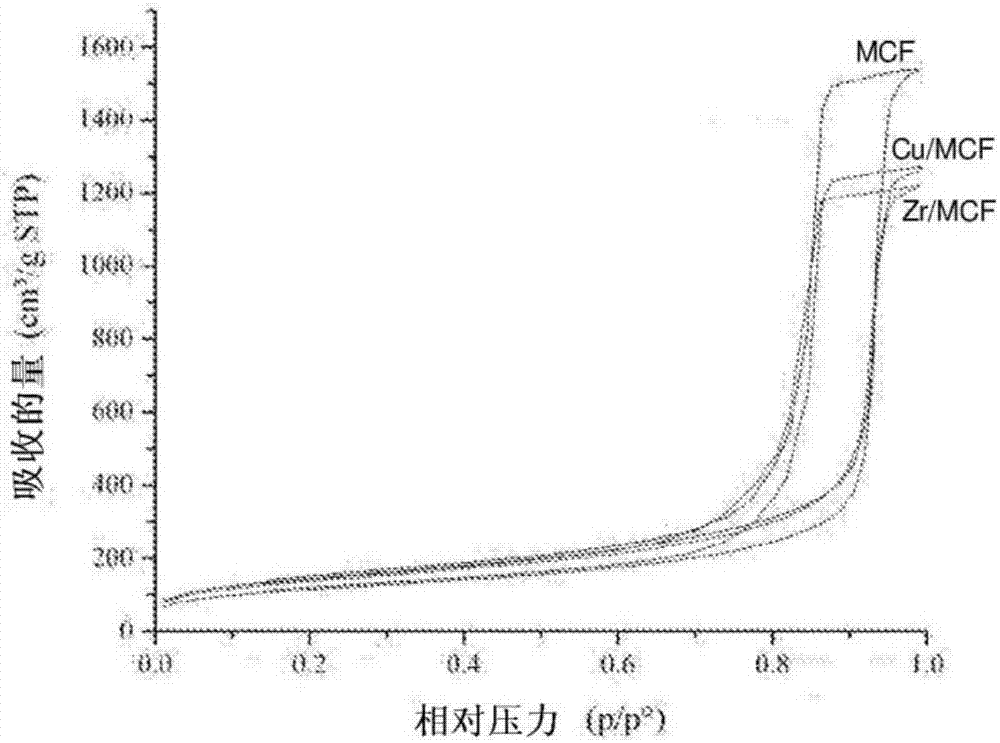
本发明通常涉及化合物的制备,更具体地说,涉及任选取代的烯烃的制备。
背景技术:
:开发将可再生的碳中性原料如生物质转化为有价值的化学物质的化学反应或工艺是21世纪最紧迫的问题之一。这些反应将减少我们对化石燃料的依赖,并最终为环境和经济带来益处。1,3-丁二烯(bd)是用于生产商业聚合物如苯乙烯-丁二烯橡胶的高价值化学单体。bd可以直接或通过两个或更多个步骤工艺从乙醇转化而来。近来,通过石油气或石脑油的蒸汽裂解从油中提取bd。然而,随着原油价格的上涨以及衍生自廉价生物质的化学品价格的下跌,近年来诸如乙醇-至-丁二烯转化的反应再次出现。在乙醇转化为bd中已经使用了几种催化剂系统。然而,乙醇的转化率和bd的选择性在实际工业应用中并不理想。因此,需要提供克服或至少改善上述一个或多个缺点的方法和系统。发明概述根据第一方面,提供了一种制备任选取代的烯烃的方法,包括以下步骤:在第一组反应条件下,在包含负载于多孔二氧化硅基颗粒上的第一催化剂的第一反应区中,使任选取代的醇脱氢以形成任选取代的羰基;在与第一组反应条件不同并且被选择用以形成任选取代的烯烃的第二组反应条件下,在第二反应区中,转化来自第一反应区的任选取代的醇和任选取代的羰基,其中所述第二反应区包含负载在多孔二氧化硅基颗粒上的第二催化剂。根据第二方面,提供了一种用于制备任选取代的烯烃的系统,所述系统包括:第一反应区,其具有用于使任选取代的醇脱氢以形成任选取代的羰基的第一催化剂;以及第二反应区,其具有用于转化来自第一反应区的任选取代的醇和任选取代的羰基以形成任选取代的烯烃的第二催化剂;其中所述第一和第二催化剂负载在多孔二氧化硅基颗粒上。定义本文使用的以下词语和术语应具有以下所述的含义:如本文所用,术语“泡沫”,是指由介孔组成的颗粒,所述介孔由与介孔相比尺寸较小的均匀孔(称为窗孔)相互连接,由此形成三维多孔系统或网络。这种泡沫颗粒中的介孔的孔径倾向于在5nm至50nm的范围内,并且泡沫颗粒的尺寸倾向于在至少1um或1um-100um的范围内。窗孔的尺寸可以是至少2nm或2nm-100nm的范围内。介孔的尺寸与窗孔的尺寸之比可以在12:1至1.1:1之间或其它一些比例,只要介孔的孔径大于窗孔。如本文所用,术语“烯烃”可与术语“烯”互换使用,指含有通过双键连接的一对或多对碳原子的任何不饱和烃。烯烃可以是环状或非环状(脂族)烯烃,其中双键分别位于形成环状(封闭环)基团或开链基团的一部分的碳原子之间。“烯烃”也可以是单烯烃、二烯烃、三烯烃等,其中每个分子的双键数分别是一个、两个、三个或另一些数目。在适用的情况下,每个双键的取向可以独立地为e、z、顺式或反式立体化学。本文所用的术语“二烯”是指含有两个碳双键,特别是具有至少4个碳原子的不饱和烃,例如但不限于c4-c20二烯或具有落在这个范围内的任何碳原子数的二烯。因此,“二烯”可以与术语“二烯烃”互换使用。同样,在适用的情况下,关于每个双键的取向可以独立地为e、z、顺式或反式立体化学。本文所用的术语“任选取代的”是指该术语所指的基团可以是未取代的,或可以被一个或多个独立地选自以下的基团取代:-c1-c20-烷基、c1-c20-烯基,-c1-c20-炔基、-c3-c20-环烷基、-c5-c20-环烯基,在环中具有1-5个选自n、o和s的杂原子的-c5-c20-杂环烷基、卤素、-c1-c20-卤代烷基。作为基团或基团的一部分的“烷基”是指直链或支链脂族烃基,特别是但不限于,至少一个碳原子、或c1–c20烷基、c1-c10烷基、c1-c6烷基或落在这些范围内的任何碳原子数。合适的直链和支链c1-c6烷基取代基的实例包括甲基、乙基、正丙基、2-丙基、正丁基、仲丁基、叔丁基、己基等。该基团可以是末端基团或桥联基团。作为基团或基团的一部分的“烯基”表示在正链中含有至少一个碳-碳双键的脂族烃基,其可以是直链或支链的,具有但不限于,至少2个碳原子、2-20个碳原子、2-10个碳原子、2-6个碳原子或落在这些范围内的任何碳数目。该基团可以在正链中含有多个双键,并且在适用的情况下,独立地为e、z、顺式或反式。示例性烯基包括但不限于乙烯基、丙烯基、丁烯基、戊烯基、己烯基、庚烯基、辛烯基和壬烯基。该基团可以是末端基团或桥联基团。本文所用的术语“炔基”在其含义中包括直链或支链不饱和脂族烃基,具有但不限于,至少2个碳原子或2至20个碳原子,并且在碳链中任意位置具有至少一个三键。炔基的实例包括但不限于乙炔基、1-丙炔基、1-丁炔基、2-丁炔基、1-甲基-2-丁炔基、3-甲基-1-丁炔基、1-戊炔基、1-己炔基、甲基戊炔基、1-庚炔基、2-庚炔基、1-辛炔基、2-辛炔基、1-壬炔基、1-癸炔基等。除非另有说明,“环烷基”是指每个环含有至少3个碳原子或3-20个碳原子的饱和单环碳环或稠环多环碳环或螺环多环碳环,如环丙基、环丁基、环戊基、环己基等。它包括单环系统如环丙基和环己基,双环系统如十氢化萘,以及多环系统如金刚烷。环烷基通常是c3-c20烷基。该基团可以是末端基团或桥联基团。本文所用的术语“环烯基”是指环状不饱和脂族基团,并且在其含义中包括具有至少3个碳原子或3-20个碳原子并在烷基链中的任意位置具有至少一个双键(在适用的情况下为e、z、顺式或反式立体化学)的单环、双环、多环或稠合多环烃基。