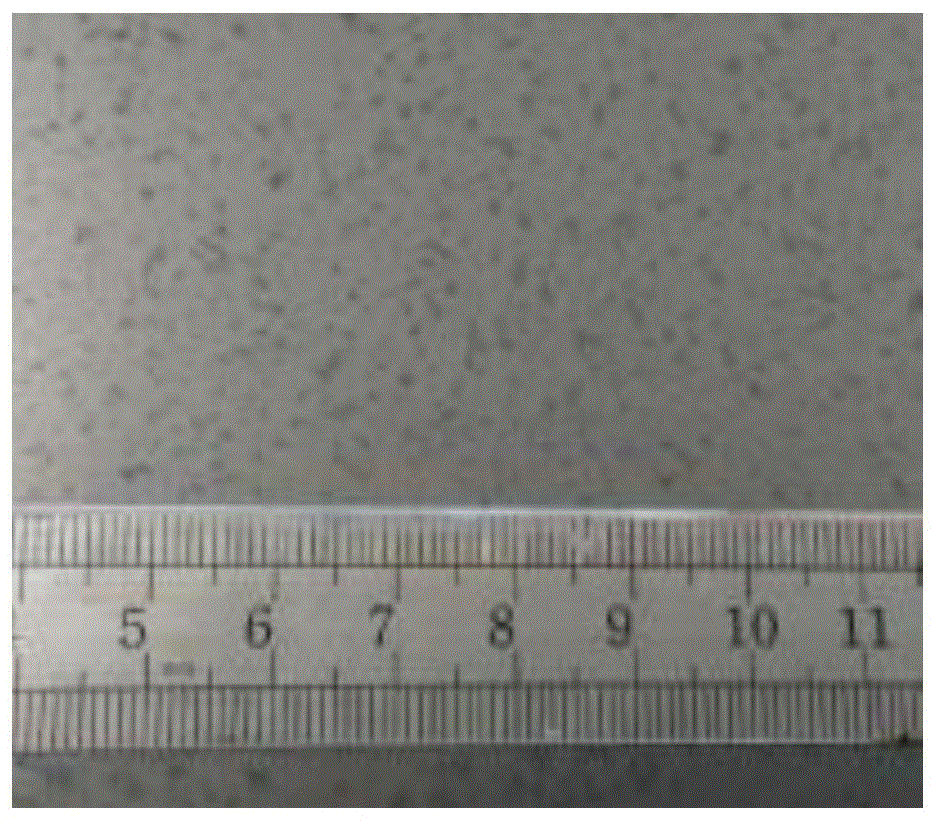
本发明涉及钢铁冶金
技术领域:
,特别涉及一种减少含b碳素结构钢酸洗板表面铁皮压入缺陷的方法。
背景技术:
:酸洗板作为板带材生产发展的新兴品种,以优质热轧薄板为原料,经酸洗机组去除氧化层、切边、精整后作为成品使用,其表面质量和使用要求介于热轧板和冷轧板之间,是部分冷轧板的理想替代产品。国内热轧酸洗板主要用途有:摩托车车身及结构件、家电行业的压缩机外壳、乘用车和轿车的车轮、底盘及结构件等。产品特点包括:1)弥补冷轧产品难以生产的厚规格产品;2)具有良好的表面质量,与普通热轧板相比,酸洗板去除了表面铁皮,便于焊接、涂油和上漆;3)尺寸精度高,产品经过平整处理后减少平直度偏差,提高板型质量,有利于表面处理和深加工。但产线在生产含b的碳素结构钢系列产品时常常发生铁皮压入缺陷。因此,如何开发一种减少含b碳素结构钢酸洗板表面铁皮压入缺陷的方法,成为亟待解决的技术问题。技术实现要素:本发明目的是提供一种减少含b碳素结构钢酸洗板表面铁皮压入缺陷的方法,减少了含b碳素结构钢酸洗板表面铁皮缺陷。为了实现上述目的,本发明提供了一种减少含b碳素结构钢酸洗板表面铁皮压入缺陷的的方法,所述方法包括:获得含b碳素结构钢的铸坯;将所述铸坯进行轧前加热、粗轧、精轧和轧后冷却,获得精轧板;其中,所述精轧中开启冷却水以控制位于前三道次的钢带表面温度<950℃,所述精轧入口温度为980~1000℃,所述精轧终轧温度为880~900℃;将所述精轧板进行卷取,获得氧化铁皮厚度<8μm的热轧卷;将所述热轧卷进行酸洗,获得表面质量好的含b碳素结构钢酸洗板。进一步地,所述钢的化学成分以质量分数计为:c:0.15~0.18%,si:0.03~0.05%,mn:0.35~0.5%,p≤0.015%,s≤0.015%,al:0.04~0.06%,b:0.001~0.002%,其余为fe和不可避免的杂质。进一步地,所述获得含b碳素结构钢的铸坯,具体包括:采用所述的化学成分进行熔炼、锻造,获得含b碳素结构钢的铸坯。进一步地,所述轧前加热包括:加热段和均热段,所述加热段为以室温升温至均热温度1150~1180℃,所述均热段为在均热温度1150~1180℃下保温;所述轧前加热的总时间为130~160min。进一步地,所述粗轧中,采用3+3道次进行轧制,控制轧制速度为2~5mm/s,控制粗轧总变形量为80~85%,控制粗轧进口温度为1120~1140℃。进一步地,所述精扎中,采用6道次进行轧制,控制轧制速度为8~10mm/s,控制精轧总变形量为85~92%;开启精轧双道次除鳞,精轧抛钢速度达到8~10m/s。进一步地,所述轧后冷却包括:以30~50℃/s的速度冷却至500~530℃。进一步地,所述卷取温度为500~530℃。进一步地,所述精轧中前三机架的冷却水开启比例≥50%。进一步地,所述将所述热轧卷进行酸洗,获得表面质量好的含b碳素结构钢酸洗板,具体包括:将所述热轧卷采用酸洗槽以150~250m/min的速度进行酸洗,后漂洗,获得表面质量好的含b碳素结构钢酸洗板;所述酸洗槽中酸的温度控制在75~90℃,酸的浓度为45~30g/l;所述漂洗中hcl浓度为0.0008~0.001g/l。本发明还提供了一种所述方法制备得到的表面质量好的含b碳素结构钢酸洗板。