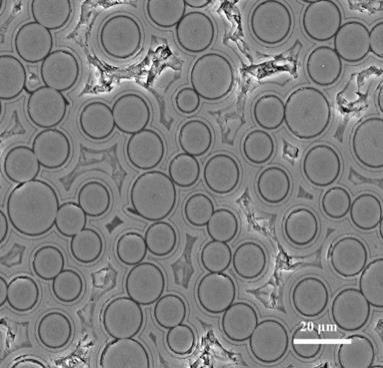
一种高性能sicf/sic复合材料的制备方法
技术领域
1.本发明总体地涉及复合材料技术领域,具体地涉及一种高性能sicf/sic复合材料的制备方法。
背景技术:2.为了提高航空发动机的热效率这一航空工业的永恒目标,提高发动机的工作温度有着巨大的推动力。传统的镍基高温合金温度上限约为1100℃,已经不能满足新型航空发动机使用温度持续升高的要求,因此,开发一种低密度、能够承受更高温度的新型结构材料成为发展高性能发动机的关键和基础,并将接替高温合金和难熔金属材料。
3.sicf/sic复合材料是理想的可以替代高温合金的材料,在热端构件如燃烧室、涡轮叶片、导向器叶片、涡轮盘等中已经得到应用。sicf/sic 复合材料具有低的密度,高比强度和比模量,优异的高温力学性能、抗氧化及热冲击性能、高可靠性和损伤容限,不但可以有效提高航空发动机的进气温度,还能使构件减重50%以上,这对于提高航空发动机的推重比,推动自主研发新一代航空发动机意义重大。
4.目前sicf/sic复合材料常用的制备工艺有:先驱体浸渍裂解法 (precursor infiltration and pyrolysis,pip)、化学气相渗透法 (chemical vapor infiltration,cvi)以及反应熔渗法(reactive melt infiltration,rmi)。
5.先驱体浸渍裂解法是利用抽真空的办法排除纤维预制件中的空气,然后将先驱体通过浸渍的方法填充到预制件中,交联固化后进行高温裂解。多次浸渍裂解后实现材料的致密化。
6.化学气相渗透法将纤维预制件置于沉积炉中,通过压差法将裂解气输送至预制件,在预制件内部孔隙壁上沉积生成的固体产物(成晶粒子),该产物经表面扩散进入晶格点阵,使孔隙壁表面的厚度逐渐增加以实现致密化。
7.反应熔渗法通过利用真空中的毛细作用原理,实现si与c的反应生成sic实现致密化。
8.其中,pip工艺能制备形状复杂的构件,且制备温度较低对纤维损伤小;但裂解产物为无定形sic,过程中有小分子逸出,孔隙率高。cvi工艺可制备复杂构件,产物为高纯度、高结晶性的sic;但不适合制备厚壁构件,设备复杂、制备周期长、成本高,不能填充纤维束间的大孔。rmi工艺快捷简单,成本较低,且孔隙率低;但残余si的存在损害了高温性能,另外制备温度高,对纤维损伤大。
9.sicf/sic复合材料的性能与其制备工艺密切相关,对用于新型航空发动机热端部件的sicf/sic复合材料,必须要求复合材料具有高的稳定性和可靠性,优异的耐高温性能,以及低的制备成本和短的制备周期。
10.目前采用传统工艺制备的sicf/sic复合材料孔隙率高,且孔隙率分布不均匀,显微结构不均匀,导致性能稳定差,离散性高,且制备周期长,成本高。因此,亟待发展一种高密度、高稳定性、组织结构均匀、力学性能优良、制备周期短的sicf/sic复合材料制备方法。
技术实现要素:11.本发明要解决的技术问题是克服现有技术的不足,提出了一种高性能sicf/sic复合材料的制备方法。本发明产品密度高、稳定性高、组织结构均匀、力学性能优良,满足其在航空发动机热端部件上的应用需求,本发明制备方法周期短,工艺简便。
