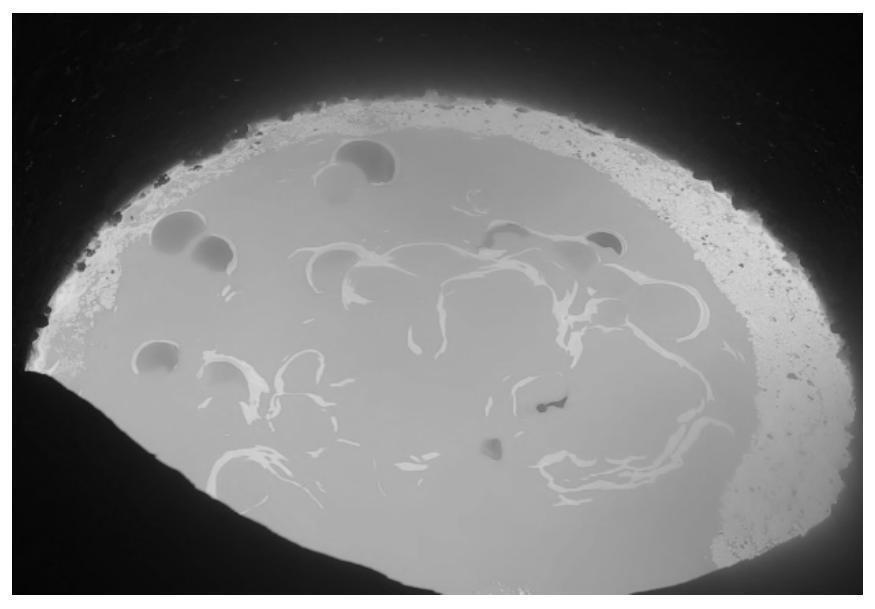
:
1.本发明涉及金属熔炼、铸造领域,具体涉及一种用于高温合金母合金纯净化冶炼的底吹氩方法。
背景技术:2.高温合金具有优异的高温抗氧化、腐蚀、蠕变及疲劳性能,因而被广泛应用于制造航空航天发动机和燃气轮机的关键结构件。合金的纯净度对高温性能影响尤为巨大,研究表明,铸件中的非金属夹杂是合金发生损伤甚至断裂的主要原因之一。目前高温合金母合金的制备通常以真空感应熔炼,或配合电渣重熔或真空自耗的方式进行。其中,通过真空感应炉进行高温精炼,可促进一部分杂质元素形成非金属夹杂上浮至熔体表面,并通过坩埚的吸附作用或中间包的挡渣作用去除,另一部分则以气体形式通过真空炉内的高真空负压效应被真空泵抽出,从而使合金中的气体和杂质元素总量降至200ppm以下。但熔炼过程中形成的细小非金属夹杂(10μm以下)在熔体中的上浮速率极慢,并且难以通过挡渣过滤手段去除,一旦进入高温合金铸件,将严重影响合金的服役性能。采用电渣重熔或真空自耗的方式虽然可进一步去除母合金中的夹杂含量,但二次重熔不仅会损耗一部分母合金(二次打磨和头尾切除),加重了能源和人工消耗,更会影响合金中al、ti、c、hf等高活性易挥发元素的浓度,在一定程度上降低了母合金的生产效率。因此,提出一种简单高效去除母合金熔体中夹杂物的工艺方法,在高温合金纯净化冶炼工程化应用领域方面具有十分重要的意义。
3.熔体吹氩作为一门专业的技术在冶金铸造行业已广泛应用,对于去除熔体中非金属夹杂物和有害气体具有良好的效果,并有利于均匀熔体化学成分和温度,而且氩气作为惰性气体,在钢水中无残留。因此,熔体吹氩技术是一种绿色的最理想的净化手段。其中,可通过埋入式炉底吹氩法,将透气塞预埋在炉衬材料底下,氩气透过炉衬料均匀进入到熔体中,可产生均匀的微气泡,通过连续的微气泡上浮可将熔体中的细小非金属夹杂颗粒快速带至熔体表面,提高了熔体中细小夹杂物的去除效率。
4.但由于目前广泛应用的底吹氩工艺通常只适用于常压冶炼工况,而高温合金冶炼过程通常需在高真空条件下进行,极高的真空度会导致吹氩过程中熔体表面沸腾严重,产生大量飞溅,若工艺参数控制不当,不仅不利于熔体纯净化,还降低了冶炼过程的安全系数,上述因素也成为了底吹氩技术难以适用于高温合金真空熔炼的主要原因之一。
技术实现要素:5.为了解决现有技术的缺点和不足,本发明的目的在于提供一种用于高温合金母合金纯净化冶炼的底吹氩方法,该方法操作简单、经济实用,不仅有助于提高高温合金母合金的纯净度,还可降低高温合金铸件由于夹杂产生的废品率。
6.本发明采用的技术解决方案是:
7.一种用于高温合金母合金纯净化冶炼的底吹氩方法,该底吹氩方法包括以下步骤:
8.(1)根据实际情况定制底吹氩透气塞尺寸,并与坩埚主体进行组合、烧结,形成底吹氩坩埚;
