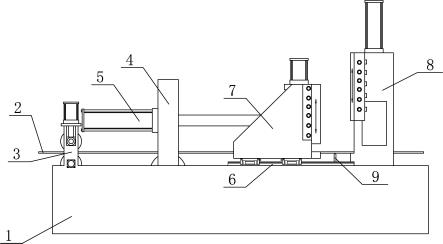
1.本发明涉及变压器制造设备技术领域,具体涉及一种不用补焊的变压器外壳挤压焊接成型机及成型方法。
背景技术:2.油浸式变压器是电力系统的重要组成部分,油浸式变压器的电力传输特性稳定,其结构简单,可靠性高,可以长期在室外的恶劣环境下使用,因此其在电力系统中占据了重要的一席。
3.油浸式变压器的油箱内盛装变压器油,变压器油承担了铁芯和绕组的散热和绝缘功能,为了使得散热面积更大,油浸式变压器的外壳多采用波纹板式,通过板材的波纹式折叠大大增加变压器油与外壳的接触面积,而为了防止绝缘油渗漏,波纹外壳边缘采取焊接进行密封,这种波纹片式外壳采用波纹成型机进行折叠挤压成型后再对边缘进行焊接,波纹成型机是变压器波纹油箱外壳的常用设备,例如中国专利文献cn 216802449u就记载了一种变压器波纹片自动生产线,通过波纹片成型机、剪断机、输送机构以及波纹片焊接机对变压器波纹油箱外壳进行自动生产。
4.但现有的波纹片生产线都存在共同的缺陷,波纹成型机通过两端夹持住板材,正中顶出折叠板,然后两端靠拢挤压板材和折叠板成型,在成型过程中容易出现波纹板边缘贴合处错缝及褶皱现象,导致后续的波纹焊接边缝存在漏焊现象,在机器生产完成后还需要人工检测补焊操作,无疑降低了设备的自动化程度,加大了生产成本。
技术实现要素:5.本发明所要解决的技术问题是提供一种不用补焊的变压器外壳挤压焊接成型机及成型方法,能够解决波纹板成型过程中的成型缺陷,避免后续机器自动焊接后还需要人工补焊。
6.为解决上述技术问题,本发明所采用的技术方案是:不用补焊的变压器外壳挤压焊接成型机,波纹片成型机和波纹片焊接机依次排列,由送料机构进行送料依次进行波纹挤压成型及边缝焊接,波纹片成型机包括底座,底座上方沿板材的送料方向依次排列有送料装置、液压缸支撑座、挤压座和承压座,压缸支撑座上设有挤压液压油缸,挤压液压油缸的活塞杆与挤压座固定连接,挤压座下方设有和底座连接的直线导轨,挤压座与直线导轨的滑块固定连接,挤压座和承压座之间设有可随着挤压座平移滑动而同步升降及平移的折叠顶板,挤压座后部设有可升降的挤压板,承压座前部设有可升降的承压板,挤压板和承压板上分别设有相对设置的挤压模和承压模,在挤压模或/和承压模两端设有对准板材边缘的对缝检测器。
7.上述的挤压液压油缸为伺服液压油缸,折叠顶板的升降及平移动作由伺服电机驱动,折叠顶板的升降及平移动作与挤压液压油缸推动挤压座的平移动作进行同步控制。
8.优选的方案中,上述的液压缸支撑座和挤压座之间设有矫直滚轮,矫直滚轮接触
板材表面,矫直滚轮由矫直电机驱动,矫直电机为伺服电机,当板材处于送料状态时,矫直电机处在跟随模式,矫直滚轮跟随板材的送料而移动,当送料完成后,承压板落下对板材折叠的后端进行夹持后,矫直电机向送料的反方向驱动达到设定扭矩后挤压板落下夹持住板材折叠的前端,随后矫直电机重新恢复跟随模式。
9.上述的挤压板下端设有与挤压座的座体底部连接的挤压座导料块,挤压座导料块中部设有向下凹陷的挤压座导料槽,挤压座导料槽宽度等于板材宽度,挤压座导料槽深度小于板材厚度,板材与挤压座导料槽滑动接触;承压座底部沿着送料方向设有承压座导料板,承压座导料板中部设有承压座导料槽,承压座导料槽宽度等于板材宽度,承压座导料板前端设有凸出的接触板,接触板位于承压板下端且接触板上表面与承压座导料槽地面平齐;挤压座导料槽和承压座导料槽的槽体水平位置和槽体底面平齐,挤压座导料块和承压座导料板的硬度大于板材硬度。
10.上述的挤压模与挤压座导料槽两端对应水平位置处设有边缝挤压槽,两端边缝挤压槽之间设有中部容纳槽;承压模与承压座导料槽两端对应水平位置处设有边缝挤压槽,两端边缝挤压槽之间设有中部容纳槽;挤压模和承压模的边缝挤压槽底面设有对缝检测器,对缝检测器表面与边缝挤压槽底面平齐,对缝检测器检测部分对准板材边缘。
