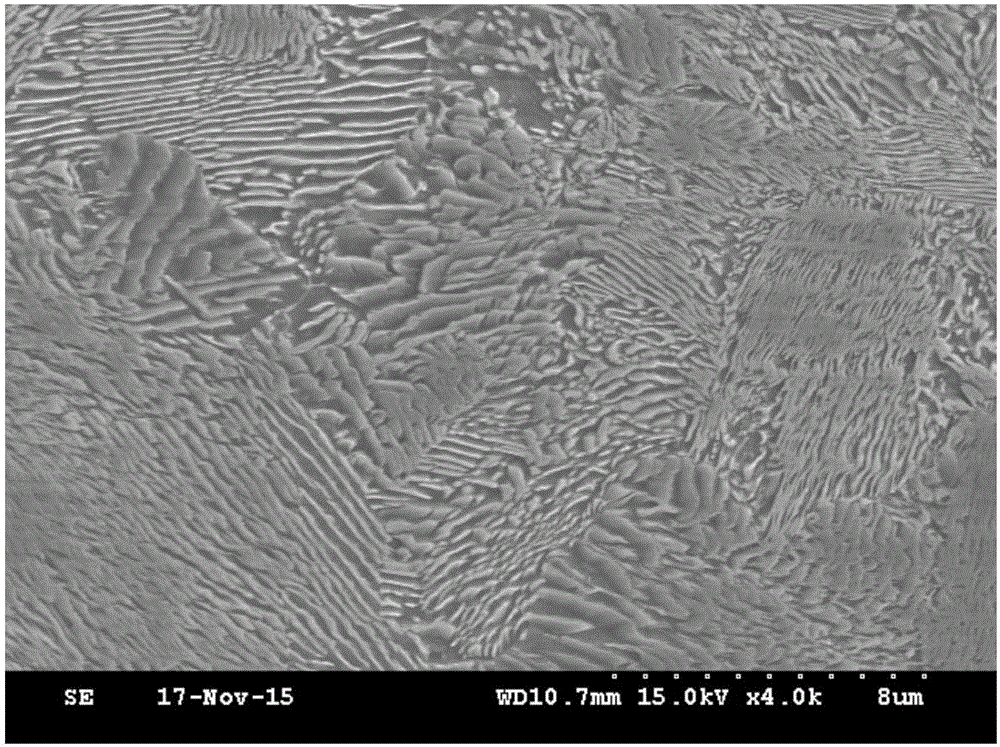
本发明属于铁路车轮用钢
技术领域:
,涉及一种具有高强度和高韧性的重载列车车轮用钢及其热处理方法。
背景技术:
:车轮是铁道和轨道交通车辆用钢的重要产品品种,近几年中国轨道交通行业得到了迅猛发展,特别是随着我国轨道交通客运高速化,货运重载化,车轮服役环境恶化,各种隐患问题日趋严重,如车轮的剥离、磨损等,已突显出现在的车轮品种无法满足目前铁路大发展的需要。重载铁路标志着一个国家的货运水平,重载铁路技术的突破,提升的不仅是物流效率,更重要的是提高了载货运输能力。目前中国铁道行业用的货车车轮的技术条件有TB/T2817-1997《铁道车辆用辗钢整体车轮的技术条件》和TB/T1013-2011《碳素钢铸钢车轮技术条件》两个行业标准。TB/T2817-1997规定的车轮钢钢种为CL60,TB/T1013-2011规定了2种车轮钢钢种:ZL-B和ZL-C。其中,ZL-B和ZL-C钢种参考了北美铁路协会标准AARM107/M208标准,与AAR-B级和C级钢的成分和硬度要求基本一致。随着我国铁路重载运输的发展,对车轮的使用性能提出了更高要求,由于轴重增加,车轮的磨损情况更为严重,因此,对车轮耐磨性能的要求不断提高。而目前使用的CL60车轮,由于碳含量较低,耐磨性能不足,已不能满足重载货车实际使用要求,而提高车轮用钢的碳含量是保证车轮耐磨性能的关键。但同时,由于碳含量的提高,车轮材料的韧性、抗热损伤性能会降低,这对车轮使用过程中的安全性也是不利的。通过微合金化处理是改善车轮用钢综合性能的手段之一,例如,中国专利CN104451401A(一种车轮用车轮钢及其制备方法)提供了一种高碳Nb微合金化车轮钢(Nb:0.02-0.04wt.%);美国专利US2015/0147224A1(Steelforwheel)提供了一种V微合金化高碳车轮钢(V:0.02-0.12wt.%)。这些专利采用了单一微合金化,没有注意到Nb、V复合微合金的匹配对于强韧性的影响;而美国专利US7559999B2(Railroadwheelsteelshavingimprovedresistancetorollingcontactfatigue)提供了一种高碳车轮钢,采用了Nb、V复合微合金化(Nb:0.01-0.12wt.%,V:0.10-0.30wt.%)设计,以提高车轮的接触疲劳性能。然而,该专利的不足之处在于V含量的设计较高,VC高温析出较多,不利于细化奥氏体晶粒、保证车轮钢珠光体组织C含量及车轮钢强度。本发明在于发现并利用了中高碳钢微Nb处理后高温相变的新特点,并协同V微合金化和Si、Cr合金化的特点,发明了一种新型的Nb-V-Si-Cr珠光体型重载列车车轮用钢,采用新的热处理方法,可以获得高强度和高韧性的优良匹配,具有良好的耐磨、抗接触疲劳、抗冷热疲劳性能。技术实现要素:本发明的目的在于提供一种高强度高韧性重载列车车轮用钢及其热处理方法。