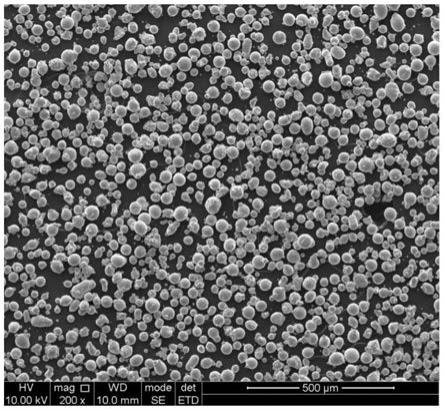
fesibccr非晶磁粉及其制备方法
技术领域
1.本发明涉及非晶软磁材料制备技术领域,尤其涉及一种fesibccr非晶磁粉及其制备方法。
背景技术:2.软磁材料作为具有低矫顽力、高磁导率、高饱和磁感应强度、低损耗、高稳定性的磁性材料,被广泛应用于各类电力设备和电子器件中。在各类软磁材料中,由非晶带材绕成的铁芯以其优良的软磁性能得到了人们的广泛使用,但这类软磁材料力学性能较差,在使用过程中会出现碎裂掉渣的危险,限制了其广泛应用。基于此,非晶磁粉经压力成型,得到的磁粉芯具有高频下恒磁导率、低损耗等优势,同时不存在使用安全问题,逐渐受到研究者的广泛关注,如何制备具有优异软磁性能的非晶磁粉也成为了当前的研究重点。
3.在各类非晶磁粉中,fesibccr非晶磁粉具有频率稳定性好、损耗低等特点,因而得到了广泛应用。目前,fesibccr非晶磁粉的制备主要是根据成分配比选择相应的纯铁、铬与铁硼、铁碳、铁硅等中间合金作为原料,经熔炼后采用雾化法将其制成非晶磁粉。
4.例如,公开号为cn109396416a的专利公开了一种新型铁基非晶合金粉末的制备方法,该专利按照所需铁基非晶合金粉末的成分,采用真空感应熔炼炉熔炼母合金,对所得母合金经二次熔融后,采用气雾化法雾化制粉,得到铁基非晶合金粉末,经干燥和筛分处理后获得目标粒径的铁基非晶合金粉末。然而,这样的制备方法不仅具有较高的原料成本,其熔炼过程中使用的中间合金中含有的较多杂质还会影响非晶合金的形成,进而导致制得的非晶磁粉的成分及性能受限于原料的种类与纯度;并且,在熔炼过程中难以对熔炼的温度进行有效控制,容易出现熔炼温度不均匀的问题,影响产品性能。
5.为了提高产品成分的可控性,公开号为cn111001767a的专利提供了一种高饱和磁感应强度铁基非晶软磁合金及其制备方法,该方法利用铁矿石经高炉炼铁、转炉吹炼或利用废钢经电炉熔炼得到初炼钢液;再对初炼钢液进行炉外精炼,进一步脱氧、脱硫、去除夹杂物,控制残余元素的含量,并进行合金成分微调,得到精炼钢液后,再通过单辊旋淬及热处理得到具有高饱和磁感应强度的铁基非晶软磁合金。然而,该专利中采用的高炉炼铁、转炉吹炼或电炉熔炼的方式单次产量过高,不符合软磁产品的实际需求量;且这些冶炼方式对原料的成分有非常高的要求,如p、s、cu、碱金属等高炉炼铁过程的有害元素的含量都需要被严格控制,不仅无法充分利用铁矿石种类和冶炼方式的多样性,成分设计单一,还需要在制备过程中对钢液进行复杂的脱硫、脱氧处理,在出钢过程中再添加含量较高的硅铁、硼铁、磷铁等高成本原料,整体存在操作工序复杂、操作时间长且生产成本和生产能耗大等问题。
6.有鉴于此,有必要设计一种改进的fesibccr非晶磁粉的制备方法,以解决上述问题。
技术实现要素:7.针对上述现有技术的缺陷,本发明的目的在于提供一种fesibccr非晶磁粉及其制备方法。通过采用碳基还原或氢基还原的方式对反应原料进行还原熔炼,并通过熔融除渣除去精炼钢液中的杂质,再利用合金化有效控制精炼钢液的成分,经气雾化和热处理后制备fesibccr非晶磁粉,从而有效利用冶金工艺与非晶磁粉成型工艺之间的协同作用,在精确控制冶炼条件及非晶磁粉成分的基础上有效简化工艺流程,并大幅降低生产成本,在保证制得的非晶磁粉具有优异软磁性能的同时以较低的成本实现大规模高效生产,以满足工业化生产与应用的需求。
8.为实现上述目的,本发明提供了一种fesibccr非晶磁粉的制备方法,包括如下步骤:
9.s1、将铁矿石或铁矿石与铬砂、硼砂的混合物作为反应原料,采用碳基还原或氢基还原的方式对所述反应原料进行还原熔炼,得到还原产物;
10.s2、对步骤s1得到的所述还原产物进行熔融除渣并合金化,得到精炼钢液;当步骤s1中所述反应原料为铁矿石时,所述熔融除渣后还加入了铬、硼铁和硅铁进行所述合金化;
11.s3、采用气雾化法对步骤s2得到的所述精炼钢液进行快速冷却,得到fesibccr非晶粉体;
12.s4、对步骤s3得到的所述fesibccr非晶粉体进行热处理,得到fesibccr非晶磁粉。
13.作为本发明的进一步改进,当步骤s1中采用所述碳基还原的方式进行还原熔炼时,在步骤s2中所述熔融除渣后还包括脱碳处理;当步骤s1中采用所述氢基还原的方式进行还原熔炼时,在步骤s2中所述熔融除渣后还包括增碳处理。
14.作为本发明的进一步改进,在步骤s1中,所述碳基还原具体包括如下步骤:
15.将所述反应原料粉碎后与还原剂煤粉或焦炭混匀,造团、干燥后放置于高温还原反应炉中,控制还原反应气氛为惰性气氛,还原温度为1000~1350℃,反应时间为10~60min,反应完成后,将得到的反应产物再破碎、磁选、熔分,得到的还原合金即为所述还原产物;
16.或者,将所述反应原料造球、干燥后置于高温还原反应炉中,按照预定的流量通入co还原气体;控制还原反应温度为900~1300℃,反应完成后,将得到的反应产物再破碎、磁选、熔分,得到的还原合金即为所述还原产物。
17.作为本发明的进一步改进,在步骤s1中,所述氢基还原具体包括如下步骤:
18.将所述反应原料造球、干燥后置于还原装置中,将氢基还原气体以预定速度通入还原反应装置内,控制所述还原反应装置内的温度为900~1300℃,反应完成后,将得到的反应产物再破碎、磁选、熔分,得到的还原合金即为所述还原产物;
19.或者,将所述反应原料制成粉状,与氢基还原气体经加热预处理后一同喷入闪速还原反应管道内,控制所述闪速还原反应管道内温度为900~1500℃,所述氢基还原气体和粉状的所述反应原料在所述闪速还原反应管道内下降的过程中完成闪速还原反应;所述闪速还原反应管道下部连通熔分装置,在1550~1700℃环境温度设置下,在所述熔分装置中收集得到还原合金,即为所述还原产物。
20.作为本发明的进一步改进,在步骤s2中,所述合金化处理前还包括去除杂质处理,所述合金化的处理温度为1350~1600℃。
21.作为本发明的进一步改进,在步骤s2中,所述精炼钢液的组成成分及其质量百分比包括:在步骤s2中,所述精炼钢液的组成成分及其质量百分比包括:84.9%≤fe≤89.5%、5.3%≤si≤9.2%、2.0≤b≤3.6%、0.3≤c≤1.1%、1.6≤cr≤4.5%、p≤0.015%、s≤0.01%、mn≤0.02%、ti≤0.005%、al≤0.01%。
22.作为本发明的进一步改进,在步骤s3中,采用所述气雾化法时,选择流量为15~25m3/h的氮气,设置雾化温度为1550~1700℃,压力为5~6mpa,得到的所述fesibccr非晶粉体的粒径为10~100μm。
23.作为本发明的进一步改进,在步骤s4中,所述热处理的方式为等温热处理,设置保温温度为300~500℃,保温时间为10~180min。
24.为实现上述目的,本发明还提供了一种根据上述制备方法制备得到的fesibccr非晶磁粉;所述fesibccr非晶磁粉的化学式为feasibbccdcremf,其中,其中,m代表微量元素mn、p、s、ti、al中的一种或多种混合,下标a、b、c、d、e、f分别表示各组成成分的原子百分含量,且满足下述条件:70≤a≤76、9≤b≤15、9≤c≤15、1≤d≤4、1.5≤e≤4、f≤0.3、a+b+c+d+e+f=100。
