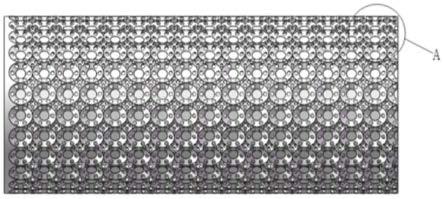
1.本发明涉及激光打印领域,具体涉及一种基于吸入式多喷砂口喷砂的硒鼓磁辊表面处理方法。
背景技术:2.硒鼓也称为是感光鼓,其基本基材一般是由铝制材料,以及基材上涂抹的感光材料所组成。在激光打印机中,70%以上的成像部件集中在硒鼓中,打印质量的好坏实际上在很大程度上是由硒鼓决定的。硒鼓不仅决定了打印质量的好坏,还决定了使用者在使用过程中需要花费的金钱多少。而磁辊又是硒鼓中重要的核心组成部件,也是对图像密度影响最大的部件之一。硒鼓磁辊表面涂有一层石墨材料,以增强磁辊与碳粉和出粉刀之间的摩擦力。硒鼓磁辊采用的材料一般为特殊橡胶,硒鼓磁辊工作时,表面带有电荷(根据不同品牌机器带正或负电荷),吸附碳粉,当输入的打印数据经过处理后,转化为相应的激光信号,通过一组棱镜折射到硒鼓(opc)表面,从而形成电荷潜影。当opc旋转经过硒鼓磁辊时,潜影部分从硒鼓磁辊表面吸附相应碳粉,形成碳粉实相,当opc携带碳粉实相转动至纸张相应位置,经过静电处理的纸张又会将碳粉吸附到纸张表面。这样,一幅图像已经出现在纸面了。为了稳定图形,纸张输出时还要经过热压辊,使碳粉中树脂成分在高温下迅速溶解,从而将碳粉牢牢附着在纸张表面。
3.硒鼓磁辊需要有良好的表面涂层性能,磁辊表面涂层的导电率和表面粗糙度对打印黑度和鬼影有显著的控制作用,表面涂层的导电率不良会直接导致打印鬼影,而表面粗糙度过低会使碳粉的摩擦带电量变小对打印黑度有明显影响,表面涂层的耐磨度直接影响打印的寿命,如果涂层不耐磨页面黑度明显降低,灰度较大页面不均匀现象就会十分明显。
4.现有的磁性碳粉类硒鼓显影辊表面所涂覆的主要是以石墨为主要原料配成的化学混合涂液,采用气动喷枪将化合混合涂液喷洒于表面形成涂层,再经过烘烤干燥,制成成品,生产流程复杂、生产工艺繁琐、化学涂料调配比例等技术难掌握,且易受外界环境的影响。生产出的产品涂层存在耐磨性不够,不耐腐蚀,并且化学涂层在生产及存放的过程中容易因空气水分受潮,打印时涂层容易磨损,造成其打印黑度分辨率等质量下降,对打印质量有一定的影响。同时生产中和生产后所产生的化学废液对环境具有一定的污染性。
5.现有的非磁性碳粉类(带正电碳粉类硒鼓除外)硒鼓显影辊表面是橡胶层作为显影层,存在生产成本高,生产工艺复杂等问题,生产时所产生的废水、废气、废料等对环境污染比较明显;经过回收处理的废弃显影辊很难处理再生利用,一般只有作报废处理,且报废处理时对环境污染大。
技术实现要素:6.本发明的目的在于克服现有技术中存在的上述缺点,提供一种基于吸入式多喷砂口喷砂的硒鼓磁辊表面处理方法。
7.为了实现上述目的,本发明采用的技术方案如下:
一种基于吸入式多喷砂口喷砂的硒鼓磁辊表面处理方法,其特征在于:维持负压式喷砂机固定不动,磁辊匀速转动,在喷砂总管上线性均匀排列的多个喷砂孔同时对硒鼓磁辊表面进行喷砂,负压式喷砂机产生负压将质粒均匀的砂粒吸出,形成高速喷射束将砂粒高速喷射到硒鼓磁辊表面;所述喷砂的次数为两次,第二次喷砂采用的砂粒目数大于第一次喷砂采用的砂粒目数,经过两次喷砂后在硒鼓磁辊表面形成大小不同且相互叠加的凹坑。
8.其中,对硒鼓磁辊表面进行第一次喷砂时,采用60~80目的砂粒,喷砂气压控制在4-6kpa,高速喷射出的砂粒与硒鼓磁辊表面相互碰撞形成的规整球型大凹坑均匀排列于硒鼓磁辊表面;对硒鼓磁辊表面进行进行第二次喷砂时,保持喷砂枪的喷砂角度和位置不变,采用160~180目的砂粒,喷砂气压控制在6-8 kpa,高速喷射出的砂粒在大凹坑表面形成一个至多个小凹坑。
9.两次喷砂所形成的凹坑的直径控制在0.2-0.25mm。
10.所述砂粒为圆型陶瓷砂或石英砂。
11.本发明具有以下优点:1、本发明的硒鼓磁辊表面处理方法采用吸入式多喷砂口喷砂的物理处理方法,采用颗粒目数不同的砂粒,依次经过两次喷砂,在磁辊表面形成大小不同且相互叠加的球型凹坑。喷砂时,通过负压式喷砂机产生的气压将质粒均匀的圆型陶瓷砂或石英砂吸出,形成高速喷射束将圆型陶瓷砂或石英砂颗粒高速喷射到硒鼓磁辊表面进而形成分布均匀的球型凹坑。喷砂管固定不动,磁辊匀速转动,多个喷砂孔在喷砂总管上线性均匀排列同时喷砂,大大提高了喷砂的效率,缩短了喷砂时间。第一次喷砂使用的陶瓷砂或石英砂采用60-80目的粒径,第二次喷砂使用的陶瓷砂或石英砂采用160-180目的粒径,在第一次喷砂的大凹坑表面形成一个至多个小凹坑,球型凹坑的直径控制在0.2-0.25mm之间。圆型陶瓷砂或石英砂粒通过吸入式多喷砂口喷砂在磁辊表面产生分布均匀的凹坑,工艺操作简单,喷砂效率高,节省了喷砂时间。磁辊可以多次回收再利用,耐磨损,延长了使用寿命,极大的降低了成本。磁辊在储存放置时不易受潮,进行喷砂处理的过程中对环境不造成污染,生产消耗的能源低。
