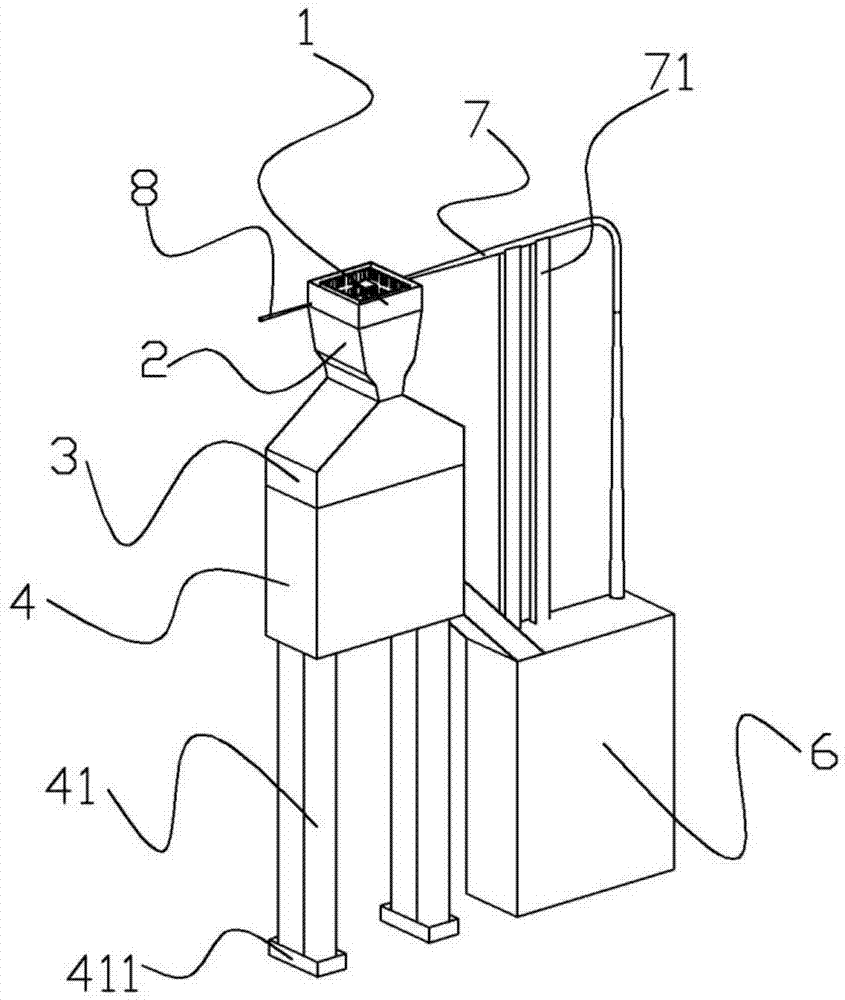
本发明涉及工业生产
技术领域:
,更具体地说,它涉及一种活性炭的生产设备及方法。
背景技术:
:中国是世界上最大的活性炭出产国和出口国,最近几年,活性炭应用市场不断扩大,其中煤基活性炭产业迎来了一个新的发展时期。煤基活性炭主要分为原煤直接破碎活性炭、柱状成型活性炭以及压块破碎活性碳三种,这三种类型的活性炭生产都需要对煤炭进行粉碎或磨粉,粉碎或磨粉的质量直接影响到最后产品的优劣。常用设备对煤炭的破碎和磨粉效率不高,设备上经常残留有碎渣,对原料产生浪费,活性炭生产过程中能源的利用率较低。技术实现要素:针对现有技术存在的不足,本发明的目的在于提供一种活性炭的生产设备及方法,其具有的特点:可以对煤炭进行预热,提高破碎和磨粉的效率以及质量;对碎渣充分利用;充分利用活化时产生的蒸汽来减耗。一种活性炭的生产设备及方法,生产设备包括预热部、碾碎部、中转部、碳化部、碳化部支撑柱、传送部、活化部、导气管以及出气管;碳化部支撑柱的底部接地,碳化部支撑柱的顶部与碳化部的底部固定连接,碳化部的顶部与中转部的底部固定连接,中转部的顶部与碾碎部的底部固定连接,碾碎部的顶部与预热部的底部固定连接,传送部的一端与碳化部的侧面固定连接,传送部的另一端与活化部的顶部固定连接,活化部的顶部还与导气管固定连接,导气管还与预热部靠近传送部的侧面固定连接,活化部的底部接地,出气管与预热部固定连接,出气管设置在预热部远离传送部的侧面上。生产方法包括:s1、保证升降台顶面与加热板顶面持平,将原料倒入预热部,通过推动板和升降台上的加热片、加热板以及储气层来对原料进行预热;s2、预热完成后,第二液压杆缩短,升降台因此升高,升降台升至一定高度后,第一液压杆开始伸长,推动板因此向升降槽的方向运动,并将预热好的原料推入升降台内,当推动板推动到刚好与升降台接触的位置时,第二液压杆开始伸长,升降台因此下降,当升降台下降到其顶部与加热板顶部持平的位置,第一液压杆开始缩短,推动板退回初始位置,原料顺着升降台进入碾碎部进行破碎、磨粉;s3、将碾碎好的原料通过所述中转部倒入所述碳化部进行碳化;s4、将碳化好的原料通过所述传送部送入所述活化部进行蒸汽活化;s5、活化部产生的蒸汽通过导气管进入到储气层,当这部分蒸汽温度降低到一定程度后,通过出气管将蒸汽排出。通过采用上述技术方案,在实现活性炭的碳化和活化功能的前提下,增加了预热部、导气管以及出气管,预热部可以实现对煤炭原料的预热,促进其破碎磨粉的效率和质量,同时预热部还可以实现对一些残留的碎渣原料的充分清理和利用,导气管和出气管则可以实现对蒸汽的循环利用,总的来说,体现了装置可以对煤炭进行预热;对碎屑充分利用;充分利用活化时产生的蒸汽来减耗的特点。进一步地,预热部包括预热部外壳、推动板、第一液压杆、加热板、加热片、升降槽、升降台、以及第二液压杆;预热部外壳是上下贯通的,第一液压杆的一端与预热部外壳的内侧壁固定连接,推动板与第一液压杆的另一端固定连接,推动板上固定设有两根第一液压杆,预热部外壳内共设有四块推动板,这四块推动板分别设置在预热部外壳的四个内侧壁上,加热板的顶部与预热部外壳的底部固定连接,推动板的底面与加热板的顶面接触,第二液压杆的一端与加热板的底部固定连接,第二液压杆另一端与升降台的底板固定连接,升降槽固定设于加热板上且贯通,升降台穿过升降槽与加热板活动连接,升降台的顶部以及推动板远离第一液压杆的一面上都固定设有加热片。