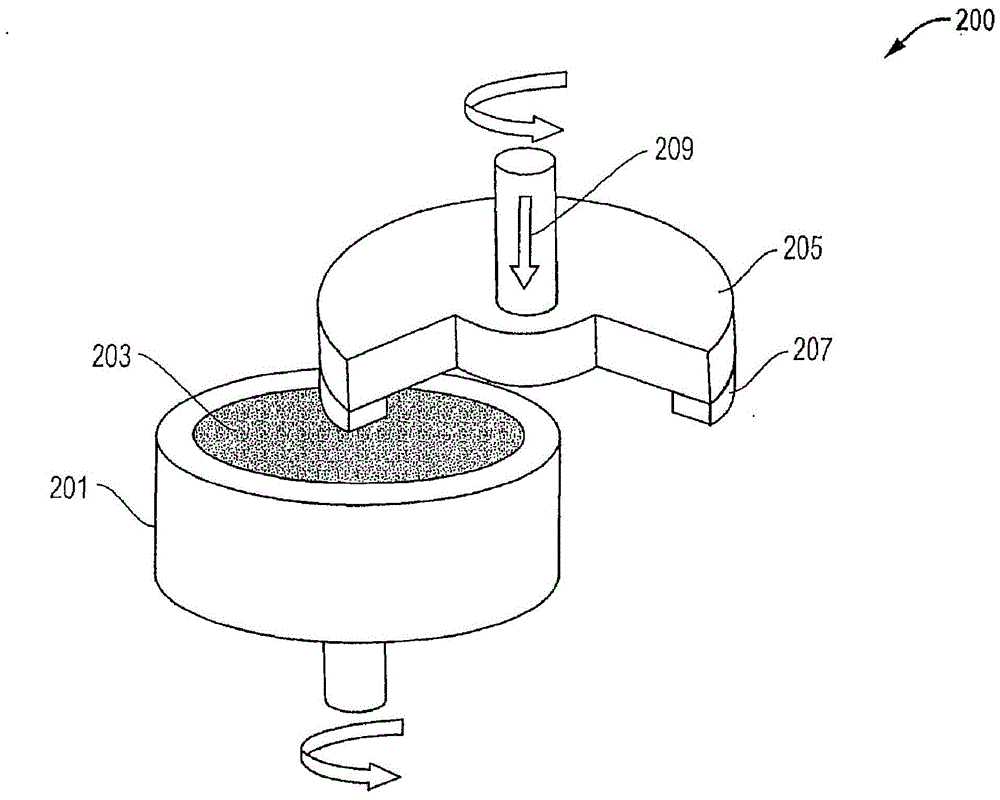
蓝宝石基材本申请是申请日为2007年12月21日,申请号为200780048893.5,发明名称为研磨蓝宝石基材的方法的申请的分案申请。技术领域本申请一般涉及蓝宝石基材以及精整这种基材的方法。
背景技术:基于第III族和第V族元素的单晶氮化物材料的半导体组件非常适合用于发光二极管(LED)、激光二极管(LD)、显示器、晶体管和检测器之类的器件。利用第III族和第V族氮化物的半导体元件尤其可用于紫外和蓝/绿波长区域内的发光器件。例如,氮化镓(GaN)及相关材料如AlGaN、InGaN和它们的组合是高需求的氮化物半导体材料的最普通的例子。但是,由于种种原因,已经证明制造这种氮化物半导体材料的梨晶(boules)和基材是困难的。因此,在异质基底材料上外延生长氮化物半导体材料被认为是一种可行的替代方案。SiC(碳化硅)、Al2O3(蓝宝石或刚玉)和MgAl2O4(尖晶石)等基材是常用的异质基底材料。这种异质基材与氮化物半导体材料、特别是GaN具有不同的晶格结构,因此产生晶格失配。尽管面对着这种失配及其伴生问题如半导体材料覆盖层中存在应力和缺陷,工业上仍然需要大表面积、高质量的基材,特别是蓝宝石基材。但是,生产高质量、大尺寸基材仍然面临一些挑战。
技术实现要素:一个实施方式涉及一种蓝宝石基材,该基材包括大致平坦的表面,其具有选自a-平面、r-平面、m-平面和c-平面取向的晶体取向,nTTV不大于约0.037μm/cm2,其中nTTV是相对于大致平坦的表面的表面积进行标准 化之后的总厚度变化,基材的直径不小于约9.0cm。另一个实施方式涉及一种蓝宝石基材,该基材包括大致平坦的表面,其具有选自a-平面、r-平面、m-平面和c-平面取向的晶体取向,TTV不大于约3.00μm,其中TTV是大致平坦的表面的总厚度变化。基材的直径不小于约6.5cm,厚度不大于约525μm。另一个实施方式涉及机械加工蓝宝石基材的方法,该方法包括使用第一固定磨料研磨蓝宝石基材的第一表面,使用第二固定磨料研磨蓝宝石基材的第一表面。第二固定磨料的平均粒度小于第一固定磨料的平均粒度,且第二固定磨料是自修整的(self-dressing)。另一个实施方式涉及提供含蓝宝石基材的蓝宝石基材组的方法,该方法包括使用磨料研磨各蓝宝石基材的第一表面,使第一表面具有c-平面取向,其中蓝宝石基材组含至少20个蓝宝石基材。各蓝宝石基材具有第一表面,该第一表面具有(i)c-平面取向、(ii)晶体m-平面取向差角度(θm)和(iii)晶体a-平面错误取向角度(θa),其中(a)取向差角度θm的标准偏差σm不大于约0.0130和/或(b)取向差角度θa的标准偏差σa不大于约0.0325。另一实施方式涉及包括至少20个蓝宝石基材的蓝宝石基材组。各蓝宝石基材具有第一表面,该第一表面具有(i)c-平面取向、(ii)晶体m-平面取向差角度(θm)和(iii)晶体a-平面取向差角度(θa),其中(a)取向差角度θm的标准偏差σm不大于约0.0130和/或(b)取向差角度θa的标准偏差σa不大于约0.0325。附图简要说明参考附图,能更好地理解本发明,本发明的许多特征和优点对本领域的技术人员而言将是显而易见的。图1是依据一个实施方式形成基材的方法的流程图。图2显示了根据一个实施方式的研磨设备。图3A及3B是使用依据一个实施方式的研磨工具与传统研磨工具的比较图。图4显示了根据一个实施方式的抛光设备。图5显示了c-平面取向的蓝宝石基材的取向差角度。在不同附图中使用相同的附图标记来表示类似或相同的事项。具体实施方式依据一方面,提供一种包括以下步骤的方法:使用第一固定磨料研磨蓝宝石基材的第一表面,使用第二固定磨料研磨蓝宝石基材的第一表面。该方法还要求第二固定磨料比第一固定磨料细小,这样第二固定磨料的平均粒度小于第一固定磨料的平均粒度,且第二固定磨料具有自修整研磨面。为了便于说明问题,通常可将磨料分为自由磨料和固定磨料。自由磨料通常由以粉末形式或微粒形式在液体介质中形成悬浮液的研磨粒或研磨粉组成。固定磨料与自由磨料的差别通常在于固定磨料使用在材料基质内的研磨粉,所述材料基质将研磨粉相互之间的位置固定。固定磨料通常包括结合磨料和涂敷磨料。涂敷磨料的例子是砂纸;涂敷磨料通常是平坦片(或平坦片经过几何处理形成带、薄片(flaps)等),其依赖于在上面沉积研磨粉以及各种胶结涂层(sizecoat)和构造涂层(makecoat)的挠性基材。相反,结合磨料通常不依赖于这种基材,由于研磨粉分布在基质结合材料中,研磨粉就利用基质结合材料固定彼此间的位置。