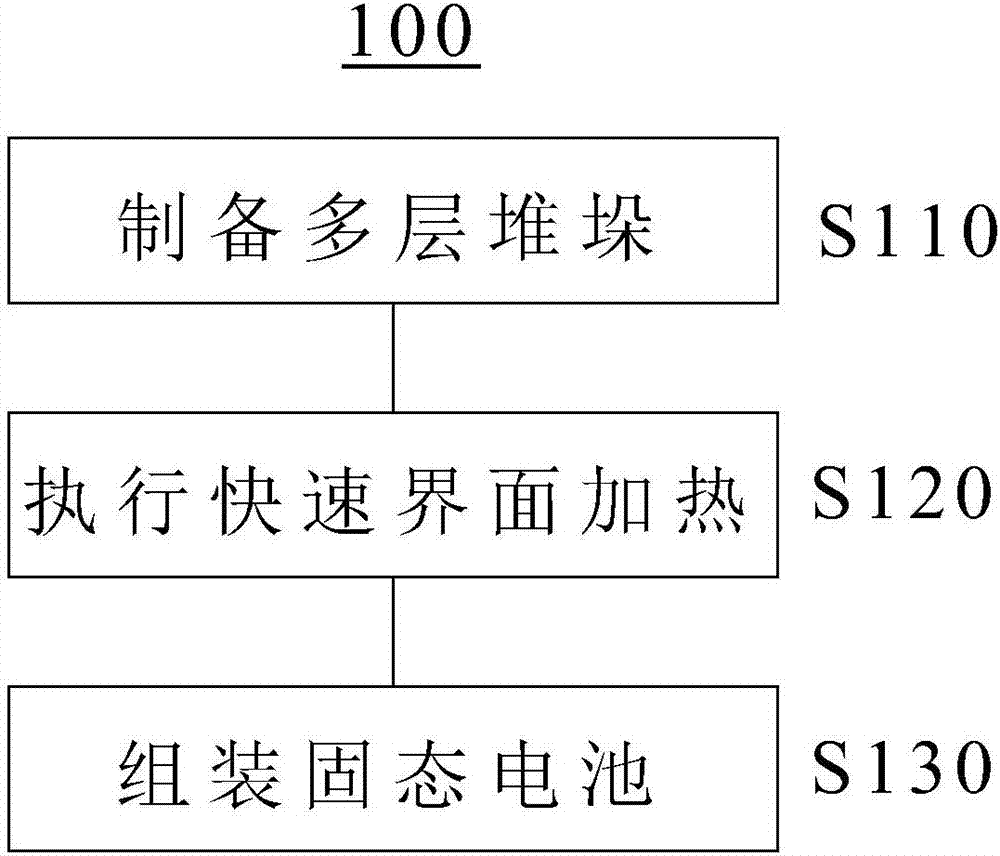
本发明总体上涉及新能源领域,更特别地,涉及一种简易、快速、可大规模制备固态电池的方法、以及通过该方法制备的固态电池。
背景技术:
:近年来,快速发展的电动汽车和储能行业对以锂离子电池、铅酸电池为代表的二次电池的能量密度、成本、循环特性和安全特性提出了更高的要求。以锂离子电池为例,常规的锂离子电池主要采用石墨负极,石墨负极的理论容量为372mah/g,目前国内主要的石墨负极生产商,例如江西紫宸、深圳贝特瑞等已经实现了365mah/g的容量,接近于理论容量的极限。为了实现更高的能量密度和功率密度,人们开始关注能够满足对全新电池更高要求的新型负极材料,例如金属锂负极,然而目前锂电池的电解质多为易燃液体,因此如果该电池受到损坏,可能带来危险。科研人员希望替换液体电解质采用固态电解质,从而制备出更加安全可靠的固态电池。目前使用或研究中的固态电解质主要为氧化物固态电解质、硫化物电解质、聚合物电解质、以及它们的复合类型。基于氧化物的固态电池公司例如有sakti3等,一般采用磁控溅射的方法在金属锂表面溅射沉积lipon电解质和钴酸锂正极材料,但这种方法的制作成本高,lco的厚度薄,电池的能量密度低。基于硫化物电解质发展的固态电池公司例如有丰田、三星、日立造船和日本富士等,一般采用加压技术制备固态电池,但这种技术条件要求高、制作成本大。基于聚合物的固态电池质量轻、粘性好、易成膜、化学稳定性好、能很好地抑制锂枝晶体的生长,然而,电化学窗口小于3.8v,因此不能采用高电压正极,从而使得电池系统能量密度低,例如seeo的聚合电池能量密度仅为100wh/kg。此外,与液态电解质相比,固体电解质不具备界面浸润和流动性,这导致固态电池和液态电池相比制备较为困难。为了解决界面的问题,研究人员尝试了烧结工艺来解决固体电解质与固体电解质之间以及固体电解质与正极材料之间的界面接触,然而烧结时间较长容易造成正极和电解质之间较大的界面电阻。因此,需要对固态电池进行持续不断地深入研究,以克服现有技术中存在的上述问题。技术实现要素:为了解决上述问题,本申请提出一种制备固态电池的方法,其能够改善固态电池中的颗粒之间的接触界面属性,有利于锂离子的输运,从而提高固态电池的性能和安全性。这种方法可以简易、快速地执行,能用于大规模制备固态电池。根据一示例性实施例,一种制备固态电池的方法可包括:制备堆垛结构,所述堆垛结构至少包括正极层和设置在所述正极层上的固体电解质层,所述正极层包括正极活性材料颗粒和固体电解质颗粒;对所述堆垛结构进行快速界面加热,以使得所述正极层中的正极活性材料颗粒和固体电解质颗粒中的至少一种在界面处发生熔化,以生成界面融合相,从而直接连接所述正极活性材料颗粒和所述固体电解质颗粒。在一些示例中,所述快速界面加热包括微波加热、高周波加热、机械波加热、振动摩擦加热、声波加热、超声波加热、次声波加热、电磁场感应电流加热中的一种或多种。高周波加热和电磁感应加热的频率大于20khz,机械波加热、振动摩擦加热、声波加热、超声波加热和次声波加热的频率范围为20hz至1ghz,微波加热的频率范围为300mhz至300ghz。波的形式可以正弦波、余弦波、方波、横波、纵波、以及它们的任意组合。在一些示例中,所述快速界面加热的温度在300℃至1000℃的范围,优选地在400℃至800℃的范围。所述快速界面加热的时间在0.01-1500秒的范围,优选地在0.5-900秒的范围,更优选地在1-600秒的范围。在一些示例中,所述方法还包括:在执行所述快速界面加热之前,将所述堆垛结构预热至预定温度,所述预定温度在25℃至800℃的范围,优选地在100℃至500℃的范围。在一些示例中,所述方法还包括:在执行所述快速界面加热之后,对所述堆垛结构执行退火处理,退火温度在100℃至500℃的范围,优选地在200℃至400℃的范围,退火时间在0.5分钟至120分钟的范围,优选地在1分钟至60分钟的范围。