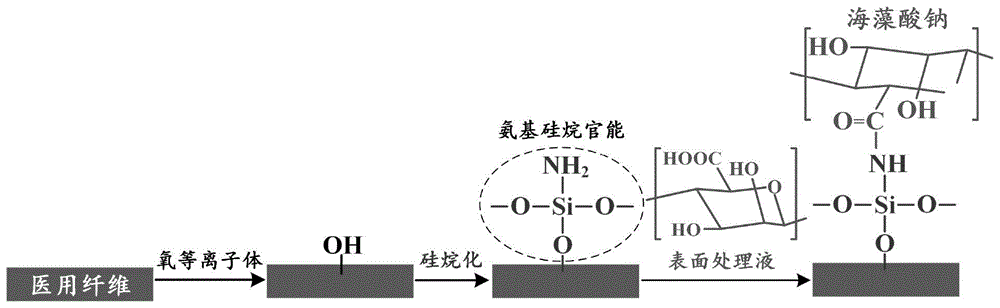
本发明涉及医用复合材料
技术领域:
,尤其涉及一种高强度医用纤维复合材料的制备方法。
背景技术:
:天然水凝胶是由天然原料制成的三维网络高分子聚合物,可以吸收大量水分,并束缚在水凝胶三维网状结构中,吸水保湿性强,其中,海藻酸钠水凝胶具有良好的生物相容性和低毒性,已经在食品、药品和生物医学等领域得到了广泛的应用。然而,与人工合成的高分子聚合物相比,海藻酸钠水凝胶的机械性能较差(刚度和强度较低),外力作用下容易碎裂,所以在单独使用时往往难以满足实际应用要求,只能应用在敷料、吸水填料和载药剂等对机械性能要求很低的产品中。随着医疗技术的发展,临床上对人工皮肤、人工肌肉、人工肌腱等组织修复材料的需求与日俱增,因此,如何在保留优异生物兼容性和吸水保湿性的同时,显著增强海藻酸钠水凝胶的机械性能,提高其实用性,是亟待解决的关键问题。目前,科研人员普遍通过聚合物复合法来提高天然水凝胶的机械性能,即通过互穿网络技术将两种聚合物结合,使两者之间产生互补和协同效用,从而克服单一水凝胶的缺陷,例如中国发明专利cn104311841a公开了一种高强度共价/离子互穿网络易塑形凝胶的制备方法,并进一步公开了其所制备材料的拉伸强度可以达到1.8mpa。这种互穿网络技术仅仅是在分子层面改进高分子聚合物的三维网络结构,对材料整体的机械性能,尤其是强度和刚度的提高有限,一般不超过2个数量级,仍无法达到人工肌肉和人工肌腱等所需的负载能力。因此,很有必要寻找一种可以将海藻酸钠水凝胶的刚度和强度提高2-3个数量级的方法。技术实现要素:针对现有技术中存在的问题,本发明要解决的技术问题是:海藻酸钠水凝胶的机械性能较差,刚度和强度较低,外力作用下容易碎裂,所以在单独使用时往往难以满足实际应用要求。本发明解决其技术问题所采用的技术方案是:本发明提供一种高强度医用纤维复合材料,包括海藻酸钠水凝胶和纤维骨架,所述纤维骨架完全嵌入海藻酸钠水凝胶中,纤维骨架表面接枝有化学锚定点与海藻酸钠水凝胶化学键合。具体地,所述纤维骨架由若干根支撑层纤维和若干根增强层纤维复合而成,所述增强层纤维位于支撑层纤维的上方,增强层纤维与支撑层纤维相互正交。具体地,所述若干根增强层纤维等间距排列,所述支撑层纤维若干根等间距排列。具体地,所述增强层纤维相邻两根纤维之间的间距为0.4-0.8mm,所述支撑层纤维相邻两根纤维之间的间距为1.2-1.6mm。具体地,所述增强层纤维为涤纶纤维、尼龙纤维或聚醚醚酮树脂纤维,增强层纤维直径为0.1-0.3mm。具体地,所述支撑层纤维为涤纶纤维、尼龙纤维或聚醚醚酮树脂纤维,支撑层纤维直径为0.1-0.3mm。具体地,所述化学锚定点是纤维骨架表面经表面处理液浸泡后的氨基硅烷官能团。具体地,所述表面处理液是将1g海藻酸钠、241mgsolfo-nhs、178mgedc溶解于100mlmes水合物中而成。具体地,所述海藻酸钠的分子量为26000-28000。具体地,一种高强度医用纤维复合材料的制备方法,按照以下步骤进行:(1)将增强层纤维和支撑层纤维加热软化,将纤维直径拉伸至0.1-0.3mm,然后,对得到的纤维进行冷却,得到备用纤维;(2)使用等离子体清洗机对步骤(1)得到的备用纤维进行等离子体刻蚀,刻蚀气体为氧气,刻蚀功率为30w-40w,刻蚀时间为5min-10min;(3)将等离子体刻蚀后的纤维立即浸泡在质量浓度为2.5%的kh550水溶液中,进行3h的硅烷化处理后,用去离子水和乙醇清洗增强层纤维和支撑层纤维,干燥后备用;(4)将步骤(3)处理后的增强层纤维和支撑层纤维通过组合模具实现两种纤维的定向、固定和锁紧得到增强层纤维与支撑