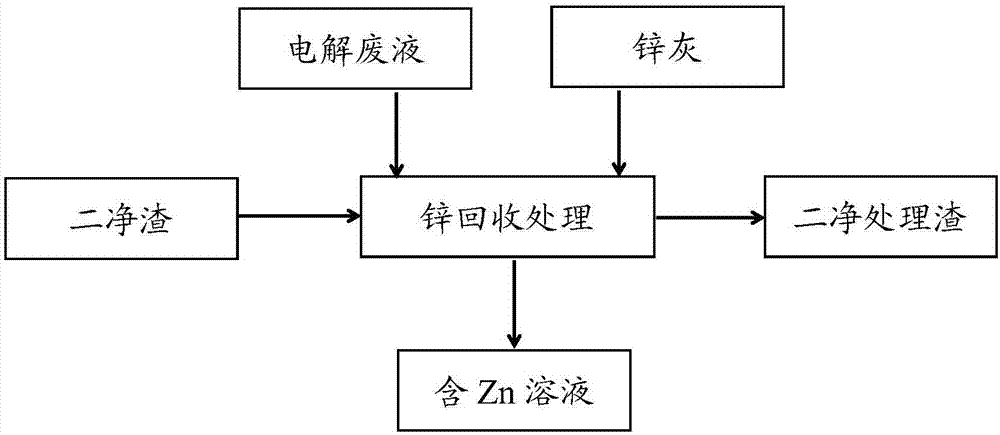
本发明属于冶金
技术领域:
,尤其涉及一种浸出渣回收锌工艺。
背景技术:
目前锌冶炼投产,弥补了对锌回收的空缺。在原有的工艺中,炼锌产出的铅渣、铁渣、锌镉渣没有做任何处理全部送回冶炼铅系统,以上渣料因含有一定的锌,特别二净渣含锌约50%,而对炼锌系统的直收率造成很大的影响。并且,随着冶炼的持续生产,二净渣越来越多,由于二净渣仅是以添加剂的形式进入炼铅系统,不仅造成大量有价金属流失,还污染环境。如果将二净渣送到冶炼铅系统,对锌系统来说损失了二净渣中50%的锌,如果回收这部分锌,直收率可提高1~2个百分点。同时由于锌的回收,渣量减半,一是渣场相对变大,二是与铅系统消耗量匹配。即解决了当今严峻的环保问题,又能满足铅冶炼系统的需求。所以二净渣的锌回收处理是冶炼系统中不可缺少的部分。技术实现要素:有鉴于此,本发明针对现有技术中存在的问题,提供一种浸出渣回收锌工艺。为了实现上述目的,本发明的技术方案如下:一种浸出渣回收锌工艺,所述回收锌工艺具体包括如下步骤:步骤一:将电解废液注入处理罐中,边搅拌边缓慢加入二净渣;步骤二:待步骤一中的二净渣加入1/3电解废液量时,测定反应混合液ph值;步骤三:待步骤二中混合液的ph值为3.5~4.5时,停止加入二净渣,反应25~35min,取样分析合格后压滤,滤液泵入锌制液系统。以上所述的浸出渣回收锌工艺,原理:1、二净渣中金属锌与电解液中的硫酸发生置换反应;2、溶出的镉与二净渣中金属锌或锌灰进行置换反应。其中,反应方程式如下:zn+h2so4=znso4+h2↑cd2++zn=zn2++cd通过采用上述技术方案,本发明的有益效果如下:本发明采用电解液废液浸出二段净化渣具有工艺简单可靠,与锌生产主流程结合好,锌镉分离效果好。二段净化渣中有98%以上的锌得到了回收,可使炼锌系统直收率提高2%,且本发明既提高了金属回收率,又减少了二段净化渣对环境的污染。另外,本发明通过采用二净渣本身含的金属锌或锌灰去除掉镉,较直接运用锌粉除镉,既减少和净化废渣,又降低了生产成本,其在行业上具有良好的推广示范作用。优选的,步骤一中,电解废液的加入量为50~60%,且所述电解废液中硫酸的浓度为140~150g/l。优选的,步骤一中,控制所述二净渣和所述电解废液的固液比为1:3~5。优选的,步骤二中,控制二净渣和电解废液反应过程中的ph≥3.5,反应终点的ph为3.5~4.5。发明人通过创造性试验得到浸出渣回收锌工艺的最佳工艺条件为:二净渣和电解废液的固液比为1:3~5,电解废液中硫酸的浓度为140~150g/l,反应过程中的ph≥3.5,反应终点的ph为3.5~4.5。因为二净渣浸出回收锌工艺其核心问题是二净渣中还没有反应完的金属锌粉与酸发生置换反应,使金属锌以硫酸盐的形态存在,金属锌与硫酸的量要适宜,酸少则锌反应不完全;酸过量则二净渣的其它杂质被浸出,这会增加系统的生产成本。所以此工艺关键技术控制好ph值,即通过调控二净渣和电解废液的固液比得到反应体系最佳ph值为3.5-4.5。优选的,步骤三中,分析合格样品中cd2+浓度低于1g/l,zn2+浓度在98~100g/l之间。优选的,cd2+浓度高于1g/l时,在反应体系中继续加入二净渣或锌灰以使cd2+浓度低于1g/l。本发明中,二净渣具有一定杂质镉,镉在酸性中很容易浸出来,以geso4盐的形式存在,返回到生产系统时会增加锌粉用量而增加生产成本,在回收处理工艺中,需采取低于生产成本即用二净渣本身含的金属锌或价值低于锌粉的锌灰去除掉镉。