在一些示例中,所述堆垛结构还包括设置在所述固体电解质层上的负极层,所述负极层包括负极活性材料颗粒。在一些示例中,所述负极层还包括固体电解质颗粒,所述快速界面加热使得所述负极层中的负极活性材料颗粒和固体电解质颗粒中的至少一种在界面处发生熔化,以生成界面融合相,从而直接连接所述负极活性材料颗粒和所述固体电解质颗粒。在一些示例中,所述方法还包括:在所述快速界面加热步骤之后,在所述固体电解质层上依次设置聚合物固体电解质层和负极层,或者直接设置负极层。在一些示例中,所述快速界面加热步骤仅使所述正极层中的正极活性材料颗粒和固体电解质颗粒中的至少一种在界面处发生熔化以生成界面融合相,而不改变所述正极活性材料颗粒和所述固体电解质颗粒的内部结构。根据一示例性实施例,提供一种固态电池,其根据上述方法制备而成。在一些示例中,所述界面融合相是非晶相。在一些示例中,所述正极层中的正极活性材料颗粒和固体电解质颗粒中的所述至少一种的颗粒内部是结晶相。在一些示例中,所述固态电池是碱金属固态电池。本发明通过对堆垛结构进行快速界面加热处理,使得颗粒之间接触更好,更利于碱金属离子例如锂离子传输,同时也抑制了正极活性物质和电解质界面在加热过程中容易发生的相互扩散,生成电化学性能差的惰性层。与通过常规的长时间烧结方法来处理界面接触的方案相比,采用快速界面加热,界面过渡层薄,在0.1nm~100nm之间,界面组分多为熔化相的非晶相。当界面加热处理时间较长功率较大时,熔化相的产物会大面积连在一起,致密的大于90%;而非熔化相,则保持晶相;当界面加热处理时间较短及功率较小时,如果熔化相棱角分明,在熔化后棱角会消失,界面处熔化相变成一颗一颗的球形颗粒并连着一起。如果制备堆垛结构,采用粘结剂,快速界面加热后,堆垛结构中存在是界面融合和粘结剂粘结颗粒共存状态,若再次采用退火处理,堆垛结构粘结剂会存在分解产物。本发明的方法简单,成本低,能够用于固态电池的大规模制造。本发明的上述和其他特征和优点将从下面对示例性实施例的描述而变得显而易见。附图说明附图示意性示出了本发明的示例性实施例。应理解,附图不是按比例绘制的。图1示出根据本发明一示例性实施例的制造固态电池的方法的流程图图2a示出根据本发明一示例性实施例的多层堆垛结构的示意图。图2b示出根据本发明一示例性实施例的快速界面加热之后的多层堆垛结构的示意图。图3a示出根据本发明一示例性实施例的多个多层堆垛结构的示意图,其具有内部串联结构。图3b示出根据本发明另一示例性实施例的多个多层堆垛结构的示意图,其具有内部并联结构。图4示出利用固相烧结法850℃下烧结3h制备的正极/电解质片的sem照片。图5示出利用固相烧结法850℃下烧结5h制备的正极/电解质片的sem照片。图6示出根据本发明另一示例性实施例制备的正极/电解质片的sem照片。图7示出利用图6的正极/电解质片组装的电池的首周充放电曲线。图8示出根据本发明另一示例性实施例制备的正极/电解质片的sem照片。图9示出利用图8的正极/电解质片组装的电池的首周充放电曲线。具体实施方式下面将参照附图描述本发明的示例性实施例。应理解,附图不是按比例绘制的。针对现有固态电池的上述问题,本发明提出一种快速界面加热的方法,使全固态电池中的正极、负极以及固体电解质层中的颗粒的界面处的温度达到使界面熔化的程度,从而使固体电解质与正极颗粒之间、固体电解质与固体电解质颗粒之间、以及固体电解质与负极颗粒之间的界面发生局部融合,从而在原子尺度、纳米尺度或微米尺度,通过界面融化的相形成固体电解质颗粒与正、负极颗粒之间的直接连接,进而使得在全固态电池中,离子可以在正极、电解质、负极相之间传输,并且在全固态电池充放电过程中,界面连接相也不会因为正、负极颗粒体积变化而失去与正、负极颗粒的连接。在快速界面加热之后,界面融合的相可以是非晶相,也可以是结晶相,可以是来自全固态电池中的正极、负极、固体电解质的相,也可以是因为快速界面加热而产生的新相。由于快速界面加热的原因,正、负极颗粒内部保持了原来的晶体结构和微观结构,仅在界面处发生了融化和连接,而颗粒之间的互相扩散小,从而电池界面阻抗小,并且抑制了正极活性物质和电解质界面在加热过程中因互扩散而生成电化学性能差的惰性层。