通过采用上述技术方案,推动板底面与加热板顶面接触,保证了可以将一些细小的碎屑通过推动输送到升降台中,实现了对碎屑原料的充分利用,预热部上设置的加热片可以保证预热部的预热效果,升降台则是丰富了原料的传送方式,液压杆实现推动板的推动与升降台的升降运动。进一步地,碾碎部包括碾碎部外壳、第一碾碎轮、第二碾碎轮、第三碾碎轮以及第四碾碎轮;第一碾碎轮与第二碾碎轮啮合连接,第三碾碎轮与第四碾碎轮啮合连接,第一碾碎轮与第二碾碎轮固定设于碾碎部外壳内部上端,第三碾碎轮与第四碾碎轮固定设于碾碎部外壳内部下端,碾碎部外壳的形状尽可能地贴合这两组啮合的碾碎轮,碾碎轮外壳上下贯通。通过采用上述技术方案,可以实现对原料的破碎和磨粉,且两组碾碎轮的设计可以使得破碎和磨粉更加充分。进一步地,加热板内部固定设有储气层,导气管和出气管接入储气层,导气管和出气管内设有阀门。通过采用上述技术方案,活化部的蒸汽可以传输到加热板内部的储气层,实现了对蒸汽热能的充分利用,加热板采用电加热和蒸汽热传导互相配合的方式对原料进行预热。进一步地,导气管上设有固定架,固定架顶部与导气管固定连接,固定架底部与活化部顶部固定连接。通过采用上述技术方案,固定架对导气管起支撑稳固的作用,保证蒸汽传输的安全进行,且不占用多余的空间。进一步地,碳化部支撑柱底部固定设有加强底座。通过采用上述技术方案,碳化部支撑柱对碳化部加强稳固,加强底座对碳化部支撑柱进行加强稳固,最终碳化部设置得更加稳固。进一步地,传送部内壁上涂覆有一层耐热层,耐热层的制备方法是:取以下以重量计各组分原料备用:纯丙乳液10-11.5份、聚异丁烯12.3-13.9份、硅灰石6.2-6.4份、去离子水10-20份、钛白粉13.7-14.2份、云母粉12-13份、三飞粉20-30份、乙炔二醇4-8份、玻璃微珠15-20份、亚硝酸钙1.1-1.3份。s1、预制有机溶剂:将纯丙乳液、聚异丁烯、去离子水、乙炔二醇、玻璃微珠混合后加热至58-60℃,搅拌均匀后,保温3-6h;s2、制备耐热涂料:将硅灰石、三飞粉、亚硝酸钙、钛白粉、云母粉依次加入到s1中的有机溶剂中,搅拌均匀后,将温度加热至68-72℃后保温1-2h;s3、处理:将s2制得的耐热涂料进行超声波处理0.5-1h,然后降温至40-50℃,于1000-1200r/min转速搅拌0.5h,然后冷却至室温;s4、涂覆:将s3得到的耐热涂料用静电涂覆的方法均匀涂覆在传送部的内壁表面;s5、干燥:将s4得到的传送部放置到阴凉通风处进行吹干5-6h。通过采用上述技术方案,传送部输送的原料带有极高的温度,耐热层可以保护传送部不被高温影响而导致融化变形或者损耗,保证了它的正常使用,并延长其使用寿命。附图说明图1为本发明提供的一种实施方式的总体结构正三轴侧视图;图2为本发明提供的一种实施方式的预热部俯视图;图3为本发明提供的一种实施方式的预热部正三轴侧视图;图4为本发明提供的一种实施方式的碾碎部剖视图;图5为本发明提供的一种实施方式的碳化部、活化部、中转部以及传送部连接结构示意图;图6为本发明提供的一种实施方式的加热板剖视图;图7为本发明提供的一种实施方式的升降台正三轴侧视图;图中:1、预热部;11、预热部外壳;12、推动板;13、第一液压杆;14、加热板;141、储气层;15、加热片;16、升降槽;17、升降台;18、第二液压杆;2、碾碎部;21、碾碎部外壳;22、第一碾碎轮;23、第二碾碎轮;24、第三碾碎轮;25、第四碾碎轮;3、中转部;4、碳化部;41、碳化部支撑柱;411、加强底座;5、传送部;6、活化部;7、导气管;71、固定架;8、出气管。