11.上述的对缝检测器采用超声波换能器,在挤压模或/和承压模两端垂直方向设有多个对缝检测器,对缝检测器检测部分对准板材边缘。
12.上述的折叠顶板结构为:包括平移滑座,平移滑座内设有上下滑动接触的升降顶板,升降顶板由升降电机驱动进行升降,平移滑座由平移驱动装置上的平移电机驱动进行水平位移,升降电机和平移电机为伺服电机。
13.上述的升降顶板内设有气管,气管与升降顶板表面及顶部的导气孔联通,气管从升降顶板穿出并通过导气软管与平移滑座上的导气管连接,导气管与气泵连接,气泵通过转换方向实现向导气孔灌气或抽气;升降顶板两侧设有与平移滑座内部欢动接触的t型滑块,升降顶板表面设有升降齿条,升降齿条与升降电机驱动的升降驱动齿轮啮合。
14.上述的平移驱动装置包括与平移滑座底部滑动接触的导向滑杆,导向滑杆两端与平移支座固定连接,平移支座下端与平移底板固定连接,平移电机驱动与平移支座转动连接的平移丝杠转动,平移丝杠与平移滑座底部的平移螺母座啮合。
15.使用上述的不用补焊的变压器外壳挤压焊接成型机的成型方法,成型的步骤为:步骤一、送料装置将板材送至承压座处,使板材在挤压座和承压座上依次落入挤压座导料槽和承压座导料槽内进行对齐,挤压座和折叠顶板位于挤压起始点,升降顶板处于落下起始位置,矫直电机处于跟随模式;步骤二、从板材达到承压座处时送料装置开始进行板材送料长度检测,当达到需要进行首次折叠的距离时,承压板落下夹持住准板材的折叠后端,步骤三、矫直电机启动向送料的反方向驱动板材绷直,当矫直电机检测达到设定
的扭矩后,板材绷直完成,挤压模落下夹持住板材的折叠的前端,矫直电机回到跟随模式,升降顶板升起接触到绷直板材的下表面;步骤四、挤压液压油缸推动挤压座向后端水平移动,同时折叠顶板水平移动,升降顶板同步升起,三者处于位置同步控制状态,挤压座到达承压座处、折叠顶板到达承压座处和升降顶板到达指定的升起位置这三个动作同步完成,此时折叠后的板材边缘未受到边缝挤压槽的挤压;步骤五、气泵启动进行导气孔的排气作业,气泵达到设定的排气压力;步骤六、挤压液压油缸推动挤压座朝向承压座进行挤压作业,边缝挤压槽和中部容纳槽分别对折叠后的板材边缘和中间升降顶板与板材的组合体进行挤压成型,直到挤压液压油缸达到设定的挤压压力;步骤七、气泵反向向导气孔进行灌气,直到气泵达到设定的灌气压力,设定的灌气压力小于设定的排气压力;步骤八、升降顶板落下至起始位置后,气泵停止,承压板和挤压模升起松开对挤压成型后的板材两端的夹持;步骤九、挤压液压油缸缩回带动推动挤压座远离承压座回到挤压起始点,同时折叠顶板远离承压座回到挤压起始点,此时一个波纹板挤压成型;步骤十、送料装置再驱动板材向前移动使成型好的波纹板移动至承压板后档并使板材送料距离达到波纹板成型间隔,然后重复上述步骤二至步骤十进行后续的波纹板挤压作业;步骤十一、当成型的波纹板数量达到设定数值后,送料装置驱动成型好的波纹板材向后方移动直到达到设定的距离,承压座后端的剪切装置落下对板材进行剪切,波纹板挤压成型完成。
16.本发明提供的一种不用补焊的变压器外壳挤压焊接成型机及成型方法,通过板材加压折叠和挤压过程中的位置对齐及各部件的位移控制,使得折叠后的板材边缘精准对齐,且不产生褶皱,挤压前可以通过超声波换能器对是否对齐及是否有褶皱进行检测并发出告警,并通过挤压过程中的升降顶板的抽排气防止挤压褶皱的产生,从而使得挤压成型后的板材边缘对缝精准,使用波纹板焊接机可以精准地对挤压边缘进行焊接密封,不再需要进行人工补焊。
附图说明
17.下面结合附图和实施例对本发明作进一步说明:图1为本发明变压器外壳挤压成型机的结构示意图;图2为优选的变压器外壳挤压成型机的结构示意图;图3为本发明挤压座的结构示意图一;图4为本发明挤压座的结构示意图二;图5为图4中a-a的剖切示意图;图6为承压座的结构示意图;图7为承压座导料板的结构示意图;图8为折叠顶板的结构示意图;
