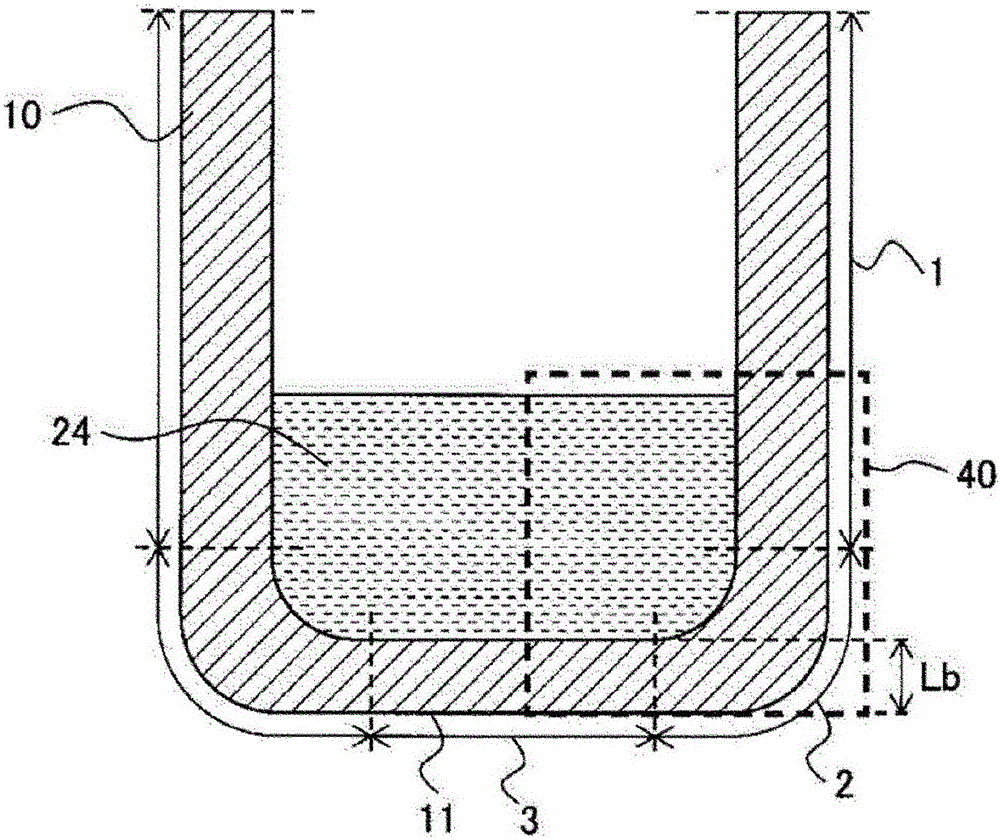
本公开涉及作为半导体元件合适的SiC单晶的制造方法。
背景技术:
:SiC单晶在热学、化学方面非常稳定、机械强度优异、耐放射线方面强,而且与Si单晶相比具有高的绝缘击穿电压、高的热导率等优异的物理性质。因此,可实现Si单晶和GaAs单晶等现有半导体材料不能实现的高输出、高频、耐电压、耐环境性等,作为可进行大电力控制和节能的功率器件材料、高速大容量信息通信用器件材料、车载用高温器件材料、耐放射线器件材料等这样宽范围的新一代半导体材料的期待正在高涨。以往,作为SiC单晶的生长方法,代表性的已知有气相法、艾奇逊(Acheson)法和溶液法。在气相法中,例如在升华法中,虽然具有在生长的单晶中易于产生被称作微管缺陷的中空贯穿状的缺陷、层叠缺陷等晶格缺陷和多晶型等的缺点,但在以往,SiC块状单晶大多通过升华法制造,也进行了减少生长晶体的缺陷的尝试。在艾奇逊法中,由于使用硅石和焦炭作为原料在电炉中进行加热,因此,因原料中的杂质等而不可能得到结晶性高的单晶。而且,溶液法为如下方法:在石墨坩埚中形成Si熔液或熔化了Si以外的金属的Si熔液,使C从石墨坩埚溶解到该熔液中,使SiC晶体层在设置于低温部的晶种基板上析出并生长。由于溶液法与气相法相比进行在接近热平衡的状态下的晶体生长,因此最能够期待低缺陷化。因此,最近,提出了一些基于溶液法的SiC单晶的制造方法。在专利文献1中,提出了一种基于溶液法的SiC单晶的制造方法,其中,通过在坩埚的底部区域内配置具有规定形状的隔热材料,抑制在Si-C溶液中产生杂晶。现有技术文献专利文献专利文献1:特开2012-180244号公报技术实现要素:发明所要解决的课题但是,在专利文献1记载的方法中,虽然可一定程度抑制在Si-C溶液中产生杂晶,但是杂晶的抑制依然不充分。本公开的方法解决了上述课题,目的在于提供一种与以往相比可抑制杂晶产生的基于溶液法的SiC单晶的制造方法。用于解决课题的手段本公开以SiC单晶的制造方法为对象,该SiC单晶的制造方法为使晶种基板与置于坩埚内的具有从内部向液面温度降低的温度梯度的Si-C溶液接触以使SiC单晶晶体生长的SiC单晶的制造方法,其中,坩埚具有厚度Lu和厚度Ld,厚度Lu是在与Si-C溶液的液面相同高度之处的坩埚的水平方向的厚度,厚度Ld是在与坩埚的底部内壁相同高度之处的坩埚的水平方向的厚度,Ld相对于Lu之比即Ld/Lu为2.00~4.21;在厚度Lu与厚度Ld之间,坩埚的水平方向的厚度从厚度Lu向厚度Ld单调增加;坩埚的壁厚为1mm以上;坩埚的底部的铅直方向的厚度Lb为1mm以上15mm以下;坩埚的底部外壁具有平坦部,平坦部的面积为100mm2以上;使置于坩埚内的Si-C溶液距坩埚的底部内壁的深度为30mm以上;该制造方法包括:利用配置于坩埚周围的高频线圈对Si-C溶液进行加热和电磁搅拌。发明效果根据本公开的方法,可利用溶液法与以往相比抑制杂晶的产生来制造SiC单晶。附图说明图1是可用于本公开的方法的坩埚的一例的截面示意图。图2是可用于本公开的方法的坩埚的其它例子的截面示意图。图3是可用于本公开的方法的坩埚的其它例子的截面示意图。图4是可用于本公开的方法的坩埚的其它例子的截面示意图。图5是图1中示出的底侧面部的区域40的放大截面图。图6是图2中示出的底侧面部的区域41的放大截面图。图7是表示基于式(1)和式(2)的Lx/Lu相对于高度x的优选范围的图。图8是可用于本公开的方法的坩埚和配置于坩埚底部的支持部件的一例的截面示意图。图9是可用于本公开的方法的SiC单晶制造装置的一例的截面示意图。图10是形成于晶种基板与Si-C溶液之间的弯液面的截面示意图。图11是实施例1中使用的坩埚的布局。图12是实施例2中使用的坩埚的布局。图13是实施例3中使用的坩埚的布局。图14是实施例4中使用的坩埚的布局。图15是实施例2中得到的Si-C溶液的温度分布的模拟结果。图16是比较例1中使用的坩埚的布局。图17是比较例2中使用的坩埚的布局。图18是表示Ld/Lu与ΔT的关系的图。图19是基于表2示出的数学式的Lx/Lu相对于高度x的图。图20是表示Lb与ΔT的关系的图。图21是可用于本公开的方法的SiC单晶制造装置的一例的截面示意图。图22是实施例7中使用的坩埚的布局。图23是实施例8中使用的坩埚的布局。图24是比较例5中使用的坩埚的布局。图25是比较例6中使用的坩埚的布局。图26是比较例7中使用的坩埚的布局。图27是实施例8中得到的Si-C溶液的温度分布的模拟结果。图28是表示Lzo/OD与ΔT的关系的图。图29是实施例9中使用的坩埚的布局。图30是实施例9中得到的模拟结果。图31是实施例10中使用的坩埚的布局。图32是实施例10中得到的模拟结果。图33示出从侧面观察的生长晶体的外观照片。图34示出从生长面观察的生长晶体的外观照片。图35示出从侧面观察的生长晶体的外观照片。图36示出从生长面观察的生长晶体的外观照片。