本发明实施例中的一个或多个技术方案,至少具有如下技术效果或优点:本发明提供的一种减少含b碳素结构钢酸洗板表面铁皮压入缺陷的方法,降低精轧入口温度(精轧入口温度为980~1000℃)有利于避开氧化增重波峰位置,减少精轧过程铁皮厚度;经试验发现:轧辊氧化膜厚度随着轧制温度的升高而增加,降低轧制温度(精轧终轧温度为880~900℃)以及开启高温段机架间冷却水(精轧中的机架的冷却水开启比例≥50%),有利于缓解轧辊结瘤物的产生;从而本发明实施例可以在不增加设备的条件下较容易的解决含b碳素结构钢酸洗板铁皮缺陷问题,提高酸洗板的表面质量;方法简单,经济高效。附图说明为了更清楚地说明本发明实施例中的技术方案,下面将对实施例描述中所需要使用的附图作一简单地介绍,显而易见地,下面描述中的附图是本发明的一些实施例,对于本领域普通技术人员来讲,在不付出创造性劳动的前提下,还可以根据这些附图获得其它的附图。图1为热卷铁皮压入缺陷宏观形貌图;图2为铁皮压入缺陷微观形貌图;图3为氧化增重曲线图;图4为轧辊氧化膜结瘤形貌图;图5为本发明实施例1提供的表面质量好的含b碳素结构钢酸洗板的图片;图6为本发明实施例提供的一种减少含b碳素结构钢酸洗板表面铁皮压入缺陷的方法的流程图。具体实施方式下文将结合具体实施方式和实施例,具体阐述本发明,本发明的优点和各种效果将由此更加清楚地呈现。本领域技术人员应理解,这些具体实施方式和实施例是用于说明本发明,而非限制本发明。在整个说明书中,除非另有特别说明,本文使用的术语应理解为如本领域中通常所使用的含义。因此,除非另有定义,本文使用的所有技术和科学术语具有与本发明所属领域技术人员的一般理解相同的含义。若存在矛盾,本说明书优先。除非另有特别说明,本发明中用到的各种原材料、试剂、仪器和设备等,均可通过市场购买得到或者可通过现有方法制备得到。本发明实施例提供的技术方案为解决上述技术问题,总体思路如下:为解决上述问题,根据本发明实施例一种典型的实施方式,提供一种减少含b碳素结构钢酸洗板表面铁皮压入缺陷的方法,如图6所示,包括:s1、获得含b碳素结构钢的铸坯;s2、将所述铸坯进行轧前加热、粗轧、精轧和轧后冷却,获得精轧板;其中,所述精轧中开启冷却水以控制位于前三道次的钢带表面温度<950℃,所述精轧入口温度为980~1000℃,所述精轧终轧温度为880~900℃;s3、将所述精轧板进行卷取,获得氧化铁皮厚度<8μm的热轧卷;s4、将所述热轧卷进行酸洗,获得表面质量好的含b碳素结构钢酸洗板。通过上述内容可以看出,本发明实施例提供的一种减少含b碳素结构钢酸洗板表面铁皮压入缺陷的方法,对含b碳素结构钢酸洗板表面存在的铁皮缺陷的原因分析,并提出本发明实施例的技术方案的总体思路为:(1)热轧轧制温度对铁皮压入的影响本发明实施例在热轧过程中控制精轧终轧温度为880~900℃,有利于钢板表面形成feo层,feo层有一定的延展性,可与基体同步变形,使得热轧过程中压入可能性降低,如热轧过程温度过高或过低,影响feo层比例,会导致精轧过程中,存在铁皮压入风险。(2)精轧入口温度对铁皮压入的影响如图3所示,针对其钢种分析氧化特性发现,温度升高至800℃以后,试样重量开始随温度增加;温度达到1026℃时氧化增重率达到高峰;随后氧化速率急剧下降,至1150-1200℃区间存在达到一个低谷;而后随温度升高氧化速率再次上升。1026℃的氧化峰值对应精轧约f1-f3附近。本发明实施例降低精轧入口温度(精轧入口温度为980~1000℃)有利于避开氧化增重波峰位置,减少精轧过程铁皮厚度。