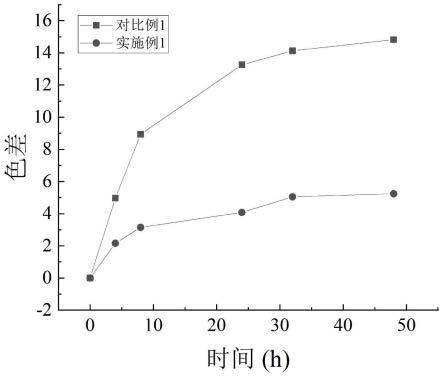
1.本发明涉及首饰合金材料技术领域,尤其涉及一种耐磨耐蚀的首饰黄铜合金及其制备方法。
背景技术:2.首饰在佩戴过程中会受到摩擦、碰撞等机械作用,以及汗液、化妆品、洗涤水、大气等的化学腐蚀作用,要求材料本身有良好的耐磨耐蚀性能,否则在经受摩擦或腐蚀作用后,其表面会失去其亮泽,出现晦暗变色而恶化装饰效果。
3.黄铜由于具有较好的仿金颜色,成为应用广泛的首饰材料。但是,多年来首饰行业没有专门的商业化饰用黄铜合金,而主要沿用了工业生产中的黄铜材料,以h62、h68、h70等牌号最为普遍,这些材料普遍硬度偏低,容易因碰撞摩擦而出现凹坑划痕,耐蚀性差,容易出现晦暗变色而恶化装饰性能。以h70为例,经抛光后的产品,在大气中放置短暂时间后就出现可辨色差,放置3天后,颜色明显暗淡无光。如在腐蚀性环境或气氛中,该材料容易出现脱锌腐蚀,变色更快更严重。h70的铸态硬度不到hv80,容易出现划痕磨花,导致饰品装饰效果变差。
4.首饰不同于工业产品,是佩戴在人体身上的装饰品,使用的材料不能对人体产生有害影响;另外,首饰产品结构纤细复杂,石膏型精密铸造是其主要的成型方式,这就要求首饰材料对人体友好,具有优良的铸造性能,不容易出现缩松、夹杂、气孔等缺陷。但是,多年来报道的一些耐磨黄铜合金材料研究成果,也不适合首饰生产。
5.例如,cn202011421859.1公布了一种种高强耐磨黄铜合金及其制备方法,它采用mn、co、si、pb、al、ni、fe、zn等元素,形成的一种具有优异耐磨性能、较高强度和硬度的黄铜合金,但是该合金含有致敏元素镍和有害元素铅,不适合用作饰品材料。
6.cn200810243568.0公开了一种高强耐磨黄铜,其化学成分为铜的质量含量58~65%,铁的质量含量2~8%,锌的质量含量20~26%,锰的质量含量2~6%,铝的质量含量3~9%,钴的质量含量为0.03%,该合金的硬度较高,但是其颜色装饰效果差,而且其中的铁、锰含量使其不适合饰品的石膏型铸造成型工艺。
7.cn201811015948.9公开了一种基于硅锰化合物相变控制的耐磨黄铜合金,它采用mn、si、zn、pb等合金元素,形成了锰硅金属间化合物,可以提高合金的强度硬度,但是合金中含有有害元素铅,而且锰含量也使得合金不适合采用石膏型精密铸造成型工艺。
8.cn200510080322.2公开了一种高强耐磨黄铜管材的制备方法,它以cu-zn合金为基,通过能形成耐磨相的合金元素如fe、ni、mn、co、ti、cr、si、al多元少量合金元素,在基体上形成成分复杂、硬度高的耐磨相,但是该合金也含有致敏元素镍,且铁、锰等元素也使得其不适合采用石膏型精密铸造成型工艺。
9.cn02119486.6公开了一种多组元耐磨黄铜合金及其管材成形方法,其化学组成为56~65%cu,0.9~6%al,1.5~7%mn,0.4~0.8%si,0.5~1%fe,0.1~0.3%sn,0.1~0.3%pb,0.05~0.4%re,余量为zn。该合金含有害元素铅,且其中的锰和铁使其不能适合
石膏型精密铸造工艺,并且过高的铝含量使其铸造性能变差。
10.cn94111234.9公开了一种高强度耐磨多元黄铜合金及其热处理工艺,其化学组成为59~67%cu,2~4%al,1.5~4.5%mn,0.5~2%si,0.5~2%fe,《0.5%sn,《0.2%ce,余量为zn。该合金中的锰和铁使其不能适合石膏型精密铸造工艺,并且过高的铝含量使其铸造性能变差。