通常对这种结合磨料组件进行成形或模塑,在结合基质会软化、流动和润湿粉料的固化温度(通常高于750℃)进行热处理,然后冷却。可以使用各种三维形式,例如环形、圆锥形、圆柱形、截头圆锥形、各种多边形,并且可以形成为研磨轮、研磨块、研磨钻头等形式。本文所描述的具体实施方式使用结合磨料形式的固定研磨料组件。参看图1,显示了依据一个实施方式形成基材的方法的流程图。该方法首先在步骤101中形成单晶蓝宝石的梨晶。应理解,蓝宝石可形成为适合用作半导体器件、特别是LED/LD应用的基材的任何尺寸或形状的坯体(blank)或梨晶。因此,常见的形状是大致具有圆柱形轮廓的梨晶。根据所需的梨晶尺寸和形状以及晶体的取向,可以使用科佐池(Czochralski)法、定边喂膜生长法(Edge-DefinedFilmFedGrowth)(EFG)或凯罗珀罗(Kyropoulos)法等技术形成单晶蓝宝石。在步骤101形成单晶蓝宝石后,可以在步骤103将梨晶或坯体锯切为一片片蓝宝石,形成晶片。依据一个具体实施方式,锯切蓝宝石包括用线锯锯切大致为圆柱形的蓝宝石梨晶。用线锯锯切蓝宝石梨晶可以提供多个未经精整的蓝宝石晶片。通常,用线锯锯切的持续时间约为数小时,例如约2.0-30小时。未精整的蓝宝石晶片所需的厚度可以小于约10mm,例如约8.0mm,或小于约5.0mm。依据一个实施方式,在步骤103中用线锯锯切后,蓝宝石晶片的厚度小于约3.0mm,例如小于约1.0mm。依据一个实施方式,使用一个或多个固定磨料线锯元件,例如镀覆或涂布了研磨颗粒的线锯阵列来进行线锯锯切。在一个实施方式中,将超磨料如立方氮化硼(CBN)或金刚石涂敷在多个线锯上,使蓝宝石梨晶抵靠该线锯网高速旋转(例如,最多5000rpm),从而单步就完成整个梨晶的切片。这种技术的一个例子是非绕卷型线锯锯切,例如由美国马萨诸塞州塞勒姆的晶体系统公司(CrystalSystemsInc.ofSalem,Mass)提供的FAST(固定磨料切片技术)。另一个例子是卷轴-卷轴(spool-to-spool)线锯锯切系统。对于由EFG方法生产的通常为带状或片形的单晶原料,线锯锯切处理不是必需的,去芯的(cored-out)(即成形的)晶片可直接用于研磨步骤。为了清楚起见,文中所用的术语“晶片”和“基材”是同义词,都指切成片的蓝宝石材料,该材料形成或经处理后,用作半导体层在其上外延生长的基材,例如用于形成光电器件。通常将未精整的蓝宝片称为晶片,将经过精整的蓝宝石片称为基材,但是在本文中使用时,这些术语不一定表示这种区别。依据图1所示的实施方式,在步骤103中经过锯切形成多个蓝宝石晶片后,可以对未精整的蓝宝石晶片的表面进行处理。通常可对未精整蓝宝石晶片的一个或两个主要相对表面进行研磨,以提高表面的精整度。依据一个实施方式,在步骤105中对未精整蓝宝石晶片进行粗磨。粗磨步骤可包括对未精整蓝宝石基材两个主表面的研磨。通常,粗磨处理以合理的高材料去除速率除去足够多的材料,从而消除主表面由于线锯锯切造成的不规则性。因此,粗磨过程可除去未精整蓝宝石基材主表面上不少于约30微米的材料,例如除去未精整蓝宝石晶片主表面上不少于约40微米、或不少 于约50微米的材料。通常,粗磨过程可使用固定粗磨料,该粗磨料包含在结合材料基质中的粗磨颗粒。粗磨颗粒可包括常规的研磨颗粒,例如晶体材料或陶瓷材料,包括氧化铝、二氧化硅、碳化硅、氧化锆-氧化铝等。作为补充或另选地,粗磨颗粒可包括超磨颗粒,包括金刚石和立方氮化硼或它们的混合物。在一些具体的实施方式中采用超磨颗粒。使用超磨颗粒的实施方式可使用非超磨陶瓷材料(例如上述的那些陶瓷材料)作为填料。关于粗磨料的其它方面,粗磨颗粒的平均粒径不大于约300微米,例如不大于约200微米,甚至不大于约100微米。依据一个具体实施方式,粗磨颗粒的平均粒径在约2.0微米至约300微米的范围内,例如在约10微米至200微米的范围内,更优选在约10微米至100微米的范围内。典型的粗磨颗粒的平均粒径在约25微米至75微米的范围内。如上所述,粗磨料包含结合材料基质。通常,结合材料基质可包括金属或金属合金。合适的金属包括铁、铝、钛、青铜、镍、银、锆、它们的合金等。在一个实施方式中,粗磨料包含不超过约90体积%的结合材料,例如不超过约85体积%的结合材料。通常,粗磨料包含不少于约30体积%的结合材料,甚至不少于约40体积%的结合材料。在一个具体的实施方式中,粗磨料中结合材料的含量在约40体积%至90体积%的范围内。具体磨轮的例子包括US6,102,789、US6,093,092和US6,019,668中所描述的那些磨轮,这些专利文献通过参考结合于此。