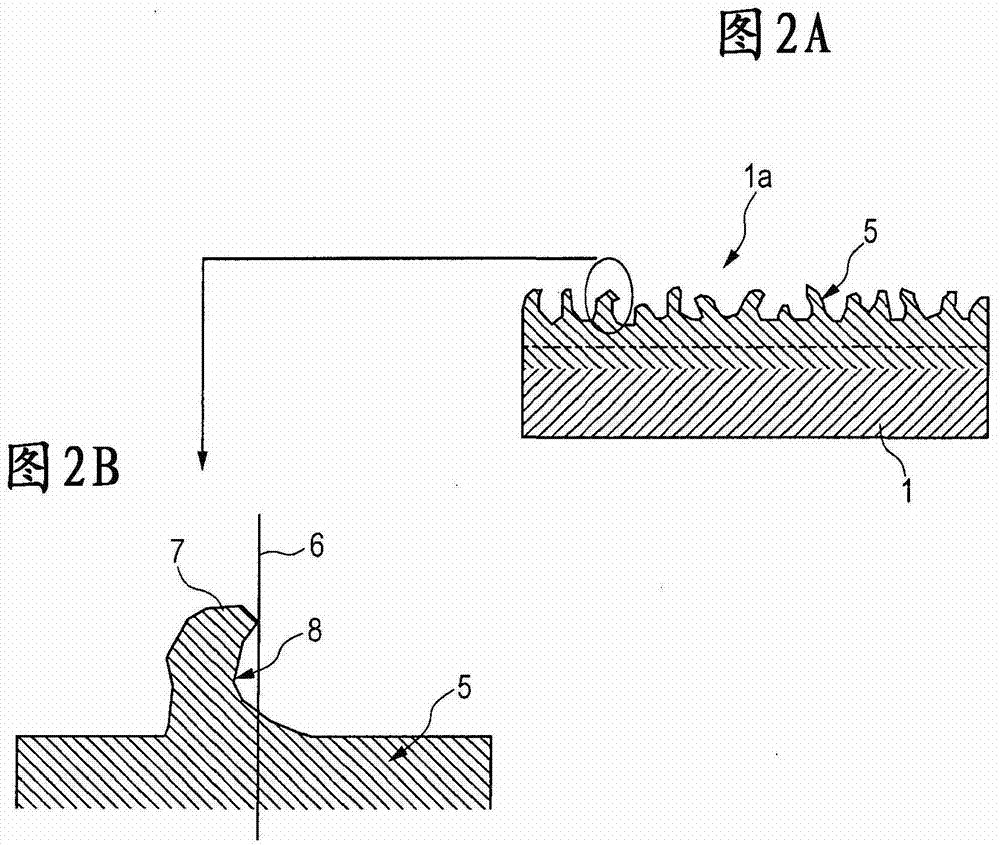
半导体器件及其制造方法相关申请的交叉引用2012年3月1日提交的日本专利申请No.2012-045115的公开,包括说明书、附图和摘要,通过引用整体合并于此。技术领域本发明涉及半导体器件,更特别地,涉及一种当应用到例如使用金属构件的树脂密封型半导体器件时有效的技术。
背景技术:汽车领域等中使用的半导体器件用在严酷使用环境下,从而要求它们与消费使用或工业使用的半导体器件相比具有远远更高的可靠性。在使用金属构件的树脂密封型半导体器件中,归因于树脂的湿气吸收和密封体(封装)中的热应力,产生密封树脂从金属构件(金属引线(lead)等)剥离。这种剥离成为在半导体元件与金属构件之间的结合处生成裂缝的原因,导致形成有缺陷的半导体器件。作为用于稳固地结合金属构件和密封树脂的传统方法,通过镀敷(plating)或刻蚀进行金属构件的表面的粗糙化的方法是已知的。例如,日本专利公开No.148508/1997(专利文献1)公开了涉及树脂密封型半导体器件的如下内容。通过在超过临界电流密度的电流密度下用Cu、CuNi、Zn、Ni等电镀基于Cu或基于Fe的引线框架来形成针状或树枝状粗糙化层。然后通过以下方式在所得粗糙化层上形成覆盖层:以不大于临界电流密度的电流密度用两个Cu和Zn层、CuZn、Cr、ZnCr、两个Ni和InZn层、NiP、或两个Ni和CuZn层对所得粗糙化层进行电镀。粗糙化层和覆盖层协作地贡献于引线框架与树脂之间的结合强度方面的改进以及可靠性(例如湿气耐受性、热冲击耐受性等)方面的改进。日本专利公开No.2002-299538(专利文献2)公开了涉及一种引线框架以及使用所述引线框架的半导体封装的如下内容。待与密封树脂接触的引线框架的表面经历粗糙化镀敷,然后是用金属对镀敷了的引线框架上的导线键合所需的部分进行镀敷。日本专利公开No.46116/1996(专利文献3)公开了涉及一种引线框架的如下内容。以下方法中的任一种用于形成待模制(mold)的引线框架的至少一部分表面上的粗糙化表面。方法之一是:在含水溶性还原剂(例如氯化铁或肼)的水溶液中刻蚀Cu或Ag。另一方法是:在10V或更大但不大于50V的电压和40A/dm2或更大但不大于200A/dm2的阳极电流密度的处理条件下用硝酸盐类电解质进行电解刻蚀。这种粗糙化表面的形成改进了引线框架与模制树脂之间的粘合。专利文献1:日本专利公开No.148508/1997专利文献2:日本专利公开No.2002-299538专利文献3:日本专利公开No.46116/1996
技术实现要素:专利文献1或专利文献2中公开的表面粗糙化镀敷技术不能总是改进引线框架与镀敷膜之间的粘合,并且它依赖于表面粗糙化镀敷的材料。另一方面,在专利文献3公开的刻蚀诱导的表面粗糙化技术中,对于引线框架所使用的材料是有限制的,因此,并未改进金属构件(例如引线框架)与密封树脂之间的粘合。从这里的描述和附图,其它问题和新颖特征将是清楚的。根据一实施例的制造半导体器件的方法包括:通过使用已经经历基材(basematerial)和其表面上所镀敷的Zn的合金化处理的金属构件(例如引线框架)来进行树脂密封。以上述实施例作为一示例,可以改进金属构件与密封树脂之间的粘合。附图说明图1包括示出根据第一实施例的半导体器件制造方法的步骤流程图以及与步骤对应的示意性横截面视图;图2A和2B是示出从第一实施例至第七实施例的悬突(overhang)结构的定义的示意性横截面视图;图3示出Cu板的Zn镀敷时间和抗切强度(shearstrength);图4示出镀Ni的Cu板的Zn镀敷时间和抗切强度;图5示出Cu板的Zn扩散处理条件与抗切强度之间的关系;图6示出镀Ni的Cu板的Zn扩散条件与抗切强度之间的关系;图7示出每个都应用于Cu板的比较性示例中的表面处理方法与Zn扩散合金化处理方法之间的抗切强度比较;图8A、8B、8C和8D包括模制之后的横截面SEM图像,示出在改变Zn镀敷时间的同时经历扩散处理的Cu板的横截面结构;图9A和9B包括模制之前和之后的横截面SEM图像,示出接连经历Zn镀敷和扩散处理的镀Ni的Cu板的横截面结构;图10A、10B和10C包括在每个表面处理之后Cu板的表面形式和横截面形状的SEM图像;图11A、11B和11C示出在使用每种表面处理方法进行处理之后Cu板在模制之前和之后的横截面形状的SEM图像;图12是示出根据第二实施例的半导体器件制造方法的步骤流程图;图13A和13B示出在Zn扩散合金化处理之前引线框架的部分外观;图14A和14B示出将掩模夹具附连到引线框架的结构;图15示出掩模夹具已经附连到的引线框架的Zn电镀方法;图16A和16B包括示出在通过掩模夹具而选择性地镀敷Zn之前以及在镀敷和合金化处理之后引线框架的外观的视图;图17A和17B示出通过根据第二实施例的半导体器件制造方法所制造的半导体器件;图18是示出基于根据第三实施例的半导体器件制造方法的制造步骤的步骤流程图;图19包括与根据第三实施例的半导体器件制造方法的步骤流程图的各个步骤对应的引线框架外观的平面视图和横截面视图;图20A和20B示出通过使用根据第三实施例的半导体器件制造方法所制造的半导体器件;图21包括示出根据第四实施例的半导体器件制造方法的引线框架外观的平面视图和横截面视图;图22是示出基于根据第五实施例的半导体器件制造方法的制造步骤的步骤流程图;图23A、23B和23C示出通过使用根据第五实施例的半导体器件制造方法所制造的半导体器件;图24是示出基于根据第六实施例的半导体器件制造方法的制造步骤的步骤流程图;图25A、25B、25C和25D示出通过使用根据第六实施例的半导体器件制造方法所制造的半导体器件;图26A和26B示出通过使用根据第七实施例7的半导体器件制造方法所制造的半导体器件;以及图27示出实施例1至7应用到的半导体器件的引线框架表面的金属化规格与连接材料等之间的关系。具体实施方式1.首先,接下来将描述发明人通过在本发明之前进行的研究和测试、测试结果分析等而新揭示的问题。