25.作为本发明的进一步改进,所述fesibccr非晶磁粉的饱和磁感应强度≥1.32t。
26.本发明的有益效果是:
27.(1)本发明提供的fesibccr非晶磁粉的制备方法根据非晶产品的成分特征,选择铁矿石或铁矿石与铬砂、硼砂的混合物作为反应原料,采用碳基还原或氢基还原的方式对反应原料进行还原熔炼,并通过熔融除渣除去精炼钢液中的杂质,利用微合金化有效控制精炼钢液的成分。基于此,fesibccr非晶磁粉的制备过程不需要进行脱磷、脱氧等复杂的除杂过程,还能够保证获得成分可控的精炼钢液,不仅简化了工艺流程,还降低了对原料的限制,从而在保证产品质量的同时大幅降低成本与能耗。在此基础上,本发明通过对得到的精炼钢液进行气雾化处理,再对得到的非晶粉体进行热处理,即可得到具有优异软磁性能的fesibccr非晶磁粉,整体过程流程短,非晶产品能够一次成型,大幅简化了工艺流程,并进一步降低了生产成本与能耗、提高了生产效率,能够实现大规模工业化生产。且本发明提供的fesibccr非晶磁粉的制备方法单次产量可控,更能满足实际生产与应用的需求。
28.(2)本发明提供的fesibccr非晶磁粉的制备方法充分利用了冶金工艺与非晶磁粉成型工艺之间的协同作用,能够在精确控制冶炼条件及非晶磁粉成分的基础上,有效简化工艺流程,并大幅降低生产成本。并且,本发明提供的fesibccr非晶磁粉的制备方法能够对制备过程的工艺参数及产品的成分进行精确控制,产品质量并不依赖于原料质量,因而对原料纯度的要求较低、限制较少,能够在保证制得的非晶磁粉具有优异软磁性能的同时以较低的成本实现高效生产,具有较高的应用价值。
29.(3)本发明提供的fesibccr非晶磁粉的制备方法能够通过对还原熔炼、微合金化及气雾化处理等过程的参数控制,对fesibccr非晶磁粉的成分及其性能进行精确有效的调控。且基于本发明提供的制备方法制得的fesibccr非晶磁粉,其磁感应强度≥1.32t,具有优异的软磁性能,能够满足实际应用的需求。
附图说明
30.图1为本发明实施例1制备的fesibccr非晶磁粉的形貌图。
31.图2为本发明实施例1制备的fesibccr非晶磁粉的xrd图。
32.图3为本发明实施例1制备的fesibccr非晶磁粉的磁滞回线。
具体实施方式
33.为了使本发明的目的、技术方案和优点更加清楚,下面结合附图和具体实施例对本发明进行详细描述。
34.在此,还需要说明的是,为了避免因不必要的细节而模糊了本发明,在附图中仅仅示出了与本发明的方案密切相关的结构和/或处理步骤,而省略了与本发明关系不大的其他细节。
35.另外,还需要说明的是,术语“包括”、“包含”或者其任何其他变体意在涵盖非排他性的包含,从而使得包括一系列要素的过程、方法、物品或者设备不仅包括那些要素,而且还包括没有明确列出的其他要素,或者是还包括为这种过程、方法、物品或者设备所固有的要素。
36.本发明提供了一种fesibccr非晶磁粉的制备方法,包括如下步骤:
37.s1、将铁矿石或铁矿石与铬砂、硼砂的混合物作为反应原料,采用碳基还原或氢基还原的方式对所述反应原料进行还原熔炼,得到还原产物;
38.s2、对步骤s1得到的所述还原产物进行熔融除渣并合金化,得到精炼钢液;当步骤s1中所述反应原料为铁矿石时,所述熔融除渣后还加入了铬、硼铁和硅铁进行所述合金化;
