图形,所述第一掩膜图形的宽度取决于聚合物层155的侧壁表面的第一掩膜材料层160的厚度,因此,通过控制所述第一掩膜材料层160的厚度,就可以控制最终形成的刻蚀图形的宽度。本发明实施例形成的所述第一掩膜材料层的工艺为原子层沉积工艺、低压化学气相沉积工艺或亚常压化学气相沉积工艺。由于上述几种沉积工艺的沉积速率较慢,形成的第一掩膜材料层均匀性较佳,位于所述聚合物层155的侧壁表面的第一掩膜材料层160的侧壁平整垂直,形貌较佳,使得后续形成的第一掩膜图形的侧壁形貌较佳,以所述第一掩膜图形为掩膜对第二掩膜材料层或待刻蚀材料层进行刻蚀时,刻蚀形成的图形的形貌较佳。在本实施例中,利用原子层沉积工艺在所述底部抗反射层130表面和聚合物层155的顶部、侧壁表面形成氧化硅层,由于所述原子层沉积工艺的温度较低,温度范围为20摄氏度至100摄氏度,不会对所述其他半导体结构产生不良影响。请参考图13,对所述第一掩膜材料层160(参考图12)进行回刻蚀,直到暴露出所述底部抗反射层130表面和位于牺牲光刻胶层145表面的聚合物层155,位于所述聚合物层155侧壁表面的第一掩膜材料层160形成第一掩膜图形165。所述第一掩膜图形165的宽度与第一掩膜材料层160的厚度相对应。当所述牺牲光刻胶层145和聚合物层155的俯视视角的形状为长条形时,所述第一掩膜图形165的形状为围绕牺牲光刻胶层145、聚合物层155的环形掩膜图形,在本实施例中,由于最终形成的刻蚀图形为金属互连线,当后续去除所述牺牲光刻胶层后,再利用光刻胶覆盖长条形中间区域对应的第一掩膜图形,暴露出长条形两端对应的第一掩膜图形,以所述光刻胶为掩膜去除所述长条形两端对应的第一掩膜图形,使得所述第一掩膜图形变为条形的直线或折线。请参考图14,利用灰化工艺去除所述牺牲光刻胶层145(请参考图13)和聚合物层155(请参考图13)。由于所述聚合物层和光刻胶层的材料由C、O、H、N等元素构成的有机物组成,所述灰化工艺的反应气体为O2,将所述氧气等离子体化,并利用所述氧气等离子体与聚合物层155和牺牲光刻胶层145的有机物发生反应,形成挥发性的一氧化碳、二氧化碳、水等主要生成物,从而去除所述聚合物层155和牺牲光刻胶层145。在其他实施例中,所述灰化工艺的反应气体还可以包括N2或H2等,所述N2或H2有利于提高去除聚合物层、牺牲光刻胶层的能力。请参考图15,以所述第一掩膜图形165为掩膜,对所述底部抗反射层130(请参考图14)、第二掩膜材料层120(请参考图14)进行干法刻蚀,形成牺牲底部抗反射层135、第二掩膜图形125。由于回刻蚀形成的第一掩膜图形的上端往往不是规则的长方形,具有一定的弧度,直接利用所述第一掩膜图形为掩膜对待刻蚀材料层进行刻蚀会影响最终形成的刻蚀图形的侧壁形貌,因此,在本实施例中,形成第二掩膜图形125后,去除位于其表面的第一掩膜图形165、牺牲底部抗反射层135,以所述上端形状为规则长方形的第二掩膜图形125为掩膜,刻蚀所述待刻蚀材料层110,有利于控制最终形成的刻蚀图形的形貌。在其它实施例中,去除位于其表面的第一掩膜图形后,也可以以所述牺牲底部抗反射层为掩膜,刻蚀所述待刻蚀材料层,形成刻蚀图形。请参考图16,去除所述第一掩膜图形165(参考图15)和牺牲底部抗反射层135(参考图15),以所述第二掩膜图形125为掩膜,对所述待刻蚀材料层110进行刻蚀(参考图15),形成自对准双重图形的刻蚀图形115。在本实施例中,去除所述第一掩膜图形165和牺牲底部抗反射层135的工艺为湿法刻蚀。由于所述刻蚀图形115的宽度根据第一掩膜材料层的厚度决定,所述第一掩膜材料层的厚度可以小于现有工艺的光刻、刻蚀工艺的最小尺寸,使得所述刻蚀图形115的宽度小于利用光刻工艺形成的图形的宽度,且通过控制最终形成的聚合物层的宽度,可以控制相邻的刻蚀图形115之间的间距,使得相邻刻蚀图形115的间距小于利用光刻工艺形成的图形的间距,有利于提高集成电路的集成度。本发明虽然已以较佳实施例公开如上,但其并不是用来限定本发明,任何本领域技术人员在不脱离本发明的精神和范围内,都可以利用上述揭示的方法和技术内容对本发明技术方案做出可能的变动和修改,因此,凡是未脱离本发明技术方案的内容,依据本发明的技术实质对以上实施例所作的任何简单修改、等同变化及修饰,均属于本发明技术方案的保护范围。