(1)镀敷诱导的粗糙化根据用于粗糙化镀敷的材料,用Zn、Cu、Ni等对基于Cu或基于Fe的引线框架进行粗糙化镀敷且然后在所得引线框架上形成覆盖层的方法具有以下问题。因此,使用粗糙化镀敷方法难以提供在湿气耐受性和热冲击耐受性方面优异的树脂密封型半导体器件。(a)具体地,在Zn镀敷中,当在粗糙化镀敷之前的脱脂或氧化膜移除不完全时,与位于其下的引线框架的粘合并未得到改善,并且归因于镀敷膜的弱粘合,界面分离出现在镀敷膜与引线框架之间。(b)具体地,当在镀Ni的Cu框架中,Ni和Cu从引线框架的表面暴露时,难以保持不同材料的各个表面的最佳条件,因为适合于它们的预处理液体是不同的。难以通过相同的镀敷处理获得在Cu表面和Ni表面二者上都良好粘合并且可以提供大的锚固(anchor)效应的具有不规则物的粗糙化表面。(c)在用Cu进行的粗糙化镀敷中,与下面的Ni具有差的粘合,这使得难以选择适当的下层材料。当Cu是下层金属时,其上所形成的树枝状粗糙化层可以改善结合强度,但因为控制树枝状(dendrite)结构的树干(trunk)的厚度和粗糙化层的厚度方面的困难,所以难以获得稳定且高强度的结合部分。增大树枝状粗糙化层的厚度增加了自由Cu淀积,这使粗糙化层自身的强度恶化。因此,通过用Cu进行粗糙化镀敷在获得高锚固效应方面存在限制。(d)用Ni进行粗糙化镀敷在与Cu或Ni粘合方面是优异的,但其不规则形式是V形且具有向上直径增大的开口,从而不能实现足够的锚固效应。因此,难以在不依赖于下层金属材料的情况下通过使用相同的粗糙化镀敷方法来获得高强度地结合到下层Cu或Ni的部分。(2)刻蚀诱导的粗糙化另一方面,刻蚀诱导的粗糙化具有以下问题。(a)由于在该方法中表面被刻蚀,所以存在镀敷构件损失其镀敷膜的可能性。此外,刻蚀剂根据金属材料而不同,从而在复合材料的情况下,不能均匀地对不同金属制成的表面进行粗糙化。结果,在某些位置中,结合强度变弱。(b)当用于刻蚀时产生大的锚固效应的材料仅是容易刻蚀的材料(例如Cu),具有良好抗蚀性的材料(例如Ni)不适合于在刻蚀诱导的粗糙化中使用。因此,仅可以对以Cu为基础的引线框架使用该方法。在此情况下,由于粗糙化表面的剥离方向上的结合强度不够高,因此结合部分的Cu/树脂界面发生剥离,在早期在芯片的焊料接合处生成裂缝,导致抗冲击可靠性方面的恶化。特别地,该问题倾向于出现在例如与密封树脂的结合区域小的单侧模制封装中。2.实施例的细节接下来将参照附图具体地描述实施例。在以下实施例中,为了方便,如果需要的话描述将在划分为多个章节或实施例之后进行。除非另外具体地声明,否则它们并非彼此独立,而是关联的,从而一个是另一个的一部分或全部的修改示例、应用示例、详细描述、补充描述等。在以下实施例中,除非另外具体地声明或在原理上显然的是数量被限制到特定数目,否则当提及元件的数量时(包括数量、值、量、范围等),数量不限于特定数量,而是可以大于或小于特定数量。此外,在以下实施例中,构成元素(包括元件、步骤等)并非总是必要的,除非另外具体声明或原理上显然它们是必要的。类似地,在以下实施例中,当提及组成元素的形状、位置关系等时,与其基本相近或类似的形状、位置关系等也被涵盖,除非另外地具体表明或者原理上显然并非如此。这也适用于上述数量(包括数量、值、量、范围等)。在用于描述下述实施例的所有附图中,相似附图标记将指示相似功能的构件,并且将省略重复描述。在以下实施例中,除非特别必要,否则原则上将省略相同或相似部分的重复描述。<第一实施例>(1)构成和方法:图1包括示出根据第一实施例的半导体器件制造方法的步骤流程图以及与步骤对应的示意性横截面图。在图1A、图1B、图1C和图1D中分别是与左侧示出的步骤对应的示意性横截面视图。这些示意性横截面视图示出处理为预定形状并且具有外部耦合端子的基材的一部分。这是没有半导体元件结合到的区域,并且同时,是将要镀有下述Zn膜4的区域。这些附图中未示出其中外部耦合端子和半导体元件将要耦合到彼此的区域。(a)准备金属构件的步骤首先,将描述准备将要在制造步骤中使用的金属构件的步骤。如图1A所示,准备处理为预定形状并且具有外部耦合端子的基材1(步骤S11)。这里,基材1是例如引线框架。基材1包含例如诸如Cu或Cu合金的金属,并且同时在材料表面上具有Ni、Cu、Ag、Pd/Au等中的任何一种的一个或多个金属化层(未示出)。基材1在其表面上具有如图1A的示意性横截面图所示的氧化膜(自然氧化膜)2。然后,如图1B所示,基材1的表面经历脱脂和酸液浸洗(pickling)处理(例如,碱性电解质脱脂、漂洗、酸液浸洗等)(步骤S12)。如图1C所示,通过镀敷在基材1的表面上形成Zn膜4(步骤S13)。在某些区域(例如半导体元件将要耦合到的区域)中并不形成Zn膜4。换句话说,在基材1的表面上有选择地形成Zn膜4。Zn膜4具有从0.1μm至几十μm的厚度,优选地从1μm至5μm。例如,通过镀敷来形成Zn膜4。然后,在非氧化气氛或还原气氛中对其上形成有Zn膜4的基材1进行加热,以通过Zn膜4和金属构件1的相互扩散来进行合金化处理(步骤S14)。加热温度从200°C至600°C,优选地从300°C至400°C。结果,在基材1的表面上形成具有带悬突结构的不规则表面的合金层5。简而言之,制备了已经经历Zn扩散合金化处理的金属构件1a(步骤S15)。当用密封树脂覆盖基材1的侧表面或下表面以及上表面时,在侧表面或下表面上也形成合金层5。(b)制造步骤接下来,将描述半导体器件的制造方法。制备金属构件1a和半导体元件(步骤S15和S16)。半导体元件(未示出)然后结合到未形成Zn膜4的金属构件1a的预定区域(未示出)。所述预定区域是半导体元件结合部分,并且其与管芯焊盘、接片(tab)等对应。这里可使用的管芯结合材料是例如高熔点焊料、Ag烧结物膏剂(sinterpaste)、树脂结合Ag膏剂等。在此使用的术语“管芯结合材料”表示用于将半导体元件结合到半导体元件结合部分的材料。半导体元件的电极(未示出)经由导体电耦合到金属构件1a的外部耦合端子(步骤S18)。作为导体,例如,使用键合导线(bondingwire)(未示出)或键合带(未示出)。半导体元件的电极以例如Al制成。键合导线材料以例如Al或Au制成。带材料以例如Al制成。