通常,粗磨过程包括将未精整的蓝宝石晶片设置在支架上,使蓝宝石晶片相对于粗磨表面旋转。参看图2,它以部分剖开的示意图的形式,显示了典型研磨设备200的示意图。研磨设备200可包括设置在支架201上的未精整晶片203,使得晶片203至少部分地凹入支架201。支架201可以旋转,因而带动未精整晶片203旋转。具有磨边207的磨轮205(图中以剖开形式显示)可以相对于未精整晶片203旋转,从而研磨未精整晶片的表面;晶片203和磨轮205可以朝相同的方向旋转(例如,都为顺时针或逆时针),由于旋转轴之间的差异而产生研磨作用。如图中所示,除了使磨轮205旋转外,还可以向磨轮203施加下向力209。如图中所示,粗磨料可以是具有围绕内轮周边的大致呈圆形的磨边207的磨轮。依据一个实施方式,细磨处理包括使磨轮以大于约2000转/分钟(rpm)、例如大于约3000rpm、例如在3000-6000rpm范围内的速度旋转。通常使用液体冷却剂,包括水性冷却剂和有机冷却剂。在一个具体的实施方式中,可以使用自修整粗磨表面。不同于许多常规固定磨料,自修整磨料通常不需要在使用过程中进行修整或额外的调理,特别适合于精确且稳定的研磨。对于自修整,结合材料基质可具有与研磨颗粒相应的特定组成、孔隙率和浓度,从而在研磨颗粒被磨平(wearflat)时,结合材料基质能够如所期望的那样破裂。在此,随着研磨颗粒被磨平,基质的负载力增加,导致结合材料基质破裂。破裂有益地导致磨损的颗粒丢失,暴露出新鲜颗粒以及与之相关联的新鲜切割边。具体而言,自修整粗磨料的结合材料基质的破裂韧度小于约6.0MPa-m1/2,例如小于约5.0MPa-m1/2,特别在约1.0MPa-m1/2至3.0MPa-m1/2的范围内。通常,自修整粗磨料中的一些结合材料被孔替代,这些孔通常是互连的孔隙。因此,结合材料的实际含量低于上述值。在一个具体实施方式中,粗磨料的孔隙率不小于约20体积%,例如不小于约30体积%,通常在约30体积%至约80体积%之间,例如约30体积%至约80体积%,约30体积%至约70体积%。依据一个实施方式,粗磨料包含约50体积%至约70体积%的孔隙。应理解,孔隙可以是开放或闭合的,在具有较高百分孔隙率的粗磨料中,孔隙通常是开放的互连孔。孔径通常在约25微米至约500微米的范围内,例如约150微米至约500微米的范围内。上述孔相关值和文中描述的孔相关值是联系各种组件的预加工或预研磨提出的。依据一个实施方式,限制粗磨颗粒的含量,以进一步提高自修整能力。例如,粗磨料含有不超过约50体积%、不超过40体积%、不超过30体积%、例如不超过约20体积%、甚至不超过约10体积%的粗磨颗粒。在一个具体实施方式中,粗磨料包含不少于约0.5体积%且不超过约25体积%的粗磨颗粒,例如在约1.0体积%至约15体积%范围内的粗磨颗粒,或特别在约2.0体积%至约10体积%范围内的粗磨颗粒。参看图3,所示两幅图比较了自修整磨料表面和传统磨料表面施加于 磨轮的法向力与研磨时间之间的函数关系。如图所示,在所示三个研磨操作301、302和303(301-303)的每一个中,自修整磨料都具有基本恒定的峰值法向力。另外,研磨操作301-303相互比较的峰值法向力几乎无差别。相反,对于传统磨料表面,各研磨操作304、305、306和307(304-307)相互比较,为了有效研磨表面所需的法向力增加,并且在各研磨操作304-307的过程中,法向力也增加。研磨过程中的法向力这样增加,很容易导致明显的表面缺陷和表面下缺陷(高缺陷密度)以及不均匀的研磨,即使经常进行修整操作也是如此。依据一个实施方式,在使用自修整粗磨料的研磨过程中,峰值法向力包括在研磨操作期间向基材表面施加的不超过约200N/mm宽度(沿着基材与磨轮之间的接触面测得)的法向力。在另一个实施方式中,在研磨操作期间,施加的峰值法向力不大于约150N/mm宽度,例如不大于约100N/mm宽度,甚至不大于约50N/mm宽度。粗磨后,晶片的平均表面粗糙度Ra通常小于约1微米。通常,随后进行细磨,这样不仅可以改善基材的宏观性质,包括平坦度、弯曲度、翘曲度、总厚度变化和表面粗糙度,而且可以减少尺度更小的缺陷,例如减少表面下损害,例如结晶度损害,尤其包括减少或消除晶体位错。在一些情况中,第一粗磨步骤可以省略,或者用精研(lapping)操作代替,精研操作使用通常为浆料形式的自由磨料。在这种情况中,第二研磨操作使用上述自修整固定磨料。再回头讨论图1所示的实施方式,在步骤105中完成粗磨后,在步骤107中对蓝宝石晶片进行细磨。细磨过程通常除去材料,直到基本上消除粗磨过程105导致的缺陷。