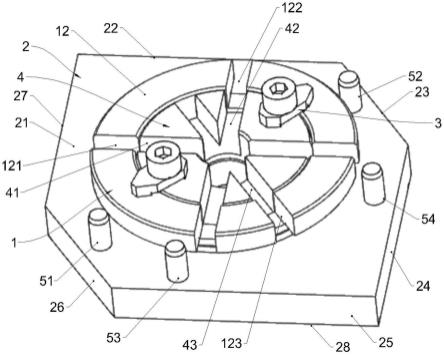
1.本实用新型涉及机械工装夹具,具体涉及一种用于加工带槽套筒的磨夹具。
背景技术:2.磨削具有对称度要求的端面槽,在机械加工行业中十分常见。图1和图2中的带槽套筒1是某种燃油喷射系统的重要零部件之一,该带槽套筒1淬火后硬度高达hrc62以上。该带槽套筒1包括基座11以及设置在基座11上的圆环12,基座11和圆环12的中部具有沿上下方向贯通的中孔13,圆环12上设置有多个通槽,多个通槽分别为第一通槽121、第二通槽122以及第三通槽123,第一通槽121沿左右方向贯通,第二通槽122沿前后方向贯通,并且第一通槽121和第二通槽122组合形成十字形结构,第一通槽121的中心线与第二通槽122的中心线互相垂直,并且这两条中心线的交点经过中孔轴线,第三通槽123位于圆环12的右后部,第三通槽123沿中孔轴线向外贯通,第三通槽123的中心线与第一通槽121的中心线的夹角为α
°
(α可以为50-60,例如52、55、57或者58)。此零件的加工难点在于保证各个通槽与中孔的对称度0.02mm要求,同时保证第一通槽121的中心线与第二通槽122的中心线的夹角为90
°±5′
,保证第三通槽123的中心线与第一通槽121的中心线的夹角为α
°±5′
。该带槽套筒1在平面磨床上磨各个通槽时,必须依靠夹具才能有效保证对称度及夹角的技术要求。在批量加工时,要提高生产效率,减少计量,还必须依靠检验装置才能提高工效。
3.cn205254727u公开了一种磨槽装置,包括两个带腰形缺口的压板、定位轴、底座、压紧螺钉和定位螺钉;所述定位轴通过定位螺钉固定在底座的中心孔位置,工件的台阶孔套在定位轴上,工件的外圆底座通过两个压板的腰形缺口及压紧螺钉压紧在底座上。所述定位轴外圆与底座的同轴度要求为φ0.012mm。所述底座上下两面平行度为0.01mm,且与外圆保证垂直度0.012mm。该实用新型通过两个压板将工件压紧,而压板上的腰形缺口设计便于拆卸、快速更换工件。所述定位轴外圆与底座的同轴度要求为φ0.012mm。所述底座上下两面平行度为0.01mm,且与外圆保证垂直度0.012mm,就省去了原先要求保证工件的槽外圆与内台阶孔的同轴度要求,简化了加工工序。毋庸置疑,上述专利文献公开的技术方案是所属技术领域的一种有益的尝试。
技术实现要素:4.有鉴于此,本实用新型的目的在于提供一种用于加工带槽套筒的磨夹具,兼具定位以及检测两种功能,加工后不需要每件带槽套筒均进行三坐标计量,直接依靠磨夹具测量,加工效率高,质量稳定,特别适合于批量生产。
5.本实用新型中的一种用于加工带槽套筒的磨夹具,包括夹具底座,还包括设置在所述夹具底座上的夹持组件以及检测组件;所述夹持组件包括定位构件以及用于与带槽套筒的中孔配合的定位凸台,所述定位凸台向上凸出于所述夹具底座,所述定位凸台上对应带槽套筒上待加工的多个通槽的位置分别设置有一个让位槽,所述定位构件能够将带槽套筒固定;所述检测组件包括间隔设置在所述夹具底座上的多个检测销。
6.进一步,所述定位构件设置有两个,两个定位构件均包括定位板和紧固件,所述定位板通过所述紧固件以能够拆卸的方式固定在所述定位凸台上,并且所述定位板能够沿径向向外伸出于所述定位凸台,所述定位板与所述夹具底座之间形成用于夹持带槽套筒的夹持空间。
7.进一步,所述紧固件为螺栓,所述定位凸台上设置有用于与所述紧固件配合的螺纹孔。
8.进一步,所述定位板上设置有腰形通孔,所述腰形通孔的长度沿径向,所述螺栓穿过所述腰形通孔并与所述螺纹孔连接;通过旋松所述螺栓,使所述定位板在径向上的位置能够调节,以实现所述定位板能够沿径向向内缩回所述定位凸台或者能够沿径向向外伸出于所述定位凸台。
9.进一步,多个所述让位槽的槽宽大于对应的待加工的通槽的槽宽,多个所述让位槽的槽深大于对应的待加工的通槽的槽深。
10.进一步,多个所述让位槽分别为第一让位槽、第二让位槽以及第三让位槽,所述第一让位槽的位置与带槽套筒上待加工的第一通槽的位置相对应,所述第二让位槽的位置与带槽套筒上待加工的第二通槽的位置相对应,所述第三让位槽的位置与带槽套筒上待加工的第三通槽的位置相对应。
