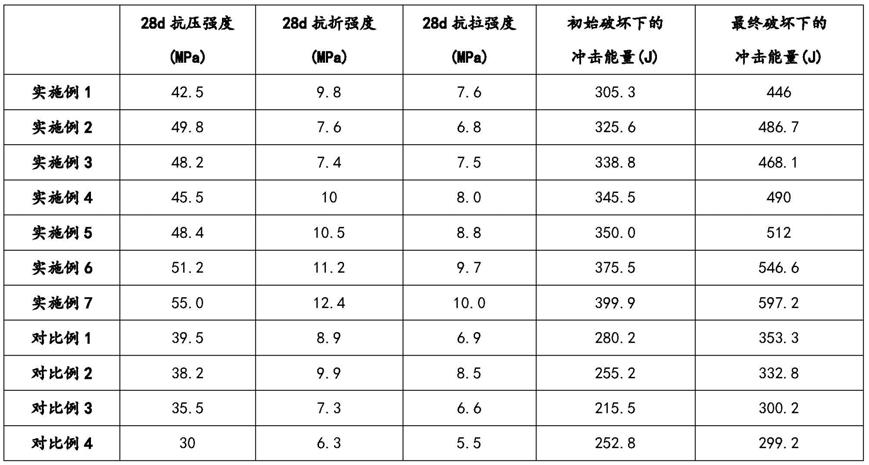
1.本发明属于建筑材料的技术领域,具体涉及一种高强抗裂抗冲击混凝土的制备方法以及由该方法制得的高强抗裂抗冲击混凝土。
背景技术:2.因为混凝土材料的广泛应用,这也使得越来越多的混凝土结构遭受频繁或者偶然的抗冲击荷载,如机场跑道受到飞机着陆冲击,海洋结构物受到海浪冲击,遭受炸弹冲击的保护结构和地震区可能发生强烈地震的民用建筑。然而,传统混凝土的变形有限,能量吸收能力差,这使得在冲击荷载条件下对混凝土结构的安全性带来了具体挑战。虽然胶凝材料具有较高的抗压强度,但是他们也具有脆性断裂特性,所以在满足强度的同时,制备高抗裂性混凝土也是必须实现的。
3.因此,近些年人们积极研究纤维增强水泥基复合材料,利用纤维水泥基体之间的粘结性能和交联反应,通过对遭受冲击应力的吸收和分布,表现出较高的弯曲和拉伸特性,从而控制水泥基体的开裂。但是,在满足抗裂的同时,钢纤维的掺入可能会带来其他不利因素,例如钢纤维密度大会增加结构重量,此外,钢纤维在潮湿和空气中极易被腐蚀,降低结构材料耐久性。
4.专利201810455234.3公开了一种利用双螺旋纤维制备的混凝土,虽然掺入的双螺旋纤维比传统纤维混凝土具有抗裂方面的增强效果,但是因为其所涉及纤维结构的负泊松比有限,无法实现混凝土的抗冲击性和抗爆性能。
技术实现要素:5.本发明的目的在于:一方面克服传统方法制得的高强抗裂抗冲击混凝土的抗压强度和抗折强度差的特点;另一方面改善骨料之间的粘结性,使得在抗冲击试验中,混凝土在高能量的冲击下可以很好地吸收能量和均匀分散能量,以避免应力集中产生微裂缝甚至破坏。因此,本发明提供一种节约成本,保护环境,且满足抗压、抗折强度,有效吸收冲击能量,避免冲击破坏的高强抗裂抗冲击混凝土的制备方法以及利用该方法制得的高强抗裂抗冲击混凝土。
6.本发明提供一种高强抗裂抗冲击混凝土的制备方法,其特征在于,包括以下步骤:
7.(1)利用滚筒干磨机将铜渣、矿渣干磨至粉状,分别得到铜渣粉和矿渣粉;
8.(2)取190-210重量份所述铜渣粉、85-105重量份水,加入0.1-0.2重量份减水剂,用立式球磨机湿磨35-45min,得到铜渣浆料,记作浆料a;
9.取100-120重量份所述矿渣粉、100-120重量份水,加入0.1-0.3重量份减水剂,湿磨15-25min,得到矿渣粉浆料,记作浆料b;
10.(3)使用破碎机,将废弃橡胶切割成橡胶碎屑;
11.(4)制备沥青涂层粗骨料:预先准备煤矸石粗骨料;而后将沥青置于钢盆中并用恒
温电磁炉融化,当沥青的温度达到100-110℃,然后将已备好的煤矸石粗骨料倒入钢盆中与沥青混合,最后用电动搅拌器将混合物搅拌3-8min,得到带有沥青涂层的粗骨料,即:沥青涂层粗骨料;
12.(5)取步骤(2)中制得的所述浆料a 10-20重量份、所述浆料b 30-40重量份、水泥50-60重量份,混合得到胶凝材料;
13.取步骤(3)中制得的所述橡胶碎屑20-60重量份与140-180重量份的铜尾矿混合,得到细骨料;