用密封树脂(未示出)密封半导体元件和金属构件1a以形成半导体器件(步骤S19)。例如,通过在使用热固化环氧树脂的同时使用传递模制来进行密封。环氧树脂含有填料。当在金属构件1a的下表面或侧表面以及金属构件1a的其上安装半导体元件的上表面上形成合金层5时,可以用密封树脂来覆盖所述下表面或侧表面。可以在步骤S12之前进行步骤S17和S18。这意味着半导体元件结合到金属构件1a的未形成Zn膜4的预定区域(步骤S17)。半导体元件的电极和金属构件1a的外部耦合端子经由导体彼此电耦合(步骤S18)。在这些步骤之后,可以进行步骤S12、S13、S14和S19中的每个。(2)机制接下来,将基于图1描述具有带悬突结构的不规则表面的合金层5的形成机制。图1A所示的基材经历脱脂和酸液浸洗预处理。结果,如图1B所示,氧化膜2有选择地残留作为基材1的表面上的残余氧化膜3。如图1C所示,以高电流密度在基材1的表面上高速电镀的Zn膜4归因于残余氧化膜3而在微小级别上不均匀地淀积在基材1的表面上。淀积开始点局部地分散。在基材1与Zn膜4之间的粘合程度方面存在限制差异,这取决于淀积时间的差异。当在不允许熔化Zn膜4的条件下执行扩散处理时,通过Zn膜4与基材1之间的相互扩散来形成合金层5并非在基材1的整个表面上均匀地进行,而是局部地进行。结果,在合金化之后在表面上形成范围从纳米(10-9m)到微米(10-6m)的不规则物。基材1的金属元素形成合金层5,从而从Zn膜4中的扩散入口扩展。Zn膜4的金属元素从扩散入口扩展到基材1一侧,使合金层5生长以提升该扩散入口区。远离入口的位置凹入。归因于相互扩散速率的差异,在扩散速率高的金属元素侧生成Kirkendall孔洞。当一些Kirkendall孔洞从表面暴露时,形成开口部分,并且形成在其内具有凹陷的悬突结构。具有这种结构的不规则物对于膜形成/扩散处理工艺是特定的,并且其特征在于:合金层5与基材1之间不存在界面,合金层的晶体颗粒和成分都从基材1是连续的。这样的合金层5与基材1是一体的,从而不产生合金层5的剥离。更特别地,由于具有带悬突结构的精细不规则表面的合金层5的表面和密封树脂经由强锚固效应彼此结合,因此在合金层5与密封树脂之间的界面处不产生剥离。即使基材1的材料不同,相互扩散现象也是相同的。当与以上例举的Ni、Cu、Ag或Pd/Au不同的金属制成基材1时,可以通过相同处理工艺来获得允许与密封树脂的稳固结合的半导体器件。此外,仅有几百nm至几十μm厚度的Zn膜4可以形成必要的不规则物,从而可以减少用于膜形成的镀敷时间以及镀敷溶液的消耗,使得可以实现低成本处理工艺。无论基材的材料如何,当采用根据实施例1的所述制造方法时,与密封树脂的结合强度对应于树脂中的破裂强度。因此,可以获得即使暴露到高温高湿度环境或剧烈温度波动时在密封树脂与金属构件之间的界面处也不产生剥离并且表现出长期高稳定性的树脂密封型半导体器件。形成具有带悬突结构的不规则表面的合金层5的上述机制也与稍后将描述的第二实施例至第七实施例中的相似。简而言之,通过与第一实施例相似的机制来形成合金层。(3)悬突结构的轮廓接下来将参照图2A和2B描述第一实施例中描述的不规则物的悬突结构的定义。图2A和2B是示出第一实施例至第七实施例的悬突结构的定义的横截面视图。该横截面视图示出金属构件1a的包括合金层5的部分。如该图所示,相对于金属构件1a的底表面的垂直线6作为标准,凹陷8相对于上部的凸出7存在于下部处。这种结构在此定义为“悬突结构”。这将类似地应用到稍后将描述的第二实施例至第七实施例。(4)测试结果接下来将参照图3至图11描述根据第一实施例的半导体器件制造方法的测试结果。图3示出Cu板的Zn镀敷时间和抗切强度。图4示出镀Ni的Cu板的Zn镀敷时间和抗切强度。在两种情况下评估基材对密封树脂的结合强度,即在基材是Cu板时(图3)和在基材是镀Ni的Cu板(图4)时。用抗切强度(MPa)来指示结合强度。图3和图4示出密封树脂与没有Zn镀敷的样本、镀Zn到各个膜厚度的样本以及已经镀Zn到各个膜厚度且然后在400°C加热2分钟的样本之间的结合强度。此外,在以下条件下进行Zn镀敷:25°C的镀敷溶液温度以及3A/dm2的电流密度。以镀敷时间来指示Zn镀敷的各个膜厚度。没有Zn镀敷的样本的镀敷时间与示为“未处理”的0s镀敷时间对应。示为结合强度的测量结果是在密封树脂的模制之后的结合强度以及在85%和85°C的湿气吸收处理达168小时且然后进行三次在260°C的回流(reflow)处理之后的树脂模制样本的结合强度。前者指示为“树脂模制之后”,后者指示为“湿气吸收和回流之后”。图3的Cu板和图4的镀Ni的Cu板每个都具有1mm的厚度。图5示出Cu板的Zn扩散处理条件与抗切强度之间的关系。图6示出镀Ni的Cu板的Zn扩散处理条件与抗切强度之间的关系。图5和图6示出在变化的热处理温度和时间(Zn扩散处理条件)下处理Cu板和镀Ni的Cu板中的每个时密封树脂的结合强度。Cu板的厚度是0.5mm,镀Ni的Cu板的厚度是1mm。如图3和图4中,以抗切强度(MPa)来指示结合强度。Zn镀敷时间在图5和图6中是20s,镀敷厚度是0.2μm。在以下条件下进行Zn镀敷:25°C的镀敷溶液温度以及3A/dm2的电流密度。作为密封树脂,使用环氧树脂。图7示出都应用于Cu板的比较性示例中的表面处理方法与根据第一实施例的Zn扩散合金化处理方法之间的抗切强度比较。在图7中,比较性示例中所采用的表面处理方法是通过刻蚀(刻蚀诱导的粗糙化)和Cu镀敷诱导的粗糙化进行的表面粗糙化。为了比较,还示出未经历表面粗糙化的Cu板。未经历表面粗糙化的Cu板指示为“ref”。沿横坐标绘制Cu镀敷时间和Zn镀敷时间。在以下条件下进行Zn镀敷:25°C的镀敷溶液温度以及3A/dm2的电流密度。基材是具有1mm厚度的Cu板。图7包括两个样本的测量结果。它们之一是在密封树脂模制之后的样本,另一个是接连经历密封树脂模制、在85%和85°C湿气吸收处理达168小时、以及在260°C三次回流处理的样本。以“在树脂模制之后”指示前者,以“在湿气吸收回流之后”指示后者。