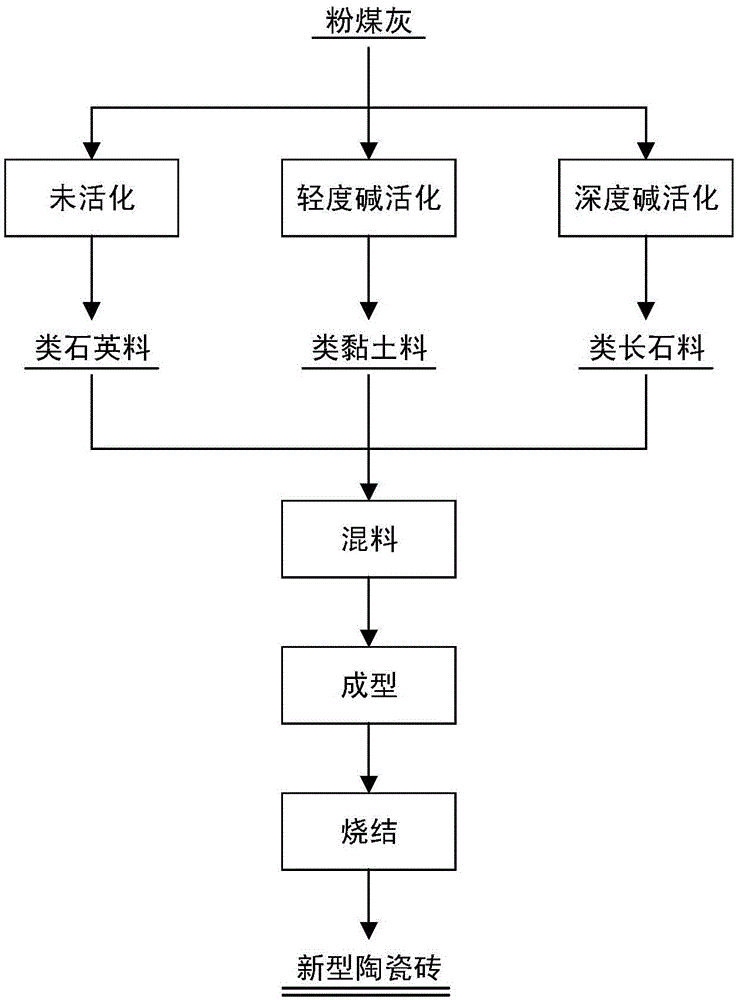
本发明涉及固体废物综合利用和陶瓷材料生产领域,具体涉及一种工业固体废弃物的利用方法,尤其涉及一种仅利用粉煤灰作为原料制备陶瓷砖的方法。
背景技术:
:粉煤灰是燃煤电厂在生产过程中产生的固体废弃物。由于我国目前仍以火力发电为主,粉煤灰排放居高不下,且由于产生量大、产地集中且有效利用不足,粉煤灰大量堆存,目前累计堆存量已近30亿吨,粉煤灰已成为我国最大单一固体污染源。粉煤灰的处置越来越受到整个社会的关注。近年来,随着城镇化的进一步推动,我国房地产行业迅猛发展,与此相关联的陶瓷砖生产行业也发生着日新月异的变化。然而随着陶瓷砖产量的大幅增长,其主要生产原料粘土、长石和石英也日益匮乏。陶瓷砖生产行业原料供需矛盾日益突出。针对粉煤灰利用附加值低,陶瓷砖生产原料资源紧缺的问题,众多科研工作者与陶瓷生产厂家进行了积极的研究,成功地将粉煤灰资源利用到了陶瓷砖生产过程当中,实现了粉煤灰的高附加值资源化利用。例如cn103922699a公开了一种粉煤灰制备日用陶瓷的方法,利用固体废弃物粉煤灰以及粘土、长石为原料,制备陶瓷坯体,粉煤灰掺入量为10-60%。cn103951388a公开了一种粉煤灰质陶瓷酒瓶及其制备方法,其粉煤灰掺量为45-65wt%。cn103833330a公开了一种高铝粉煤灰制备瓷质砖的方法,通过配料、球磨、出浆与干燥、造粒、陈腐、成型、干燥、烧结等步骤制得了符合国家标准的瓷质砖,所得瓷质砖中粉煤灰掺量量达到30-75%。cn103833331a公开了一种利用高铝粉煤灰制备陶质砖的方法,其粉煤灰产量可达到60-70%,烧成周期为3-5h。现有方法均是将粉煤灰与其他原料简单物理混合,粉煤灰未经化学活化处理。而未经活化的粉煤灰可塑性低、熔点高,仅仅只能取代陶瓷原料中的石英组分起到降低陶瓷烧成过程收缩的作用。粉煤灰难以取代陶瓷原料中的黏土和长石组分,导致粉煤灰制备陶瓷时添加量有限,限制了粉煤灰在陶瓷砖生产中的大量应用。技术实现要素:鉴于现有技术中存在的问题,本发明的目的在于提供一种仅利用粉煤灰作为原料制备陶瓷砖的方法,通过化学改性将粉煤灰活化成“类黏土料”和“类长石料”分别取代传统陶瓷中的黏土和长石矿物的作用,仅利用粉煤灰为原料即对传统陶瓷原料进行了100%的替代,实现了粉煤灰的高附加值利用,缓解了陶瓷生产原料日益紧缺的现状。为达此目的,本发明采用以下技术方案:本发明提供了一种仅利用粉煤灰作为原料制备陶瓷砖的方法,所述方法包括以下步骤:(1)将浓度为60-100g/l的碱液与粉煤灰混合,加热至80-150℃进行轻度碱性活化反应,得到类黏土料;(2)将浓度为105-500g/l的碱液与粉煤灰混合,加热至120-200℃进行深度碱性活化反应,得到类长石料;(3)将粉煤灰与步骤(1)所得类黏土料和步骤(2)所得类长石料进行机械混合,得到固态混合料;(4)将步骤(3)所得固态混合料进行压力成型,得到生坯;(5)将步骤(4)所得生坯进行烧结,烧结完成后得到陶瓷砖产品。本发明通过对粉煤灰进行轻度碱性活化改性,得到了类黏土料。改性后的“类黏土料”表面存在丰富的结晶水和羟基结构,导致颗粒之间存在氢键作用,使其作为陶瓷原料时起到类似黏土矿物的粘接剂作用。克服了粉煤灰作为瘠性料不利陶瓷成型的难题,其生坯强度完全达到工厂生产的要求。得到的“类黏土料”的化学成分更加接近莫来石的化学成分,同时其具备非常高的反应活性。低温烧结过程中在新型陶瓷体内可以生成比传统陶瓷更多的针状莫来石,这些针状莫来石可以显著提高陶瓷的力学性能。