层纤维相互正交复合在一起的纤维骨架;(5)将步骤(4)得到的纤维骨架连同组合模具一起浸泡在表面处理液中18-24h,实现纤维骨架表面化学接枝化学锚定点,然后将纤维骨架连同组合模具一起取出后,用去离子水清洗后,进行干燥备用;(6)将海藻酸钠配制成质量分数为3-4%的海藻酸钠水溶液,将溶液加热至50-60℃,搅拌均匀,在60khz下超声至溶液澄清后,静置12h,得到海藻酸钠水凝胶;(7)将步骤(6)得到的海藻酸钠水凝胶注入步骤(5)干燥后的组合模具的模具2中,使用刮板沿模具2的上表面反复涂抹后刮平,使得海藻酸钠水凝胶与纤维骨架充分接触,涂抹完成后,静置12h,得到预成型材料;(8)将步骤(7)得到的预成型材料连同组合模具一起浸泡在质量分数为1-3%的氯化钙水溶液中,固化4h,采用去离子水反复清洗掉材料表面残留的氯化钙后并干燥,按照需要的尺寸裁切组合模具中固化后的材料,并从模具上剥离,即得到高强度医用纤维复合材料。本发明的有益效果是:(1)本发明提出的医用纤维增强复合材料是将由尼龙、涤纶和聚醚酮树脂等高强度的医用纤维构成的纤维骨架嵌入到海藻酸钠水凝胶基质中,有效的提高了医用复合材料整体的机械性能,其刚度可提高3-4个数量级,拉伸强度可提高2-3个数量级,具备良好的生物相容性和安全性;(2)本发明提出的医用纤维增强复合材料具有良好的可设计性和可调节性,根据具体的应用需求可通过调节增强层纤维的疏密程度来调控材料整体的机械性能,如纤维的间距缩小,排布紧密,则复合材料整体的刚度和强度增加,柔性降低,如纤维的间距曾大,排布稀疏,则材料整体的刚度、强度降低,柔性增加;(3)本发明提出的医用纤维增强复合材料的制备方法只需使用简单的模具结构便可实现纤维定向、编织,疏密度调节、固定,锁紧和注模成型等功能,无需复杂、昂贵的机器设备,具有低成本、高效率、操作简单,可批量生产的特点;(4)本发明的方法具有普适性,可适用于尼龙、涤纶和聚醚酮树脂等具有不同物理、化学性质的医用纤维。附图说明图1:本发明高强度医用纤维复合材料的制备过程示意图。图2:本发明高强度医用纤维复合材料的结构示意图。图3:模具1的结构示意图。图4:组合模具的结构示意图。图5:利用模具1制作纤维骨架的过程示意图。图中:1、支撑层纤维,2、增强层纤维,3、化学锚定点,4、海藻酸钠水凝胶,5、模具1,6、模具2,7、固定基板,8、螺孔。具体实施方式现在结合附图对本发明作进一步详细的说明。本发明以下实施例中高强度医用纤维复合材料的制备过程如图1所示,图2是实施例1-7所制备高强度医用纤维复合材料的结构示意图。本发明以下实施例和对比例所使用的组合模具如图4所示,由模具1和模具2组成。如图3所示,模具1是四周各开设两排等间距圆孔的不锈钢板,不锈钢板的厚度为1-3mm,不锈钢板横向相邻两排圆孔的间距为6mm,不锈钢板纵向相邻两排圆孔的间距为5mm,孔的直径为0.2-0.4mm,不锈钢板横向分布的任意一排圆孔的圆心距为1.2-1.6mm,不锈钢板纵向分布的任意一排圆孔的圆心距为0.4-0.8mm,不锈钢板横向设置有2-1,2-2,2-3,2-4,纵向设置有1-1,1-2,1-3,1-4,其中,1-2与1-3以及2-2与2-3的圆孔一一对应;模具2是特氟龙材料制成的厚度为0.25-0.5mm,内边框长×宽=29mm×68mm,边框宽度为3-4mm,使用时,支撑层纤维依次穿过模具1上2-1,2-2,2-3,2-4设置的一一对应的圆孔并锁紧,增强层纤维依次穿过模具1上1-1,1-2,1-3,1-4设置的一一对应的圆孔并锁紧,然后,将模具2的四个边框正好落在模具1四周相对应的两排圆孔之间的无孔区域,并使用螺纹连接的方法将模具1和模具2共同固定在基板上(在组合模具上制作的纤维骨架如图5所示),之后,在模具2内注入海藻酸钠水凝胶并进行后续操作。