从图7已经发现,当进行Zn镀敷达到100s或更大时,在树脂模制之后和在湿气吸收回流之后的抗切强度都优于比较性示例的表面处理方法的抗切强度。从图3至图7显见,已经确认,与没有热处理的情况相比,Cu板通过400°C的热处理获得改进的结合强度,镀Ni的Cu板通过250°C或更高的热处理获得改进的结合强度。特别地,已经确认,镀Ni的Cu板通过250°C或更高的热处理获得显著改进的结合强度。在Cu板和镀Ni的Cu板二者中,在400°C的加热条件下实现最大强度。这些结果已经揭示,仅通过Cu板或镀Ni的Cu板的Zn镀敷并不能实现稳定的树脂结合特性,而当增加热处理时可以实现稳定且高的结合强度。此外,与比较性示例中的刻蚀诱导的粗糙化或Cu镀敷诱导的粗糙化相比,改进了抗切强度。还已经发现,作为减少归因于湿气吸收和回流而导致的劣化并且增加强度的Zn镀敷条件,以下镀敷条件是优选的:25°C的镀敷溶液温度、3A/dm2的电流密度,并且100s或更长的镀敷时间(Zn膜厚度≥大约1μm)。图8A、8B、8C和8D包括示出在密封树脂模制之后在改变Zn镀敷时间的同时通过在400°C加热而经历扩散处理的Cu板的截面结构的横截面SEM(扫描电子显微镜)图像。图8A的Zn镀敷时间是20s,图8B的是50s,图8C的是100s,图8D的是200s。图9A和9B包括示出经历了Zn镀敷且然后通过在400°C加热进行了扩散处理的镀Ni的Cu板在密封树脂模制之前和之后的截面结构的横截面SEM图像。图9A示出在密封树脂模制之前的截面结构,图9B示出在密封树脂模制之后的截面结构。Zn镀敷时间在图9A和图9B中都是100s。以相同倍率(即×50000)来拍摄图8A、8B、8C和8D以及图9A和9B的SEM图像。在以下条件下进行Zn镀敷:25°C的镀敷溶液温度以及3A/dm2的电流密度。图8A、8B、8C和8D以及图9B示出在彼此结合的金属构件与密封树脂之间的界面处的结构。图8A、8B、8C和8D的金属构件以Zn和Cu的合金制成,图9A和9B的金属构件以Zn和镀Ni的Cu的合金制成。金属构件在其表面层上具有带精细节距(pitch)的无定形凹入和凸出,密封树脂中所含的填料保留在凸出的上部分中。另一方面,已经确认,通过已经穿透并且填充凹入空间的密封树脂的树脂成分形成了稳固结合的界面。简而言之,当Zn镀敷时间是20s或50s时,金属表面未被充分粗糙化,带有悬突结构的不规则表面既没有所需高度,也没有所需形状。另一方面,当Zn镀敷时间是100s或200s时,带有悬突结构的不规则表面具有足够的高度,树脂成分已经穿透并且填充凹入空间,树脂和金属已经通过机械锚固效应而得以结合。已经发现,甚至当向上的力施加到树脂时,已经穿透到凹入内的树脂在很多地方与金属部分缠结以防止树脂向上拉起,从而可以通过该不规则形式得到强机械锚固效应。图10A、10B和10C包括示出在各个表面处理之后Cu板的表面形状(上级)和横截面形状(下级)的SEM图像。图10A示出通过刻蚀所得的粗糙化表面,图10B示出通过Cu镀敷所得的粗糙化表面,图10C示出通过Zn镀敷和扩散所得的粗糙化表面。它们是在密封树脂模制之前的粗糙化表面。以45°的倾斜来取得图10A和图10B的表面形状(上级)。在无倾斜的情况下取得图10C的表面形状(上级)。图10B中的Cu镀敷时间是120s,图10C中的Cu镀敷时间是100s。从这些图可见,通过Zn镀敷和扩散所得的粗糙化表面上的悬突结构高于通过刻蚀所得的粗糙化表面或通过Cu镀敷所得的粗糙化表面上的悬突结构。图11A、11B和11C包括示出经历各种表面处理方法的Cu板在密封树脂模制之前和之后的横截面形状的SEM图像。在图11A、11B和11C中,在上级示出在密封树脂模制之前的SEM图像,在下级示出在密封树脂模制之后的SEM图像。图11A示出通过刻蚀所粗糙化的表面与树脂之间的界面的横截面形状;图11B示出通过Cu镀敷所粗糙化的表面与树脂之间的界面的横截面形状;图11C示出通过Zn镀敷和扩散所粗糙化的表面与树脂之间的界面的横截面形状。基于第一实施例进行图11C中的通过Zn镀敷和扩散进行的表面粗糙化。图11A的样本具有23.2MPa的抗切强度;图11B的样本具有25.6MPa的抗切强度;图11C的样本具有30.0MPa的抗切强度。具有Zn镀敷和扩散所粗糙化的表面的样本具有最大的抗切强度并且在树脂结合强度方面是优异的。根据第一实施例的通过Zn镀敷和热处理扩散所粗糙化的表面具有合金层,其具有带悬突结构的多个不规则物并且与在比较性示例中通过刻蚀所粗糙化的表面或通过Cu镀敷所粗糙化的表面相比具有更大的高度和更多的凹入。具有该悬突结构的多个不平坦部分被用密封树脂完全填充。(5)结论如上所述,归因于在金属构件的表面上形成具有带悬突结构的多个不规则物的含Zn层,在密封步骤中结合的密封树脂刺入金属构件的凹入以形成具有良好粘合的界面。归因于密封树脂与金属构件之间的机械锚固效应,可以获得稳固结合的部分。在通过锚固效应获得的结合部分中,与通过化学相互作用所获得的结合部分不同,结合强度不受水的侵入影响,从而即使在暴露于高温高湿度环境之后,也可以保持高稳定性。结果,密封树脂导致的压应力可以施加到半导体元件与金属构件所结合到的半导体元件部分之间的结合部分。因此,可以提供能够防止在接合处生成裂缝且因此即使在温度波动重复出现的环境下也具有高可靠性的树脂密封型半导体器件。可以提供可靠性高到足以在严酷环境(例如汽车领域)中使用的半导体器件。相应地,可以提供一种制造半导体器件的方法,该半导体器件即使在高温高湿度环境下或即使重复地施加热应力也能够防止半导体元件从金属构件剥离。此外,通过使用进行Zn镀敷然后加热/合金化处理以稳固地结合金属构件的方法,可以在不依赖于金属构件的材料的情况下在相同处理条件下改进与密封树脂的结合强度。结果,即使金属构件是以不同金属制成的复合构件,也可以提供具有高可靠性的半导体器件。此外,无论金属是什么种类,都可以通过相同处理改进与树脂的粘合,这对于减少金属构件的处理线数量并且由此减小设备成本是有效的。此外,当Zn金属板用作电极时,可以减少Zn镀敷溶液的消耗量,而且相对粗略地进行预处理并且执行高速镀敷以减少镀敷时间,这对于提供仅需要低运作成本并且因此减少生产成本的处理方法是有效的。