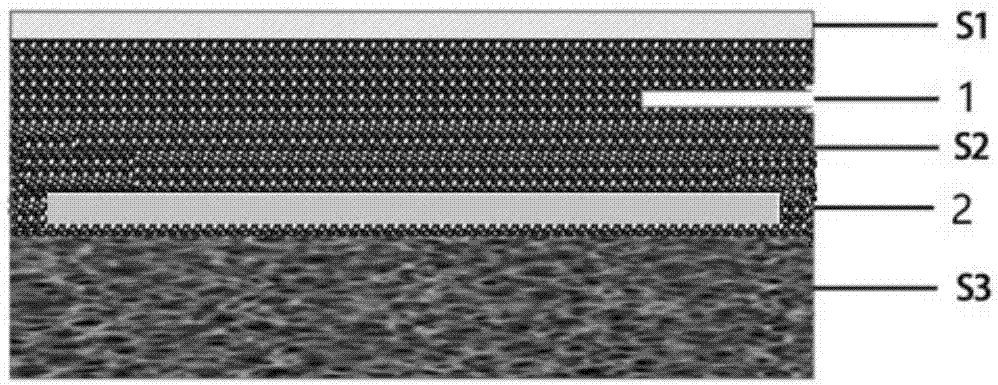
本发明涉及电热陶瓷板的制造方法,具体涉及一体压胚与烧结成型高导热碳晶智能电热陶瓷板的制备方法。
背景技术:
:随着现代生活水平的提高,各种新型加热取暖的材料被研发出来,具有优异性能的新型加热取暖材料的开发日益成为科研人员研究的焦点。电热陶瓷材料由于其耐腐蚀、耐高温和经久耐用等优点,受到人们的广泛关注。目前,采暖方式主要有:暖气片式水暖,空调和地暖等。水暖终端散热方式以外置散热片为主,其需要占据一定的空间,检修麻烦,具有安全隐患。空调预热采暖能耗较高,舒适度差。地暖式采暖中,发热线基本都是有金属电阻丝组成,且通常是在地板下面埋设发热线,发热线通电发热并将热量通过地表散发到室内中对室内进行供暖保温,其存在的问题是:电热利用率不高,金属电热丝导电也产生大量对人体有害的电磁辐射,不利于健康保健,室内供暖的热量散发不均匀且效率低下。近年来,一种新型的取暖方式被广泛应用,即电热陶瓷板,其发展比较迅速,但是,其也有很多不完善的地方,大多数电热陶瓷板的加热元件安装在瓷砖底部的安装槽内,加热元件与瓷砖之间存有空气,两者之间没有无缝对接,空气的导热系数非常小,从而,传热效率低,热损失大。中国专利申请号201611002581.8公布了碳素纤维发热片瓷砖及其生产方法,该瓷砖由墙砖本体、碳纤维发热片和发热管、聚氨酯泡沫层组成,碳纤维发热片安装在发热管中,发热管中存有空气,导致传热效率低下。中国专利申请号201720123171.x公布了一种碳纤维发热瓷砖;中国专利申请号201520813518.7公布了一种碳纤维加热泡沫砖;这两项专利均是将碳纤维发热丝置于发热层的凹槽内。这种将发热体置于发热管或置于发热层凹槽内的方式对于热的传递是不利的,因为这种排布方式导致在发热体的周围存有大量的空气,空气的传热效率非常差,从而,严重影响了传热的速率和质量。因此,解决好发热体与瓷砖之间的无缝衔接,提高传热效率是当前亟待解决的问题。在电热陶瓷板的制备中,发热材料(元件)的选择是关键,发热材料的优劣决定着电热陶瓷板的好坏。碳晶具有优良的发热性能,其制备的碳晶电热板是很好的发热产品,它是以短碳纤维制成平板充当发热体。由于碳晶电热板在发热领域的特殊优势,其开发和利用日益成为采暖设备领域研究的热点,有待在新的领域显示其发热的优势。技术实现要素:本发明的目的是克服以往技术的不足,提供一种一体压胚与烧结成型高导热碳晶智能电热陶瓷板的制备方法。所述的陶瓷板由表面层s1、碳晶板发热层s2、微孔隔热基底层s3组成,如附图1所示。碳晶是一种重要的电热材料,本发明将其用于电热陶瓷板的发热元件,拓宽了其应用领域,具有重要意义。本发明制备的电热陶瓷板采用一体压胚和烧结成型技术,将碳晶板嵌在陶瓷里面,实现碳晶板与陶瓷无缝接触,制备的电热陶瓷板使用方便,碳晶传热效率高,具有广阔的市场前景。