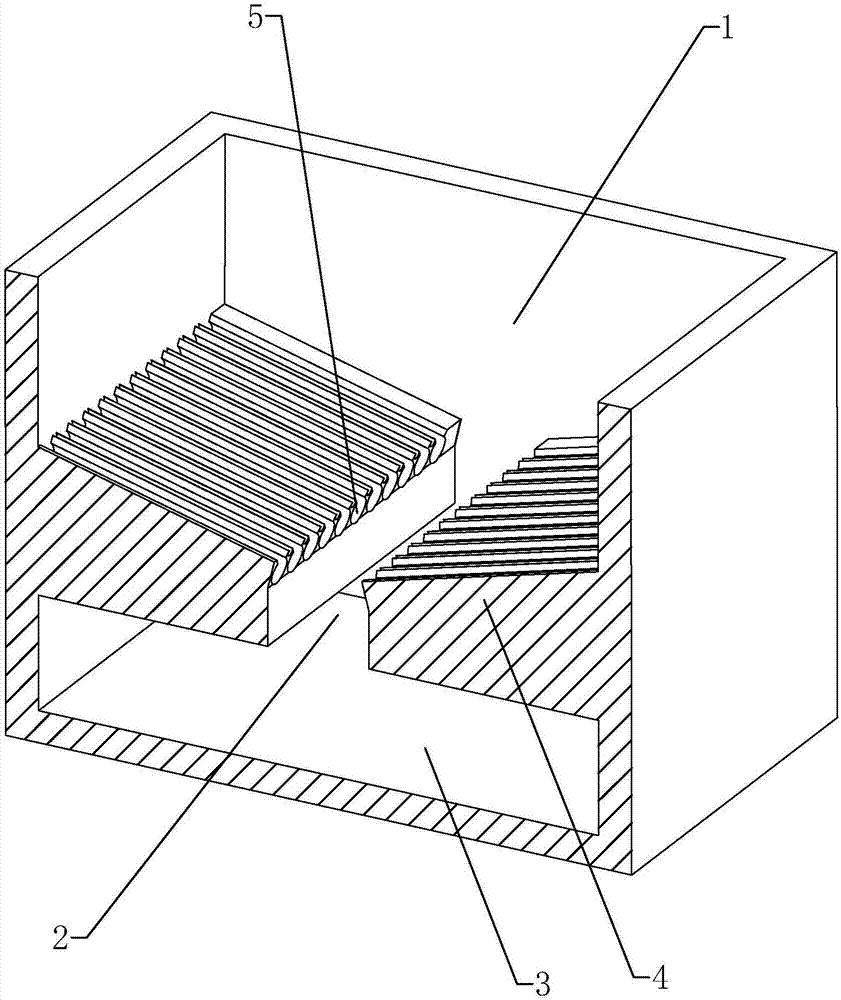
本发明涉及钢材处理
技术领域:
,特别涉及一种用于热镀锌工艺的热镀池及热镀锌工艺。
背景技术:
:热镀锌也叫热浸锌和热浸镀锌,是一种有效的金属防腐方式,主要用于各行业的金属结构设施上。是将除锈后的钢件浸入熔融的锌液中,使钢构件表面附着锌层,从而起到防腐的目的。热镀锌工艺中,热镀锌钢构件因锌渣造成的表面缺陷是热镀锌钢构件最重要的问题。生产过程中,一定数量的fe与zn反应会产生fezn7,它的熔点为640℃,高于锌液的温度,比重为7.25g/cm3,由于其比重比zn大,因此会落入锌液底部形成我们通常所说的底渣,其大小换算成球形的直径为5-300μm。如果镀槽内熔融金属不流动、处于静止状态,这些锌渣就会堆积在镀槽的底部。但是由于钢构件的运行和镀槽内镀液中辊子的转动,或者要通过熔解锌锭补充附着在钢构件上被带走的施镀金属,会产生熔融金属的自然对流等,使镀槽内的熔融金属受到搅拌。其结果是,与熔融金属比重差小的锌渣不堆积在底部,或堆积的锌渣被卷起附着在钢构件上,成为热镀锌钢构件的表面缺陷。不但会造成大量的浪费而且会严重影响钢构件的表面及性能。现有技术中,提出了很多去除锌渣的提议,这些提议中有把熔融锌浴抽到镀槽外使锌渣沉淀的方法、过滤的方法等。关于这些沉淀分离的方法,设计的装置要使熔融锌在向镀槽外输送过程中不凝固是非常重要的,此外必须在设备设计时考虑到熔融锌从输送管道泄漏的情况,所以设备上需要加大成本,所以可行性不高。技术实现要素:本发明的目的一是提供一种用于热镀锌工艺的热镀池,其解决了现有热镀池中在镀锌过程中,锌渣被水流卷起并附着在钢构件表面成为热镀锌钢构件的表面缺陷的问题,具有减少锌渣被水流卷起的可能,从而减少钢构件的表面缺陷的优点。本发明的上述技术目的是通过以下技术方案得以实现的:一种用于热镀锌工艺的热镀池,热镀池内设有用于承接锌渣的承接部,承接部上设有若干用于承接锌渣的第一承接腔,第一承接腔在垂直于承接部的方向上的截面为弧形,第一承接腔上设有开口,第一承接腔在开口处的曲率圆的圆心位于朝向第一承接腔内部一侧。采用上述方案:生成的锌渣沉到承接部上,并从开口掉落至第一承接腔内,当锌渣在水流的作用下被带动向上移动,由于第一承接腔在开口处的曲率圆的圆心位于开口处朝向第一承接腔内部一侧,开口相对于第一承接腔来说有向内包的趋势,锌渣沿着第一承接腔的内表面移动的过程中,在开口附近,锌渣向上移动的趋势较小,从而具有一定的回落的趋势,减少锌渣向开口外流出的可能,从而将大部分锌渣围在第一承接腔的范围内,减少锌渣向上扩散从而附着在钢构件表面成为热镀锌钢构件的表面缺陷的可能。进一步优选为:第一承接腔在垂直于承接部的方向上的截面为圆弧形或椭圆弧形,圆弧形为优弧,椭圆弧形为大于半椭圆,开口位于第一承接腔的正上方。采用上述方案:圆弧形或椭圆弧形结构简单,制造方便。进一步优选为:第一承接腔为依次紧密排列于承接部的、截面为椭圆弧形的柱型腔,第一承接腔的短轴垂直于承接部,第一承接腔的长轴平行于承接部。采用上述方案:椭圆弧形的设置能够使得开口处更加平坦,有利于将被卷起的锌渣包覆在第一承接腔内。