环烯基的实例包括但不限于环丙烯基、环戊烯基、环己烯基等。本文所用的术语“杂环烷基”在其含义中包括具有至少3个碳原子或3-20个环原子的一价(“杂环烷基”)和二价(“杂环亚烷基”)、饱和的单环、双环、多环或稠环烃基,其中1-5个环原子是选自o、n、nh或s的杂原子。实例包括吡咯烷基、哌啶基、奎宁环基、氮杂环丁烷基、吗啉基、四氢噻吩基、四氢呋喃基、四氢吡喃基等。本文所用的术语“卤代”或其变化形式如“卤化物”或“卤素”是指氟、氯、溴和碘。“卤代烷基”是指如本文所定义的烷基,其中一个或多个氢原子被选自由氟、氯、溴和碘所组成的组的卤素原子替代。卤代烷基通常具有式cnh(2n+1-m)xm,其中每个x独立地选自f、cl、br和i。在这种基团中,n通常为1-20、1-10、或1-6。m通常为1-10、1-6或1-3。卤代烷基的实例包括氟甲基、二氟甲基和三氟甲基。本文所用的术语醇是指具有一个或多个羟基(-oh)部分的烃,所述烃具有至少一个碳原子、1-20个碳原子、2-20个碳原子、2-10个碳原子或落在任意这些范围之内的任意数目的碳原子。示例性的醇可以包括但不限于乙醇、丙醇、丁醇、戊醇或其它取代的醇。本文所用的术语“羰基”是指具有r1-c(=o)-r2基团的烃,其中r1和r2可以独立地为氢或任何如上定义的任选的取代基。这样的羰基可包括醛或酮。本文使用的乙醇(etoh)转化率如下导出:本文使用的丁二烯(bd)选择性如下导出:本文使用的重时空速(whsv)如下导出:其中反应器1指第一反应区,反应器2指第二反应区。单词“基本上”不排除“完全”,例如,“基本上不含”y的组合物可以完全不含y。如果需要,可以从本发明的定义中省略“基本上”一词。除非另有规定,术语“包括”和“包含”及其语法变体旨在表示“开放”或“包容性”的语言,使得它们包括所提及的元素但也允许包含另外的未被提及的元素。如本文所用,在制剂组分浓度的上下文中,术语“约”通常是指所述值的+/-5%,更典型地为所述值的+/-4%,更典型地为所述值的+/-3%,更典型地为所述值的+/-2%,甚至更典型地为所述值的+/-1%,甚至更典型地为所述值的+/-0.5%。在整个本公开中,某些实施方案可能以范围的形式公开。应当理解,范围形式的描述仅仅是为了方便和简洁,不应被解释为对所公开范围的大小的僵化限制。因此,对一范围的描述应认为已经具体公开了所有可能的子范围以及所述范围内的各个数值。例如,对诸如1-6这一范围的描述应认为具体公开了1-3、1-4、1-5、2-4、2-6、3-6等的子范围,以及所述范围内的各个值,例如1、2、3、4、5和6。不管范围的宽度如何,上述均使用。某些实施方案还可能在本文中被广泛地和一般性地描述。落入一般性公开内的每个较窄的种类和次一般性类别也构成了本公开的一部分。这包括实施方案的一般性描述,该描述具有从该种类中除去任意内容的附带条件或负面限定,而不管本文中是否具体叙述了去除的材料。实施方案的详细公开现在将公开用于制备任选取代的烯烃的方法的示例性、非限制性实施方案。在一个实施方案中,提供了一种制备任选取代的烯烃的方法,包括以下步骤:在第一组反应条件下,在包含负载于多孔二氧化硅基颗粒上的第一催化剂的第一反应区中,使任选取代的醇脱氢以形成任选取代的羰基;在与第一组反应条件不同并且被选择用以形成任选取代的烯烃的第二组反应条件下,在第二反应区中,转化来自第一反应区的任选取代的醇和任选取代的羰基,其中所述第二反应区包含负载在多孔二氧化硅基颗粒上的第二催化剂。醇至烯烃反应的一种示例性机理,以乙醇至丁二烯反应作为代表,示于图1。该机理可能涉及通过脱氢途径将乙醇转化为乙醛(图1中的步骤1),然后进行乙醛的醛醇缩合,然后脱水为巴豆醛(图1中的步骤2),其与乙醇经历meerwein-ponndorf-verley还原成为巴豆醇,然后脱水得到丁二烯(图1的步骤3)。有利地,作为进入到图1第3个步骤的反应进料的乙醛(或巴豆醛)与乙醇的比例可能提高总的丁二烯产率。此外,为了减少生产、纯化和/或储存乙醛的碳足迹,之后在独立的工艺过程中将其与乙醇混合,可以如本文所述在单一的工艺过程中原位产生固定的、最佳比例的乙醛与乙醇以用作图1第3个步骤的反应进料,从而提供更具有成本有效性和绿色的反应。因此,在所公开的方法中,可以控制脱氢步骤的反应条件以获得最佳的醇与羰基摩尔比。有利地,可优化最终烯烃产物的选择性和总收率。第一反应区中的第一组反应条件可包括控制提供给第二反应区的醇/羰基摩尔比。可以控制提供给第二反应区的任选取代的醇和任选取代的羰基之间的比例,以获得所产生的任选取代的烯烃的最佳选择性。可以通过固定第二反应的温度同时改变第一反应的温度来改变任选取代的醇和任选取代的羰基之间的比例。可以通过固定第二反应区内的温度同时控制第一反应区内的温度来控制任选取代的醇和任选取代的羰基之间的比例。可以通过分析在产生了最高烯烃选择性的那一特定温度下的第一反应输出气流来获得醇/羰基的最佳比例。通过用于脱氢反应的强力催化剂提供的对醇/羰基比例的控制和/或控制脱氢反应温度条件提供了改进的方法。所公开的催化剂可以基本上分散在多孔二氧化硅基载体上,所述载体可具有相对较大的纳米级的孔。有利地,优化第二反应区的进料以及催化剂和载体材料的制备以增强醇转化率和烯烃选择性。