<第二实施例>图12是示出根据第二实施例的半导体器件制造方法的步骤流程图。图13A至图16B示出图12所示的步骤流程的各个步骤。图13A和13B示出在Zn合金化处理之前的部分引线框架。图13A是平面视图,图13B是沿着图13A的线a-a'取得的横截面视图。图14A和14B示出用于引线框架的掩模夹具附连结构。图14A是横截面视图,图14B是从方向W观察的图14A的侧视图。图15示出与掩模夹具附连的引线框架的Zn电镀方法。图16A和16B示出在使用掩模夹具的选择性Zn镀敷之前和在镀敷和合金化处理之后的引线框架的外观。图16A是在镀敷之前的引线框架的外观的平面视图,图16B是在镀敷和合金化处理之后的引线框架的外观的平面视图。图17A和17B包括使用根据第二实施例的半导体器件制造方法所制造的半导体器件的平面视图和横截面视图,其中,图17A是已经移除上部分密封树脂的半导体器件的平面视图,图17B是沿图17A的直线a-a'取得的横截面视图。第二实施例是使用经历Zn镀敷和合金化处理的引线框架的半导体器件制造方法。根据图12所描述的步骤流程,接下来将参照图12和图13A至图17B描述第二实施例。(1)准备引线框架的步骤首先,描述准备将在制造步骤中使用的引线框架的步骤。制备如图13A和图13B描述的处理为预定形状并且具有外部耦合端子的引线框架21(步骤S21)。引线框架21包括管芯焊盘9、基台(header)10和管芯焊盘引线端子11。此外,引线框架21包括主电极键合焊盘12、主电极引线端子13、控制电极键合焊盘14和控制电极引线端子15。此外,引线框架21包括框体(framework)19和悬置引线20。基台10具有穿透孔。管芯焊盘9和基台10其间具有密封树脂固定槽16。管芯焊盘9具有第一掩模化区域17,用于对管芯焊盘区域33进行掩模化。引线框架21具有第二掩模化区域18,用于对管芯焊盘引线端子11的一部分、主电极键合焊盘12和主电极引线端子13进行掩模化。引线框架21具有第二掩模化区域18,用于对控制电极键合焊盘14、控制电极引线端子15和框体19进行掩模化。引线框架21与基材1对应;管芯焊盘区域33与半导体元件结合部分对应;管芯焊盘引线端子11、主电极引线端子13和控制电极引线端子15与外部耦合端子对应。主电极引线端子13也称为第一引线端子;控制电极引线端子15也称为第二引线端子;管芯焊盘引线端子11也称为第三引线端子。主电极键合焊盘12也称为第一焊盘;控制电极键合焊盘14也称为第二焊盘;管芯焊盘9也称为第三焊盘。对引线框架21进行脱脂和酸液浸洗(步骤S22)。例如,进行碱性电解质脱脂、漂洗、酸液浸洗等。然后,如图14A和14B所示,用作为掩模夹具的橡胶掩模24和25来覆盖所得脱脂和酸液浸洗了的引线框架21的将不被镀敷的区域(掩模化区域17和18)。引线框架21以及橡胶掩模24和25夹在下保持夹具22与上保持夹具23之间,并且用夹持螺栓26和螺母27固定。如图15所示,与掩模夹具附连的引线框架21、电极29和镀敷溶液30放置在容器31中,引线框架21和电极29耦合到电源28以进行选择性Zn电镀(步骤S23)。此时以3A/dm2的电流密度和200s的镀敷时间来进行电镀。在400°C在H2气体气氛中对用Zn有选择地电镀了的引线框架21进行加热达到2分钟,以进行Zn扩散合金化处理(步骤S24)。结果,可以制备经历Zn扩散合金化处理的引线框架21a。图16A和16B示出在镀敷之前的状态和在Zn扩散合金化处理之后的状态。图16A是示出在选择性镀敷之前引线框架21的部分外观的平面视图,图16B是示出经历选择性镀敷且然后被合金化处理的引线框架21a的部分外观的平面视图。通过Zn镀敷和合金化处理所获得的粗糙化Zn合金层32a、32b和32c对应于通过Zn膜4与金属构件1之间的相互扩散进行的合金化所获得的并且在金属构件1的表面上具有带悬突结构的不规则表面的根据第一实施例的半导体器件的合金层5。(2)制造步骤接下来,将描述半导体器件的制造步骤。准备已经经历了Zn扩散合金化处理的引线框架21a和半导体元件34(步骤S25、步骤S26)。这里所使用的半导体元件34是例如半导体芯片,诸如MOS晶体管或双极晶体管。半导体元件34包括主电极35、控制电极36和背电极37。主电极35也称为第一电极;控制电极36也称为第二电极,背电极37也称为第三电极。如图17A和17B所示,半导体元件34的背电极37通过管芯结合材料38结合到管芯焊盘9的管芯结合区域33上(步骤S27)。作为管芯结合材料,例如,高熔点焊料、Ag烧结物膏剂或树脂结合Ag膏剂是可使用的。半导体元件34的主电极35和引线端子15的主电极键合焊盘12经由导线39彼此耦合(步骤S28)。此外,控制电极36和引线端子13的控制电极键合焊盘14经由导线40彼此耦合(步骤S28)。可以用带或引线代替导线39和40。导线、带或引线的材料也可以是Al、Cu或Au。然后,以密封树脂41密封引线框架21a、半导体元件34以及导线39和40(步骤S29)。用例如热固化环氧树脂使用传递模制来进行该密封。环氧树脂含有填料。金属引线暴露部分(例如待耦合到安装板的部分)经历焊料镀敷42a和42b(步骤S30)。最后,引线框架21a被切割为所期望的形状(步骤S31),以完成图17A和17B所示的半导体器件45(步骤S32)。如图17A和17B所示,以密封树脂41来覆盖粗糙化的Zn合金层32b、32c和32d,从而它们具有改进的与密封树脂41的结合强度。(3)结论根据第二实施例,除了将经由导线或带键合到管芯结合区域33的区域12和14之外,至少已经用Zn镀敷了将通过密封树脂41密封的引线框架21的区域。通过加热处理,Zn和引线框架21的金属构成粗糙化的Zn合金层32a、32b、32c和32d。这使得可以显著改进在密封树脂41的模制之后的引线框架21a和密封树脂41的界面结合强度。在如此获得的半导体器件中,密封树脂41归因于机械锚固效应而稳固地结合到管芯焊盘9或管芯焊盘引线端子11。在管芯焊盘9或管芯焊盘引线端子11与密封树脂41之间不产生界面剥离。