附图标记说明1侧面部2底侧面部3底部100单晶制造装置200单晶制造装置10坩埚50支持部件11坩埚底部的外壁12晶种保持轴51支持部件的顶面14晶种基板15坩埚底部的内壁16坩埚深度18隔热材料22高频线圈22A上段高频线圈22B下段高频线圈24Si-C溶液26石英管28坩埚上部的开口部34弯液面40坩埚的底侧面部的区域41坩埚的底侧面部的区域ID坩埚的内径OD坩埚的外径Lb坩埚底部的铅直方向的厚度Lzo支持部件的外径Lu坩埚的Si-C溶液的液面高度之处的水平方向的厚度Ld坩埚的底部内壁的高度之处的水平方向的厚度Lx坩埚的Ld与Lu之间的水平方向的厚度具体实施方式在本说明书中,(000-1)面等的表达中的“-1”是将原本在数字上方赋予横线而表达之处表达为“-1”。在Si-C溶液中产生杂晶时,杂晶附着于生长晶体而不能得到均匀的单晶。在对杂晶的产生机理进行专心研究时知晓,当在坩埚的内壁附近Si-C溶液的温度梯度增大时,产生杂晶。由于Si-C溶液在与坩埚内壁相接触的部位显示最高温度,从显示该最高温度的部位向着晶体生长面的中心部的正下方的Si-C溶液的表面、在间隔了规定距离的地点显示相对低的温度,因此在Si-C溶液内形成了以与坩埚内壁相接触的部位为最高温度而温度降低的温度差ΔT。由于碳在温度高的Si-C溶液中更多地溶解,因此温度差ΔT大时,过饱和度增大,结果在坩埚内壁附近溶解的碳从Si-C溶液中析出,作为杂晶附着于生长晶体。本发明人得到上述认识,发现了一种与以往相比可进一步抑制杂晶产生的基于溶液法的SiC单晶的制造方法。本公开的方法以SiC单晶的制造方法为对象,该制造方法为使晶种基板与置于坩埚内的具有从内部向液面温度降低的温度梯度的Si-C溶液接触以使SiC单晶晶体生长的SiC单晶的制造方法,坩埚具有厚度Lu和厚度Ld,厚度Lu是在与Si-C溶液的液面相同高度之处的坩埚的水平方向厚度,厚度Ld是在与坩埚的底部内壁相同高度之处的坩埚的水平方向的厚度,Ld相对于Lu之比即Ld/Lu为2.00~4.21;在厚度Lu与厚度Ld之间,坩埚的水平方向的厚度从厚度Lu向厚度Ld单调增加;坩埚的壁厚为1mm以上;坩埚的底部的铅直方向的厚度Lb为1mm以上15mm以下;坩埚的底部外壁具有平坦部,平坦部的面积为100mm2以上;使置于坩埚内的Si-C溶液距坩埚的底部内壁的深度为30mm以上;该制造方法包括:利用配置于坩埚周围的高频线圈对Si-C溶液进行加热和电磁搅拌。根据本公开的方法,由于可减小在Si-C溶液中显示最高温度的坩埚内壁附近的Si-C溶液的温度梯度,因此可与以往相比抑制杂晶的产生。在本说明书中,将与坩埚内壁相接触的部位的Si-C溶液的最高温度、与从显示最高温度的部位向着晶体生长面的中心部的正下方的Si-C溶液的表面并距显示最高温度的部位6mm的地点的温度之差设为ΔT(以下,称作温度差ΔT或ΔT)。通过减小该范围的温度差ΔT,可抑制杂晶的产生。通过本公开的方法得到的温度差ΔT基本上为0℃。与坩埚内壁相接触的部位的Si-C溶液的最高温度与晶体生长面的中心部正下方的Si-C溶液的表面的温度之差最大,将该温度差设为ΔTmax(以下,称作ΔTmax)。从抑制杂晶的观点考虑不特别限定ΔTmax,但从得到高的生长速度的观点考虑,优选为5℃以上。图1示出可用于本公开的方法的坩埚的一例的截面示意图。坩埚10收容Si-C溶液24。在本说明书中,将坩埚10的侧面部、底侧面部和底部称作图1中例示的坩埚的侧面部1、底侧面部2和底部3。侧面部1是指坩埚10的内壁在铅直方向以直线状延伸的区域,底部3是指坩埚的内壁在水平方向以直线状延伸的区域,底侧面部2是指侧面部1与底部3之间的区域。在图1的坩埚10中,底侧面部2的内壁和外壁具有曲线形状。图2示出坩埚10的其它例子的截面示意图。在图2的坩埚10中,侧面部1和底部3之间的底侧面部2的外壁具有直线(直角)形状。图3示出坩埚的其它例子的截面示意图。在图3的坩埚10中,底侧面部和底部的内壁全部以曲线形状形成。在该情况下,坩埚10也由侧面部1、底侧面部2和底部3构成。在图3的坩埚10中,底部3是内壁位于最低位置的部位。图4示出坩埚的其它例子的截面示意图。在图4的坩埚10中,内壁全部以曲线形状形成。图4的坩埚10不具有侧面部,由底侧面部2和底部3构成。在图4的坩埚10中,底部3是内壁位于最低位置的部位。如图1~4所示,底侧面部2的内壁和外壁可具有曲线状、直线状等所期望的形状。底侧面部2的内壁优选具有规定的曲率半径。底侧面部2的内壁的曲率半径的下限值优选为R20mm以上、R25mm以上、R30mm以上或R35mm以上,上限值优选为R50mm以下、R45mm以下、R40mm以下或R35mm以下。坩埚10的侧面部的水平方向的厚度优选为5~20mm,底侧面部的内壁的位置之处的水平方向的厚度优选为10~84mm。通过坩埚10的侧面部和底侧面部为这样的水平方向的厚度范围,可在抑制杂晶的产生的同时使Si-C溶液因高频线圈的电磁搅拌效应而更良好地流动。在图5中示出图1所示的底侧面部的区域40的放大截面图。如图5所示,将与Si-C溶液24的液面相同高度之处的坩埚10的水平方向的厚度称作Lu。另外,将与坩埚10的底部内壁15相同高度之处的坩埚10的水平方向的厚度称作Ld。