脱氢步骤可以在适于提高对羰基的选择性、同时降低对其它副产物的选择性的条件下进行。第一组反应条件可包括在100℃至500℃、或100℃至400℃、或200℃至320℃的温度、或在这些范围内的任何温度进行脱氢步骤。脱氢步骤可在约220℃、或约225℃、或约230℃、或约235℃、或约240℃进行。在这些温度下,所得任选取代的烯烃的选择性可被最大化且不损害任选取代的醇原料的转化百分比。醇原料可以以适于优化其与第一负载型催化剂的接触的形式提供给第一反应区。醇原料可以以蒸气形式提供。醇原料可以在水溶液中提供给第一反应区。醇原料可作为干原料提供给第一反应区。醇可以是基本上纯的醇,由此醇原料中的水含量可忽略不计。醇进料中的水含量可小于0.05v/v%,或小于0.01v/v%,或小于0.005v/v%。醇进料中的水含量可小于20v/v%,或小于15v/v%,或小于10v/v%。醇原料可以是水含量为10vol%的含水醇。第一负载催化剂可包括一元金属催化剂、二元金属催化剂、三元金属催化剂或它们的任何对应的金属氧化物催化剂。用于该第一负载型催化剂的金属或金属氧化物可以选自由如下所组成的组:银、金、铜、锌、铝、镁、锆、钽、钛、钒及它们的组合。该第一负载型催化剂可以是铜-mcf负载型催化剂。第一反应区可以作为包含所述第一负载型催化剂的填充床或固定床反应器提供。第一反应区可以作为包含所述第一负载型催化剂的流化床提供。二氧化硅基颗粒可以是硅质泡沫。硅质泡沫可以是大孔、微孔或介孔的。特别地,硅质泡沫可以是介孔的并且能够具有介孔网络。这种介孔的多孔硅质泡沫(mcf)可以具有任何规则或不规则形状,其中规则形状的介孔硅质颗粒可以是球形、圆柱形、长方形或椭圆形。该mcf可具有本文所公开的孔径和表面积,例如,在2-50nm范围内的孔径和至少350m2/g的表面积。通过使用这种mcf作为第一和第二催化剂的载体,由于mcf的孔径大,有助于增加催化剂和反应物之间的接触,因此可提高这些催化剂的催化活性。任选取代的醇可以是能够脱氢形成任选取代的羰基的任何醇。示例性的醇可包括但不限于乙醇、丙醇、丁醇、戊醇或任何其它取代的醇。任选取代的醇可具有至少2个碳原子。任选取代的烯烃可以是任选取代的二烯。任选取代的烯烃或二烯可具有至少4个碳原子。任选取代的烯烃或二烯可具有4-20个碳原子。示例性二烯可以包括但不限于,丁二烯、戊二烯、己二烯、庚二烯、辛二烯和壬二烯或其它取代的二烯。任选取代的羰基可以是任何酮或醛,例如但不限于乙醛或巴豆醛。该任选取代的羰基可具有与由其衍生的任选取代的醇相同数目的碳原子。任选取代的醇可以是乙醇,任选取代的烯烃可以是丁二烯,任选取代的羰基可以是乙醛。第二组反应条件与第一组反应条件不同并且被选择用以形成任选取代的烯烃。第二组反应条件可包括在250℃-550℃的温度或落入该范围内的任何温度进行转化步骤。特别地,转化可以在约375℃或约400℃进行。有利地,这些温度可使所得任选取代的烯烃的选择性最大化且不损害任选取代的醇原料的转化百分比。转化步骤还可包括将任选取代的醇与任选取代的羰基偶联的步骤,以及使偶联的任选取代的醇和任选取代的羰基脱水以形成任选取代的烯烃的步骤。第一催化剂和第二催化剂可以是由不同金属组成的不同的金属催化剂。第二负载型催化剂可以是一元金属催化剂、二元金属催化剂、三元金属催化剂或它们的任何等效的金属氧化物催化剂。用于第二负载型催化剂的金属或金属氧化物可选自由如下所组成的组:银、金、铜、锌、铝、镁、锆、钽、钛、钒及它们的组合。特别地,第二负载型催化剂可以是锆-mcf负载型催化剂。第二反应区可以作为包含所述第二负载型催化剂的填充床或固定床反应器提供。第二反应区可以作为包含所述第二负载型催化剂的流化床提供。第一和第二负载型催化剂可以能够再生。例如,所公开的负载型催化剂可以通过煅烧再生。所公开的方法有利地包括使用流体连接的两个反应区。提供两个分离但流体连接的反应区有利地使得能够优化每个反应的反应条件。在本发明方法中使用双反应器系统允许最佳地实现任选取代的醇和任选取代的羰基的比例以进料到第二反应器,从而实现所产生的任选取代的烯烃的最佳选择性。使用所公开的双反应器系统有利地减少了对纯化、储存羰基或将羰基与任选取代的醇混合的需求,而如果用于脱氢步骤和转化步骤的反应器是分离的则具有这种需求。因此,双反应器系统和方法可提供更具有成本有效性和环境友好的方式,用于从任选取代的醇制备任选取代的烯烃,例如从乙醇生产丁二烯。现在将公开用于制备任选取代的烯烃的系统的示例性、非限制性实施方案。在一个实施方案中,提供了一种用于制备任选取代的烯烃的系统,所述系统包括:第一反应区,其具有用于使任选取代的醇脱氢以形成任选取代的羰基的第一催化剂;以及第二反应区,其具有用于转化来自第一反应区的任选取代的醇和任选取代的羰基以形成任选取代的烯烃的第二催化剂;其中所述第一和第二催化剂负载在多孔二氧化硅基颗粒上。有利地,上述公开的多孔二氧化硅基颗粒能够增强任选取代的醇至任选取代的烯烃的转化率且不损害中间体任选取代的羰基的选择性。这样的优点可通过多孔二氧化硅基颗粒实现,由于其增加的孔径或孔隙率而提供了改进的催化活性。另一方面,典型的硅胶不能提高催化活性和转化率。这些硅胶可以与如上所述的多孔二氧化硅基颗粒相区分。