11.进一步,所述夹具底座为八面体结构,所述八面体结构具有上端面、前端面、右斜面、右端面、后端面、左斜面、左端面以及下端面,所述前端面与后端面互相平行,所述前端面与左端面互相垂直,所述右端面与左端面互相平行,所述右斜面与前端面呈180
°‑
α
°
夹角,所述左斜面与后端面呈180
°‑
α
°
夹角。
12.进一步,多个所述检测销的位置均与多个所述让位槽错开。
13.进一步,多个所述检测销的轴线均沿上下方向,以保证所述检测销的轴线与带槽套筒上待加工的各个通槽的侧壁平行。
14.进一步,多个所述检测销分别为第一检测销、第二检测销、第三检测销以及第四检测销,所述第一检测销、第二检测销、第三检测销以及第四检测销的轴线均与同一圆相交;四个所述检测销的半径均为r,带槽套筒上待加工的第一通槽、第二通槽以及第三通槽的槽宽均为s,所述第一检测销的轴线与带槽套筒上待加工的第一通槽的中心线之间的距离、所述第一检测销的轴线与带槽套筒上待加工的第二通槽的中心线之间的距离、所述第二检测销的轴线与带槽套筒上待加工的第一通槽的中心线之间的距离、所述第二检测销的轴线与带槽套筒上待加工的第二通槽的中心线之间的距离、所述第三检测销的轴线与带槽套筒上待加工的第三通槽的中心线之间的距离以及所述第四检测销的轴线与带槽套筒上待加工的第三通槽的中心线之间的距离均为l。
15.本实用新型的有益效果是:
16.1、本实用新型的夹持组件在加工时能够对带槽套筒进行定位,让位槽能够在加工时避让磨床砂轮,打磨过程中以及打磨完成后,均能够以多个检测销为依据,对加工后的通槽与中孔的对称度进行检测,从而实现在一个磨夹具上兼具定位以及检测两种功能,加工后不需要每件带槽套筒均进行三坐标计量,直接依靠磨夹具测量,加工效率高,质量稳定,特别适合于批量生产;
17.2、本实用新型的夹具底座的具有多个分别与待加工通槽相匹配的面,能够与平面
磨床上的定位块的定位基准面配合,便于磨床砂轮对各个通槽进行打磨;
18.3、本实用新型的多个检测销的位置以及大小设计合理,使得测量的标准值大小相同,使用外径千分尺测量时非常简便,显著提高了测量效率。
附图说明
19.为了使本实用新型的目的、技术方案和有益效果更加清楚,本实用新型提供如下附图进行说明:
20.图1为应用本实用新型加工完成的带槽套筒的结构示意图;
21.图2为图1的a-a截面示意图;
22.图3为本实用新型与带槽套筒配合的结构示意图;
23.图4为本实用新型与带槽套筒配合的俯视示意图(图中虚线为带槽套筒);
24.图5为本实用新型的俯视示意图;
25.图6为图5的ⅰ处局部放大示意图;
26.图7为本实用新型的截面示意图。
27.附图中标记如下:
28.1-带槽套筒,11-基座,12-圆环,121-第一通槽,122-第二通槽,123-第三通槽,13-中孔;
29.2-夹具底座,21-上端面,22-前端面,23-右斜面,24-右端面,25-后端面,26-左斜面,27-左端面,28-下端面;
30.3-定位构件,31-定位板,311-腰形通孔,32-紧固件;
31.4-定位凸台,41-第一让位槽,42-第二让位槽,43-第三让位槽;
32.51-第一检测销,52-第二检测销,53-第三检测销,54-第四检测销。
具体实施方式
33.下面结合附图对本实用新型作详细说明。
34.如图3-图7所示,本实施例中的一种用于加工带槽套筒的磨夹具,包括夹具底座2,还包括设置在夹具底座2上的夹持组件以及检测组件;夹持组件包括定位构件3以及用于与带槽套筒1的中孔13配合的定位凸台4,定位凸台4向上凸出于夹具底座2,定位凸台4上对应带槽套筒1上待加工的多个通槽的位置分别设置有一个让位槽,定位构件3能够将带槽套筒1固定;检测组件包括间隔设置在夹具底座2上的多个检测销。夹持组件在加工时能够对带槽套筒1进行定位,让位槽能够在加工时避让磨床砂轮,打磨过程中以及打磨完成后,均能够以多个检测销为依据,对加工后的通槽与中孔13的对称度进行检测,从而实现在一个磨夹具上兼具定位以及检测两种功能,加工后不需要每件带槽套筒1均进行三坐标计量,直接依靠磨夹具测量,加工效率高,质量稳定,特别适合于批量生产。