在本公开的方法中,与坩埚10的底部内壁15相同高度之处的坩埚10的水平方向的厚度Ld相对于与Si-C溶液24的液面相同高度之处的坩埚10的水平方向的厚度Lu之比即Ld/Lu之比为2.00~4.21。Ld/Lu之比的上限优选为3.68以下,下限优选为3.12以上。通过Ld/Lu之比在上述范围内,可使Si-C溶液24内的温度差ΔT为0℃。在图6中示出图2所示的底侧面部的区域41的放大截面图。在图6中示出的坩埚的情况下,与图5所示的底侧面部的外壁为曲线形状的坩埚10同样,Ld/Lu之比也满足上述范围。如图5和6所示,将厚度Lu和厚度Ld之间的坩埚10的水平方向的厚度称作Lx。厚度Lx可根据距坩埚10的底部内壁15的铅直方向的高度x而变化。优选地,厚度Lx从厚度Lu向厚度Ld(从坩埚10的上方向下方)单调增加。在坩埚10的底侧面部,从厚度Lu向厚度Ld(向下方),优选增加比例逐渐地变大。上述单调增加也包括恒定,在坩埚10的侧面部,坩埚10的水平方向的厚度为恒定。Lx在Si-C溶液的液面高度之处等于Lu,在坩埚10的底部内壁15的高度之处等于Ld。优选地,距坩埚10的底部内壁15铅直方向向上的高度x越大,厚度Lx越小,在与Si-C溶液24的液面相同的高度之处,厚度Lx等于坩埚的水平方向的厚度Lu。可将厚度Lx相对于厚度Lu的比例的优选范围作为距坩埚10的底部内壁15铅直方向向上的高度x的函数通过式(1)和式(2)来表示:6.981×10-8x6-8.192×10-6x5+3.756×10-4x4-8.572×10-3x3+1.052×10-1x2-7.503×10-1x+4.21≥Lx/Lu(1),Lx/Lu≥1.190×10-9x6-2.308×10-7x5+1.832×10-5x4-7.550×10-4x3+1.706×10-2x2-2.019×10-1x+2.00(2)(在式(1)和式(2)中,x为0~35)。图7中以图示出基于式(1)和式(2)的Lx/Lu相对于高度x的优选范围。由通过式(1)和式(2)描绘的曲线所夹着的范围为Lx/Lu的优选范围。坩埚10在侧面部、底侧面部和底部的全部位置具有1mm以上、优选2mm以上、更优选3mm以上的壁厚。在本说明书中,壁厚是指垂直于坩埚10的内壁面的方向的坩埚10的侧面部、底侧面部和底部的厚度。通过坩埚10具有上述范围的壁厚,能够防止由坩埚10的破损或溶解引起的孔的形成。如图1~4所示,坩埚10具有底部厚度Lb。底部厚度Lb是坩埚10的底部的铅直方向的厚度。如图3和4所示,在坩埚10的底部内壁具有曲线形状的情况下,底部厚度Lb是指坩埚10的底部内壁最低部分的铅直方向的厚度。底部厚度Lb与底部的上述壁厚相同。坩埚10的底部厚度Lb为1mm以上15mm以下。底部厚度Lb的上限优选为12mm以下、更优选为10mm以下,底部厚度Lb的下限优选为2mm以上、更优选为3mm以上。通过底部厚度Lb在上述范围内,可减小从坩埚10的下方的加热对于Si-C溶液24的影响并减小温度差ΔT,并且可防止由坩埚的破损和溶解引起的孔的形成。如图1~4所示,坩埚10具有底部外壁11,该底部外壁11为在水平方向延伸的基本平坦的平坦部。底部外壁11的平坦部的面积为100mm2以上,优选为200mm2以上,更优选为300mm2以上。通过底部外壁11的平坦部的面积在上述范围内,可将坩埚10稳定地配置在SiC单晶制造装置内。在使SiC单晶生长时,也可以使坩埚10的位置上下移动和/或使坩埚10旋转,在该情况下,通过底部外壁11的平坦部的面积在上述范围内,也可稳定地配置坩埚10。在将坩埚10配置于SiC单晶制造装置内时,优选将坩埚10配置在隔热材料上。坩埚10在隔热材料上的配置可以通过将坩埚10载置在隔热材料上来进行,也可以通过使用粘接剂将坩埚10固定在隔热材料上来进行,或者还可以通过将坩埚10的至少一部分嵌入隔热材料内来进行。通过使底部外壁11的平坦部的面积在上述范围内,仅将坩埚10载置在隔热材料上也可稳定地配置坩埚10。即使在使用粘接剂将坩埚10固定在隔热材料上的情况下,由于可在底部外壁11的平坦部与隔热材料之间配置粘接剂,因此通过使底部外壁11的平坦部的面积在上述范围内,可更稳定地固定坩埚10。即使在将坩埚10的至少一部分嵌入隔热材料内的情况下,通过使底部外壁11平坦且具有上述范围内的面积,也可稳定地配置坩埚。作为粘接剂,可使用碳粘接剂。在本公开的方法中,如图8所示,优选地,在坩埚10的底部外壁的下方将支持部件50与底部外壁相接触地配置。支持部件50由与坩埚10相同的材料构成。坩埚10和支持部件50可以为石墨等碳质材料或SiC,与构成隔热材料18的材料相比强度大。作为坩埚10和支持部件50的材质,优选密度为1.55~2.00g/cm3范围的石墨。作为隔热材料18,可使用通常具有0.1~0.16g/cm3范围的密度的石墨。在配置了支持部件50的情况下,支持部件50具有规定大小的外径Lzo,外径Lzo相对于坩埚10的外径OD具有规定的比例。在本说明书中,坩埚10的外径OD是指与Si-C溶液24的液面位置相同高度之处的坩埚10的外径。