图9为平移驱动装置的结构示意图;图10为平移滑座的结构示意图;图11为平移滑座的剖视图;图12为升降顶板的结构示意图;图13为挤压后的波纹板侧视图;图14为挤压后的波纹板正视图;图15为发生折叠左右移位的波纹板示意图;图16为发生挤压褶皱的波纹板示意图;图17为挤压座和承压座的作业示意图。
18.其中:底座1、板材2、边缝挤压部21、边缝接触线22、隆起容油部23、送料装置3、液压缸支撑座4、挤压液压油缸5、直线导轨6、挤压座7、座体71、挤压座导料块72、挤压座导料槽721、走料槽73、挤压板74、第一升降油缸75、挤压模76、承压座8、框体81、底板82、第二升降油缸83、承压板84、承压模85、承压座导料板86、承压座导料槽861、接触板862、折叠顶板9、平移滑座91、平移螺母座911、升降顶板92、气管921、导气软管922、导气管923、导气孔924、t型滑块925、升降齿条926、升降电机93、升降驱动齿轮94、平移驱动装置95、平移底板951、平移支座952、导向滑杆953、平移丝杠954、平移电机955、气泵96、矫直滚轮10、驱动电机11、矫直电机12、驱动油缸13、对缝检测器14、边缝挤压槽15、中部容纳槽16。
具体实施方式
19.以下结合附图和实施例详细说明本发明技术方案。
20.如图1-17中所示,不用补焊的变压器外壳挤压焊接成型机,波纹片成型机和波纹片焊接机依次排列,由送料机构进行送料依次进行波纹挤压成型及边缝焊接,波纹片成型机包括底座1,底座1上方沿板材2的送料方向依次排列有送料装置3、液压缸支撑座4、挤压座7和承压座8,压缸支撑座4上设有挤压液压油缸5,挤压液压油缸5的活塞杆与挤压座7固定连接,挤压座7下方设有和底座1连接的直线导轨6,挤压座7与直线导轨6的滑块固定连接,挤压座7和承压座8之间设有可随着挤压座7平移滑动而同步升降及平移的折叠顶板9,挤压座7后部设有可升降的挤压板74,承压座8前部设有可升降的承压板84,挤压板74和承压板84上分别设有相对设置的挤压模76和承压模85,在挤压模76或/和承压模85两端设有对准板材2边缘的对缝检测器14。
21.由于板材是由平面通过两端的靠近及中间顶出的复合动作,而两端靠近挤压动作和中间顶出依靠的是油缸推进,两者的动作位移不匹配不均匀以及板材未对齐会造成波纹板边缘贴合处出现错缝及褶皱现象,且在折叠挤压时由于板材的局部密闭使得内部的密闭气体作用于边缝,也会使边缘出现挤压褶皱。
22.在板材2送料距离到位时,挤压板74和承压板84落下夹持住板材2需要折叠焊接的部位两端,如图17中所示,假定波纹板的高度为l,及折叠后的波纹板高度为l,则夹持两端之间的距离为2l,此时折叠顶板9位于2l的中间点,折叠顶板9的顶出和向右平移随着挤压座7的向右同步动作,使得折叠顶板9始终顶住折叠的中间点,折叠顶板9的顶端与板材下端面的接触点一直为2l的中间点且不产生相对位移,则板材的折叠不会产生褶皱,从而可以防止后续的波纹片对缝焊接不完全而需要人工补焊,且对缝检测器14可以对板材边缘的折
叠效果进行检查,可以对边缘的错缝及褶皱进行预警,从而提醒进行设备检查。
23.上述的挤压液压油缸5为伺服液压油缸,折叠顶板9的升降及平移动作由伺服电机驱动,折叠顶板9的升降及平移动作与挤压液压油缸5推动挤压座7的平移动作进行同步控制。
24.通过将挤压液压油缸5采用伺服液压油缸,可以精准控制挤压座7的平移位置,且折叠顶板9的升降及平移动作与挤压座7的平移采用同步动作,如图17中所示,挤压座7的平移距离为2l,而折叠顶板9的升降及平移的距离都为l,采用同步控制后,挤压座7与承压座8接触的同时,折叠顶板9也平移和顶升到预定位置,使得挤压座7平移的同时折叠顶板9始终顶着折叠的中点防止产生褶皱。
