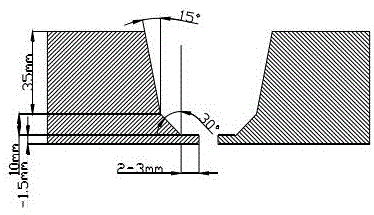
本发明涉及一种管道焊接方法,特别涉及一种高压蒸汽管道焊接方法。
背景技术:
:从化学成分看,现在通常采用的高压蒸汽管为单相奥氏体组织,具有较好的耐高温和耐腐蚀性能,较大的碳含量反映出此管道在焊接时具有较大的淬硬倾向;并且此种管道的口径大,管壁厚,结构钢性大,焊接时容易产生较大的拘束应力和三维应力;同时,由于管壁很厚,坡口加工深度深,焊接时冷却速度快,此时焊缝中的扩散氢不能够及时逸出,就会使得焊缝中的扩散氢含量高;总而言之,此种超厚管道在焊接时,在淬硬组织、扩散氢和焊接应力的作用下,非常容易产生冷裂纹。由于此种超厚管道可焊性较差,焊接接头主要产生的问题一是焊后无法进行调制热处理保证接头的强度,二是焊接热输入可能造成材料的韧性下降,工艺措施不当容易产生冷裂纹;三是高含cr量带来的剩磁造成焊接过程的电弧磁偏吹容易形成的熔敷金属缺欠;选择采用与母材组织相近的组织作为焊缝的填充金属,降低了母材因可焊性差可能产生冷裂纹缺陷的风险,从而简化了现场焊接工艺措施的复杂性,但是由于焊条的高熔点性,焊接熔池表面张力大,流动性差,同时母材的低特性又要求尽可能的使用小电流,因此加大了焊接操作的难度,研究焊接工艺的关键是找到不同焊接位置条件下最佳的焊接参数和方式,以获得一致的热输入。技术实现要素:本发明的目的是为了解决
背景技术:
而提出的一种高压蒸汽管道焊接方法,不仅能够有效促使金相组织的转变,明显减小晶粒的长大,有效避免焊接裂纹的发生,相对于传统手工电弧焊,能够明显提高高压蒸汽管道的焊接质量和焊接区域的综合性能,具有广阔的应用前景。为了实现上述目的,本发明采用了如下技术方案:一种高压蒸汽管道焊接方法,其特征在于,依次包括如下步骤:(1)焊接前准备:焊条在使用前进行烘干处理,烘干后的焊条应保持在100~150℃的恒温箱中,焊条出恒温箱后应在焊条保温筒内存放,并在4h内用完,若4小时内未使用,焊条必须重新进行烘干,且重复烘干不能超过2次;(2)加工坡口:采用机械加工方式对坡口进行加工,采用连续分段式坡口,坡口钝边不大于1.5mm,坡口底部与管道长度方向夹角为60°,高度10mm,坡口上部与管道长度方向夹角为75°;(3)管道组对:组对时设置的组对间隙片以保证对口间隙,间隙宜大于焊丝的直径,即2.8~3mm,管子或管件组对时,内壁应齐平,内壁错边量不宜超过管壁厚度的10%且不应大于0.5mm,当管道的内壁差超过0.5mm或外壁差超过2mm,应修边以保证焊接质量;(4)手工钨极氩弧焊打底:对管道焊接部位采用电加热方式进行预热,将管道两头有效封堵,第一次预热至150℃,升温速度为75℃/h,焊件达到预热温度后保温15min再采用多层单道焊方式进行手工钨极氩弧焊打底,保证厚度方向上温度均匀,并一次连续焊完,焊接过程中跟踪预热,预热范围以焊接接头中心线为基准,两侧不小于100mm,加热区以外的100mm区域进行保温处理;(5)手工电弧焊填充:打底后进行后续预热,第二次预热至250-350℃,升温速度为75℃/h,进行两遍手工电弧焊填充和一遍多道多层手工电弧焊填充,焊接过程中跟踪预热,预热范围以焊接接头中心线为基准,两侧不小于100mm,加热区以外的100mm区域进行保温处理;(6)手工电弧焊盖面:填充完成后保持预热温度在350℃,采用手工电弧焊进行填充盖面;(7)焊后热处理:焊接垢封堵管道两端端口,采用局部电加热法进行加热,加热范围以焊缝中心为基准,两侧各不小于焊缝宽度的3倍且不小于25mm,加热区外的100mm范围内应予保温,选择75℃/h的升温速度升温至720~750℃,恒温3h后进行降温处理,降温速度为75℃/h,温度在300℃时进行自然冷却;(8)焊后检验:管道壁厚大于40mm的焊缝在打底完毕并填充至约20mm的焊缝厚度后进行射线检测,合格后将剩余厚度焊完,并进行100%超声波检测;对外观检查、无损检测不合格的焊缝应进行返修,返修后的焊缝按原检测方法进行检验。