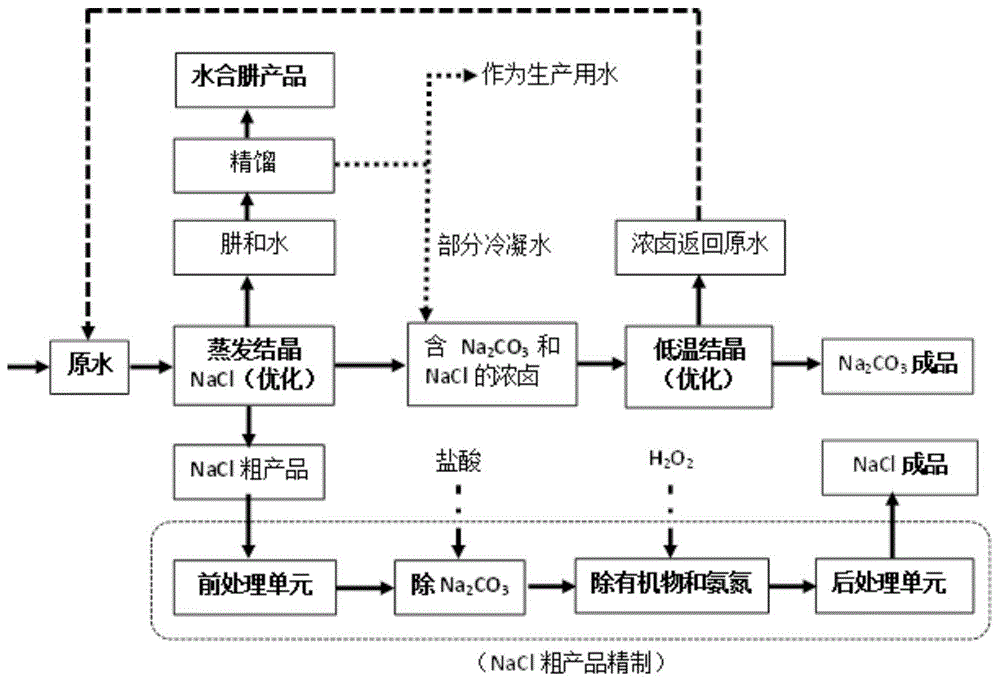
本发明属于化工
技术领域:
,涉及化学工业废水的处置与资源回收
技术领域:
,具体涉及一种从高盐水合肼溶液中回收并精制盐碱的方法。
背景技术:
:近年来,随着我国经济的快速增长,工业规模不断扩大,工业生产中产生的废水量也随之迅速增加,使得工业废水的处理面临空前的挑战。高盐废水是工业废水中的一类,主要来源于工业生产、海水利用及居民生活污水等,其含盐量较高(通常所含总溶解性固体质量分数≥3.5%),通常含有大量cl-、so42-、na+、ca2+等可溶性无机盐离子,且有些高盐废水中还含有有机污染物。我国每年会产生大量高盐废水。据统计,2009年仅印染行业产生的高cod、高盐度染料废水总量就已达2.43×109m3。由于高盐废水中的盐分会一定程度上抑制微生物的生长,未经处理的高盐废水直接排放至下游污水处理厂,将对其生物处理单元造成冲击,因此高盐废水在企业内的预处理至关重要。随着国家对水环境管理与保护的不断加强,对工业高盐废水的处理往往要求达到“零排放”。目前,工业高盐废水“零排放”处理工艺的基本思路是使盐和水分离,得到回用水和结晶盐,但分离出的盐是含多种无机盐的杂盐,属于危险废弃物的范畴,其处理成本较高,且处置不当会造成环境的污染。当前,高盐废水的处理技术主要有膜分离技术、热浓缩技术、膜蒸馏技术以及生物处理技术等,其中,热浓缩技术包括多效蒸发技术、热力蒸汽再压缩蒸发技术、机械蒸汽再压缩蒸发技术。采用膜分离技术、热浓缩技术、膜蒸馏技术和生物处理技术处理工业高盐废水时,无法实现单质盐与资源化利用,因此如何将工业高盐废水中的盐以单质盐的形式分离出来成为当前高盐废水处理的重点与难点。当高盐废水中所含两种无机盐在水中的溶解度随温度变化差异较大时,采用蒸发浓缩-冷却结晶-蒸发结晶工艺可以将两种无机盐分别析出达到分离之目的。郝红勋等发明了一种从高盐废水(氯化钠质量分数为2.28%,硫酸钠质量分数为0.72%)中提纯氯化钠和硫酸钠的方法并已应用于生产实践中。由于氯化钠在水中的溶解度随温度变化不大,而硫酸钠对温度变化较为敏感,因此废水先经电渗析和机械蒸汽再压缩蒸发装置浓缩后将浓缩液送入结晶器冷却结晶得到芒硝;从冷冻结晶器出来的浓缩液再经两级蒸发结晶可得到氯化钠产品。该工艺所得的氯化钠和无水硫酸钠产品纯度均可达99%,且两者的回收率均达到90%以上。该工艺的适应条件为:在水中的溶解度对温度变化较为敏感的无机盐含量大于溶解度随温度变化不大的无机盐含量,或两者含量相差不大的高盐废水。对于在水中的溶解度随温度变化不大的无机盐含量远大于溶解度对温度变化较为敏感的无机盐含量的高盐废水,目前还缺乏实用的分盐工艺。技术实现要素:针对现有技术的不足,本发明的目的在于提供一种从高盐水合肼溶液中回收并精制盐碱的方法,该方法针对所含盐分主要为氯化钠和碳酸钠且氯化钠浓度远大于碳酸钠浓度的高盐水合肼溶液。