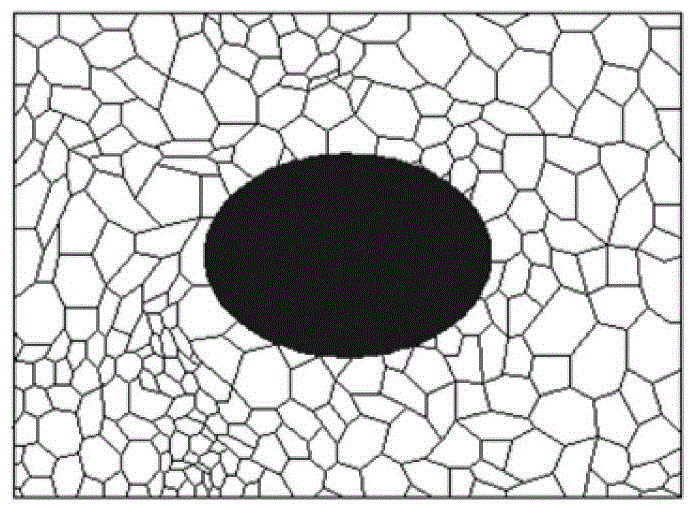
本发明涉及一种金属材料制造方法,具体来说是通过构筑方式实现金属或金属基材料成形的加工方法。该方法不但适用于同质材料的均质化制造,而且还适用于异质材料的复合制造。
背景技术:
:金属材料是人类历史发展中最不可或缺的材料,基于其得天独厚的廉价性、强韧性、耐久性等特点,金属在当代材料工业中始终占据主导地位。经过数千年的积累,人类已掌握一整套相当成熟的金属材料生产技术,例如传统的钢铁生产历经冶炼、浇铸、压力加工和热处理工序,产品质量稳定,价格低廉。近年来出现的金属基复合材料结合了金属材料与非金属材料的优点,具有比重小、比强度高等特点,进一步拓宽了金属材料的应用范围。一些关键领域对复合界面的结合强度要求较高,传统的爆炸复合方式由于在常温下压力复合,界面上存在显微缺陷,已难以满足要求,需要开发更加可靠、更加安全的新的金属复合方法。技术实现要素:本发明的目的在于提供一种制备大型金属材料或复合金属材料的构筑成形方法,以铸坯、锻坯、轧坯等为基元,通过表面加工和清洁后,将多个基元封装在一起,并使界面内部保持高真空状态,然后施加以镦粗变形、锻间保温、多向锻造为特点的锻焊工艺,最终制备优质大型金属器件。其中锻焊是指在高温锻造过程中,通过不同基元间的原子扩散使界面充分焊合而实现冶金连接的过程。本发明的技术方案为:一种金属构筑成形方法,包括如下步骤:首先制备基元:将多块小规格金属坯(可为铸坯、锻坯或轧坯)下料为指定尺寸,通过机械加工方式将表面加工平整,露出新鲜金属,并采用有机溶剂清洗洁净,处理后的坯料称之为基元;然后将基元构筑、封焊成预制坯:将多块基元按照使用需求进行排列组合,堆垛成大规格长方体或圆柱体,采用廉价金属板将构筑后的坯料整体封装成箱,并对箱内抽真空处理;或采用真空焊接方式分别将各基元间的界面封装;封装后的坯料称之为预制坯;然后将预制坯锻焊成毛坯:将封装后的预制坯加热到指定温度出炉,在液压机上进行锻造,实施镦粗变形、锻间保温的措施,使界面充分焊合,实现冶金连接,成为一体化的毛坯;最后成形为器件:将毛坯采用锻造、轧制等压力加工方式进一步成形,采用机加工方式精确成形为最终规格尺寸。该方法的具体步骤如下:第一步,按照预先计算好的尺寸规格裁切金属坯;第二步,加工、清洗金属坯表面;第三步,按照使用需求将多块金属坯排列组合、堆垛;第四步,将排列后的金属坯封装,使各接触界面处于真空状态;第五步,对封装后的金属坯实施锻前加热;第六步,对金属坯实施(多向)镦粗变形锻焊;第七步,对金属坯实施保温扩散连接;第八步,将金属坯加工成形至最终规格尺寸。所述的金属构筑成形方法,第一步中,裁切金属坯时,将坯料裁切成板型。准备合适数量裁切后的板坯,使其叠加之后总高度与宽度/厚度的比例不超过3∶1,便于实施镦粗变形。所述的金属构筑成形方法,第二步中,采用角磨、钢刷打磨金属坯表面,去除氧化皮,必要时采用铣床加工表面。然后采用丙酮、酒精等有机溶剂清洗表面,保障表面高度清洁,露出新鲜金属。所述的金属构筑成形方法,第三步中,按照使用需求,将多块金属坯排列组合、堆垛成大规格长方体,使边缘对齐。排列方式可为堆垛成多层,每层包括一个基元,也可为堆垛成多层,每层包括多个基元。所述的金属构筑成形方法,第四步中,采用廉价金属板将构筑后的坯料整体封装成箱,箱体预留抽真空接口,对箱内抽真空处理后再封堵接口;或将堆垛后的坯料整体放入真空室内,再采用真空焊接方式分别将各基元间的界面封装,封装界面的焊接深度为10~50mm。所述的金属构筑成形方法,第五步中,将焊接完成的坯料送入加热炉加热,加热温度为0.8至0.9Tm,Tm为材料的熔点,单位为℃。优选温度为0.85Tm。所述的金属构筑成形方法,第六步中,将加热后的坯料水平放置于锻压机操作平台上,使首次变形方向垂直于坯料内界面最多的方向;采用镦粗板对坯料进行镦粗;首先压下坯料总高度的10-20%;重复此变形动作于长方体坯料的三个法线方向,直至各接触界面均产生变形。所述的金属构筑成形方法,第七步中,将镦粗后的坯料送回加热炉加热,实施高温扩散,加热温度为0.85Tm,Tm为材料的熔点,单位为℃;坯料温度均匀后保温时间为3至8小时,优选时间为5小时。