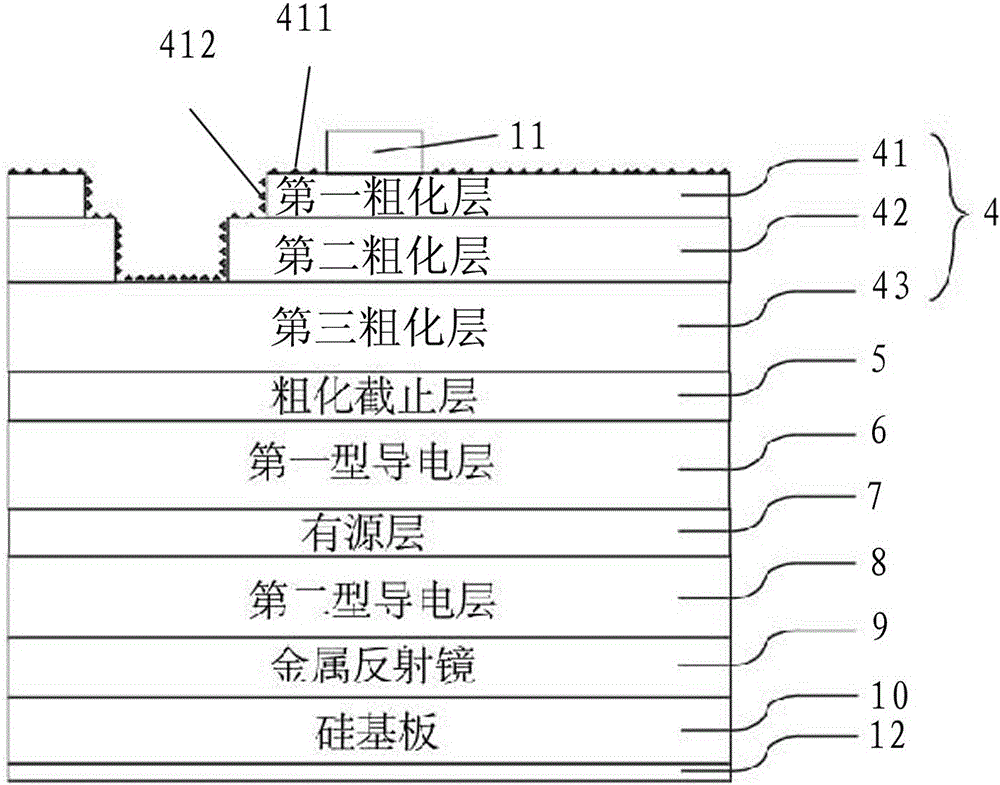
本发明涉及红外发光二极管技术领域,尤其是指一种具有多粗化层的红外发光二极管的粗化方法。
背景技术:红外发光二极管由于功耗低、尺寸小和可靠性高等优点,广泛应用于通信、遥感装置等领域。现有技术中,采用金属有机化合物气相外延生长具有量子阱的外延结构能取得较高的内量子效率。但是,由于存在外延材料与空气的折射率差较大,容易导致有源层在出光界面上出现全反射,因此,通常对出光界面表面进行粗化,表面粗化技术改善了发光二极管的光萃取率,明显地提升红外发光二极管的外量子效率。公开号为CN101409321A公开一种具界面粗化的发光二极管及其制作方法,提供一种在发光结构上还通过曝光、显影及湿法蚀刻的方式,蚀刻出发光区,具有粗化界面。所述粗化界面可以增加出光面积,提高发光效率。然而,所述粗化界面的缺陷在于:粗化界面基于单层、简单的粗化外延层,外延层粗化后表面呈简单的粗化形貌,其粗化效果不理想。
技术实现要素:本发明的目的在于提供一种具有多粗化层的红外发光二极管粗化方法,以增加二极管表面出光面积,提高红外发光二极管的外量子效率。为达成上述目的,本发明的解决方案为:一种具有多粗化层的红外发光二极管的粗化方法,包括以下步骤:步骤一,在基板上形成发光结构,在发光结构上形成N层粗化层,N≧3;步骤二,采用具有元素监测的干法蚀刻ICP在最外层粗化层表面形成粗化界面,蚀刻深度至与其相邻的第二粗化层接触表面;步骤三,采用粗化液蚀刻最外层粗化层及其相邻的第二粗化层露出的部分表面及侧面,形成粗化界面;步骤四,接着ICP刻蚀的掩膜,采用ICP在露出的第二粗化层的表面形成面积较最外层粗化层小的粗化界面,蚀刻深度至与第二粗化层相邻的第三粗化层接触表面;步骤五,采用粗化液蚀刻第二粗化层及与第二粗化层相邻的第三粗化层露出的部分表面及侧面,形成粗化界面;步骤六,重复操作步骤四及步骤五,直至露出N层粗化层表面,并形成粗化界面。进一步,步骤一中,在外延衬底上面自下而上依次形成腐蚀截止层、粗化层、粗化截止层、第一型导电层、有源层、第二型导电层;在第二型导电层上蒸镀金属反射镜;将金属反射镜的表面键合在具有导电性的基板上;去除外延衬底,湿法腐蚀去除腐蚀截止层,露出粗化层中的最外层粗化层;在最外层粗化层表面形成第一电极,且在第一电极上形成保护层;在基板背面蒸镀第二电极,去除第一电极的保护层,裂片后即得到具有多层粗化层的红外发光二极管。进一步,不同粗化层表面的粗化界面为在平面内规则排列的方形结构或圆形结构。进一步,步骤六中,所述N层粗化层表面及侧面形成粗化界面,且最终在不同的粗化层呈台阶下降式展露出粗化表面及侧面。进一步,步骤一中,在粗化层上形成第一电极,在基板的另一面形成第二电极。进一步,粗化截止层的材料包括AlGaInP三五族化合物。进一步,所述N层粗化层由不同外延材料构成,包括AlxGa1-xAs材料,0.85≥x≥0.15。