因此,依据一个实施方式,细磨过程从蓝宝石基材主表面上除去不少于约5.0微米的材料,例如不少于约8.0微米的材料,或者不少于约10微米的材料。在另一个实施方式中,除去更多的材料,这样从蓝宝石基材表面上除去的材料不少于约12微米,甚至不少于约15微米。通常,细磨步骤107在一个表面上进行,这一点与步骤105中的粗磨过程不同,后者可包括在未精整蓝宝石晶片的两个主表面上都进行研磨。细磨可使用固定细磨料,其包括在结合材料基质中的细磨颗粒。细磨 颗粒可包括常规的研磨颗粒,例如晶体材料或陶瓷材料,包括氧化铝、二氧化硅、碳化硅、氧化锆-氧化铝或超磨颗粒,例如金刚石和立方氮化硼,或它们的混合物。在一些具体的实施方式中采用超磨颗粒。使用超磨颗粒的实施方式可使用非超磨陶瓷材料(例如上述的那些陶瓷材料)作为填料。依据一个实施方式,细磨料含有不超过约50体积%、不超过40体积%、不超过30体积%、例如不超过约20体积%、甚至不超过约10体积%的细磨颗粒。在一个具体实施方式中,细磨料包含不少于约0.5体积%且不超过约25体积%的细磨颗粒,例如在约1.0体积%至约15体积%范围内的细磨颗粒,或特别在约2.0体积%至约10体积%范围内的细磨颗粒。关于细磨料的其它方面,细磨颗粒的平均粒径不大于约100微米,例如不大于约75微米,甚至不大于约50微米。依据一个具体实施方式,细磨颗粒的平均粒径在约2.0微米至约50微米的范围内,例如在约5微米至35微米的范围内。通常,粗固定磨料和细固定磨料之间的平均粒径差值至少为10微米,通常至少为20微米。类似于粗磨料,细磨料可包含结合材料基质,该结合材料基质可包括金属或金属合金之类的材料。合适的金属包括铁、铝、钛、青铜、镍、银、锆、它们的合金。在一个实施方式中,细磨料包含不超过约70体积%的结合材料,例如不超过约60体积%的结合材料,或不超过约50体积%的结合材料。依据另一个实施方式,细磨料包含不超过约40体积%的结合材料。通常,细磨料中结合材料的含量不少于约10体积%,通常不少于15体积%,或不少于20体积%。此外,细固定磨料可包括一定程度的孔隙率。在一个具体实施方式中,细磨料的孔隙率不小于约20体积%,例如不小于约30体积%,通常在约30体积%至约80体积%之间,例如约50体积%至约80体积%,或约30体积%至约70体积%。依据一个实施方式,细磨料包含约50体积%至70体积%的孔隙。应理解,孔隙可以是开放或闭合的,在具有较高百分孔隙率的细磨料中,孔隙通常是开放的互连孔。孔径通常在约25微米至约500微米的范围内,例如约150微米至500微米的范围内。在步骤107的细磨过程中,如上所述,细磨料是自修整的。类似于自 修整粗磨料,自修整细磨料包含结合材料基质,其通常包括具有特定破裂韧度的金属。依据一个实施方式,结合材料基质的破裂韧度小于约6.0MPa-m1/2,例如小于约5.0MPa-m1/2,特别在约1.0MPa-m1/2至约3.0MPa-m1/2的范围内。US6,755,729和US6,685,755中描述了自修整细磨组件,这些专利文献通过参考结合于此。通常,细磨过程107包括与上述粗磨过程105中描述的类似的设备和过程。也就是通常将未精整蓝宝石晶片设置在支架上,使蓝宝石晶片相对于细磨表面旋转,所述细磨表面通常是具有围绕内轮周边的大致呈圆形的磨边的磨轮。依据一个实施方式,细磨处理包括使磨轮以大于约2000转/分钟(rpm)、例如大于约3000rpm、例如在3000-6000rpm范围内的速度旋转。通常使用液体冷却剂,包括水性冷却剂和有机冷却剂。如上所述,细磨料可以是自修整的,因此通常具有在自修整粗磨料中描述的性质。但是,依据一个实施方式,在细磨过程中的峰值法向力包括在细磨操作期间所施加的不超过约100N/mm宽度的法向力。在另一个实施方式中,在研磨操作期间,峰值法向力不大于约75N/mm宽度,例如不大于约50N/mm宽度,甚至不大于约40N/mm宽度。以上关于粗磨料和细磨料的描述涉及实际研磨工具的固定磨料组件。显然,这些组件不构成研磨工具的整体,仅仅是工具中经设计用于接触工件(基材)的一部分,固定磨料组件可以为区段形式。在未精整蓝宝石晶片经过细磨后,晶片的平均表面粗糙度Ra通常小于约0.10微米,例如小于约0.05微米。在对蓝宝石晶片细磨(107)后,可以对晶片进行如EP0221454B1中所描述的应力释放处理。如文中所描述的,应力释放可通过蚀刻或退火处理进行。退火可以在1000℃以上的温度进行数小时。再参看图1的实施方式,在步骤107细磨后,在步骤111中对经过研磨的蓝宝石晶片进行抛光。通常,抛光利用在晶片表面与加工工具之间的浆料,晶片和加工工具可以相互相对移动,以进行抛光操作。