结果,可以提供能够防止在密封树脂41中的界面处的热应力诱导的裂缝并且因此具有高可靠性的半导体器件。此外,在如此获得的半导体器件中,不产生管芯结合或导线键合的质量方面的恶化,也不产生管芯焊盘9或键合焊盘12或14与密封树脂41之间的界面剥离。结果,可以避免将归因于在每个接合处(密封树脂41与管芯焊盘9或管芯焊盘引线端子11之间的接合处)的温度波动而产生的热应力聚集,压应力恒定地施加到接合处。相应地,可以防止在接合处生成穿透裂缝,使得可以提供高度可靠的半导体器件。因此,能够提供高度可靠的半导体器件,即使其特别地用在暴露于高温和高湿度的严酷环境中或暴露于温度重复波动的环境中时。在第二实施例中,作为粘合改进处理,Zn镀敷后跟着是加热和合金化处理。可以在不依赖于引线框架质量的情况下在相同处理条件下改进与密封树脂的结合强度。即使引线框架是以不同种类的金属制成的复合构件,也可以提供具有高可靠性的半导体器件。由于与树脂的粘合可以通过相同处理得到改善而不管金属为何种类,所以可以减少引线框架的处理线的数量,导致设备成本方面的减少。此外,可以通过使用Zn金属板作为电极来减少溶液的消耗。以相对粗略的方式来进行预处理,并且使用高速镀敷,可以减少镀敷时间,从而可以提供具有小运作成本的处理方法,并且可以减少制造成本。<第三实施例>图18是示出根据第三实施例的半导体器件制造方法的步骤流程图。图19的(A)至(F)包括与图18所示的步骤流程对应的平面视图(左侧)和横截面视图(右侧)。它们每个对应于一个半导体器件。图20A和20B包括使用根据第三实施例的半导体器件制造方法所制造的半导体器件的平面视图(图20A)和横截面视图(图20B)。图20A是已经移除上部分密封树脂的平面视图,图20B是沿图20A的线a-a'取得的横截面视图。在第三实施例中,除了抗镀剂(platingresist)用作镀敷掩模之外,与第二实施例相似地进行Zn扩散合金化处理。接下来,基于图18的步骤流程,将参照图19和图20A-20B描述第三实施例。(1)准备引线框架的步骤首先,将描述准备将在制造步骤中使用的引线框架的步骤。如图19(A)所示,准备引线框架21b(步骤S31)。在此所使用的引线框架21b与引线框架21相似,除了引线框架21b没有密封树脂固定槽16之外。如图19(B)所示,抗镀剂43a、43b和43c分别形成在引线框架21b的管芯结合区域33、主电极键合焊盘12和控制电极键合焊盘14上,以对其进行覆盖(步骤S32)。图19(C)示出在引线框架21b的脱脂和酸液浸洗以及Zn电镀以在未用抗焊剂43a、43b和43c覆盖的区域中有选择地形成Zn镀敷膜44之后(步骤S33)。在以下条件下进行镀敷:3A/dm2的电流密度,200s的镀敷时间。然后,移除抗焊剂43a、43b和43c(步骤S34)。如图19(D)所示,进行Zn扩散合金化处理以形成粗糙化的Zn合金层32a、32b、32c、32d(步骤S35)。在400°C的加热温度在H2气体气氛中进行合金化处理,加热时间为2分钟。这准备了已经完成Zn扩散合金化处理的引线框架21c(步骤S36)。(2)制造步骤接下来将描述半导体器件的制造步骤。准备已经完成了Zn扩散合金化处理的引线框架21c和半导体元件34(步骤S36、步骤S37)。作为半导体元件34,使用与第二实施例相似的半导体芯片。如图19(E)所示,半导体元件34的背电极37用管芯结合材料38管芯结合到引线框架21b的管芯焊盘9(步骤S38)。这里可使用的管芯结合材料是例如高熔点焊料、Ag烧结物膏剂或树脂结合Ag膏剂。高熔点焊料的示例包括Pb焊料和SnSb焊料。半导体元件34的电极35和36分别经由导线39和40耦合到引线端子的主电极键合焊盘12和控制电极键合焊盘14(步骤S39)。电极35和36的材料是例如Al。代替导线39和40,带或引线可以用于耦合。导线、带或引线的材料还可以是Al、Cu或Au。如图19(F)所示,以树脂来密封引线框架21c、半导体元件34、导线39和40、主电极键合焊盘12、控制电极键合焊盘14等(步骤S40)。对于该密封,可以采用以例如热固化环氧树脂进行的传递模制。环氧树脂含有填料。以密封树脂41覆盖半导体元件34、导线39和40、主电极键合焊盘12、控制电极键合焊盘14等。图19(F)的平面视图示出移除上部分树脂之后。然后,通过碱性清洁来移除金属引线暴露部分的Zn(步骤S41),接着是金属引线暴露部分的焊料镀敷(步骤S42)。切割引线框架21c的不必要部分以获得期望的形状(步骤S43)。结果,完成图20A和20B所示的半导体器件45a(步骤S44)。在图19中,可以用源电极键合焊盘和栅电极键合焊盘分别代替主电极键合焊盘12和控制电极键合焊盘14。相似地,可以用源电极和栅电极分别代替半导体元件的电极35和36。可以用源电极导线和栅电极导线分别代替导线39和40。(3)结论根据第三实施例,除了将经由导线或带键合到管芯结合区域33的区域12和14之外,Zn镀敷至少应用到将要用密封树脂41密封的引线框架21的区域。通过加热处理,从Zn和引线框架21的金属形成粗糙化的Zn合金层32b、32c和32d。结果,可以改进在密封树脂41的模制之后的引线框架21b与密封树脂41之间的界面结合强度。简而言之,第三实施例可以产生与第一实施例和第二实施例相似的优点。除了第二实施例的步骤之外,第三实施例还包括步骤S32、步骤S34和步骤SB。然而,在第三实施例中,用密封树脂41覆盖的管芯焊盘引线端子11、主电极引线端子13和控制电极引线端子15已经经历用Zn进行的粗糙化处理,从而与第二实施例的半导体器件相比,第三实施例的半导体器件具有改进的引线框架21b与密封树脂41之间的界面结合强度。<第四实施例>图21示出根据第四实施例的半导体器件制造方法,其包括制造步骤的平面视图和横截面视图。在图21的(A)至(F)中,左侧示出平面视图,右侧示出横截面视图。每个视图对应于一个半导体器件。在第四实施例中,与第三实施例相似,使用抗镀剂来进行Zn扩散合金化处理。然而,第四实施例中的抗镀剂的形成位置与第三实施例不同。与第三实施例的另一不同在于:密封树脂固定槽16位于管芯焊盘9与基台10之间。