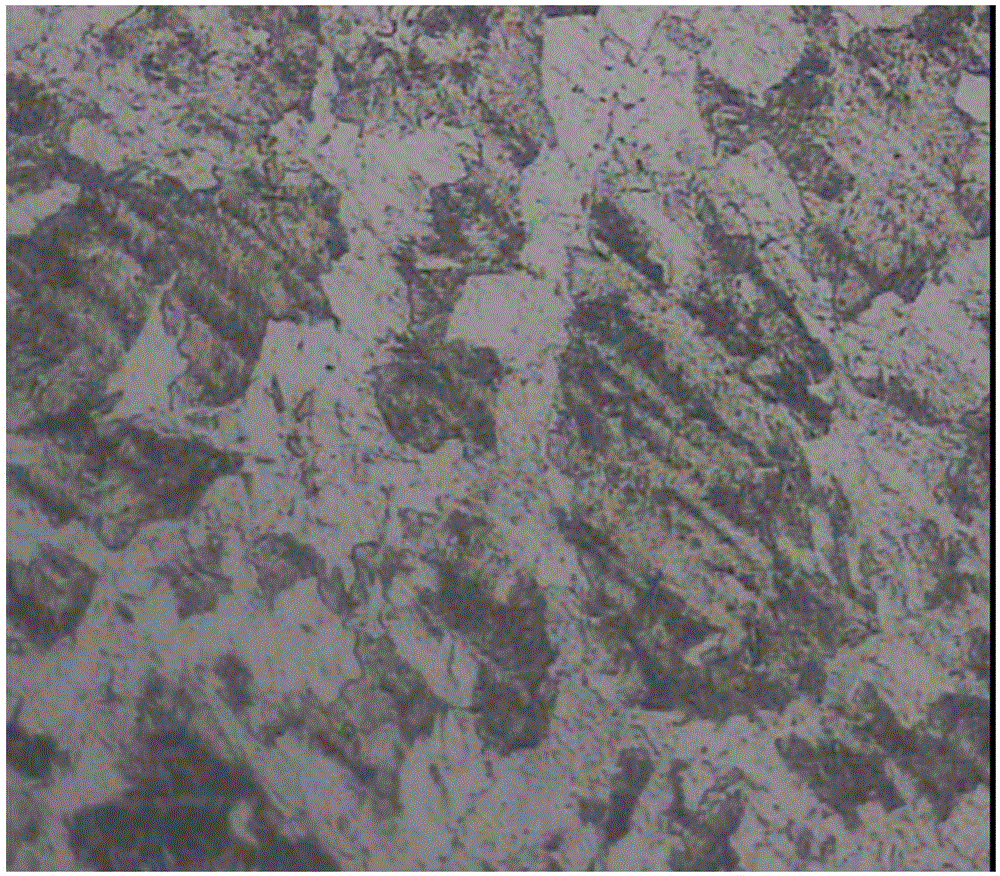
本发明涉及冶金
技术领域:
,属于合金钢类,具体涉及一种风电中间轴齿轮渗碳用钢及其制备方法。
背景技术:
:风力发电机组运转环境非常恶劣,受力情况复杂,要求所用的材料除了要满足机械强度条件外,还应满足极端温差条件下所具有的材料特性,如抗低温冷脆性、冷热温差影响下的尺寸稳定性等等。对齿轮和轴类零件而言,由于其传递动力的作用而要求极为严格的选材和结构设计,一般情况下不推荐采用装配式拼装结构或焊接结构,齿轮毛坯只要在锻造条件允许的范围内,都采用轮辐轮缘整体锻件的形式。当齿轮顶圆直径在2倍轴径以下时,由于齿轮与轴之间的连接所限,常制成轴齿轮的形式。中国专利文献CN102367549A涉及大型风力发电机齿轮用棒材及其制备方法,组分:C:0.37~0.42%,Si:0.15~0.40%,Cr:0.80~1.25%,Mn:0.50~0.90%,Mo:0.15~0.30%,S≤0.015%,Al:0.02~0.04%,O≤0.0015%,H≤0.00020%,P≤0.012%,余量为Fe和不可避免的杂质。工艺:采用EAF+LF精炼+VD真空处理冶炼,控制电炉终点碳、终点磷及出钢温度,出钢过程钢包内加入合成渣、硅锰合金、复合中铝进行预脱氧;精炼过程全程吹氩搅拌,充分进行脱氧、脱硫、去夹杂;在VD炉小于0.5乇的真空度下处理至少10分钟,破真空后喂入Al线控制钢中Al在0.02%~0.04%之间;连铸执行全保护及低过热度浇注,凝固末端采用中等强度轻压下工艺,轧制采用大压下轧制。该发明具有高纯净度和致密度的棒材,适应风电齿轮复杂而恶劣的工作环境。但是,该发明开发的齿轮钢为中碳CrMo齿轮钢,可用于生产风电齿圈,但是无法用于生产轴齿。技术实现要素:本发明针对现有技术存在的问题,提供了一种风电中间轴齿轮渗碳用钢及其制备方法。本发明风电中间轴齿轮渗碳用钢具有淬透性高和稳定、带窄,可满足高强度轴齿轮的加工及使用要求。本发明的具体技术方案如下:本发明的风电中间轴齿轮渗碳用钢,其化学成分按重量百分比计为:C:0.15%~0.21%,Si:0.17%~0.37%,Mn:0.50%~0.70%,P≤0.025%,S≤0.025%,Cr:1.50%~1.80%,Ni:1.40%~1.70%,Mo:0.25%~0.35%,Al:0.015%~0.050%,H:≤1.5×10-4%,N:≤90×10-4%,T.O:≤15×10-4%,余量为Fe及不可避免的杂质。根据本发明的渗碳用钢,其中优选地,其化学成分按重量百分比计为:C:0.17%~0.19%,Si:0.18%~0.22%,Mn:0.55%~0.65%,P≤0.015%,S≤0.010%,Cr:1.60%~1.65%,Ni:1.45%~1.48%,Mo:0.26%~0.30%,Al:0.015%~0.030%,H:≤1.5×10-4%,N:≤90×10-4%,T.O:≤15×10-4%,余量为Fe及不可避免的杂质。