利用浆料的抛光操作通常落在化学-机械抛光(CMP)的类别中,浆料可包括悬浮在液体介质中的疏松研磨颗粒,以有利于从晶片上除去精确量的材料。因此,依 据一个实施方式,抛光过程111可包括CMP,使用含磨料和添加剂化合物的浆料,所述添加剂化合物的作用是增强或缓和材料的去除。化学组分可以是例如磷化合物。实际上,磨料提供机械组分,添加剂提供化学活性组分。疏松磨料通常是纳米级的,平均粒径小于1微米,通常小于200纳米。通常,中值粒度(medianparticlesize)在略窄的范围内,例如在约10-150纳米的范围内。为了解释技术术语,低于约1微米的中值粒度通常表示一种对应于下文所述的主题内容的抛光过程,在该过程中是通过以低材料去除速率进行机械加工来进行表面精修整。如果中值粒度大于约1.0微米,例如约2.0-5.0微米,则机械加工通常为精研操作。特别有用的疏松磨料是氧化铝,例如多晶或单晶γ-氧化铝形式的氧化铝。如上所述,在浆料中可存在磷添加剂。通常,磷添加剂的浓度在约0.05重量%-5.0重量%的范围内,例如约0.10重量%-3.0重量%的范围内。具体实施方式采用的浓度在略窄的范围内,例如约0.10重量%-2.0重量%。依据一个实施方式,磷化合物含氧,其中氧与磷元素键合。该类材料称为氧磷(oxophosphorus)材料。具体地,氧磷化合物含一价、三价或五价的磷,在具体的实施方式中,使用含五价磷的氧磷化合物可以进行有效的机械加工。在其它实施方式中,除了与氧键合外,磷还可以与碳键合,通常称为有机磷化合物,也就是膦酸酯/盐。其它磷化合物包括磷酸酯/盐、焦磷酸酯/盐、连二磷酸酯/盐、碱式磷酸酯/盐、亚磷酸酯/盐、焦亚磷酸酯/盐、次磷酸酯/盐和鏻化合物。具体的磷化合物包括磷酸钾、六偏磷酸钠、羟基膦酰乙酸(Belcor575)和氨基三-(亚甲基膦酸)(Mayoquest1320)。通常,包含磨料组分和含磷化合物的添加剂的浆料通常是水性的,即是基于水的。实际上浆料通常具有碱性pH,例如pH大于约8.0,例如大于约8.5。pH的数值最多约为12。关于对经过研磨的蓝宝石晶片进行抛光的设备,图4显示了依据一个实施方式的抛光设备的基本结构的示意图。设备401包括加工工具,在此情况中是由抛光垫410和支撑抛光垫的台板组成的工具。台板和抛光垫410具有大致相同的直径。台板可沿着箭头所指的旋转方向围绕中心轴旋 转。模板412具有多个圆形凹槽,各凹槽分别容纳基片414,基片414夹在抛光垫410和模板412之间。带有基片414的模板412绕其中心轴旋转,其中rp表示从抛光垫旋转中心到模板412中心的径向距离,rt表示从各基片到模板旋转中心的径向距离。设备401的构造是常用于抛光操作的构造,但是也可以使用不同的构造。与无磷基添加剂的浆料相比,向浆料中加入磷化合物通常会提高材料去除速率(MRR)。就此而言,这种提高可用MRRadd/MRRcon的比值表示,依据一个实施方式,该比值不小于约1.2。MRRadd表示包含磨料和含磷化合物的添加剂的浆料的材料去除速率,而MRRcon是对照浆料在完全相同的处理条件下的材料去除速率,对照浆料与上述浆料基本完全相同,仅仅是无包含磷化合物的添加剂。依据其它实施方式,该比值较大,例如不小于约1.5,甚至不小于约1.8,在一些特定的样品中,去除速率是仅含氧化铝磨料但无磷化合物添加剂的浆料的两倍。虽然上文中已经重点讨论了几种实施方式,包括基于氧化铝基抛光浆料的实施方式,但是也可以使用具有极佳效果的其它研磨材料,包括二氧化硅、氧化锆、碳化硅、碳化硼、金刚石等。实际上,含磷基化合物的氧化锆基浆料经证实具有特别良好的抛光性质,即与氧化铝基材上只有二氧化硅相比,材料去除速率提高了30%-50%。依据一个特定方面,提供一种高表面积蓝宝石基材,该基材包括大致平坦的表面,其具有a-平面取向、r-平面取向、m-平面取向或c-平面取向,并且包括受控的维数。文中所用的术语“x-平面取向”表示基材具有大致沿着晶体x-平面延伸的主表面,根据基材的具体规格,例如终端客户所规定的规格,通常具有轻微的偏离x-平面的取向差。具体的取向包括r-平面和c-平面取向,某些实施方式采用c-平面取向。如上所述,基材可具有所需的受控维数。受控维数的一种量度是总厚度变化,包括TTV(总厚度变化)和nTTV(标准化的总厚度变化)中的至少一种。例如,依据一个实施方式,TTV通常不大于约3.00μm,例如不大于约2.85μm,甚至不大于约2.75μm。上述TTV参数与大尺寸晶片、特别是 具有受控厚度的大尺寸晶片相关。例如,一些实施方式中直径可以不小于约6.5cm,厚度不大于约490μm。