本发明对粉煤灰进行深度碱性活化改性后,得到了类长石料。改性后的“类长石料”结构中存在丰富的碱金属元素,可以起到类似长石的助熔剂作用。本发明将制备的“类黏土料”和“类长石料”和未活化的粉煤灰(“类石英料”)复配,可同时起到黏土(增塑剂、析出莫来石)、石英(降低收缩的填充剂)和长石(助熔剂)的作用,进而实现了仅使用粉煤灰作为原料制备陶瓷砖,其对传统陶瓷原料的替代量可以达到100%。对于本发明而言,步骤(1)和步骤(2)无先后顺序之分,本发明同样可以先进行步骤(2)中制备类长石料的步骤,再制备步骤(1)所述类黏土料,或者二者同时进行,其不应作为对本发明的限制。根据本发明,步骤(1)所述轻度碱性活化反应中碱液的浓度为60-100g/l,例如可以是60g/l、65g/l、70g/l、75g/l、80g/l、85g/l、90g/l、95g/l或100g/l,以及上述数值之间的具体点值,限于篇幅及出于简明的考虑,本发明不再穷尽列举。根据本发明,步骤(1)所述轻度碱性活化反应中反应的温度为80-150℃,例如可以是80℃、90℃、100℃、110℃、120℃、130℃、140℃或150℃,以及上述数值之间的具体点值,限于篇幅及出于简明的考虑,本发明不再穷尽列举。根据本发明,步骤(2)所述深度碱性活化反应中碱液的浓度为105-500g/l,例如可以是105g/l、150g/l、200g/l、250g/l、300g/l、350g/l、400g/l、450g/l或500g/l,以及上述数值之间的具体点值,限于篇幅及出于简明的考虑,本发明不再穷尽列举。根据本发明,步骤(2)所述深度碱性活化反应中反应的温度为120-200℃,例如可以是120℃、130℃、140℃、150℃、160℃、170℃、180℃、190℃或200℃,以及上述数值之间的具体点值,限于篇幅及出于简明的考虑,本发明不再穷尽列举。根据本发明,步骤(1)和步骤(2)所述碱液为氢氧化钠溶液和/或氢氧化钾溶液。根据本发明,步骤(1)所述碱液与粉煤灰的液固比为(2-10):1,例如可以是2:1、3:1、4:1、5:1、6:1、7:1、8:1、9:1或10:1,以及上述数值之间的具体点值,限于篇幅及出于简明的考虑,本发明不再穷尽列举。根据本发明,步骤(1)所述轻度碱性活化反应的时间为0.5-20h,例如可以是0.5h、1h、3h、5h、8h、10h、13h、15h、18h或20h,以及上述数值之间的具体点值,限于篇幅及出于简明的考虑,本发明不再穷尽列举。根据本发明,当步骤(1)中碱液的浓度≥80g/l时,所述轻度碱性活化反应的温度为≤120℃。根据本发明,当步骤(1)中碱液的浓度<80g/l时,所述轻度碱性活化反应的温度为>120℃。根据本发明,步骤(2)所述碱液与粉煤灰的液固比为(2-10):1,例如可以是2:1、3:1、4:1、5:1、6:1、7:1、8:1、9:1或10:1,以及上述数值之间的具体点值,限于篇幅及出于简明的考虑,本发明不再穷尽列举。本发明所述液固比的单位均为ml/g。根据本发明,步骤(2)所述轻度碱性活化反应的时间为0.5-20h,例如可以是0.5h、1h、3h、5h、8h、10h、13h、15h、18h或20h,以及上述数值之间的具体点值,限于篇幅及出于简明的考虑,本发明不再穷尽列举。根据本发明,当步骤(2)中碱液的浓度≥300g/l时,所述重度碱性活化反应的温度为≤160℃。根据本发明,当步骤(2)中碱液的浓度<300g/l时,所述重度碱性活化反应的温度为>160℃。