35.本实施例中,定位构件3设置有两个,两个定位构件3均包括定位板31和紧固件32,定位板31通过紧固件32以能够拆卸的方式固定在定位凸台4上,并且定位板31能够沿径向向外伸出于定位凸台4,定位板31与夹具底座2之间形成用于夹持带槽套筒1的夹持空间。在本实施例中,紧固件32为螺栓,定位凸台4上设置有用于与紧固件32配合的螺纹孔。在本实施例中,定位板31上设置有腰形通孔311,腰形通孔311的长度沿径向,螺栓穿过腰形通孔
311并与螺纹孔连接;通过旋松螺栓,使定位板31在径向上的位置能够调节,以实现定位板31能够沿径向向内缩回定位凸台4或者能够沿径向向外伸出于定位凸台4。使用时,首先将螺栓旋松,然后将定位板31沿径向向内缩回定位凸台4,接着将带槽套筒1的中孔13套在定位凸台4上,直至带槽套筒1的下端面28与夹具底座2的上端面21接触,随后将定位板31沿径向向外伸出于定位凸台4,最后旋紧螺栓,将带槽套筒1固定在定位板31与夹具底座2之间。
36.本实施例中,多个让位槽的槽宽大于对应的待加工的通槽的槽宽,多个让位槽的槽深大于对应的待加工的通槽的槽深,保证让位槽能够在加工时避让磨床砂轮。
37.本实施例中,多个让位槽分别为第一让位槽41、第二让位槽42以及第三让位槽43,第一让位槽41的位置与带槽套筒1上待加工的第一通槽121的位置相对应,第二让位槽42的位置与带槽套筒1上待加工的第二通槽122的位置相对应,第三让位槽43的位置与带槽套筒1上待加工的第三通槽123的位置相对应。
38.本实施例中,夹具底座2为八面体结构,八面体结构具有上端面21、前端面22、右斜面23、右端面24、后端面25、左斜面26、左端面27以及下端面28,前端面22与后端面25互相平行,前端面22与左端面27互相垂直,右端面24与左端面27互相平行,右斜面23与前端面22呈180
°‑
α
°
夹角,左斜面26与后端面25呈180
°‑
α
°
夹角。这使得前端面22和后端面25均与带槽套筒1上待加工的第一通槽121的中心线平行,右端面24和左端面27均与带槽套筒1上待加工的第二通槽122的中心线平行,右斜面23和左斜面26均与带槽套筒1上待加工的第三通槽123的中心线平行。加工时,上端面21用于与带槽套筒1的下端面28相接触,前端面22、右斜面23、右端面24、后端面25、左斜面26以及左端面27能够作为加工的基准面,前端面22、右斜面23、右端面24、后端面25、左斜面26以及左端面27均能够用于与平面磨床上的定位块的定位基准面接触,然后使用磨床砂轮打磨各个通槽,能够降低加工难度,缩短加工用时,提高加工效率。
39.本实施例中,多个检测销的位置均与多个让位槽错开,能够防止检测销影响磨床砂轮进给。
40.本实施例中,多个检测销的轴线均沿上下方向,以保证检测销的轴线与带槽套筒1上待加工的各个通槽的侧壁平行,从而能够通过测量检测销的外壁与带槽套筒1上待加工的各个通槽的侧壁之间的间距是否符合要求,实现检测各个通槽的轴线夹具以及各槽与中孔13的对称度是否符合要求。
41.本实施例中,多个检测销分别为第一检测销51、第二检测销52、第三检测销53以及第四检测销54,第一检测销51、第二检测销52、第三检测销53以及第四检测销54的轴线均与同一圆相交,并且该圆的圆心在带槽套筒1的中孔13的轴线上;四个检测销的半径均为r,带槽套筒1上待加工的第一通槽121、第二通槽122以及第三通槽123的槽宽均为s,第一检测销51的轴线与带槽套筒1上待加工的第一通槽121的中心线之间的距离、第一检测销51的轴线与带槽套筒1上待加工的第二通槽122的中心线之间的距离、第二检测销52的轴线与带槽套筒1上待加工的第一通槽121的中心线之间的距离、第二检测销52的轴线与带槽套筒1上待加工的第二通槽122的中心线之间的距离、第三检测销53的轴线与带槽套筒1上待加工的第三通槽123的中心线之间的距离以及第四检测销54的轴线与带槽套筒1上待加工的第三通槽123的中心线之间的距离均为l,由上可知,第一通槽121靠近第一检测销51一侧的侧壁与第一检测销51的外壁之间的最大距离、第一通槽121靠近第二检测销52一侧的侧壁与第二