本发明的方法易于操作,适于规模化生产,具有很好的应用前景。图1示出根据本发明一示例性实施例的制备固态电池的方法100的流程图。如图1所示,制备固态电池的方法100始于步骤s110,制备多层结构的堆垛。图2a示出了多层堆垛结构的示例。如图2a所示,多层堆垛结构包括正极层10、电解质层20和负极层30。正极层10包括正极活性材料颗粒11,电解质层20包括电解质颗粒21,负极层30包括负极活性材料颗粒31。应注意,正极层10和负极层30每个中也包括有电解质颗粒21。换言之,正极层10包括正极活性材料颗粒11和电解质颗粒21的混合物,负极层30包括负极活性材料颗粒31和电解质颗粒21的混合物。在另一些实施例中,负极层30也可以不包括电解质颗粒21。虽然未示出,但是正极层10和负极层30每个还可以包括集流体层。制备该多层堆垛结构的步骤s110可包括制备正极混合材料、电解质材料和负极材料,制备方法可包括手动研磨、球磨、振动、翻滚混合等。正极混合材料中至少包括正极活性材料和电解质,还可以包括导电添加剂和粘结剂等。电解质材料中除了包括电解质之外,还可以包括粘结剂等。负极材料中至少包括负极活性材料,还可以包括电解质、粘结剂和导电添加剂等。可利用这些材料按照图2a所示的顺序形成堆垛结构,形成堆垛结构的方法有多种,例如喷涂、丝网印刷、转移涂布、挤压涂布、微凹版、静电纺丝、或者干粉多层混压等。这些方法都是现有技术中已经使用的,这里不再详细描述。在一些实施例中,正极层10可包括固体电解质、正极活性物质、粘结剂和导电添加剂,它们的质量比范围可以为例如20:80≤m正极活性物质:m固体电解质≤98:2;70:30≤m正极活性物质+固体电解质:m粘结剂≤100:0;82:20≤m正极活性物质+固体电解质:m导电添加剂≤100:0。可以按照现有的锂离子电池搅拌工艺,将正极混合材料制备成正极浆料。在一示例中,例如,正极混合材料中的物质质量比可以为正极活性物质:固态电解质:导电剂:粘结剂=68:28:2:2。将这些浆料采用转移涂覆的方式涂覆在正极集流体上,可采用单面涂覆或双面涂覆形成正极层,正极层厚度在2μm-500μm,优选厚度为10μm-200μm,正极集流体可以是材质可以是铝、不锈钢、镍、碳中的一种或多种,存在形式可以是箔、孔、条、网,厚度为1μm~25μm。在一些实施例中,负极层30可包括负极活性物质、固体电解质、粘结剂和导电添加剂,它们的质量比范围可以为例如40:60≤m负极活性物质:m固体电解质≤98:2;80:20≤m负极活性物质+固体电解质:m粘结剂≤100:0;80:20≤m负极活性物质+固体电解质:m导电添加剂≤100:0。按照现有锂离子电池搅拌工艺,将负极混合材料制备成负极浆料,其中负极混合材料中的物质质量比可以为负极活性物质:固态电解质:导电剂:粘结剂=66:30:2:2。将这些浆料采用挤压涂覆的方式涂覆在负极集流体上,可采用单面涂覆或双面涂覆形成负极层,负极层的厚度可以在2μm-500μm,优选厚度为10μm-120μm。负极集流体可以是材质可以是铜、不锈钢、镍、碳中的一种或多种。存在形式可以是箔、孔、条、网,厚度为1μm~25μm。在一些实施例中,固体电解质层20可以包括固体电解质和粘结剂,其中它们的质量比范围可以为例如80:20≤m固体电解质:m粘结剂≤100:0。同样,可以按照现有锂离子电池搅拌工艺,制备出电解质浆料,其中电解质层的物质质量比可以为例如电解质:粘结剂=97:3。可以将电解质浆料转移涂布或者微凹法涂覆在正极层或负极层的表面上,电解质层的厚度可以在1μm-100μm的范围,优选厚度为2μm-50μm。在另一些实施例中,也可以直接将正极层的粉体平铺到磨具中,轻轻加压;然后平铺电解质的粉体,轻轻加压;再最后平铺负极层的粉体,然后加压,以制备出三层结构的堆垛。在该方法中,粉体可含有粘结剂,也可以不含有粘结剂。