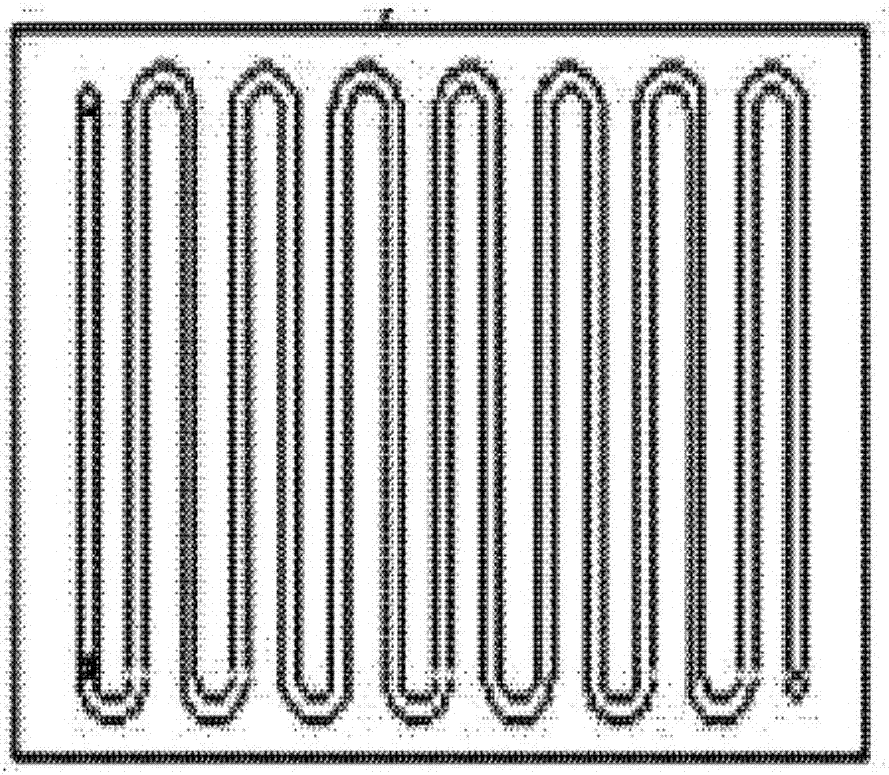
本发明涉及高分子材料
技术领域:
,尤其涉及一种采用微通道反应器制备氟树脂的方法。
背景技术:
:以氟代聚丙烯酸酯为主组分的有机氟树脂,由于其低表面能的物理特性,所表现出来的优异的拒水拒油性能,目前被广泛使用于玻璃、金属或纤维基材的处理,一方面可以改善基材的表面性能与手感,另一方面又赋予基材理想的拒水拒油防污性能,因此在功能涂层及功能涂料领域的应用十分广泛。在氟树脂的工业化生产中面临着生产工艺落后,工艺条件苛刻等工艺问题,由于单体原料均为易燃物质,生产过程中安全危险性大,而且面临产品质量不够稳定以及市场竞争剧烈等诸多难题。目前有文献报道将氟代丙烯酸酯与其他丙烯酸酯及功能单体进行多元共聚可制备拒水拒油性能良好的有机氟树脂,如us5705276、wo2009/126467、us5242487、cn103937357、us2001/0020077等所公开的专利均报道了采用常规的反应釜或反应瓶制备有机氟树脂的方法。在美国化学会的期刊macromolecules2012,45,9551-9570中,报道了一些微通道合成树脂的文献研究,但是对于含氟丙烯酸树脂的微通道法制备方法,尚未见相关的专利报道。微通道反应器在进行前期合成条件筛选过程中所需要的原料用量少,可以降低原料成本,而且反应过程安全环保,是一种环境友好型的技术设备,连续流方式大大提高了反应的条件筛选速度和研究方案的优化,同时微通道反应器中制备的产物与现代分析仪器如gc\gc-ms、hplc、gpc以及nmr等进行匹配分析,使现代分析仪器可以直接用于在线监测反应进行的程度,大大提高了合成工艺开发的速度。然而微通道反应器在化学合成上的应用,目前主要集中于小分子方向的研究,而对树脂聚合方面的研究目前处于较为前期的探索阶段。在文献j.flowchem.2014,4(4),168–172中,报道了一种阳离子聚合含氟丙烯酸树脂的方法,但是该法使用了工业上难以得到的有机锂强碱引发,不利于工业化放大生产。技术实现要素:本发明的目的在于:针对上述存在的问题,提供一种采用微通道反应器制备氟树脂的方法,本方法使用的单体原料来源广泛,生产成本低廉,操作工艺简便易行,聚合反应时间短,利于工业化放大回收,同时提高了氟单体利用率,生产得到的氟树脂分子量分布窄、疏水性能高。为了实现上述发明目的,本发明采用的技术方案如下:一种采用微通道反应器制备氟树脂的方法,所述制备方法在微通道反应器中进行,包括如下步骤:(1)将乙烯基化合物、引发剂与溶剂混合,得到混合溶液ⅰ;(2)将混合溶液ⅰ、含氟丙烯酸单体分别预热后混合反应,得到混合液ⅱ;(3)将常规丙烯酸酯单体预热后,与所述混合液ⅱ混合反应,得到混合液ⅲ;(4)将功能性丙烯酸酯单体预热后,与所述混合液ⅲ混合,进行聚合反应,得到氟树脂。较佳地,所述乙烯基化合物、含氟丙烯酸单体、常规丙烯酸单体、功能性丙烯酸单体及引发剂的质量比为:5-15:20-40:40-60:1-5:0.5-1.0。较佳地,所述乙烯基化合物为苯乙烯或n-乙烯基吡咯酮;所述含氟丙烯酸单体为丙烯酸六氟丁酯、甲基丙烯酸十二氟庚酯、全氟烷基丙烯酸酯、丙烯酸八氟戊酯中的一种或多种。