除了以上点之外,它们是相似的。如图21(B)所示,分别用抗镀剂43d和43e覆盖管芯焊盘引线端子11、主电极引线端子13、控制电极引线端子15和框体19中的每个的表面和背表面。此外,用抗镀剂43f覆盖管芯焊盘9的背表面。如图21(C)所示,对引线框架21d进行脱脂和酸液浸洗。然后,进行Zn电镀以在未用抗镀剂43a、43b、43c、43d、43e和43f覆盖的区域中有选择地形成Zn镀敷膜44。在以下条件下进行镀敷:3A/dm2的电流密度,200s的镀敷时间。如图21(D)所示,在移除抗镀剂43a、43b、43c、43d、43e和43f之后,进行Zn扩散合金化处理。形成粗糙化的Zn合金层32a、32b、32c和32d以制备引线框架21e。在以下条件下进行Zn扩散合金化处理:在H2气体气氛中,在400°C的加热温度,并且2分钟的加热时间。半导体器件的制造步骤与第三实施例相似。如图21(D)、(E)和(F)所示,在第四实施例中,没有粗糙化Zn合金层32形成在从密封树脂41暴露的管芯焊盘引线端子11、主电极引线端子13和控制电极引线端子15中的每一个上,这与第三实施例不同。第四实施例可以产生与第一实施例至第三实施例产生的优点相似的优点。在第四实施例中,可以获得与第一实施例至第三实施例中所获得的优点相似的优点。在第四实施例中,形成抗镀剂的区域的数量大于第三实施例。然而,在第四实施例中,在金属引线暴露部分上不形成粗糙化Zn合金层,因此,步骤S3B不是必需的,使得与第三实施例相比可以减少步骤数量。<第五实施例>图22是示出根据第五实施例的半导体器件制造方法的步骤流程图。图23A、23B和23C包括用于根据第五实施例的半导体器件制造方法的引线框架的平面视图(图23A)以及通过该制造方法所制造的半导体器件的平面视图(图23B)和横截面视图(图23C)。图23B是已经移除上部分密封树脂的平面视图,图23C是沿着图23B的线A-A'取得的横截面视图。第五实施例与第二实施例至第四实施例的不同之处在于:在半导体元件结合到引线框架的预定位置之后,进行Zn镀敷和Zn扩散合金化处理。如图22所示,准备引线框架21f和半导体元件34(步骤S51和S52)。作为半导体元件34,使用与第二实施例中采用的半导体芯片相似的半导体芯片。半导体元件34的背电极37用管芯结合材料38a管芯结合到引线框架21f的管芯焊盘9上(步骤S53)。作为管芯结合材料38a,例如,使用Ag烧结物膏剂。半导体元件34的主电极35和主电极键合焊盘12以及控制电极36和控制电极键合焊盘14分别经由Al导线(或Al带)39和40被耦合(步骤S54)。在对引线框架21f进行脱脂之后,Al表面经历Zn置换镀敷处理(锌酸盐处理)(步骤S55),然后引线框架21f的金属表面经历Zn电镀处理(步骤S56)。在以下条件下进行该镀敷:3A/dm2的电流密度,200s的镀敷时间。然后,进行Zn扩散合金化处理(步骤S57)。在以下条件下进行该处理:在H2气体气氛中,在400°C的加热温度,以及2分钟的加热时间。然后,用树脂来密封半导体元件34、导线39和40、主电极键合焊盘12、控制电极键合焊盘14等(步骤S58)。在使用例如热固化环氧树脂的同时使用传递模制来进行密封。环氧树脂含有填料。然后,通过碱性清洁来移除金属引线暴露部分的Zn(步骤S59),接着是金属引线暴露部分上的焊料镀敷(步骤S5A)。引线框架的框体19等被切割为期望的形状(步骤S5B)以完成半导体器件45b(步骤S5C)。如图23B和23C所示,管芯焊盘9、管芯焊盘引线端子11、主电极引线端子13和控制电极引线端子15在其表面上具有粗糙化Zn合金层32b、32c和32d,从而它们具有改进的与密封树脂41的粘合。此外,主电极35、控制电极36、主电极键合导线39和控制电极键合导线40在其表面上具有粗糙化Zn合金层32e和32f,从而它们具有改进的与密封树脂41的粘合。第五实施例也可以产生与第一实施例至第四实施例中描述的优异相似的优点。第五实施例需要锌酸盐处理,但在第五实施例中,管芯结合和导线键合后跟随着Zn扩散合金化处理,从而不需要在第二实施例中使用的引线框架的掩模化。因此,与第四实施例相比,在第五实施例中可以减少步骤的数量。<第六实施例>图24是示出根据第六实施例的半导体器件制造方法的步骤流程图。图25A、25B、25C和25D示出将要在第六实施例中使用的引线框架以及使用半导体器件制造方法所制造的半导体器件。图25A是引线框架的平面视图,图25B是处理了的引线框架的平面视图,图25C是已经移除密封树脂的上部分的平面视图,图25D是沿图25C的线a-a'取得的横截面视图。在第六实施例中,与第五实施例相似,半导体元件结合到引线框架的预定位置,接着是Zn镀敷和Zn扩散合金化处理。如图25A所示,准备处理为预定形状并且具有外部端子的引线框架21f(步骤S61)。如图25B所示,在引线框架21f的管芯结合区域33、主电极管芯键合区域12和控制电极管芯键合区域14上形成Ag镀敷(步骤S62)。这意味着在引线框架21f上形成管芯键合Ag镀敷焊盘46、主电极Ag镀敷焊盘47和控制电极Ag镀敷焊盘48。主电极Ag镀敷焊盘47也称为第一镀敷焊盘;控制电极Ag镀敷焊盘48也称为第二镀敷焊盘,管芯键合Ag镀敷焊盘46也称为第三镀敷焊盘。结果,准备了将要在制造步骤中使用的引线框架21g(步骤S63)。如图24所示,准备引线框架21g和半导体元件34a(步骤S63和S64)。半导体元件34a与半导体元件34的不同之处仅在于电极35和36的位置。半导体元件34a的背电极37通过结合材料52管芯结合到引线框架21g的管芯焊盘9上(步骤S65)。例如Ag烧结物膏剂可以用作结合材料52。半导体元件34a的主电极35和主电极Ag镀敷焊盘47以及控制电极36和控制电极Ag镀敷焊盘48分别经由主电极耦合引线49和控制电极耦合引线51彼此耦合(步骤S66)。作为主电极耦合引线49和控制电极耦合引线51,例如使用镀Ag的Cu引线。主电极35和主电极耦合引线49以及主电极Ag镀敷焊盘47和主电极耦合引线49用结合材料52耦合。