进一步优选为:相邻两个第一承接腔的连接处上方设有第二承接腔,第二承接腔为截面为椭圆弧形的柱型腔。采用上述方案,第二承接腔填补了第一承接腔的开口之间的空档,进一步将锌渣收纳,阻止锌渣掉落在第二承接腔之间的平台上,从而进一步减少锌渣向上扩散从而附着在钢构件表面成为热镀锌钢构件的表面缺陷的可能。进一步优选为:第一承接腔的开口处设有导板,导板为倾斜的斜面,从开口处向上不断张开;导板的上端面与第二承接腔的开口平齐。采用上述方案,导板的设置在不扩大第一承接腔的开口的情况下,能够承接更多的锌渣收纳到第一承接腔内并在一定程度上将其限制在第一承接腔内,进一步减少锌渣向上扩散从而附着在钢构件表面成为热镀锌钢构件的表面缺陷的可能。进一步优选为:热镀池包括从上至下依次设置的活性池、连接部和沉淀池,连接部竖直设置并连接活性池和沉淀池的中部,活性池的底部为承接部,承接部从两侧向连接部不断下降,第一承接腔和第二承接腔的长轴方向朝向连接部设置。采用上述方案,沉积在第一承接腔和第二承接腔内的锌渣会沿着承接部的斜面向下掉落至连接部,并通过连接部掉落到沉淀池,并沉积在沉淀池的底部,连接部处比较狭窄,可以将掉落在沉淀池内的锌渣阻挡在沉淀池内,从而进一步减少锌渣向上扩散从而附着在钢构件表面成为热镀锌钢构件的表面缺陷的可能。本发明的第二目的是提供一种热镀锌工艺。本发明的上述技术目的是通过如下技术方案得以实现的:一种热镀锌工艺,包括如下步骤:s1:将钢构件置于酸池中除去表面的铁锈,并在水中漂洗除去酸液;s2:将钢构件转移至助镀池中的助镀液内,65-68℃的条件下浸泡;s3:将钢构件转移至如权利要求1-6所述的热镀池上方,控制热镀池内的温度为435-450℃,用捞渣勺将热镀池内的浮渣捞去,将钢构件放入热镀池中的熔融锌液中,同时开启风机将热镀池上方的沿其吹散,之后将钢构件从热镀池中取出,并用敲击的方式除去钢构件表面未成型的锌液滴;s4:将钢构件放入冷却池冷却后再放入钝化池钝化,即完成热镀锌工艺。采用上述方案,首先在酸池中除去钢构件表面的铁锈,再在助镀池内经过活化处理,一方面提高钢构件的表面活性,另一方面减少表面氧化,在热镀之前用捞渣勺将热镀池内的浮渣捞去,有利于减少浮渣附着在钢构件表面成为热镀锌钢构件的表面缺陷的可能。热镀池的结构设置有利于将大部分锌渣围在第一承接腔和第二承接腔的范围内,减少锌渣向上扩散从而附着在钢构件表面成为热镀锌钢构件的表面缺陷的可能。有利于提高钢构件的表面性能和强度。最后经钝化,在钢构件表面形成一层保护膜。进一步优选为:步骤s2中的助镀液包括如下含量的原料:氯化锌:60-120g/l;稀土氯化物:10-20g/l;钼酸锌:60-120g/l;edta:10-30g/l;螯合剂:10-30g/l;氟系表面活性剂:5-15g/l;余量为水;螯合剂为二乙醇胺和三乙醇胺中的一种或两种。采用上述方案,与传统的助镀液相比,不使用氯化铵,从而不会在助镀池上方形成白色的烟气,从而减少烟气重新结合生成的小颗粒掉落至热镀池形成的浮渣小颗粒。氯化锌、稀土氯化物和钼酸锌充当成膜剂,在钢构件表面形成一层盐膜,将钢构件的表面与空气隔开,阻止氧化;当钢构件移动至热镀池后,在高温作用下,盐膜受热熔融,使钢制件表面具有活性作用和湿润能力,使得锌液能够顺利地镀在钢制件的表明。