11.综上,现有黄铜材料用作首饰时硬度偏低,耐蚀性不好,耐磨黄铜合金大多数对人体穿戴不友好,其主要用途是机械、工程等领域,其性能不能满足首饰生产的要求。
技术实现要素:12.为了克服现有技术的不足,鉴于首饰产品的特殊结构及性能要求,本发明的目的之一在于提供一种耐磨耐蚀的首饰黄铜合金,其对人体友好,不含有毒有害元素,不引起皮肤刺激反应;颜色接近14k~18k金合金;不含与石膏铸型材料发生化学反应的合金元素,能适合石膏型精密铸造工艺良,满足精细首饰件的铸造成型;合金的铸态硬度达到hv180以上,并可通过时效处理进一步提高硬度,具有优良的耐磨性能;合金具有优良的耐腐蚀性能,尤其是对汗液、化妆品等耐蚀性良好,不容易黯淡变色、出现斑点等。
13.本发明的目的之二在于提供一种采用上述耐磨耐蚀的首饰黄铜合金的制备方法,其制备工艺简单,易于推广。
14.本发明目的之一采用如下技术方案实现:
15.一种耐磨耐蚀的首饰黄铜合金,包括如下重量百分比的组分:
16.20%~24%锌,1.0%~2.0%锡,0.15%~0.5%镓,0.03%~0.09%碲,0.4%~1.0%锗,0.02%~0.08%硼,0.06%~0.15%钌,0.3%~0.8%铝,其余为铜以及不可避免的杂质元素。
17.其中,(1)铜,是合金的基本组成元素。铜本身呈现紫红色,与白色金属化合时,紫红色得以漂白,并提高亮度值。铜含量过高时合金颜色偏紫红,明亮度降低,且不利于铸造质量;铜含量过低时合金颜色淡,合金的加工性能也受到影响。
18.(2)锌,对铜有一定的强化作用,可以调节铜的颜色,降低合金的熔点,有较好的改善铸造性能的作用。但锌含量过高时,对合金的加工性能不利,熔炼铸造容易产生氧化锌夹杂,影响首饰表面质量,而且降低材料的耐蚀性能。综上,铜锌二元合金中,锌对基体的强化作用有限,且需要较高的锌含量才能获得较好的黄色,但是锌含量高时对铸造性能、加工性能和耐蚀性都不利,因此简单黄铜难以满足饰品合金的综合性能要求。
19.(3)锡,可有效改善合金的耐蚀性,提高合金强度和硬度,降低合金熔点。但是过高时会影响合金的韧塑性。
20.(4)镓,有助于改善合金的硬度和黄度,可改善合金的抗氧化变色性能,降低合金熔点,改善合金流动性和铸造性能。但含量高时会增加缩松和热裂倾向。
21.(5)碲,可有效改善合金的强度和硬度,改善合金的磨削性能。但是含量过高时会对韧塑性产生不利影响。
22.(6)锗,有助于改善合金的硬度和黄度,可改善合金的铸造性能和抗氧化变色性能,但是含量过高时有导致合金热裂和晶粒粗大的倾向,使加工性能变差。
23.(7)硼,可以降低合金的表面张力,改善合金的铸造性能和焊接性能,并有助于细
化晶粒,提高合金的硬度。但含量高时容易形成熔渣,反而对铸造性能不利。
24.(8)钌,具有明显的晶粒细化效果,可改善首饰表面抛光效果,提高铜合金的亮度,并有助于改善合金的强度和耐蚀性。但是钌含量高时容易偏聚形成硬质点。
25.(9)铝,有利于改善合金的耐蚀性,增加黄色色度,但是含量过高时对铸造性能不利。
26.综上,鉴于上述锡、镓、碲、锗、硼和钌的性能,本发明的首饰黄铜合金是在铜锌合金的基础上通过引入晶粒细化元素、固溶强化元素、第二相强化元素、间隙强化元素,实现固溶强化、细晶强化、第二相强化等多种强化机制,在保证合金韧塑性基础上提高其强度硬度性能;通过控制合金锌含量,并引入氧活性致钝元素、化学惰性元素,提高合金的腐蚀电位和致钝能力,改善合金的耐蚀性能;通过对铜的颜色产生不同影响的合金元素匹配,实现在降低合金色度值a*基础上,提高亮度值l*和色度值b*,以获得较好的明黄效果。在合金元素选择中,排除对人体有毒副作用的元素,以及在高温下会与石膏铸型材料发生化学反应的合金元素。