12.本发明的技术方案是,一种高性能sicf/sic复合材料的制备方法,sicf/sic复合材料以sic纤维为增强体,以碳化硅为基体,所述sic纤维的体积分数为35-45%;所述复合材料的孔隙率在10.0%-14.0%范围内、密度在2.36-2.40g/cm3范围内、力学性能在430-500mpa范围内;离散性在5%范围内,该方法包括以下步骤:s1、sic纤维预制件真空条件下进行高温热处理,得到除胶后的预制件;s2、将s1中得到的预制件置于化学气相沉积炉中,以丙烯为源气,氢气为载气,在sic纤维表面沉积裂解碳界面层;s3、将s2中处理后的预制件置于碳化硅化学气相沉积炉中,以甲基三氯硅烷为先驱体,氢气为载气,氩气为稀释气体,化学气相沉积 sic基体,得到第一密度中间体;s4、将固态聚碳硅烷与二甲苯配制成sic先驱体溶液;s5、将第一密度中间体真空浸渍于s4制得的sic先驱体溶液中,取出晾干后进行交联固化,然后在氩气或氮气气氛条件下于进行裂解,之后随炉冷却,得到先驱体浸渍裂解 sic基体;s6、重复s5周期5-7次,得到第二密度中间体;s7、将第二密度中间体通过机械辅助加压浸渍在聚碳硅烷溶液中,将经过浸渍后的第二密度中间体连同盛先驱体溶液容器一起取出,一起进行原位交联固化,然后在氩气或氮气气氛条件下进行裂解,之后随炉冷却;机械辅助压力为50-250mpa,保压时间10-30min,浸渍的时间为5-8h;s8、重复s7周期2-4次,得到所述高性能sicf/sic复合材料。
13.进一步的,上述步骤s1中,高温热处理条件:温度500~800℃,保温时间30min~90min。
14.进一步的,上述步骤s2中,丙烯流量140-160ml/min,氢气流量140-160ml/min,沉积温度900-1050℃,沉积压力1.5-2kpa,沉积时间10-15h;所得裂解碳界面层最终厚度为200-400nm。
15.进一步的,上述步骤s3中,氢气流量280-320ml/min,氩气流量180-220ml/min,在1050-1100
ꢀ°
c温度下,1.3-1.5 kpa压力条件下沉积cvi sic基体,沉积时间100-160h;所得第一中间体密度为1.8-1.9g/cm3。
16.进一步的,上述步骤s4中,固态聚碳硅烷与二甲苯按照(1:1)-(1:2)的质量比配制sic先驱体溶液。
17.进一步的,上述步骤s6中,第二中间体密度为2.20-2.25g/cm3。
18.进一步的,上述步骤s5中:浸渍的时间为5-8h;步骤s5和s7原位交联固化的温度140-160℃保温时间为:3-5h;所述裂解的温度为1000-1200℃,保温时间为1-2h。
19.本发明相比现有技术的先进性在于:1、相比于现在有技术,发明制得的复合材料密度更高,孔隙率更低,大幅的提高弯曲强度,且均匀性好离散性低。孔隙率可从现有技术的高于15%降低到14%以下,弯曲强度相
比于现在技术能提高30%左右,且离散性能控制在5%以下。
20.2、本发明针对目前采用传统工艺制备的sicf/sic复合材料孔隙率高,一般高于15%,且孔隙率分布不均匀,显微结构不均匀,导致力学性能稳定差,离散性大于10%等不足,在cvi+pip联用工艺的基础上,进一步采用机械辅助加压浸渍的方法,以期制备出致密度高,组织结构均匀,性能稳定离散性低的sicf/sic复合材料。
21.3、本发明制备方法中首先采用cvi工艺沉积sic基体,通过控制沉积速率,使得纤维束内的小孔能被有效填充,当此中间体密度达到1.8-1.9g/cm3时,再通过pip工艺裂解的sic基体来填充纤维束间的大孔。通过cvi+pip工艺的联用可以有效降低孔隙率。
22.4、本发明方法针对pip裂解的sic基体是无定型的,在pip的过程中很容易堵塞先驱体进入预制件内部的通道,不可避免地会在预制件内部形成一定的闭孔,影响复合材料的性能等技术问题,在cvi+pip工艺之后,利用机械辅助加压进行浸渍的方式,来打通堵塞的闭孔,使先驱体能够进入闭孔内部,这样可以提高致密度,降低闭孔率,提高纤维组织结构的均匀性,不仅可以提高其力学性能,还可以提高其稳定性。
23.5、本发明方法采用的机械辅助加压浸渍方式,大大提高了致密度,降低了闭孔率,提高了组织结构的均匀性及稳定性。
附图说明