所述的金属构筑成形方法,第八步中,将锻焊成一体的坯料通过锻造、轧制等压力加工方式进一步成形,采用机加工方式精确成形为最终规格尺寸。本发明的物理冶金学和力学分析如下:在金属坯叠加、封焊边缘之后,虽然在宏观上界面两侧的板接触在一起,实际上由于板坯表面存在一定的粗糙度,微观上两块板之间是多点接触,在接触点之间存在大量空隙,这种空隙可以等效为孔洞。以其中一个孔洞为例,分析其在坯料镦粗锻造过程的演化历程:如图1所示,(a)变形开始阶段,孔洞被压扁,晶粒发生畸变;(b)孔洞宏观上闭合,形成裂纹状缺陷,基体发生再结晶;(c)裂纹缺陷失稳分解为圆柱体或球状微孔洞;(d)晶界迁移、晶粒长大,微孔洞在原子扩散作用下逐渐消失,两块板坯之间实现冶金结合。孔洞型缺陷的愈合过程包括孔洞的闭合与闭合表面的焊合:闭合是指孔洞表面在应力应变的作用下实现物理接触,焊合是指闭合表面在一定温度、接触压力以及保温时间的条件下通过扩散、再结晶等方式实现冶金结合。闭合是实现焊合的前提,采用锻造方式加工真空叠焊或真空封箱后的预制坯,预制坯中心的应变量远大于轧制方法,能够保证缺陷的闭合。焊合是实现缺陷完全愈合的关键,发明人前期通过系统的实验研究,发现显微尺度上一些缺陷虽然已经闭合,但尚未焊合,在外力作用下极易重新张开。同时,刚刚焊合的界面成分、组织与基体存在较大差异,形成“结合带”,这种“瘢痕”组织需变形后长时间高温热处理才能完全消除。基于上述考虑,本发明提出了“锻间保温”和“多向锻造”的方法实现界面的愈合和成分、组织的均匀化。“锻间保温”可以保障通过高温扩散,使变形时微观上仍存在的显微孔洞完全愈合;“多向锻造”可以保障焊合界面在多个方向上均发生大变形,使界面上残留的氧化膜尽可能地分散到基体当中,降低其对力学性能的危害。上述方法结合使用,可以最大程度上实现界面与基体的一致性。本发明突破了金属器件的母材只能比其更大的传统思维,使用品质更优、成本更低的小型金属坯构筑成形,具有如下的优点和有益效果:1、实现大尺寸金属器件的均质化制造。采用多块体积更小的金属坯作为构筑基元,由于凝固速度快,因此其成分均匀性远远好于传统整体铸造的大型金属坯,在此基础上构筑而成的大尺寸金属器件不存在显著的宏观偏析。2、实现大尺寸金属器件的致密化制造。采用多块体积更小的金属坯作为构筑基元,由于凝固速度快,几乎可以实现同时凝固,因此坯料内部集中的缩孔疏松少。焊合界面经变形、保温和多向锻造后,致密性高于传统整体铸坯制成的锻件。3、实现大尺寸金属器件的纯净化制造。采用多块体积更小的金属坯作为构筑基元,由于制备成本、难度低,因此可采用各种灵活的精炼方法实现基元的纯净化,在此基础上构筑而成的大尺寸金属器件纯净度高于传统整体铸坯制成的锻件。4、实现大尺寸金属器件的低成本制造。由于制备体积较小的金属坯可采用连铸等大生产手段,其制造成本远低于制备体积较大的金属坯必须采用的模铸手段,因此可大幅降低制造成本。此外,使用连铸坯作为构筑基元,没有传统钢锭的冒口、水口损耗,可提升材料利用率15%以上。5、实现大尺寸金属器件的清洁化、稳定化制造。传统模铸方法制备金属坯需人工准备模具、浇道、保温材料,同时浇注后冒口发热剂和覆盖剂存在较大的环境污染。采用金属构筑成形方法,过程可实现完全自动化,不但可以改善劳动环境,而且减少了人为因素影响,产品质量将更加稳定。6、实现金属器件的结构、功能一体化。传统整铸方法制备的金属坯采用单一材料,虽能实现耐蚀、耐热、耐磨等功能,但制造成本较高,存在浪费现象。采用金属构筑成形方法,表面为特殊的功能性金属,内部为廉价的结构性金属,可实现金属器件的结构、功能一体化,降低制造成本,节约合金资源。附图说明图1为界面愈合机理,其中,图1a为界面变形开始阶段;图1b为界面孔洞宏观上闭合阶段;图1c为界面裂纹缺陷失稳分解阶段;图1d为界面冶金结合阶段。图2a至图2j为本发明工艺流程图,其中,图2a显示金属坯切割下料;图2b显示将金属坯表面加工平整,露出新鲜金属,并进行清洗;图2c显示在真空坏境下对界面四周进行封焊,以获得预制坯;图2d显示将预制坯放入高温炉中加热;图2e显示在锻压机上采用镦粗板沿预制坯的高度方向镦粗;图2f显示镦粗变形到位,使缺陷充分焊合以获得毛坯;图2g显示将毛坯回炉高温扩散;图2h显示在液压机上采用镦粗板沿毛坯的长度方向镦粗;图2i显示在液压机上采用镦粗板沿毛坯的宽度方向镦粗,保障每个方向均有变形;图2j显示将毛坯料进一步锻造、加工成最终零件形状和尺寸。