27.进一步地,所述不可避免的杂质元素的总含量不超过0.1%。
28.进一步优选地,该耐磨耐蚀的首饰黄铜合金包括如下重量百分比的组分:
29.24%锌,1%锡,0.5%镓,0.09%碲,0.4%锗,0.05%硼,0.08%钌,0.3%铝,其余为铜以及不可避免的杂质。
30.进一步优选地,该耐磨耐蚀的首饰黄铜合金包括如下重量百分比的组分:
31.22%锌,2%锡,0.15%镓,0.03%碲,1.0%锗,0.07%硼,0.1%钌,0.75%铝,其余为铜以及不可避免的杂质。
32.进一步优选地,该耐磨耐蚀的首饰黄铜合金包括如下重量百分比的组分:
33.20%锌,1.5%锡,0.37%镓,0.06%碲,0.7%锗,0.02%硼,0.15%钌,0.5%铝,其余为铜以及不可避免的杂质。
34.本发明目的之二采用如下技术方案实现:
35.一种耐磨耐蚀的首饰黄铜合金的制备方法,包括如下制备步骤:
36.s1:中间合金配置
37.分别配制如下中间合金:含锌40wt%的铜锌合金、含锡10wt%的铜锡合金、含镓10wt%的铜镓合金、含碲10wt%的铜碲合金、含锗10wt%的铜锗合金、含硼5wt%的铜硼合金、含钌5wt%的铜钌合金和含铝10wt%的铜铝合金;上述中间合金均在真空保护气氛下熔炼浇注成锭;
38.s2:合金熔制:以含铜量为99.95wt%的无氧纯铜以及上一个步骤制备的中间合金为原料,配制要求成分的首饰用铜合金。
39.称取如下重量份的组分:
40.纯铜0.1份~13.5份,铜锌合金52份~63份,铜碲合金0.3份~1份,铜铝合金3份~8份,铜锡合金10份~21份,铜硼合金0.5份~1.5份,铜镓合金1.5份~5.1份,铜锗合金4份~10.5份,铜钌合金1.5份~3份;
41.将按比例配制的无氧纯铜、铜锡合金、铜镓合金、铜碲合金、铜锗合金、铜硼合金、铜钌合金及铜铝合金放置在真空粒化机熔炼室的的石墨坩埚内,将铜锌合金放置在二次加料斗内,抽真空至10pa~20pa,然后充入工业纯氩,升温到1130℃~1150℃,待炉料全部变
成熔清,通过机械搅拌装置对金属液进行搅拌,使其温度成分均匀,接着,降温到1040℃~1060℃,然后启动二次加料装置,将铜锌合金加入,待炉料熔清后,启动机械搅拌装置,使金属液成分均匀和温度均匀,最后将温度降低到1000℃~1030℃,将金属液注入清水池中冷却,制成金属珠,将金属珠烘干,即得耐磨耐蚀的首饰黄铜合金原料。
42.进一步地,在步骤s1中,含锌40wt%的铜锌合金采用含铜量为99.95wt%的无氧纯铜配制而成;
43.含锡10wt%的铜锡合金采用含铜量为99.95wt%的无氧纯铜和含锡量为99.95wt%的纯锡配制而成;
44.含镓10wt%的铜镓合金采用含铜量为99.95wt%的无氧纯铜和含镓量为99.9wt%的纯镓配制而成;
45.含碲10wt%的铜碲合金采用含铜量为99.95wt%的无氧纯铜和含碲量为99.9wt%的纯碲配制而成;
46.含锗10wt%的铜锗合金采用含铜量为99.95wt%的无氧纯铜和含锗量为99.9wt%的纯锗配制而成;
47.含硼5wt%的铜硼合金采用含铜量为99.95wt%的无氧纯铜和含硼量为99.95wt%的纯硼配制而成;
48.含钌5wt%的铜钌合金采用含铜量为99.95wt%的无氧纯铜和含钌量为99.95wt%的金属钌配制而成;
49.含铝10wt%的铜铝合金采用含铜量为99.95wt%的无氧纯铜和含铝量为99.95wt%的纯铝配制而成。
50.进一步地,在步骤s2中,无氧纯铜为含铜量99.95wt%的无氧纯铜。