从上面观察,坩埚10可以为圆形(包括正圆和椭圆)、多边形等,外径OD是指从上面观察坩埚10时的形状的最长对角线的长度(在内部包含正圆、椭圆或多边形的最小圆的直径)。在从上面观察时,坩埚10优选具有正圆形状。在该情况下,使坩埚或晶种基板旋转时以旋转轴为中心Si-C溶液的流动变得各向同性,可使均匀的SiC单晶稳定地生长。支持部件50只要是在铅直方向具有基本一定的外径Lzo的形状就可以为任意的形状。支持部件50例如可具有圆柱形状(包括正圆柱或椭圆柱)或棱柱形状。支持部件50的外径Lzo在支持部件50具有正圆柱形状的情况下是指其直径,在支持部件50具有椭圆柱形状或棱柱形状的情况下是指最长对角线的长度(在内部包含椭圆柱或多边形的最小圆的直径)。在坩埚10的底部外壁11的下方配置支持部件50。支持部件50具有顶面51,该顶面51为在水平方向延伸的基本平坦的平坦部。可以以支持部件50的顶面51与为平坦部的底部外壁11相接触的方式配置坩埚10和支持部件50,或者也可以配置将底部外壁11与顶面51一体化的坩埚10和支持部件50。在以支持部件50的顶面51与为平坦部的底部外壁11相接触的方式配置坩埚10和支持部件50的情况下,将底部外壁11的至少一部分与支持部件50的顶面51的至少一部分粘接。可使用碳粘接剂等将底部外壁11与支持部件50的顶面51粘接。作为支持部件50的外径Lzo相对于坩埚10的外径OD之比的Lzo/OD的上限为0.25以下,优选为0.1以下。但是,支持部件50的外径Lzo为10mm以上,优选为15mm以上,更优选为20mm以上。外径OD的大小只要Lzo/OD具有上述比例就不特别限定,但例如可以为50~300mm。通过使Lzo/OD和外径Lzo处于上述范围内,可减小从坩埚10的下方的加热对Si-C溶液24的影响,可减小温度差ΔT,并且也可在利用支持部件50稳定地保持坩埚10的同时防止支持部件50的破损。从保持坩埚10的稳定的观点考虑,优选支持部件50的铅直方向的长度为5mm以上。支持部件50的铅直方向的长度的上限不特别限定,但例如可以为100mm以下、50mm以下或30mm以下。与支持部件的直径相比,铅直方向的长度对ΔT的影响小,但支持部件的铅直方向的长度越短,可进一步减小Si-C溶液24的ΔT。可以在支持部件50的周围配置隔热材料18,或者在支持部件50的周围形成空间。在配置隔热材料18的情况下,也可以将隔热材料18的一部分设为空间。可将氩气、氮气等气氛气体导入空间中。可从石墨切出而得到一体化的坩埚10和支持部件50。在该情况下,如下地决定坩埚10与支持部件50的边界。在作为坩埚10的平坦部的底部外壁11的面积大于作为面对底部外壁11的平坦部的支持部件50的顶面51的面积的情况下,面积更大的坩埚10的底部外壁11的水平部分成为边界。在坩埚10的底部外壁11的面积小于面对底部外壁11的支持部件50的顶面51的面积的情况下,面积更大的支持部件50的顶面51成为边界。在坩埚10的底部外壁11的面积与面对底部外壁11的支持部件50的顶面51的面积相同的情况下,按如下这样确定边界。由于支持部件50具有在整个铅直方向基本一定值的外径Lzo,因此支持部件50的顶面51成为边界,但在坩埚10与支持部件50具有相同外径的情况下,坩埚10的底部厚度Lb为15mm、即距底部内壁15铅直方向向下15mm的位置成为边界。置于坩埚10内的Si-C溶液24的深度(从坩埚10的底部内壁15沿着铅直方向向上的深度)为30mm以上,优选为40mm以上,更优选50mm以上。通过使Si-C溶液24的深度处于上述范围,可提高面向晶体生长面的Si-C溶液的上升流速,从而进行稳定的SiC单晶的生长。通过配置于坩埚10的周围的高频线圈来对Si-C溶液24进行加热和电磁搅拌。高频线圈的频率不特别限定,但例如可设为1~10kHz或1~5kHz。以下,对根据本公开的方法的上述以外的构成的例子进行说明。根据本公开的方法为基于溶液法的SiC单晶的制造方法。在溶液法中,可使SiC晶种基板与从内部向表面(液面)在垂直于液面的方向上具有温度降低的温度梯度的Si-C溶液接触从而使SiC单晶生长。通过形成从Si-C溶液的内部向溶液的液面温度降低的温度梯度,可使Si-C溶液的表面区域过饱和,以与Si-C溶液接触的晶种基板为基点,使SiC单晶生长。图9中示出可用于本公开的方法的SiC单晶制造装置的一例的截面示意图。图示的SiC单晶制造装置100具备收容了C在Si或Si/X(X为Si以外的一种以上的金属)的熔液中溶解而成的Si-C溶液24的坩埚10,形成从Si-C溶液24的内部向溶液的表面温度降低的温度梯度,能够使保持于可在铅直方向移动的晶种保持轴12的前端的晶种基板14与Si-C溶液24接触,以晶种基板14为基点使SiC单晶生长。通过将原料装入坩埚10,使C溶解在经加热熔化而制备的Si或Si/X的熔液中来制备Si-C溶液24。X只要为Si以外的一种以上的金属,并且可与SiC(固相)形成在热力学上成为平衡状态的液相(溶液)就不特别限定。作为合适的金属X的例子,可举出Ti、Cr、Ni等。例如,在坩埚10内除Si以外再装入Cr等,可形成Si/Cr溶液等。