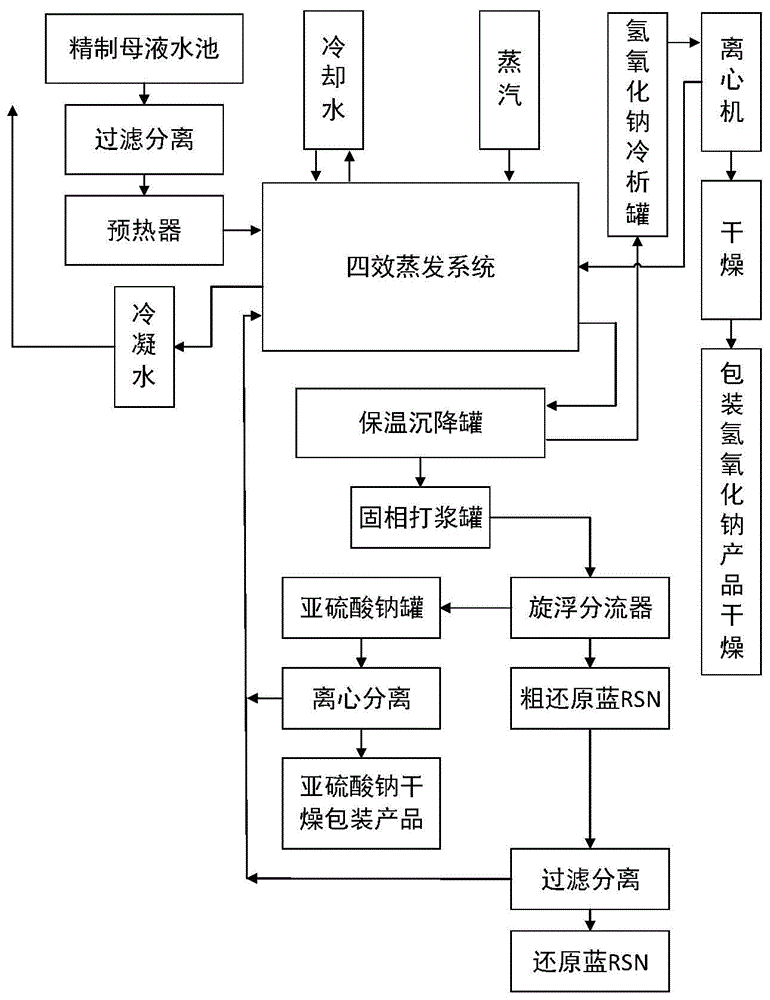
本发明涉及一种还原蓝rsn精制母液处理方法,用于对还原蓝rsn精制母液进行处理。
背景技术:
:蒽醌系还原染料具有悠久的历史,从1901年发现还原蓝rsn到今已有100多年,是用于制造纤维素纤维高级制品或功能制品的重要棉用染料之一。随着国民经济的快速发展,人们的消费需求逐渐趋向多元化,对纺织品功能性、舒适性和时装性的要求越来越高,预计到2020年,超过半数的纺织品需求要达到中高档要求。还原染料rsn是指在碱性条件下被还原而使纤维着色,再经氧化,在纤维上恢复成原来不溶性的染料而染色,用于染纤维素纤维;将不溶性还原染料制成硫酸酯钠盐,可变成可溶性还原染料,主要用于棉布印花。还原染料是指一类性能优良的染料,具有色光鲜艳,色谱齐全,染色效果牢度优良,尤其是耐晒牢度高,是目前要求高染色质量的各类纺织品染色中极其重要的染料品种。也可用于高档颜料制作原料,用于军工、汽车喷涂、油墨等。我国是世界公认的纺织大国,随着中国纺织业的快速发展提高了对染料化学品的需求,染料行业与纺织业的相互依存显示我国染料行业市场巨大。据统计,2012年我国染料、有机颜料产量合计达到超过100万吨,全国染料进出口总量超过40万吨,我国染料产量、出口量和消费量位列世界各国之首。还原蓝rsn生产一般经过缩合、水析、加入在碱性溶液中加入保险粉精制还原,氧化酸化中和,洗涤干燥制得还原蓝rsn产品。生产反应工程方程式如下:缩合:精制还原:氧化酸化:通过对还原蓝rsn的物化性质及反应机理分析,还原蓝rsn生产母液主要含有的组分为:亚硫酸钠、氢氧化钠、少量的隐色还原蓝rsn钠盐、微量的隐色还原蓝rsn钾盐90%的水。还原蓝rsn生产母液具有高盐、高bod的工业废水,每生产一吨还原蓝rsn就能产生50吨工业洗涤水。废水首先将废水进行酸碱中和,再经四效蒸发装置进行脱盐,并将离心机产生的含固量大于80%的混合盐作为固废进一步集中处理,另将产生的污冷水与其他废水一起进入调节池调节水质水量。由于废水中缺氮缺磷,故在此投加适量尿素和磷酸二氢钠,以满足厌氧和好氧微生物生长对营养的均衡要求(cod∶n∶p=100~500∶5∶1)。调节池中废水由提升泵送入一级uasb,并自流入二级uasb,废水中有机物被厌氧反应器中的厌氧微生物所吸附分解为甲烷、二氧化碳、水及小分子物质,厌氧产生的沼气,量小无回收价值,经15m高排气筒高空排放。厌氧反应器出水进入厌氧沉淀池,沉淀带出的厌氧污泥并将其回流到厌氧塔。厌氧塔出水进入生物接触氧化池,池中安装有供微生物生长的组合式生物填料和为微生物提供氧气的曝气器,废水中剩余有机物被附着在填料上的微生物所吸附、氧化、分解为二氧化碳和水;生物接触氧化池出水进入二沉他沉淀脱落的生物膜和活性污泥后达标排放。二沉池及uasb厌氧反应器剩余的污泥约进入污泥浓缩池进行浓缩后,再送入叠螺式污泥脱水机及进行脱水,滤液返回调节池,得到的含水率约80%的污泥按一般固废进行最终处置。由于洗涤水量水量较大,大量的还原蓝rsn进入生产废水中,还原蓝rsn的收率降低,大量的氢氧化钠以硫酸中和,原料浪费严重,生产成本居高不下。