51.进一步地,在步骤s2中,在金属液流进入清水池前,采用高速射流水对准金属液流将其打散并增加冷却效果,射流速度为140m/s~200m/s,三股射流呈120
°
均布,且射流与水平面的夹角为5
°
~10
°
。
52.进一步地,在步骤s2中,金属珠的粒度为2mm~7mm。
53.相比现有技术,本发明的有益效果在于:
54.1、本发明的耐磨耐蚀的首饰黄铜合金在铜锌合金的基础上,通过引入晶粒细化元素、固溶强化元素、第二相强化元素和间隙强化元素,实现固溶强化、细晶强化、第二相强化等多种强化机制,在保证合金韧塑性基础上提高其强度硬度性能;通过控制合金锌含量,并引入氧活性致钝元素和化学惰性元素,提高合金的腐蚀电位和致钝能力,改善合金的耐蚀性能;通过对铜的颜色产生不同影响的合金元素匹配,实现在降低合金色度值a*基础上,提高亮度值l*和色度值b*,以获得较好的明黄效果;在合金元素选择中,排除对人体有毒副作用的元素,以及在高温下会与石膏铸型材料发生化学反应的合金元素。
55.2、本发明的耐磨耐蚀的首饰黄铜合金解决了在铜锌二元合金中,锌对基体的强化作用有限,且需要较高的锌含量才能获得较好的黄色,但是锌含量高时对铸造性能、加工性能和耐蚀性都不利,因此简单黄铜难以满足饰品合金的综合性能要求的问题,本发明所得的首饰黄铜合金的颜色接近14k~18k金合金;不含与石膏铸型材料发生化学反应的合金元素,能适合石膏型精密铸造工艺良,满足精细首饰件的铸造成型;合金的铸态硬度达到hv180以上,并可通过时效处理进一步提高硬度,具有优良的耐磨性能;合金具有优良的耐
腐蚀性能,尤其是对汗液、化妆品等耐蚀性良好,不容易黯淡变色、出现斑点等。
56.3、本发明的耐磨耐蚀的首饰黄铜合金的制备方法所得的黄铜材料可采用连铸或模铸工艺制成坯料,材料的颜色指数l*为85~88,a*为1.9~2.5,b*为23~26,与常用14k~18k黄的颜色较接近。经模拟太阳光照48小时后,其色差不超过5.5,耐光照变色性能是对比例的2.7~3.3倍;经人工汗液浸泡24小时后,其色差不超过10,耐汗液腐蚀性能是对比例的2.5~3倍。材料铸态硬度为hv180~200,是对比例铸态硬度的2倍以上,并可通过时效处理形成弥散分布的中间相,使硬度进一步提高。经人工汗液+塑胶磨料连续腐蚀磨损后,材料的失重率仅为对比例的三分之一。本材料应用于首饰领域,在满足装饰性能的前提下又有很好的耐磨耐蚀性。
附图说明
57.图1为实施例1的黄铜合金与对比例1的黄铜合金经模拟太阳光照的变色情况对比图;
58.图2为实施例1的黄铜合金在人工汗液中的阻抗值图;
59.图3为对比例1的黄铜合金在人工汗液中的阻抗值图;
60.图4为实施例1的黄铜合金与对比例1的黄铜合金在人工汗液中的极化曲线对比图;
61.图5为实施例1的黄铜合金与对比例2的黄铜合金在人工汗液中经浸泡后变色情况对比图;
62.图6为实施例1的黄铜合金与对比例2的黄铜合金的失重率对比图。
具体实施方式
63.下面,结合具体实施方式,对本发明做进一步描述,需要说明的是,在不相冲突的前提下,以下描述的各实施例之间或各技术特征之间可以任意组合形成新的实施例。
64.实施例1
65.一种耐磨耐蚀的首饰黄铜合金,包括如下重量百分比的组分:
66.24%锌,1%锡,0.5%镓,0.09%碲,0.4%锗,0.05%硼,0.08%钌,0.3%铝,其余为铜以及不可避免的杂质。其中,不可避免的杂质元素的总含量不超过0.1%。
67.该首饰黄铜合金采用如下步骤制成:
68.s1:中间合金配置