图3为本发明实施例1中,连铸坯基元堆垛成多层,每层包括一个基元。图4为本发明实验例1中,对应原基元界面位置的金相组织。图5为本发明实验例1中,沿锻件轴线方向等间距测试34个点的硬度分布。图6为本发明实施例2中,异质连铸坯、轧坯基元堆垛成多层,每层包括一个基元。图7a为本发明实施例3中,连铸坯基元堆垛成多层,每层包括一个基元。图7b为本发明实施例3中,使用薄钢板将堆垛后的基元六面封箱后的截面图。图8a为本发明实施例4中,连铸坯基元堆垛成多层,每层包括一个基元。图8b为本发明实施例4中,使用薄钢板将堆垛后的基元四面封箱后的截面图。图9为本发明实施例5中,连铸坯基元堆垛成多层,每层包括两个基元。图10为本发明实施例6中,连铸坯基元堆垛成多层,每层包括四个基元。图11为本发明实施例7中,连铸坯基元的多层交叉堆垛方式。图12为本发明实施例8中,16Mn连铸坯基元位于中心,304不锈钢轧坯基元环绕四周的环绕堆垛方式。图13a为本发明实施例9中,位于中心的16Mn连铸坯基元堆垛方式,图13b为本发明实施例9中,16Mn连铸坯基元位于中心,304不锈钢轧坯基元环绕周围六面的环绕堆垛方式。图14为本发明实施例10中,锻坯基元堆垛成多层,每层包括一个基元,堆垛后呈圆柱体。和图15为连铸坯封装结构示意图。具体实施方式图1为界面愈合机理,其中,图1a为界面变形开始阶段;图1b为界面孔洞宏观上闭合阶段;图1c为界面裂纹缺陷失稳分解阶段;图1d为界面冶金结合阶段。术语“界面”一般是指两个金属坯堆垛在一起时相互接触的表面。图2a至图2j为本发明工艺流程图,其中,图2a显示金属坯切割下料;图2b将金属坯表面加工平整,露出新鲜金属,并进行清洗;图2c显示在真空坏境下对界面四周进行封焊,以获得预制坯;图2d显示将预制坯放入高温炉中加热;图2e显示在锻压机上采用镦粗板沿预制坯的高度方向镦粗;图2f显示镦粗变形到位,使缺陷充分焊合以获得毛坯;图2g显示将毛坯回炉高温扩散;图2h显示在液压机上采用镦粗板沿毛坯的长度镦粗;图2i显示在液压机上采用镦粗板沿毛坯的宽度方向镦粗,保障每个方向均有变形;图2j显示将毛坯料进一步锻造、加工成最终零件形状和尺寸。图3为本发明实施例1中,连铸坯基元堆垛成多层,每层包括一个基元。图4显示本发明实验例1中对应的原基元界面位置的金相组织。图5显示本发明实验例1中沿锻件轴线方向等间距测试34个点的硬度分布。实施例1本实施例的目标产品为30万千瓦火电转子。首先采用连铸方式,浇注宽度1500mm、厚度370mm连铸板坯,其钢种为16Mn,化学成分为列于表1。然后切取长度为1700mm的连铸坯基元,加工、清洗后在真空室内封焊成预制坯。最后进行锻造、机加工。具体步骤如下:表116Mn钢的实测成分(重量百分数,%)元素CSiMnPSCrNiMoV成分0.160.371.460.010.0010.030.080.010.004第一步,按照一定的规格裁切连铸坯。切取规格为1500×1700×370mm连铸坯4块,使其叠加之后,宽(X方向)=1500mm,长(Y方向)=1700mm,高(Z方向)=1480mm(图3)。第二步,加工、清洗待焊接表面。采用龙门铣床加工连铸坯表面,然后采用丙酮清洗,保障表面高度清洁,露出新鲜金属。第三步,对连铸坯基元进行真空电子束焊接。将连铸坯基元放入真空室并叠加好,对面四周进行真空电子束焊接,焊接深度为50mm,焊接完成后得到预制坯(图3)。第四步,对预制坯实施锻前加热。将焊接完成的预制坯送入加热炉加热,加热温度为1250℃。第五步,对预制坯实施镦粗与锻焊。将加热后的预制坯放置于锻压机操作平台上,使预制坯高度方向(Z方向)沿竖直方向。参见附图2e,采用镦粗板沿高度方向(Z方向)对预制坯进行镦粗,压下预制坯总高度的10%。变形完成后得到毛坯。第六步,对毛坯实施高温扩散连接。将镦粗后的毛坯送回加热炉加热,加热温度为1250℃,毛坯均温后的保温时间为6小时。第七步,参见附图2h和2i,对毛坯实施三个方向的镦粗、拔长操作。每次镦粗变形量不小于毛坯沿镦粗方向高度的40%,镦粗后进行拔长修整外形,更换方向进行下一次镦粗。第八步,将毛坯锻造成形至最终锻件尺寸,总长度6500mm,最大直径1100mm,最小直径420mm。