决定齿轮使用寿命的三大要素为:抗弯曲疲劳、抗接触疲劳、齿轮的啮合精度。齿轮材料合金元素与淬透能力的构成是决定三大要素的先决条件。齿轮钢通常为渗碳钢,较低的碳含量能保证零件心部有良好的韧性。硅(Si):在炼钢过程中加硅作为还原剂和脱氧剂。铬、锰、镍、钼的作用是增加钢的淬透性。但铬和钼为碳化物形成元素,将促使面层碳含量增加,容易在渗层组织中出现大量碳化物,使渗层性能恶化。镍使钢渗碳后各种力学性能优越,但工艺性差,锻坯渗碳后不能直接淬火,要经过再次加热淬火,工艺较复杂,且价格较贵。渗碳热处理工艺是决定齿轮质量、使用性能和使用寿命的重要工序,它决定齿轮的表面、心部硬度和金相组织、热处理后的变形和齿轮工作时齿轮的接触情况,钢材化学成分的设计应使渗碳后表面到心部碳分布平缓过度,淬火后渗碳层不出现增加脆性、使零件早期破坏的大块碳化物或网状碳化物。硅会降低渗碳层深度和表面碳含量,且在渗碳层中增加形成氧化物倾向;锰会增加渗碳层中残余奥氏体的数量;磷(P):在一般情况下,磷是钢中有害元素,增加钢的冷脆性,降低塑性,使冷弯性能变坏。P控制在P≤0.015%;硫(S):硫在通常情况下也是有害元素。使钢产生热脆性,S≤0.010%;铝是钢中常用的脱氧剂。钢中加入少量的铝,可细化晶粒,提高冲击韧性,铝还具有抗氧化性和抗腐蚀性能,铝与铬、硅合用,可显著提高钢的高温不起皮性能和耐高温腐蚀的能力。铝的缺点是影响钢的热加工性能、切削加工性能。本发明的上述渗碳用钢的制备方法,包括以下步骤:(1)电炉冶炼:热装铁水和废钢配料,热装铁水占配料质量的60~70%;控制出钢时P≤0.010%,出钢温度1630~1660℃;(2)精炼炉冶炼:控制炉渣碱度不小于2.5,精炼过程保持白渣;在白渣下充分搅拌后,取一次样全分析,根据一次样分析结果,按内控要求调整C、Si、Mn、Cr、Mo、Ni等成分含量;LF精炼炉出钢前,按0.5~1.5m/t钢喂入铝线调整控制钢中全铝含量目标在0.015%~0.030%,按照1.5~3.0m/t钢喂入钙线,白渣保持时间大于30min;(3)VD炉真空精炼:真空度小于等于67Pa保持时间≥27分钟,VD炉处理后软吹氩时间≥20分钟,VD炉软吹氩处理后控制上钢温度:连铸第一炉:1600~1605℃,第二炉:1570~1575℃,第三炉以后:1565~1570℃。