采用高温蒸发高盐水合肼溶液后室温结晶回收nacl粗产品,并用浓hcl和h2o2精制并焙烧得到高纯度nacl成品;低温冷冻结晶回收高纯度na2co3成品;采用精馏手段回收水合肼。为实现上述目的,本发明采取的技术方案为:一种从高盐水合肼溶液中回收并精制盐碱的方法,包括以下步骤:步骤1,蒸发高盐水合肼溶液后,室温下结晶回收nacl粗产品测定高盐水合肼溶液中氯化钠、碳酸钠、硫酸钠、总盐、toc、水合肼的含量,务必保证高盐水合肼溶液中nacl浓度远大于na2co3浓度,再将高盐水合肼溶液原水输入至蒸发装置中进行蒸发,当蒸发量达到最优蒸发量时停止加热,室温下冷却结晶,然后分离晶体和溶液,分离出来的晶体经105℃烘干和300℃焙烧后即得到nacl粗产品,而分离出来的滤液则用于低温冷冻结晶回收高纯度na2co3成品;所述高盐水合肼溶液中的盐分主要为nacl和na2co3;步骤2,精馏分离回收水合肼在步骤1中蒸发高盐水合肼溶液的过程中,将产生的蒸汽(包含水合肼和水分)冷凝后,再通过精馏设备分离回收水合肼,分离后的部分冷凝水则回流至步骤1中蒸发结晶nacl后过滤产生的滤液中,得到含na2co3和nacl的浓卤,其余冷凝水作为生产用水;步骤3,精制nacl粗产品取nacl粗产品于坩埚中,加入质量分数37%的浓盐酸紧接着再向坩埚内加入质量分数30%的双氧水,用玻璃棒小心搅拌后,室温下静置30min,置于马弗炉内,高温焙烧后,得nacl纯度>99.1%、总有机碳<10ppm与氨氮<5ppm的精制nacl;步骤4,回收高纯度na2co3成品将步骤2中得到的浓卤进行-5~5℃下冷冻结晶回收纯度应大于95%碳酸钠;步骤5,饱和碳酸钠溶液的循环处理将步骤4中冷冻结晶后剩余的饱和碳酸钠溶液回流至步骤1中未开始蒸发的高盐水合肼溶液原水中得到混合后的溶液,然后开始新一轮的蒸发,实现零废水排放。进一步的是,步骤1中所述最优蒸发量时,蒸发结晶得到的nacl粗产品中碳酸钠的质量百分比为6%~7%,且在蒸发过程中水合肼的损失量以质量分数计低于2%。进一步的是,步骤3中高温焙烧的温度为600℃。进一步的是,步骤3中高温焙烧的时间为3~5h。有益效果:与现有技术相比,本发明一种从高盐水合肼溶液中回收并精制盐碱的方法的优势是从高盐水合肼溶液中回收水合肼的同时回收氯化钠和碳酸钠,降低了生产成本,并实现了废水零排放。本发明的主要特点如下:(1)工艺简单易行,运行维护费用低;(2)回收得到的氯化钠成品可满足:nacl纯度>99.1%、toc<10ppm、氨氮<5ppm;(3)回收得到的碳酸钠(含结晶水)成品纯度>95%;(4)水合肼溶液在蒸发过程中水合肼的损失量低于以质量分数计的2%。附图说明图1是本发明从高盐水合肼溶液中回收并精制盐碱的方法的流程图;图2是本发明的实施例1中的循环实验结果。具体实施方式下面结合附图和具体实施例对本发明作进一步描述。