实验例1将实施例1的锻件沿中部锯开,加工切割表面至镜面,然后采用冷酸进行低倍实验,低倍检验结果显示截面元素分布均匀,无明显偏析。取对应界面位置的组织在显微镜下做高倍实验,高倍组织见图4。沿锻件轴线方向等间距测试34个硬度点,硬度分布见图5。由图可见,采用本发明的方法制造的大型锻件组织致密、均匀,头尾之间没有显著硬度差别。实施例结果表明,本发明可大幅降低制造成本,提升材料利用率,解决常规钢锭难以克服的偏析、粗晶、夹杂和缩孔疏松等问题,实现均质化锻件的热制造。另外,本发明也可用于复合金属器件的制造。图6为本发明实施例2中,异质连铸坯基元堆垛成多层,每层包括一个基元。实施例2本实施例的目标产品为厚板,厚板上下表面为不锈钢,心部为碳钢。首先采用连铸方式,浇注宽度1500mm、厚度370mm的16Mn连铸板坯,采用连铸连轧方式,轧制宽度1500mm、厚度100mm的304不锈钢轧坯。然后切取长度为1700mm的坯料基元,加工、清洗后在真空室内封焊成预制坯。最后进行锻造、机加工。具体步骤如下:第一步,按照一定的规格裁切连铸坯和轧坯。切取规格为1500×1700×370mm的16Mn连铸坯3块和规格为1500×1700×100mm的304不锈钢轧坯2块,5块坯料基元叠加后宽(X方向)=1500mm,长(Y方向)=1700mm,高(Z方向)=1310mm(图6)。第二步,加工、清洗待焊接表面。采用龙门铣床加工连铸坯表面,然后采用丙酮清洗,保障表面高度清洁,露出新鲜金属。第三步,对坯料进行真空电子束焊接。将坯料放入真空室并叠加好,将2块304不锈钢轧坯2放置在顶端和底端,3块16Mn连铸坯1放置在中间。对待焊合面四周进行真空电子束焊接,焊接深度为50mm,焊接完成后得到预制坯(图6)。第四步,对预制坯实施锻前加热。将焊接完成的预制坯送入加热炉加热,加热温度为1200℃。第五步,对预制坯实施镦粗与锻焊。将加热后的预制坯放置于锻压机操作平台上,使预制坯高度方向(Z方向)沿竖直方向。采用镦粗板沿高度方向(Z方向)对预制坯进行镦粗,压下预制坯总高度的10%。变形完成后得到毛坯。第六步,对毛坯实施高温扩散连接。将镦粗后的毛坯送回加热炉加热,加热温度为1200℃,毛坯均温后的保温时间为6小时。第七步,对毛坯实施三个方向的镦粗、拔长操作。每次镦粗变形量不小于毛坯沿镦粗方向高度的40%,镦粗后进行拔长修整外形,更换方向进行下一次镦粗。其中第三次镦粗方向为原始预制坯的高度方向,即垂直于堆叠界面方向。第八步,将毛坯锻造成形至最终锻件尺寸。厚板尺寸为300×1500×7000mm。厚板上下表面为不锈钢,内部为碳钢。图7a为本发明实施例3中,连铸坯基元堆垛成多层,每层包括一个基元。图7b为本发明实施例3中,使用薄钢板将坯料六面封箱后的截面图。实施例3本实施例的目标产品为模块。首先采用连铸方式,浇注宽度1500mm、厚度162mm的Q235连铸板坯。然后切取长度为1830mm的连铸坯基元,加工、清洗后进行封箱抽真空。最后进行锻造、机加工。具体步骤如下:第一步,按照一定的规格裁切连铸坯。切取规格为1500×1830×162mm的Q235连铸坯15块。使其叠加后,宽(X方向)=1500mm,长(Y方向)=1830mm,高(Z方向)=2430mm(图7a)。将16mm厚的Q235薄钢板裁切为6块,尺寸分别为2480×1560mm的2块,2480×1890mm的2块,1560×1890mm的2块,在薄钢板四周开坡口用于焊接。第二步,加工、清洗待焊接表面。采用龙门铣床加工连铸坯表面,然后采用丙酮清洗,保障表面高度清洁,露出新鲜金属。第三步,对连铸坯基元进行真空封箱。将连铸坯基元堆垛在一起,并将相邻两块连铸坯基元点焊在一起进行固定。使用16mm厚的Q235薄钢板3将堆垛后的连铸坯基元六面完全包围成箱。在薄钢板与堆垛后的坯料上下面之间铺垫石棉板,并在薄钢板箱的内侧涂覆脱模涂料。使用二氧化碳气体保护焊封箱,使6块薄钢板形成一个箱体将坯料包围。在箱侧面留Φ10mm圆孔,使用抽真空装置将箱内抽成真空状态,抽真空后将圆孔封住,使箱内保持真空。此步骤完成后得到预制坯(图7b)。第四步,对预制坯实施锻前加热。将焊接完成的预制坯送入加热炉加热,加热温度为1200℃。第五步,对预制坯实施镦粗与锻焊。