14.先将所述胶凝材料倒入搅拌机混合搅拌30-60s后,再放入1-2重量份的非晶态金属纤维,继续搅拌1-2min,最后倒入所述细骨料和280-320重量份的步骤(4)中制得的所述沥青涂层粗骨料以及0.5-2重量份减水剂,搅拌均匀。
15.2、如第1项所述的方法,其特征在于,步骤(1)中的所述铜渣和矿渣均是工业生产产生的废渣,铜渣颜色为灰黑色,比表面积为370-410m2/kg;矿渣中sio2和al2o3的含量分别是25-35%和5-15%。
16.3、如第1项所述的方法,其特征在于,步骤(2)和步骤(5)中所述的减水剂是聚羧酸和萘系减水剂按照重量比1:1混合而得到的混合减水剂。
17.4、如第1项所述的方法,其特征在于,步骤(2)中所述的立式球磨机的转速为350-450r/s。
18.5、如第1项所述的方法,其特征在于,步骤(2)中,所述铜渣浆料中的铜渣的中值粒径为1.5-2.3μm,所述矿渣粉浆料中的矿渣的中值粒径为3-4μm。
19.6、如第1项所述的方法,其特征在于,步骤(3)中,所述橡胶碎屑的粒径范围在1-4mm。
20.7、如第1项所述的方法,其特征在于,步骤(4)中,所述煤矸石粗骨料是通过将平均粒径为5-10mm和平均粒径10-16mm的两种煤矸石、以质量比为4:6的比例混合而成的,且沥青涂层粗骨料需隔离冷却至室温,沥青涂层厚度为80-120μm。
21.8、如第1项所述的方法,其特征在于,步骤(4)中,所述电动搅拌器的转速为150-190r/min。
22.9、如第1项所述的方法,其特征在于,步骤(5)中,所述非晶态金属纤维的等效直径为0.2-0.3mm,长径比为110-130,密度为7-7.5g/cm3。
23.10、由第1-9项中任意一项所述的方法制得的高强抗裂抗冲击混凝土。
24.本发明的有益效果如下:
25.1.采用湿磨处理铜渣和矿渣,可以有效地激发铜渣和矿渣潜在的胶凝特性,促进体系强度的生成,此外,矿渣含有高量的sio2和al2o3,保证了水化反应的持续进行。
26.2.矿渣作为体系辅助胶凝材料之一,可以改善橡胶碎屑与水泥基体的粘结界面。
27.3.湿磨处置的铜渣增强了铜渣颗粒与水化产物的粘结效果,显著改善了界面性能,在受到外力时,能够保障足够的力学性能,不至于发生破坏。
28.4.细骨料中含有的橡胶碎屑有利于吸收冲击能量,从而显著提高抗冲击能力,延缓了混凝土中裂缝的产生和扩展。
29.5.固废铜渣粉-矿渣粉胶凝材料的使用以及橡胶和铜尾矿、煤矸石粗骨料的使用,节约成本,保护生态环境。
30.6.非晶态金属纤维的重量轻,密度低,具有较大的比表面积和粗糙的表面,所以它们与水泥基体有很好的粘结性能,改善了胶凝材料和骨料的粘结界面;长径比较大的非晶态金属纤维显著改善混凝土的弯曲和拉伸性能,有效地抑制了裂缝的生成。
31.7.沥青涂层粗骨料可以有效地缓解和吸收巨大能量,缓解界面过渡区的应力集中,避免较多裂缝的产生,提高了抗冲击性能和抗裂性。
具体实施方式
32.为更好的理解本发明,下面的实施例是对本发明的进一步说明,但本发明的内容不仅仅局限于下面的实施例。