经由上述的技术方案可知,与现有技术相比,本发明提供了一种浸出渣回收锌工艺,通过将电解废液注入处理罐中,边搅拌边缓慢加入二净渣,且将反应体系ph值控制在3.5~4.5,反应25~35min,取样分析合格后压滤,滤液泵入锌制液系统。本发明不仅能够大大提高炼锌系统直收率,同时减少和净化废渣,而且通过采用二净渣本身含的金属锌或价值低于锌粉的锌灰去除掉镉。本发明所公开的浸出渣回收锌工艺在行业上有良好的推广示范作用。附图说明为了更清楚地说明本发明实施例或现有技术中的技术方案,下面将对实施例或现有技术描述中所需要使用的附图作简单地介绍,显而易见地,下面描述中的附图仅仅是本发明的实施例,对于本领域普通技术人员来讲,在不付出创造性劳动的前提下,还可以根据提供的附图获得其他的附图。图1附图为本发明浸出渣膏回收锌工艺流程图。具体实施方式下面将结合本发明实施例中的附图,对本发明实施例中的技术方案进行清楚、完整地描述,显然,所描述的实施例仅仅是本发明一部分实施例,而不是全部的实施例。基于本发明中的实施例,本领域普通技术人员在没有做出创造性劳动前提下所获得的所有其他实施例,都属于本发明保护的范围。本发明实施例公开了一种浸出渣回收锌工艺,不仅工艺简单、能耗低,而且金属锌回收率高,并且该工艺具有工艺流程短、加工费用低、资源综合利用等特点,在行业上有良好的推广示范作用。为更好地理解本发明,下面通过以下实施例对本发明作进一步具体的阐述,但不可理解为对本发明的限定,对于本领域的技术人员根据上述
发明内容所作的一些非本质的改进与调整,也视为落在本发明的保护范围内。参见说明书附图1,本发明公开的一种浸出渣回收锌工艺,所述回收锌工艺具体包括如下步骤:步骤一:将电解废液注入处理罐中,边搅拌边缓慢加入二净渣;步骤二:待步骤一中的二净渣加入1/3电解废液量时,测定反应混合液ph值;步骤三:待步骤二中混合液的ph值为3.5~4.5时,停止加入二净渣,反应25~35min,取样分析合格后压滤,滤液泵入锌制液系统。为了进一步实现本发明的技术效果,步骤一中,电解废液的加入量为50~60%,且所述电解废液中硫酸的浓度为140~150g/l。为了进一步实现本发明的技术效果,步骤一中,控制所述二净渣和所述电解废液的固液比为1:3~5。为了进一步实现本发明的技术效果,步骤二中,控制二净渣和电解废液反应过程中的ph≥3.5,反应终点的ph为3.5~4.5。为了进一步实现本发明的技术效果,步骤三中,分析合格样品中cd2+浓度低于1g/l,zn2+浓度在98~100g/l之间。为了进一步实现本发明的技术效果,cd2+浓度高于1g/l时,在反应体系中继续加入二净渣或锌灰以使cd2+浓度低于1g/l。下面,将结合具体实施例,对本发明的技术方案进行进一步的说明。实施例1一种浸出渣回收锌工艺,所述回收锌工艺具体包括如下步骤:步骤一:在处理罐中加入体积为55%v的电解废液,且电解废液中硫酸的浓度为145g/l,据二净渣和电解废液的固液比为1:4称取二净渣,然后边搅拌边向处理罐中缓慢加入二净渣;步骤二:待步骤一中的二净渣加入1/3电解废液量时,测定反应混合液ph值;步骤三:待步骤二中混合液的ph值为3.8时,停止加入二净渣,反应30min后取样,分别测定样品中锌、铜、镉的浓度,分析合格(cd2+浓度低于1g/l)后压滤,滤液泵入锌制液系统。