将加热后的预制坯放置于锻压机操作平台上,使预制坯高度方向(Z方向)沿竖直方向。采用镦粗板沿高度方向(Z方向)对预制坯进行镦粗,压下预制坯总高度的10%。将薄钢板箱剥离,得到毛坯。第六步,对毛坯实施高温扩散连接。将镦粗后的毛坯送回加热炉加热,加热温度为1200℃,毛坯均温后的保温时间为6小时。第七步,对毛坯实施三个方向的镦粗、拔长操作。每次镦粗变形量不小于毛坯沿镦粗方向高度的40%,镦粗后进行拔长修整外形,更换方向进行下一次镦粗。第八步,将毛坯锻造成形至最终锻件尺寸。模块尺寸为1000×1500×4400mm。图8a为本发明实施例4中,连铸坯基元堆垛成多层,每层包括一个基元。图8b为本发明实施例4中,使用薄钢板将坯料四面封箱后的截面图。实施例4本实施例的目标产品为模块。首先采用连铸方式,浇注宽度1500mm、厚度162mm的Q235连铸板坯。然后切取长度为1830mm的连铸坯基元,加工、清洗后进行封箱抽真空。最后进行锻造、机加工。具体步骤如下:第一步,按照一定的规格裁切连铸坯。切取规格为1500×1830×162mm的Q235连铸坯15块。使其堆垛后,宽(X方向)=1500mm,长(Y方向)=1830mm,高(Z方向)=2430mm(图8a)。将16mm厚的Q235薄钢板,裁切为4块,尺寸分别为2430×1520mm的2块,2430×1850mm的2块,在薄钢板四周开坡口用于焊接。第二步,加工、清洗待焊接表面。采用龙门铣床加工连铸坯表面,然后采用丙酮清洗,保障表面高度清洁,露出新鲜金属。第三步,对连铸坯基元进行真空封箱。将连铸坯基元叠放在一起,并将相邻两块连铸坯基元点焊在一起进行固定。使用16mm厚的Q235薄钢板将叠放后的连铸坯基元四周包围,使连铸坯基元的堆叠界面被完全覆盖。在薄钢板箱的内侧涂覆脱模涂料。使用二氧化碳气体保护焊将薄钢板上下两端焊在最上和最下一块坯料上,并对4块薄钢板侧面进行封焊,相当于使用4块薄钢板和最上、最下两块坯料形成密封箱体。在其中一块薄钢板中心留φ10mm圆孔,使用抽真空装置将箱内抽成真空状态,抽真空后将圆孔封住,使箱内保持真空。此步骤完成后得到预制坯(图8b)。第四步,对预制坯实施锻前加热。将焊接完成的预制坯送入加热炉加热,加热温度为1200℃。第五步,对预制坯实施镦粗与锻焊。将加热后的预制坯放置于锻压机操作平台上,使预制坯高度方向(Z方向)沿竖直方向。采用镦粗板沿高度方向(Z方向)对预制坯进行镦粗,压下预制坯总高度的10%。将表面薄钢板剥离,得到毛坯。第六步,对毛坯实施高温扩散连接。将镦粗后的毛坯送回加热炉加热,加热温度为1200℃,毛坯均温后的保温时间为6小时。第七步,对毛坯实施三个方向的镦粗、拔长操作。每次镦粗变形量不小于毛坯沿镦粗方向高度的40%,镦粗后进行拔长修整外形,更换方向进行下一次镦粗。第八步,将毛坯锻造成形至最终锻件尺寸。模块尺寸为1000×1500×4400mm。图9为本发明实施例5中,连铸坯基元堆垛成多层,每层包括两个基元。实施例5本实施例的目标产品为模具钢模块。首先采用连铸方式,浇注截面为500×500mm的738H连铸方坯。然后切取长度为1000mm的连铸坯基元,加工、清洗后在真空室内封焊成预制坯。最后进行锻造、机加工。具体步骤如下:第一步,按照一定的规格裁切连铸坯。切取规格为500×1000×500mm的738H连铸方坯6块。使其堆垛成两列之后,宽(X方向)=1000mm,长(Y方向)=1000mm,高(Z方向)=1500mm(图9)。第二步,加工、清洗待焊接表面。采用龙门铣床加工连铸坯表面,然后采用丙酮清洗,保障表面高度清洁,露出新鲜金属。第三步,对连铸坯基元进行真空电子束焊接。将6块连铸坯分为3组,每组两块。将两块连铸坯放入真空室,使用真空电子束焊接成1000×1000×500mm的坯料。重复此过程得到3块1000×1000×500mm的坯料,将这3块坯料放入真空室,使用真空电子束焊接成1000×1000×1500mm的预制坯(图9)。第四步,对预制坯实施锻前加热。将焊接完成的预制坯送入加热炉加热,加热温度为1200℃。第五步,对预制坯实施镦粗与锻焊。将加热后的预制坯放置于锻压机操作平台上,使预制坯的高度方向(Z方向)沿竖直方向。采用镦粗板沿高度方向(Z方向)对预制坯进行镦粗,压下预制坯总高度的10%。