69.分别配制如下中间合金:含锌40wt%的铜锌合金、含锡10wt%的铜锡合金、含镓10wt%的铜镓合金、含碲10wt%的铜碲合金、含锗10wt%的铜锗合金、含硼5wt%的铜硼合金、含钌5wt%的铜钌合金和含铝10wt%的铜铝合金;上述中间合金均在真空保护气氛下熔炼浇注成锭;
70.其中,含锌40wt%的铜锌合金采用含铜量为99.95wt%的无氧纯铜配制而成;含锡10wt%的铜锡合金采用含铜量为99.95wt%的无氧纯铜和含锡量为99.95wt%的纯锡配制而成;含镓10wt%的铜镓合金采用含铜量为99.95wt%的无氧纯铜和含镓量为99.9wt%的纯镓配制而成;含碲10wt%的铜碲合金采用含铜量为99.95wt%的无氧纯铜和含碲量为99.9wt%的纯碲配制而成;含锗10wt%的铜锗合金采用含铜量为99.95wt%的无氧纯铜和
含锗量为99.9wt%的纯锗配制而成;含硼5wt%的铜硼合金采用含铜量为99.95wt%的无氧纯铜和含硼量为99.95wt%的纯硼配制而成;含钌5wt%的铜钌合金采用含铜量为99.95wt%的无氧纯铜和含钌量为99.95wt%的金属钌配制而成;含铝10wt%的铜铝合金采用含铜量为99.95wt%的无氧纯铜和含铝量为99.95wt%的纯铝配制而成。
71.s2:合金熔制
72.称取如下重量份的组分:
73.纯铜13份,铜锌合金62.5份,铜碲合金0.9份,铜铝合金3.05份,铜锡合金10.3份,铜硼合金1份,铜镓合金5.1份,铜锗合金4.05份,铜钌合金1.5份;
74.将按比例配制的99.95wt%的无氧纯铜、铜锡合金、铜镓合金、铜碲合金、铜锗合金、铜硼合金、铜钌合金及铜铝合金放置在真空粒化机熔炼室的的石墨坩埚内,将铜锌合金放置在二次加料斗内,抽真空至15pa,然后充入工业纯氩,升温到1140℃,待炉料全部变成熔清,通过机械搅拌装置对金属液进行搅拌,使其温度成分均匀,接着,降温到1050℃,然后启动二次加料装置,将铜锌合金加入,待炉料熔清后,启动机械搅拌装置,使金属液成分均匀和温度均匀,最后将温度降低到1020℃,将金属液注入清水池中冷却,制成粒度为3mm~6mm金属珠,将金属珠烘干,即得耐磨耐蚀的首饰黄铜合金原料。
75.其中,在金属液流进入清水池前,采用高速射流水对准金属液流将其打散并增加冷却效果,射流速度为150m/s,三股射流呈120
°
均布,且射流与水平面的夹角为7
°
。
76.实施例2
77.一种耐磨耐蚀的首饰黄铜合金,包括如下重量百分比的组分:
78.22%锌,2%锡,0.15%镓,0.03%碲,1.0%锗,0.07%硼,0.1%钌,0.75%铝,其余为铜以及不可避免的杂质。其中,不可避免的杂质元素的总含量不超过0.1%。
79.该首饰黄铜合金采用如下步骤制成:
80.s1:中间合金配置
81.分别配制如下中间合金:含锌40wt%的铜锌合金、含锡10wt%的铜锡合金、含镓10wt%的铜镓合金、含碲10wt%的铜碲合金、含锗10wt%的铜锗合金、含硼5wt%的铜硼合金、含钌5wt%的铜钌合金和含铝10wt%的铜铝合金;上述中间合金均在真空保护气氛下熔炼浇注成锭;
82.其中,含锌40wt%的铜锌合金采用含铜量为99.95wt%的无氧纯铜配制而成;含锡10wt%的铜锡合金采用含铜量为99.95wt%的无氧纯铜和含锡量为99.95wt%的纯锡配制而成;含镓10wt%的铜镓合金采用含铜量为99.95wt%的无氧纯铜和含镓量为99.9wt%的纯镓配制而成;含碲10wt%的铜碲合金采用含铜量为99.95wt%的无氧纯铜和含碲量为99.9wt%的纯碲配制而成;含锗10wt%的铜锗合金采用含铜量为99.95wt%的无氧纯铜和含锗量为99.9wt%的纯锗配制而成;含硼5wt%的铜硼合金采用含铜量为99.95wt%的无氧纯铜和含硼量为99.95wt%的纯硼配制而成;含钌5wt%的铜钌合金采用含铜量为99.95wt%的无氧纯铜和含钌量为99.95wt%的金属钌配制而成;含铝10wt%的铜铝合金采用含铜量为99.95wt%的无氧纯铜和含铝量为99.95wt%的纯铝配制而成。