在上面描述的各种材料中,正极活性物质可选自i2、s、o2、me(nixcoymnz)fo2g、me(feacobmncnid)f(po4)g、m2e(feacobmncnid)f(sio4)g、m2e(fe2aco2bmn2cni2d)f(so4)3g、me(feacobmncnid)f(bo3)g、m3ev2f(po4)3g、mecofo2g、fefs2g、mnfo2g、me(niacobalc)fo2、m2emnfo3g、me(nixcoymnz)fo2g、me(nipmnq)2fo4g中的一种或多种,其中m为碱金属例如li、na、k,x+y+z=1,且0≤x≤1,0≤y≤1,0≤z≤1,a+b+c+d=1,且0≤a≤1,0≤b≤1,0≤c≤1,0≤d≤1,0.5≤e≤1.5,0.5≤f≤1.5,0.5≤g≤1.5,p+q=2且0≤p≤2,0≤q≤2。在上面描述的各种材料中,负极活性物质可选自碳材料、硅材料、锡材料、碱金属单质、碱金属合金化合物max(1-a)中的一种或多种,其中碳材料包括石墨、硬碳、软碳及其衍生物,硅材料包括纳米硅、硅碳复合材料、氧化亚硅、氧化亚硅和碳复合材料,锡材料包括纳米锡、锡碳复合材料、氧化锡及其复合材料,碱金属可包括li、na、k,碱金属合金化合物max(1-a)中的m可选自li、na、k,x可选自sn、si、al、ge、sb、b、mg,0.1<a<1。在上面描述的各种材料中,固态电解质可包括mgs、cas、srs、bas、b2s3、al2s3、ga2s3、in2s3、sis2、ges2、sns2、ces2、nb2s5、sc2s3、y2s3、la2s3、tis2、zrs2、hfs2、zns、p2s5、as2s5、mgo、cao、sro、bao、b2o3、al2o3、ga2o3、in2o3、sio2、geo2、sno2、sc2o3、y2o3、la2o3、tio2、zro2、hfo2、nb2o5、zno、na2o、k2o、rb2o、cs2o、cuo、m3n、mf、mcl、mbr、mi中的一种或多种与m2s或者m2o形成的固溶体、复合物、非晶、非晶与晶态的复合物,其中m为碱金属li、na、k。例如,用于锂离子固态电池的固体电解质可以包括li1+palpge2-p(po4)3、li3qla2/3-qtio3、lizr2-rtir(po4)3、li1+malmti2-m(po4)3、li4-tge1-tpts4、li7-2n-janla3zr2-jbjo12和li7-2n-2janla3zr2-jcjo12,li7p3p11,li3ps4,其中,0≤p≤2,0≤q≤2/3,0≤r≤2,0≤m≤2,0≤t≤1,0≤n≤3,0≤j≤2,a为ge和/或al,b为nb和/或ta,c为te和/或w。例如,用于钠离子固态电池的固体电解质可以包括β-al2o3、na1+2x+yaxbyczp3o12,其中a=mg2+,b=al3+、cr3+、ga3+、b3+,c=ti4+、ge4+、si4+、zr4+等,0≤x≤1,0≤y≤1,1≤z≤2。例如,固体电解质也可以是用于钠离子固态电池的固体电解质,这里不再一一例举。一些实施例中,粘结剂可选自聚偏氯乙烯(pvdf)、聚偏氯乙烯-六氟丙烯(pvdf-hfp)、聚四氟乙烯(ptfe)、聚氧化乙烯、聚酯、聚醚、聚酰胺、聚甲基丙烯酸甲酯、聚碳酸酯、羧甲基纤维素、苯乙烯-丁二烯共聚物、聚丙烯腈中的一种或多种。在一些实施例中,导电添加剂可选自sp、乙炔黑、kb、碳纳米管、石墨烯、铝粉、铜粉、镍粉、镁粉、锌粉、金粉、银粉、锡粉及上述材料的合金中的一种或多种。导电添加剂的颗粒尺寸可以为例如5nm-1μm,优选为10nm-500nm。应理解的是,虽然图2a示出了正极层10和负极层30中的电解质颗粒与电解质层20中的电解质颗粒相同,但是它们也可以不同,并且正极层10中的电解质可以还可以与负极层30中的电解质颗粒(如果有的话)不同。在一些实施例中,其中正负极活性材料表面还可含有包覆层,以抑制颗粒表面互扩散。