(3)精轧机架水开启比例对铁皮压入的影响经试验发现:轧辊试样表面的结瘤状氧化膜内存在大量v、cr元素的富集如图4所示,而普通氧化膜内v、cr含量较低,由此可以推断,结瘤状氧化膜形成的根本原因在于不同类似碳化物所发生的选择性氧化:富含v的mc型碳化物和富含cr的m7c3型碳化物氧化抗性最低,最容易发生氧化,因而这些区域氧化膜生长较快,会逐渐成为凸出,随着温度的升高,不同类型碳化物和钢基体的氧化速率差别进一步增大,结瘤状氧化膜表现的更为凸出,轧辊表面也变得更为粗糙。轧辊氧化膜厚度随着轧制温度的升高而增加,降低轧制温度(精轧终轧温度为880~900℃)以及开启高温段机架间冷却水(精轧中的机架f1-f3的冷却水开启比例≥50%),有利于缓解轧辊结瘤物的产生。(4)氧化铁皮厚度对铁皮压入的影响热卷铁皮较厚,若超过10微米,极其容易在拉矫或开平过程发生铁皮脱落,压入钢板表面,形成冷态铁皮压入问题。因此本发明实施例控制热轧卷厚度小于8μm。作为一种可选的实施方式,所述钢的化学成分以质量分数计为:c:0.15~0.18%,si:0.03~0.05%,mn:0.35~0.5%,p≤0.015%,s≤0.015%,al:0.04~0.06%,b:0.001~0.002%,其余为fe和不可避免的杂质。本申请经实验发现:钢种合金元素含量对铁皮液化温度存在影响,具体为:钢种中添加有一定b元素,易于造成热轧过程铁皮压入缺陷或麻点形貌,主要源自b元素在加热和热轧过程存在表面偏聚情况,富集量可达基体的5~10倍。b元素富集后,改变界面处fe2sio4的熔点,可使得界面铁皮液化温度降低到1000℃左右,而本发明实施例在成分体系中添加一定含量al元素可起到适当提高铁皮fe2sio4液化温度点的目的,避免热轧过程中发生由于铁皮液化粘附带钢表面造成无法去除,进而压入表面的情况。al元素若小于0.04%难以提高铁皮fe2sio4液化温度点;若高于0.06%易于出现铁皮压入的不利影响。作为一种可选的实施方式,所述轧前加热包括:加热段和均热段,所述加热段为以室温升温至均热温度1150~1180℃,所述均热段为在均热温度1150~1180℃下保温;所述轧前加热的总时间为130~160min。本申请经实验发现:钢种出炉温度对热卷铁皮和界面平直度存在影响,具体为:随着钢种出炉温度的升高,铁皮厚度增加,热轧过程铁皮压入几率升高。由于较厚铁皮变形能力较弱,非常容易造成除鳞不净,造成成品表面粗糙度存在差异,形成色差或粗糙感。采用低温加热(将均热温度控制在1150~1180℃),有效改善铁皮去除性和提高热轧过程铁皮变形能力。作为一种可选的实施方式,所述卷取温度为500~530℃;所述卷取温度有利于降低热卷铁皮厚度。作为一种可选的实施方式,所述轧后冷却包括:采用层冷前端冷却模式,以30~50℃/s的速度冷却至500~530℃;有利于降低热卷铁皮厚度。作为可选的实施方式之一,所述轧前加热中,控制铸坯长宽高分别为230mm×(900~2150)mm和250mm×(900~2150)mm,定尺长度为8000~105000mm,控制铸坯截面温差≤30℃。这样设置有利于保证板坯全长度、全宽度方向铁皮均匀性。作为可选的实施方式之一,所述粗轧中,采用3+3道次进行轧制,控制轧制速度为2~5mm/s,控制粗轧总变形量为80~85%,控制粗轧进口温度为1120~1140℃。这样设置有利于控制粗轧过程温降,保证精轧入口温度的命中率以及精除鳞的效果。作为可选的实施方式之一,所述精扎中,采用6道次进行轧制,控制轧制速度为8~10mm/s,控制精轧总变形量为85~92%;开启精轧双道次除鳞,精轧抛钢速度达到8~10m/s。这样设置有利于控制精轧过程钢卷表面温度和过程温降低,保证铁皮塑性变形,防止铁皮破碎压入。作为可选的实施方式之一,所述精轧中前三机架的冷却水开启比例≥50%;从而保证位于前三机架的钢板表面温度<950℃,有利于缓解轧辊结瘤物的产生。