通过含C的坩埚10的溶解,C溶解在熔液中,可形成Si-C溶液。这样,在Si-C溶液24中不存在未溶解的C,可防止由SiC单晶在未溶解的C上的析出而引起的SiC的浪费。C的供给例如可以利用烃气的吹入或者将固体的C供给源与熔液原料一起装入的方法,或者可以将这些方法与坩埚的溶解组合。为了保温,用隔热材料18覆盖坩埚10的外周。可以将它们一并收容在石英管26内。在石英管26的外周配置加热用的高频线圈22。高频线圈22可以由上段线圈22A和下段线圈22B构成,上段线圈22A和下段线圈22B可各自独立地控制。通过利用配置于其侧面部周围的高频线圈对石墨坩埚等碳质坩埚或SiC坩埚进行加热,由高频引起的感应电流在坩埚的外周部流动,将该部分加热并将内部的Si-C溶液加热,另外,由于由高频线圈引起的电磁场的一部分到达Si-C溶液,因此由高频加热引起的洛伦兹力被施加于石墨坩埚内部的Si-C溶液,也可得到对Si-C溶液进行电磁搅拌的效果。由于坩埚10、隔热材料18、石英管26和高频线圈22成为高温,因此配置在水冷腔室的内部。为了可调整装置内的气氛,水冷腔室具备气体导入口和气体排出口。坩埚10在上部具备隔热材料18,隔热材料18具备通过晶种保持轴12的开口部28。通过调节开口部28处的隔热材料18与晶种保持轴12之间的间隙(间隔),可改变来自Si-C溶液24的表面的辐射热损失的程度。通常坩埚10的内部需要保持为高温,但较大地设定开口部28处的隔热材料18与晶种保持轴12之间的间隙时,可增大来自Si-C溶液24的表面的辐射热损失;使开口部28处的隔热材料18与晶种保持轴12之间的间隙变窄时,可减小来自Si-C溶液24的表面的辐射热损失。开口部28处的隔热材料18与晶种保持轴12之间的间隙(间隔)优选为1~5mm,更优选为3~4mm。在形成后述的弯液面时,也可以自弯液面部分发生辐射热损失。Si-C溶液24的温度通常由于辐射等形成与Si-C溶液24的内部相比表面的温度低的温度分布,但进一步地,通过调整高频线圈22的圈数及间隔、高频线圈22与坩埚10的高度方向的位置关系以及高频线圈22的输出,可在Si-C溶液24中形成垂直于Si-C溶液24的表面的方向的温度梯度,使得晶种基板14接触的溶液上部成为低温、溶液下部(内部)成为高温。例如,使上段线圈22A的输出小于下段线圈22B的输出,能够在Si-C溶液24中形成溶液上部成为低温、溶液下部成为高温的温度梯度。在例如从溶液表面至深度为约1cm的范围内,温度梯度优选为10~50℃/cm。在Si-C溶液24中溶解的C通过扩散和对流而被分散。通过高频线圈的输出控制、来自Si-C溶液24表面的热损失以及经由晶种保持轴12的热损失等,晶种基板14的底面附近可形成与Si-C溶液24的内部相比成为低温的温度梯度。在高温且溶解度大的溶液内部溶入的C在到达低温且溶解度低的晶种基板附近时成为过饱和状态,可以以该过饱和度为驱动力使SiC晶体在晶种基板14上生长。在本公开的方法中,可以将Si-C溶液的机械搅拌与利用高频加热的电磁搅拌组合。例如,可以使晶种基板和坩埚中的至少一者旋转。可以使晶种基板和坩埚中的至少一者以规定的速度在一定方向上连续旋转规定的时间以上,周期性地转换旋转方向。晶种基板和坩埚的旋转方向和旋转速度可任意地确定。通过使晶种基板的旋转方向周期性地变化,可使SiC单晶以同心圆状生长,能够抑制可在生长晶体中发生的缺陷的产生,此时,通过将同一方向的旋转维持规定的时间以上,可使晶体生长界面正下方的Si-C溶液的流动稳定化。如果旋转保持时间过短,则频繁地进行旋转方向的转换,可认为Si-C溶液的流动变得不充分或不稳定。在使晶种基板的旋转方向周期性地变化的情况下,同方向的旋转保持时间优选长于30秒,更优选为200秒以上,进一步优选为360秒以上。通过使晶种基板的同方向的旋转保持时间处于上述范围,易于进一步抑制夹杂物以及贯穿位错的产生。在使晶种基板的旋转方向周期性地变化的情况下,将旋转方向向反方向转换时的晶种基板的停止时间越短越好,优选为10秒以下,更优选为5秒以下,进一步优选为1秒以下,进一步更优选基本上为0秒。在使SiC单晶生长时,优选在晶种基板与Si-C溶液之间形成弯液面的同时使晶体生长。如图10所示,弯液面是指由于表面张力而在向上润湿晶种基板14的Si-C溶液24的表面所形成的凹状的曲面34。可在晶种基板14与Si-C溶液24之间形成弯液面的同时使SiC单晶生长。例如,在使晶种基板14与Si-C溶液24接触后,可通过将晶种基板14的底面提拉至晶种基板14的底面高于Si-C溶液24的液面的位置并进行保持,从而形成弯液面。由于在生长界面外周部所形成的弯液面部分因辐射热损失而温度易于下降,因此通过形成弯液面,易于增大温度梯度。另外,由于可形成与晶体生长面的界面正下方的中央部相比外周部的Si-C溶液的温度降低的温度梯度,因此可使生长界面的外周部的Si-C溶液的过饱和度大于生长界面的中心部的Si-C溶液的过饱和度。通过这样在晶体生长界面正下方的Si-C溶液内形成水平方向的过饱和度的倾斜,可使SiC晶体以具有凹形状的晶体生长面的方式生长。