检测销52的外壁之间的最大距离、第二通槽122靠近第一检测销51一侧的侧壁与第一检测销51的外壁之间的最大距离、第二通槽122靠近第二检测销52一侧的侧壁与第二检测销52的外壁之间的最大距离、第三通槽123靠近第三检测销53一侧的侧壁与第三检测销53的外壁之间的最大距离以及第三通槽123靠近第四检测销54一侧的侧壁与第四检测销54的外壁之间的最大距离均为l+r-s/2,而各个通槽的侧壁与对应检测销的外壁之间的距离可以使用外径千分尺直接测量得出,因此本实施例通过合理设置各个检测销的位置以及大小,使得测量的标准值大小相同,使用外径千分尺测量时非常简便,显著提高了测量效率。
42.本实施例在使用时按照以下步骤:
43.s1、带槽套筒1的固定;首先将螺栓旋松,然后将定位板31沿径向向内缩回定位凸台4,接着将带槽套筒1的中孔13套在定位凸台4上,直至带槽套筒1的下端面28与夹具底座2的上端面21接触,随后将定位板31沿径向向外伸出于定位凸台4,最后旋紧螺栓,将带槽套筒1固定在定位板31与夹具底座2之间。
44.s2、在平面磨床的磁台上安装一个定位块,该定位块具有定位基准面;
45.s3、将夹具底座2放在定位块上,并使夹具底座2的前端面22或者后端面25与上述定位基准面贴合,上磁固定夹具底座2,通过磨床砂轮的侧面打磨带槽套筒1的第一通槽121的两个侧壁;打磨加工过程中,使用外径千分尺测量加工后的第一通槽121靠近第一检测销51一侧的侧壁与第一检测销51的外壁之间的最大距离,并且使用外径千分尺测量加工后的第一通槽121靠近第二检测销52一侧的侧壁与第二检测销52的外壁之间的最大距离;若此步骤所测量的两个尺寸相对于标准值l+r-s/2的误差不小于0.005mm,则继续使用磨床砂轮进行打磨第一通槽121的两个侧壁,若此步骤所测量的两个尺寸相对于标准值l+r-s/2的误差小于0.005mm,则进入下一步;
46.s4、退磁松开夹具底座2后,旋转夹具底座2,并使夹具底座2的右端面24或者左端面27与上述定位基准面贴合,上磁固定夹具底座2,通过磨床砂轮的侧面打磨带槽套筒1的第二通槽122的两个侧壁;加工完成后,使用外径千分尺测量加工后的第二通槽122靠近第一检测销51一侧的侧壁与第一检测销51的外壁之间的最大距离,并且使用外径千分尺测量加工后的第二通槽122靠近第二检测销52一侧的侧壁与第二检测销52的外壁之间的最大距离,保证此步骤所测量的两个尺寸相对于标准值l+r-s/2的误差小于0.005mm;若此步骤所测量的两个尺寸相对于标准值l+r-s/2的误差不小于0.005mm,则继续使用磨床砂轮进行打磨第二通槽122的两个侧壁,若此步骤所测量的两个尺寸相对于标准值l+r-s/2的误差小于0.005mm,则进入下一步;
47.s5、退磁松开夹具底座2后,旋转夹具底座2,并使夹具底座2的右斜面23或者左斜面26与上述定位基准面贴合,上磁固定夹具底座2,通过磨床砂轮的侧面打磨带槽套筒1的第三通槽123的两个侧壁;加工完成后,使用外径千分尺测量加工后的第三通槽123靠近第三检测销53一侧的侧壁与第三检测销53的外壁之间的最大距离,并且使用外径千分尺测量加工后的第三通槽123靠近第四检测销54一侧的侧壁与第四检测销54的外壁之间的最大距离,保证此步骤所测量的两个尺寸相对于标准值l+r-s/2的误差小于0.005mm;若此步骤所测量的两个尺寸相对于标准值l+r-s/2的误差不小于0.005mm,则继续使用磨床砂轮进行打磨第三通槽123的两个侧壁,若此步骤所测量的两个尺寸相对于标准值l+r-s/2的误差小于0.005mm,则进入下一步;
48.s6、退磁松开夹具底座2,在检验平台上以多个检测销为依据,对加工后的通槽与中孔13的对称度进行检测,检测方法与步骤s3-s5中测量的原理相同,此处不再赘述。
49.最后说明的是,以上实施例仅用以说明本实用新型的技术方案而非限制,尽管参照较佳实施例对本实用新型进行了详细说明,本领域的普通技术人员应当理解,可以对本实用新型的技术方案进行修改或者等同替换,而不脱离本实用新型技术方案的宗旨和范围,其均应涵盖在本实用新型的权利要求范围当中。