还原蓝rsn染料中间体生产如何做到清洁无污染,提高还原蓝rsn的产率,降低生产成本成为染料中间体生产企业面临的主要问题。母液(废水)的难处理及生态环境的保护直接影响还原蓝rsn企业的发展及生产规模。技术实现要素:本发明所要解决的技术问题是提供一种还原蓝rsn(对还原漂蓝bc同样适用)精制母液处理方法,操作简单,处理过程纯物理,不添加任何附加剂,提取产品不残留,能耗小,成本低,能够连续处理。为解决上述技术问题,本发明还原蓝rsn精制母液处理方法,包括以下步骤:(1)精制母液中隐色还原蓝rsn钠盐会被氧化,生成固态还原蓝rsn,将精制母液通入过滤器,除去已经沉淀的固态还原蓝rsn,得到澄清精制母液,固态还原蓝rsn做为粗产品进一步精制。(2)对澄清精制母液进行蒸发浓缩(如采用四效蒸发器或mvr蒸发器),隐色还原蓝rsn钠盐进一步氧化形成固态还原蓝rsn沉淀下来,由于亚硫酸钠相对于氢氧化钠在高温时溶解度小得多,随着水分蒸发,故亚硫酸钠会首先析出,进一步蒸发浓缩,精制母液中的氢氧化钠浓度越来越高,当体系(蒸发体系)溶液中氢氧化钠接近饱和时,混合固液进入保温沉降罐,使体系中悬浮的亚硫酸钠析出并沉积,高浓度氢氧化钠溶液送至冷析工段;混合固相进入打浆罐,使亚硫酸钠和固态还原蓝rsn完全剥离,利用悬浮离心分离原理,蒸蒸汽冷凝回收。(3)利用氢氧化钠溶解度随温度降低而溶解度减小原理,将步骤(2)中得到的氢氧化钠溶液采用闪发结晶冷析装置(如采用三级闪发结晶冷析装置,满足闪发结晶在绝热条件下的技术要求,实现热能和动能的自发转换,运行能耗更低)处理,温度从100℃冷却至30℃,此时亚硫酸钠溶解度达到最大,分离的氢氧化钠品质更高,分离出氢氧化钠,氢氧化钠经过滤、淋洗后获得,可返回生产工段重复利用或干燥包装后作为产品销售。(4)根据固态还原蓝rsn和亚硫酸钠的水溶性、粒度、比重不同,将步骤(2)中得到混合固体进行打浆,使不同物质粘连颗粒剥离,利用悬浮离心分离原理进行分离亚硫酸钠及粗制固态还原蓝rsn。亚硫酸钠过滤、淋洗、干燥包装成产品外售,还原蓝rsn洗涤后进一步精制成产品或做还原漂蓝bc原料去做下游原料。本发明方法还包括收集步骤(2)中蒸发产生的冷凝水步骤。当采用四效蒸发器时,i、ii、iii效冷凝水返回水系统或做软化水用于生产系统,iv效冷凝水经过混合冷凝器冷却进入冷却水循环系统,循环使用。本发明处理方法为物理处理技术,不添加任何添加剂,所分离产品均可以返回生产工段作为生产原料使用。采用四效蒸发浓缩技术,工艺成熟,蒸汽耗量仅为0.3吨/吨精制母液。氢氧化钠回收采用三级闪发结晶器技术,前一级产生的废热转换动能,减少搅拌装置,节约投资成本、降低能耗,同时补充闪发冷析损失热量,可以保证闪发结晶在绝热条件下进行的技术要求。采用四效蒸发,对每效产生的冷凝水可以合理安排预热母液,使余热得到重复利用。根据物理化学特性,蒸发采用平流补料及错流提料技术,选择蒸发器的第二效提取完成液,此温度下亚硫酸钠溶解度相对较低,而氢氧化钠溶解度相对较大,并且利于保温沉降技术条件。保温沉降(保温沉降灌)、打浆及悬浮选料(旋流分离器)使几种物料更有效分离,且产品纯度更高,设备投资更低,占地面积较小,蒸发蒸汽耗量和选择mvr蒸发基本一样,降低能耗。