25.优选的方案中,上述的液压缸支撑座4和挤压座7之间设有矫直滚轮10,矫直滚轮10接触板材2表面,矫直滚轮10由矫直电机12驱动,矫直电机12为伺服电机,当板材2处于送料状态时,矫直电机12处在跟随模式,矫直滚轮10跟随板材的送料而移动,当送料完成后,承压板84落下对板材2折叠的后端进行夹持后,矫直电机12向送料的反方向驱动达到设定扭矩后挤压板74落下夹持住板材2折叠的前端,随后矫直电机12重新恢复跟随模式。
26.通过承压板84夹持板材2折叠的后端,矫直电机12向反方向驱动板材2并达到设定扭矩,消除板材2由于重力和应力而产生的塌落和变形,使得板材2变得笔直,然后挤压板74落下夹持住板材2折叠的前端,此时板材2夹持的两端为标准的折叠距离,矫直滚轮10和矫直电机12使得折叠的板材长度更将精准,消除重力和板材应力变形产生的折叠误差,使得折叠后的波纹板外形精度高,波纹片成型机的重复精度和定位精度稳定,使得后端的波纹片焊接机只需要夹持住挤压后的边缝沿竖直方向进行焊接即可完全的密封边缝,不需要人工补焊。
27.上述的挤压板74下端设有与挤压座7的座体71底部连接的挤压座导料块72,挤压座导料块72中部设有向下凹陷的挤压座导料槽721,挤压座导料槽721宽度等于板材2宽度,挤压座导料槽721深度小于板材2厚度,板材2与挤压座导料槽721滑动接触;承压座8底部沿着送料方向设有承压座导料板86,承压座导料板86中部设有承压座导料槽861,承压座导料槽861宽度等于板材2宽度,承压座导料板86前端设有凸出的接触板862,接触板862位于承压板84下端且接触板862上表面与承压座导料槽861地面平齐;挤压座导料槽721和承压座导料槽861的槽体水平位置和槽体底面平齐,挤压座导料块72和承压座导料板86的硬度大于板材2硬度。
28.如图4-6中所示,通过槽体底面平齐使得板材2折叠两端的底部平齐,通过槽体水平位置对齐,使得板材2折叠两端底部水平对齐,提高折叠的对缝精度,挤压座导料块72和承压座导料板86作为常年和板材接触的部位,为磨损件,挤压座导料块72和承压座导料板86的硬度大于板材2硬度,使得板材2送料时,挤压座导料块72和承压座导料板86不易磨损,延长其使用寿命。
29.上述的挤压模76与挤压座导料槽721两端对应水平位置处设有边缝挤压槽15,两端边缝挤压槽15之间设有中部容纳槽16;承压模85与承压座导料槽861两端对应水平位置处设有边缝挤压槽15,两端边缝挤压槽15之间设有中部容纳槽16;挤压模76和承压模85的边缝挤压槽15底面设有对缝检测器14,对缝检测器14表面
与边缝挤压槽15底面平齐,对缝检测器14检测部分对准板材2边缘。
30.通过挤压模76和承压模85两端的边缝挤压槽15的挤压作用使得板材2折叠两端紧密贴合,在通过对边缝焊接实现边缘的密封,对缝检测器14贴合对折叠后的板材边缘进行举例检测,正常情况下折叠好的板材与对缝检测器14端面贴合,距离为零,当出现挤压褶皱或者折叠的边缘没有对齐使,使得板材没有与传感器端面贴合,则传感器检测出有距离值,则表示折叠出现问题,传感器将信息发送至检测装置提出告警。
31.上述的对缝检测器14采用超声波换能器,在挤压模76或/和承压模85两端垂直方向设有多个对缝检测器14,对缝检测器14检测部分对准板材2边缘。
32.如图4、图6以及图13至图15中所示,超声波换能器对准板材2边缘,即检测部分对准图15中的检测对准线,当板材折叠发生左右移位时,板材的边缘发生错位,折叠的板材两面不再对缝,边缝接触线22发生对齐挪位,则不管是左右哪个方向发生移位,两端的超声波换能器总有一端的对准部位不再贴合板材,超声波检测检测出距离值,发出告警提醒出现折叠挤压故障,对设备进行检查;如图5和16中所示,当出现挤压褶皱时,折叠板材的边缝挤压部21出现凹凸不平,使得垂直分布的超神波换能器端面不再贴合边缝挤压部21表面,超声波换能器能够检测出距离值,则发出告警提醒出现折叠挤压故障,对设备进行检查。