包覆层的厚度可以为例如0.5nm-500nm,包覆层材料可为氧化物,硫化物、以及聚合物中的一种或多种。通过上述步骤,制备了图2a所示的多层堆垛结构。接下来,在步骤s120中,可以执行快速界面加热过程。与现有技术中的烧结工艺不同,本发明的快速界面加热旨在实现颗粒界面之间的融合,尤其是正极活性材料颗粒11与电解质颗粒21之间的界面融合,但是应避免过度加热而导致的颗粒之间的互扩散,这种互扩散可能生成电化学性能差的惰性层,从而增大电池的界面阻抗,使电池的性能变差。因此,在快速界面加热步骤s120中,应注意控制加热的温度和时间,以使得上述堆垛结构中的正极层10、负极层30和固体电解质层20中的一种或多种的颗粒界面处的温度达到使界面熔化的程度,从而使固体电解质与正极颗粒之间、固体电解质与固体电解质颗粒之间、以及固体电解质与负极颗粒之间的界面发生局部融合,例如在固体电解质颗粒21与正极颗粒11之间产生界面融合相12,在固体电解质颗粒21与固体电解质颗粒21之间产生界面融合相22,以及在固体电解质颗粒21与负极颗粒31之间产生界面融合相32,如图2b所示的那样。这些界面融合相可以是非晶相,也可以是结晶相;可以是来自全固态电池中的正极、负极、固体电解质的相,也可以是因为快速界面加热而产生的新相。这样,可以在原子尺度、纳米尺度或微米尺度,通过界面融合相来形成固体电解质颗粒与正、负极颗粒之间的直接连接,进而使得在全固态电池中,离子可以在正极、电解质、负极之间传输,并且在全固态电池充放电过程中,界面连接相也不会因为正、负极颗粒体积变化而失去与正、负极颗粒的连接。由于颗粒间接触良好形成整体,电池整体将有更好的机械性能,同时将拥有更高的电导率。另一方面,由于快速界面加热的原因,正、负极颗粒内部保持了原来的晶体结构和微观结构,仅在界面处发生了融化和连接,而颗粒之间的互相扩散小,从而电池界面阻抗小,并且抑制了正极活性物质和电解质界面在加热过程中因互扩散而生成电化学性能差的惰性层。与通过常规的长时间烧结方法来处理界面接触的方案相比,采用快速界面加热,界面过渡层薄,在0.1nm~100nm之间,界面组分多为熔化相的非晶相。当界面加热处理时间较长功率较大时,熔化相的产物会大面积连在一起,致密的大于90%;而非熔化相,则保持晶相;当界面加热处理时间较短及功率较小时,如果熔化相棱角分明,在熔化后棱角会消失,界面处熔化相变成一颗一颗的球形颗粒并连着一起。如果制备堆垛结构,采用粘结剂,快速界面加热后,堆垛结构中存在是界面融合和粘结剂粘结颗粒共存状态,若再次采用退火处理,堆垛结构粘结剂会存在分解产物。可以通过各种手段来执行步骤s120的快速界面加热过程,包括但不限于微波加热、闪烧加热、高周波加热、机械波加热、声波加热、超声波加热、次声波加热、电磁场感应电流加热、以及它们的任意组合等等。作为一些示例,高周波加热和电磁感应加热的频率一般大于20khz,机械波加热、振动摩擦加热、声波加热、超声波加热和次声波加热的频率可以在20hz至1ghz的范围,微波加热的频率范围可以为300mhz至300ghz。波的形式可以正弦波、余弦波、方波、横波、纵波、以及它们的任意组合等。可以理解,采用不同的加热方式,对不同种类、厚度的堆垛层进行界面快速加热,都将影响加热处理的时间和功率。在处理不同厚度的堆垛层时,进行界面快速加热处理的时间也不同,对于越厚的堆垛层,界面快速加热融合的时间越长,加热功率也应该越大。但是应注意的是,不同于现有技术中的烧结工艺,本发明的快速界面加热的加热时间一般不应超过1800秒,以防止不同颗粒之间发生严重的相互扩散。在对不同的电解质材料和正负极的材料进行界面快速加热时也应该采用不同的时间和加热功率。对于熔点高的颗粒材料,加热的时间就越长,加热的功率就越大。虽然如上所述,快速界面加热的加热温度和时间因材料和堆垛厚度而异,但是一般而言,加热温度可在300℃至1000℃的范围,优选在400℃至800℃的范围,加热时间可以在0.01-1500秒的范围,优选在0.5-900秒的范围,更优选地在1-600秒的范围。