实施例2一种浸出渣回收锌工艺,所述回收锌工艺具体包括如下步骤:步骤一:在处理罐中加入体积为55%v的电解废液,且电解废液中硫酸的浓度为145g/l,据二净渣和电解废液的固液比为1:4称取二净渣,然后边搅拌边向处理罐中缓慢加入二净渣;步骤二:待步骤一中的二净渣加入1/3电解废液量时,测定反应混合液ph值;步骤三:待步骤二中混合液的ph值为4.0时,停止加入二净渣,反应30min后取样,分别测定样品中锌、铜、镉的浓度,分析合格(cd2+浓度低于1g/l)后压滤,滤液泵入锌制液系统。实施例3一种浸出渣回收锌工艺,所述回收锌工艺具体包括如下步骤:步骤一:在处理罐中加入体积为55%v的电解废液,且电解废液中硫酸的浓度为145g/l,据二净渣和电解废液的固液比为1:4称取二净渣,然后边搅拌边向处理罐中缓慢加入二净渣;步骤二:待步骤一中的二净渣加入1/3电解废液量时,测定反应混合液ph值;步骤三:待步骤二中混合液的ph值为4.2时,停止加入二净渣,反应30min后取样,分别测定样品中锌、铜、镉的浓度,分析合格(cd2+浓度低于1g/l)后压滤,滤液泵入锌制液系统。实施例4一种浸出渣回收锌工艺,所述回收锌工艺具体包括如下步骤:步骤一:在处理罐中加入体积为55%v的电解废液,且电解废液中硫酸的浓度为145g/l,据二净渣和电解废液的固液比为1:4称取二净渣,然后边搅拌边向处理罐中缓慢加入二净渣;步骤二:待步骤一中的二净渣加入1/3电解废液量时,测定反应混合液ph值;步骤三:待步骤二中混合液的ph值为3.0时,停止加入二净渣,反应30min后取样,分别测定样品中锌、铜、镉的浓度,结果分析样品中cd2+浓度为3.0g/l,则需要往反应体系中继续加入二净渣以使最终混合溶液中cd2+浓度低于1g/l,随后经压滤,滤液泵入锌制液系统,即可。实施例5一种浸出渣回收锌工艺,所述回收锌工艺具体包括如下步骤:步骤一:在处理罐中加入体积为55%v的电解废液,且电解废液中硫酸的浓度为145g/l,据二净渣和电解废液的固液比为1:4称取二净渣,然后边搅拌边向处理罐中缓慢加入二净渣;步骤二:待步骤一中的二净渣加入1/3电解废液量时,测定反应混合液ph值;步骤三:待步骤二中混合液的ph值为2.8时,停止加入二净渣,反应30min后取样,分别测定样品中锌、铜、镉的浓度,结果分析样品中cd2+浓度为2.8g/l,则需要往反应体系中继续加入二净渣以使最终混合溶液中cd2+浓度低于1g/l,随后经压滤,滤液泵入锌制液系统,即可。实施例6一种浸出渣回收锌工艺,所述回收锌工艺具体包括如下步骤:步骤一:在处理罐中加入体积为55%v的电解废液,且电解废液中硫酸的浓度为145g/l,据二净渣和电解废液的固液比为1:4称取二净渣,然后边搅拌边向处理罐中缓慢加入二净渣;步骤二:待步骤一中的二净渣加入1/3电解废液量时,测定反应混合液ph值;步骤三:待步骤二中混合液的ph值为2.8时,停止加入二净渣,反应30min后取样,分别测定样品中锌、铜、镉的浓度,结果分析样品中cd2+浓度为2.8g/l,则需要往反应体系中继续加入锌灰以使最终混合溶液中cd2+浓度低于1g/l,随后经压滤,滤液泵入锌制液系统,即可。接下来,运用实施例1~6所述的浸出渣回收锌工艺分别对二净渣进行回收锌处理,并分别测定最终金属锌、未加二净渣/锌灰的金属镉浸出率。其中,所述二净渣的化学成分如表一所示。表一二净渣的化学成分(wt/%)gecdcuznpb水分0.25~0.300.25~0.300.35~0.4045~550.2~0.622~28测定结果,如表二所示表二测试结果分析由表二结果可知,本发明公开的浸出渣回收锌工艺运行稳定、治理简单彻底,其中金属锌回收率可达到98%以上,大于锌浸出率90%的目标值;且要想使镉的浸出率小于10%,就要控制终点的ph在3.5~4.5之间。