在化学成分上,采用高C、以Si、Mn、Cr、Nb、V、Al为主的合金化设计,采用多元复合微合金化的思路,重点在于Nb、V、Mn、Si、Cr元素的合理匹配,充分发挥其在车轮钢中的作用,获得以片层珠光体为主的显微组织,使车轮用钢具有高强度、高韧性和良好的延伸率等综合力学性能,具有良好的耐磨、抗接触疲劳、抗冷热疲劳等服役性能。为了达到上述技术目标,本发明的技术方案具体如下:一种高强度高韧性重载列车车轮用钢,化学成分为:C:0.75~0.85wt.%、Si:0.80~1.00wt.%、Cr:0.40~0.80wt.%、Mn:0.30~0.50wt.%、Nb:0.01~0.03wt.%、V:0.02~0.06wt.%、Al:0.010~0.025wt.%、P:<0.015wt.%、S:<0.015wt.%,余为Fe和不可避免的杂质,均为重量百分数。优选地,化学成分为:C:0.75~0.78wt.%、Si:0.80~0.90wt.%、Cr:0.40~0.55wt.%、Mn:0.30~0.42wt.%、Nb:0.01~0.018wt.%、V:0.02~0.036wt.%、Al:0.010~0.015wt.%、P:<0.015wt.%、S:<0.015wt.%,余为Fe和不可避免的杂质,均为重量百分数。优选地,化学成分为:C:0.80~0.85wt.%、Si:0.92~1.00wt.%、Cr:0.58~0.80wt.%、Mn:0.45~0.50wt.%、Nb:0.023~0.03wt.%、V:0.042~0.06wt.%、Al:0.022~0.025wt.%、P:<0.015wt.%、S:<0.015wt.%,余为Fe和不可避免的杂质,均为重量百分数。进一步地,提供一种制造上述重载列车车轮用钢的热处理方法,将车轮装入真空炉或气氛保护炉中加热,加热温度为820-900℃,保温时间为1-2小时,出炉后采用踏面淬火、分段冷却的方式,首先采用喷水冷却的方式,控制踏面冷却速度为15-30℃/s;当踏面冷却至600-650℃区间后,再采用喷雾冷却的方式,控制踏面冷却速度为3-8℃/s,连续冷却至400℃以下后进行空冷至室温,然后在真空炉或气氛保护炉中进行回火处理,回火温度为500-520℃,保温时间为1-2小时,回火后空冷到室温。优选地,高强度高韧性重载列车车轮用钢采用铁路整体碾压车轮的生产方法制造,采用转炉或电炉冶炼,炉外精炼后连铸或模铸,铸坯经开坯后进行车轮锻轧,加热温度为1250-1300℃,锻轧后空冷,热处理时采用踏面淬火热处理装备。优选地,将车轮装入真空炉或气氛保护炉中加热,加热温度为820-845℃,保温时间为1.5-2小时,出炉后采用踏面淬火、分段冷却的方式,首先采用喷水冷却的方式,控制踏面冷却速度为15-20℃/s;当踏面冷却至600-620℃区间后,再采用喷雾冷却的方式,控制踏面冷却速度为3-5℃/s,连续冷却至380℃以下后进行空冷至室温,然后在真空炉或气氛保护炉中进行回火处理,回火温度为500-505℃,保温时间为1.5-2小时,回火后空冷到室温。优选地,将车轮装入真空炉或气氛保护炉中加热,加热温度为850-890℃,保温时间为1-1.5小时,出炉后采用踏面淬火、分段冷却的方式,首先采用喷水冷却的方式,控制踏面冷却速度为25-30℃/s;当踏面冷却至625-650℃区间后,再采用喷雾冷却的方式,控制踏面冷却速度为6-8℃/s,连续冷却至400℃以下后进行空冷至室温,然后在真空炉或气氛保护炉中进行回火处理,回火温度为510-520℃,保温时间为1-1.5小时,回火后空冷到室温。