之后将预制坯翻转,沿宽度方向(X方向)进行镦粗,压下预制坯总宽度的10%,。变形完成后得到毛坯。第六步,对毛坯实施高温扩散连接。将镦粗后的毛坯送回加热炉加热,加热温度为1200℃,毛坯均温后的保温时间为6小时。第七步,对毛坯实施三个方向的镦粗、拔长操作。每次镦粗变形量不小于毛坯沿镦粗方向高度的40%,镦粗后进行拔长修整外形,更换方向进行下一次镦粗。第八步,将毛坯锻造成形至最终锻件尺寸。模块尺寸为500×1000×3000mm。图10为本发明实施例6中,连铸坯基元堆垛成多层,每层包括四个基元。实施例6本实施例的目标产品为模具钢模块。首先采用连铸方式,浇注截面为500×500mm的738H连铸方坯。然后切取长度为500mm的坯料,加工、清洗后在真空室内封焊成预制坯。最后进行锻造、机加工。具体步骤如下:第一步,按照一定的规格裁切连铸坯。切取规格为500×500×500mm的738H连铸方坯12块。使其堆垛成四列之后,宽(X方向)=1000mm,长(Y方向)=1000mm,高(Z方向)=1500mm(图10)。第二步,加工、清洗待焊接表面。采用龙门铣床加工连铸坯表面,然后采用丙酮清洗,保障表面高度清洁,露出新鲜金属。第三步,对连铸坯基元进行真空电子束焊接。将12块连铸坯分为3组,每组4块。将4块连铸坯放入真空室,使用真空电子束焊接成1000×1000×500mm的坯料。重复此过程得到3块1000×1000×500mm的坯料,将这3块坯料放入真空室,使用真空电子束焊接成1000×1000×1500mm的预制坯(图10)。第四步,对预制坯实施锻前加热。将焊接完成的预制坯送入加热炉加热,加热温度为1250℃。第五步,对预制坯实施镦粗与锻焊。将加热后的预制坯放置于锻压机操作平台上,使预制坯的高度方向(Z方向)沿竖直方向。采用镦粗板沿高度方向(Z方向)对预制坯进行镦粗,压下预制坯总高度的10%。之后将预制坯翻转,沿宽度方向(X方向)进行镦粗,压下预制坯总宽度的10%。再次将预制坯翻转,沿长度方向(Y方向)进行镦粗,压下预制坯总长度的10%。变形完成后得到毛坯。第六步,对毛坯实施高温扩散连接。将镦粗后的毛坯送回加热炉加热,加热温度为1250℃,毛坯均温后的保温时间为6小时。第七步,对毛坯实施三个方向的镦粗、拔长操作。每次镦粗变形量不小于毛坯沿镦粗方向高度的40%,镦粗后进行拔长修整外形,更换方向进行下一次镦粗。第八步,将毛坯锻造成形至最终锻件尺寸。模块尺寸为500×1000×3000mm。图11为本发明实施例7中,连铸坯基元堆垛成多层,每层包括两个基元,并且相邻两层的金属坯的排列方向不一致。实施例7本实施例的目标产品为模具钢模块。首先采用连铸方式,浇注截面为500×500mm的738H连铸方坯。然后切取长度为1000mm的连铸坯基元,加工、清洗后在真空室内封焊成预制坯。最后进行锻造、机加工。具体步骤如下:第一步,按照一定的规格裁切连铸坯。切取规格为500×500×1000mm的738H连铸方坯6块。采用交叉式堆垛,使其堆垛后,宽(X方向)=1000mm,长(Y方向)=1000mm,高(Z方向)=1500mm(图11)。第二步,加工、清洗待焊接表面。采用龙门铣床加工连铸坯表面,然后采用丙酮清洗,保障表面高度清洁,露出新鲜金属。第三步,对连铸坯基元进行真空电子束焊接。将6块连铸坯分为3组,每组两块。将两块连铸坯放入真空室,使用真空电子束焊接成1000×1000×500mm的坯料。重复此过程得到3块1000×1000×500mm的坯料,将这3块坯料放入真空室,采用交叉式堆垛(如图11所示),使用真空电子束焊接成1000×1000×1500mm的预制坯。第四步,对预制坯实施锻前加热。将焊接完成的预制坯送入加热炉加热,加热温度为1250℃。第五步,对预制坯实施镦粗与锻焊。将加热后的预制坯放置于锻压机操作平台上,使预制坯的高度方向(Z方向)沿竖直方向。采用镦粗板沿高度方向(Z方向)对预制坯进行镦粗,压下预制坯总高度的10%。之后将预制坯翻转,沿宽度方向(X方向)进行镦粗,压下预制坯总宽度的10%。再次将预制坯翻转,沿长度方向(Y方向)进行镦粗,压下预制坯总长度的10%。变形完成后得到毛坯。第六步,对毛坯实施高温扩散连接。