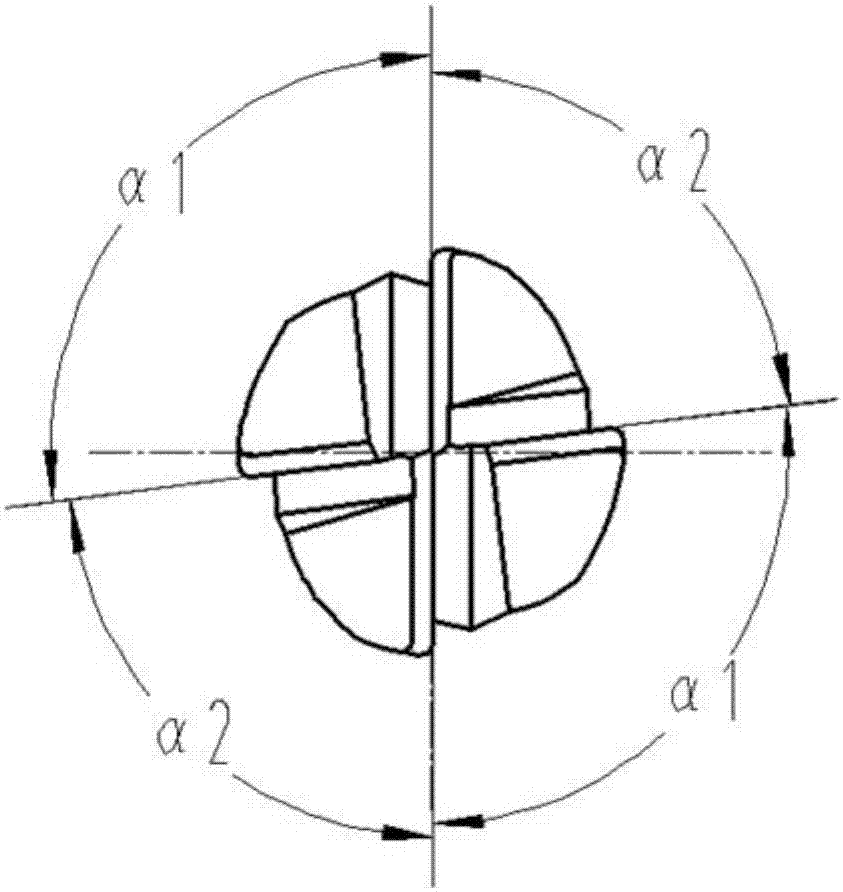
本实用新型属于切削刀具
技术领域:
,具体涉及一种加工超硬材质的立铣刀。
背景技术:
:近些年,随着加工中心主轴高速化技术的不断发展,以及模具行业中超高硬度材料的广泛使用,为提高加工效率及降低成本的需求,要求实现对难以切削的高硬度材料进行直接高速、低切深、大进给加工,实现已加工工件表面粗糙度值明显减小,甚至消除手工抛光的加工处理的目的,因此对高硬度材料加工中的刀具的性能及刀具的寿命提出了更高的要求。在高速条件下加工高硬度材料时,刀具容易产生振动或共振,易造成工件表面粗糙,且在连续加工过程中,刀具的失效形式不单单是切削刃磨损,更多的情况下为刀具的缺损而达到了刀具的使用寿命。因此,对于高速条件下加工高硬度材料时,就需要对刀具结构提出更合理的设计来满足需求。技术实现要素:为解决上述技术问题,本实用新型提供一种螺旋沟槽具有不对等、变导程且变刀芯结构的特征的立铣刀,其结构特征能确保提高刀具整体刚性的同时,增强刀尖的抗冲击强度,从而提高刀具的耐缺损性和耐用度,同时还可以避免在高速切削条件下因刀具振动或共振,得到良好的工件表面质量。本实用新型的技术方案如下:一种加工超硬材质的立铣刀,包括柄部以及与柄部同轴的铣削部,铣削部包括端面切削部和刀周切削部,位于铣削部顶端的端面切削部设有端面切削刃,刀周切削部位于铣削部顶部与柄部之间,刀周切削部包括刀芯、螺旋盘绕于刀芯外围的四条螺旋沟槽以及螺旋沟槽形成的刀周切削刃,其特征在于,所述四个螺旋沟槽分为两组,间隔的第一螺旋沟槽与第三螺旋沟槽为一组,采用恒定且相等的螺旋导程结构,间隔的第二螺旋沟槽与第四螺旋沟槽为第二组,采用相同的变导程结构,即第二螺旋沟槽与第四螺旋沟槽的导程沿铣刀轴线向柄部方向逐渐增大变化的结构,且间隔的第二螺旋沟槽和第四螺旋沟槽的整条螺旋展开线的各点相切;基于第二组螺旋沟槽采用变导程结构,四个螺旋沟槽的径向分布为不对等结构,相邻两螺旋沟槽的分度角α不等,同组螺旋沟槽的分度角α相等;所述的四个螺旋沟槽分为两组,第一组螺旋沟槽采用恒定且相等的螺旋导程结构,与导程相对应的螺旋角范围为50°≤ω1≤55°内的恒定数值;第二组螺旋沟槽采用沿轴线向柄部逐渐增大变化的变导程结构,单一螺旋沟槽上与导程相对应的螺旋角由ω1逐渐减小至ω2,螺旋角差值ω'=ω1-ω2的最大值在螺旋沟槽尾末端处,ω'范围为0°≤ω'≤5°。