较佳地,所述常规丙烯酸单体为丙烯酸甲酯、丙烯酸丁酯、丙烯酸正辛酯、甲基丙烯酸甲酯和甲基丙烯酸丁酯中的一种或多种;所述功能性丙烯酸单体为丙烯酸羟乙酯、丙烯酸羟丙酯、甲基丙烯酸缩水甘油酯和丙烯酸缩水甘油酯的一种或多种。较佳地,所述引发剂为偶氮二异丁腈、偶氮二异庚腈、偶氮二异丁酸二甲酯、过氧化二苯甲酰和过氧化苯甲酸叔丁酯的一种或两种;所述溶剂为乙酸乙酯、乙酸丁酯、二甲苯、甲苯或二氯甲烷,其中优选乙酸丁酯。较佳地,在步骤(2)、(3)及(4),所述预热的温度为40-50℃;较佳地,在步骤(2)、(3)及(4),所述混合反应、聚合反应的温度为60-120℃,所述聚合反应的时间为70-300s。本发明还提供了一种采用微通道反应器制备氟树脂的方法,所述微通道反应器包括进料口a-d,预热模块a-d,混合反应模块e-g;所述进料口a与预热模块a顺次连接,所述进料口b与预热模块b顺次连接,所述进料口c与预热模块c顺次连接,所述进料口d与预热模块d顺次连接;所述预热模块a和预热模块b的出口分别与混合反应模块e连接,所述混合反应模块e和预热模块c的出口分别与混合反应模块f连接,所述混合反应模块f与预热模块d的出口分别与混合反应模块g连接,所述混合反应模块g与出料口连通。较佳地,所述预热模块、混合模块及反应模块为直形通道模块或心形通道模块。本发明所用的为高通量微通道连续流的微通道反应器,该反应器由多个模块组装而成,模块间可以并联组装或者串联组装,模块将换热通道和反应通道集成,并且配有专门的热电偶,可以测定换热通路中换热介质或外界导热介质的温度。模块为单晶硅、特种玻璃、陶瓷、耐腐蚀的合金、特氟龙等组成。反应系统可以防腐耐压,耐压能力最大达到18bar。模块中微通道为混合型结构,通道水力直径0.5mm~10mm。综上所述,由于采用了上述技术方案,本发明的有益效果是:(1)本发明采用微通道反应器的溶液聚合方式,单体和引发剂在微通道中混合效果极佳,避免了放大效应,反应温度精确控制,反应过程中,由于氟丙烯酸酯单体的利用率的提高,对降低生产成本具有明显的优势;同时,聚合反应时间从传统的十几小时缩短为几十秒至几分钟,大大提高了反应效率,氟树脂的分子量分布范围变窄,性能得到进一步提高。(2)本发明中使用的微通道反应器材质为特种玻璃,计量泵的材质为聚四氟乙烯,耐腐蚀性优良。在微通道反应器中,从进料、混合、反应等过程为连续流聚合,有效避免了常规间歇性聚合中带来的需要额外配置和转移中出现的气体泄露等严重问题,安全环保,提高生产效率,适合工业化放大回收。(3)本发明具有操作工艺简单、能耗低、生产成本低廉、适用范围广、树脂分子量分布窄,疏水性能高的特点,提高了氟单体的利用率,适合工业化生产。附图说明图1为本发明氟树脂的合成工艺流程框图;图2为本发明使用的微通道反应器的直形通道模块;图3为本发明使用的微通道反应器的心形通道模块;图4为本发明所使用的微通道反应器的流程示意图。其中,1-进料口a,2-进料口b,3-进料口c,4-进料口d,5-预热模块a,6-预热模块b,7-预热模块c,8-预热模块d,9-混合反应模块e,10-混合反应模块f,11-混合反应模块g,12-出料口。