尽管这些颗粒和用于形成硅胶的颗粒是多孔的,具有宽的孔径分布,但硅胶内的孔隙率或孔径不能提供上述优点。这是因为典型的由硅胶负载的金属催化剂是通过浸渍方法制备的,其导致形成具有相对较大粒径的金属催化剂氧化物。这些较大尺寸的金属氧化物颗粒有可能降低硅胶的孔径和孔隙率。因此,由于这种硅胶的孔径或孔隙率的降低,负载在硅胶上的金属催化剂遭受催化活性的降低。因此,金属催化剂本身也在组成上受到影响,在这种意义上由于由浸渍法形成的氧化物,原始金属催化剂的量被减少,从而导致转化率降低。所报导的包含负载在硅胶上的二元或三元金属-金属氧化物组分的催化剂仅具有平均约33%的低的乙醇转化率和0.3hr-1的低重时空速(whsv),即使每摩尔起始乙醇获得的最高丁二烯产率只有81%。此外,当whsv增加到15hr-1时,乙醇转化率和丁二烯选择性分别降低到12%和67%。因此,基于这些报道的结果,硅胶-负载型催化剂不是高效的或有效的。同时,用作载体的常规硅酸盐颗粒不是足够多孔的或不能够在颗粒内具有介孔网络,这与本文公开的二氧化硅基颗粒载体相反。因此,结构上不同于本文公开的介孔二氧化硅基颗粒的常规离散型硅酸盐颗粒仍然不足以增强催化活性和转化率。这些离散型硅酸盐颗粒通常通过混合金属、硅和氧而形成,然后在水中进行缩合以得到上述离散型硅酸盐颗粒。这意味着不是所有的金属都可以成功地固定在硅酸盐颗粒表面上。因此,这种离散型硅酸盐颗粒由于固定在其上的金属催化剂较少而遭受降低的催化活性的困扰。相比之下,本发明的二氧化硅基颗粒形成于金属催化剂被固定在其上之前。因此,更多的金属催化剂可被成功地固定在二氧化硅基颗粒上。与本发明的二氧化硅基颗粒的孔径和孔隙率的增加相伴随的,是这种载体上更多的金属催化剂可被暴露以与反应物进行最大的相互作用,导致增加的催化活性以获得更高的转化率。值得注意的是,与本发明的二氧化硅基颗粒相比,硅胶和离散型硅酸盐颗粒具有不同的颗粒形态。本发明的多孔二氧化硅基颗粒可以是硅质颗粒。二氧化硅基颗粒或硅质颗粒可以是大孔或介孔的。大孔颗粒可具有大于介孔颗粒的孔径的典型孔径,而微孔颗粒可具有比介孔颗粒的孔径小的典型孔径。在一些实施方案中,所公开的颗粒可以是介孔的。所公开的颗粒可以是介孔二氧化硅。介孔二氧化硅具有广泛的应用,并广泛用于催化。所公开的颗粒可以是高度多孔的,包括每个颗粒内的均匀孔的互连网络,并且在结构上与硅胶和离散型硅酸盐颗粒不同。例如,所公开的颗粒可以具有在离散型硅酸盐颗粒或用于形成硅胶的颗粒中不存在的海绵状孔结构。离散型硅酸盐颗粒或用于形成硅胶的颗粒倾向于是刚性的,在这种意义上在不将颗粒分裂成更小颗粒的情况下,其可能不能够改变形状。另一方面,本发明具有海绵状孔结构的二氧化硅基颗粒可以是可形变的,在这种意义上在不分裂成更小颗粒的情况下,二氧化硅基颗粒可能能够改变其形状。在其它实施方案中,本发明的二氧化硅基颗粒可能不是可形变的。二氧化硅基颗粒或介孔硅质颗粒可以在颗粒内具有介孔网络。这种介孔颗粒可以称为多孔硅质泡沫或介孔硅质泡沫(mcf)。因此,多孔二氧化硅基颗粒可以是多孔二氧化硅基泡沫。介孔结构多孔泡沫由尺寸均匀的、大球形孔组成,其通过称为窗孔的均匀、较小尺寸的孔相互连接,以产生连续的3-d孔系统。大的均匀孔相互连接的性质使得这些新的介孔结构二氧化硅成为用作催化剂载体的有希望的候选物,因为它们具有可用于支持催化剂的高表面积。另外,孔隙的相互连接的网络可允许反应流体流过载体的孔并接触分散在孔的内表面上的催化剂。介孔的多孔硅质泡沫可由包含任何规则或不规则形状的颗粒组成。本文公开的二氧化硅基颗粒可以是规则的或不规则的形状。规则形状的颗粒可以是球形、圆柱形、长方形或椭圆形。这些颗粒可以是微粒。这些颗粒的尺寸可以为至少1um。这些颗粒的尺寸也可以为1μm-20μm,或者1um-15um,或1um-10μm,或5um-20μm,或5um-15um。术语“粒径”是指颗粒的平均轴向长度,例如直径。介孔硅质泡沫的孔径可以在1nm-100nm的范围内、或更具体地5nm-50nm、或10nm-40nm、或25nm、或29nm、或30nm、或35nm。窗孔的孔径可以在0.1nm-100nm的范围内、或2nm-100nm、或10nm-50nm、或10nm-20nm、或14nm、或15nm、或16nm。孔径可能与烯烃的选择性和生产率正相关。有利地,较大的孔径可能对焦化的敏感性较小。因此,负载在介孔二氧化硅或介孔硅质泡沫上的催化剂可能比负载在常规二氧化硅上的催化剂具有更好的寿命。所公开的二氧化硅基颗粒的表面积可以为至少300m2/g,或至少350m2/g,或大于400m2/g,或大于500m2/g。有利地,如上所述的二氧化硅基颗粒能够用作第一和第二催化剂的介孔载体,其中由于其改善的孔径和孔隙率,两种催化剂的活性可以得到增强。公开的二氧化硅基颗粒可包含90-100重量%的二氧化硅含量。公开的二氧化硅基颗粒可基本上由二氧化硅组成。任选取代的烯烃可以是任选取代的二烯。任选取代的烯烃或任选取代的二烯可具有至少4个碳原子。任选取代的烯烃或任选取代的二烯可具有4-20个碳原子或落在该范围内的任何数目的碳原子。示例性二烯可包括但不限于,丁二烯、戊二烯、己二烯、庚二烯、辛二烯和壬二烯或其它取代的二烯。所述任选取代的醇可以是能够脱氢形成任选取代的羰基的任何醇。