33.本发明通过将湿磨铜渣作为部分胶凝材料来替代传统的抗裂抗冲击混凝土的制备方法中仅使用硅灰作为胶凝材料,能满足高强混凝土的强度,并且由于使用的是铜渣废渣,因此减少了成本;湿磨矿渣替代部分水泥,补充了体系硅铝酸盐的含量;通过使用橡胶碎屑和铜尾矿来取代传统的抗裂抗冲击混凝土的制备方法中所使用的石英砂,可提高抗裂和抗冲击能力;非晶态金属纤维的使用,能改善混凝土的弯曲和拉伸性能,提高抗冲击能力;沥青涂层能进一步改善优化混凝土的和易性和抗冲击性能,从而能够制备节能环保的高强抗裂抗冲击混凝土。
34.本发明中的铜渣、矿渣、橡胶碎屑、铜尾矿和煤矸石从工业场中托运。减水剂可以为本领域常用的减水剂,目的是改善浆料的流动性,减少用水量;例如可以是聚羧酸减水剂和萘系减水剂按照重量比1:1混合而得到的减水剂,本发明实施例和对比例中使用的就是该减水剂,在市场上购得。非晶态金属纤维是在市场上购买的,沥青涂层粗骨料为自发研制。
35.实施例1:
36.一种高强抗裂抗冲击混凝土及其制备方法,步骤如下:
37.(1)利用滚筒干磨机将铜渣、矿渣(均为工业废渣、铜渣颜色为灰黑色,比表面积为390m2/kg;矿渣中sio2和al2o3的含量分别是31重量%和11重量%)干磨至粉状,分别得到铜渣粉和矿渣粉;
38.(2)取上述200重量份铜渣粉,100重量份水,加入0.1重量份减水剂,用立式球磨机(转速为400r/s)湿磨40min,得到铜渣浆料,记作浆料a;
39.取上述100重量份矿渣,100重量份水,加入0.2重量份减水剂,湿磨20min,得到矿渣粉浆料,记作浆料b;
40.其中,所述铜渣浆料中的铜渣的中值粒径为2μm,所述矿渣粉浆料中的矿渣的中值粒径为3.5μm;
41.(3)使用破碎机,将废弃橡胶切割成橡胶碎屑;其中,所述橡胶碎屑的粒径范围在1-4mm;
42.(4)制备沥青涂层粗骨料:预先准备煤矸石粗骨料,所述煤矸石粗骨料是通过将平均粒径为8mm和平均粒径13mm的两种煤矸石、以质量比为4:6的比例混合而成的;
43.而后将沥青置于钢盆中并用恒温电磁炉融化,当沥青的温度达到105℃,然后将已备好的煤矸石粗骨料倒入钢盆中与沥青混合,最后用电动搅拌器(转速为170r/min)将混合物搅拌5min,得到带有沥青涂层的粗骨料,即:沥青涂层粗骨料,其中,沥青涂层粗骨料需隔
离冷却至室温,沥青涂层厚度为80μm;
44.(5)取步骤(2)中制得的所述浆料a 20重量份,所述浆料b 30重量份,水泥50重量份,混合得到胶凝材料;
45.取步骤(3)中制得的所述橡胶碎屑20重量份与180重量份铜尾矿混合,得到细骨料;
46.先将所述胶凝材料倒入搅拌机混合搅拌30s后,再放入1重量份的非晶态金属纤维(其等效直径为0.25mm,长径比为120,密度为7.2g/cm3),继续搅拌2min,最后倒入所述细骨料和300重量份的步骤(4)中制得的所述沥青涂层粗骨料以及1重量份减水剂,搅拌均匀。
47.实施例2:
48.一种高强抗裂抗冲击混凝土及其制备方法,步骤如下:
49.(1)利用滚筒干磨机将铜渣、矿渣(均为工业废渣、铜渣颜色为灰黑色,比表面积为390m2/kg;矿渣中sio2和al2o3的含量分别是25重量%和5重量%)干磨至粉状,分别得到铜渣粉和矿渣粉;
50.(2)取上述190重量份铜渣粉,85重量份水,加入0.2重量份减水剂,用立式球磨机(转速为350r/s)湿磨35min,得到铜渣浆料,记作浆料a;
51.取上述110重量份矿渣,110重量份水,加入0.1重量份减水剂,湿磨15min,得到矿粉浆料,记作浆料b;
52.其中,所述铜渣浆料中的铜渣的中值粒径为1.5μm,所述矿渣粉浆料中的矿渣的中值粒径为3μm;
53.(3)使用破碎机,将废弃橡胶切割成橡胶碎屑;其中,所述橡胶碎屑的粒径范围在1-4mm;
54.(4)制备沥青涂层粗骨料:预先准备煤矸石粗骨料,所述煤矸石粗骨料是通过将平均粒径为5mm和平均粒径10mm的两种煤矸石、以质量比为4:6的比例混合而成的;
55.而后将沥青置于钢盆中并用恒温电磁炉融化,当沥青的温度达到100℃,然后将已备好的煤矸石粗骨料倒入钢盆中与沥青混合,最后用电动搅拌器(转速为150r/min)将混合物搅拌3min,得到带有沥青涂层的粗骨料,即:沥青涂层粗骨料,其中,沥青涂层粗骨料需隔离冷却至室温,沥青涂层厚度为100μm;
56.(5)取步骤(2)中制得的所述浆料a 15重量份,所述浆料b 35重量份,水泥55重量份,混合得到胶凝材料;
57.取步骤(3)制得的所述橡胶碎屑30重量份与170重量份铜尾矿混合,得到细骨料;
58.先将所述胶凝材料倒入搅拌机混合搅拌45s后,再放入2重量份的非晶态金属纤维(其等效直径为0.2mm,长径比为110,密度为7g/cm3),继续搅拌1min,最后倒入所述细骨料和280重量份的步骤(4)中制得的所述沥青涂层粗骨料以及0.5重量份减水剂,搅拌均匀。
59.实施例3:
60.一种高强抗裂抗冲击混凝土及其制备方法,步骤如下:
61.(1)利用滚筒干磨机将铜渣、矿渣(均为工业废渣、铜渣颜色为灰黑色,比表面积为410m2/kg;矿渣中sio2和al2o3的含量分别是35重量%和15重量%)干磨至粉状,分别得到铜渣粉和矿渣粉;
62.(2)取上述210重量份铜渣粉,105重量份水,加入0.2重量份减水剂,用立式球磨机
(转速为450r/s)湿磨45min,得到铜渣浆料,记作浆料a;
63.取上述120重量份矿渣,120重量份水,加入0.3重量份减水剂,湿磨25min,得到矿粉浆料,记作浆料b;
64.其中,所述铜渣浆料中的铜渣的中值粒径为2.3μm,所述矿渣粉浆料中的矿渣的中值粒径为4μm;
65.(3)使用破碎机,将废弃橡胶切割成橡胶碎屑;其中,所述橡胶碎屑的粒径范围在1-4mm;
66.(4)制备沥青涂层粗骨料:预先准备煤矸石粗骨料,所述煤矸石粗骨料是通过将平均粒径为10mm和平均粒径16mm的两种煤矸石、以质量比为4:6的比例混合而成的;