具体实施方式为使本发明的目的、技术方案及优点更加清楚明白,以下举出优选实施例,对本发明进一步详细说明。然而,需要说明的是,说明书中列出的许多细节仅仅是为了使读者对本发明的一个或多个方面有一个透彻的理解,即便没有这些特定的细节也可以实现本发明的这些方面。实施例1根据图1所示的氟树脂的合成工艺流程图,利用图2、3的微通道反应器模块,所用装置为高通量微通道反应器(直形通道模块+心型通道模块),参照图4确定微通道反应器连接模式,混合反应模块数据流速和反应停留时间确定,导热介质为硅油。(1)称取40g全氟烷基丙烯酸酯、5g丙烯酸羟乙酯、45g丙烯酸丁酯,备用;称取10g苯乙烯、0.5g偶氮二异丁腈和100g乙酸丁酯预先混合成溶液,得到混合溶液ⅰ;设定单体的加料泵的流速比;(2)将混合溶液ⅰ通过加料泵从进料口a通入直通道预热模块a中,全氟烷基丙烯酸酯通过加料泵从进料口b通入直通道预热模块b中,然后再将预热后的混合溶液ⅰ和全氟烷基丙烯酸酯通入反应模块e中,混合反应后,得到混合液ⅱ;然后导入反应模块f中;(3)将丙烯酸丁酯通过加料泵从进料口c通入直通道预热模块c中,然后再通入反应模块f中与混合液ⅱ汇合反应,得到混合液ⅲ;然后再通入混合反应模块g中;(4)将丙烯酸羟乙酯通过加料泵从进料口d通入直通道预热模块d中,然后再通入混合反应模块g中与混合液ⅲ聚合反应;其中预热模块a、b、c、d的温度控制在40℃,混合反应模块e、f、g的温度控制在80℃,混合反应模块为心形通道模块;混合反应模块g中总停留时间为90s,反应产物经出料口流入收集容器,得到氟树脂。实施例2根据图1所示的氟树脂的合成工艺流程图,利用图2、3的微通道反应器模块,所用装置为高通量微通道反应器(直形通道模块+心型通道模块),参照图4确定微通道反应器连接模式,混合反应模块数据流速和反应停留时间确定,导热介质为硅油。(1)称取40g丙烯酸六氟丁酯、1g丙烯酸羟丙酯、40g甲基丙烯酸甲酯,备用;称取10g苯乙烯、0.5g偶氮二异庚腈和100g乙酸乙酯预先混合成溶液,得到混合溶液ⅰ;设定单体的加料泵的流速比;(2)将混合溶液ⅰ通过加料泵从进料口a通入直通道预热模块a中,丙烯酸六氟丁酯通过加料泵从进料口b通入直通道预热模块b中,然后再将预热后的混合溶液ⅰ和丙烯酸六氟丁酯通入反应模块e中,混合反应后,得到混合液ⅱ;然后导入反应模块f中;(3)将甲基丙烯酸甲酯通过加料泵从进料口c通入直通道预热模块c中,然后再通入反应模块f中与混合液ⅱ汇合反应,得到混合液ⅲ;然后再通入混合反应模块g中;(4)将丙烯酸羟丙酯通过加料泵从进料口d通入直通道预热模块d中,然后再通入混合反应模块g中与混合液ⅲ聚合反应;其中预热模块a、b、c、d的温度控制在45℃,混合反应模块e、f、g的温度控制在100℃,混合反应模块为心形通道模块;混合反应模块g中总停留时间为100s,反应产物经出料口流入收集容器,得到氟树脂。实施例3根据图1所示的氟树脂的合成工艺流程图,利用图2、3的微通道反应器模块,所用装置为高通量微通道反应器(直形通道模块+心型通道模块),参照图4确定微通道反应器连接模式,混合反应模块数据流速和反应停留时间确定,导热介质为硅油。