由此,可以以SiC单晶的晶体生长面不成为正面(on-axisplane)的方式使晶体生长,易于抑制夹杂物以及贯穿位错的产生。在本公开的方法中,可使用通常用于SiC单晶制造的质量的SiC单晶作为晶种基板,例如可使用通过升华法通常制作的SiC单晶作为晶种基板。作为晶种基板,例如可使用生长面为平坦的且具有(0001)正面或(000-1)正面的SiC单晶,生长面为平坦的且具有自(0001)正面或(000-1)正面大于0°例如8°以下的偏离角度的SiC单晶,或者生长面具有凹形状且在凹形状的生长面的中央部附近的一部分具有(0001)面或(000-1)面的SiC单晶。晶种基板的整体形状例如可以为板状、圆盘状、圆柱状、棱柱状、圆锥台状或棱锥台状等任意形状。晶种基板在单晶制造装置中的设置可通过使用粘接剂等使晶种基板的顶面保持于晶种保持轴来进行。粘接剂可以为碳粘接剂。晶种基板与Si-C溶液的接触可通过如下进行:使保持有晶种基板的晶种保持轴向着Si-C溶液的液面下降,使晶种基板的底面相对于Si-C溶液面平行地与Si-C溶液接触。然后,可将晶种基板相对于Si-C溶液面保持于规定位置以使SiC单晶生长。晶种基板的保持位置可以是晶种基板的底面的位置与Si-C溶液面一致,或可以相对于Si-C溶液面位于下侧,或者可以相对于Si-C溶液面位于上侧。在将晶种基板的底面相对于Si-C溶液面保持于上方的位置的情况下,一旦使晶种基板与Si-C溶液接触以使晶种基板的底面与Si-C溶液接触之后,提拉至规定的位置。也可以使晶种基板的底面的位置与Si-C溶液面一致,或者与Si-C溶液面相比位于下侧,但为了如上所述形成弯液面,优选将晶种基板的底面相对于Si-C溶液面保持于上方的位置来使晶体生长。另外,为了防止多晶的产生,优选Si-C溶液不与晶种保持轴接触。通过形成弯液面,可容易地防止Si-C溶液与晶种保持轴的接触。在这些方法中,也可以在晶体生长中调节晶种基板的位置。晶种保持轴可以是将晶种基板保持于其端面的石墨轴。优选地,晶种保持轴由与坩埚相同的材质构成。晶种保持轴可以为圆柱状、棱柱状等任意形状,也可以使用具有与晶种基板的顶面的形状相同的端面形状的石墨轴。Si-C溶液优选其表面温度为C在Si-C溶液中的溶解量的变动少的1800~2200℃。Si-C溶液的温度测定可以使用热电偶、辐射温度计等来进行。关于热电偶,从高温测定和防止杂质混入的观点考虑,优选在石墨保护管中放入了被覆有氧化锆或氧化镁玻璃的钨-铼线的热电偶。在SiC单晶的生长前,也可以进行使晶种基板的表面层溶解在Si-C溶液中而被除去的回熔。在使SiC单晶生长的晶种基板的表层,有时存在位错等的加工变质层或自然氧化膜等,在使SiC单晶生长前将它们溶解并除去对于使高质量的SiC单晶生长是有效的。溶解的厚度根据晶种基板的表面的加工状态而变化,但为了充分地除去加工变质层和自然氧化膜,优选为约5~50μm。回熔可通过如下进行:在Si-C溶液中形成从Si-C溶液的内部向溶液的表面温度增加的温度梯度,即形成与SiC单晶生长反方向的温度梯度。可通过控制高频线圈的输出来形成上述反方向的温度梯度。也可以在预先加热晶种基板之后使晶种基板与Si-C溶液接触。如果使低温的晶种基板与高温的Si-C溶液接触,则有时在晶种中产生热冲击位错。在使晶种基板与Si-C溶液接触前预先加热晶种基板,对于防止热冲击位错并使高质量的SiC单晶生长是有效的。晶种基板的加热可与加热晶种保持轴一同进行。在该情况下,在使晶种基板与Si-C溶液接触后、在使SiC单晶生长前停止晶种保持轴的加热。另外,代替该方法,也可以在使晶种与较低温的Si-C溶液接触之后,将Si-C溶液加热至使晶体生长的温度。在该情况下,对于防止热冲击位错并使高质量的SiC单晶生长也是有效的。实施例(基于Ld/Lu比的ΔT的模拟)对于通过溶液法(Flux法)使SiC单晶生长时的基于Ld/Lu比的ΔT,使用CGSim(从溶液生长块状晶体的模拟软件,STRJapan制,Ver.14.1)进行模拟。作为和坩埚内壁相接触的部位的Si-C溶液的最高温度与从显示最高温度的部位向着晶体生长面的中心部正下方的Si-C溶液的表面并距显示最高温度的部位6mm地点的温度之差来计算出ΔT。作为模拟条件,设定以下的标准条件。(标准模型的制作)作为单晶制造装置,制作如图9所示的单晶制造装置100的构成的对称模型。将在直径为9mm及长度为180mm的圆柱的前端具备有厚度2mm及直径25mm的圆板的石墨轴作为晶种保持轴12。将厚度1mm、直径25mm的圆盘状4H-SiC单晶作为晶种基板14。使晶种基板14的顶面保持于晶种保持轴12的端面的中央部。配置隔热材料18,使得从上面观察围绕正圆形状的坩埚10的周围和上部。隔热材料18的厚度在坩埚10的侧面部和上部分别设为15mm。将晶种保持轴12通过在坩埚10的上部配置的隔热材料18中开设的直径20mm的开口部28,配置晶种保持轴12和晶种基板14。将开口部28处的隔热材料18和晶种保持轴12之间的间隙分别设为5.5mm。在石墨的坩埚10内配置Si熔液。使单晶制造装置内部的气氛为氦。