将镦粗后的毛坯送回加热炉加热,加热温度为1250℃,毛坯均温后的保温时间为6小时。第七步,对毛坯实施三个方向的镦粗、拔长操作。每次镦粗变形量不小于毛坯沿镦粗方向高度的40%,镦粗后进行拔长修整外形,更换方向进行下一次镦粗。第八步,将毛坯锻造成形至最终锻件尺寸。模块尺寸为500×1000×3000mm。图12为本发明实施例8中,16Mn连铸坯基元位于中心,304不锈钢轧坯基元环绕四周的环绕堆垛方式。实施例8本实施例的目标产品为轴类锻件,锻件表面为不锈钢,心部为碳钢。首先采用连铸方式,浇注宽度500mm、厚度200mm的16Mn连铸板坯,采用连铸连轧方式,轧制宽度1000mm、厚度100mm的304不锈钢轧坯。然后切取连铸坯、轧坯基元,加工、清洗后在真空室内封焊成预制坯。最后进行锻造、机加工。具体步骤如下:第一步,按照一定的规格裁切连铸坯和轧坯。切取规格为200×500×700mm的16Mn连铸坯4块,规格为100×500×700mm的304不锈钢轧坯2块,规格为100×700×1000mm的304不锈钢轧坯2块,8块坯料基元堆垛后宽(X方向)=700mm,长(Y方向)=700mm,高(Z方向)=1000mm(图12)。第二步,加工、清洗待焊接表面。采用龙门铣床加工连铸坯表面,然后采用丙酮清洗,保障表面高度清洁,露出新鲜金属。第三步,对连铸坯、轧坯基元进行真空电子束焊接。将4块连铸坯和2块规格为100×500×700mm的不锈钢轧坯2堆垛放入真空室,2块不锈钢轧坯2放置在顶端和底端,4块连铸坯放置在中间,使用真空电子束焊接成500×700×1000mm的坯料。将这块坯料与2块100×700×1000mm的不锈钢轧坯2堆垛放入真空室,2块不锈钢轧坯2放在两端,使用真空电子束焊接成700×700×1000mm的坯料。焊接完成后得到预制坯(图12)。第四步,对预制坯实施锻前加热。将焊接完成的预制坯送入加热炉加热,加热温度为1200℃。第五步,对预制坯实施镦粗与锻焊。将加热后的预制坯放置于锻压机操作平台上,使预制坯的高度方向(Z方向)沿竖直方向。采用镦粗板沿高度方向(Z方向)对预制坯进行镦粗,压下预制坯总高度的10%。之后将预制坯翻转,沿宽度方向(X方向)进行镦粗,压下预制坯总宽度的10%。变形完成后得到毛坯。第六步,对毛坯实施高温扩散连接。将镦粗后的毛坯送回加热炉加热,加热温度为1200℃,毛坯均温后的保温时间为5小时。第七步,对毛坯实施三个方向的镦粗、拔长操作。每次镦粗变形量不小于毛坯沿镦粗方向高度的40%,镦粗后进行拔长修整外形,更换方向进行下一次镦粗。第八步,将毛坯锻造成形至最终锻件尺寸。轴类件尺寸为Φ400×3900mm。轴类件外周面为不锈钢,内部和端面为碳钢。图13a为本发明实施例9中,位于中心的16Mn连铸坯基元堆垛方式,图13b为本发明实施例9中,16Mn连铸坯基元位于中心,304不锈钢轧坯基元环绕周围六面的环绕堆垛方式。实施例9本实施例的目标产品为模块,锻件表面为不锈钢,心部为碳钢。首先采用连铸方式,浇注宽度500mm、厚度200mm的16Mn连铸板坯,采用连铸连轧方式,轧制宽度1000mm、厚度100mm的304不锈钢轧坯。然后切取连铸坯、轧坯基元,加工、清洗后在真空室内封焊成坯料。最后进行锻造、机加工。具体步骤如下:第一步,按照一定的规格裁切连铸坯和轧坯。切取规格为200×500×500mm的16Mn连铸坯4块、规格为100×500×500mm的304不锈钢轧坯2块,规格为100×500×1000mm的304不锈钢轧坯2块,规格为100×700×1000mm的304不锈钢轧坯2块。10块坯料基元堆垛后宽(X方向)=700mm,长(Y方向)=700mm,高(Z方向)=1000mm,便于实施三向锻造(图13b)。第二步,加工、清洗待焊接表面。采用龙门铣床加工连铸坯表面,然后采用丙酮清洗,保障表面高度清洁,露出新鲜金属。第三步,对连铸坯、轧坯基元进行真空电子束焊接。将4块连铸坯和2块规格为100×500×500mm的不锈钢轧坯2堆垛放入真空室,图13a为4块连铸坯的堆垛方式,2块不锈钢轧坯2放置在顶端和底端,4块连铸坯放置在中间,使用真空电子束焊接成500×500×1000mm的坯料。将这块坯料与2块100×500×1000mm的不锈钢轧坯2堆垛放入真空室,2块不锈钢轧坯放在两侧,使用真空电子束焊接成700×500×1000mm的坯料。