作为本发明更进一步的限定,加工坡口时将坡口表面及边缘20mm内的淬硬层磨削干净,清除油漆、毛刺、锈斑、氧化皮,加工完后进行检测,坡口表面不得有裂纹、夹层的缺陷,并对母材的坡口进行磁性检测和渗透性检测,对管道内部切削端面进行打磨处理,形成坡口端面的平滑过渡。作为本发明更进一步的限定,手工钨极氩弧焊工艺参数为:氩弧焊喷嘴直径12mm,钨极伸出长度5-6mm,氩弧焊喷嘴与焊件角度75°~80°,用纯度为99.99%的氩气进行保护焊接,正面保护气体流量12~18l/min,背面保护气体流量10~12l/min;电源直流正接,电流105~125a,电弧电压10~12v,焊接速度6~9cm/min,线能量不大于15kj/cm。作为本发明更进一步的限定,两遍手工电弧焊工艺参数分别为:第一遍手工电弧焊填充采用直径3.2mm的r407焊丝,用纯度为99.99%且含水量低于0.05‰的二氧化碳气进行保护焊接,背面保护气体流量10~12l/min,电源直流反接,电流95~115a,电弧电压21~24v,焊接速度7~11cm/min,线能量不大于24kj/cm;第二遍手工电弧焊填充采用直径3.2mm的r407焊丝,用纯度为99.99%且含水量低于0.05‰的二氧化碳气进行保护焊接,背面保护气体流量10~12l/min,电源直流反接,电流100~120a,电弧电压21~24v,焊接速度7~11cm/min,线能量不大于25kj/cm。作为本发明更进一步的限定,多道多层手工电弧焊工艺参数为:采用直径4.0mm的r407焊丝,电源直流反接,电流140~165a,电弧电压21~24v,焊接速度10~13cm/min,线能量不大于24kj/cm。作为本发明更进一步的限定,手工电弧焊盖面工艺参数为:采用直径4.0mm的r407焊丝,电源直流反接,电流140~160a,电弧电压21~24v,焊接速度10~14cm/min,线能量不大于23kj/cm。作为本发明更进一步的限定,焊接过程中因特殊情况中断或整体焊缝完成后不能立即进行热处理时,应进行后热处理,后热处理温度控制在300℃~350℃之间,保温时间2h,升温速度不大于75℃/h。作为本发明更进一步的限定,焊接过程中随时对层间温度进行检测,严格控制层间温度在预热温度250~300℃,达不到要求时重新进行预热后方可继续焊接;焊接过程中加热设施不拆除,进行保温处理。本发明的有益效果是:1、由于高压蒸汽管所用的耐热钢有较大淬硬倾向和裂纹倾向,为了减少淬硬组织以及减小焊接应力,降低冷却速度及焊接区的温差,采用焊接预热处理,有利于焊缝中扩散氢的逸出,防止出现焊接冷裂纹等焊接缺陷。2、采用在焊接过程中随时对层间温度进行检测的技术,严格控制层间温度在预热温度250℃~300℃,达不到要求时重新进行预热后继续施焊,对于采用电加热法预热的焊缝,施焊过程中加热设施不拆除,进行保温,一是使焊件整个截面热透,即里外温度均匀;二是保证组织转变完全。3、在焊件达到预热温度后,保持15分钟再开始打底焊接并一次连续焊完,能够保证在厚度方向上温度均匀;打底焊接完后,立即进行下一层的焊接并连续焊完,能够保证焊接层间温度防止焊接裂纹的产生。4、焊接过程中须中断、整道焊缝完成不能立即热处理时采取后热处理,后热温度加热至300~350℃,恒温2h,升温速度为不大于75℃/h,这样能够消除焊缝中的扩散氢,防止产生冷裂纹。5、对焊接后的接头进行焊后热处理,选择75℃/h的升温速度升温至720~750℃,恒温3h后进行降温处理,降温速度为75℃/h,温度在300℃时进行自然冷却,这样的处理方式能够消除焊接接头的残余应力,减少淬硬性,改善组织,加速氢的逸出,防止出现焊接裂纹,提高接头的综合力学性能。