在坩埚10的水平方向的周围配置由可各自独立地控制输出的上段线圈22A和下段线圈22B构成的高频线圈22。上段线圈22A具备5圈高频线圈,下段线圈22B具备10圈高频线圈。将各线圈在水平方向上距坩埚10的侧面部65mm的位置在铅直方向上排成一列,在从坩埚10的外周面的最下部沿铅直方向向上从54.5mm的位置到223.5mm(距坩埚10的外周面的最上部沿铅直方向向下33.5mm)的位置的范围内均等地配置。以晶种基板14的底面相对于Si-C溶液24的液面位置位于上方1.5mm的方式配置保持于晶种保持轴的晶种基板14,以Si-C溶液润湿晶种基板14的全部底面的方式形成如图10所示的弯液面。使Si-C溶液24的液面处的弯液面部分的直径为30mm,为了计算的简便,将Si-C溶液24的液面与晶种基板14的底面之间的弯液面的形状视为直线形状。将Si-C溶液24的液面中心的温度设为2000℃,将Si-C溶液的表面作为低温侧,将Si-C溶液的表面温度与距Si-C溶液24表面向着溶液内部铅直方向的深度1cm的位置处的温度的温度差设为25℃。以5rpm、以晶种保持轴12的中心轴为中心使坩埚10旋转。其它模拟条件如下所述。使用2D对称模型计算;各材料的物理性质如下所述:坩埚10、晶种保持轴12:材质为石墨,密度为1.8g/cm3,2000℃下的热导率=17W/(m·K),辐射率=0.9;隔热材料18:材质为石墨,密度为0.13g/cm3,2500℃下的热导率=1.2W/(m·K),辐射率=0.8;Si-C溶液:材质为Si熔液,2000℃下的热导率=66.5W/(m·K),辐射率=0.9,密度=2600kg/m3,导电率=2245000S/m;He:2000℃下的热导率=0.579W/(m·K);水冷腔室和高频线圈的温度=300K。(实施例1~4)(基于Ld/Lu的ΔT的模拟)除了上述条件外,改变坩埚10的底侧面部的外壁形状以改变厚度Ld,对Ld/Lu与ΔT的关系进行模拟。将模拟中使用的坩埚10、晶种保持轴12、晶种基板14、隔热材料18和Si-C溶液24的布局示于图11~14。在坩埚10中,将外径设为100mm,将内径设为85mm,将底侧面部的内壁的曲率半径设为R35mm,将侧面部的水平方向的厚度(与Si-C溶液24的液面相同高度之处的水平方向的厚度Lu)设为7.5mm,将底部的铅直方向的厚度Lb设为15mm,并且将坩埚深度(从底部内壁15至侧面部的上部前端的铅直方向的长度)设为120mm,将与底部内壁15相同高度之处的水平方向的厚度Ld改变为15mm、23.37mm、27.6mm和31.58mm。Ld/Lu比为2.00、3.12、3.68和4.21。将具有与坩埚10的外径相同外径以及30mm的铅直方向的厚度的隔热材料18配置于坩埚10的下部。将高频线圈22的频率设为5kHz。将Si-C溶液24的深度设为沿铅直方向向上距底部内壁15为35mm。通过基于上述条件的模拟计算ΔT时,均为ΔT=0.0℃。图15中示出实施例2(图12的布局)中得到的Si-C溶液的温度分布的模拟结果以及温度差ΔT和ΔTmax的测定部位。(比较例1~2)如图16和17的布局所示,将厚度Ld设为7.5mm和37.5mm、将Ld/Lu比分别设为1和5,除此以外,在与实施例1~4同样的条件下进行ΔT的模拟。ΔT分别为1.1℃和3.1℃。图18中示出通过模拟得到的表示Ld/Lu与ΔT的关系的图。另外,表1中示出实施例1~4和比较例1~2的坩埚形状以及得到的ΔT和ΔTmax。表1LdLuLd/LuΔTΔTmax实施例1157.52.000.05.9实施例223.377.53.120.06.1实施例327.67.53.680.07.5实施例431.587.54.210.07.7比较例17.57.51.001.17.5比较例237.57.55.003.113.5当Ld/Lu在2.00~4.21的范围内,得到了ΔT=0.0℃。将坩埚10的底侧面部的水平方向的厚度、即距坩埚10的底部内壁15在铅直方向上方的高度x(mm)处的厚度设为厚度Lx(mm),在表2中以数学式示出厚度Lx相对于实施例1~4和比较例1~2的布局中的坩埚10的高度x,并在图19中图表化地表示。表2(实施例4~6和比较例3~4)(基于Lb的ΔT的模拟)除了将坩埚底部的铅直方向的厚度Lb在5~50mm的范围内改变以外,在与实施例4同样的条件下,对厚度Lb与ΔT的关系进行模拟。表3中示出实施例4~6和比较例3~4中的厚度Lb以及通过模拟计算出的ΔT。图20中示出表示厚度Lb与ΔT的关系的图。当厚度Lb在15mm以下的范围内,得到了ΔT=0.0℃。表3LbΔT实施例650.0实施例5100.0实施例4150.0比较例4306.1比较例35010.8(基于Lzo/OD比的ΔT的模拟)(实施例4和7~8)作为单晶制造装置,制作了图21所示的单晶制造装置200的构成的对称模型。除了配置保持部件50以外,与图9中示出的单晶制造装置100的构成相同。除了如图22和23所示在坩埚10的下方配置保持部件50以外,在与实施例4同样的条件下进行ΔT的模拟。在保持部件50的周围配置隔热材料18。