依据某些实施方式,上述TTV参数与特别大尺寸的晶片相关,包括直径不小于7.5cm、不小于9.0cm、不小于9.5cm或不小于10.0cm的晶片。晶片尺寸还可以用表面积表示,上述TTV值可以与表面积不小于约40cm2、不小于约70cm2、不小于约80cm2、甚至不小于约115cm2的基材相关。另外,晶片的厚度可以进一步控制在不大于约500μm、例如不大于约490μm的值上。应注意,文中在描述晶片、基材或梨晶尺寸时使用的术语“直径”是指与晶片、基材或梨晶吻合的最小圆周的直径。因此,如果这类组件具有一个或多个平面(flats),这类平面不会影响组件的直径。各种实施方式具有受控良好的nTTV,例如不大于约0.037μm/cm2。在具体的实施方式中,具有更佳的nTTV,例如不大于0.035μm/cm2,甚至不大于0.032μm/cm2。尤其是这些受控nTTV可以在大尺寸基材中获得,例如基材的直径不小于约9.0cm,甚至不小于约10.0cm。晶片尺寸还可以用表面积表示,上述nTTV值可以与表面积不小于约90cm2、不小于约100cm2、不小于约115cm2的基材相关。关于蓝宝石基材的总厚度变化值,TTV是蓝宝石基材(忽略边缘禁区,该区域通常包括从晶片边缘围绕晶片圆周延伸的3.0mm的环)的最大厚度与最小厚度之间的绝对差值,nTTV是该值(TTV)对蓝宝石基材的表面积进行标准化后的值。测量总厚度变化的方法如ASTM标准F1530-02中所述。通常,nTTV值以及本发明揭示的所有其它标准化的特征,可以针对具有大致平坦表面和大致圆形周长的蓝宝石基材进行标准化,所述蓝宝石基材可包括用于识别基材取向的平面。依据一个实施方式,蓝宝石基材的表面积不小于约25cm2,例如不小于约30cm2,不小于35cm2,甚至不小于约40cm2。而且,所述基材可具有更大的表面积,例如大致平坦的表面的表面积不小于约50cm2,甚至不小于约60cm2,或不小于约70cm2。蓝宝石基材的直径可大于约5.0cm(2.0英寸),例如不小于约6.0cm(2.5英寸)。但是,蓝宝石基材的直径一般为7.5cm(3.0英寸)或更大,特别包括10cm(4.0英寸)的晶片。关于蓝宝石基材的其它特征,在一个实施方式中,蓝宝石基材的大致平坦的表面的表面粗糙度Ra不大于约例如不大于约或约为甚至不大于约可以获得更佳的表面粗糙度,例如不大于约例如不大于约或不大于约依据上述方法处理的蓝宝石基材的大致平坦表面还具有优良的平坦度。表面的平坦度通常理解为表面与最佳拟合参考平面的最大偏差(参见ASTMF1530-02)。就此而言,标准化的平坦度是用大致平坦表面的表面积对表面平坦度进行标准化之后得到的数值。依据一个实施方式,大致平坦的表面的标准化平坦度(n-平坦度)大于约0.100μm/cm2,例如不大于约0.080μm/cm2,甚至不大于约0.070μm/cm2。而且,大致平坦的表面的标准化平坦度可以小于、例如不大于约0.060μm/cm2,或不大于约0.050μm/cm2。依据本发明方法处理的蓝宝石基材的翘曲度减小,翘曲度用标准化的翘曲度表示,在下文中称为n-翘曲度。基材的翘曲度通常理解为基材与最佳拟合参考平面之间中心表面的偏差(参见ASTMF697-92(99))。关于n-翘曲度的测量,翘曲度根据蓝宝石基材的表面积进行标准化。依据一个实施方式,n-翘曲度不大于约0.190μm/cm2,例如不大于约0.170μm/cm2,甚至不大于约0.150μm/cm2。大致平坦的表面还具有减小的弯曲度。表面的弯曲度通常理解为表面或一部分表面凹陷或变形的绝对测量值,该值是相对于与任何厚度变化无关的基材中心线测量的。依据本发明方法处理的基材的大致平坦表面还具有减小的标准化弯曲度(n-弯曲度),该值是用大致平坦表面的表面积标准化后得到的弯曲度值。因此,在一个实施方式中,大致平坦表面的n-弯曲度不大于约0.100μm/cm2,例如不大于约0.080μm/cm2,甚至不大于约0.070μm/cm2。依据另一个实施方式,基材的n-弯曲度在约0.030μm/cm2至约0.100μm/cm2的范围内,特别在约0.040μm/cm2至约0.090μm/cm2的范围内。关于蓝宝石基材的取向,如上所述,大致平坦的表面具有c-平面取向。C-平面取向可包括大致平坦表面与c-平面在各个方向上人为造成或特意形成的倾斜角度。就此而言,依据一个实施方式,蓝宝石基材的大致平坦表 面的倾斜角度不大于约2.0°,例如不大于约1.0°。通常,倾斜角度不小于约0.10°,或不小于0.15°。倾斜角度是在基材表面法线与c-平面法线之间形成的角度。依据文中所述的实施方式,蓝宝石晶片的加工需要产生控制良好的晶片-晶片精准性。