螯合剂和edta的分子链上均有氨基和羟基(edta为羧羟基),能够在钢制件的表面与铁离子形成螯合作用,从而在钢制件的表面形成稳定的保护膜,另一方面,钼酸锌中的钼酸根离子与氯离子之间具有竞争吸附作用,钼酸根能够吸附在钢制件表面的膜缺陷处,使形成的保护膜更加完整。保护膜的存在有利于减少钢构件表面的氧化,从而减少因氧化物与锌液中的铝反应产生的锌渣量。进一步优选为:稀土氯化物为氯化镧、氯化钇、氯化铈中的一种。进一步优选为:edta和螯合剂的添加比为1:3。采用上述方案,当edta和螯合剂的添加总量不变的情况下,edta和螯合剂的添加比为1:3时具有最好的助镀效果。综上所述,本发明具有以下有益效果:1、设计热镀池的结构,将热镀池分成活性池、连接部和沉淀池,并且活性池的底部设有第一承接腔和第二承接腔,第一承接腔和第二承接腔的形状设置有利于将锌渣包裹在第一承接腔和第二承接腔内,阻止其随液态锌流动至钢构件表面,从而在钢构件表面形成缺陷,处于第一承接腔和第二承接腔内的锌渣会在倾斜表面上滚落至沉淀池内,进一步阻止其随液态锌流动至钢构件表面,减少由于锌渣引起的钢构件表面缺陷;2、助镀液的配方优化有利于在钢制件表面形成完整的保护膜,保护膜的存在有利于减少钢构件表面的氧化,从而减少因氧化物与锌液中的铝反应产生的锌渣量,进一步减少钢构件的表面缺陷。附图说明图1是实施例1的剖面示意图;图2是实施例1的结构示意图(剖去一个侧壁);图3是实施例1的立体结构示意图(剖去一个侧壁和一半的热镀池);图4是实施例1的图3中a部局部放大图,示出了第一承接腔、第二承接腔和导板的结构;图5是实施例1的第一承接腔、第二承接腔和导板的截面结示意图;图6是实施例2的第一承接腔、第二承接腔和导板的截面结示意图。图中,1、活性池;2、连接部;3、沉淀池;4、承接部;5、第一承接腔;6、第二承接腔;7、导板。具体实施方式以下结合附图对本发明作进一步详细说明。本具体实施例仅仅是对本发明的解释,其并不是对本发明的限制,本领域技术人员在阅读完本说明书后可以根据需要对本实施例做出没有创造性贡献的修改,但只要在本发明的保护范围内都受到专利法的保护。实施例1:一种用于热镀锌工艺的热镀池,结合图1和图2,包括从上至下依次设置的活性池1、连接部2和沉淀池3,活性池1和沉淀池3为长方体。连接部2竖直设置并连接活性池1和沉淀池3的中部,活性池1的底部为承接部4,承接部4从活性池1的两侧向连接部2不断下降。结合图3和图4,承接部4上设有若干用于承接锌渣的第一承接腔5。第一承接腔5为柱形腔,第一承接腔5的轴向沿着承接部4的倾斜方向设置,轴向上靠近连接部2的一端敞口,从而第一承接腔5与连接部2连通。不同的第一承接腔5之间依次紧密排列。第一承接腔5的截面为优弧形,第一承接腔5的正上方设有开口。结合图3和图4,相邻两个第一承接腔5的连接处上方设有第二承接腔6,第二承接腔6同样为优弧形的柱型腔,第二承接腔6的正上方设有开口。第一承接腔5的开口处设有导板7,导板7为倾斜的斜面,从开口处向上不断张开。导板7的顶端与第二承接腔6的开口齐平。