(1)称取15g甲基丙烯酸十二氟庚酯、5g全氟烷基丙烯酸酯、3g甲基丙烯酸缩水甘油酯、2g丙烯酸羟丙酯、30g丙烯酸甲酯及30g丙烯酸正辛酯,备用;称取10gn-乙烯基吡咯酮、0.3g偶氮二异丁酸二甲酯、0.2g过氧化二苯甲酰和100g二甲苯预先混合成溶液,得到混合溶液ⅰ;设定单体的加料泵的流速比;(2)将混合溶液ⅰ通过加料泵从进料口a通入直通道预热模块a中,甲基丙烯酸十二氟庚酯及全氟烷基丙烯酸酯通过加料泵从进料口b通入直通道预热模块b中,然后再将预热后的混合溶液ⅰ和甲基丙烯酸十二氟庚酯及全氟烷基丙烯酸酯通入反应模块e中,混合反应后,得到混合液ⅱ;然后导入反应模块f中;(3)将丙烯酸甲酯及丙烯酸正辛酯通过加料泵从进料口c通入直通道预热模块c中,然后再通入反应模块f中与混合液ⅱ汇合反应,得到混合液ⅲ;然后再通入混合反应模块g中;(4)将甲基丙烯酸缩水甘油酯及丙烯酸羟丙酯通过加料泵从进料口d通入直通道预热模块d中,然后再通入混合反应模块g中与混合液ⅲ聚合反应;其中预热模块a、b、c、d的温度控制在50℃,混合反应模块e、f、g的温度控制在120℃,混合反应模块为心形通道模块;混合反应模块g中总停留时间为70s,反应产物经出料口流入收集容器,得到氟树脂。实施例4根据图1所示的氟树脂的合成工艺流程图,利用图2、3的微通道反应器模块,所用装置为高通量微通道反应器(直形通道模块+心型通道模块),参照图4确定微通道反应器连接模式,混合反应模块数据流速和反应停留时间确定,导热介质为硅油。(1)称取15g甲基丙烯酸十二氟庚酯及15g丙烯酸八氟戊酯、1g丙烯酸缩水甘油酯、15g丙烯酸甲酯及40g甲基丙烯酸丁酯,备用;称取10gn-乙烯基吡咯酮、0.5g偶氮二异丁腈、0.3g偶氮二异庚腈和100g二氯甲烷预先混合成溶液,得到混合溶液ⅰ;设定单体的加料泵的流速比;(2)将混合溶液ⅰ通过加料泵从进料口a通入直通道预热模块a中,甲基丙烯酸十二氟庚酯及丙烯酸八氟戊酯通过加料泵从进料口b通入直通道预热模块b中,然后再将预热后的混合溶液ⅰ和甲基丙烯酸十二氟庚酯及丙烯酸八氟戊酯通入反应模块e中,混合反应后,得到混合液ⅱ;然后导入反应模块f中;(3)将丙烯酸甲酯及甲基丙烯酸丁酯通过加料泵从进料口c通入直通道预热模块c中,然后再通入反应模块f中与混合液ⅱ汇合反应,得到混合液ⅲ;然后再通入混合反应模块g中;(4)将丙烯酸缩水甘油酯通过加料泵从进料口d通入直通道预热模块d中,然后再通入混合反应模块g中与混合液ⅲ聚合反应;其中预热模块a、b、c、d的温度控制在40℃,混合反应模块e、f、g的温度控制在60℃,混合反应模块为心形通道模块;混合反应模块g中总停留时间为300s,反应产物经出料口流入收集容器,得到氟树脂。实施例5根据图1所示的氟树脂的合成工艺流程图,利用图2、3的微通道反应器模块,所用装置为高通量微通道反应器(直形通道模块+心型通道模块),参照图4确定微通道反应器连接模式,混合反应模块数据流速和反应停留时间确定,导热介质为硅油。