更具体地,关于c-平面取向的晶片,晶片表面相对于蓝宝石晶体的c-平面的精确取向应该精确固定,特别是通过晶片-晶片结晶差异定量地固定。参看图5,Z是蓝宝石抛光表面的单位法线,θA、θM和θC是分别与a-平面、m-平面和c-平面规化正交的正交单位矢量。A和M分别是θA、θM在蓝宝石表面限定的平面上的投影(A=θA-Z(θA.Z),M=θM-Z(θM.Z))。a-方向上的取向差角度是θA与其在含A和M的平面上的投影之间的角度,而m-方向上的取向差角度是θM与其在含A和M的平面上的投影之间的角度。取向差角度标准变差σ是取向差角度在整个晶片组(通常至少包括20个晶片)中的标准偏差。依据实施方式,如文中所述进行加工,特别是结合上文详述的研磨过程,得到多个具有精确晶体取向的蓝宝石晶片。基材组通常具有不少于20个晶片,有时具有30或更多个晶片,各基材组中的晶片可来自不同蓝宝石芯或梨晶。应注意,一个组可包括若干单独包装的亚组。晶片组的θM在整个晶片组中的标准偏差σM不大于约0.0130度,例如不大于0.0110度,或不大于0.0080度。晶片组的θA的标准偏差σA不大于约0.0325度,例如不大于0.0310度,或不大于0.0280度。与现有技术中制造用于LED/LD基材的晶片/基材的方法相比,本发明的实施方式具有显著的优点。例如,依据若干实施方式,使用粗磨料(常称为自修整粗固定磨料)结合自修整细磨料,以及特定的CMP抛光技术和化学处理,有利于生产具有优良几何性质(即nTTV、n-翘曲度、n-弯曲度和n-平坦度)的精确精整蓝宝石晶片。除了控制几何性质外,上文提供的方法再结合精确的线锯锯切,有利于获得在整个基材上对倾斜角度差异具有良好控制的精确取向的晶片。在这些方面,改善的几何性质以及对基材与基材间表面取向的精确控制,有利于生产具有更均一发光性质的稳定可靠的LED/LD器件。经历文中所述的各处理步骤之后,经过处理的蓝宝石基材表面通常具有适合用于LED/LD器件的晶体结构。例如,在一些实施方式中,根据X射线图谱分析测得的位错密度小于1E6/cm2。特别值得注意的是,通过本发明实施方式对大尺寸基材和具有受控厚度的基材实现了对尺寸和/或晶体取向的控制。在这些方面,依据现有技术水平,对于给定厚度,对尺寸和晶体的控制随着晶片尺寸(表面积)的增加而迅速变差。因此,现有技术的加工通常依赖于增加厚度以至少部分地保持尺寸控制和晶体控制。相反,本发明的实施方式可以提供基本与厚度无关并且对晶片或基材尺寸依赖性减小的这种控制。实施例以下实施例提供了依据若干实施方式处理晶片的方法,尤其描述了生产具有改善的尺寸性质和取向的高表面积晶片的加工参数。在以下实施例中,依据本发明实施方式加工和形成直径为2英寸、3英寸和4英寸的c-平面蓝宝石晶片。如上所述,从对梨晶进行切割或切片开始加工。使用线锯锯切技术将梨晶切开,其中将梨晶放在涂敷了切割元件(例如金刚石颗粒)的线锯上,并开始旋转。梨晶高速旋转,旋转速度在约2000rpm至5000rpm的范围内。在梨晶旋转的同时,梨晶与多个线锯锯段接触,所述线锯锯段通常在与梨晶表面相切的方向上高速往返运动,从而促进锯切。线锯锯段以约100次循环/分钟的速度往返运动。可以引入其它液体,例如浆料,以促进切片。在此情况中,线锯锯切处理持续数小时,在约4-8小时的范围内。应理解线锯锯切处理的持续时间至少部分地依赖于被切片的梨晶的直径,因此可以持续8小时以上。在线锯锯切后,晶片的平均厚度约为1.0mm或更薄。通常,晶片的平均表面粗糙度(Ra)小于约1.0微米,平均总厚度变化约为30微米,平均弯曲度约为30微米。在用线锯锯切梨晶后产生晶片,对该晶片进行研磨处理。研磨过程至少包括第一粗磨过程和第二细磨过程。在粗磨过程中,使用自修整粗磨轮, 例如PICO型磨轮,Coarse#3-17-XL040,由圣戈本磨料公司(Saint-GobainAbrasives,Inc.)生产,该磨轮结合了平均粒度约60-80微米的金刚石砂粒。例如,使用Strasbaugh7AF超精密磨机完成对晶片的粗磨。下表1提供了粗磨过程的周期和参数。在下表1和2中,在一系列重复研磨步骤中连续去除材料。步骤1-3表示在所述磨轮和夹盘速率以及进给速率下进行的主动研磨步骤。在无偏置的情况下停顿,即进给速率为零。此外,在相反方向以进给速率进行提升,磨轮以所示的进给速率从基材表面提升。表1:在粗磨过程之后,对晶片进行细磨处理。细磨过程也使用自修整磨轮,例如IRIS型磨轮Fine#4-24-XL073,由圣戈本磨料公司(Saint-GobainAbrasives,Inc.)生产,该磨轮使用平均粒度约10-25微米的金刚石磨粒。