(4)连铸:中间包液面800±50mm,结晶器液面波动误差在±2mm以内,钢种液相线温度1498~1509℃,中包过热度按20~30℃控制,中包第一炉:1540~1550℃,第二炉以后1525~1535℃;拉速控制:Ф500mm坯型按照0.35±0.01m/min控制;Ф650mm坯型按照0.25±0.01m/min控制;铸坯矫直温度≥950℃;铸坯缓冷要求:不能在冷床停留,要及时入坑缓冷,要轻吊轻放;缓冷制度:圆坯入坑温度大于等于650℃,出坑温度小于等于200℃,其中,Ф500mm连铸圆坯缓冷时间不小于56小时,Ф650mm连铸圆坯缓冷时间不小于96小时;(5)轧制:预热段温度600~850℃,加热段温度1100~1270℃,均热段温度1200~1240℃,允许温差≤30℃;Ф500mm冷坯加热时间7~8h,Ф500mm热坯加热时间5~6h;Ф650mm冷坯加热时间8~9h,Ф650mm热坯加热时间7~8h;开轧温度1100℃~1190℃,终轧温度900~1000℃。本发明配料优化及精炼过程合适精炼渣系解决了钢中气体含量[O]、[N]含量及纯净度的控制。轧钢过程中合适的加热时间及加热温度保证了钢材的组织均匀性及表面质量的要求。根据本发明的制备方法,其中优选地,步骤(1)在配料过程中加入石灰25~35kg/t钢,白云石4~8kg/t钢,随出钢流加入钢芯铝2.0~3.5kg/t钢,钢包合金化时按照成分下限配入合金调整,促进剂用量2.5±0.5kg/t钢。进一步优选地,步骤(1)中热装铁水占配料质量的65%~70%;在配料过程中加入石灰28~33kg/t钢,白云石5~6kg/t钢;在熔化早期喷碳粉造泡沫渣,终点碳低于0.10%时,按上限随出钢流加入钢芯铝2.5~3.0kg/t钢,钢包合金化时按照成分下限配入合金调整,促进剂用量2.5kg/t钢,控制出钢时P≤0.010%。根据本发明的制备方法,其中优选地,步骤(2)控制炉渣成分为CaO50wt%~55wt%、SiO24wt%~8wt%、Al2O320wt%~30wt%、MgO3wt%~8wt%以及FeO+MnO≤1.0wt%。进一步优选地,步骤(2)中控制精炼渣碱度大于2.5,渣成分CaO53wt%~55wt%、SiO24wt%~6wt%、Al2O320wt%~25wt%、MgO3wt%~5wt%以及FeO+MnO≤1.0wt%。根据本发明的制备方法,其中优选地,步骤(5)冷坯在600℃以下以120~150℃/h加热速度缓慢升温预热,待钢坯完全奥氏体化后,再提高加热速度,以160~200℃/h加热速度进行加热。进一步优选地,步骤(5)中加热段分段加热:预热段600~850℃,加热1段1100~1170℃,加热2段1200~1270℃;均热段温度1200~1240℃,允许温差≤30℃;Ф500mm冷坯加热时间7.5h,Ф650mm冷坯加热时间8.5h,相应的热坯加热时间降低1~2h;保证炉内弱还原性气氛;开轧温度1190℃;加强对轧制节奏的控制,保证终轧温度900~1000℃。本发明的优异效果如下:1、镍、钼、锰、铬合金的加入及合理搭配改善了材料的热处理性能;保证了材料的各项力学性能;同时增加了材料的淬透性能;满足了风电轴齿轮的性能要求。