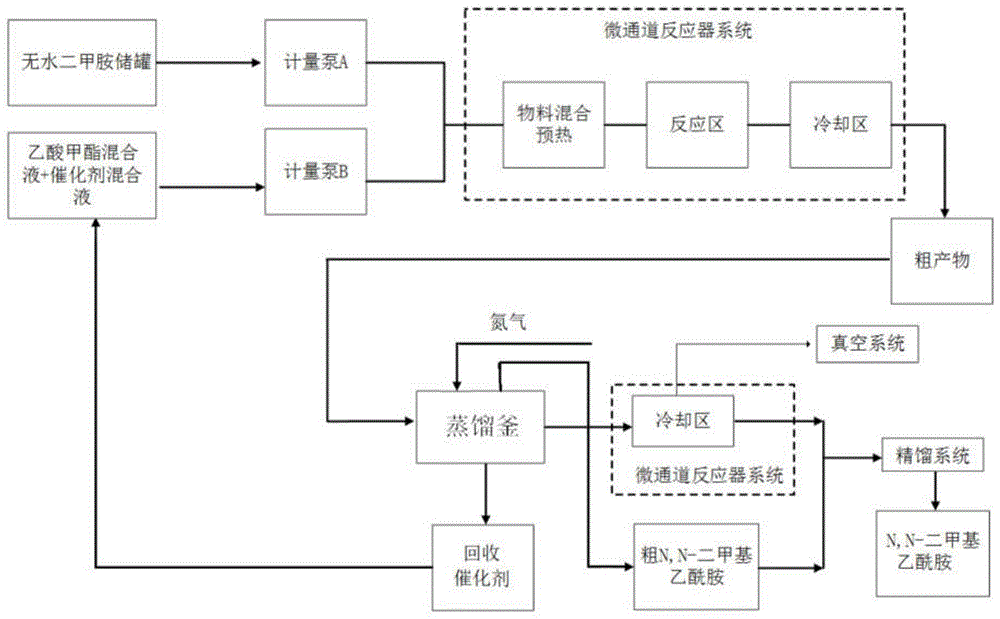
本发明属于有机合成领域,涉及一种在微通道反应器中进行液-液均相合成n,n-二甲基乙酰胺的方法。
背景技术:
:n,n-二甲基乙酰胺是一种高沸点、高极性的非质子化溶剂,具有热稳定性高、不易水解、腐蚀性低、毒性小等优点,主要用于合成材料和石油化工方面。目前,n,n-二甲基乙酰胺是许多有机合成反应的优良溶剂,国外多用于生产聚酰亚胺薄膜、可溶性聚酰亚胺、聚酰亚胺-聚全氟乙丙烯复合薄膜、聚酰亚胺(铝)薄膜、可溶性聚酰亚胺模塑粉等,国内主要用于高分子合成纤维纺丝和其他有机合成的优良极性溶剂。目前,合成和生产n,n-二甲基乙酰胺的技术工艺有乙酰氯法、酸酐法,乙酸法、三甲胺与一氧化碳碳基化法、乙酸甲酯法。从现有工艺中综合考虑,乙酸甲酯法工艺路线较短,毒性小,废液少、原料成本较低,选择性和收率较高,被认为是一种可供选择的工艺路线。巴斯福股份有限公司生产n,n-二甲基乙酰胺的方法的专利(cn101072748a)中报道了一种以聚thf二乙酸酯和甲醇酯交换制备聚thf过程中副产物乙酸甲酯甲醇溶液、二甲胺为原料,碱性催化剂,在喷射回路反应器反应(气-液混合反应),反应温度范围80~140℃,反应压力约在3~30巴,平均停留时间1h,反应产物经过中和、除盐、精馏后得到产品,产品纯度可达99.7%。西南化工研究设计院有限公司专利cn102807500a报道了以纯乙酸甲酯和二甲胺合成n,n-二甲基乙酰胺的工艺方法,甲醇为溶剂,三氧化钼或偏矾酸钠为催化剂,反应温度60~170℃,反应压力约在0.30~2.00mpa,反应时间4h,高压釜式搅拌反应器内反应(气-固-液多相催化反应),该专利中乙酸甲酯转化率高,n,n-二甲基乙酰胺收率高。在现有关于以乙酸甲酯为原料与二甲胺合成n,n-二甲基乙酰胺的报道中,主要的问题是反应器多为间歇釜式反应器,反应精馏等方式,反应多为气-液混合或气-液-固多相催化反应,反应时间长,且需高温、高压的反应条件,能耗较高,对操作要求高,安全风险较大。同时,现有技术中包含有以有机碱性催化剂合成n,n-二甲基乙酰胺,如类似甲醇钠类型有机碱。发现这类型有机碱完全溶于粗产物中时,与原料和产物分离就比较困难。以甲醇钠为例,且甲醇钠对水、空气、温度都较敏感,如甲醇钠在含水或遇水的情况下易形成氢氧化钠和甲醇;当温度超过126℃后,甲醇钠受热易分解。正是因为甲醇钠或类似有机碱作催化剂分离困难,反应后的催化剂甲醇钠,现多以酸性溶液中和,产生大量的具有较高cod含量的含盐含甲醇废水,处理工艺复杂。技术实现要素:本发明针对上述问题,提出一种在微通道反应器中进行液-液均相合成n,n-二甲基乙酰胺的方法,包括以下步骤:步骤s100,将甲醇钠溶解在乙酸甲酯甲醇溶液中得到物料a;步骤s200,将物料a和作为物料b的无水二甲胺分别以液相形式导入微通道反应器中并且以液-液均相形式在100~160℃下进行混合和反应得到含有n,n-二甲基乙酰胺的物料c;步骤s300,蒸馏物料c得到馏出物d和残留物e;步骤s400,将残留物e进行固-液分离得到含n,n-二甲基乙酰胺的物料f和含甲醇钠的物料g;其中,在步骤s100中,甲醇钠的至少部分来自于物料g。