分离原理:利用亚硫酸钠在33.8℃溶解度最大,而且溶解度相对于氢氧化钠小的多的物质特性,及氢氧化钠在水溶液中溶解度随温度变化较大,而且温度越高溶解度越大的原理进行蒸发分离固相亚硫酸钠及氢氧化钠高浓度溶液。利用母液中的还原蓝rsn隐色钠盐可溶于水而还原蓝rsn不溶于水的原理,及还原蓝rsn钠盐遇空气(氧气)会自动还原为还原蓝rsn的原理,使还原蓝rsn隐色钠盐在系统中运行始终会以还原蓝rsn形式出现并析出的原理,达到分离目的,对还原蓝rsn精制母液进行分步、分离提纯。在实现提取反应产物亚硫酸钠、还原蓝rsn、氢氧化钠的过程中,水分通过蒸发冷凝作为生产补充水,实现了生产废水零排放;采用这种处理方法处理还原蓝rsn精制母液,能耗低,产品收率高,产品无干扰因素介入,操作简单,生产条件温和,易于实现连续化、工业化大规模处理,节约能源,优质资源提取、合理利用。本发明的有益效果:分离反应产物亚硫酸钠、提取母液中夹带的还原蓝rsn,回收过量附加生产原料氢氧化钠,提高还原蓝rsn产率;采用四效蒸发或mvr蒸发浓缩原理尽可能降低蒸汽耗量。采用闪发结晶技术提取氢氧化钠、打浆悬浮技术有效分离亚硫酸钠和还原蓝rsn。多效蒸发或mvr提高了蒸汽的利用率,能耗仅为普通蒸发的30%;采用闪发结晶技术,随着温度降低,亚硫酸钠不饱和,闪发结晶带走一部分水蒸气(第三级结晶器接混合冷凝器或蒸汽喷射泵),亚硫酸钠始终处于饱和状态,保证氢氧化钠的析出量,并可以在闪发结晶器补水调浆,保证析出氢氧化钠产品纯度。分离母液返回蒸发系统进一步浓缩,循环往复,达到提取分离目的。析出产品经过转料、保温、打浆、形成粒度更大,在分离、洗涤时更利于生产。本技术发明产生的亚硫酸钠做产品销售,还原蓝rsn可以做还原漂蓝bc原料,也可以进一步酸化中和后做为产品销售。回收的氢氧化钠经离心、淋洗、脱水后直接作为还原蓝rsn工段或还原漂蓝bc生产原料使用。本发明回收母液中夹带的还原蓝rsn,提高还原蓝rsn的收率,回收反应系统过量的氢氧化钠,分离副产物亚硫酸钠,实现母液处理零排放较大程度降低还原蓝rsn的生产成本。附图说明下面结合附图和具体实施方式对本发明作进一步详细的说明。图1为本发明的原理图。具体实施方式还原蓝rsn精制母液主要包括亚硫酸钠、还原蓝rsn隐色钠盐、氢氧化钠、水,成分为:名称亚硫酸钠氢氧化钠还原蓝rsn水含量3.5%5.5%0.5%90.5%上述精制母液处理步骤如图1所示:步骤一:过滤,精制母液在收集池中放置,精制母液中隐色还原蓝rsn钠盐会被氧化,生成固态还原蓝rsn,将精制母液送至过滤器,除去已经沉淀的固态还原蓝rsn,得到澄清精制母液,固态还原蓝rsn做为粗产品进一步精制。步骤二:澄清精制母液送至四效蒸发器(或mvr蒸发器),进行多效蒸发(或mvr蒸发),隐色还原蓝rsn钠盐进一步氧化形成固态还原蓝rsn沉淀下来,由于亚硫酸钠相对于氢氧化钠在高温时溶解度小得多,随着水分蒸发,故亚硫酸钠会首先析出,进一步蒸发浓缩氢氧化钠浓度会越来越高,当体系(蒸发体系)溶液中氢氧化钠接近饱和时,混合固液进入保温沉降罐,使悬浮的亚硫酸钠析出并沉积,高浓度氢氧化钠去冷析。混合固相进入打浆罐,使亚硫酸钠和固态还原蓝rsn完全剥离,采用旋流分离器分离,蒸发回收冷凝水返回生产系统循环利用。