本发明所述的一体压胚与烧结成型高导热碳晶智能电热陶瓷板的制备方法,其特征在于,所述方法包含如下步骤:(1)微孔隔热基底层s3的制备:通过发泡剂工艺配置的微孔隔热基底层陶泥(粉),然后平铺于胚体模具底层,其厚度为胚体模具总厚度的0.4~0.6,优选的,微孔隔热基底层陶泥(粉)料主要成分及含量为:50~70%的sio2,5~10%的tio2,5~10%的石棉纤维,5~10%的碳化钙,5~10%的氢氧化钙,5~10%的双氧水;(2)碳晶板发热层s2的制备:将碳晶板直接铺设在微孔隔热基底层陶泥(粉)s3上,并用胚体粉料均匀覆盖,其施料厚度为胚体模具总厚度的0.4~0.6,平整后压胚;优选的,碳晶板发热层s2陶泥(粉)料主要成分及含量为:45~55%的sio2,26~30%的al2o3,10~15%的碳纤维(短),1~2%的fe2o3,2~5%的tio2,1~2%的cao及1~2%的mgo;(3)铺设方式与结构设计:碳晶板的铺设方式如附图2所示,把碳晶板平铺在微孔隔热基底层s3平面上;碳晶板电热层中的温度传感器预留空腔及导线槽规格及设计如图3所示,针孔状温度传感器置于空腔内部,碳晶板的两端预埋至电极端子孔位置,并由外接铜丝导线沿导线槽连接至智能数据控制装置;(4)压胚与烧结成型:分层布料完成后,在模具中进行压胚或定型,其中粉料胚体压胚条件为压强不低于30mpa,压胚或定型完成后出模得半成品,干燥后放入窑炉烧结得到成品,其烧结温度为1000~1400℃,烧结时间为1~3h;(5)表面层s1的制备:称取适量陶瓷釉料的原料,其组成为:19~22%的钾长石,3~5%的烧滑石,7~9%的方解石,7~9%的球土,19~21%的烧高岭土,24~26%的熔块,10~15%的氧化铍,1~2%的烧氧化锌,1~2%的烧氧化铝,将称量好的陶瓷釉料原料放入到球磨机中进行球磨,球磨时间1~3h,然后加入占釉料质量2~4%的葡萄糖,再次球磨1~3h,得到的釉浆施加在步骤4制备的陶瓷坯体上,经干燥后在1000~1400℃下烧结获得陶瓷板,优选地,烧成制度为常温~850℃,升温时长为10min,850℃~1100℃,升温时长为7min,1100℃保温10min,最后冷却15min。本发明具有如下显著特点:(1)本发明通过一体压胚和烧结成型技术,实现电热陶瓷板的发热元件与陶瓷之间无缝衔接,实现升温迅速,效率高,具有优良的电--热转换性能。(2)本发明制备的碳晶板基电热陶瓷板在通电30~45秒之后表面温度可以达到52~53℃,在持续通电80~100秒后,样品的表面温度达到了84~86℃,而2~3分钟后样品的表面温度达到了122~124℃。(3)本发明制备的电热陶瓷板的发热元件选用碳晶板,而不是普通的碳纤维;对比实施例表明:采用碳晶板作为发热元件,相比较普通的碳纤维,碳晶板在电热陶瓷板中的传热效率更高。(4)本发明制备的电热陶瓷板的隔热基底层含有很多微孔和绝热材料石棉纤维,隔热效果好;碳晶板发热层含有导热性能优异的碳纤维(短),有利于热量向上传递;表面层含有氧化铍,其具有很好的导热和绝缘性能。通过在不同层内添加不同的添加剂,实现电热陶瓷板具有优异的传热性能,热损失小;(5)本发明采用了分层布料,一次压胚、一次性烧结工艺,整个制造流程工艺简单且一体完成,易于产业化生产,而且安装铺设简单,便于市场普及。附图说明图1本发明电热陶瓷板纵向剖面结构示意图(1.温度传感器空腔;2.碳晶板;s1.表面层;s2.碳晶板发热层;s3.微孔隔热基底层);图2本发明电热陶瓷板内部碳晶板的平面排布示意图(1.电极端子;2.碳晶板);图3本发明电热陶瓷板的温度传感器孔腔、导线槽和电极端子规格及结构示意图(1.导线槽;2.电极端子;3.温度传感器孔腔;s1.表面层;s3.微孔隔热基底层);图4本发明电热陶瓷板内部碳纤维的平面排布示意图(1.