根据本发明,按质量百分含量计,步骤(3)所述固态混合料包括以下组分:类黏土料40-60%,类长石料15-35%,粉煤灰10-30%。根据本发明,按质量百分含量计,所述固态混合料中类黏土料的含量为40-60%,例如可以是40%、43%、45%、48%、50%、52%、55%、58%或60%,以及上述数值之间的具体点值,限于篇幅及出于简明的考虑,本发明不再穷尽列举。根据本发明,按质量百分含量计,所述固态混合料中类长石料的含量为15-35%,例如可以是15%、18%、20%、23%、25%、28%、30%、33%或35%,以及上述数值之间的具体点值,限于篇幅及出于简明的考虑,本发明不再穷尽列举。根据本发明,按质量百分含量计,所述固态混合料中粉煤灰的含量为10-30%,例如可以是10%、13%、15%、18%、20%、23%、25%、27%或30%,以及上述数值之间的具体点值,限于篇幅及出于简明的考虑,本发明不再穷尽列举。上述固态混合料中的粉煤灰为未经过改性的粉煤灰,即原始粉煤灰。根据本发明,步骤(3)所述机械混合的方式为球磨,球磨后所得固态混合料的粒径为-250目。根据本发明,步骤(4)所述成型的压力为20-100mpa,例如可以是20mpa、30mpa、40mpa、50mpa、60mpa、70mpa、80mpa、90mpa或100mpa,以及上述数值之间的具体点值,限于篇幅及出于简明的考虑,本发明不再穷尽列举。根据本发明,步骤(5)所述烧结的温度为1000-1300℃,例如可以是1000℃、1050℃、1100℃、1150℃、1200℃、1250℃或1300℃,以及上述数值之间的具体点值,限于篇幅及出于简明的考虑,本发明不再穷尽列举。根据本发明,步骤(5)所述烧结的时间为0.2-3h,例如可以是0.2h、0.5h、1h、1.5h、2h、2.5h或3h,以及上述数值之间的具体点值,限于篇幅及出于简明的考虑,本发明不再穷尽列举。作为优选的技术方案,本发明所述仅利用粉煤灰作为原料制备陶瓷砖的方法包括以下步骤:(1)按照(2-10):1的液固比将浓度为60-100g/l的碱液与粉煤灰混合,加热至80-150℃进行轻度碱性活化反应0.5-20h,得到类黏土料;所述碱液为氢氧化钠溶液和/或氢氧化钾溶液;当碱液的浓度≥80g/l时,所述轻度碱性活化反应的温度为≤120℃,当碱液的浓度<80g/l时,所述轻度碱性活化反应的温度为>120℃;(2)按照(2-10):1的液固比将浓度为105-500g/l的碱液与粉煤灰混合,加热至120-200℃进行深度碱性活化反应0.5-20h,得到类长石料;所述碱液为氢氧化钠溶液和/或氢氧化钾溶液;当碱液的浓度≥300g/l时,所述重度碱性活化反应的温度为≤160℃;当碱液的浓度<300g/l时,所述重度碱性活化反应的温度为>160℃;(3)按质量百分含量计,将10-30%粉煤灰与40-60%类黏土料和15-35%类长石料混合后球磨,得到粒径为-250目的固态混合料;(4)将步骤(3)所得固态混合料在20-100mpa下进行压力成型,得到生坯;(5)将步骤(4)所得生坯在1000-1300℃下烧结0.2-3h,烧结完成后得到陶瓷砖产品。与现有技术方案相比,本发明至少具有以下有益效果:(1)本发明通过化学改性将粉煤灰活化成“类黏土料”和“类长石料”分别取代传统陶瓷中的黏土和长石矿物的作用,并通过后续对原料成分的复配,仅利用粉煤灰为原料即对传统陶瓷原料进行了100%的替代,实现了对粉煤灰高附加值利用,同时缓解陶瓷生产原料日益紧缺的现状。