进一步,N层不同材料的粗化层的Al组分含量呈阶梯式递增,且接近发光结构的Al组分含量较高。进一步,N层粗化层的厚度d为1.5≤d≤4μm;每一层粗化层的单层厚度ds≥300nm。进一步,所述N层粗化层的厚度呈阶梯式递增,且接近发光结构的厚度较大。一种具有多粗化层的红外发光二极管,在基板上形成发光结构,在发光结构上形成N层粗化层,N≧3;不同粗化层的表面及侧面形成粗化界面。进一步,在粗化层上形成第一电极,在基板的另一面形成第二电极。进一步,在粗化层与发光结构之间还形成粗化截止层。进一步,粗化截止层的材料AlGaInP三五族化合物。进一步,所述N层粗化层由不同外延材料构成,AlxGa1-xAs材料,0.85≥x≥0.15。进一步,N层不同材料的粗化层的Al组分含量呈阶梯式递增,且接近发光结构的Al组分含量较高。进一步,N层粗化层的厚度d为1.5≤d≤4μm。进一步,所述N层粗化层的厚度呈阶梯式递增,且接近发光结构的厚度较大。进一步,每一层粗化层的单层厚度ds≥300nm。采用上述方案后,采用上述方法形成的具有多粗化层的红外发光二极管,在基板上形成发光结构,在发光结构上形成N层粗化层,N≧3,不同粗化层的表面及侧面形成粗化界面,减少有源层在出光界面上出现全反射,增加发光二极管表面出光面积,提高红外发光二极管的外量子效率。同时,不同粗化层的外延材料不断改变,且不同材料层厚度不同,通过干法蚀刻形成规则图形,再通过湿法蚀刻对不同材料层的表面形成粗化界面,不同粗化层侧面形成粗化界面,进一步明显增加红外发光二极管的表面出光面积,提高红外发光二极管的外量子效率。附图说明图1为本发明实施例一外延结构示意图;图2为本发明实施例一粗化层粗化示意图;图3为本发明实施例一粗化后表面示意图;图4为本发明实施例二的外延结构示意图;图5为本发明实施例二粗化层粗化示意图;图6为本发明实施例二粗化后表面示意图。标号说明外延衬底1缓冲层2腐蚀截止层3粗化层4第一粗化层41粗化界面(411、412)第二粗化层42第三粗化层43第四粗化层44第五粗化层45粗化截止层5第一型导电层6有源层7第二型导电层8金属反射镜9硅基板10第一电极11第二电极12。具体实施方式以下结合附图及具体实施例对本发明做详细描述。实施例一参阅图1至图3所示,本发明揭示的一种具有多粗化层的红外发光二极管实施例一,图1为近红外发光二极管的外延结构,包括外延衬底1的上表面由下自上依次形成缓冲层2、腐蚀截止层3、粗化层4、粗化截止层5、第一型导电层6、有源层7、第二型导电层8,外延衬底1为GaAs衬底。粗化层4由第一粗化层41、第二粗化层42、第三粗化层43构成,第一粗化层41为远离有源层7的最外层粗化层。粗化层4的组成材料为AlGaAs,具体为:第一粗化层41为Al0.3Ga0.7As材料,且第一粗化层41的厚度为300nm;第二粗化层42为Al0.5Ga0.5As材料,且第二粗化层42的厚度为500nm;第三粗化层43为Al0.7Ga0.3As材料,且第三粗化层43的厚度为700nm。