12.2、本发明采用吸入式多喷砂口喷砂的物理处理方法,形成如图1、2所示均匀排列的凹坑,提高了磁辊表面的利用率,大大增加了磁辊的携粉效率,使得硒鼓磁辊表面吸附碳粉的面积相较于以往常规的硒鼓磁辊有所增大,从而能够吸附更多的碳粉,提高打印的质量。
13.3、由于本硒鼓磁辊表面处理方法采用的是吸入式喷砂物理处理的方法,所以并不改变硒鼓磁辊材料的性质,不存在材料组织的化学性质和物理性质的改变,以及发生类似采用化学处理改变材料性质等其它的现象。
附图说明
14.图1是本发明凹坑排列示意图;图2是示意图1中a部的局部放大示意图;图3是磁辊表面视图一;图4是磁辊表面视图二。
具体实施方式
15.一种基于吸入式多喷砂口喷砂的硒鼓磁辊表面处理方法,包括以下步骤:第一次喷砂:采用60~80目的陶瓷砂或石英砂,喷砂气压控制在4-6kpa,维持负压式喷砂机固定不动,磁辊匀速转动,在喷砂总管上线性均匀排列的多个喷砂孔同时对硒鼓磁辊表面进行喷砂,负压式喷砂机产生负压将质粒均匀的陶瓷砂或石英砂吸出,形成高速喷射束将砂粒高速喷射到硒鼓磁辊表面,高速喷射出的砂粒与硒鼓磁辊表面相互碰撞形成的规整球型大凹坑均匀排列于硒鼓磁辊表面,如图1所示;第二次喷砂:保持喷砂枪的喷砂角度和位置不变,采用160~180目的砂粒,喷砂气压控制在6-8 kpa,维持负压式喷砂机固定不动,磁辊匀速转动,在喷砂总管上线性均匀排列的多个喷砂孔同时对硒鼓磁辊表面进行喷砂,负压式喷砂机产生负压将质粒均匀的陶瓷砂或石英砂吸出,高速喷射出的砂粒在大凹坑表面形成一个至多个小凹坑,如图2所示;两次喷砂所形成的凹坑的直径控制在0.2-0.25mm。
技术特征:1.一种基于吸入式多喷砂口喷砂的硒鼓磁辊表面处理方法,其特征在于:维持负压式喷砂机固定不动,磁辊匀速转动,在喷砂总管上线性均匀排列的多个喷砂孔同时对硒鼓磁辊表面进行喷砂,负压式喷砂机产生负压将砂粒吸出,形成高速喷射束将砂粒高速喷射到硒鼓磁辊表面;所述喷砂的次数为两次,两次喷砂采用的砂粒目数不同从而在硒鼓磁辊表面形成大小不同且相互叠加的凹坑。2.根据权利要求1所述的一种基于吸入式多喷砂口喷砂的硒鼓磁辊表面处理方法,其特征在于:第二次喷砂采用的砂粒目数大于第一次喷砂采用的砂粒目数。3.根据权利要求2所述的一种基于吸入式多喷砂口喷砂的硒鼓磁辊表面处理方法,其特征在于:对硒鼓磁辊表面进行第一次喷砂时,采用60~80目的砂粒,喷砂气压控制在4-6kpa,高速喷射出的砂粒与硒鼓磁辊表面相互碰撞形成的规整球型大凹坑均匀排列于硒鼓磁辊表面;对硒鼓磁辊表面进行进行第二次喷砂时,保持喷砂枪的喷砂角度和位置不变,采用160~180目的砂粒,喷砂气压控制在6-8 kpa,高速喷射出的砂粒在大凹坑表面形成一个至多个小凹坑。4.根据权利要求1所述的一种基于吸入式多喷砂口喷砂的硒鼓磁辊表面处理方法,其特征在于:两次喷砂所形成的凹坑的直径控制在0.2-0.25mm。5.根据权利要求1所述的一种基于吸入式多喷砂口喷砂的硒鼓磁辊表面处理方法,其特征在于:所述砂粒为陶瓷砂或石英砂。
技术总结本发明公开了一种基于吸入式多喷砂口喷砂的硒鼓磁辊表面处理方法,该方法步骤如下:维持负压式喷砂机固定不动,磁辊匀速转动,在喷砂总管上线性均匀排列的多个喷砂孔同时对硒鼓磁辊表面进行喷砂,负压式喷砂机产生负压将砂粒吸出,形成高速喷射束将砂粒高速喷射到硒鼓磁辊表面;所述喷砂的次数为两次,两次喷砂采用的砂粒目数不同从而在硒鼓磁辊表面形成大小不同且相互叠加的凹坑。本发明采用吸入式多喷砂口喷砂的物理处理方法,提高了磁辊表面的利用率,大大增加了磁辊的携粉效率,工艺操作简单,喷砂效率高,磁辊可以多次回收再利用,耐磨损,延长了使用寿命,极大的降低了成本。本。本。
技术研发人员:陈心流 黄金波
受保护的技术使用者:上海洛辰数码科技有限公司
技术研发日:2022.05.27
技术公布日:2022/8/26