33.上述的折叠顶板9结构为:包括平移滑座91,平移滑座91内设有上下滑动接触的升降顶板92,升降顶板92由升降电机93驱动进行升降,平移滑座91由平移驱动装置95上的平移电机955驱动进行水平位移,升降电机93和平移电机955为伺服电机。
34.上述的升降顶板92内设有气管921,气管921与升降顶板92表面及顶部的导气孔924联通,气管921从升降顶板92穿出并通过导气软管922与平移滑座91上的导气管923连接,导气管923与气泵96连接,气泵96通过转换方向实现向导气孔924灌气或抽气;升降顶板92两侧设有与平移滑座91内部欢动接触的t型滑块925,升降顶板92表面设有升降齿条926,升降齿条926与升降电机93驱动的升降驱动齿轮94啮合。
35.如图11、12和13中所示,当进行折叠后的挤压成型时,气泵96通过导气孔924将隆起容油部23内的空气抽出,并可以带动挤压边缘处的气体均匀流动防止形成密闭气室,防止挤压时由于板材的不平整形成局部密封气室环境,挤压作用使得气室体积缩小内部压强增大形成挤压阻力,最终形成挤压褶皱;、当挤压成型后,气泵96向导气孔924内灌气方便升降顶板92下降抽出;巧妙利用升降顶板92的折叠顶升动作内置与折叠板材内成为挤压成型的模具一部分,升降顶板92被折叠的板材包围,因此在其内部布置管道可以很好地进行成型时波纹箱内的气体排除和灌气作业,防止形成挤压褶皱。
36.上述的平移驱动装置95包括与平移滑座91底部滑动接触的导向滑杆953,导向滑杆953两端与平移支座952固定连接,平移支座952下端与平移底板951固定连接,平移电机955驱动与平移支座952转动连接的平移丝杠954转动,平移丝杠954与平移滑座91底部的平移螺母座911啮合。
37.使用上述的不用补焊的变压器外壳挤压焊接成型机的成型方法,成型的步骤为:步骤一、送料装置3将板材2送至承压座8处,使板材在挤压座7和承压座8上依次落
入挤压座导料槽721和承压座导料槽861内进行对齐,挤压座7和折叠顶板9位于挤压起始点,升降顶板92处于落下起始位置,矫直电机12处于跟随模式;步骤二、从板材2达到承压座8处时送料装置3开始进行板材送料长度检测,当达到需要进行首次折叠的距离时,承压板84落下夹持住准板材2的折叠后端,步骤三、矫直电机12启动向送料的反方向驱动板材2绷直,当矫直电机12检测达到设定的扭矩后,板材2绷直完成,挤压模76落下夹持住板材2的折叠的前端,矫直电机12回到跟随模式,升降顶板92升起接触到绷直板材2的下表面;步骤四、挤压液压油缸5推动挤压座7向后端水平移动,同时折叠顶板9水平移动,升降顶板92同步升起,三者处于位置同步控制状态,挤压座7到达承压座8处、折叠顶板9到达承压座8处和升降顶板92到达指定的升起位置这三个动作同步完成,此时折叠后的板材2边缘未受到边缝挤压槽15的挤压;步骤五、气泵96启动进行导气孔924的排气作业,气泵96达到设定的排气压力;步骤六、挤压液压油缸5推动挤压座7朝向承压座8进行挤压作业,边缝挤压槽15和中部容纳槽16分别对折叠后的板材2边缘和中间升降顶板92与板材的组合体进行挤压成型,直到挤压液压油缸5达到设定的挤压压力;步骤七、气泵96反向向导气孔924进行灌气,直到气泵96达到设定的灌气压力,设定的灌气压力小于设定的排气压力;步骤八、升降顶板92落下至起始位置后,气泵96停止,承压板84和挤压模76升起松开对挤压成型后的板材2两端的夹持;步骤九、挤压液压油缸5缩回带动推动挤压座7远离承压座8回到挤压起始点,同时折叠顶板9远离承压座8回到挤压起始点,此时一个波纹板挤压成型;步骤十、送料装置3再驱动板材2向前移动使成型好的波纹板移动至承压板84后档并使板材送料距离达到波纹板成型间隔,然后重复上述步骤二至步骤十进行后续的波纹板挤压作业;步骤十一、当成型的波纹板数量达到设定数值后,送料装置3驱动成型好的波纹板材向后方移动直到达到设定的距离,承压座8后端的剪切装置落下对板材进行剪切,波纹板挤压成型完成。