步骤三:利用氢氧化钠溶解度随温度降低而溶解度减小原理,将步骤二中得到氢氧化钠溶液采用三级闪发结晶装置(授权公开号为201775979u专利文献公开)处理,温度从100℃冷却至30℃,此时亚硫酸钠溶解度达到最大,分离的氢氧化钠品质更高。氢氧化钠经过滤、淋洗后返回生产工段重复利用或干燥包装后作为产品销售。步骤四:根据固态还原蓝rsn和亚硫酸钠的水溶性、粒度、比重不同,将步骤二中得到混合固体进行打浆,使不同物质粘连颗粒剥离,利用悬浮原理进行分离亚硫酸钠及粗制固态还原蓝rsn,亚硫酸钠过滤、淋洗、干燥包装成产品外售,还原蓝rsn洗涤后进一步精制成产品或做还原漂蓝bc原料去做下游原料。采用旋流分离器悬浮分离,避免分离还原蓝rsn时大量水的加入,增加蒸汽耗量、增加设备投资成本及运行成本。步骤五:收集步骤二中蒸发产生的i、ii、iii效(四效蒸发器的i、ii、iii效)冷凝水,返回水系统或做软化水用于生产系统,iv效(四效蒸发器的iv效)冷凝水经过混合冷凝器冷却进入冷却水循环系统,循环使用。氢氧化钠采用三级闪发结晶技术,实现废热自由转换为动能过程并降低闪发冷析需要在绝热情况下进行的技术条件。采用分步分离,目的其一、提高氢氧化钠、亚硫酸钠的纯度;其二、回收母液中还原蓝rsn;其三、增加物料从析出到形成产品过程的时间,使还原蓝rsn隐色钠盐尽可能在第一轮运行中转化成还原蓝rsn。生产提取的还原蓝相当于1.14倍的1-氨基蒽醌,提高原料转化滤,生产产品粗还原蓝rsn酸化中和处理,干燥包装为产品或去下游做还原漂蓝bc的生产原料。亚硫酸钠、氢氧化钠、还原蓝rsn洗涤液进入母液池循环往复蒸发达到分离反应产物亚硫酸钠、原料氢氧化钠和产品还原蓝rsn冷凝水可以当软化水做生产工艺补充水,实现零排放而提产品收率,降低生产成本的目的。采用上述处理方法:每生产1吨还原蓝rsn产生50吨废水,提取1.75吨亚硫酸钠,2.75吨氢氧化钠,0.25吨还原蓝rsn,收率可以达到98%,回收冷凝水29.5吨,消耗蒸汽18.4吨。相比于现有技术对还原蓝rsn处理方法中废水蒸发浓缩分离混合固废6吨。消耗蒸汽38吨,节约能耗51.98%。实现生产母液零排放;还原蓝rsn收率提高18%。目前国内1-氨基蒽醌市场售价:13万元/吨左右,工业级氢氧化钠产品市场售价:0.5万元/吨左右,亚硫酸钠0.2万元/吨。采用此处理方法增加产值:1.75×2000+2.75×5000+0.25×1.14×130000+29.5×6-18.4×200=5.077万元。目前国内处理1吨固废的平均价格为0.4万元/吨,废水排放6.0元/1吨,由于染料中间体很难降解,生化处理是至少要加入5倍的工业水,故采用传统工艺处理每生产1吨还原蓝rsn的废水处理成本为:200×6+250×6+6×4000+38×200=3.35万元。采用上述处理方法进行还原蓝rsn母液处理,可以有效分离亚硫酸钠、还原蓝rsn、氢氧化钠,回收冷凝水,提高还原蓝rsn产率15%,实现还原蓝rsn生产过程零排放。上述实施例不以任何方式限制本发明,凡是采用等同替换或等效变换的方式获得的技术方案均落在本发明的保护范围内。当前第1页12