提高了齿轮的疲劳性能,提高了风电轴齿轮的使用寿命。2、发明的齿轮钢低倍组织好,纯净度高,气体含量低,晶粒细小,组织致密,带状组织级别低,末端淬透性和稳定性明显提高。改善了材料的工艺加工性能及热处理。附图说明图1为为本发明实施例1制得的齿轮钢热轧状态金相组织照片100×。图2为本发明实施例1制得的齿轮钢热轧状态金相组织照片500×。具体实施方式下面结合具体实施例对本发明做进一步说明,但本发明并不局限于此。生产工艺流程为:配料→电弧炉冶炼→LF精炼炉精炼→VD真空精炼炉精炼→圆坯连铸(Ф650mm)→连轧轧机轧制。试验生产4炉次,分别编号1#、2#、3#和4#。(1)电弧炉冶炼炉料结构为废钢+铁水,铁水比例大于60%;主要控制工艺参数列于表1。表1电弧炉冶炼主要工艺参数(2)LF精炼炉冶炼钢包底吹氩气搅拌,采用SiC扩散脱氧,喂铝线进行沉淀脱氧;造渣采用预熔渣、石灰、萤石进行调整;主要控制工艺参数见表2,终渣主要成分见表3。表2LF精炼炉冶炼主要控制工艺参数表3LF精炼炉冶炼终渣主要成分(质量百分数,%)(3)VD炉真空精炼钢包入VD炉之前,扒除50%左右的炉渣;钢包至VD炉工位后,主要控制工艺参数列于表4。表4VD炉真空精炼主要控制工艺参数(4)连铸连铸机五机五流,铸坯规格Ф650mm。连铸采用大包长水口氩封保护,中间包加低碳覆盖剂和碳化稻壳保温,中间包钢液液面770~800mm,结晶器浸入式水口保护浇注方式。液压非正弦振动;结晶器液位自动控制;采用结晶器电磁搅拌,参数210A/1.2HZ;二冷采用动态控制气一雾冷却的弱冷方式;铸坯多点矫直。连铸控制工艺参数列于表5。表5连铸控制工艺参数(5)轧制铸坯热送轧制,热送铸坯表面温度800~830℃,装入加热炉铸坯表面温度530~580℃。轧制规格Ф250mm的圆钢。轧制控制工艺参数列于表6。表6轧制控制工艺参数炉次编号均热温度,℃加热时间,h开轧温度,℃终轧温度,℃1#12007.511909402#12007.511909403#12108.511909424#12108.51180931结果数据(1)成分本实施例成分列于表7。表7本发明实施例成分(质量百分比,%)(2)轧材性能检验结果本实施例低倍、高倍检验及末端淬透性试验分别列于表8、表9和表10。表8本发明实施例的低倍检验表9本发明实施例的高倍检验表10本发明实施例的末端淬透性试验由表8~10和图1~2可以看出:本发明的风电中间轴齿轮钢低倍组织好,夹杂物级别低,气体含量低,晶粒细小,组织致密,带状组织级别低,末端淬透性明显提高和稳定等优点。本发明的渗碳用钢组织为铁素体+珠光体,组织均匀。然而,本发明并不受限于上述实施例,任何本领域技术人员在不脱离本发明的精神和范围内,都可以做出可能的变动和修改,因此本发明的保护范围应当以权利要求书中所界定的范围为准。当前第1页1 2 3