39.s3、采用气雾化法对步骤s2得到的所述精炼钢液进行快速冷却,得到fesibccr非晶粉体;
40.s4、对步骤s3得到的所述fesibccr非晶粉体进行热处理,得到fesibccr非晶磁粉。
41.其中,当步骤s1中采用所述碳基还原的方式进行还原熔炼时,在步骤s2中所述熔融除渣后还包括脱碳处理;当步骤s1中采用所述氢基还原的方式进行还原熔炼时,在步骤s2中所述熔融除渣后还包括增碳处理。
42.在步骤s1中,所述碳基还原具体包括如下步骤:
43.将所述反应原料粉碎后与还原剂煤粉或焦炭混匀,造团、干燥后放置于高温还原反应炉中,控制还原反应气氛为惰性气氛,还原温度为1000~1350℃,反应时间为10~60min,反应完成后,将得到的反应产物再破碎、磁选、熔分,得到的还原合金即为所述还原产物;
44.或者,将所述反应原料造球、干燥后置于高温还原反应炉中,按照预定的流量通入co还原气体;控制还原反应温度为900~1300℃,反应完成后,将得到的反应产物再破碎、磁选、熔分,得到的还原合金即为所述还原产物。
45.所述氢基还原具体包括如下步骤:
46.将所述反应原料造球、干燥后置于还原装置中,将氢基还原气体以预定速度通入还原反应装置内,控制所述还原反应装置内的温度为900~1300℃,反应完成后,将得到的反应产物再破碎、磁选、熔分,得到的还原合金即为所述还原产物;
47.或者,将所述反应原料制成粉状,与氢基还原气体经加热预处理后一同喷入闪速还原反应管道内,控制所述闪速还原反应管道内温度为900~1500℃,所述氢基还原气体和粉状的所述反应原料在所述闪速还原反应管道内下降的过程中完成闪速还原反应;所述闪
速还原反应管道下部连通熔分装置,在1550~1700℃环境温度设置下,在所述熔分装置中收集得到还原合金,即为所述还原产物。
48.在步骤s2中,所述合金化处理前还包括去除杂质处理,所述合金化的处理温度为1350~1600℃;所述精炼钢液的组成成分及其质量百分比包括:84.9%≤fe≤89.5%、5.3%≤si≤9.2%、2.0≤b≤3.6%、0.3≤c≤1.1%、1.6≤cr≤4.5%、p≤0.015%、s≤0.01%、mn≤0.02%、ti≤0.005%、al≤0.01%。在步骤s3中,采用所述气雾化法时,选择流量为15~25m3/h的氮气,设置雾化温度为1550~1700℃,压力为5~6mpa,得到的所述fesibccr非晶粉体的粒径为10~100μm。
49.在步骤s4中,所述热处理的方式为等温热处理,设置保温温度为300~500℃,保温时间为10~180min。
50.本发明还提供了一种根据上述制备方法制备得到的fesibccr非晶磁粉;所述fesibccr非晶磁粉的化学式为feasibbccdcremf,其中,其中,m代表微量元素mn、p、s、ti、al中的一种或多种混合,下标a、b、c、d、e、f分别表示各组成成分的原子百分含量,且满足下述条件:70≤a≤76、9≤b≤15、9≤c≤15、1≤d≤4、1.5≤e≤4、f≤0.3、a+b+c+d+e+f=100。
51.所述fesibccr非晶磁粉的饱和磁感应强度≥1.08t。
52.下面结合具体的实施例对本发明提供的fesibccr非晶磁粉及其制备方法进行说明。
53.实施例1
54.本实施例提供了一种fesibccr非晶磁粉的制备方法,包括如下步骤:
55.s1、以铁矿石为反应原料,采用氢基还原的方式,将该反应原料制成粉状,与载气n2混合后,再与氢基还原气体h2经加热预处理后一同喷入闪速还原反应管道中,控制闪速还原反应管道内的温度为反应温度为1100℃,反应2.0s后,进入与闪速还原反应管道下部连通的熔分装置中,在1600℃下收集得到还原铁粉;其中,反应原料的加料速率为100g/h,载气n2的流量为0.5l/min,氢基还原气体h2的流量为3l/min。
56.s2、对步骤s1得到的还原铁粉进行熔融除渣、增碳处理及脱硫处理,其中,增碳处理为向还原铁粉中加入焦炭作为增碳剂,并控制增碳剂的添加量为铁矿石的0.11%~0.12%;然后,再加入铬、硼铁和硅铁,在1550℃下进行合金化,得到精炼钢液;其中,铁矿石与铬、硼铁、硅铁的质量比为33:1:27:6;得到的精炼钢液的组成成分及其百分含量包括:fe 87.86%、si 6.6%、b 2.5%、c 0.5%、cr 2.5%、p 0.005%、mn 0.015%、s 0.005%、ti 0.005%、al 0.01%。
57.s3、控制钢液温度在1300℃,采用气雾化法对步骤s2得到的所述精炼钢液进行快速冷却,选择流量为20m3/h的氮气,设置雾化温度为1600℃,压力为5mpa,得到平均粒径为50μm的fesibccr非晶粉体。
58.s4、将步骤s3得到的所述fesibccr非晶粉体置于管式真空退火炉中进行等温热处理,设置保温温度为420℃,保温时间为60min,此时保温温度低于晶化温度,得到fesibccr非晶磁粉,其化学式为fe
73.6
si
11b11
c2cr
2.4
。
59.其中,步骤s1中所述的铁矿石可以来源于天然富矿或人造富矿,其磷含量低于0.1wt%。具体到本实施例中,使用的铁矿石的软化开始温度为1157℃,软化结束温度为1213℃,软化区间为56℃,熔滴温度为1479℃;该铁矿石的化学组成成分如表1所示。
60.表1铁矿石的化学成分
[0061][0062]
经测试,本实施例制备的fesibccr非晶磁粉的形貌图、xrd图和磁滞回线分别如图1-3所示。由图3可以看出,本实施例制备的fesibccr非晶磁粉的饱和磁感应强度为1.33t,表明其具有优异的软磁性能,能够满足实际应用的需求。
[0063]
实施例2
[0064]
实施例2提供了一种fesibccr非晶磁粉的制备方法,与实施例1相比,不同之处在于步骤s1中将铁矿石与铬砂、硼砂的混合物作为反应原料,并控制铁矿石与铬砂、硼砂的质量比为17:1:13;同时,在步骤s2中未加入铬、硼铁和硅铁;其余步骤均与实施例1一致,在此不再赘述。
[0065]
经测试,本实施例制备的化学式为fe
73.6
si
11b11
c2cr
2.4
的fesibccr非晶磁粉的饱和磁感应强度为1.32t。
[0066]
实施例3
[0067]
实施例5提供了一种fesibccr非晶磁粉的制备方法,与实施例1相比,不同之处在于将步骤s1中的还原方式改为碳基还原,并将步骤s2中的增碳处理改为脱碳处理,其余步骤均与实施例1一致,在此不再赘述。
[0068]
其中,碳基还原具体包括如下步骤:
[0069]
将所述反应原料粉碎后与还原剂煤粉混匀,造团、干燥后放置于高温气氛控制炉中,控制还原反应气氛为惰性气氛,还原反应温度为1200℃,反应时间为30min,将得到的反应产物再破碎、磁选、熔分,得到还原合金。需要说明的是,在本发明的其他实施例中,该碳基还原过程的还原反应温度可以根据实际需要在1000~1350℃之间进行调整,反应时间可以在10~60min之间进行调整,均能够达到与本实施例类似的效果。
[0070]
经测试,本实施例制备的化学式为fe
73.6
si
11b11
c2cr
2.4