附图说明图1是本发明提出的高压蒸汽管道焊接方法中对接焊口坡口的结构示意图。图2是本发明提出的高压蒸汽管道焊接方法的焊接接头金相组织图。具体实施方式下面结合具体实施例来对本发明进一步说明。实施例一参照图1,一种高压蒸汽管道焊接方法,其特征在于,依次包括如下步骤:(1)焊接前准备:焊条在使用前进行烘干处理,烘干后的焊条应保持在100~150℃的恒温箱中,焊条出恒温箱后应在焊条保温筒内存放,并在4h内用完,若4小时内未使用,焊条必须重新进行烘干且重复烘干不能超过2次;(2)加工坡口:采用机械加工方式对坡口进行加工,采用连续分段式坡口,坡口钝边不大于1.5mm,坡口底部与管道长度方向夹角为60°,高度10mm,坡口上部与管道长度方向夹角为75°;(3)管道组对:组对时设置的组对间隙片以保证对口间隙,间隙宜大于焊丝的直径,即2.8~3mm,管子或管件组对时,内壁应齐平,内壁错边量不宜超过管壁厚度的10%且不应大于0.5mm,当管道的内壁差超过0.5mm或外壁差超过2mm,应修边以保证焊接质量;(4)手工钨极氩弧焊打底:对管道焊接部位采用电加热方式进行预热,将管道两头有效封堵,第一次预热至150℃,升温速度为75℃/h,焊件达到预热温度后保温15min再采用多层单道焊方式进行手工钨极氩弧焊打底,保证厚度方向上温度均匀,并一次连续焊完,焊接过程中跟踪预热,预热范围以焊接接头中心线为基准,两侧不小于100mm,加热区以外的100mm区域进行保温处理;(5)手工电弧焊填充:打底后进行后续预热,第二次预热至250-350℃,升温速度为75℃/h,进行两遍手工电弧焊填充和一遍多道多层手工电弧焊填充,焊接过程中跟踪预热,预热范围以焊接接头中心线为基准,两侧不小于100mm,加热区以外的100mm区域进行保温处理;(6)手工电弧焊盖面:填充完成后保持预热温度在350℃,采用手工电弧焊进行填充盖面;(7)焊后热处理:焊接垢封堵管道两端端口,采用局部电加热法进行加热,加热范围以焊缝中心为基准,两侧各不小于焊缝宽度的3倍且不小于25mm,加热区外的100mm范围内应予保温,选择75℃/h的升温速度升温至720~750℃,恒温3h后进行降温处理,降温速度为75℃/h,温度在300℃时进行自然冷却;(8)焊后检验:管道壁厚大于40mm的焊缝在打底完毕并填充至约20mm的焊缝厚度后进行射线检测,合格后将剩余厚度焊完,并进行100%超声波检测;对外观检查、无损检测不合格的焊缝应进行返修,返修后的焊缝按原检测方法进行检验。其中,加工坡口时将坡口表面及边缘20mm内的淬硬层磨削干净,清除油漆、毛刺、锈斑、氧化皮,加工完后进行检测,坡口表面不得有裂纹、夹层的缺陷,并对母材的坡口进行磁性检测和渗透性检测,对管道内部切削端面进行打磨处理,形成坡口端面的平滑过渡。其中,手工钨极氩弧焊工艺参数为:氩弧焊喷嘴直径12mm,钨极伸出长度5-6mm,氩弧焊喷嘴与焊件角度75°~80°,用纯度为99.99%的氩气进行保护焊接,正面保护气体流量12~18l/min,背面保护气体流量10~12l/min;电源直流正接,电流105~125a,电弧电压10~12v,焊接速度6~9cm/min,线能量不大于15kj/cm。其中,两遍手工电弧焊工艺参数分别为:第一遍手工电弧焊填充采用直径3.2mm的r407焊丝,用纯度为99.99%且含水量低于0.05‰的二氧化碳气进行保护焊接,背面保护气体流量10~12l/min,电源直流反接,电流95~115a,电弧电压21~24v,焊接速度7~11cm/min,线能量不大于24kj/cm;第二遍手工电弧焊填充采用直径3.2mm的r407焊丝,用纯度为99.99%且含水量低于0.05‰的二氧化碳气进行保护焊接,背面保护气体流量10~12l/min,电源直流反接,电流100~120a,电弧电压21~24v,焊接速度7~11cm/min,线能量不大于25kj/cm。