对于控制电极36与控制电极耦合引线之间的耦合以及控制电极Ag镀敷焊盘48与控制电极耦合引线之间的耦合,使用结合材料52。主电极耦合引线49也可以称为第一耦合引线,控制电极耦合引线也可以称为第二耦合引线。在对引线框架21g进行脱脂之后,Al表面经历Zn置换镀敷处理(锌酸盐处理)(步骤S67),引线框架21g的金属表面经历Zn电镀处理(步骤S68)。在以下条件下进行该镀敷:3A/dm2的电流密度,200s的镀敷时间。然后,进行Zn扩散合金化处理(步骤S69)。在以下条件下进行该处理:在H2气体气氛中,在400°C的加热温度,以及2分钟的加热时间。然后,以树脂来密封半导体元件34a、主电极耦合引线49、控制电极耦合引线51等(步骤S6A)。使用例如热固化环氧树脂通过传递模制来进行密封。环氧树脂含有填料。通过碱性清洁从金属引线暴露部分移除Zn(步骤S6B)。然后,焊料镀敷应用于金属引线暴露部分(步骤S6C)。然后,引线框架的框体19等背切割为期望的形状(步骤S6D),完成半导体器件45b(步骤S6E)。如图25C和图25D所示,管芯焊盘9和管芯焊盘引线端子11在其表面上分别具有粗糙化Zn合金层32b和32c。主电极35和控制电极36在其表面上分别具有粗糙化Zn合金层32e。主电极引线端子13和控制电极引线端子15以及主电极耦合引线49和控制电极耦合引线51在其表面上分别具有粗糙化Zn合金层32h和32i。这些构件因此具有改进的与密封树脂4的粘合。此外,由于用粗糙化Zn合金层32h来覆盖控制电极耦合引线51,因此其并未被直接示出。在第六实施例中,可以获得与第五实施例相似的优点。<第七实施例>图26A和26B包括根据第七实施例的半导体器件的平面视图和横截面视图。图26A是已经移除上部分密封树脂的半导体器件的平面视图,图26B是沿图26A的线a-a'取得的横截面视图。第七实施例的半导体器件与使用根据第二实施例至第六实施例的半导体器件制造方法所制造的半导体器件的不同之处在于:甚至以密封树脂来密封未安装半导体元件的引线框架的表面。除此之外,例如通过与根据第一实施例至第四实施例的半导体器件制造方法相似的方法来制造第七实施例的半导体器件。通过将半导体元件54通过管芯结合而固定到引线框架的接片55上且然后以密封树脂41进行密封来获得根据第七实施例的半导体器件53。例如使用热固化环氧树脂通过传递模制来进行该密封。环氧树脂含有填料。半导体元件54是例如微型计算机的信号处理LSI(大规模集成电路)、ASIC等。作为管芯结合材料56,例如使用Ag膏剂(例如树脂Ag膏剂或Ag烧结物膏剂)。接片与第二实施例至第六实施例的管芯焊盘9对应。除了半导体元件54将要固定到的接片55的部分之外,粗糙化Zn合金层32还形成在接片55的表面、背表面和侧表面上。此外,还在除了键合导线57耦合到的区域之外的用密封树脂41覆盖的引线58的区域中形成粗糙化Zn合金层32。在图26中,未示出引线上表面上的粗糙化Zn合金层32,但是当键合导线57耦合到的区域远离密封树脂41的边缘时,还在引线58的上表面上形成粗糙化Zn合金层32。图26示出其引线58在四个方向上从密封树脂41延伸的QFP(方形扁平式封装)。可以使用引线在两个方向上或在一个方向上延伸的QFP。引线在两个方向上延伸的QFP的示例包括SOP(小外形封装)。例如,当半导体元件54是小信号晶体管时,优选使用引线仅在两个方向上或在一个方向上延伸的QFP。当以一个密封树脂41来密封多个小信号晶体管时,引线仅在两个方向上延伸的QFP是优选的。根据第七实施例的半导体器件可以产生与第一实施例至第六实施例的半导体器件相似的优点。由于接片55的背表面与密封树脂41接触,因此与密封树脂的接触面积增加,这改进了密封树脂41与引线框架之间的粘合。此外还在接片55的背表面上形成粗糙化Zn合金层32,这进一步改进了密封树脂41与引线框架之间的粘合。<结论>第一实施例至第七实施例中所使用的引线框架表面的金属化规范、管芯结合材料以及耦合材料根据半导体器件的类型而列于图27中。图27所示的器件、管芯结合材料、LF表面、管芯焊盘、耦合材料和键合焊盘的组合是优选示例。表中所使用的术语“器件”表示半导体器件,其也称为“半导体元件”。术语“TRS”表示晶体管。表中所使用的术语“耦合材料”表示将半导体元件的电极电耦合到引线框架的外部耦合端子的导体。表中所使用的术语“管芯焊盘”表示半导体元件将要耦合到的地方。管芯焊盘也称为“接片”。术语“键合焊盘”表示耦合材料将要耦合到的地方。表中所使用的术语“管芯结合材料”表示用于将半导体元件耦合到管芯焊盘的管芯结合材料。表中所使用的术语“LF表面”表示引线框架的表面。LF表面的列中所列出的Ni、Pd/Au和Ag分别是LF表面上的金属化层。术语“Cu”表示引线框架材料自身。引线框架的材料是Cu或Cu合金。管芯焊盘和键合焊盘的列中所列出的Ni、Pd/Au和Ag也是LF表面上的金属化层,Cu是引线框架材料自身。当管芯焊盘和键合焊盘的材料与LF表面上的材料不同时,通过引线框架的管芯焊盘和键合焊盘区域的镀敷等来形成管芯焊盘和键合焊盘的材料。当耦合材料是导线或带时,半导体元件的电极优选地是Al电极。当是镀Ag的Cu引线时,电极优选地是Ni/Au金属化电极。如图27所示,作为半导体元件,例如使用功率晶体管、小信号晶体管或信号处理LSI。功率晶体管使用以Cu或Cu合金制成的引线框架以及通过以Ni对Cu或Cu合金的表面进行金属化所获得的引线框架。小信号晶体管和信号处理LSI使用以Cu或Cu合金制成的引线框架以及通过以Pd/Au、Ag或Ni对Cu或Cu合金的表面进行金属化所获得的引线框架。从该表显见,本发明可以应用于根据以上实施例的各种金属化规范的引线框架,此外,可以应用于各种半导体器件。迄今已经基于实施例具体地描述了发明人进行的本发明。然而,应理解,本发明不限于这些实施例,而是可以在不脱离本发明的主旨的情况下进行修改。例如,在上述实施例中对功率晶体管、小信号晶体管和信号处理LSI进行了描述,但本发明不仅可以用于它们,而且还可以用于树脂密封型二极管、树脂密封型IC以及其它LSI。此外,本发明可以用于所谓的单侧模制型半导体器件,即具有背表面暴露的管芯焊盘或接片的器件。