示例性的醇可包括但不限于乙醇、丙醇、丁醇、戊醇或任何其它取代的醇。任选取代的醇可具有至少2个碳原子。任选取代的醇可具有落在2-20的范围内的碳原子数。所述任选取代的羰基可以是能够被转化为任选取代的烯烃例如二烯的任何羰基化合物。该任选取代的羰基可以是醛或酮。取决于所使用的反应物、反应及其动力学,任选取代的羰基中间体可包括一种或多种类型的羰基中间体。取决于反应途径,任选取代的羰基可具有与衍生该羰基的任选取代的醇相同数目的碳原子,或者可具有与衍生该羰基的任选取代的醇不同数目的碳原子。一种或多种类型的羰基中间体可具有与衍生该羰基的任选取代的醇相同或不同数目的碳原子。当存在多于一种类型的羰基中间体时,羰基中间体可具有与其它中间体相同或不同数目的碳原子。例如,当醇是乙醇时,任选取代的羰基可以是乙醛和/或巴豆醛。在脱氢过程中,可以在第一反应区中形成巴豆醛作为副产物。巴豆醛可能由于乙醛缩合而形成。在使用铜催化剂作为第一催化剂的实施方案中,预期可以生产巴豆醛,因为铜是略微碱性的。然而,由于任选取代的醇的脱氢倾向于对形成乙醛具有选择性,因此形成的这种巴豆醛可能是微量的。乙醇转化为丁二烯通常使用催化剂,诸如基于二氧化硅和氧化铝的一元、二元或三元金属氧化物,例如铜、锌、锆、钽和镁的氧化物。在一个实例中,氧化银/氧化镁/二氧化硅三元催化剂可与纯乙醇一起使用,在91.8%的乙醇转化率提供45.4%的丁二烯产率。在另一个实例中,过氧化氢可用于在乙醇/过氧化氢溶液上引发氧化锌/γ-al2o3催化剂,以得到丁二烯产率为24.5%,选择性为55%。在另一个实例中,负载在有序介孔二氧化硅上的钽(ta)氧化物催化剂在气流上10小时时间后可用于提供47%的乙醇转化率和79%的丁二烯选择性。在另一个实例中,氧化铝上的还原铜催化剂可用于脱氢步骤,二氧化硅上的氧化钽催化剂可用于转化步骤,在20小时中以23%的丁二烯产率和每小时每升催化剂43g丁二烯的生产率生产丁二烯。相比而言,本文公开的负载型催化剂可有利地实现比现有技术实例更高的丁二烯产率。例如,本文公开的负载型催化剂可为本文公开的方法提供60%-95%的乙醇转化率和从85%至95%以上或97%以上的乙醛选择性。总的丁二烯产量可为60%以上,大于70%以上,或大于73%以上。可通过合适的分析方法如通过气相色谱法分析丁二烯产率。分析方法可利用合适的检测器,如热导检测器或火焰离子化检测器。在一个实施方案中,检测器是火焰离子化检测器,其可以能够在具有四个碳的其它分子中检测出丁二烯。在一个实例中,使用配备有火焰离子化检测器(gc-fid)的气相色谱法,用氮气作为载气并使用基本上纯的乙醇,以1.5hr-1的乙醇whsv,在15小时中总丁二烯产率超过73%。在另一个实例中,使用gc-fid,用氮气作为载气并使用具有10vol%水的含水乙醇,以1.5hr-1的乙醇whsv,在15小时中总丁二烯产率超过71%。第一催化剂可以是一元金属催化剂、二元金属催化剂、三元金属催化剂或它们的任何对应的金属氧化物催化剂,即一元金属氧化物催化剂、二元金属氧化物催化剂或三元金属氧化物催化剂。第一催化剂的金属或金属氧化物可以选自由如下所组成的组:银、金、铜、钴、锌、铝、镁、锰、锆、钽、钛、钒及它们的组合。第一催化剂可以是负载在多孔二氧化硅基颗粒上的铜。第一催化剂可以是包含上面列出的两种金属或金属氧化物的二元催化剂。第一催化剂可以是包含上面列出的三种金属或金属氧化物的三元催化剂。特别地,第一催化剂可以是铜-mcf负载型催化剂。有利地,当与其他金属如金、银或钒相比时,铜用作相对便宜的催化剂并且更丰富。第二催化剂可以是单金属催化剂、二元金属催化剂、三元金属催化剂或它们的任何对应的金属氧化物催化剂,即单金属氧化物催化剂、二元金属氧化物催化剂或三元金属氧化物催化剂。第二催化剂的金属或金属氧化物可以选自由如下所组成的组:银、金、铜、锌、铝、镁、锆、钽、钛、钒、铈及它们的组合。第二催化剂可以是负载在多孔二氧化硅基颗粒上的锆。第二催化剂可以是包含上面列出的两种金属或金属氧化物的二元催化剂。第二催化剂可以是包含上面列出的三种金属或金属氧化物的三元催化剂。在一个实施方案中,第二催化剂可以是具有通式m1/m2的二元催化剂,其中m1和m2独立地选自上述列举的基团。在一个实例中,m1是锆,m2选自由铈(ce)、铜(cu)、镁(mg)和锌(zn)所组成的组。特别地,第二催化剂可以是锆-mcf负载型催化剂。由于与上述关于铜-mcf负载型催化剂的相同理由,可以选择锆作为第二催化剂,因为它相对更实惠。此外,锆提供更好的催化性能,并且锆-mcf催化剂的合成程序能够更直接地用于放大量产。所公开的负载型催化剂可包含约1-15重量%、或约1-10重量%、或约1-8重量%的金属含量,约1-20重量%、或约1-15重量%、或约1-10重量%的金属含量。在实施方案中,所公开的催化剂基本上由金属氧化物组成。在其它实施方案中,所公开的催化剂基本上由金属组成。催化剂可具有优化以允许催化剂表面和反应物接触的粒径和/或表面积。可以考虑二氧化硅基颗粒载体的孔的尺寸来优化催化剂的粒径。催化剂颗粒可具有不妨碍反应物与分散在载体内表面上的催化剂接触的尺寸。