与常规的烧结工艺相比,本发明的加热时间要短得多,而且加热效果主要集中在界面处,因此可称为“快速界面加热”。在一些实施例中,对于熔点非常高的材料,还可以在施加界面快速加热之前进行预加热处理,预加热温度必须应低于颗粒熔点,以抑制颗粒之间发生相互扩散。预先达到一定温度可以使材料更容易在快速界面加热时达到熔点温度,使界面融合更好。预先加热的温度可以从25℃至800℃,优选地从100℃至500℃。在执行快速界面加热时,还可以对堆垛结构进行加压,加压压强可以为例如10kpa至10000kpa,也可以在常压下加热。加热可以在空气中进行,必要时也可以在特定气氛中进行以防止不期望的化学反应。下面描述快速界面加热的一些具体实施方式。在一些实施例中,可以利用微波加热来执行快速界面加热步骤s120。在利用微波加热时,可以预先使堆垛结构处于300℃左右,然后执行微波加热。而且,在微波加热时,可对体系进行加压,压强10kpa~10000kpa;加热时间可以为0.01~1800s,优选为0.01~1000s。在另一些实施例中,可以利用高周波加热来执行快速界面加热步骤s120。在进行高周波加热时,可以预先使堆垛结构处于25℃,并且对体系进行加压,压强例如为800kpa,加热时间可以为50~200s,例如为100s。在另一些实施例中,可以利用机械波加热来执行快速界面加热步骤s120。机械波是通过颗粒摩擦产生热量来进行加热。在采用机械波加热时,可以预先将体系加热至300~500℃,例如预加热至455℃。机械波加热时可以对体系进行施压,压强例如为800kpa,加热时间可以为5~30s,例如10s、15s、20s等。在另一些实施例中,可以利用电磁感应加热来执行快速界面加热步骤s120。在采用电磁感应加热时,可以将体系预加热至300~500℃,例如预加热至455℃。机械波加热时可以对体系进行施压,压强例如为800kpa,加热时间可以为5~30s,例如10s、15s、20s等。当然,还可以通过其他方式来执行快速界面加热步骤s120,这里不再一一例举。通过上述快速界面加热步骤s120,得到了图2b所示的结果,其中例如在固体电解质颗粒21与正极颗粒11之间、在固体电解质颗粒21与固体电解质颗粒21之间、以及在固体电解质颗粒21与负极颗粒31之间分别产生了界面融合相12、22和32。本发明人实验发现,在经过快速界面加热融合之后,形成的界面融合相的碱金属离子电导有可能相对于颗粒体相材料变得更高或者更低。为了确保界面融合相的电导率足够高,还可以在快速界面加热融合后,对堆垛结构进行进一步的处理来增加融合相的电导率,从而提高电池性能。例如,在一些实施例中,可对快速界面加热之后的堆垛结果进行退火处理,退火温度可以在100℃至500℃的范围,优选在200℃至400℃的范围,退火时间可以在0.5分钟至120分钟的范围,优选1分钟至60分钟的范围。退火同样可以在空气或特殊气氛中进行,例如可以在氮气、氩气、氧气或它们的混合物的气氛中进行。然后,可以执行步骤s130,利用步骤s120处理后的堆垛结构来组装固态电池,例如将堆垛结构封装到电池壳体中,并且将正极集流体和负极集流体分别连接到固态电池的正负电极等。固态电池的封装工艺是本领域已知的,这里不再重复描述,以避免不必要地模糊本发明的要点。在上面参照图1、2a和2b描述的实施例中,堆叠结构包括正极层10、电解质层20和负极层30,即具有三层结构。在另一些实施例中,堆叠结构也可以只包括两层,即正极层10和电解质层20。此时,在执行组装步骤s130前,则还需要在电解质层20上设置负极层。此时,可以直接贴上负极层,也可以先在电解质层20的表面上设置聚合物电解质层,其厚度可以为例如0.5μm~50μm,优选1μm~20μm。然后,再将负极层设置在聚合物电解质层上。在这些实施例中,负极层中可以不包括电解质颗粒。可以理解,类似地,在上面参照图2a和2b描述的实施例中,负极层30也可以不包括电解质颗粒21。聚合物电解质可以为干聚合物电解质、溶胶聚合物电解质、多孔溶胶聚合物电解质、以及有机物复合电解质中的一种或多种。