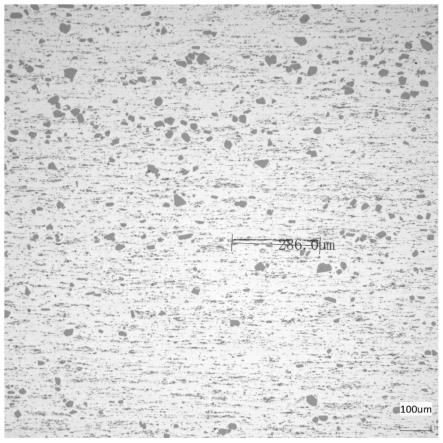
1.本发明涉及金属材料技术领域,特别涉及一种铝钛硼杆及其制备方法。
背景技术:2.国内外普遍采用氟盐法制备al-ti-b系列晶粒细化剂,即将氟钛酸钾和氟硼酸钾的混合盐和液态铝发生化学反应,然后通过连铸连轧或连铸连挤的方式制备9.5mm的线杆。目前铝熔铸行业使用的习惯是将铝钛硼杆原料在线除气或过滤箱前面连续地加入到铝熔体中。而随着铝熔铸、轧制行业对于板、带、箔质量和成本的要求不断提高,他们希望能够将晶粒细化剂的添加位置尽量靠后,包括在所有的净化系统之后添加,即在过滤器到铸机的这段流槽中添加。
3.dr paul cooper and allan barber在第二届国际熔体质量研讨会上发表的论文《review of the latest developments and best use of grain refiners》也介绍了一些铸造厂想要在尽可能晚地添加晶粒细化剂,甚至在所有的净化系统之后,而实现这一目的的主要阻碍就是铝钛硼杆的清洁度和第二相tial3颗粒的溶解速度,对应就是更少的氧化渣和更小的tial3颗粒。目前常规生产技术得到的铝钛硼杆氧化渣含量≤1000μm/cm2,第二相tial3颗粒的平均尺寸25~30μm,导致现有的铝钛硼杆均难以满足高清洁度和第二相tial3颗粒高溶解速度的要求。
技术实现要素:4.为了克服上述现有技术的缺陷,本发明所要解决的技术问题是:提供一种铝液中氧化夹渣量低且tial3颗粒尺寸小的铝钛硼杆及其制备方法。
5.为了解决上述技术问题,本发明提供一种铝钛硼杆的制备方法,包括如下步骤:
6.s1、将氟硼酸钾和部分的氟钛酸钾混合,获得混盐;
7.s2、将铝锭熔化,获得第一铝液;
8.s3、将所述混盐加入所述铝液中并搅拌,获得第二铝液;
9.s4、将剩余部分的氟钛酸钾加入所述第二铝液中并搅拌,对所述第二铝液表面所产生的浮渣进行清理至剩余部分的氟钛酸钾添加完毕,获得第三铝液;
10.s5、向所述第三铝液中加入铝钒中间合金,并依次进行精炼、铸造、轧制后获得所述铝钛硼杆;
11.其中,所述混盐中氟钛酸钾和氟硼酸钾的质量比为(46~50):(50~54)。
12.进一步提供由前述制备方法所制备得到的铝钛硼杆,包含如下组分:
13.2.6~5.5wt%ti,0.15~1.2wt%b,0.02~0.10wt%v,余量为al和不可避免的杂质。
14.本发明的有益效果在于:本发明通过在铝钛硼中加入一定量的铝钒中间体,以通过铝钒中间体中的钒提高浮渣的表面张力,以促使浮渣和铝液充分分离,从而达到降低铝液的含渣量的效果;同时,通过采用分次加入氟钛酸钾的工艺,以获得更小的tial3颗粒和
更加干净的熔体。
附图说明
15.图1所示为本发明在具体实施方式中实施例1所制备得到的铝钛硼的金相照片;
16.图2所示为本发明在具体实施方式中对比例1所制备得到的铝钛硼的金相照片。
具体实施方式
17.为详细说明本发明的技术内容、所实现目的及效果,以下结合实施方式并配合附图予以说明。
18.一种铝钛硼杆的制备方法,包括如下步骤:
19.s1、将氟硼酸钾和部分的氟钛酸钾混合,获得混盐;
20.s2、将铝锭熔化,获得第一铝液;
21.s3、将所述混盐加入所述铝液中并搅拌,获得第二铝液;
22.s4、将剩余部分的氟钛酸钾加入所述第二铝液中并搅拌,对所述第二铝液表面所产生的浮渣进行清理至剩余部分的氟钛酸钾添加完毕,获得第三铝液;
23.s5、向所述第三铝液中加入铝钒中间合金,并依次进行精炼、铸造、轧制后获得所述铝钛硼杆;