第一催化剂的金属和/或金属氧化物(如果存在)或第二催化剂的金属和/或金属氧化物(如果存在)的尺寸可独立地具有如下尺寸:比二氧化硅基颗粒的尺寸小(因此比二氧化硅基颗粒的孔小)少于2个数量级、或少于3个数量级、或少于4个数量级,从而不会阻碍反应物与固定在多孔二氧化硅基颗粒载体内表面上的催化剂接触。与通过浸渍法生产的金属氧化物催化剂相比,所公开的金属氧化物催化剂(如果存在)可有利地具有更小的粒径。在一个实例中,当二氧化硅基颗粒的尺寸为1μm时,金属氧化物催化剂的尺寸可以为5nm或更小。在其他实例中,金属和/或金属氧化物催化剂的尺寸可以为5nm或更小,或4.5nm或更小,或4nm或更小。有利地,可以控制催化剂颗粒的尺寸和组成以优化对烯烃的转化率。本文公开的负载型催化剂可以是非均相催化剂。所公开的负载型催化剂可包含90重量%或更多、或92重量%或更多、或95重量%或更多的二氧化硅含量。所公开的负载型催化剂可包含10重量%或更少、或9重量%或更少、或8重量%或更少、或7重量%或更少、或5重量%或更少的金属和/或金属氧化物含量。所公开的负载型催化剂可包含90-100重量%的二氧化硅含量和0-10重量%的金属和/或金属氧化物含量。第一负载型催化剂可包含大于3mol%、大于3.5mol%、或大于4mol%的金属和/或金属氧化物含量。在第一催化剂是铜且多孔二氧化硅基颗粒为mcf的一个实例中,当使用电感耦合等离子体质谱法(icp-ms)分析时,cu/mcf催化剂的铜负载量可为4mol%或4.1mol%。第二负载型催化剂可包含1mol%以上、1.5mol%以上、2mol%以上、2.5mol%以上、或3mol%以上的金属和/或金属氧化物含量。在第二催化剂为锆且多孔二氧化硅基颗粒为mcf的一个实例中,当用icp-ms分析时,zr/mcf催化剂的锆负载量可为2mol%。所公开的负载型催化剂可通过将催化剂的前体与所公开的多孔二氧化硅基颗粒载体(其可以根据文献程序合成)的悬浮液混合来合成。催化剂前体可以是可溶于水溶液的。催化剂前体可以是金属离子。催化剂前体可以是金属盐或金属盐的混合物,其中金属如本文所公开。二氧化硅基颗粒的溶液或悬浮液可以是水性的。负载型催化剂的合成方法可以在ph大于7的溶液中即在碱性环境中进行。碱性环境赋予二氧化硅基颗粒表面上的负电荷。碱性环境可具有大于7、或约7.5、或约8、或约8.5、或约9、或约9.5、或约10的ph。可以将碱性化合物如氨或尿素加入到溶液中以增加ph。带负电的二氧化硅基颗粒可通过化学吸附吸引金属前体,从而实现催化剂在二氧化硅基颗粒载体上的改善的分散。混合物可以例如通过过滤和干燥而纯化,然后加热以形成所公开的负载型催化剂。加热可以在空气存在下进行。加热可能使载体上的催化剂氧化。加热可能在载体上产生金属氧化物催化剂颗粒。加热可能不会分解催化剂颗粒。氧化的催化剂可至少部分地被还原,使得固定在载体上的催化剂可包含氧化的催化剂和原始的纯催化剂。还原通常在氢气存在下在升高的温度下进行数小时。所公开的负载型催化剂可包括载体/氧化的催化剂界面和氧化的催化剂/纯催化剂界面。暴露于反应环境的一部分催化剂可以是还原的或纯的催化剂。例如,所公开的负载型催化剂可包括金属氧化物/二氧化硅界面,其中二氧化硅通过氧桥接与金属氧化物结合,并且其中金属氧化物外面的部分可通过还原过程还原成纯金属。由于公开的二氧化硅基颗粒载体可以是高度多孔的,所以相当大百分比的载体表面,例如90%以上的表面或95%以上的表面,可能在颗粒内。也就是说,二氧化硅基颗粒载体的相当大百分比的表面积可包括颗粒内的互相连接的孔网络的表面。有利地,催化剂可以生长或固定或负载于基本上在颗粒载体内的表面上。进一步有利地,负载在颗粒载体内的孔表面上的大量催化剂可具有相对较小的尺寸,例如5nm或更小。与现有技术的负载型催化剂相比,颗粒载体的孔径可以有利地不会被减少那么多,从而提高催化活性。还有利的是,暴露于反应物的部分催化剂可以是原始的纯催化剂。因此,与常规催化剂相比,由于原始催化剂更高程度地暴露于反应环境,催化剂的失活可能会降低。无论如何,即使暴露于反应物的一部分催化剂可能是氧化的催化剂,氧化的催化剂也可能不会被完全分解,从而保持了其催化活性。添加的碱性化合物的量相对于催化剂前体的量来说可以是摩尔过量的。催化剂前体与碱性化合物的摩尔比可以为1:5。在使用尿素的情况下,催化剂前体与碱性化合物的摩尔比可以为约1:10。尿素在加热过程中可能被水解和热分解。尿素在水溶液中的热分解产生氨,这增加了溶液的ph。碱性环境有助于催化剂前体逐渐沉淀到多孔二氧化硅基颗粒的表面上。例如,锆前体,例如zrocl2·8h2o,可逐渐在二氧化硅基颗粒的孔表面上沉淀为氢氧化锆。所公开的合成方法可进行3小时或更多的时间。有利地,所公开的合成方法控制催化剂的沉淀过程以产生较小的催化剂颗粒。有利地,所公开的合成方法可在碱性环境中进行以使催化剂颗粒在载体表面上的分散得到改善。有利地,所公开的催化剂形成在二氧化硅基颗粒的表面上。因此,与现有技术的催化剂相比,所公开的方法可有利地使得催化剂更多地分散在多孔二氧化硅基颗粒载体上。与现有技术的催化剂相比,本文公开的负载型催化剂,包含负载在多孔二氧化硅基颗粒上的催化剂,可具有改善的催化活性和稳定性。所公开的方法可有利地产生保持了金属的催化活性的负载型催化剂。所公开的方法可有利地导致形成的金属氧化物的量较少,从而产生改进的负载型催化剂系统。