所述的四个螺旋沟槽的径向分度为不对等结构,第一螺旋沟槽与第二螺旋沟槽间的分度角α1大于第二螺旋沟槽与第三螺旋沟槽间的分度角α2,分度角差值α’的范围为1°≤α'≤15°。所述刀周切削部的螺旋沟槽的径向前角γ采用负前角,刀楔角β为钝角,可提高刀周切削刃的刃尖强度,从而提高刀周切削刃的耐缺损性。所述的螺旋沟槽的径向前角γ的范围为-11°至-15°,刀楔角β范围为91°至97°。所述铣刀刀芯的直径沿轴线向柄部方向逐渐增大,刀芯直径在螺旋沟槽沟槽末端达到最大值。所述的铣刀刀芯的直径沿轴线向柄部呈单侧轮廓4°至6°锥度变化。与现有技术相比,本实用新型的有益效果是:采用螺旋沟槽不对等、变导程设计,可降低刀具产生振动或共振的可能性,实现最佳工件表面质量;螺旋沟槽采用50°至55°较大的螺旋角,增大螺旋角使切削单位深度上参与切削的刃数增多,减小切削刃单位长度上的承载,确保轻快切削,从而降低切削力,提高刀具的耐用度,大螺旋角带来良好的切屑输送效果,避免划伤工件表面;减小刀具的沟槽前角,采用负前角结构,来增大刀楔角,使其为钝角结构,提高刀尖的抗冲击强度,从而提高耐缺损性;采用变刀芯结构,可使螺旋沟槽的沟槽末端具有较大的容屑空间,同时刀芯向沟槽末端逐渐增大,提高刀具整体刚性和抗震动能力,能够加工超硬材质,使得切削工艺可靠性更高。附图说明图1为本实用新型的主视图;图2为图1的左视图;图3为图1的A-A向剖视图;图4为本实用新型实施例1中测试二的切削力对比曲线;图中:1、柄部,21、第一螺旋沟,22、第二螺旋沟,23、第三螺旋沟,24、第四螺旋沟,3、铣削部,4端面切削刃,5、刀周切削刃,6、沟槽末端,7、刀芯,9、轴线。具体实施方式下面结合具体实施例对本实用新型做进一步详细的说明。实施例1如图1所示,一种加工超硬材质的立铣刀,包括柄部以及与柄部1同轴的铣削部3,铣削部3包括端面切削部和刀周切削部,位于铣削部3顶端的端面切削部设有端面切削刃4,刀周切削部位于铣削部3顶部与柄部1之间,刀周切削部包括刀芯7、螺旋盘绕于刀芯7外围的四条螺旋沟槽2以及螺旋沟槽形成的刀周切削刃5,其特征在于,所述四个螺旋沟槽2分为两组:第一螺旋沟槽21与第三螺旋沟槽23为一组,采用恒定且相等的螺旋导程结构,与导程相对应的螺旋角范围为50°≤ω1≤55°内的恒定数值,第二螺旋沟槽22与第四螺旋沟槽24为第二组,采用相同的变导程结构,即导程沿铣刀沿轴线9向柄部1逐渐增大变化的结构,单一螺旋沟槽上与导程相对应的螺旋角由ω1逐渐减小至ω2,螺旋角差值ω'=ω1-ω2的最大值在第二螺旋沟槽22与