进一步地,在步骤s100中,乙酸甲酯甲醇溶液中,乙酸甲酯的含量为60.0~85.0wt%,优选78.0wt%;进一步地,乙酸甲酯甲醇溶液中还含有1.0~5.0wt%的四氢呋喃,例如,乙酸甲酯含量为78.0wt%,甲醇为20.0wt%,四氢呋喃为2.0wt%。进一步地,在步骤s100中,全部甲醇钠都来自于物料g。进一步地,在步骤s200中,反应压力为1.00~1.80mpa,反应时间为10~200秒,乙酸甲酯与二甲胺的摩尔比为1:0.80至1:1.30,催化剂与乙酸甲酯的质量比为0.005:1至0.15:1。进一步地,在步骤s300中,在蒸馏釜中蒸馏物料c,得到含甲醇、二甲胺、乙酸甲酯、四氢呋喃的馏出物d,以及含n,n-二甲基乙酰胺的残留物e。进一步地,在步骤s400中,向蒸馏釜中充入氮气将残留物e中的液体压出蒸馏釜得到含n,n-二甲基乙酰胺的物料f,并且得到留存于蒸馏釜中的含固体甲醇钠的物料g。进一步地,在步骤s100中,在蒸馏釜中加入乙酸甲酯甲醇溶液以溶解物料g中的甲醇钠;优选地,加入的乙酸甲酯与物料g中甲醇钠的质量比为0.003:1至0.20:1,优选0.005:1至0.15:1。进一步地,在步骤s300中,蒸馏温度为60~110℃,馏出物d用微通道反应器冷却,并用微通道反应器的背压阀控制蒸馏釜的压力为-0.05~-0.01mpa;优选地,微通道反应器内的冷却温度为-30~-10℃。本发明所选用的微通道反应器模块材质包括单晶硅、特种玻璃、陶瓷、涂有耐腐涂层的不锈钢或金属合金、聚四氟乙烯等,该微通道反应器由多组模块组装而成,模块间可并联组装或串联组装,模块将换热通路与反应通路集成与一体,或只含反应通路,并浸没在控温导热介质中。在换热通路或导热介质中配有热电偶,可用于测定换热通路中换热介质或外界导热介质的实际温度,模块的反应通道分为直型管状通道与增强传质型通道两种。本发明所用的微通道反应器为增强传质型微通道反应器,该反应系统由多块模块组装而成。该模块的材质为硼硅玻璃,反应系统可防腐耐压,耐压能力视材质不同而不同,且与操作温度有关,本系统反应最大安全压力为18bar。模块内微通道结构是以增强传质型通道,增强传质型通道是以“心型”结构单元串联组形成,微通道特征尺寸为0.2mm。与现有n,n-二甲基乙酰胺合成工艺技术相比较,本发明的在微通道反应器中催化合成n,n-二甲基乙酰胺工艺采用无水二甲胺液相进料方式,在微通道反应器进行液-液均相催化反应,能增强原料与催化剂活性中心的接触机会,从而有效提高原料的利用率。该工艺具有反应副产物少,反应条件控制精确,且连续安全生产,且在极短的时间内完成n-酰化反应,转化率高,n,n-二甲基乙酰胺收率高。同时,针对液相催化剂甲醇钠的回收问题,本发明采用微通道反应器,反应过程选择性高,副产物少,同时缩短催化剂的受热停留时间,通过减压蒸馏/过滤分离得到的回收甲醇钠催化剂能够保持较高的活性,可再用于合成n,n-二甲基乙酰胺,从而提高了催化剂的使用率,节约了成本。