具体实施方式实施例1:以下结合附图1-7对本发明作进一步详细说明。一种活性炭的生产设备及方法,如图1-7所示,一种活性炭的生产设备,包括预热部1、碾碎部2、中转部3、碳化部4、碳化部支撑柱41、传送部5、活化部6、导气管7以及出气管8;碳化部支撑柱41的底部接地,碳化部支撑柱41的顶部与碳化部4的底部固定连接,碳化部4的顶部与中转部3的底部固定连接,中转部3的顶部与碾碎部2的底部固定连接,碾碎部2的顶部与预热部1的底部固定连接,传送部5的一端与碳化部4的侧面固定连接,传送部5的另一端与活化部6的顶部固定连接,活化部6的顶部还与导气管7固定连接,导气管7还与预热部1靠近传送部5的侧面固定连接,活化部6的底部接地,出气管8与预热部1固定连接,出气管8设置在预热部1远离传送部5的侧面上;预热部1包括预热部外壳11、推动板12、第一液压杆13、加热板14、加热片15、升降槽16、升降台17、以及第二液压杆18;预热部外壳11是上下贯通的,第一液压杆13的一端与预热部外壳11的内侧壁固定连接,推动板12与第一液压杆13的另一端固定连接,推动板12上固定设有两根第一液压杆13,预热部外壳11内共设有四块推动板12,这四块推动板12分别设置在预热部外壳11的四个内侧壁上,加热板14的顶部与预热部外壳11的底部固定连接,推动板12的底面与加热板14的顶面接触,第二液压杆18的一端与加热板14的底部固定连接,第二液压杆18另一端与升降台17的底板固定连接,升降槽16固定设于加热板14上且贯通,升降台17穿过升降槽16与加热板14活动连接,升降台17的顶部以及推动板12远离第一液压杆13的一面上都固定设有加热片15。碾碎部2包括碾碎部外壳21、第一碾碎轮22、第二碾碎轮23、第三碾碎轮24以及第四碾碎轮25;第一碾碎轮22与第二碾碎轮23啮合连接,第三碾碎轮24与第四碾碎轮25啮合连接,第一碾碎轮22与第二碾碎轮23固定设于碾碎部外壳21内部上端,第三碾碎轮24与第四碾碎轮25固定设于碾碎部外壳21内部下端,碾碎部外壳21的形状尽可能地贴合这两组啮合的碾碎轮,碾碎部外壳21上下贯通。加热板14内部固定设有储气层141,导气管7和出气管8接入储气层141。导气管7上设有固定架71,固定架71顶部与导气管7固定连接,固定架71底部与活化部6顶部固定连接。碳化部支撑柱41底部固定设有加强底座411。一种活性炭的生产方法:s1、保证升降台17顶面与加热板14顶面持平,将原料倒入预热部1,通过推动板12和升降台17上的加热片15、加热板14以及储气层141来对原料进行预热;s2、预热完成后,第二液压杆18缩短,升降台17因此升高,升降台17升至一定高度后,第一液压杆13开始伸长,推动板12因此向升降槽16的方向运动,并将预热好的原料推入升降台17内,当推动板12推动到刚好与升降台17接触的位置时,第二液压杆18开始伸长,升降台17因此下降,当升降台17下降到其顶部与加热板14顶部持平的位置,第一液压杆13开始缩短,推动板12退回初始位置,原料顺着升降台17进入碾碎部2进行破碎、磨粉;s3、将碾碎好的原料通过所述中转部3倒入所述碳化部4进行碳化;s4、将碳化好的原料通过所述传送部5送入所述活化部6进行蒸汽活化;s5、活化部6产生的蒸汽通过导气管7进入到储气层141,当这部分蒸汽温度降低到一定程度后,通过出气管8将蒸汽排出。