实施例1一种从高盐水合肼溶液中回收并精制盐碱的方法,包括以下步骤(如图1所示):首先测得江苏省某化工企业高盐水合肼溶液的水质如表1所示:表1江苏省某化工企业高盐水合肼溶液水质序号项目单位数值1ph无12.822naclg/l147.123na2co3g/l80.254na2so4g/l0.235总盐g/l248.606tocg/l2.597水合肼wt%4.831.蒸发高盐水合肼溶液后,25℃下结晶回收nacl粗产品用1000ml玻璃量筒取1l高盐水合肼溶液置于90℃电热鼓风干燥箱(型号dhg-9070a)进行蒸发,当溶液的蒸发量达到10%时,装置中开始出现晶体;当溶液的蒸发量达到35%时,到达最优蒸发量,停止蒸发,室温下冷却48h,过滤得到晶体和滤液。将过滤得到的nacl结晶体于105℃烘干至恒重,然后再置于马弗炉(型号sx2-8-10)内300℃焙烧2h后即可得到nacl粗产品。每升高盐水合肼溶液最终可获得10.27gnacl粗产品,该粗产品中nacl含量为91.63%(质量分数),碳酸钠含量为6.30%(质量分数)。2.精馏分离回收水合肼在步骤1中蒸发高盐水合肼溶液的过程中,将产生的蒸汽(包含水合肼和水分)冷凝后,再通过精馏设备分离回收水合肼,分离后的部分冷凝水则回流至步骤1中蒸发结晶nacl后过滤产生的滤液中,得到含na2co3和nacl的浓卤,其余冷凝水作为生产用水。经测定,在蒸发过程中水合肼的损失量为1.6%(质量分数)。水合肼的损失量按以下公式计算:m肼=m1+m2+m损=w1·m剩+w2·m冷+m损m=m剩+m冷式中:m剩——所取蒸馏剩余液质量,g,m剩=1.0191g;m冷——所取蒸馏冷凝液质量,g,m冷=1.0358g;.m——蒸馏前水样的质量,g,m=m剩+m冷;m肼——蒸馏前水样中肼的质量,g,m肼=m1+m2;m1——剩余液中肼的质量,g,m1=w1·m剩;m2——冷凝液中肼的质量,g,m2=w2·m冷;m损——蒸馏过程中损失的肼的质量,g;w1——剩余液中肼的质量分数,%;w2——冷凝液中肼的质量分数,%;w——蒸馏前水样中肼的质量分数,%;w损——损失的肼的质量分数,%。水溶液中水合肼含量的测定采用《工业水合肼》(hg/t3259-2012)中水合肼含量的测定方法。3.精制nacl粗产品称取3.0000g氯化钠粗产品于坩埚中,加入2.5g质量分数37%的浓盐酸(分析纯),紧接着再向该坩埚内加入3.5g质量分数30%的双氧水(分析纯),用玻璃棒小心搅拌后,室温下静置30min,然后将其置于马弗炉内,经过3h升温至600℃并保持3h,最终得到纯度为99.52%的氯化钠成品2.9557g,其中氨氮浓度为4.501ppm,toc浓度小于检出限。nacl水溶液中cl-的测定采用《制盐工业通用试验方法-氯离子的测定》(gb/t13025.5-2012);水溶液中氨氮浓度的测定采用《水质氨氮的测定纳氏试剂分光光度法》(hj535-2009);水溶液中toc浓度采用toc仪(型号lignitoc/tn)测定。4.回收高纯度na2co3成品将步骤2中的浓卤在0℃条件下进行冷冻结晶(不加任何晶种)得碳酸钠结晶体。