83.s2:合金熔制
84.称取如下重量份的组分:
85.纯铜0.16份,铜锌合金57.3份,铜碲合金0.3份,铜铝合金7.82份,铜锡合金20.5
份,铜硼合金1.5份,铜镓合金1.53份,铜锗合金10.2份,铜钌合金2份;
86.将按比例配制的99.95wt%的无氧纯铜、铜锡合金、铜镓合金、铜碲合金、铜锗合金、铜硼合金、铜钌合金及铜铝合金放置在真空粒化机熔炼室的的石墨坩埚内,将铜锌合金放置在二次加料斗内,抽真空至10pa,然后充入工业纯氩,升温到1130℃,待炉料全部变成熔清,通过机械搅拌装置对金属液进行搅拌,使其温度成分均匀,接着,降温到1040℃,然后启动二次加料装置,将铜锌合金加入,待炉料熔清后,启动机械搅拌装置,使金属液成分均匀和温度均匀,最后将温度降低到1000℃,将金属液注入清水池中冷却,制成粒度为4mm~7mm金属珠,将金属珠烘干,即得耐磨耐蚀的首饰黄铜合金原料。
87.其中,在金属液流进入清水池前,采用高速射流水对准金属液流将其打散并增加冷却效果,射流速度为100m/s,三股射流呈120
°
均布,且射流与水平面的夹角为10
°
。
88.实施例3
89.一种耐磨耐蚀的首饰黄铜合金,包括如下重量百分比的组分:
90.20%锌,1.5%锡,0.37%镓,0.06%碲,0.7%锗,0.02%硼,0.15%钌,0.5%铝,其余为铜以及不可避免的杂质。其中,不可避免的杂质元素的总含量不超过0.1%。
91.该首饰黄铜合金采用如下步骤制成:
92.s1:中间合金配置
93.分别配制如下中间合金:含锌40wt%的铜锌合金、含锡10wt%的铜锡合金、含镓10wt%的铜镓合金、含碲10wt%的铜碲合金、含锗10wt%的铜锗合金、含硼5wt%的铜硼合金、含钌5wt%的铜钌合金和含铝10wt%的铜铝合金;上述中间合金均在真空保护气氛下熔炼浇注成锭;
94.其中,含锌40wt%的铜锌合金采用含铜量为99.95wt%的无氧纯铜配制而成;含锡10wt%的铜锡合金采用含铜量为99.95wt%的无氧纯铜和含锡量为99.95wt%的纯锡配制而成;含镓10wt%的铜镓合金采用含铜量为99.95wt%的无氧纯铜和含镓量为99.9wt%的纯镓配制而成;含碲10wt%的铜碲合金采用含铜量为99.95wt%的无氧纯铜和含碲量为99.9wt%的纯碲配制而成;含锗10wt%的铜锗合金采用含铜量为99.95wt%的无氧纯铜和含锗量为99.9wt%的纯锗配制而成;含硼5wt%的铜硼合金采用含铜量为99.95wt%的无氧纯铜和含硼量为99.95wt%的纯硼配制而成;含钌5wt%的铜钌合金采用含铜量为99.95wt%的无氧纯铜和含钌量为99.95wt%的金属钌配制而成;含铝10wt%的铜铝合金采用含铜量为99.95wt%的无氧纯铜和含铝量为99.95wt%的纯铝配制而成。
95.s2:合金熔制
96.称取如下重量份的组分:
97.纯铜13.28份,铜锌合金52.1份,铜碲合金0.9份,铜铝合金5.16份,铜锡合金15.5份,铜硼合金0.5份,铜镓合金3.8份,铜锗合金7.1份,铜钌合金3份;