在本发明的一些实施方式中,以聚四氢呋喃装置的副产物乙酸甲酯甲醇溶液和无水二甲胺为反应原料,其中配置乙酸甲酯甲醇溶液并与催化剂甲醇钠混合形成物料a,以无水二甲胺溶液为物料b,其中催化剂为甲醇钠粉末。物料a、物料b用计量泵打入微通道反应器,在控制一定的工艺条件下合成n,n-二甲基乙酰胺,从反应器出口排出的液相混合物连续通入带搅拌的釜式储罐。将储罐内收集到的液相产物减压蒸馏出低沸物,冷凝后的粗产物转移至精馏塔中进行后续的精馏分离;高沸点物质n,n-二甲基乙酰胺用微正压排出;残留的固体催化剂加入适量的原料溶解,搅拌,作为回收催化剂以备后续循环使用。在一些情况下,由于物料b无水二甲胺,沸点7℃,大气压下为气体,为与乙酸甲酯形成液-液均相反应,将钢瓶中压缩液化的无水二甲胺转移至一定容积的储罐内,转移过程对储罐进行低温冷却,-20~-10℃,转移结束后通少量的氮气,保持储罐内压力在0.30~0.80mpa,使得无水二甲胺以液相进入微通道反应器内。在一些情况下,蒸馏分离后的液相粗产物经分段精馏(先常压粗馏脱除二甲胺、乙酸甲酯、甲醇、四氢呋喃等轻沸点物质,然后进行减压精馏),得到纯度大于≥99.90%的n,n-二甲基乙酰胺。在一些情况下,在残留的甲醇钠催化剂中加入一定量的乙酸甲酯甲醇溶液,搅拌使其溶解,然后用计量泵控制流量,与另一原料无水二甲胺(用计量泵控制流量)通入微通量反应器中,反应合成n,n-二甲基乙酰胺。在一些情况下,上述制备n,n-二甲基乙酰胺的方法中,催化剂为甲醇钠粉末,催化剂与乙酸甲酯质量比为0.003:1至0.20:1,优选为0.005:1至0.15:1;反应温度为80~180℃,优选100~160℃,例如120~140℃;反应压力为0.5~2.0mpa,优选1.0~1.80mpa;反应时间为5~300秒,优选10~200秒,更优选20~180秒,30~160秒,40~140秒,60~120秒,80~100秒等;乙酸甲酯与二甲胺摩尔比1:0.80至1:1.50,优选为1:0.90至1:1.30;减压蒸馏低沸物的表压为-0.09~-0.01mpa,优选-0.05~-0.01mpa;减压蒸馏温度为30~150℃,优选60~110℃。在一些情况下,精馏分离的塔釜采用电热套加热,精馏柱的填料外直径φ40mm,提留段和精馏段共1500mm,316lθ环填料。先在常压精馏中,塔顶采出过量的二甲胺、甲醇、乙酸甲酯等轻组分;然后在减压精馏中采出约10.00wt%的含甲醇及n,n-二甲基乙酰胺的混合溶液,然后收集纯度≥99.90%的n,n-二甲基乙酰胺,其中常压精馏的温度优选在50~120℃;减压精馏的表压为-0.09~-0.05mpa,温度优选为80~160℃。与现有的合成n,n-二甲基乙酰胺的工艺技术比较,本发明的一些优点如下:(1)本发明选择将原料无水二甲胺气体以液相进料的方式,进入反应器,反应物和催化剂形成液-液均相混合反应,增强了原料与催化剂活性中心的接触机会,从而有效提高原料的转化率和催化剂的选择性,降低副产物含量。