本发明以下实施例和对比例所使用的表面处理液是将1g海藻酸钠(分子量26000-28000)、241mgn-羟基硫代琥珀酰亚胺(solfo-nhs,cas:106627-54-7)、178mg1-乙基-(3-二甲基氨基丙基)碳二亚胺(edc,cas:25952-53-8)溶解于100ml吗啉乙磺酸水合物(mes水合物,cas:1266615-59-1)中而成。本发明以下实施例和对比例所采用海藻酸钠的分子量为26000-28000。实施例1(1)将涤纶纤维、聚醚醚酮树脂纤维加热软化、拉伸、冷却后,获得长度为100mm的纤维,其中涤纶纤维直径为0.12±0.01mm,聚醚醚酮树脂纤维直径为0.16±0.01mm;(2)使用等离子体清洗机对步骤(1)得到的涤纶纤维和聚醚醚酮树脂纤维进行等离子体刻蚀,刻蚀气体为氧气,涤纶纤维的刻蚀功率为30w,涤纶纤维的刻蚀时间为5min;聚醚醚酮树脂纤维的刻蚀功率为40w,刻蚀时间为10min(3)将等离子体刻蚀后的涤纶纤维和聚醚醚酮树脂纤维立即浸泡在质量浓度为2.5%的kh550水溶液中,进行3h的硅烷化处理后,用去离子水和乙醇清洗涤纶纤维和聚醚醚酮树脂纤维,干燥后备用;(4)将步骤(3)处理后的9根涤纶纤维依次穿过模具1上1-1,1-2,1-3,1-4设置的一一对应的圆孔并锁紧,将步骤(3)处理后的36根聚醚醚酮树脂纤维依次穿过模具1上2-1,2-2,2-3,2-4设置的一一对应的圆孔并锁紧,即得到涤纶纤维和聚醚醚酮树脂纤维相互正交并复合在一起的纤维骨架;(5)将步骤(4)得到的纤维骨架连同组合模具一起浸泡在表面处理液中20h,实现纤维骨架表面化学接枝化学锚定点,然后将纤维骨架连同组合模具一起取出后,用去离子水清洗后,进行干燥备用;(6)将海藻酸钠配制成质量分数为3.5%的海藻酸钠水溶液,将溶液加热至60℃,搅拌均匀,在60khz下超声至溶液澄清后,静置12h,得到海藻酸钠水凝胶;(7)将步骤(6)得到的海藻酸钠水凝胶注入步骤(5)干燥后的组合模具的模具2中,使用刮板沿模具2的上表面反复涂抹后刮平,使得海藻酸钠水凝胶与纤维骨架充分接触,涂抹完成后,静置12h,得到预成型材料;(8)将步骤(7)得到的预成型材料连同组合模具一起浸泡在质量分数为2%的氯化钙水溶液中,固化4h,采用去离子水反复清洗掉材料表面残留的氯化钙后并干燥,按照需要的尺寸裁切组合模具中固化后的材料,并从模具上剥离,即得到高强度医用纤维复合材料。实施例2(1)将尼龙纤维加热软化、拉伸、冷却后,获得长度为100mm的备用纤维,其中,9根直径为0.12±0.01mm,36根直径为0.16±0.01mm;(2)使用等离子体清洗机对步骤(1)得到的尼龙纤维进行等离子体刻蚀,刻蚀气体为氧气,刻蚀功率为35w,刻蚀时间为7min;(3)将等离子体刻蚀后的尼龙纤维立即浸泡在质量浓度为2.5%的kh550水溶液中,进行3h的硅烷化处理后,用去离子水和乙醇清洗尼龙纤维,干燥后备用;(4)将步骤(3)处理后的9根尼龙纤维(直径为0.12±0.01mm)依次穿过模具1上1-1,1-2,1-3,1-4设置的一一对应的圆孔并锁紧,将36根尼龙纤维(直径为0.16±0.01mm)依次穿过模具1上2-1,2-2,2-3,2-4设置的一一对应的圆孔并锁紧,即得到尼龙纤维相互正交并复合在一起的纤维骨架;(5)将步骤(4)得到的纤维骨架连同组合模具一起浸泡在表面处理液中24h,实现纤维骨架表面化学接枝化学锚定点,然后将纤维骨架连同组合模具一起取出后,用去离子水清洗后,进行干燥备用;(6)将海藻酸钠配制成质量分数为4