同样,在该实施例中使用Strasbaugh7AF超精密磨机完成对晶片的细磨。与粗磨过程相比,细磨过程中在表2所示的特定加工周期和参数下处理晶片。表2在粗磨和细磨过程后,如上所述对蓝宝石晶片进行应力释放处理。在应力释放后,对蓝宝石晶片进行最后的抛光。制备几种抛光浆料,用于研究pH和磷酸酯/盐的作用以及碱和钙的作用。如下所述,表3显示了对基本浆料(浆料1)的改进。使用直径2”的C-平面蓝宝石圆盘,在Buehler ECOMET4抛光机上进行抛光。抛光在H2垫(可购自美国宾夕法尼亚州费城的罗门哈斯公司(RohmandHaasCompanyofPhiladelphia,PA))上进行,浆料流速为40毫升/分钟,台板转速为400rpm,支架转速为200,下向力为3.8psi。表3表4浆料编号化学组成1氧化铝浆料,10%固体,含NaOH2氧化铝浆料,10%固体,含NaOH3氧化铝浆料,10%固体,含NaOH4氧化铝浆料,10%固体,含NaOH5氧化铝浆料,10%固体,含NaOH和1%焦磷酸钠6氧化铝浆料,10%固体,含NaOH和1%Dequest20667氧化铝浆料,10%固体,含NaOH和1%Dequest20548氧化铝浆料,10%固体,含NaOH9氧化铝浆料,10%固体,含KOH10氧化铝浆料,10%固体,含氢氧化铝11氧化铝浆料,10%固体,含NaOH和1%氯化钙关于抛光数据,从上述表3和表4可以看出,浆料3和浆料4显示,当pH从9迁移到11时,抛光性能明显提高。另外,已经发现表面精整度更佳,这意味着生产率更高。有机膦酸(浆料6和7)和无机磷酸盐(浆料5) 进一步提高了表面精整度和材料去除速率。较高的碱性pH可以提高去除速率和精整度,与氢氧化钾(浆料9)和氢氧化铵(浆料10)相比,氢氧化钠是合适的增加pH的途径(浆料8)。浆料11组合使用了作为疏松磨料组分的氧化铝,从而显著影响了材料的去除速率,使之适中。在对蓝宝石晶片进行了上述处理后,进行晶片尺寸几何性质(dimensionalgeometry)的表征。通过比较依据本发明方法和使用常规方法加工的蓝宝石晶片的尺寸几何性质,可以得到比较数据,所述常规方法依赖于用自由研磨浆料进行的精研而非研磨。表5中提供了比较数据,TTV和翘曲度的单位是微米,而nTTV和n-翘曲度的单位是微米/厘米2,直径(d)和厚度(t)的单位分别是英寸和微米。表5对于所有晶片直径,基本表面的法线与晶片c轴之间的角度小于1度。此外,测量晶片组中各晶片的取向差角度θM和θA,以检测晶片与晶片之间的偏差度,用标准偏差σM和σA定量地表示。结果列于表6。表6,取向差角度标准偏差σ依据实施例处理的晶片具有改善的尺寸几何性质,特别是改善的TTV、nTTV、翘曲度和n-翘曲度,以及以取向差角度标准偏差表示的结晶精确性。表5中的各值是至少8个数据的平均值。表6中所示的标准偏差值σ是在依据上述处理流程制得的晶片和用常规处理方法制得的晶片的不同晶片组 中测得的,其中在常规处理中,在整个研磨过程中都使用精研。值得注意的是,实施例通常在比常规处理薄的晶片厚度下实现尺寸几何性质的改善,这些性质用TTV和翘曲度值定量地表示。一些实施方式还对各晶片的尺寸几何性质提供了更好的控制,使之更加稳定,并且还对晶片组提供了更佳的晶体学控制。而且,实施例提供了改善的可缩放性,表现为尺寸几何性质随着晶片直径的增加而提高。虽然固定磨料研磨一般已经用于精整应用中,但是本发明人发现在严密尺寸控制下加工蓝宝石晶片是特定的方法特征。常规加工方法依赖低进给速率和高夹盘速率来改善尺寸几何性质。但是,已经发现这种低进给速率(例如0.5微米/秒)和高夹盘速率(例如590rpm)产生具有过度n-弯曲度、n-翘曲度和/或nTTV的晶片。增强尺寸控制能在非常规处理条件下获得成功的原因至今为止还未得到完全理解,但是似乎与蓝宝石基材、尤其是大尺寸基材(例如3英寸和4英寸的蓝宝石基材)的机械加工相关。依据文中所述的实施方式,以显著的高产率和生产率产生高表面积、高质量的用于支撑有源器件的基材。文中所提供的加工程序所产生的晶片具有可重复的、在尺寸上高度精确的几何晶体学参数。而且,文中提供的实施方式提供了处理技术、参数、化学试剂和设备的独特组合,表现出与现有技术和常规方法的差异,可提供具有明显改善的尺寸几何性质和晶体精确性的晶片。上述主题内容应认为是说明性的,不构成限制,所附权利要求书意在覆盖落在本发明的真正范围之内的所有这样的改进、提高和其他实施方式。因此,为得到法律允许的最大范围,本发明的范围由对以下权利要求书和其等同内容所允许作的最宽泛的解释来确定,并且不受前面的详细描述的限制或限定。