优选地,热处理后轮辋进行标准拉伸试验位置的组织为全片层珠光体组织,珠光体团尺寸2-6μm,珠光体片层间距0.05-0.09μm。优选地,本发明所涉及的高强度高韧性重载列车车轮用钢采用铁路整体碾压车轮的常规生产方法制造。本发明各元素的作用及配比依据如下:碳:C是关系车轮钢强韧性、耐磨性等的主要元素。随着含C量的提高,强度提高,耐磨性提高,韧性和抗热损伤性能降低。但是,重载车轮最关键的指标是高耐磨性,因此本发明钢的碳含量采用高C成分设计以保证高强度、高硬度,碳含量定为0.75~0.85wt.%。在此碳含量范围下的低合金钢本质上为过共析钢,很容易出现网状渗碳体。如何采用新颖的成分设计以及热处理方法、避免网状渗碳体是本发明要解决的主要问题之一。硅:钢中脱氧元素之一,具有显著的固溶强化和细化珠光体片层间距的作用,从而能显著提高车轮钢的强度和硬度;Si提高淬透性,但提高程度并不十分显著;Si还能显著提高加热过程中奥氏体的开始形成温度。因此,在重载车轮钢中可以适当提高Si含量增加耐磨性和抗冷热疲劳性能,但过量的Si将恶化钢的韧性,增加车轮踏面淬火时的马氏体层厚度。本发明钢的Si含量控制在0.80~1.00wt.%。铬:Cr显著提高钢的淬透性,显著细化珠光体的片层间距,提高车轮钢的强度和硬度;Cr能溶入渗碳体中形成合金渗碳体,使珠光体组织更稳定;Cr还提高加热过程中奥氏体的开始形成温度;因此,提高Cr含量还有利于提高车轮踏面的抗剥离性能和抗冷热疲劳性能。本发明钢的Cr含量控制在0.40~0.80wt.%,突破了车轮钢相关标准的Cr含量成分上限。锰:钢中的脱氧元素之一,具有固溶强化和细化珠光体片层间距的作用,提高车轮钢的强度和硬度。Mn显著提高钢的淬透性,也显著降低加热过程中奥氏体的开始形成温度。本发明钢主要采用Si、Cr合金化方法,因此,Mn含量控制在较低的范围,为0.30~0.50wt.%,有利于提高车轮的抗冷热疲劳性能。铌:中高碳钢中进行Nb微合金化,大部分的Nb将在高温奥氏体相区以NbC形式析出,起细化奥氏体晶粒的作用,从而细化珠光体块、团尺寸。高温奥氏体化时固溶Nb含量为5-10ppm量级,但显著提高共析碳含量。Nb微合金化促使中高碳钢连续冷却过程中的高温相变曲线向右上方移动。本发明利用微量Nb提高共析碳含量的特点,与高C设计、较高的Si、Cr合金化匹配,可以获得高强度高韧性匹配的细晶细片层珠光体型车轮钢,无网状渗碳体。本发明钢的Nb含量控制为0.01~0.03wt.%,过高的Nb含量会导致NbC析出温度升高从而粗化,不利于对奥氏体晶粒的细化。过低的Nb含量也不利于细化奥氏体晶粒。钒:中高碳钢中的微合金V在高温奥氏体化时部分析出以外,还有相当部分以固溶形式存在,在后续的相变过程中细化珠光体片层间距,并以相间析出的形式析出,具有沉淀强化作用,提高抗接触疲劳性能。高温析出的VC也具有一定的沉淀强化效果,但其主要作用是细化奥氏体晶粒,从而细化珠光体块、团尺寸,获得高强度高韧性匹配。