(1)称取40g全氟烷基丙烯酸酯、5g甲基丙烯酸十二氟庚酯、5g丙烯酸八氟戊酯、1g丙烯酸羟乙酯、2g甲基丙烯酸缩水甘油酯、2g丙烯酸缩水甘油酯、45g丙烯酸丁酯,备用;称取10g苯乙烯、0.2g偶氮二异庚腈、0.2g过氧化苯甲酸叔丁酯和100g甲苯预先混合成溶液,得到混合溶液ⅰ;设定单体的加料泵的流速比;(2)将混合溶液ⅰ通过加料泵从进料口a通入直通道预热模块a中,全氟烷基丙烯酸酯、甲基丙烯酸十二氟庚酯及丙烯酸八氟戊酯通过加料泵从进料口b通入直通道预热模块b中,然后再将预热后的混合溶液ⅰ和全氟烷基丙烯酸酯、甲基丙烯酸十二氟庚酯及丙烯酸八氟戊酯通入反应模块e中,混合反应后,得到混合液ⅱ;然后导入反应模块f中;(3)将丙烯酸丁酯通过加料泵从进料口c通入直通道预热模块c中,然后再通入反应模块f中与混合液ⅱ汇合反应,得到混合液ⅲ;然后再通入混合反应模块g中;(4)将丙烯酸羟乙酯、甲基丙烯酸缩水甘油酯、丙烯酸缩水甘油酯通过加料泵从进料口d通入直通道预热模块d中,然后再通入混合反应模块g中与混合液ⅲ聚合反应;其中预热模块a、b、c、d的温度控制在40℃,混合反应模块e、f、g的温度控制在80℃,混合反应模块为心形通道模块;混合反应模块g中总停留时间为90s,反应产物经出料口流入收集容器,得到氟树脂。如图4所示为本发明实施例1-5所使用的微通道反应器的流程示意图。微通道反应器包括进料口a-d,预热模块a-d,混合反应模块e-g;所述进料口a(1)与预热模块a(5)顺次连接,所述进料口b(2)与预热模块b(6)顺次连接,所述进料口c(3)与预热模块c(7)顺次连接,所述进料口d(4)与预热模块d(8)顺次连接;所述预热模块a(5)和预热模块b(6)的出口分别与混合反应模块e(9)连接,所述混合反应模块e(9)和预热模块c(7)的出口分别与混合反应模块f(10)连接,所述混合反应模块f(10)与预热模块d(8)的出口分别与混合反应模块g(11)连接,所述混合反应模块g(11)与出料口(12)连通。对比实施例1所用装置:高通量微通道反应器(直行通道模块+心型通道模块),确定微通道反应器连接模式,混合反应模块数据流速和反应停留时间确定,导热介质为硅油。先将40g全氟烷基丙烯酸酯、10g苯乙烯、0.5g偶氮二异丁腈和50g乙酸丁酯预先混合成溶液a,再将5g丙烯酸羟乙酯、45g丙烯酸丁酯和50g乙酸丁酯预先混合成溶液b;通过加料泵将溶液a通入直通道预热模块a中,通过加料泵将溶液b通入直通道预热模块b中,然后分别将预热后的溶液a和溶液b通入反应模块e、f、g聚合反应,其中预热模块温度控制在40℃,反应模块温度控制在80℃,反应模块中总停留时间为90秒,反应产物经出料口流入收集容器,得到氟树脂。对比实施例2所用装置:高通量微通道反应器(直行通道模块+心型通道模块),确定微通道反应器连接模式,混合反应模块数据流速和反应停留时间确定,导热介质为硅油。