的fesibccr非晶磁粉的饱和磁感应强度为1.34t。
[0071]
实施例4
[0072]
实施例4提供了一种fesibccr非晶磁粉的制备方法,与实施例2相比,不同之处在于将步骤s1中的还原方式改为与实施例5一致的碳基还原,并将步骤s2中的增碳处理替换为与实施例3一致的脱碳处理,其余步骤均与实施例2一致,在此不再赘述。
[0073]
经测试,本实施例制备的化学式为fe
73.6
si
11b11
c2cr
2.4
的fesibccr非晶磁粉的饱和磁感应强度为1.33t。
[0074]
根据上述实施例可以看出,本发明提供的方法工艺流程短、生产成本低、参数可控性强,能够满足大规模工业化生产的需求;且按照本发明提供的方法制备的fesibccr非晶磁粉均具有优异的软磁性能,能够满足实际应用的需求。
[0075]
同时,需要说明的是,本领域技术人员应当理解,在步骤s1中采用碳基还原的方式进行还原熔炼时,还可以将所述反应原料造球、干燥后置于高温还原反应炉中,按照3~4l/min的流量通入co还原气体;控制还原反应温度为900~1300℃,反应完成后,将得到的反应产物再破碎、磁选、熔分,得到还原合金。在步骤s1中采用氢基还原的方式进行还原熔炼时,还可以将所述反应原料造球、干燥后置于还原装置中,将氢基还原气体以预定速度通入还
原反应装置内,控制所述还原反应装置内的温度为900~1300℃,反应完成后,得到还原合金。在步骤s2中,合金化的处理温度可以根据需要在1350~1600℃之间进行调整;在步骤s3中,氮气的流量可以在15~25m3/h之间进行调整,雾化的温度可以为1550~1700℃,压力可以为5~6mpa;在步骤s4中,热处理的保温温度可以在300~500℃之间进行调整,保温时间可以在10~180min之间进行调整,均属于本发明的保护范围。
[0076]
并且,基于上述制备工艺的调控,能够使步骤s2制得的精炼钢液的组成成分及其质量百分比调节为:84.9%≤fe≤89.5%、5.3%≤si≤9.2%、2.0≤b≤3.6%、0.3≤c≤1.1%、1.6≤cr≤4.5%、p≤0.015%、s≤0.01%、mn≤0.02%、ti≤0.005%、al≤0.01%;进而使制得的fesibccr非晶磁粉的化学式为feasibbccdcremf,其中,m代表微量元素mn、p、s、ti、al中的一种或多种混合,下标a、b、c、d、e、f分别表示各组成成分的原子百分含量,且满足下述条件:70≤a≤76、9≤b≤15、9≤c≤15、1≤d≤4、1.5≤e≤4、f≤0.3、a+b+c+d+e+f=100。
[0077]
综上所述,本发明提供了一种fesibccr非晶磁粉及其制备方法。该制备方法以铁矿石或铁矿石与铬砂、硼砂的混合物作为反应原料,采用碳基还原或氢基还原的方式对反应原料进行还原熔炼,将得到的还原产物熔融除渣并合金化,得到精炼钢液;再采用气雾化法快速冷却精炼钢液,得到fesibccr非晶粉体;经热处理后,得到fesibccr非晶磁粉。本发明能够有效利用冶金工艺与非晶磁粉成型工艺之间的协同作用,在精确控制冶炼条件的基础上有效简化工艺流程,控制杂质含量,并精确控制非晶磁粉的成分,大幅降低生产成本,在保证制得的非晶磁粉具有优异软磁性能的同时以低成本实现大规模高效生产,满足工业化生产与应用的需求。
[0078]
以上实施例仅用以说明本发明的技术方案而非限制,尽管参照较佳实施例对本发明进行了详细说明,本领域的普通技术人员应当理解,可以对本发明的技术方案进行修改或者等同替换,而不脱离本发明技术方案的精神和范围。