67.而后将沥青置于钢盆中并用恒温电磁炉融化,当沥青的温度达到110℃,然后将已备好的煤矸石粗骨料倒入钢盆中与沥青混合,最后用电动搅拌器(转速为190r/min)将混合物搅拌8min,得到带有沥青涂层的粗骨料,即:沥青涂层粗骨料,其中,沥青涂层粗骨料需隔离冷却至室温,沥青涂层厚度为120μm;
68.(5)取步骤(2)中制得的所述浆料a 10重量份,所述浆料b 40重量份,水泥60重量份,混合得到胶凝材料;
69.取步骤(3)制得的所述橡胶碎屑60重量份与140重量份铜尾矿混合,得到细骨料;
70.先将所述胶凝材料倒入搅拌机混合搅拌60s后,再放入2重量份的非晶态金属纤维(其等效直径为0.3mm,长径比为130,密度为7.5g/cm3),继续搅拌1min,最后倒入所述细骨料和320重量份的步骤(4)中制得的所述沥青涂层粗骨料以及2重量份减水剂,搅拌均匀。
71.实施例4:
72.在实施例4中,除了在步骤(5)中,取步骤(3)中制得的所述橡胶碎屑40重量份与160重量份铜尾矿混合后作为细骨料、且使用1.5重量份的非晶态金属纤维以外,其他方法与实施例1相同,制得高强抗裂抗冲击混凝土。
73.实施例5:
74.在实施例5中,除了在步骤(5)中,取步骤(3)中制得的所述橡胶碎屑40重量份与160重量份铜尾矿混合后作为细骨料、且使用2重量份的非晶态金属纤维以外,其他方法与实施例1相同,制得高强抗裂抗冲击混凝土。
75.实施例6:
76.在实施例6中,除了在步骤(4)中制得的沥青涂层粗骨料中的沥青涂层厚度为100μm、且在步骤(5)中取步骤(3)中制得的所述橡胶碎屑40重量份与160重量份铜尾矿混合后作为细骨料以外,其他方法与实施例3相同,制得高强抗裂抗冲击混凝土。
77.实施例7:
78.在实施例7中,除了在步骤(5)中取步骤(3)中制得的所述橡胶碎屑40重量份与160重量份铜尾矿混合后作为细骨料以外,其他方法与实施例3相同,制得高强抗裂抗冲击混凝土。
79.对比例1:
80.对比例1,用于与实施例5对比,说明采用不含沥青涂层的煤矸石粗骨料时,制得的高强抗裂抗冲击混凝土的抗压强度、抗冲击性能和抗裂性较差。
81.在对比例1中,除了省略步骤(4)、并且在步骤(5)中添加不含沥青涂层的煤矸石粗
骨料以外,其他方法与实施例5相同,制得高强抗裂抗冲击混凝土。
82.对比例2:
83.对比例2,用于与实施例5对比,说明细骨料中未使用橡胶碎屑时,制得的高强抗裂抗冲击混凝土的抗压强度、抗冲击性能和抗裂性较差。
84.在对比例2中,除了省略步骤(3)、并且在步骤(5)中未添加橡胶碎屑、而是采用200重量份的铜尾矿作为细骨料以外,其他方法与实施例5相同,制得高强抗裂抗冲击混凝土。
85.对比例3:
86.对比例3,用于与实施例5对比,说明未使用非晶态金属纤维时,制得的高强抗裂抗冲击混凝土的抗压强度、抗折强度、拉伸强度、抗冲击性能和抗裂性都比较差。
87.在对比例3中,除了在步骤(5)中未添加非晶态金属纤维以外,其他方法与实施例5相同,制得高强抗裂抗冲击混凝土。
88.对比例4:
89.对比例4,用于与实施例5对比,说明现有技术中未使用浆料a和浆料b时,制得的高强抗裂抗冲击混凝土的抗压强度、抗折强度、拉伸强度、抗冲击性能和抗裂性都比较差。