(2)本发明中选择以微通道反应器为载体,相较于传统的间歇反应器或,反应过程中无反混,有效降低乙酸甲酯水解及副产物的产生;反应过程中,反应器内部独特的“心型”结构及构造,有效的强化了传质、传热效率,使得原料乙酸甲酯转化率高,n,n-二甲基乙酰胺收率高。(3)本发明以微通道反应器为载体,工艺过程中大大缩短了反应时间,同等反应条件下,若微通道反应工艺对应的原料转化率与传统的间歇釜式反应工艺相近时,本发明将传统工艺的反应时间几小时缩短至几十秒为单位。(4)本发明中以微通道反应器为载体,有效降低催化剂的副产物的产生,如水,同时反应时间短,催化剂的热反应时间短,能有效减少对催化剂的毒害,通过减压蒸馏分离催化剂与粗产物,且简化了催化剂分离、回收过程,回收催化剂催化效率仍然较高,有效的提高催化剂的利用率。(5)本发明中以连续化合成工艺,通过减少反应区的持液物料量,反应工艺过程可控性明显提升,相比于传统的间歇釜式反应器,有效的降低安全风险。附图说明图1示出了本发明的在微通道反应器中进行液-液均相合成n,n-二甲基乙酰胺的方法的一个实施方式的流程示意图。具体实施方式以下为本发明的非限定实施例,这些实施例的给出仅仅是为了说明的目的,并不能理解为对本发明的限定。基于本发明中的实施例,本领域普通技术人员在没有做出创造性劳动前提下所获得的所有其他实施例,都属于本发明保护的范围。除非另有说明,以下实施例中使用的试剂、仪器和设备都为商业上可获得的常规产品。实施例1按照附图1塔建实验装置,在微通道反应器中合成n,n-二甲基乙酰胺。因微通道反应器可以模块化设计,将部分模块作为反应合成区,将部分模块作为冷却物质的冷却区,冷却蒸馏分离低沸点物质。配置物料a:将乙酸甲酯甲醇溶液(其中乙酸甲酯的质量约为78.0wt%,甲醇为20.0wt%,四氢呋喃为2.0wt%)与甲醇钠(催化剂)粉末按比例配置,其中甲醇钠与乙酸甲酯的质量比为0.015:1,搅拌溶解。物料b:为无水二甲胺(储存于带压储罐内)。用液体计量泵以1.99kg/h的速度将物料a打入微通量反应器中,用液体计量泵以1.03kg/h的速度将物料b打入微通量反应器中,乙酸甲酯与无水二甲胺的摩尔比为1:1.1,在微通道反应器控制压力在1.5mpa,反应温度为140℃,停留时间(也即反应时间)约72秒,反应结束后,粗产物中n,n-二甲基乙酰胺的单程收率约97.50%。将合成段的液体粗产物收集到带加热搅拌的釜式储罐中,其中反应产物中n,n-二甲基乙酰胺含量为59.66wt%,甲醇含量为35.08wt%,二甲胺为3.43wt%,乙酸甲酯、四氢呋喃和副产物的总含量为1.83wt%。对釜体加热,温度控制约在80℃,用微通道反应器作冷却装置,冷却温度约-20℃,减压蒸馏,表压约-0.04mpa,将液体产物蒸馏冷凝收集,待低沸点物质排出后。充入约0.5mpa的n2进入釜体内,将含n,n-二甲基乙酰胺产物排出。然后用计量泵打入实例1等量的乙酸甲酯甲醇溶液,搅拌溶解,配置成物料a。