粗化截止层5由(Al0.05Ga0.95)0.5In0.5P材料组成。如图2所示,一种具有多粗化层的红外发光二极管的粗化工艺过程,包括以下步骤:步骤一,在外延衬底1上表面自下而上形成缓冲层2、腐蚀截止层3、粗化层4、粗化截止层5、第一型导电层6、有源层7、第二型导电层8。步骤二,在第二型导电层8上蒸镀金属反射镜9。步骤三,将金属反射镜9的表面键合在具有导电性的硅基板10的表面。步骤四,去除外延衬底1及缓冲层2,湿法腐蚀去除腐蚀截止层3,露出粗化层4中的第一粗化层41。步骤五,在第一粗化层41表面形成第一电极11,且在第一电极11上形成保护层。步骤六,采用具有元素监测的干法蚀刻ICP在粗化层4表面的第一粗化层41形成在平面内规则排列的方形结构(粗化界面),蚀刻深度至第二粗化层42接触表面。步骤七,采用粗化液蚀刻第一粗化层41及第二粗化层42露出的部分表面及侧面,形成表面粗化形貌(粗化界面)。步骤八,接着ICP刻蚀的掩膜,然后采用ICP在露出的第二粗化层42的表面形成面积较第一粗化层41的方形结构面积小的方形结构(粗化界面),蚀刻深度至第三粗化层43接触表面。步骤九,采用粗化液蚀刻第二粗化层42及第三粗化层43露出的部分表面及侧面,形成表面粗化形貌(粗化界面)。步骤十,去除所有的ICP刻蚀的掩膜,最终在不同的粗化层呈台阶下降展露出粗化部分表面及侧面,如图3所示。步骤十一,在硅基板10背面蒸镀第二电极12,去除第一电极11的保护层,裂片后得到具有多粗化层的红外发光二极管。所述方法形成的红外发光二极管结构为:在硅基板10上依次形成金属反射镜9、第二型导电层8、有源层7及第一型导电层6,所述金属反射镜9、第二型导电层8、有源层7及第一型导电层6形成发光结构,在第一型导电层6上形成粗化截止层5,在粗化截止层5上形成三层粗化层4,分别为第三粗化层43、第二粗化层42、第一粗化层41,在第一粗化层41上形成第一电极11,在硅基板1的另一面上形成第二电极12。不同粗化层第一粗化层41、第二粗化层42、第三粗化层43的表面及侧面形成粗化界面。如图2所示,第一粗化层41的表面形成粗化界面411,第一粗化层41的侧面形成粗化界面412。实施例二参阅图4至图6所示,本发明揭示的一种具有多粗化层的红外发光二极管实施例二,图4为近红外发光二极管的外延结构,包括包括外延衬底1的上表面由下自上依次形成缓冲层2、腐蚀截止层3、粗化层4、粗化截止层5、第一型导电层6、有源层7、第二型导电层8,外延衬底1为GaAs衬底。粗化层4由第一粗化层41、第二粗化层42、第三粗化层43、第四粗化层44、第五粗化层45构成,第一粗化层41为远离有源层7的最外层粗化层。