作为可选的实施方式之一,所述将所述热轧卷进行酸洗,获得表面质量好的含b碳素结构钢酸洗板,具体包括:将所述热轧卷采用酸洗槽以150~250m/min的速度进行酸洗,后漂洗,获得表面质量好的含b碳素结构钢酸洗板;所述酸洗槽中酸的温度控制在75~90℃,酸的浓度为45~30g/l;所述漂洗中hcl浓度为0.0008~0.001g/l。这样设置有利于保证酸洗效果,防止局部铁皮酸洗不净。根据本发明实施例另一种典型的实施方式,提供采用所述方法制备得到的表面质量好的含b碳素结构钢酸洗板。下面将结合实施例、对比例及实验数据对本申请的一种减少含b碳素结构钢酸洗板表面铁皮压入缺陷的方法进行详细说明。s1、将铁水经过转炉冶炼,采用连铸方式获得含b碳素结构钢的铸坯;实际化学成分如表1所示。表1-含b碳素结构钢化学成分(wt%)组别csimnpsaltb实施例10.15%0.04%0.4%0.009%0.009%0.05%0.0015%实施例20.16%0.03%0.35%0.012%0.012%0.04%0.001%实施例30.18%0.05%0.5%0.015%0.015%0.06%0.002%对比例10.15%0.04%0.4%0.009%0.009%0.02%0.0015%对比例20.15%0.04%0.4%0.009%0.009%0.05%0.0015%对比例30.15%0.04%0.4%0.009%0.009%0.05%0.0015%对比例40.15%0.04%0.4%0.009%0.009%0.05%0.0015%s2、将所述铸坯进行轧前加热、粗轧、精轧和轧后冷却,获得精轧板;其中,各组别的工艺参数具体如表2所示。表2-工艺参数s3、将所述精轧板进行卷取,获得热轧卷;各组别具体如表2所示。s4、将所述热轧卷进行酸洗,获得表面质量好的含b碳素结构钢酸洗板。对各组别含b碳素结构钢酸洗板表面的情况进行统计,结果见表3。表3组别铁皮压入缺陷的表面积百分比%实施例10%实施例20%实施例30%对比例120%对比例210%对比例315%对比例413%由表3的数据可知:对比例1中,al元素添加过少,存在表面铁皮缺陷,铁皮压入缺陷达20%;对比例2中,精轧入口温度1050℃,大于本发明实施例精轧入口温度980~1000℃;精轧终轧温度950℃,大于本发明实施例精轧终轧温度880~900℃的范围,存在表面铁皮缺陷,铁皮压入缺陷达10%;对比例3中,卷曲温度为540℃,大于本发明实施例500~530℃的范围,存在表面铁皮缺陷,铁皮压入缺陷达15%;对比例4中,机架f1-f3的冷却水开启比例为40%,小于本发明的范围,存在表面铁皮缺陷,铁皮压入缺陷达13%;实施例1-实施例3中无铁皮缺陷问题,酸洗板的表面质量好。最后,还需要说明的是,术语“包括”、“包含”或者其任何其他变体意在涵盖非排他性的包含,从而使得包括一系列要素的过程、方法、物品或者设备不仅包括那些要素,而且还包括没有明确列出的其他要素,或者是还包括为这种过程、方法、物品或者设备所固有的要素。尽管已描述了本发明的优选实施例,但本领域内的技术人员一旦得知了基本创造性概念,则可对这些实施例作出另外的变更和修改。所以,所附权利要求意欲解释为包括优选实施例以及落入本发明范围的所有变更和修改。显然,本领域的技术人员可以对本发明进行各种改动和变型而不脱离本发明的精神和范围。这样,倘若本发明的这些修改和变型属于本发明权利要求及其等同技术的范围之内,则本发明也意图包含这些改动和变型在内。当前第1页12