所公开的方法可简单地通过化学吸附并且没有复杂的反应途径或添加剂的使用而有利地将更多的金属催化剂固定在多孔载体上。附图说明附图示出了所公开的实施方案,并且用于解释所公开的实施方案的原理。然而,应当理解,设计附图仅用于说明的目的,而并非用于限定本发明的范围。图1[图1]是用于将乙醇转化为丁二烯的示例性反应方案。图2[图2]示出了实施例1中提及的制备的催化剂以及空白mcf载体的氮等温线。图3[图3]示出了实施例1中提及的制备的催化剂以及空白mcf载体的x射线衍射(xrd)光谱。图4[图4]是实施例2-4中使用的实验装置的示意图。图5[图5]是实施例2中乙醇转化率和bd选择性对催化剂温度的图。图6[图6]是实施例3中乙醇转化率和乙醛选择性对(a)纯乙醇中和(b)乙醇水溶液中cu/mcf催化剂的反应时间的图。图7[图7]是实施例4的项1的乙醇转化率和丁二烯选择性对(a)纯乙醇中和(b)乙醇水溶液中的双反应系统的反应时间的图。图8[图8]是在实施例2中使用再生催化剂时乙醇转化率和bd选择性对反应时间的图。图9[图9]是实施例5中使用的实验装置的示意图。图10[图10]是实施例6和8中使用的实验装置的示意图。实施例将通过参考具体实施例更详细地描述本发明的非限制性实施例,其不应被解释为以任何方式限制本发明的范围。实施例1制备mcf上的cu催化剂(cu/mcf)将30ml去离子(di)水加入到1g根据已知方法(y.han,s.s.lee和j.y.ying,chemistryofmaterials,2007,19,2292-2298)合成的mcf中。将适量的可溶性铜前体(例如,cuno3或cucl2)加入到mcf/水混合物中并迅速搅拌。滴加氨水溶液(4m)直到ph达到~9。在ph9,二氧化硅表面带负电并吸引溶液中带正电的[cu(nh3)4]2+物质。将混合物搅拌10分钟,过滤,用水洗涤数次,然后真空干燥12小时。将得到的粉末在500℃加热3小时,得到最终的绿色cu/mcf催化剂。实现了在mcf载体上形成高度分散的铜。cu/mcf催化剂在其xrd光谱(图3)中没有显示任何可见的峰,证实mcf表面上高度分散的铜元素。然而,通过现有技术的浸渍法制备的cu-im-mcf催化剂显示出cuo的典型xrd图谱(未显示),这表明在mcf表面上形成较大的cuo颗粒。制备mcf上的zr催化剂(zr/mcf)将20mldi水加入到1gmcf中。尿素水解法用于制备zr/mcf催化剂。向mcf/水混合物中加入适量的锆前体(zrocl2·8h2o或zrono3·xh2o)和摩尔比为1:10的尿素并迅速搅拌。将所得混合物加热至90℃并搅拌6小时。冷却后,过滤混合物,用水洗涤数次,然后真空干燥12小时。将得到的粉末在500℃加热3小时以得到最终的无色zr/mcf催化剂。表征分析了制备的负载型催化剂和空白mcf载体。在200℃真空下将催化剂样品真空脱气过夜后,在micromeriticsasap2020(georgia,usa)上在-196℃、p/po为0.01-0.995测量氮等温线。测得的氮等温线如图2所示。使用brunauer-emmett-teller(bet)方程计算所有样品的表面积。使用barret-joyner-halenda(bjh)方法,使用从氮等温线获得的数据,计算样品的孔径分布。结果如下表1所示。[表1]用配备有cukα辐射源在20°-80°的2θ范围内操作的philipsx’pertpro衍射仪获得粉末x射线衍射(xrd)图谱。使用perkin-elmerelandrcii(massachusetts,usa)对hf/hno3-消化的样品和适当的标准溶液进行电感耦合等离子体质谱(icp-ms)分析。xrd数据如图3所示。实施例2双反应器系统进行的催化反应乙醇、乙醛、乙醚、巴豆醛、巴豆醇通过手动注射已知量(平均5次注射)至配备有热导检测器(fid)的气相色谱(gc)机器中来进行校准。使用氮平衡中经认证的各2mol%的气体共混物来校准乙烯和bd。使用250ul气体注射器将两种气体注入gc。使用液相色谱(lc)泵来控制本文公开的系统中的乙醇的量。使用质量流量控制器(mfc)来控制氮气流速率,其将汽化的乙醇递送通过填充有20mgcu/mcf的固定床反应器(第一反应区)。然后将所得的气体流输送到装有60mgzr/mcf的另一固定床反应器(第二反应区)。所述装置的示意图示于图4。通过在两个反应器中使用气阀系统在150℃进行取样来确定气流中的初始乙醇量。反应在环境压力下进行,并以1小时的间隔监测。通过气阀系统,使用gc-fid用30m长的poraplotq柱定期分析出口的产品。将输出的气体吹送到cdcl3中以进行以定性为目的的1hnmr光谱和分析。通过将乙醇转化率和bd选择性针对催化剂温度作图而优化了反应器1和2中两种负载型催化剂的反应温度,其代表了反应器的温度。在反应100分钟时获得第一个数据点。cu/mcf催化剂的cu负载为4.1mol%,zr/mcf催化剂的zr负载为2.0mol%。结果如图5所示。根据得到的结果,cu/mcf和zr/mcf的最适温度分别为235℃和400℃。催化剂通过在空气中500℃煅烧3小时再生。用再生的催化剂重复实验,并在110小时内监测乙醇转化率和丁二烯选择性,并对反应时间作图。