电极端子;2.碳纤维)。具体实施方式以下所述实施例详细说明了本发明。实施例1在本实施例中,一体压胚与烧结成型高导热碳晶智能电热陶瓷板采用如下方法制备而成,包括如下步骤:(1)微孔隔热基底层s3的制备:通过发泡剂工艺配置的微孔隔热基底层陶泥(粉),然后平铺于胚体模具底层,其厚度为胚体模具总厚度的0.5,优选的,微孔隔热基底层陶泥(粉)料主要成分及含量为:60%的sio2,8%的tio2,8%的石棉纤维,8%的碳化钙,8%的氢氧化钙,8%的双氧水;(2)碳晶发热层s2的制备:将碳晶板直接铺设在微孔隔热基底层陶泥(粉)s3上,并用胚体粉料均匀覆盖,其施料厚度为胚体模具总厚度的0.5,平整后压胚;优选的,碳晶发热层s2陶泥(粉)料主要成分及含量为:50%的sio2,28%的al2o3,13%的碳纤维(短),1.5%的fe2o3,4%的tio2,1.5%的cao及2%的mgo;(3)铺设方式与结构设计:碳晶板的铺设方式如附图2所示,把碳晶板以平铺在微孔隔热基底层s3平面上;碳晶板电热层中的温度传感器预留空腔及导线槽规格及设计如图3所示,针孔状温度传感器置于空腔内部,碳晶板的两端预埋至电极端子孔位置,并由外接铜丝导线沿导线槽连接至智能数据控制装置;(4)压胚与烧结成型:分层布料完成后,在模具中进行压胚或定型,其中粉料胚体压胚条件为压强为45mpa,压胚或定型完成后出模得半成品,干燥后放入窑炉烧结得到成品,其烧结温度为1000~1100℃,烧结时间为3h;(5)表面层s1的制备:称取适量陶瓷釉料的原料,其组成为:20%的钾长石,4%的烧滑石,8%的方解石,8%的球土,19%的烧高岭土,25%的熔块,13%的氧化铍,1.5%的烧氧化锌,1.5%的烧氧化铝,将称量好的陶瓷釉料原料放入到球磨机中进行球磨,球磨时间2h,然后加入占釉料质量3%的葡萄糖,再次球磨1h,得到的釉浆施加在步骤4制备的陶瓷坯体上,经干燥后在1000~1100℃下烧结获得陶瓷板,优选地,烧成制度为常温~850℃,升温时长为10min,850℃~1100℃,升温时长为7min,1100℃保温10min,最后冷却15min,制得电热陶瓷板a。实施例2在本实施例中,一体压胚与烧结成型高导热碳晶智能电热陶瓷板采用如下方法制备而成,包括如下步骤:(1)微孔隔热基底层s3的制备:通过发泡剂工艺配置的微孔隔热基底层陶泥(粉),然后平铺于胚体模具底层,其厚度为胚体模具总厚度的0.4,优选的,微孔隔热基底层陶泥(粉)料主要成分及含量为:55%的sio2,10%的tio2,10%的石棉纤维,5%的碳化钙,10%的氢氧化钙,10%的双氧水;(2)碳晶发热层s2的制备:将碳晶板直接铺设在微孔隔热基底层陶泥(粉)s3上,并用胚体粉料均匀覆盖,其施料厚度为胚体模具总厚度的0.6,平整后压胚;优选的,碳晶发热层s2陶泥(粉)料主要成分及含量为:57%的sio2,26%的al2o3,10%的碳纤维(短),1%的fe2o3,2%的tio2,2%的cao及2%的mgo;(3)铺设方式与结构设计:碳晶板的铺设方式如附图2所示,把碳晶板以平铺在微孔隔热基底层s3平面上;碳晶板电热层中的温度传感器预留空腔及导线槽规格及设计如图3所示,针孔状温度传感器置于空腔内部,碳晶板的两端预埋至电极端子孔位置,并由外接铜丝导线沿导线槽连接至智能数据控