同时用液体计量泵以1.99kg/h的速度将物料a打入微通量反应器中,用液体计量泵以1.03kg/h的速度将物料b打入微通量反应器中,乙酸甲酯与无水二甲胺的摩尔比为1:1.1,在微通道反应器控制压力在1.5mpa,反应温度为140℃,停留时间约72秒,进行回收催化剂的验证实验,反应结束后,反应粗产物中n,n-二甲基乙酰胺的单程收率约86.80%。蒸馏段馏出液的回收率为97.55%,其中n,n-二甲基乙酰胺含量为60.65wt%,甲醇含量为35.66wt%,二甲胺为3.03wt%,乙酸甲酯、四氢呋喃和副产物的总含量为0.66wt%。塔釜采用电热套加热,精馏柱的填料外直径φ40mm,提留段和精馏段共1500mm,316lθ环填料。先常压精馏,塔顶采出过量的二甲胺、甲醇及乙酸甲酯等轻组分,然后减压精馏,表压约-0.08mpa,先收集含少量甲醇的n,n二甲基乙酰胺混合液,约占物料的10.00wt%,然后继续收集精馏馏出液,此时收集到的n,n-二甲基乙酰的产品纯度≥99.90%。实施例2在5l高压釜式加热搅拌反应器内中合成n,n-二甲基乙酰胺。常温下将1.967kg乙酸甲酯甲醇溶液(其中乙酸甲酯的质量约为78.0wt%,甲醇为20.0wt%,四氢呋喃为2.0wt%),以及0.023kg甲醇钠粉末加入高压反应釜,机械搅拌使甲醇钠溶解,约10~20min,且后续的加料过程和反应过程也要持续搅拌。然后用计量泵将1.03kg无水二甲胺(储存于带压储罐内)打入高压反应釜内。待加料结束后,通过程序控制升高温度,升温到140℃,升温过程压力自然升高,若温度达到140℃后,压力未到1.5mpa,充入氮气平衡压力。乙酸甲酯与二甲胺的摩尔比为1:1.1,甲醇钠与乙酸甲酯的质量比为0.015:1,反应温度为140℃,反应压力为1.5mpa,反应时间4h,反应结束后,粗产物中n,n-二甲基乙酰胺的单程收率约91.97%。按照实施例1中分离催化剂的方式,直接在反应釜内将反应后的物料分离出催化剂与粗产物,通过阀门控制加入等量的乙酸甲酯甲醇溶液,搅拌溶解,用作物料a,无水二甲胺为物料b,进入微通道反应器。反应过程和条件按照实施例1中回收催化剂的活性验证实验,用液体计量泵以1.99kg/h的速度将物料a打入微通量反应器中,用液体计量泵以1.03kg/h的速度将物料b打入微通量反应器中,乙酸甲酯与无水二甲胺的摩尔比为1:1.1,在微通道反应器控制压力在1.5mpa,反应温度为140℃,停留时间约72秒,反应结束后,反应粗产物中n,n-二甲基乙酰胺的单程收率为56.21%。实施例3配置物料a:将乙酸甲酯甲醇溶液(其中乙酸甲酯的质量约为78.0wt%,甲醇为20.0wt%,四氢呋喃为2.0wt%)与甲醇钠(催化剂)粉末按比例配置,其中甲醇钠与乙酸甲酯的质量比为0.015:1,搅拌溶解。物料b:为无水二甲胺(储存于带压储罐内)。同时用液体计量泵以1.99kg/h的速度将物料a打入微通量反应器中,用液体计量泵以1.03kg/h的速度将物料b打入微通量反应器中,反应温度为120℃,停留时间约72秒,其他反应条件同实施例1,反应结束后,粗产物中n,n-二甲基乙酰胺的单程收率约85.05%。