9.(2)将原料放入真空感应炉内进行熔炼,按照工艺要求化清及高温精炼,待熔体表面稳定后关闭真空泵机组;真空感应熔炼时,保证炉内气压低于40pa,精炼时间不低于20min;
10.(3)关闭真空泵机组,并充入高纯氩气至炉内气压为0.2~0.4mpa,打开底吹氩供气系统,根据坩埚内熔体质量设置底吹氩工艺参数,底吹氩工艺参数应满足下式:
[0011][0012]
其中,r为气体常数,t为熔体温度(k),f
ar
为吹氩流量(m3/min),p
ar
为吹氩气压(mpa),m为熔炼合金质量(kg),φ1透气塞直径(mm),p0为炉内气压(mpa),k气孔率(%)。
[0013]
所述的用于高温合金母合金纯净化冶炼的底吹氩方法,步骤(1)中,底吹氩坩埚为捣打坩埚,透气塞直径φ1(mm)、高度d(mm)以及气孔率k(%)计算公式如下:
[0014][0015]
其中,φ2为坩埚内径(mm);
[0016][0017]
其中,d0为捣打坩埚底厚度(mm);
[0018]
气孔率:
[0019]
25%≤k≤35%。
[0020]
所述的用于高温合金母合金纯净化冶炼的底吹氩方法,步骤(1)中,将透气塞置于坩埚底部并与连接氩气的中空螺杆相连,并在透气塞上方铺设透气砂,周围填充捣打料,并捣打紧实,透气砂高度应与捣打料高度保持一致。
[0021]
所述的用于高温合金母合金纯净化冶炼的底吹氩方法,步骤(1)中,底吹氩坩埚采用底部镂空的成型坩埚,透气塞直径φ1(mm)的计算公式如下:
[0022][0023]
其中,φ2为坩埚内径(mm);
[0024]
安装透气塞并铺设透气砂时,保证透气砂厚度为坩埚壁厚度的1/3~1/5。
[0025]
所述的用于高温合金母合金纯净化冶炼的底吹氩方法,步骤(1)中,采用纯镍洗炉,将底吹氩坩埚进行烧结,烧结工艺为:在900~1100℃保温1~3h,继续升温至1600~1800℃保温0.5~2h,获得底吹氩冶炼坩埚。
[0026]
所述的用于高温合金母合金纯净化冶炼的底吹氩方法,步骤(3)中,进行底吹氩工艺5~15min后,关闭供气系统,打开真空泵机组,将炉内气压降至40pa以下,并待熔体温度降至浇注工艺所需温度后进行浇注,获得成分分布均匀,且非金属夹杂含量少的高温合金母合金锭。
[0027]
本发明的设计思想是:通过底吹氩气泡行为的精确控制,并借助气泡上浮与吸附作用,将熔体中的气体、夹杂物等进行高效脱除,达到合金熔体纯净化的目的。
[0028]
本发明根据冶炼炉容量定制透气塞,若采用捣打坩埚,需将透气砂铺于透气塞上方,周围采用捣打料填充,通过纯镍洗炉使坩埚烧结,得到适用于底吹氩的捣打坩埚,根据经验公式初步制定吹氩压强、氩气流量和吹氩时间等工艺参数,待合金熔体精炼结束后进行底吹氩工艺,最后降温浇注。该底吹氩工艺能够大幅度降低母合金中的夹杂含量,降低母合金重熔期间的浮渣占比,提高高温合金母合金锭的冶金质量。
[0029]
本发明具有的优点和积极效果是:
[0030]