实施例2:一种用于热镀锌工艺的热镀池,对比图5与图6,与实施例1的区别在于,第一承接腔5和第二承接腔6的截面均为椭圆弧形,椭圆弧形为大于半椭圆,第一承接腔5和第二承接腔6的的短轴垂直于承接部4,长轴平行于承接部4,开口位于第一承接腔5的正上方。实施例3:一种热镀锌工艺,包括如下步骤:s1:将钢构件置于酸池中除去表面的铁锈,并在水中漂洗除去酸液;s2:将钢构件转移至助镀池中的助镀液内,65-68℃的条件下浸泡10-120min,根据铁锈的数量来调节浸泡的时间;s3:将钢构件转移至实施例2的热镀池上方,控制热镀池内的温度为440℃,用捞渣勺将热镀池内的浮渣捞去,将钢构件放入热镀池中的熔融锌液中热镀30-200s(根据需要的厚度来调节时间),同时开启风机将热镀池上方的烟气吹散,之后将钢构件从热镀池中取出,并用敲击的方式除去钢构件表面未成型的锌液滴;s4:将钢构件放入冷却池冷却后再放入钝化池钝化,即完成热镀锌工艺。其中助镀池中的助镀液包括如下含量的原料:氯化锌:80g/l;稀土氯化物:10g/l;钼酸锌:100g/l;edta:10g/l;螯合剂:30g/l;氟系表面活性剂:10g/l;余量为水;螯合剂为二乙醇胺;稀土氯化物为氯化铈。实施例4-14:一种热镀锌工艺,与实施例3的区别在于,助镀池中的助镀液中的组分和含量不同。实施例3-14的助镀池的组分和含量参见表1。表1助镀池的组分和含量表实施例15:一种热镀锌工艺,与实施例3的区别在于,螯合剂为三乙醇胺。实施例16:一种热镀锌工艺,与实施例3的区别在于,稀土氯化物为氯化镧。实施例17:一种热镀锌工艺,与实施例3的区别在于,稀土氯化物为氯化钇。实施例18:一种热镀锌工艺,与实施例3的区别在于,步骤s3中,热镀池采用实施例1的热镀池。为了更好地探究实施例的效果,制备如下对比例作为对照。对比例1:一种热镀锌工艺,与实施例3的区别在于,步骤s3中,热镀池的形状为长方体。试验部分将同一规格的若干钢构件分别采用实施例3-18、对比例1的热镀锌工艺进行热镀锌操作。在操作过程之前预先在热镀池中均匀撒入等量的5-300μm的fezn7底渣,这些底渣收集自热镀锌产线;在操作之前对热镀池辅助震荡,震荡的方式是采用一个与试验用的钢构件相同规格的钢构件在热镀池内提拉三次,再进行热镀锌操作,对比钢构件表面的缺陷情况。洒入底渣和震荡操作的目的均为增大锌渣对钢构件表面的影响,放大不同热镀锌工艺制备得到的钢构件表面粗糙度之间的区别。经过热镀锌工艺的钢构件的表面粗糙度采用time3200便携式粗糙度仪,每个试验样做3组平行试验,每个平行试验在对应位置取3个测试点,粗糙度取9个测点的平均值。每个试验样对应的平均粗糙度参见图2。图2不同试验样的粗糙度汇总表试验样粗糙度/μm试验样粗糙度/μm试验样粗糙度/μm实施例30.921实施例91.032实施例150.908实施例41.013实施例100.986实施例161.023实施例50.809实施例111.021实施例170.996实施例60.783实施例121.098实施例181.204实施例70.976实施例131.117对比例11.527实施例80.997实施例140.876当前第1页12