将碳酸钠结晶体于105℃烘干至恒重,最终每升高盐水合肼溶液可获得20.9g纯度为95.14%的碳酸钠(含结晶水)成品(含无水碳酸钠16.23g)。5.饱和碳酸钠溶液的循环处理将步骤4中冷冻结晶后剩余的饱和碳酸钠溶液回流至步骤1中未开始蒸发的高盐水合肼溶液原水中得到混合后原水,然后开始新一轮的蒸发结晶。该实施例中进行5次循环实验,经过测量冷冻结晶后溶液与原水混合的溶液中氯化钠和碳酸钠的浓度,得到如图2所示的结果。从图2中可以看出,随着循环次数的增加,氯化钠的浓度先上升,至第4次循环后浓度增长速度变缓。碳酸钠的浓度随着循环次数的增加迅速下降,且随着循环次数的增加其浓度降低趋势变缓。当循环次数继续增加,溶液中氯化钠和碳酸钠的浓度将趋于稳定,且此时随着原水的不断进入装置,由于装置中蒸发实验的进行,装置中的溶液体积将保持不变,即此处理工艺不排出废水。实施例2该实施例的步骤1~3同实施例1。步骤4.回收高纯度na2co3成品将步骤2中的浓卤在0℃条件下进行冷冻结晶(添加晶种,每1l浓卤投加0.0200g无水碳酸钠晶体)得碳酸钠结晶体。将碳酸钠结晶体于105℃烘干至恒重,然后再于600℃焙烧3h,最终每升高盐水合肼溶液可获得21.43g含无水碳酸钠。经计算,含结晶水的碳酸钠纯度为91.06%。从该实施例可知,虽然添加无水碳酸钠晶种可以显著提高碳酸钠的回收率,但所得含结晶水的碳酸钠纯度也显著下降。实施例3除步骤3的步骤改变外,其余同实施例1。步骤3.精制nacl粗产品称取2.0000g氯化钠粗产品于坩埚中,加入1.6g37%的浓盐酸,紧接着再向该坩埚内加入2.5g30%的双氧水,用玻璃棒小心搅拌后,室温下静置30min,然后将其置于马弗炉内,升温至300℃并保持2h,最终得到纯度为97.83%的氯化钠成品1.9566g。从该实施例可知,焙烧温度对氯化钠成品的纯度有显著影响,将焙烧温度由600℃降低至300℃,则氯化钠成品的纯度相应由99.52%下降至97.83%。对比例1除步骤3的步骤改变外,其余同实施例1。步骤3.精制nacl粗产品称取3.0000g氯化钠粗产品于坩埚中,加入2.5g质量分数37%的浓盐酸(分析纯),用玻璃棒小心搅拌后,室温下静置30min,然后将其置于马弗炉内,经过3h升温至600℃并保持3h,最终得到纯度为98.14%的氯化钠成品3.0136g。与实施例1对比发现,若缺少投加双氧水这一关键步骤,那么得到的精制氯化钠成品的纯度将显著降低至98.14%。对比例2除步骤3的步骤改变外,其余同实施例1。步骤3.精制nacl粗产品称取3.0000g氯化钠粗产品于坩埚中,加入2.5g质量分数37%的浓盐酸(分析纯),紧接着再向该坩埚内加入3.5g质量分数30%的双氧水(分析纯),用玻璃棒小心搅拌后,室温下静置30min,然后将其置于马弗炉内,升温至300℃并保持2h,最终得到纯度为97.83%的氯化钠成品2.9349g。与实施例1对比发现,若缺少600℃焙烧3h这一关键步骤,那么得到的精制氯化钠成品的纯度将显著降低至97.83%。当前第1页1 2 3