其中,多道多层手工电弧焊工艺参数为:采用直径4.0mm的r407焊丝,电源直流反接,电流140~165a,电弧电压21~24v,焊接速度10~13cm/min,线能量不大于24kj/cm。其中,手工电弧焊盖面工艺参数为:采用直径4.0mm的r407焊丝,电源直流反接,电流140~160a,电弧电压21~24v,焊接速度10~14cm/min,线能量不大于23kj/cm。在制定焊接工艺时注意以下几个方面能够预防各类缺陷的产生:a.不得在坡口以外引弧,焊件组对时应垫置牢固,并应采取措施防止焊接和热处理过程中产生附加应力和变形,不得强行组对;b.对高压蒸汽管道的焊接,预热温度为250~350℃;c.高压蒸汽管道的焊接要用纯度为99.99%的氩气进行保护焊接,正面保护气体流量12~18l/min,背面保护气体流量10~12l/min;d.在焊接过程中,将管道两头有效封堵,严防“穿堂风”;通风会造成气流紊乱,影响氩气保护效果,将会把氩气带走,很容易造成根部气孔,而且不容易发现;e.单层厚度不大于所用焊条直径加2mm;单焊道摆动宽度不大于所用焊条直径的5倍;f.焊道排列采用多层多道焊,对减小焊接线能量、降低焊接应力水平、防止出现不良金属组织、控制焊接变形具有重要作用;g.焊接次层焊道时,不致将打底层烧穿。根据发明人的试验,将氩弧焊打底层的最小厚度规定为3mm,保证焊缝的基本强度,防止开裂;h.在焊接中应确保起弧与收弧的质量,收弧时应将弧坑填满,多层焊的层间接头应相互错开;i.多层焊每层焊完后,应立即对层间进行清理并检查。层间清渣时间不大于15分钟,且层间温度不应低于预热温度;j.每条焊缝应一次连续焊完,如须中断,停焊时按正常后热要求,确认无裂纹后方可后按原工艺要求继续施焊。其中,焊接过程中因特殊情况中断或整体焊缝完成后不能立即进行热处理时,应进行后热处理,后热处理温度控制在300℃~350℃之间,保温时间2h,升温速度不大于75℃/h。其中,焊接过程中随时对层间温度进行检测,严格控制层间温度在预热温度250~300℃,达不到要求时重新进行预热后方可继续焊接;焊接过程中加热设施不拆除,进行保温处理。管道组对要求:a.对于管径小于200mm的焊缝,点固焊位置推荐选择3~4个点位;组对错边量应该小于壁厚的10%,质量检查等级为i级的管道不应大于1mm,其他级别的管道不超过2mm;b.定位焊及管卡具的焊接要求与正式焊接工艺相同,定位焊长度、厚度和间距应能保证焊缝在正式焊接过程中不致开裂;一般为10~15mm,高度为2~4mm,且不超过管壁厚的三分之二,焊肉不应有裂纹等缺陷,在施焊第一层前要用磨光机将定位焊焊肉两侧磨成缓坡形,以利于接头处充分融合;c.与母材焊接的管卡具其材质应与母材相同或同一类别号;需预拉伸或预压缩的管道焊缝,组对时所使用的工卡具应在整个焊缝焊接及热处理完毕并经检验合格后方可拆除;拆除时不应损伤母材,拆除后应将残留焊疤打磨修整至与母材表面平齐。d.管口的组对点固质量经检验合格后,方可进行正式焊接。预热、层间温度及焊接参数的控制需注意一下要点:由于所用高压蒸汽管道的特性是通过管道材料中的马氏体组织获得,焊接过程应采取措施保证接头金属组织在连续冷却过程能够全部转变为马氏体组织,过高的预热温度、层间温度及过大焊接热输入是造成热影响区和焊缝中形成;由于存在铁素体的原因,过高的预热和层间温度不仅对防治冷裂纹没有必要,相反会危及焊缝金属的韧度,因此在施工过程采取以下措施控制焊接热循环:a.