另外,当反应体系中酸过量,体系ph小于3.5,则使得二净渣的其他杂质(镉)被浸出。而本发明通过采用二净渣本身含的金属锌或锌粉去除掉镉,以使最终反应体系中cd2+浓度低于1g/l。至于最终采用二净渣或锌粉除镉方式,对金属镉的浸出率影响不大,且添加量均为ccd2+×3v。此外,分析结果过程中的检验规程如下:1、中和容量法酸、锌连测方法提要用甲基红—亚甲基蓝为指示剂,氢氧化钠标准溶液滴定游离酸后,再用二甲酚橙为指示剂滴定锌量。1)试剂过氧化氢(30%),六次甲基四胺,0.5%二甲酚橙溶液,0.2%甲基红乙醇溶液,0.1%亚甲基蓝溶液,0.05%mol/l氢氧化钠标准溶液,0.08mol/ledta标准溶液2)分析步骤移取酸性浸出液1ml于500ml三角烧杯中,加水适量,用洗瓶吹洗三角烧杯,用甲基红—亚甲基蓝为指示剂,调紫红色,用氢氧化钠标准溶液滴定至紫红色变绿色,记下消耗氢氧化钠标准溶液的体积v;再加2g六次甲基四胺,2滴二甲酚橙,用edta标准溶液滴定至紫色变绿色为终点,记下消耗edta标准溶液的体积v2。式中:t1表示氢氧化钠标准溶液的对酸滴定度,g/ml;v1表示消耗氢氧化钠标准溶液的体积,ml;t2表示edta标准溶液对锌的滴定度,g/ml;v0移取液体试样的体积,ml。2、铜的测定吸取试样10ml于100ml分液漏斗中,加入20%酒石酸钾钠10ml,再加入5%盐酸羟胺5ml,生成白色沉淀,再加入浓盐酸4滴,白色沉淀消失后,加入铜试剂铅-三氯甲烷溶液10ml,萃取2min,静止分层,将有机层放入1ml的比色皿中,以三氯甲烷为空白,于波长436nm处测定吸光度。cu(mg/l)=a试样×m标/a标×v×1000a试样:试样的吸光度a标:标样的吸光度m标:标样的量—c标×v标(g)v:所移取试样的体积(ml)3、苯基荧光酮萃取分光光度法测定锗移取10ml中浸液(酸浸液1.0ml,加水至10ml)于250ml分液漏斗中,滴入1%高锰酸钾溶液至呈稳定红色,放置1min,加少许亚硫酸钠使红色消失。准确加入10ml四氯化碳,30ml盐酸,震荡2min,静置分层后,将有机相移入干燥的25ml比色管中,加入3ml无水乙醇,1ml0.06%苯基荧光酮溶液,混匀,放置10min,用1cm的吸收皿,以试剂空白为参比,于波长517nm测定其吸光度。计算:ge(mg/l)=m标×a样/a标×v×1000m标:c标×v标(mg)a标:标样的吸光度a样:试样的吸光度v:所移取试样的体积(ml)4、镉的测定:酸性极谱法试剂:1)、浓盐酸2)、浓硫酸3)、镉标100ug/ml分析:1、移取10~20ml锌液或电解液入50ml容量瓶中,依次加入1ml浓盐酸,1ml浓硫酸,以水定容。吸取1ml镉标准溶液于50ml容量瓶中,依次加入1ml浓盐酸,1ml浓硫酸,以水定容。分别注入电解池中,进行极谱分析。本说明书中各个实施例采用递进的方式描述,每个实施例重点说明的都是与其他实施例的不同之处,各个实施例之间相同相似部分互相参见即可。对于实施例公开的装置而言,由于其与实施例公开的方法相对应,所以描述的比较简单,相关之处参见方法部分说明即可。对所公开的实施例的上述说明,使本领域专业技术人员能够实现或使用本发明。对这些实施例的多种修改对本领域的专业技术人员来说将是显而易见的,本文中所定义的一般原理可以在不脱离本发明的精神或范围的情况下,在其它实施例中实现。因此,本发明将不会被限制于本文所示的这些实施例,而是要符合与本文所公开的原理和新颖特点相一致的最宽的范围。当前第1页12