24.其中,所述混盐中氟钛酸钾和氟硼酸钾的质量比为(46~50):(50~54)。优选地,所述混盐中氟钛酸钾和氟硼酸钾的质量比为48:52。由于该配比接近第二相中tib2中ti与b的比例,因此相当于先反应生成tib2颗粒,然后再加入剩余的氟钛酸钾,和铝水生成tial3,从而使得生成的tial3会更细小。
25.本发明通过在铝钛硼中加入一定量的铝钒中间体,以通过铝钒中间体中的钒提高浮渣的表面张力,以促使浮渣和铝液充分分离,从而达到降低铝液的含渣量的效果;同时,通过采用分次加入氟钛酸钾的工艺,以获得更小的tial3颗粒和更加干净的熔体。
26.所述铝钒中间体优选为alv5或alv10。
27.优选地,所述氟硼酸钾和氟钛酸钾的粒度为-70μm~200μm≥90%。通过选择适当粒度的原料以有效降低tial3和tib2的颗粒尺寸。其中,氟硼酸钾和氟钛酸钾的粒度是需要严格控制的。其粒度过大或过小均会导致第二相增粗。具体而言,若原材料太细,则反应速度过快,温度迅速上升,恶化第二相;若原材料太粗,则反应时间延长,也会使得第二相增大。
28.优选地,s2具体为:将铝锭熔化,当温度达到740℃以上时用惰性气体进行杂质和氢气的消除处理,获得第一铝液。
29.其中,所述惰性气体优选为氩气。
30.在一种实施方式中,所述剩余部分的氟钛酸钾分至少两次加入所述第二铝液中。优选地,所述剩余部分的氟钛酸钾分2~10次加入所述第二铝液中。
31.优选地,所述混盐和所述氟钛酸钾的加料速率为10~60kg/min,优选为30~50kg/min。
32.优选地,所述搅拌的时间为10~40min,搅拌时的反应温度为740~850℃。通过控制搅拌的时间和搅拌时的反应温度,以促进各原料充分混合,同时促进浮渣与铝液相分离,
以达到降低铝液(熔体)清洁度的效果。
33.优选地,所述精炼的精炼温度为740~880℃,精炼时间为30~120min。通过控制精炼温度和精炼时间,以避免tib2颗粒的团聚和tial3颗粒的长大。
34.优选地,所述冷却的冷却速率为20~60℃/s。通过对熔体进行快速冷却,以获得晶粒细小且第二相细小的铸坯。
35.具体的,所述制备方法包括如下步骤:
36.s1、混料:按比例称取重熔铝锭、氟钛酸钾、氟硼酸钾和铝钒中间合金;将氟硼酸钾和一部分氟钛酸钾混合,获得混盐;
37.s2、熔炼:将纯度为99.7%以上的重熔铝锭投入熔炼炉中熔化,当温度达到740℃以上时用惰性气体进行杂质和氢气的消除处理,之后将干净的液态铝(第一铝液)转移到中频感应热炉内;
38.s3、合金化1:将所述混盐按10~60kg/min的加料速度加入第一铝液中,在此过程中中频炉进行自搅拌或外加机械搅拌,搅拌时间为10~40min以上,反应温度为740~850℃,获得第二铝液;
39.s3、合金化2:将剩余部分的氟钛酸钾按10~60kg/min的加料速度分次加入到第二铝液中,每次加入后均需要将浮渣清理干净后再进行下一次的氟钛酸钾的添加,重复至其全部加入,在此过程中中频炉进行自搅拌或外加机械搅拌,搅拌时间为10~40min以上,反应温度为740~850℃,获得第三铝液;
40.s4、精炼:将第三铝液转入保温炉内,加入铝钒中间合金,并进行除气除渣处理,精炼过程中精炼温度为740~880℃,精炼时间为30~120min,获得铝合金熔体;
41.s5、铸造:将所述铝合金熔体通过水平水冷轮式铜模或其他铸造方式进行快速冷却,冷却速度为20~60℃,获得铸坯;
42.s6、轧制:将所述铸坯进行热轧,轧制成9.5mm的圆杆,进轧温度为400~550℃,获得铝钛硼杆。
43.其中,所述轧制和铸造过程优选为连续进行,以充分利用铸坯自身的热量,从而极大的降低制造成本和提高生产效率。
44.一种由前述铝钛硼杆的制备方法所制备得到的铝钛硼杆,包含如下组分:
45.2.6~5.5wt%ti,0.15~1.2wt%b,0.02~0.10wt%v,余量为al和不可避免的杂质。
46.在本发明中,v的含量是需要被严格控制的,若低于0.02wt%则难以起到降低铝液中含渣量的效果,若高于0.10wt%则导致第二相颗粒长大,恶化晶粒细化能力。
47.在铝钛硼杆中引入一定量的v,以通过v提高浮渣的表面张力,促使浮渣的铝液充分分离,以达到降低铝液中含渣量的效果。经检测,由本发明所提供的铝钛硼杆的制备方法所制备得到的铝钛硼杆中tial3平均颗粒≤20μm;tib2分布弥散,无团聚,且平均粒径≤2μm;氧化夹渣含量≤500μm/cm2。在实际生产过程中,即使在净化系统之后添加,也能获得1级晶粒的薄板。
48.实施例1至4(s1~s4)和对比例1至5(d1~d5)
49.铝钛硼杆的制备方法,包括如下步骤:
50.s1、混料:按比例称取重熔铝锭、氟钛酸钾、氟硼酸钾和铝钒中间合金;将氟硼酸钾
和一部分氟钛酸钾混合,获得混盐;
51.s2、熔炼:将纯度为99.7%以上的重熔铝锭投入熔炼炉中熔化,当温度达到740℃以上时用惰性气体进行杂质和氢气的消除处理,之后将干净的液态铝(第一铝液)转移到中频感应热炉内;
52.s3、合金化1:将所述混盐按40kg/min的加料速度加入第一铝液中,在此过程中中频炉进行自搅拌或外加机械搅拌,搅拌时间为40min,反应温度为800℃,获得第二铝液;
53.s3、合金化2:将剩余部分的氟钛酸钾按40kg/min的加料速度以等量分次的方式加入到第二铝液中,每次加入后均需要将浮渣清理干净后再进行下一次的氟钛酸钾的添加,重复至其全部加入,在此过程中中频炉进行自搅拌或外加机械搅拌,搅拌时间为40min以上,反应温度为800℃,获得第三铝液;
54.s4、精炼:将第三铝液转入保温炉内,加入铝钒中间合金,并进行除气除渣处理,精炼过程中精炼温度为800℃,精炼时间为100min,获得铝合金熔体;
55.s5、铸造:将所述铝合金熔体通过水平水冷轮式铜模或其他铸造方式进行快速冷却,冷却速度为50℃,获得铸坯;
56.s6、轧制:将所述铸坯进行热轧,轧制成9.5mm的圆杆,进轧温度为450℃,获得铝钛硼杆。
57.根据如上制备方法并按如下表1所示的相关参数进行制备,分别获得实施例1至4所制备得到的铝钛硼杆。
58.表1
[0059][0060]
检测例1
[0061]
将实施例1至4所制备得到的铝钛硼杆进行性能检测,检测方法参考ys/t447.1-2011《铝及铝合金晶粒细化用合金线材第一部分:铝-钛-硼合金线材》,结果如表2所示。
[0062]
表2
[0063][0064]
从表2中可以看出,本发明所提供的铝钛硼杆中tial3的平均尺寸≤20μm,tib2的平均尺寸≤1.8μm,且金相中均未出现tib2颗粒团聚的现象,同时氧化夹渣符合要求(≤500μm)。
[0065]
检测例2
[0066]
将实施例1和对比例1所制备的铝钛硼杆进行拍照,结果分别为图1和图2,图中灰色块状的第二相是tial3颗粒,深灰色颗粒状的第二相是tib2颗粒,黑色长条状的是氧化夹渣(并标注了尺寸)。从图中可以看出,本发明所提供的铝钛硼杆的制备方法所制备得到的铝钛硼杆氧化夹渣符合要求且未出现tib2颗粒团聚现象。
[0067]
综上所述,本发明通过在铝钛硼中加入一定量的铝钒中间体,以通过铝钒中间体中的钒提高浮渣的表面张力,以促使浮渣和铝液充分分离,从而达到降低铝液的含渣量的效果;同时,通过采用分次加入氟钛酸钾的工艺,以获得更小的tial3颗粒和更加干净的熔体。
[0068]
以上所述仅为本发明的实施例,并非因此控制本发明的专利范围,凡是利用本发明说明书及附图内容所作的等同变换,或直接或间接运用在相关的技术领域,均同理包括在本发明的专利保护范围内。