干聚合物电解质可以为醚类聚合电解质、碳酸酯类、聚硅氧烷基和碱金属盐的复合材料等。常用的碱金属盐包括锂盐,例如为六氟磷酸锂(lipf6)、四氟硼酸锂(libf4)、六氟砷酸锂(liasf6)、三氟甲基磺酸锂(cf3so3li)、高氯酸锂、硝酸锂、双(三氟甲基磺酰亚)胺锂(litfsi)、双氟磺酰亚胺锂(lifsi)、以及双草酸硼酸锂(libob)中的一种或多种。图3a和3b示出根据本发明另一些示例性实施例的多个多层堆垛结构的示意图,其中图3a中的多个堆垛结构形成内部串联结构,图3b中的多个堆垛结构形成内部并联结构。通过多个堆垛结构的串联或并联,可以提供更高的电压、更高的容量等。图3a和3b所示的结构可以通过将多个上面制备的堆垛结构串联或并联连接而成。替代地,也可以一开始就制备图3a和3b所示的结构,然后再执行上面描述的快速界面加热处理。内部串联电池中,相邻堆垛结构之间的正负极可以在制备堆垛层的时候就共用集流体,形成正极和负极相互串联连接的结构,也可以在制备完成单个堆垛结构之后通过集流体的正负极集耳之间相互连接形成串联结构。在内部并联电池中,通过堆垛结构之间集流体的集耳相互连接形成正极和正极、负极和负极间相互连接的并联结构,也可以在堆垛结构制备时就采用长条集流体,最后卷绕成电池。最后,可通过铝塑膜密封来做成固态电池。下面来描述根据本发明的一些实例以及比较例。在这些例子中,所用到的材料如下面的表格所示。表1电解质材料电解质组成电解质1li1+palpge2-p(po4)3电解质2li3qla2/3-qtio3电解质3lizr2-rtir(po4)3电解质4li1+malmti2-m(po4)3电解质5li7-2n-janla3zr2-jbjo12电解质6li7-2n-2janla3zr2-jcjo12电解质7li2o-b2o3电解质8lipon电解质9β-li3ps4电解质9li7p3s11电解质10β-al2o3电解质11na3zr2si2po12其中,0≤p≤2,0≤q≤2/3,0≤r≤2,0≤m≤2,0≤t≤1,0≤n≤3,0≤j≤2,a为ge和/或al,b为nb和/或ta,c为te和/或w。表2界面快速加热方式表3粘结剂编号组成粘结剂1聚偏氯乙烯(pvdf)粘结剂2pi粘结剂3聚四氟乙烯(ptfe)粘结剂4羧甲基纤维素钠(cmc)粘结剂5sbr粘结剂6聚氧化乙烯粘结剂7聚丙烯酸粘结剂8聚碳酸酯类粘结剂9pvdf-hfp粘结剂10聚丙烯腈粘结剂11苯乙烯-丁二烯共聚物粘结剂12聚酰胺表4正极材料编号组成正极材料1粒径为0.58nm的linbo3包覆的钴酸锂正极材料2ncm622正极材料3锰酸锂正极材料4lini0.5mn1.5o4正极材料5nca正极材料6ncm811正极材料7lifepo4正极材料8mno2正极材料9fes2正极材料10o2正极材料11s正极材料12钴酸锂表5负极材料负极编号组成负极1金属锂负极2锂铝合金(锂质量分数为20±1%)负极3锂镁合金(锂质量分数为75±1%)负极4锂硼合金(锂质量分数为70±1%)负极5锂/石墨复合锂(锂质量分数为35±1%)负极6锂/氧化亚硅复合(锂质量分数为45±1%)负极7锂/纳米硅复合(锂质量分数为30±1%)负极7金属钠表6导电添加剂导电添加剂编号组成导电添加剂1superp导电添加剂2乙炔黑导电添加剂3carbonblack导电添加剂4纳米铝粉导电添加剂5纳米银粉导电添加剂6纳米锡粉导电添加剂7纳米铜粉比较例1通过传统的烧结工艺,将正极和电解质混合烧结分别制备:正极混合材料粉末,其中包括活性物质钴酸锂、电解质latp、导电添加剂、均匀混合,倒入φ10的模具中。将电解质颗粒lagp倒在模具中的正极层粉末上,将正极层和电解质层一起压成圆片,电解质层厚度为500μm,正极层厚度为400μm。采用传统工艺将圆片烧结成陶瓷片,并且在850℃下退火3h,得到正极-电解质片,其微观结构如图4的sem照片所示。在850℃下退火5h得到正极-电解质片,其微观结构如图5的sem照片所示。