本实施例中,装置满足了活性炭的碳化和活化功能的前提下,增加了预热部1、导气管7以及出气管8,预热部1可以实现对煤炭原料的预热,促进其破碎磨粉的效率和质量,同时预热部1还可以实现对一些残留的碎渣原料的充分清理和利用,导气管7和出气管8则可以实现对蒸汽的循环利用。实施例2与实施例1的不同之处在于,传送部5的内壁上涂覆有一层耐热层,耐热层的制备方法是:取以下以重量计各组分原料备用:纯丙乳液10份、聚异丁烯12.3份、硅灰石6.2份、去离子水10份、钛白粉13.7份、云母粉12份、三飞粉20份、乙炔二醇4份、玻璃微珠15份、亚硝酸钙1.1份。s1、预制有机溶剂:将纯丙乳液、聚异丁烯、去离子水、乙炔二醇、玻璃微珠混合后加热至58℃,搅拌均匀后,保温5.5h;s2、制备耐热涂料:将硅灰石、三飞粉、亚硝酸钙、钛白粉、云母粉依次加入到s1中的有机溶剂中,搅拌均匀后,将温度加热至72℃后保温2h;s3、处理:将s2制得的耐热涂料进行超声波处理1h,然后降温至50℃,于1200r/min转速搅拌0.5h,然后冷却至室温;s4、涂覆:将s3得到的耐热涂料用静电涂覆的方法均匀涂覆在传送部的内壁表面;s5、干燥:将s4得到的传送部放置到阴凉通风处进行吹干6h。本实施例中,通过在传送部5的内侧壁上涂覆一层耐热层,因为传送部5输送的原料带有极高的温度,耐热层可以保护传送部5不被高温影响而导致融化变形或者损耗,保证了它的正常使用,并延长其使用寿命。实施例3与实施例2的不同之处在于,对于耐热层的配方比重进行了修改:取以下以重量计各组分原料备用:纯丙乳液11.5份、聚异丁烯13.9份、硅灰石6.4份、去离子水20份、钛白粉14.2份、云母粉13份、三飞粉30份、乙炔二醇8份、玻璃微珠20份、亚硝酸钙1.3份。s1、预制有机溶剂:将纯丙乳液、聚异丁烯、去离子水、乙炔二醇、玻璃微珠混合后加热至58℃,搅拌均匀后,保温5.5h;s2、制备耐热涂料:将硅灰石、三飞粉、亚硝酸钙、钛白粉、云母粉依次加入到s1中的有机溶剂中,搅拌均匀后,将温度加热至72℃后保温2h;s3、处理:将s2制得的耐热涂料进行超声波处理1h,然后降温至50℃,于1200r/min转速搅拌0.5h,然后冷却至室温;s4、涂覆:将s3得到的耐热涂料用静电涂覆的方法均匀涂覆在传送部的内壁表面;s5、干燥:将s4得到的传送部放置到阴凉通风处进行吹干6h。本实施例中,通过对耐热层配方比重进行修改,对比后得出最佳配方。实施例4与实施例2的不同之处在于,对于耐热层的配方比重进行了修改:取以下以重量计各组分原料备用:纯丙乳液10.7份、聚异丁烯12.6份、硅灰石6.3份、去离子水15份、钛白粉14份、云母粉12.5份、三飞粉25份、乙炔二醇6份、玻璃微珠17.5份、亚硝酸钙1.2份。