(2)本发明制备所得的陶瓷砖内部具备丰富的针状莫来石结构,其容重低,断裂模数远大于国标规定,综合性能优异,较当前市场同类产品具有更大优势。附图说明图1是本发明一种具体实施方式提供的工艺流程图。下面对本发明进一步详细说明。但下述的实例仅仅是本发明的简易例子,并不代表或限制本发明的权利保护范围,本发明的保护范围以权利要求书为准。具体实施方式下面结合附图并通过具体实施方式来进一步说明本发明的技术方案。本发明在具体实施方式部分提供了一种仅利用粉煤灰作为原料制备陶瓷砖的方法,如图1所示,所述方法可以为:将浓度为60-100g/l的碱液与粉煤灰混合,加热至80-150℃进行轻度碱性活化反应,得到类黏土料;将浓度为105-500g/l的碱液与粉煤灰混合,加热至120-200℃进行深度碱性活化反应,得到类长石料;将未活化的粉煤灰(类石英料)与类黏土料和类长石料进行机械混合,得到固态混合料;对所得固态混合料进行压力成型,得到生坯;将生坯进行烧结,烧结完成后得到陶瓷砖产品。为更好地说明本发明,便于理解本发明的技术方案,本发明的典型但非限制性的实施例如下:实施例1本实例采用内蒙古自治区锡林郭勒盟某电厂粉煤灰为原料,按照以下方法制备陶瓷砖。(1)按照10:1的液固比将浓度为60g/l的naoh溶液与粉煤灰混合,加热至150℃进行轻度碱性活化反应20h,得到类黏土料;(2)按照10:1的液固比将浓度为105g/l的naoh溶液与粉煤灰混合,加热至200℃进行深度碱性活化反应20h,得到类长石料;(3)按质量百分含量计,将25%粉煤灰与50%类黏土料和25%类长石料混合后球磨,得到粒径为-250目的固态混合料;(4)将步骤(3)所得固态混合料进行压力成型,得到坯体强度为2.50mpa的生坯;(5)将步骤(4)所得生坯在1050℃下烧结3h,烧结完成后得到陶瓷砖产品。实施例2本实例采用天津某电厂粉煤灰为原料,按照以下方法制备陶瓷砖。(1)按照5:1的液固比将浓度为100g/l的naoh溶液与粉煤灰混合,加热至80℃进行轻度碱性活化反应10h,得到类黏土料;(2)按照5:1的液固比将浓度为500g/l的naoh溶液与粉煤灰混合,加热至120℃进行深度碱性活化反应10h,得到类长石料;(3)按质量百分含量计,将10%粉煤灰与60%类黏土料和30%类长石料混合后球磨,得到粒径为-250目的固态混合料;(4)将步骤(3)所得固态混合料进行压力成型,得到坯体强度为4.55mpa的生坯;(5)将步骤(4)所得生坯在1250℃下烧结1.5h,烧结完成后得到陶瓷砖产品。实施例3本实例采用内蒙古自治区呼伦贝尔市某电厂粉煤灰为原料,按照以下方法制备陶瓷砖。(1)按照10:1的液固比将浓度为100g/l的naoh溶液与粉煤灰混合,加热至90℃进行轻度碱性活化反应0.5h,得到类黏土料;(2)按照4:1的液固比将浓度为200g/l的naoh溶液与粉煤灰混合,加热至200℃进行深度碱性活化反应0.5h,得到类长石料;(3)按质量百分含量计,将30%粉煤灰与40%类黏土料和30%类长石料混合后球磨,得到粒径为-250目的固态混合料;(4)将步骤(3)所得固态混合料进行压力成型,得到坯体强度为4.55mpa的生坯;(5)将步骤(4)所得生坯在1150℃下烧结2.5h,烧结完成后得到陶瓷砖产品。实施例4本实例采用内蒙古自治区锡林郭勒盟某电厂粉煤灰为原料,按照以下方法制备陶瓷砖。