98.将按比例配制的99.95wt%的无氧纯铜、铜锡合金、铜镓合金、铜碲合金、铜锗合金、铜硼合金、铜钌合金及铜铝合金放置在真空粒化机熔炼室的的石墨坩埚内,将铜锌合金放置在二次加料斗内,抽真空至10pa,然后充入工业纯氩,升温到1150℃,待炉料全部变成熔清,通过机械搅拌装置对金属液进行搅拌,使其温度成分均匀,接着,降温到1060℃,然后启动二次加料装置,将铜锌合金加入,待炉料熔清后,启动机械搅拌装置,使金属液成分均匀和温度均匀,最后将温度降低到1030℃,将金属液注入清水池中冷却,制成粒度为2mm~
5mm金属珠,将金属珠烘干,即得耐磨耐蚀的首饰黄铜合金原料。
99.其中,在金属液流进入清水池前,采用高速射流水对准金属液流将其打散并增加冷却效果,射流速度为200m/s,三股射流呈120
°
均布,且射流与水平面的夹角为5
°
。
100.对比例1
101.对比例1的黄铜合金为h62。
102.对比例2
103.对比例2的黄铜合金为h70。
104.性能测试:
105.对实施例1、对比例1和对比例2的黄铜合金,测试其物理、化学和力学性能,测试内容如下:
106.(1)色差测试
107.将实施例1与18k黄的标准3n颜色进行对比,对比结果如下:
108.表1实施例1与18k黄的标准3n颜色对比
[0109][0110]
从上述表1可知,实施例1的颜色指数l*为87.4,a*为2.05,b*为23.8,与18k黄的标准3n颜色较接近。
[0111]
(2)变色情况测试
[0112]
将实施例1的黄铜合金与对比例1的黄铜合金经模拟太阳光照48小时后,测试其变色情况,结果如图1所示。
[0113]
在图1中,经模拟太阳光照48小时后,实施例1的黄铜合金色差不超过5.5,耐光照变色性能是对比例1的2.9倍。
[0114]
(3)耐蚀性测试
[0115]
将实施例1、对比例1的黄铜合金在人工汗液中,进行耐蚀性测试,测试结果如图2-4所示。
[0116]
在图2和图3中,实施例1在人工汗液中的阻抗值为6200ω,而对比例1为3598ω。
[0117]
在图4中,实施例1在人工汗液中的自腐蚀电位为-0.129v,自腐蚀电位为-0.162v。
[0118]
从上述图中可看出,实施例1的黄铜合金的耐蚀性要明显优于对比例1的黄铜合金的耐蚀性。
[0119]
(4)耐汗液腐蚀性测试
[0120]
将实施例1、对比例2的黄铜合金在人工汗液中,经人工汗液浸泡24小时后,测试其变色情况,结果如图5所示。
[0121]
在图中可看出,经人工汗液浸泡24小时后,实施例1的黄铜合金色差不超过10,耐汗液腐蚀性能是对比例2的2.7倍。
[0122]
(5)硬度性能测试
[0123]
将实施例1、对比例1、对比例2的黄铜合金,进行硬度性能测试,结果如下表所示。
[0124]
表2实施例1与对比例的硬度对比表
[0125]
材料铸态硬度时效态硬度实施例1hv185hv199对比例1hv91hv92对比例2hv77hv84
[0126]
从上表可看出,实施例1的黄铜合金的铸态硬度为hv185,是对比例的2倍以上,并可通过时效处理形成弥散分布的中间相,使硬度进一步提高到hv199。
[0127]
(6)腐蚀磨损测试
[0128]
将实施例1、对比例1的黄铜合金,采用人工汗液+塑胶磨料的结合方式,进行强力腐蚀磨损试验,结果如下图6所示。
[0129]
从图中可看出,实施例1的失重率仅为对比例1的三分之一。因此,实施例1的耐磨蚀性能明显优于对比例1。
[0130]
上述实施方式仅为本发明的优选实施方式,不能以此来限定本发明保护的范围,本领域的技术人员在本发明的基础上所做的任何非实质性的变化及替换均属于本发明所要求保护的范围。