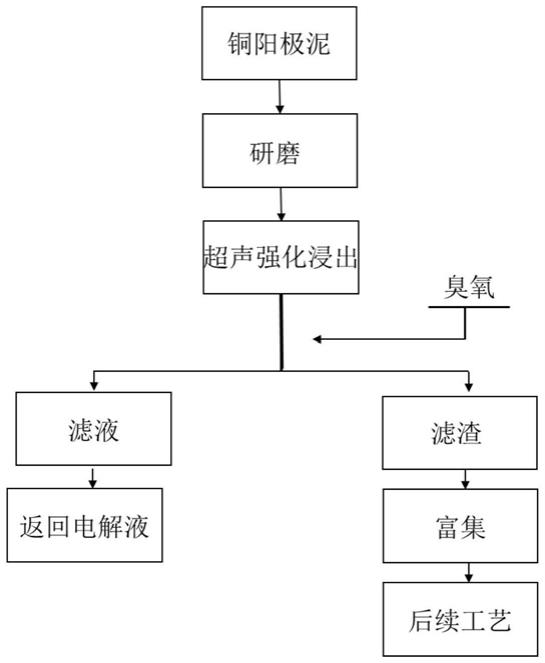
[0001]
本发明涉及一种超声强化臭氧氧化脱铜的方法,属于冶金技术领域。
背景技术:[0002]
作为铜冶炼的副产物,铜阳极泥因富含贵金属-金、银、铂族金属,稀散金属-硒、碲等,是提取稀贵金属的重要原料。铜阳极泥的处理工艺主要分火法、湿法和选冶联合流程。任何铜阳极泥的处理工艺流程的第一步都是除去大量存在的铜,其原因在于如果不预先将铜除去,不但增加了铜阳极泥熔炼和火法精炼成多尔合金时脱除杂质的难度,造成贵金属的大量循环,降低金银的直收率;而且还会延长生产周期,消耗大量燃料、原材料和增加操作人员的劳动强度。
[0003]
目前国内外铜阳极泥脱铜的方法主要包括传统火法-电解处,湿法处理,选冶联合处理三种工艺。其中被广泛应用的铜阳极泥脱铜手段是湿法处理。湿法处理主要包括硫酸化焙烧蒸硒-酸浸脱铜工艺、空气氧化脱铜工艺、加压酸浸工艺,这三种工艺在一定程度上完成了对阳极泥铜的脱铜处理,同时也存在一些问题亟待解决。前两种工艺存在的问题在于处理时间长、处理温度高、铜脱除率低。加压酸浸工艺虽然具有过程简单、处理时间短、铜回收率高等优点,但也存在设备易腐蚀、硒碲脱除率低、砷分散问题突出等缺点。
技术实现要素:[0004]
本发明针对现有技术中铜阳极泥脱铜的问题,提供一种超声强化臭氧氧化脱铜的方法,本发明将臭氧和超声联合,于浸出体系中建立一个高效、清洁的氧化系统,选择性地将铜阳极泥中的硫化铜和碲化铜等难溶相转化为可溶相,进而克服传统工艺存在的处理时间长、脱铜效率低、设备腐蚀等技术难题;实现阳极泥中铜的迅速脱除,在高效脱铜的过程中,减少运行能耗。
[0005]
一种超声强化臭氧氧化脱铜的方法,具体步骤如下:
[0006]
(1)将铜阳极泥干燥、研磨得到铜阳极泥粉;
[0007]
(2)将步骤(1)铜阳极泥粉加入硫酸溶液中,在超声、臭氧条件下进行超声臭氧氧化浸出铜,固液分离得到浸出液和除铜浸出渣。
[0008]
所述步骤(2)硫酸溶液的浓度为100-200g/l,硫酸溶液与铜阳极泥粉的液固比ml:g为1-5:1。
[0009]
所述步骤(2)超声功率为50-300w。
[0010]
所述步骤(2)臭氧流量为10-250l/h。
[0011]
进一步的,所述步骤(2)浸出温度为室温,浸出时间为1-5h。
[0012]
本发明的有益效果是:
[0013]
(1)本发明采用超声强化臭氧脱除用阳极泥中的铜,实现了常温下高效脱除铜,脱铜率高,时间短,操作简单;
[0014]
(2)本发明超声处理溶液时,当超声声强不足以产生空化效应时,其机械效应使液
体强烈搅动,降低扩散阻力,破坏边界层,加速传质、传热;在足够强的超声作用下,产生超声空化效应,在极短时间内和在空化泡周围的极小空间内,产生5000k以上的高温和大约5
×
10
7
pa的高压,温度变化率高达109k/s,形成所谓“热点”,从而可以广辟化学反应通道,骤增化学反应速度;
[0015]
(3)本发明将臭氧与超声联合,产生了高级的氧化过程,超声空化效应产生的局部高温高压条件促使空化泡中的臭氧直接快速的分解为氧气和带原子的氧,带原子的氧和水反应生成具有活性的羟基,臭氧和超声的联合形成高效的氧化系统;在超声作用下水分解产生羟基、过氧羟基等氧化性极强的中间产物;另外,超声的机械效应促使臭氧被粉碎成微气泡,提高臭氧的体积传质系数,极大地提高臭氧的溶解速度,增加单位时间内臭氧的浓度;本发明超声强化臭氧的强氧化性有利于对难溶性物质的氧化,氧化效率高,氧化产物均是易于分解且无污染的氢氧化物和臭氧化物,易处理,成本低。
附图说明
[0016]
图1为本发明工艺流程图;
[0017]
图2为本发明装置示意图。
具体实施方式
[0018]
下面结合具体实施方式对本发明作进一步详细说明,但本发明的保护范围并不限于所述内容。