先将40g丙烯酸六氟丁酯、10g苯乙烯、0.5g偶氮二异丁腈和50g乙酸乙酯预先混合成溶液a,1g丙烯酸羟丙酯、40g甲基丙烯酸甲酯和50g乙酸乙酯预先混合成溶液b;通过加料泵将溶液a通入直通道预热模块a中,通过加料泵将溶液b通入直通道预热模块b中,然后分别将预热后的溶液a和溶液b通入反应模块e、f、g聚合反应,其中预热模块温度控制在45℃,反应模块温度控制在100℃,反应模块中总停留时间为100秒,反应产物经出料口流入收集容器,得到氟树脂。对比实施例3所用装置:1000ml夹套玻璃反应釜,导热介质为硅油。在1000ml的玻璃反应釜中,在氮气保护下,依次加入40g全氟烷基丙烯酸酯、5g丙烯酸羟乙酯、45g丙烯酸丁酯和10g苯乙烯,将以上单体用100g乙酸丁酯搅拌溶解,然后加入0.5g偶氮二异丁腈,将反应液在氮气保护下加热至80℃,保温聚合12h,将反应液温度冷却至室温,得到氟树脂,导入样品瓶中存放。将本发明实施例1-5及对比实施例1-3制备得到的氟树脂分别命名为样品1-8,其中对比实施例1-3制备得到的氟树脂依次为样品6、7及8。将制备得到的氟树脂样品1-8,经醋酸丁酯稀释后均匀涂敷于玻璃表面,然后在室温流平表干30min,再在80℃烘箱中烘焙30min,得基于氟树脂所构建的拒水性涂膜;室温冷却30min后,分别测定水、二碘甲烷及乙二醇在该涂膜表面的接触角(θ),测试结果见表1。同时分别测定实施例1、对比实施例1及对比实施例3制备得到的氟树脂(即样品1、样品6及样品8)的分子量分布及氟单体转化率,测试结果见表2。表1由表1可知,样品1-7的水、二碘甲烷及乙二醇在该涂膜表面的接触角均优于样品8,说明采用微通道反应器制备得到的氟树脂的疏水性能优于常规反应釜的传统工艺制备得到的氟树脂的疏水性能。表2样品mnmwpdi氟单体转化率1554001654002.9899%6372001582003.3293%8134001242009.2788%由表2可知,采用微通道反应器制备得到样品1及样品6相对于采用常规反应釜传统工艺制备得到的树脂分子量分布窄,氟单体的利用率高。其中样品1的效果要优于样品6,将乙烯基化合物、引发剂与溶剂混合,得到混合溶液ⅰ,再将含氟丙烯酸单体预热后混合,再将常规丙烯酸酯单体及功能性丙烯酸酯单体分别预热后依次混合进行聚合反应得到的氟树脂的分子量分布及氟单体转化率等性能要优于相对将所有原料预先混合成溶液a及溶液b,再预热后混合进行聚合反应得到的氟树脂的相应性能。说明本发明的采用微通道反应器制备氟树脂的方法能有效提高树脂的分子量,降低树脂的分子量分布范围,提高树脂成膜后的性能和单体的转化利用率,提升含氟单体的利用率,进而提升树脂的疏水性。综上,本发明本发明采用微通道反应器的溶液聚合方式,单体和引发剂在微通道中混合效果极佳,避免了放大效应,反应温度精确控制,反应过程中,由于氟丙烯酸酯单体的利用率的提高,对降低生产成本具有明显的优势;同时,聚合反应时间从传统的十几小时缩短为几十秒至几分钟,大大提高了反应效率,氟树脂的分子量分布范围变窄,性能得到进一步提高。本发明具有操作工艺简单、能耗低、生产成本低廉、适用范围广等特点,适合工业化生产。以上所述仅是本发明的优选实施方式,应当指出,对于本
技术领域:
的普通技术人员来说,在不脱离本发明原理的前提下,还可以作出若干改进和润饰,这些改进和润饰也应视为本发明的保护范围。当前第1页12