90.在对比例4中,除了省略步骤(1)和步骤(2)、并且在步骤(5)中未添加浆料a和浆料b以外,其他方法与实施例5相同,制得高强抗裂抗冲击混凝土。
91.下面对实施例1~7和对比例1~4所制备的高强抗裂抗冲击混凝土试样进行如下实验,实验结果如表1所示。
92.28d抗压强度、28d抗折强度、28d抗拉强度:根据《混凝土物理力学性能试验方法标准》(gb/t50081-2019)对试样进行抗压、抗折和抗拉实验。试样在标准养护室养护28d后,取每组测试三个样品,记录其平均值作为28d抗压、抗折和抗拉强度。
93.初始破坏下的冲击能量、最终破坏下的冲击能量:制作三个圆柱形(直径150mm、高度65mm)试样,在标准养护室养护28d之后进行实验。在实验中,用直径64mm、重4.5kg的锤球从457mm高度向试样施加重复冲击荷载。将首次出现裂纹所用锤击次数记作n1,最终破坏所用锤击数记作n2。初始破坏下的冲击能量,根据方程式ui=n1mgh计算;最终破坏下的冲击能量根据方程式uu=n2mgh计算。其中,方程式中的mg为试样的重量、h为试样自由落体的高度。
94.表1
[0095][0096]
从以上数据可以看出,与利用现有技术制备的高强抗裂抗冲击混凝土的对比例4的方法相比,在制备实施例1-7的高强抗裂抗冲击混凝土的本发明方法中,通过铜渣和矿渣等工业固废的利用,减少了水泥的用量,节约了经济成本,同时保护了自然资源。湿磨处理方式更大限度地提高了铜渣和矿渣的火山灰活性,使得抗冲击混凝土有更高的抗压强度、抗折强度和抗拉强度。
[0097]
另外,从表1中还可以看出,与实施例5相比,对比例1中采用不含沥青涂层的粗骨料,不能有效缓解和吸收巨大能量,缓解界面过渡区的应力集中,这也会造成较多裂缝的产生,降低了抗冲击性能和抗裂性,具体体现在对比例1制得的高强抗裂抗冲击混凝土的抗压强度、抗冲击性能和抗裂性较差。
[0098]
与实施例5相比,对比例2中细骨料中未含有橡胶碎屑,不利于吸收冲击能量,造成了混凝土中裂缝的产生和扩展,抗冲击能力下降,具体体现在对比例2制得的高强抗裂抗冲击混凝土的抗压强度、抗冲击性能和抗裂性较差。
[0099]
与实施例5相比,对比例3中未掺非晶态金属纤维,不能改善胶凝材料和骨料的粘结界面、以及不能更好地提高混凝土的弯曲和拉伸性能,无法避免更多微裂缝的生成,导致对比例3制得的高强抗裂抗冲击混凝土的所有性能都不好。
[0100]
与实施例5相比,未使用铜渣浆料(即浆料a)和矿渣粉浆料(即浆料b)的对比例4,不能改善胶凝材料和骨料的粘结界面、以及不能更好地提高混凝土的弯曲和拉伸性能,无法避免更多微裂缝的生成,导致对比例4制得的高强抗裂抗冲击混凝土的所有性能都不好。
[0101]
以上所述是本发明的优选实施例方式而已,当然不能以此来限定本发明之权利范围,应当指出,对于本技术领域的普通技术人员来说,在不脱离本发明原理的前提下,还可以做出若干改进和变动,这些改进和变动也视为本发明的保护范围。