24.从下面结合附图对本发明实施例的详细描述中,本发明的这些和/或其它方面和优点将变得更加清楚并更容易理解,其中:图1本发明实施例1制得的高性能sicf/sic复合材料截面电镜图片;图2本发明实施例1与对比例1中s6步骤中pip过程增重对比图;图3本发明实施例1、对比例1以及对比例2制备的sicf/sic复合材料密度和弯曲强度对比图。
具体实施方式
25.为了使本领域技术人员更好地理解本发明,下面结合附图和具体实施方式对本发明作进一步详细说明。
26.实施例1:一种高性能sicf/sic复合材料的制备方法,包括以下步骤:s1、2.5d编织方式的 sic纤维预制件(纤维体积分数为45%)在真空条件下, 600℃保温1h,进行高温除胶处理;s2、在s1中得到的预制件置于化学气相沉积炉中,以丙烯(c3h6)为源气,氢气(h2)为载气,丙烯流量150ml/min,氢气流量150ml/min,沉积温度900-1050℃,沉积压力1.5-2kpa,在sic纤维表面沉积裂解碳(pyc)界面层,界面层厚度约为200nm;s3、将s2中得到的预制件置于cvi sic沉积炉中,以甲基三氯硅烷(mts)为先驱体,采用鼓泡的方式将mts带入炉腔,氢气(h2)作为载气,氩气(ar)作为稀释气体,氢气流量300ml/min,氩气流量200ml/min,在1075
ꢀ°
c温度下,1.4 kpa压力的工艺条件下沉积cvi sic基体,沉积135-145h,获得的中间体密度为1.85g/cm3;s4、将固态聚碳硅烷与二甲苯按质量比1:1的比例制备sic先驱体;
s5、将s3制得的中间体真空浸渍于s4制得的sic先驱体溶液中,浸渍8h,取出晾干后,在150℃保温4h进行交联固化,然后在氩气气氛条件下,在1200℃保温1h进行裂解,之后随炉冷却,得到pip sic基体,重复pip周期5次;s6、将s5得到中间体,通过机械辅助加压浸渍在聚碳硅烷溶液中,压力200mpa,保压10min,将样品与sic先驱体溶液一起取出,一起在150℃保温4h进行原位交联固化,然后在氩气气氛条件下,在1200℃保温1h进行裂解,之后随炉冷却,重复pip4个周期,得到高密度sicf/sic复合材料。
27.对比例1(不采用机械辅助加压浸渍)对比例1与实施例1的不同之处在于:步骤在s6中,不采用机械辅助加压浸渍,而是采取与步骤s5相同的浸渍方式进行4次pip增密,其余步骤同实施例1。
28.对比例2对比例2与实施例1的不同之处在于:不进行步骤s6中的操作,其余步骤同实施例1。
29.图1为实施例1制得的高密度sicf/sic复合材料截面电镜图片;图2为实施例1与对比例1中s6步骤中pip过程增重曲线对比图;图3给出了实施例1、对比例1以及对比例2制备的sicf/sic复合材料密度和弯曲强度对比图。
30.由图2可知,实施例1中pip过程中增重效率更高,也即是通过机械辅助加压浸渍后,得到致密化效果更好,说明机械辅助加压浸渍以及原位固化可以更好的促进复合材料致密化过程。
31.从图3中可知实施例1、对比例1以及对比例2制备的sicf/sic复合材料密度分别为2.37g/cm3,2.33g/cm3和2.25g/cm3,弯曲强度分别为472.8
±
10.1mpa,351.4
±
18.4mpa和232.4
±
25.9mpa,通过排水法测得的开孔率分别为13.6%,15.9%和22.7%。对比可知通过机械辅助加压可以使制得的复合材料密度更高,孔隙率更低,大幅的提高弯曲强度,且均匀性好离散性低。从图1的sem图片中也可以看出,复合材料显微组织结构均匀且致密。
32.以上已经描述了本发明的各实施例,上述说明是示例性的,并非穷尽性的,并且也不限于所披露的各实施例。在不偏离所说明的各实施例的范围和精神的情况下,对于本技术领域的普通技术人员来说许多修改和变更都是显而易见的。因此,本发明的保护范围应该以权利要求的保护范围为准。