保持部件50的材质设为与坩埚10相同的石墨(密度为1.8g/cm3,2000℃下的热导率=17W/(m·K),辐射率=0.9)。保持部件50为长度30mm的正圆柱形状,外径分别为10mm和25mm,Lzo/OD比分别为0.1和0.25。在通过模拟计算ΔT时,ΔT均为0.0℃。(比较例5~7)除了如图24~26的布局所示将保持部件50的外径Lzo分别变为50mm、75mm和100mm并将Lzo/OD比分别设为0.5、0.75和1以外,在与实施例7同样的条件下,进行ΔT的模拟。保持部件50的外径增大的部分减小了配置于坩埚10下方的隔热材料18,在图26的布局中,取消配置于坩埚10下方的隔热材料18。ΔT分别为2.2℃、5.1℃和8.0℃。图27中示出实施例8中得到的Si-C溶液的温度分布的模拟结果,以及温度差ΔT和ΔTmax的测定部位。表4中示出实施例4和7~8以及比较例5~7中的坩埚10的厚度Ld、厚度Lu、Ld/Lu和Lzo/OD,以及通过模拟计算出的ΔT和ΔTmax。图28中示出表示Lzo/OD与ΔT的关系的图。表4LdLuLd/LuLzoLzo/ODΔTΔTmax比较例731.587.54.2110018.010.6比较例631.587.54.21750.755.115.5比较例531.587.54.21500.52.212.1实施例831.587.54.21250.250.013.5实施例731.587.54.21100.10.013.6实施例431.587.54.21000.014.3(实施例9)(改变坩埚的外径OD、保持部件的外径Lzo、Lzo/OD以及高频线圈的频率时的ΔT的模拟)除了将坩埚10的外径OD设为135mm、保持部件50的外径Lzo设为30mm、Lzo/OD=0.22以及高频线圈的频率设为1.9kHz以外,在与实施例7同样的条件下(底侧面部的内壁的曲率半径=R35mm,厚度Lu=7.5mm,厚度Ld=31.58,Ld/Lu=4.21)模拟ΔT。图29中示出模拟中使用的坩埚的布局,图30中示出模拟结果。在本例中,也与实施例7同样地得到了ΔT=0.0℃。(实施例10)(将保持部件周围的隔热材料替代为空间时的ΔT的模拟)除了将保持部件50周围的隔热材料变为空间,在空间中以1大气压填充作为气氛气体的氩气以外,在与实施例8同样的条件下模拟ΔT。图31中示出模拟中使用的布局。图32中示出模拟结果。即使在将保持部件50周围的隔热材料变为空间的情况下,也与实施例8同样地得到了ΔT=0.0℃。(实施例11)(SiC晶体生长)准备底面具有(000-1)面的通过升华法制作的SiC单晶并用作晶种基板,该SiC单晶是直径为5.1cm、厚度为1mm的圆盘状4H-SiC单晶,在收容Si-C溶液的石墨坩埚10中以按照原子组成百分比计为60:40的比例装入Si/Cr作为熔液原料,使用图9所示的单晶制造装置100,除此以外,在与实施例4同样的条件下,使SiC晶体实际地生长。以下,示出生长条件的详细内容。在将单晶制造装置100的内部抽真空至1×10-3Pa之后,导入氩气直至成为1大气压,用氩置换单晶制造装置100内部的空气。对配置于石墨坩埚10周围的作为加热装置的高频线圈22通电,通过加热熔化石墨坩埚10内的原料,形成Si/Cr合金的熔液。然后,使足够量的C从石墨坩埚10溶解到Si/Cr合金的熔液中,形成Si-C溶液24。调节上段线圈22A和下段线圈22B的输出以加热石墨坩埚10,以使Si-C溶液24的表面处的温度升温至2000℃、且在距Si-C溶液24的表面1cm范围内从溶液内部向溶液表面温度降低的平均温度梯度成为25℃/cm的方式进行控制。利用辐射温度计进行Si-C溶液24的表面的温度测定,使用可在铅直方向移动的热电偶进行Si-C溶液24的温度梯度的测定。使与晶种保持轴12粘接的晶种基板14的底面与Si-C溶液24的液面平行,将晶种基板14的底面的位置配置在与Si-C溶液24的液面一致的位置,以Si-C溶液不向上润湿接触石墨轴的方式进行使晶种基板14的底面与Si-C溶液24接触的籽晶接触(seedtouch),接着提拉至上方1.5mm处,以Si-C溶液润湿晶种基板14的全部底面的方式形成如图10所示的弯液面。在该位置保持12小时,使晶体生长。晶体生长结束后,使晶种保持轴12上升,冷却至室温,从Si-C溶液24和晶种保持轴12切离并回收晶种基板14以及以晶种基板为基点生长的SiC晶体。在从侧面和生长面对得到的生长晶体进行显微镜照相时,在生长晶体中没有产生杂晶。图33和34中示出从侧面和生长面观察的生长晶体的外观照片。得到的生长晶体具有5.7cm的直径和2.6mm的厚度。得到的生长晶体的直径为生长面的直径。(比较例8)将生长保持时间设为10小时,在与比较例6同样的条件下使SiC晶体实际地生长,除此以外,与上述实施例11同样地使SiC晶体实际地生长。从侧面和生长面对得到的生长晶体进行显微镜照相时,在生长晶体中看到了杂晶。图35和36中示出从侧面和生长面观察的生长晶体的外观照片。得到的生长晶体具有5.8cm的直径和2.1mm的厚度。当前第1页1 2 3