制装置;(4)压胚与烧结成型:分层布料完成后,在模具中进行压胚或定型,其中粉料胚体压胚条件为压强为50mpa,压胚或定型完成后出模得半成品,干燥后放入窑炉烧结得到成品,其烧结温度为1300~1400℃,烧结时间为3h;(5)表面层s1的制备:称取适量陶瓷釉料的原料,其组成为:22%的钾长石,3%的烧滑石,7%的方解石,9%的球土,19%的烧高岭土,25%的熔块,12的氧化铍,1.5%的烧氧化锌,1.5%的烧氧化铝,将称量好的陶瓷釉料原料放入到球磨机中进行球磨,球磨时间1h,然后加入占釉料质量4%的葡萄糖,再次球磨3h,得到的釉浆施加在步骤4制备的陶瓷坯体上,经干燥后在1000~1300℃下烧结获得陶瓷板,优选地,烧成制度为常温~850℃,升温时长为10min,850℃~1100℃,升温时长为7min,1100℃保温10min,最后冷却15min,制得电热陶瓷板b。实施例3在本实施例中,一体压胚与烧结成型高导热碳晶智能电热陶瓷板采用如下方法制备而成,包括如下步骤:(1)微孔隔热基底层s3的制备:通过发泡剂工艺配置的微孔隔热基底层陶泥(粉),然后平铺于胚体模具底层,其厚度为胚体模具总厚度的0.6,优选的,微孔隔热基底层陶泥(粉)料主要成分及含量为:70%的sio2,5%的tio2,5%的石棉纤维,5%的碳化钙,5%的氢氧化钙,10%的双氧水;(2)碳晶板发热层s2的制备:将碳晶板直接铺设在微孔隔热基底层陶泥(粉)s3上,并用胚体粉料均匀覆盖,其施料厚度为胚体模具总厚度的0.4,平整后压胚;优选的,碳晶板发热层s2陶泥(粉)料主要成分及含量为:55%的sio2,26%的al2o3,10%的碳纤维(短),1%的fe2o3,4%的tio2,1.5%的cao及1.5%的mgo;(3)铺设方式与结构设计:碳晶板的铺设方式如附图2所示,把碳晶板以平铺在微孔隔热基底层s3平面上;碳晶板电热层中的温度传感器预留空腔及导线槽规格及设计如图3所示,针孔状温度传感器置于空腔内部,碳晶板的两端预埋至电极端子孔位置,并由外接铜丝导线沿导线槽连接至智能数据控制装置;(4)压胚与烧结成型:分层布料完成后,在模具中进行压胚或定型,其中粉料胚体压胚条件为压强为35mpa,压胚或定型完成后出模得半成品,干燥后放入窑炉烧结得到成品,其烧结温度为1200~1300℃,烧结时间为3h;(5)表面层s1的制备:称取适量陶瓷釉料的原料,其组成为:19%的钾长石,3%的烧滑石,9%的方解石,9%的球土,21%的烧高岭土,26%的熔块,10%的氧化铍,1.5%的烧氧化锌,1.5%的烧氧化铝,将称量好的陶瓷釉料原料放入到球磨机中进行球磨,球磨时间2h,然后加入占釉料质量2%的葡萄糖,再次球磨2h,得到的釉浆施加在步骤4制备的陶瓷坯体上,经干燥后在1000~1400℃下烧结获得陶瓷板,优选地,烧成制度为常温~850℃,升温时长为10min,850℃~1100℃,升温时长为7min,1100℃保温10min,最后冷却15min,制得电热陶瓷板c。