将这块坯料与2块100×700×1000mm的不锈钢轧坯堆2垛放入真空室,2块不锈钢轧坯2放在两端,使用真空电子束焊接成700×700×1000mm的坯料。焊接完成后得到预制坯(图13b)。第四步,对预制坯实施锻前加热。将焊接完成的预制坯送入加热炉加热,加热温度为1200℃。第五步,对预制坯实施镦粗与锻焊。将加热后的预制坯放置于锻压机操作平台上,使预制坯的高度方向(Z方向)沿竖直方向。采用镦粗板沿高度方向(Z方向)对预制坯进行镦粗,压下预制坯总高度的10%。之后将预制坯翻转,沿长度方向(Y方向)进行镦粗,压下预制坯总长度的10%。再次将预制坯翻转,沿宽度方向(X方向)进行镦粗,压下预制坯总宽度的10%。变形完成后得到毛坯。第六步,对毛坯实施高温扩散连接。将镦粗后的毛坯送回加热炉加热,加热温度为1200℃,毛坯均温后的保温时间为5小时。第七步,对毛坯实施三个方向的镦粗、拔长操作。每次镦粗变形量不小于坯料沿镦粗方向高度的40%,镦粗后进行拔长修整外形,更换方向进行下一次镦粗。第八步,将毛坯锻造成形至最终锻件尺寸。模块尺寸为400×700×1750。模块表面为不锈钢,内部为碳钢。图14为本发明实施例10中,锻坯基元的堆垛方式,堆垛后呈圆柱体。实施例10本实施例的目标产品为高温合金涡轮盘锻件。首先采用“三联”方式,即真空感应+气密电渣+真空自耗的方式制造高温合金铸锭4支,每支重600kg。将4只铸锭锻造成饼状,进行表面加工、清洗后进行封箱抽真空。最后进行锻造、机加工。具体步骤如下:第一步,按将铸坯锻造成所需规格。将4支高温合金铸锭锻造成Φ680×200的饼状锻坯,4块锻坯叠加后尺寸为Φ680×800。准备16mm厚的Q235薄钢板,裁切为6块,尺寸分别为700×820mm的4块,700×700mm的2块,在薄钢板四周开坡口用于焊接。第二步,加工、清洗待焊接表面。采用龙门铣床加工连铸坯表面,然后采用丙酮清洗,保障表面高度清洁,露出新鲜金属。第三步,对锻坯基元进行封箱。将锻坯基元堆垛在一起,并将相邻两块锻坯基元点焊在一起进行固定。使用16mm厚的Q235薄钢板将叠放后的锻坯基元六面完全包围。在薄钢板与堆垛后的坯料上下面之间铺垫石棉板,并在薄钢板箱的内侧涂覆脱模涂料。使用二氧化碳气体保护焊封箱,使6块钢板形成一个箱体将坯料包围。在箱侧面留φ10mm圆孔,使用抽真空装置将箱内抽成真空状态,抽真空后将圆孔封住,使箱内保持真空。此步骤完成后得到预制坯(图14)。第四步,对预制坯实施锻前加热。将焊接完成的预制坯送入加热炉加热,加热温度为1050℃。第五步,对预制坯实施镦粗与锻焊。将加热后的预制坯放置于锻压机操作平台上,使预制坯高度方向(Z方向)沿竖直方向。采用镦粗板沿高度方向(Z方向)对预制坯进行镦粗,压下预制坯总高度的10%。将薄钢板箱剥离,得到毛坯。第六步,对毛坯实施高温扩散连接。将镦粗后的毛坯送回加热炉加热,加热温度为1050℃,毛坯均温后的保温时间为6小时。第七步,对毛坯实施三个方向的镦粗、拔长操作。每次镦粗变形量不小于坯料沿镦粗方向高度的40%,镦粗后进行拔长修整外形,更换方向进行下一次镦粗。第八步,将毛坯锻造成形至最终锻件尺寸。高温合金涡轮盘锻件的尺寸为Φ1100×300。附图15为连铸坯封装结构示意图。说明如下:连铸坯封装结构包括待封装连铸坯1,用于封箱的薄钢板3,内封钢管4,单向阀5,外封罩6,石棉板7,脱模涂料8,抽真空设备9。通过以下封装过程,得到封装完成的预制坯:1)使用车床将6块薄钢板四条边开全尺寸坡口,然后在钢板的内侧涂覆脱模涂料。在其中一块侧面钢板中心开φ10mm圆孔,将φ30mm内封钢管焊在圆孔处,作为抽真空接口。2)使用专用对正工装,将坯料叠放在一起。将相邻两块坯料点焊在一起。3)使用薄钢板将叠放后的坯料包围,在薄钢板与叠放后的坯料上下面之间铺垫石棉板,石棉板与薄钢板之间铺洒碳粉。使用二氧化碳气体保护焊封箱。对焊缝进行100%探伤。4)将单向阀连接至φ30mm内封钢管接口,使用抽真空装置通过阀将箱内气体抽出,当真空度低于0.05Pa时停止。5)将箱体放置4~24小时后复检真空度,若不低于0.1Pa则可使用。采用φ60mm外封罩将φ30mm内封钢管及单向阀封装在内部。当前第1页1 2 3