本发明钢V含量控制在0.02~0.60wt.%,主要发挥VC的沉淀强化作用,并与Nb复合,增强细晶作用。但过高的V含量会导致VC析出温度过高、析出量过多、粒子尺寸粗大,从不利于细化奥氏体晶粒和保证珠光体组织的C含量,对车轮钢的强度、耐磨性等不利。过低的V,以上作用都不明显。铝:铝是强脱氧元素,还可与N结合形成AlN,能够起到细化晶粒作用。本发明钢中的铝含量控制在0.010~0.025wt.%。磷和硫:钢中杂质元素,显著降低塑韧性,其含量控制在0.015wt.%以内。本发明的优点在于:采用新型的高C含量、Nb、V复合微合金化、较高Si、Cr合金设计,辅以踏面淬火、分段冷却的新型热处理工艺方法,可以减少踏面淬火马氏体层,从而减少车轮的加工量。本发明车轮成品具有比传统车轮更细的珠光体片层间距和更小的珠光体团尺寸,强韧塑性优异匹配,具有高耐磨性、良好的抗接触疲劳和冷热疲劳等服役性能。附图说明下面结合附图和实施例对本发明进一步说明。图1为实施例1#热处理后组织的OM照片。图2为实施例1#热处理后组织的SEM照片。具体实施方式下面将对本发明实施例中的技术方案进行清楚、完整的描述,显然,所描述的实施例仅仅是本发明中很小的一部分,而不是全部的实施例。基于本发明中的实施例,本领域普通技术人员在没有做出创造性劳动前提下所获得的所有其他实施例,都属于本发明保护的范围。本发明钢均由转炉冶炼,其中1#~3#为实施例,对比例为常规高碳车轮钢,化学成分如表1所示。实施例与对比例经冶炼、浇铸、锻轧后,在真空炉中加热至860℃,保温2h,随后采用踏面淬火、分段冷却的方式,首先喷水冷却至620℃,然后喷雾冷却至380℃,然后空冷至室温。回火处理时的回火温度520℃,保温时间2h,回火后空冷至室温。热处理后均获得片层珠光体组织,图1和图2分别为实施例1#热处理后轮辋组织的OM和SEM照片,实施例轮辋进行标准拉伸试验位置处较对比例具有更细的珠光体片层间距和更小的珠光体团尺寸(见表2),其中珠光体团尺寸2-6μm,珠光体片层间距0.05-0.09μm。热处理后的轮辋的室温拉伸性能和辐板的20℃冲击性能在表2中列出,其中实施例1#~3#钢均获得轮辋抗拉强度1200MPa以上、辐板室温冲击功20J以上的良好综合力学性能,强韧性都优于低Cr无Nb、V添加的对比例。表1化学成分(wt.%)编号CSiMnSPCrNbVAl1#0.750.920.420.0080.0070.750.0220.0350.0122#0.80.810.340.010.0140.510.0160.0420.0123#0.840.80.480.00770.0110.420.0250.060.018对比例0.730.880.860.0110.0120.17-0.0050.016表2轮辋室温拉伸性能和辐板20℃冲击性能以及轮辋组织的珠光体团尺寸和片层间距以上所述,仅为本发明较佳的具体实施方式,但本发明的保护范围并不局限于此,任何熟悉本
技术领域:
的技术人员在本发明揭露的技术范围内,可轻易想到的变化或替换,都应涵盖在本发明的保护范围之内。当前第1页1 2 3