s1、预制有机溶剂:将纯丙乳液、聚异丁烯、去离子水、乙炔二醇、玻璃微珠混合后加热至58℃,搅拌均匀后,保温5.5h;s2、制备耐热涂料:将硅灰石、三飞粉、亚硝酸钙、钛白粉、云母粉依次加入到s1中的有机溶剂中,搅拌均匀后,将温度加热至72℃后保温2h;s3、处理:将s2制得的耐热涂料进行超声波处理1h,然后降温至50℃,于1200r/min转速搅拌0.5h,然后冷却至室温;s4、涂覆:将s3得到的耐热涂料用静电涂覆的方法均匀涂覆在传送部的内壁表面;s5、干燥:将s4得到的传送部放置到阴凉通风处进行吹干6h。本实施例中,通过对耐热层配方比重进行修改,对比后得出最佳配方。对实施例1、2、3、4中涂覆有不同配方比重的耐热涂料的传送部5进行耐热强度和剥离强度的测试,为了便于比较,所有实施例的数据基于实施例1的数据进行归一化。表1耐热强度剥离强度实施例1100%100%实施例2162%131%实施例3169%133%实施例4176%134%从表中数据可以看出,涂覆耐热材料后,传送部5的耐热强度有了明显的增强,而实施例4明显效果最佳,所以确定的最优原料配方是:纯丙乳液10.7份、聚异丁烯12.6份、硅灰石6.3份、去离子水15份、钛白粉14份、云母粉12.5份、三飞粉25份、乙炔二醇6份、玻璃微珠17.5份、亚硝酸钙1.2份。工作原理:从预热部1顶部开口倒入煤炭原料,此时升降台17顶面是与加热板14的顶面在同一平面上的,通过推动板12上的加热片15、升降台17上的加热片15、加热板14以及储气层141来对煤炭原料进行预热,预热完成后,第二液压杆18缩短,升降台17穿过升降槽16升高,同时,第一液压杆13伸长,推动板12向升降槽16的方向将预热好的煤炭原料推入升降台17内,升降台17上设有挡板,煤炭原料不会掉落到升降台17的底板上,推动板12推到与升降台17接触后,第二液压杆18伸长,升降台17下降至顶部与加热板14持平,第一液压杆13缩短,推动板12退回初始位置,由于升降台17是上下贯通的结构,煤炭原料顺着升降台17进入碾碎部2,在共计两组的啮合碾碎轮先后进行破碎、磨粉后,煤炭粉末从碾碎部2掉落到中转部3,中转部3是上部开口大,下部开口小的倒梯形结构,煤炭粉末进入碳化部4,完成碳化后,经过传送部5输送到活化部6中,活化部6采用的是蒸汽活化的方法,活化部6产生的蒸汽通过导气管7进入到储气层141,当这部分蒸汽降到一定温度后,通过出气管8将蒸汽排出。综上所述,本发明具有以下有益效果:1、对煤炭原料进行预热,有效促进了煤炭原料的粉碎、磨粉以及得到的煤炭粉末的质量;2、设置两组啮合的碾碎轮,破碎、磨粉更加充分;3、充分利用蒸汽的热能来对煤炭原料进行预热,体现了循环利用的环保思想;4、预热部的推动板12抵在加热板14上,可以有效将煤炭原料细小的碎渣推入升降台17,充分利用了煤炭原料的碎屑;5、采用升降台17升降的设计,丰富了煤炭原料的传送方式,同时保证了整体结构的封闭状态,有助于提高碳化过程与活化过程的质量和效率。需要说明的是,本发明实施例中所有使用“第一”和“第二”的表述均是为了区分两个相同名称非相同的实体或者非相同的参量,可见“第一”“第二”仅为了表述的方便,不应理解为对本发明实施例的限定,后续实施例对此不再一一说明。本具体实施例仅仅是对本发明的解释,其并不是对本发明的限制,本领域技术人员在阅读完本说明书后可以根据需要对本实施例做出没有创造性贡献的修改,但只要在本发明的权利要求范围内都受到专利法的保护。当前第1页12