从图中可以看出,高温短时间热处理的时候颗粒间存在明显的棱角,颗粒间接触是点接触,接触面积小。当高温长时间处理时,电解质颗粒融化,已经基本没有颗粒形状并且连接很好,但是颗粒之间存在严重的互扩散。将退火后的的正极-电解质片在电解质一侧贴上金属锂负极,组装成扣式电池,并在55℃、1c的条件下循环,热处理后,电池因接触差或者互扩散严重导致界面阻抗太大不能工作。没有容量放出。实例1通过分别制备:正极层混合材料,其中活性物质钴酸锂、电解质lagp、导电碳和粘结剂pvdf的质量比为7:3:0.5:0.5,以nmp为溶剂制备成浆料;电解质层混合材料,其中电解质lagp、粘结剂pvdf的质量比为90:10,以nmp为溶剂制备成浆料。将正极浆料涂布在载体al上,载体al厚度为10μm,涂布厚度为100μm。再将电解质浆料涂布在载体cu上,喷涂厚度为150μm。将正极层和电解质层重叠形成堆垛层,将得到的堆垛层进行机械波加热处理,加热时间6s,加压1mpa,得到正极-电解质片。正极-电解质片的微观结构如图6的sem照片所示,由于处理时间长,lagp晶体形貌已经消失,lagp都连接在一起,形成一个致密层,而熔点高的钴酸锂仍然保持晶体的形貌。在电解质片一侧贴上聚合物电解质膜,聚合物电解质为peo,膜厚为50μm。再贴上金属锂作负极,组装成2032扣式电池。将制备的扣式电池在55℃、1c的条件下进行循环,电池循环数据如图7所示,首周充电容量为91.3mah/g,放电容量为52.3mah/g,首周效率为57.28%。实例2通过振动混合的方法分别混合正极层混合材料,电解质层混合材料和负极层混合材料。其中正极层混合材料包括正极活性物质磷酸铁锂、电解质latp、粘结剂pva、导电添加剂superp;电解质层混合材料包括电解质latp、粘结剂pva;负极层混合材料包括负极活性物质石墨、粘结剂cmc。将三种混合均匀的材料分别按顺序大面积喷涂在集流体al上,最后再加上cu作为负极集流体。将喷涂得到的堆垛结构通过超声波加热,加热时间0.1s,加压1mpa,得到电池单元。电池单元的微观结构如图8的sem照片所示。由于处理时间较短,颗粒没有完全熔化,只在颗粒之间的界面处融化形成少量非晶相。原本棱角分明的电解质颗粒变成球形,并通过非晶相连接在一起。将得到的10个单体通过集流体的极耳形成并联连接,最后用铝塑膜封装,做成软包电池。将制备的软包电池在室温下、1c的条件下进行循环,电池循环数据如图9所示,首周充电容量为118.9mah/g,放电容量为94.8mah/g,首周效率为79.73%。实例3-12下面的表7列出了实例3-12的材料成分和快速界面加热方法,以及所得电池的电压范围和首周效率。表7实例3-12通过将上面的比较例1的结果与根据本发明的实例1-12的结果相比较可以发现,相对于单纯用长时间烧结方法制备固态电池,本发明通过利用快速界面加热方法,对颗粒界面,包括电解质颗粒间,电解质和正极颗粒间,负极和电解质颗粒间的界面进行短时间高温加热,可以达到改善界面接触,同时抑制界面互扩散和惰性层生成,以提高界面性能的目的,进而提高了固态电池的循环性能,也改善了固态电池的安全性。上面关于锂全固态描述了本发明的若干实施例,但是应理解,本发明的原理亦可应用到钠全固态电池,其与锂电池在各方面是相似的。此时,正极活性物质,电解质,粘结剂和负极活性物质均可以为相应的钠全固态电池中的材料。换言之,应理解,贯穿本说明书,在提及锂时,应也涵盖钠的实施例。上面关于锂固态电池描述了本申请的若干实施例,但是应理解的是,本申请的原理亦可应用到其他碱金属固态电池,例如钠和钾固态电池。此时,只需要进行相关材料的替换和参数的调整,在本发明的教导下,这对于本领域技术人员而言是显而易见的,不需要任何创造性的劳动。虽然上面参照示范性实施例描述了本发明,但本发明不限于此。本领域技术人员显而易见的是,在不脱离本发明的范围和思想的情况下,可以进行形式和细节上的各种变化和修改。本发明的范围仅由所附权利要求及其等价物定义。当前第1页12