实施例4按照实施例3物料比例配置物料a、b,其中物料a其他组分不变,甲醇钠与乙酸甲酯的质量比为0.00,然后用液体计量泵以1.99kg/h的速度将物料a打入微通量反应器中,用液体计量泵以1.03kg/h的速度将物料b打入微通量反应器中,停留时间72秒,其他反应条件参照实施例1,反应结束后,反应粗产物中n,n-二甲基乙酰胺的单程收率约2.53%。实施例5按照实施例3物料比例配置物料a、b,同时用液体计量泵以7.96kg/h的速度将物料a打入微通量反应器中,用液体计量泵以4.12kg/h的速度将物料b打入微通量反应器中,停留时间18秒,其他反应条件参照实施例1,反应结束后,粗产物中n,n-二甲基乙酰胺的单程收率约65.10%。实施例6按照实施例3物料比例配置物料a、b,同时用液体计量泵以3.98kg/h的速度将物料a打入微通量反应器中,用液体计量泵以2.06kg/h的速度将物料b打入微通量反应器中,停留时间约36秒,其他反应条件参照实施例1,反应结束后,粗产物中n,n-二甲基乙酰胺的单程收率约79.50%。实施例7按照实施例3物料比例配置物料a、b,同时用液体计量泵以1.59kg/h的速度将物料a打入微通量反应器中,用液体计量泵以0.82kg/h的速度将物料b打入微通量反应器中,停留时间约90秒,其他反应条件参照实例1,反应结束后,粗产物中n,n-二甲基乙酰胺的单程收率约98.20%。表1微通道反应器内不同停留时间对粗产物中nn-二甲基乙酰胺收率的影响实施例停留时间(秒)n,n-二甲基乙酰胺收率(%)17297.5051865.1063679.5079098.20从表1可以看出,随着停留时间的增加,n,n-二甲基乙酰胺收率也随之增加。因此,若需要较高的单程收率,可以采用较长的停留时间。表2不同催化剂、含量及反应器对粗产物中n,n-二甲基乙酰胺收率的影响备注:如0.015:1指代是甲醇钠与甲醇钠与乙酸甲酯的质量比为0.015:1;新鲜催化剂指外购,未使用过的催化剂;回收催化剂代表进行反应后回收的催化剂,如实施例1,2。从表2可以看出:1)即便采用微通道反应器,若不加催化剂,n,n-二甲基乙酰胺收率仅为2.53%,说明催化剂对所述反应的重要性;2)当采用回收催化剂进行反应时,实施例1中从微通道反应器回收的催化剂后又在微通道反应器内回用,n,n-二甲基乙酰胺收率仍然高达86.80%,而实施例2中从间歇釜式反应器回收的催化剂后又在微通道反应器内回用,n,n-二甲基乙酰胺收率为56.21%,后者远低于前者,这可能是因为微通道反应器能够有效降低催化剂的副产物(如水)的产生,同时反应时间短,催化剂的热反应时间短,能有效减少对催化剂的毒害,因此回收的催化剂催化效率仍然较高,有效的提高了催化剂的利用率。以上所述,仅是本发明的较佳实施例,并非对本发明作任何形式上的限制,凡是依据本发明的技术实质对以上实施例所作的任何简单修改、等同变化,均落入本发明的保护范围之内。当前第1页12