实施例4本实施例为对比实施例,采用市场采购的碳纤维替代碳晶板作为发热元件,碳纤维的用量与碳晶板相同,采用实施例3的方法制备电热陶瓷板,具体步骤如下:(1)微孔隔热基底层s3的制备:通过发泡剂工艺配置的微孔隔热基底层陶泥(粉),然后平铺于胚体模具底层,其厚度为胚体模具总厚度的0.6,优选的,微孔隔热基底层陶泥(粉)料主要成分及含量为:70%的sio2,5%的tio2,5%的石棉纤维,5%的碳化钙,5%的氢氧化钙,10%的双氧水;(2)碳纤维发热层s2的制备:将碳纤维以环状直接铺设在微孔隔热基底层陶泥(粉)s3上,并用胚体粉料均匀覆盖,其施料厚度为胚体模具总厚度的0.4,平整后压胚;优选的,碳纤维发热层s2陶泥(粉)料主要成分及含量为:55%的sio2,26%的al2o3,10%的碳纤维(短),1%的fe2o3,4%的tio2,1.5%的cao及1.5%的mgo;(3)铺设方式与结构设计:碳纤维的铺设方式如附图4所示,把碳纤维以环状平铺在微孔隔热基底层s3平面上;碳纤维电热层中的温度传感器预留空腔及导线槽规格及设计如图3所示,针孔状温度传感器置于空腔内部,碳丝束电热线的两端预埋至电极端子孔位置,并由外接铜丝导线沿导线槽连接至智能数据控制装置;(4)压胚与烧结成型:分层布料完成后,在模具中进行压胚或定型,其中粉料胚体压胚条件为压强为35mpa,压胚或定型完成后出模得半成品,干燥后放入窑炉烧结得到成品,其烧结温度为1200~1300℃,烧结时间为3h;(5)表面层s1的制备:称取适量陶瓷釉料的原料,其组成为:19%的钾长石,3%的烧滑石,9%的方解石,9%的球土,21%的烧高岭土,26%的熔块,10%的氧化铍,1.5%的烧氧化锌,1.5%的烧氧化铝,将称量好的陶瓷釉料原料放入到球磨机中进行球磨,球磨时间2h,然后加入占釉料质量2%的葡萄糖,再次球磨2h,得到的釉浆施加在步骤4制备的陶瓷坯体上,经干燥后在1000~1400℃下烧结获得陶瓷板,优选地,烧成制度为常温~850℃,升温时长为10min,850℃~1100℃,升温时长为7min,1100℃保温10min,最后冷却15min,制得电热陶瓷板d。性能评价实施例:发热性能参数检测:根据预先设计的胚体模具,实施例1~4制得4种规格的陶瓷板小样品,分别为电热陶瓷板a、b、c和d,其厚度为8~10mm,面积为50mm*40mm。经检测,烧结成陶瓷板后碳丝发热导线的电阻为5.0~40.0ω之间,复合实验预期。测试电热陶瓷板a、b、c和d的发热性能。使用flirone红外相机与稳压电源对所制得的材料电热转换性能进行了表征。将烧制形成的陶瓷板碳丝束两端接上7.5~12v的恒定电源(电流0.5~1.5a),并使用红外热成像相机对材料表面的温度进行实时测量,测试结果如表1所示:表1实施例1~4制备的电热陶瓷板a、b、c和d在不同的通电时间的表面温度通电时间电热陶瓷板a电热陶瓷板b电热陶瓷板c电热陶瓷板d30~45秒52.6℃53.5℃53.7℃42.7℃80~100秒86.5℃84.5℃85.6℃71.5℃2~3分钟122.5℃124.9℃124.6℃93.7℃由表1可知,陶瓷板的表面温度随着通电时间的增加而增加,其中,电热陶瓷板a在通电30~45秒之后表面温度可以达到52.6℃,在持续通电80~100秒后,样品的表面温度达到了86.5℃,而2~3分钟后样品的表面温度达到了122.5℃。电热陶瓷板b和电热陶瓷板c在相同的通电时间时,其表面温度与电热陶瓷板a的表面温度十分接近。电热陶瓷板d的表面温度在相同的通电时间时明显低于电热陶瓷板a、b和c,这表明,本发明制备的电热陶瓷板中碳晶板的发热与传热效率高于的碳纤维。当前第1页12