第四螺旋沟槽24的沟槽末端6处,ω'范围为0°≤ω'≤5°,间隔的第二螺旋沟槽与第四螺旋沟槽的整条螺旋展开线的各点相切;基于第二组螺旋沟槽22、24采用变导程结构,四个螺旋沟槽2的径向分布为不对等结构,相邻两螺旋沟槽2的分度角α不等,同组螺旋沟槽的分度角α相同,即第一螺旋沟槽21与第二螺旋沟槽22间的分度角α1大于第二螺旋沟槽22与第三螺旋沟槽23间的分度角α2,分度角差值α'的范围为1°≤α'≤15°。铣刀刀芯7的直径沿轴线9向柄部1逐渐增大,刀芯7变化规律为沿轴线9向柄部1呈单侧轮廓4°至6°锥度变化,刀芯7直径在沟槽末端6达到最大值。所述刀周切削部的螺旋沟槽2的径向前角γ采用负前角,径向前角γ的范围为-11°至-15°,刀楔角β为钝角,刀楔角β范围未91°至97°,可提高周刃5的刃尖强度,从而提高周刃5的耐缺损性。下面应用本实用新型实施例1产品立铣刀A与现有技术产品立铣刀B和现有技术立铣刀C进行对比测试。进行对比测试的本实用新型实施例1产品立铣刀A与现有技术产品立铣刀B和现有技术立铣刀C均为整体硬质合金铣刀,硬质合金牌号K20,其他具体规格尺寸如下:测试一:刀具切削刃强度对比测试测试刀具:本实用新型立铣刀A和现有技术立铣刀C。测试条件如下:直径:D8.0mm铣刀的安装:装夹后旋转主轴铣刀径向圆跳动小于0.02mm试验用试坯:试坯材质:SKD11;硬度:57~60HRC切削液:BlasocutBC25MD浓度8%切削线速度:126m/min进给速度:700mm/min切深Ap:4mm切宽Ae:0.12mm测试设备:DMG数控加工中心DMU60monoBLOCK停试要求:总加工长度达到54.4米测试结果如下:测试二:切削力对比测试测试刀具:本实用新型立铣刀A和现有技术立铣刀B。测试条件如下:测试结果如下:测试二所得数据均通过切削力测量系统KISTLER9255c获得,测试对比曲线如图4所示,根据图4和上述测试结果数据分析,在相同测试条件下,本实用新型立铣刀A相对现有技术产品立铣刀B切削过程中刀具的受力明显减小,刀具切削轻快,从而提到刀具的耐用度,降低加工中心主轴的负载;进一步的优势在于可以超出现有产品的进给速度进行铣削加工,提高加工效率。以上所述,仅为本实用新型较佳的具体实施方式,但本发明的保护范围并不局限于此,任何熟悉本
技术领域:
的技术人员在本发明揭露的技术范围内,根据本发明的技术方案及其发明构思加以等同替换或改变,都应涵盖在本发明的保护范围之内。当前第1页1 2 3