(1)按照2:1的液固比将浓度为100g/l的naoh溶液与粉煤灰混合,加热至110℃进行轻度碱性活化反应20h,得到类黏土料;(2)按照5:1的液固比将浓度为150g/l的naoh溶液与粉煤灰混合,加热至200℃进行深度碱性活化反应10h,得到类长石料;(3)按质量百分含量计,将30%粉煤灰与55%类黏土料和15%类长石料混合后球磨,得到粒径为-250目的固态混合料;(4)将步骤(3)所得固态混合料进行压力成型,得到坯体强度为2.40mpa的生坯;(5)将步骤(4)所得生坯在1200℃下烧结1h,烧结完成后得到陶瓷砖产品。实施例5本实例采用陕西省西安市某电厂粉煤灰为原料,按照以下方法制备陶瓷砖。(1)按照10:1的液固比将浓度为90g/l的naoh溶液与粉煤灰混合,加热至110℃进行轻度碱性活化反应2h,得到类黏土料;(2)按照4:1的液固比将浓度为120g/l的naoh溶液与粉煤灰混合,加热至190℃进行深度碱性活化反应6h,得到类长石料;(3)按质量百分含量计,将10%粉煤灰与55%类黏土料和35%类长石料混合后球磨,得到粒径为-250目的固态混合料;(4)将步骤(3)所得固态混合料进行压力成型,得到坯体强度为5.72mpa的生坯;(5)将步骤(4)所得生坯在1300℃下烧结0.5h,烧结完成后得到陶瓷砖产品。实施例6本实例采用内蒙古自治区锡林郭勒盟某电厂粉煤灰为原料,按照以下方法制备陶瓷砖。(1)按照6:1的液固比将浓度为80g/l的naoh溶液与粉煤灰混合,加热至120℃进行轻度碱性活化反应15h,得到类黏土料;(2)按照7:1的液固比将浓度为300g/l的naoh溶液与粉煤灰混合,加热至160℃进行深度碱性活化反应7h,得到类长石料;(3)按质量百分含量计,将25%粉煤灰与40%类黏土料和35%类长石料混合后球磨,得到粒径为-250目的固态混合料;(4)将步骤(3)所得固态混合料进行压力成型,得到坯体强度为4.00mpa的生坯;(5)将步骤(4)所得生坯在1000℃下烧结2h,烧结完成后得到陶瓷砖产品。实施例7本实例采用内蒙古自治区锡林郭勒盟某电厂粉煤灰为原料,按照以下方法制备陶瓷砖。(1)按照2:1的液固比将浓度为60g/l的naoh溶液与粉煤灰混合,加热至150℃进行轻度碱性活化反应20h,得到类黏土料;(2)按照5:1的液固比将浓度为400g/l的naoh溶液与粉煤灰混合,加热至150℃进行深度碱性活化反应10h,得到类长石料;(3)按质量百分含量计,将20%粉煤灰与50%类黏土料和30%类长石料混合后球磨,得到粒径为-250目的固态混合料;(4)将步骤(3)所得固态混合料进行压力成型,得到坯体强度为3.88mpa的生坯;(5)将步骤(4)所得生坯在1100℃下烧结3h,烧结完成后得到陶瓷砖产品。对各实施例和对比例所得产品进行性能测试,容重和断裂模数的测试标准分别为gb/t3810.3和gb/t3810.4,所得结果如表1所示。表1容重断裂模数实施例12.4445.4实施例22.5850.3实施例32.5148.7实施例42.4243.1实施例52.5544.8实施例62.3239.8实施例72.4042.4以上详细描述了本发明的优选实施方式,但是,本发明并不限于上述实施方式中的具体细节,在本发明的技术构思范围内,可以对本发明的技术方案进行多种简单变型,这些简单变型均属于本发明的保护范围。另外需要说明的是,在上述具体实施方式中所描述的各个具体技术特征,在不矛盾的情况下,可以通过任何合适的方式进行组合,为了避免不必要的重复,本发明对各种可能的组合方式不再另行说明。此外,本发明的各种不同的实施方式之间也可以进行任意组合,只要其不违背本发明的思想,其同样应当视为本发明所公开的内容。当前第1页1 2 3