粗化层4的组成材料为AlGaAs,其中,第一粗化层41的材料为Al0.2Ga0.8As,且第一粗化层41的厚度为400nm;第二粗化层42的材料为Al0.35Ga0.65As,且第二粗化层42的厚度为500nm;第三粗化层43的材料为Al0.5Ga0.5As,且第三粗化层43的厚度为600nm;第四粗化层44的材料为Al0.65Ga0.35As,且第四粗化层44的厚度为700nm;第五粗化层45的材料为Al0.8Ga0.2As,且第五粗化层45的厚度为800nm。粗化截止层5由Ga0.5In0.5P材料组成。图5所示,一种具有多粗化层的红外发光二极管的粗化工艺过程,包括以下步骤:步骤一,在外延衬底1上表面自下而上依次为缓冲层2、腐蚀截止层3、粗化层4、粗化截止层5、第一型导电层6、有源层7、第二型导电层8。步骤二,在第二型导电层8上蒸镀金属反射镜9。步骤三,将金属反射镜9的表面键合在具有导电性的硅基板10的表面。步骤四、去除外延衬底1及缓冲层2,湿法腐蚀去除腐蚀截止层3,露出粗化层4中的第一粗化层41。步骤五,在第一粗化层41表面形成第一电极11,且在第一电极11上形成保护层。步骤六,采用具有元素监测的干法蚀刻ICP在粗化层4表面的第一粗化层41形成在平面内规则排列的圆形结构(粗化界面),蚀刻深度至第二粗化层42接触表面。步骤七,采用粗化液蚀刻第一粗化层41及第二粗化层42露出的部分表面及侧面,形成表面粗化形貌(粗化界面)。步骤八,接着ICP刻蚀的掩膜,然后采用ICP在露出的第二粗化层42的表面形成面积较第一粗化层41的圆形结构面积小的圆形结构(粗化界面),蚀刻深度至第三粗化层43接触表面。步骤九,采用粗化液蚀刻第二粗化层42及第三粗化层43露出的部分表面及侧面,形成表面粗化形貌(粗化界面)。步骤十,依步骤八及步骤九的制作规律蚀刻去除部分粗化层区域及表面粗化裸露的粗化层,直至露出第五粗化层45及并对其表面粗化。去除所有的ICP刻蚀的掩膜,最终在不同的粗化层呈台阶下降展露出粗化部分表面及侧面,如图6所示。步骤十一,在硅基板10背面蒸镀第二电极12,去除第一电极11的保护层,裂片后得到具有多粗化层的红外发光二极管。所述方法形成的红外发光二极管结构为:在硅基板10上依次形成金属反射镜9、第二型导电层8、有源层7及第一型导电层6,所述金属反射镜9、第二型导电层8、有源层7及第一型导电层6形成发光结构,在第一型导电层6上形成粗化截止层5,在粗化截止层5上形成五层粗化层4,分别为第五粗化层45、第四粗化层44、第三粗化层43、第二粗化层42及第一粗化层41,在第一粗化层41上形成第一电极11,在硅基板1的另一面上形成第二电极12。不同粗化层第一粗化层41、第二粗化层42、第三粗化层43、第四粗化层44及第五粗化层45的表面及侧面形成粗化界面。如图5所示,第一粗化层41的表面形成粗化界面411,第一粗化层41的侧面形成粗化界面412。以上所述仅为本发明的较佳实施例,并非对本案设计的限制,凡依本案的设计关键所做的等同变化,均落入本案的保护范围。