1、与真空感应熔炼相比,能够大大提高熔体中细小非金属夹杂的上浮速率,有利于提高熔体的纯净度;与电渣和真空自耗重熔工艺相比,减少了重熔带来的原料、能源及人工消耗,并且避免了重熔期间al、ti、c、hf等元素的烧损,有利于母合金成分控制。
[0031]
2、本发明适用于绝大多数高温合金母合金纯净化冶炼,并可根据实际情况自由调整底吹氩工艺参数,操作简单,灵活多变,实用性强,实施难度低,效果显著。
[0032]
3、本发明有利于推动高温合金的产业化,对合金冶炼技术发展具有重要的社会意义和经济意义。
附图说明
[0033]
图1为底吹氩工艺实际情况图。
[0034]
图2为采用本发明制备的k40m母合金锭不同部位的浮渣情况图;其中,(a)上部;(b)下部。
具体实施方式
[0035]
在具体实施过程中,本发明提出的底吹氩方法包括以下步骤:
[0036]
(1)根据实际情况,按照公式(1)~(3)定制底吹氩透气塞尺寸,并与坩埚主体进行组合、烧结,形成底吹氩坩埚;
[0037]
1)若冶炼坩埚为捣打坩埚,则需定制透气塞,根据经验,透气塞直径φ1(mm)、高度d(mm)以及气孔率k(%)计算公式如下:
[0038][0039]
其中,φ2为坩埚内径(mm)。
[0040][0041]
其中,d0为捣打坩埚底厚度(mm)。
[0042]
气孔率:
[0043]
25%≤k≤35%
ꢀꢀꢀꢀꢀꢀꢀꢀꢀꢀꢀꢀꢀꢀꢀꢀꢀꢀꢀꢀꢀꢀꢀ
(3)
[0044]
将定制好的透气塞置于坩埚底部并与连接氩气的中空螺杆相连,并在透气塞上方铺设透气砂(plugs
‑
ram st),周围填充捣打料,并捣打紧实。透气砂高度应与捣打料高度保持一致。
[0045]
2)也可采用底部镂空的成型坩埚,透气塞尺寸设计与(1)部分一致,安装透气塞并铺设透气砂时,应保证透气砂厚度为坩埚壁厚度的1/4左右。
[0046]
采用纯镍洗炉,将底吹氩坩埚进行烧结,烧结工艺为1000℃
×
2h+1700℃
×
1h,即
可获得底吹氩冶炼坩埚。
[0047]
(2)将原料放入真空感应炉内进行熔炼,按照工艺要求化清及高温精炼,待熔体表面稳定后关闭真空泵机组;真空感应熔炼时,需保证炉内气压低于40pa,精炼时间不低于20min。
[0048]
(3)关闭真空泵机组,并充入高纯氩气至炉内气压约为0.3mpa,打开底吹氩供气系统,根据坩埚内熔体质量设置底吹氩工艺参数,底吹氩工艺参数应尽量满足下式:
[0049][0050]
其中,r为气体常数,t为熔体温度(k),f
ar
为吹氩流量(m3/min),p
ar
为吹氩气压(mpa),m为熔炼合金质量(kg),φ1透气塞直径(mm),p0为炉内气压(mpa),k气孔率(%)。进行底吹氩工艺约10min后,关闭供气系统,打开真空泵机组,将炉内气压降至40pa以下,并待熔体温度降至浇注工艺所需温度后进行浇注,可获得成分分布均匀,且非金属夹杂含量较少的高温合金母合金锭。
[0051]