结果如图8所示。碳平衡确定为通常95%以上。实施例3在该实施例中,研究了脱氢反应。将含水量小于0.005vol%的纯乙醇原料与90v/v%乙醇/h2o的原料进行比较。反应温度保持在300℃。纯乙醇的whsv为7.7hr-1,而含水乙醇的whsv为5.3hr-1。纯乙醇和含水乙醇的乙醇转化率和乙醛选择性分别如图6a和图6b所示。实施例4在本实施例中研究了不同whsv和时间下的不同催化剂系统。使用了图4所示的双催化剂系统,结果示于下表2。[表2]计算乙醇转化率和丁二烯选择性为20小时中的平均值。在项1、4和5中,zr/mcf催化剂的icp负载量为2.0mol%。在项2中,zr/mcf催化剂的icp负载量为1.0mol%。在项3中,zr/mcf催化剂的icp负载量为3.0mol%。在项1至4中,使用水含量小于0.005体积%的纯乙醇。在项6中,使用4mol%的cu和2.0mol%的zr作为催化剂,并使用湿乙醇(10vol%h2o)。反应器1和2的最佳温度分别为240℃和375℃。从上表2中的项1、2和3可以看出,zr/mcf催化剂的最佳icp负载量为2.0mol%。将项1的乙醇转化率和丁二烯选择性相对于反应时间作图并示于图7a。将项6的乙醇转化率和丁二烯选择性相对于反应时间作图并示于图7b。通过比较图7a和图7b显示,当使用纯乙醇或湿乙醇时,bd选择性相当。然而可以看出,与使用湿乙醇相比,当使用纯乙醇时乙醇转化率略高。在项1中实现了乙醇转化率为96%时平均bd选择性为73%。还实现了在15小时气流上时间中在1.7×104vppm浓度下0.62gbdgcat-1hr-1的bd生产率。因此,本发明系统的催化性能超过本发明人已知的所有报道结果,例如,在e.v.makshina,w.janssens,b.f.sels和p.a.jacobs,catalysistoday,2012,198,338-344中报道的至少0.15gbdgcat-1hr-1的bd生产率和产物流中1×104vppm浓度。实施例5该实施例中研究了在反应器2中使用不同的二氧化硅载体。使用了图9所示的双催化剂系统。该催化剂的合成与实施例1中的zr/mcf的合成相同,不同之处在于使用三种不同的二氧化硅载体(merck、davisil级635和级645)代替mcf。反应器1的催化剂仍然为cu/mcf。反应器1和2的最佳温度分别为235℃和400℃。乙醇转化率和丁二烯选择性为whsv为1.5hr-1时的15小时中的平均值。结果示于下表3。[表3]实施例6该实施例中研究了在反应器2中使用二元催化剂。使用了图10所示的双催化剂系统。对于第二反应器,使用m/zr/mcf负载型催化剂进行乙醇至丁二烯的反应,其中m为不同负载的铈(ce)、铜(cu)、镁(mg)或锌(zn)。反应器1的催化剂仍然为cu/mcf。反应器1和2的最佳温度分别为235℃和400℃。在whsv为1.5hr-1进行反应100分钟后,获得转化率和选择性值。碳平衡通常为95%以上。结果示于下表4。[表4]摩尔比zn/zr/mcfetoh转化率(%)bd选择性(%)0.01/2/9899750.05/2/9899760.1/2/989870摩尔比mg/zr/mcfetoh转化率(%)bd选择性(%)0.01/2/9899740.05/2/9898750.1/2/989971摩尔比cu/zr/mcfetoh转化率(%)bd选择性(%)0.01/2/9888710.05/2/9899710.1/2/989972实施例7制备mcf上的二元催化剂将20mldi水加入到1gmcf中。尿素水解法用于制备m/zr/mcf催化剂。向mcf/水混合物中加入适量的锆前体(zrocl2·8h2o或zrono3·xh2o)、m前体(其中m=铈、铜、镁或锌),前体和尿素的摩尔比为1:10,迅速搅动。将所得混合物加热至90℃并搅拌6小时。冷却后,过滤混合物,用水洗涤数次,然后真空干燥12小时。将所得粉末在500℃加热3小时以得到最终的无色m/zr/mcf催化剂。实施例8在该实施例中研究了按比例放大实验。以更大的规模实施了实施例6的方法,使用了图10所示的双催化剂系统。在反应器1中,使用125mgcu/mcf。在反应器2中,使用375mgzr/mcf。反应器1的温度为240℃,反应器2的温度为385℃时,15小时内平均乙醇转化率为84%,丁二烯选择性为76%,whsv为2.1hr-1。氮气流量为35ml/min。两个另外的m/zr/mcf催化剂(m=zn或mg)也用作反应器2中的催化剂。zn/zr/mcf和mg/zr/mcf的摩尔比分别为0.05zn/2zr/98mcf和0.05mg/2zr/98mcf。获得的乙醇转化率值和丁二烯选择性值为15小时内的平均值。结果示于下表5。[表5]工业应用性本文公开的系统和方法可用于以高转化率和选择性生产任选取代的烯烃。第一反应区设计用于使任选取代的醇进行高效的脱氢反应以产生中间体,第二反应区设计用于高效地偶联醇和中间体以及随后的产物脱水以产生任选取代的烯烃。显而易见的是,在阅读前述公开内容之后,在不脱离本发明的精神和范围的情况下,本发明的各种其它修改和适应性改动对于本领域技术人员将是显而易见的,本文意在所有这些修改和适应性改动都在所附权利要求的范围内。当前第1页12