预热、层间温度控制措施,接头焊前预热时测温点在加热带下且距离坡口有80mm左右的距离,测温点温度不能准确反映焊前坡口内焊中焊道上需要控制区域内的温度,对于预热温度坡口内实际温度没有达到测温点反映温度、对于层间温度控制实际温度超过测温点温度,因此必须采用测温枪辅助实测焊接区域的即时温度,控制预热温度不低于230℃开始焊接(氩弧焊打底控制在不低于180℃),规定焊工在焊接所有后一道焊缝前应实测确认层间温度,控制层间温度在230-280℃间焊接,过高过低都是不利于接头的冷裂纹控制和韧度控制;b.通过限制一次熔敷焊道宽度厚度达到控制热输入的目的,焊材合金元素含量较高,熔池铁水流动性差,为控制热输入使用小电流会带来层道间熔合不良的可见缺陷,因此需采用较大的焊接电流通过提高焊速来保证较低的焊接热输入量;严格控制单道焊道一次熔敷厚度不大于焊条直径、焊道宽度不大于焊条直径的3倍,保证了应有的焊接速度,实现了适当线能量控制热输入的目的;c.由于所用管材的马氏体完全转变温度在300℃以下,焊后应保证接头冷却到300℃以下才可重新加热进行热处理,但为防止焊后快速冷却冷裂倾向严重,应采取保温缓冷措施,对于焊后不能及时进行热处理的接头,焊后应立即加热到250-300℃保温不少于1小时进行消氢处理;当日不能连续完成的焊口应保证填充焊缝厚度不少于1/3壁厚,且应持续保温不少于150℃直至第二次开始焊接;d.氩弧打底背部保护充气保护措施,所用焊材的高合金含量增加了氩弧焊打底时背面的氧化倾向,使用更加规范化的预置封堵措施,在焊口组对前分别在两端管口内预置牢固纸板,组对预留间隙后采用高温胶布或矿砂面封堵间隙,形成密封气室,焊接时使用多孔细铜管从间隙插入增大送气量,随熔池移动逐渐撕掉胶布或矿砂面,减少氩气的泄漏量,提高管内充气保护效果,保护背面金属,防止过度氧化,克服因焊缝氧化造成的未焊透和未熔合等缺陷,且预置的纸板在热处理时烧毁,不会在管道内留下固体物。拉伸、弯曲、冲击及硬度试验对焊接接头进行拉伸、弯曲、冲击及硬度试验,试验结果下表1至4所示:表1焊接接头弯曲试验结果试验编号试样厚度(mm)弯曲角度弯曲轴直径(mm)弯曲方式缺陷类型110180°40侧向弯曲无缺陷210180°40侧向弯曲无缺陷310180°40侧向弯曲无缺陷410180°40侧向弯曲无缺陷510180°40侧向弯曲无缺陷表2焊接接头拉伸试验结果试验编号试样宽度(mm)试样厚度(mm)横截面积mm2最大载荷kn抗拉强度mpa断裂部位和断裂性质120.1234.42708405.3577热影响区韧性断裂219.8735.02783387.9572热影响区韧性断裂表3焊接接头冲击试验结果表4焊接接头硬度试验结果试验编号焊缝区热影响区母材区11991431332201145128319814714342021481395197144136最后,由图2可以看出,接头的熔合情况良好,焊接接头金相组织母材区为铁素体,焊缝组织为回火索氏体加少量铁素体,热影响区为铁素体加珠光体加少量回火贝氏体;由此说明焊接热输入看焊条焊接热输入对接头熔敷金属、热影响区的组织形态影响不大。本发明通过对高压蒸汽管道接头的坡口加工成连续分段式坡口形式,经过管道组对后采用手工钨极氩弧焊打底、两遍手工电弧焊填充和一遍多道多层手工电弧焊填充,然后采用手工电弧焊盖面,最后对高压蒸汽管道进行焊后热处理和焊后检验,通过对对高压蒸汽管的焊接进行焊接参数及热处理工艺的设置能够有效促使金相组织的转变,明显减小晶粒的长大,有效避免焊接裂纹的发生,相对于传统手工电弧焊,能够明显提高高压蒸汽管道的焊接质量和焊接区域的综合性能。以上所述,仅为本发明较佳的具体实施方式,但本发明的保护范围并不局限于此,任何熟悉本
技术领域:
的技术人员在本发明揭露的技术范围内,根据本发明的技术方案及其发明构思加以等同替换或改变,都应涵盖在本发明的保护范围之内。当前第1页12