[0019]
本发明装置示意图见图2,装置包括超声发生器、臭氧发生装置和恒温水浴;反应装置设置在恒温水浴装置中,反应体系设置在反应装置内,超声波发生器的超声探头插设在反应装置的反应体系中,臭氧发生装置的输送管插设在反应装置的反应体系底部。
[0020]
实施例1:一种超声强化臭氧氧化脱铜的方法(见图1),具体步骤如下:
[0021]
(1)将铜阳极泥干燥、研磨,过200目筛得到铜阳极泥粉;
[0022]
(2)将步骤(1)铜阳极泥粉加入硫酸溶液中,在室温、超声、臭氧条件下进行超声臭氧氧化浸出铜,浸出结束,关闭超声发生器、臭氧发生器,取出泥浆,将泥浆经过三层滤纸进行抽滤,并反复润洗3次得到虑液和除铜虑渣,滤液可返回作为铜电解液,滤渣可经火法或湿法技术富集并产出稀贵金属合金或粉末,最后经过精炼产生稀贵金属产品;其中硫酸溶液的浓度为150g/l,硫酸溶液与铜阳极泥粉的液固比为3:1(ml:g),超声功率为150w,臭氧流量为150l/h,浸出时间为2h;
[0023]
对除铜浸出渣进行铜含量检测,计算出本实施例的脱铜率为96.75%。
[0024]
实施例2:一种超声强化臭氧氧化脱铜的方法(见图1),具体步骤如下:
[0025]
(1)将铜阳极泥干燥、研磨,过200目筛得到铜阳极泥粉;
[0026]
(2)将步骤(1)铜阳极泥粉加入硫酸溶液中,在室温、超声、臭氧条件下进行超声臭氧氧化浸出铜,浸出结束,关闭超声发生器、臭氧发生器,取出泥浆,将泥浆经过三层滤纸进行抽滤,并反复润洗3次得到滤液和除铜滤渣,滤液可返回作为铜电解液,滤渣可经火法或湿法技术富集并产出稀贵金属合金或粉末,最后经过精炼产生稀贵金属产品;其中硫酸溶液的浓度为150g/l,硫酸溶液与铜阳极泥粉的液固比为4:1(ml:g),超声功率为120w,臭氧流量为200l/h,浸出时间为5h;
[0027]
对除铜浸出渣进行铜含量检测,计算出本实施例的脱铜率为98.07%。
[0028]
实施例3:一种超声强化臭氧氧化脱铜的方法(见图1),具体步骤如下:
[0029]
(1)将铜阳极泥干燥、研磨,过200目筛得到铜阳极泥粉;
[0030]
(2)将步骤(1)铜阳极泥粉加入硫酸溶液中,在室温、超声、臭氧条件下进行超声臭氧氧化浸出铜,浸出结束,关闭超声发生器、臭氧发生器,取出泥浆,将泥浆经过三层滤纸进行抽滤,并反复润洗3次得到虑液和除铜虑渣,滤液可返回作为铜电解液,滤渣可经火法或湿法技术富集并产出稀贵金属合金或粉末,最后经过精炼产生稀贵金属产品;其中硫酸溶液的浓度为100g/l,硫酸溶液与铜阳极泥粉的液固比为1:1(ml:g),超声功率为50w,臭氧流量为10l/h,浸出时间为1h;
[0031]
对除铜浸出渣进行铜含量检测,计算出本实施例的脱铜率为92.51%。
[0032]
实施例4:一种超声强化臭氧氧化脱铜的方法(见图1),具体步骤如下:
[0033]
(1)将铜阳极泥干燥、研磨,过200目筛得到铜阳极泥粉;
[0034]
(2)将步骤(1)铜阳极泥粉加入硫酸溶液中,在室温、超声、臭氧条件下进行超声臭氧氧化浸出铜,浸出结束,关闭超声发生器、臭氧发生器,取出泥浆,将泥浆经过三层滤纸进行抽滤,并反复润洗3次得到虑液和除铜虑渣,滤液可返回作为铜电解液,滤渣可经火法或湿法技术富集并产出稀贵金属合金或粉末,最后经过精炼产生稀贵金属产品;其中硫酸溶液的浓度为200g/l,硫酸溶液与铜阳极泥粉的液固比为5:1(ml:g),超声功率为300w,臭氧流量为250l/h,浸出时间为5h;
[0035]
对除铜虑渣进行铜含量检测,计算出本实施例的脱铜率为99.14%。
[0036]
以上是对本发明的具体实施方式作了详细说明,但是本发明并不限于上述实施方式,在本领域普通技术人员所具备的知识范围内,还可以在不脱离本发明宗旨的前提下做出各种变化。