通过公式(4)制定底吹氩工艺初始参数,打开底吹氩供气系统,根据现场实际情况进行微调,工艺参数变化对熔体表面气泡的影响规律如表1所示:
[0052]
表1不同工艺参数对熔体表面气泡的影响规律
[0053]
工艺参数变化影响规律真空度增加气泡体积增大吹氩气压增加气泡体积增大,覆盖面积减小吹氩流量增加气泡数量增加,覆盖面积增大
[0054]
进行底吹氩工艺10min后,关闭供气系统,打开真空泵机组,待炉内气压降至40pa以下,且熔体到达浇注温度后进行浇注,得到产品母合金。
[0055]
下面,通过实施例和附图对本发明进一步详细阐述。
[0056]
实施例
[0057]
本实施例中,进行k40m牌号共400kg母合金冶炼,使用的设备为500kg真空感应炉,合金成分为:0.5c
‑
25.5cr
‑
10.5ni
‑
7.5w
‑
0.3mo
‑
1al
‑
0.15ti
‑
0.3ta
‑
0.013b
‑
0.2zr
‑
co(质量分数,wt.%),fe余量。
[0058]
根据公式(1)~(3)进行透气塞尺寸设计,底吹氩坩埚制备如下:
[0059]
(1)涂抹线圈保护料,并在内侧铺设两层云母纸,将透气塞与中控螺杆相连;
[0060]
(2)在透气塞上方铺设透气砂,周围用炉衬料包围,并用捣打机捣打紧实;
[0061]
(3)通过镍筒和捣打料制作捣打坩埚,并用无磷铬泥修补出坩埚出钢口形状,再通过纯ni洗炉烧结,即可获得底吹氩坩埚。
[0062]
实施例中,所用坩埚内径约为390mm,透气塞设计直径约为190mm,合金精炼温度约为1500℃,根据公式(4)初步制定出底吹氩工艺参数:炉内气压0.3mpa,氩气流量0.02m3/min,吹氩气压0.2mpa。
[0063]
将待制备合金原料装入坩埚内,进行真空感应熔炼,1500℃高温精炼约30min后,关闭真空泵机组,充入氩气至真空炉内气压约为0.3mpa,打开底吹氩供气系统,设置氩气流量约为0.02m3/min,吹氩气压约为0.2mpa,进行底吹氩10min,在此过程中,需保证钢液温度维持在1500℃附近。
[0064]
在操作期间,可根据实际情况,按照表1对底吹氩工艺参数进行微调,使熔体表面气泡上浮情况达到图1所示标准(或气泡尺寸更小,覆盖面积更大)即可。
[0065]
待底吹氩工艺结束后,关闭底吹氩供气系统,打开真空泵机组,将炉内真空度恢复至40pa以下,进行降温浇注,即可获得纯净度较高的k40m母合金。采用hb5406
‑
2016标准进行浮渣检测,获得的k40m母合金上下部位的浮渣占比均可低于0.5%,如图2所示。
[0066]
实施例结果表明,采用本发明设计的工艺方法制备的母合金锭,通过真空感应熔炼降低合金熔体中的气体及杂质元素含量,再通过底吹氩工艺使熔体中气体及杂质元素与熔体反应生成的细小非金属夹杂迅速上浮至熔体表面,最后通过坩埚壁吸附及中间包的挡渣过滤作用去除,获得的母合金产品在重熔期间浮渣占比可达到极低数量级。