%的海藻酸钠水溶液,将溶液加热至50℃,搅拌均匀,在60khz下超声至溶液澄清后,静置12h,得到海藻酸钠水凝胶;(7)将步骤(6)得到的海藻酸钠水凝胶注入步骤(5)干燥后的组合模具的模具2中,使用刮板沿模具2的上表面反复涂抹后刮平,使得海藻酸钠水凝胶与纤维骨架充分接触,涂抹完成后,静置12h,得到预成型材料;(8)将步骤(7)得到的预成型材料连同组合模具一起浸泡在质量分数为3%的氯化钙水溶液中,固化4h,采用去离子水反复清洗掉材料表面残留的氯化钙后并干燥,按照需要的尺寸裁切组合模具中固化后的材料,并从模具上剥离,即得到高强度医用纤维复合材料。实施例3(1)将尼龙纤维、聚醚醚酮树脂纤维加热软化、拉伸、冷却后,获得长度为100mm的备用纤维,其中尼龙纤维直径为0.16±0.01mm,聚醚醚酮树脂纤维直径为0.12±0.01mm;(2)使用等离子体清洗机对步骤(1)得到的尼龙纤维和聚醚醚酮树脂纤维进行等离子体刻蚀,刻蚀气体为氧气,尼龙纤维的刻蚀功率为35w,涤纶纤维的刻蚀时间为7min;聚醚醚酮树脂纤维的刻蚀功率为40w,刻蚀时间为10min(3)将等离子体刻蚀后的尼龙纤维和聚醚醚酮树脂纤维立即浸泡在质量浓度为2.5%的kh550水溶液中,进行3h的硅烷化处理后,用去离子水和乙醇清洗尼龙纤维和聚醚醚酮树脂纤维,干燥后备用;(4)将步骤(3)处理后的17根尼龙纤维(直径为0.16±0.01mm)依次穿过模具1上1-1,1-2,1-3,1-4设置的一一对应的圆孔并锁紧,将步骤(3)处理后的36根聚醚醚酮树脂纤维(直径为0.12±0.01mm)依次穿过模具1上2-1,2-2,2-3,2-4设置的一一对应的圆孔并锁紧,即得到涤纶纤维和聚醚醚酮树脂纤维相互正交并复合在一起的纤维骨架;(5)将步骤(4)得到的纤维骨架连同组合模具一起浸泡在表面处理液中24h,实现纤维骨架表面化学接枝化学锚定点,然后将纤维骨架连同组合模具一起取出后,用去离子水清洗后,进行干燥备用;(6)将海藻酸钠配制成质量分数为3%的海藻酸钠水溶液,将溶液加热至60℃,搅拌均匀,在60khz下超声至溶液澄清后,静置12h,得到海藻酸钠水凝胶;(7)将步骤(6)得到的海藻酸钠水凝胶注入步骤(5)干燥后的组合模具的模具2中,使用刮板沿模具2的上表面反复涂抹后刮平,使得海藻酸钠水凝胶与纤维骨架充分接触,涂抹完成后,静置12h,得到预成型材料;(8)将步骤(7)得到的预成型材料连同组合模具一起浸泡在质量分数为1%的氯化钙水溶液中,固化4h,采用去离子水反复清洗掉材料表面残留的氯化钙后并干燥,按照需要的尺寸裁切组合模具中固化后的材料,并从模具上剥离,即得到高强度医用纤维复合材料。实施例4(1)将聚醚醚酮树脂纤维加热软化、拉伸、冷却后,获得长度为100mm的备用纤维,其中,17根直径为0.16±0.01mm,36根直径为0.12±0.01mm;(2)使用等离子体清洗机对步骤(1)得到的聚醚醚酮树脂纤维进行等离子体刻蚀,刻蚀气体为氧气,刻蚀功率为40w,刻蚀时间为10min;(3)将等离子体刻蚀后的聚醚醚酮树脂纤维立即浸泡在质量浓度为2.5%的kh550水溶液中,进行3h的硅烷化处理后,用去离子水和乙醇清洗聚醚醚酮树脂纤维,干燥后备用;(4)将步骤(3)处理后的17根聚醚醚酮树脂纤维(直径为0.16±0.01mm)依次穿过模具1上1-1,1-2,1-3,1-4设置的一一对应的圆孔并锁紧,将36根聚醚醚酮树脂纤维(直径为0.12±0.01mm)依次穿过模具1上2-1,2-2,2-3,2-4设置的一一对应的圆孔并锁紧,即得到聚醚醚酮树脂纤维相互正交并复合在一起的纤维骨架;(5)将步骤(4)得到的纤维骨架连同组合模具一起浸泡在表面处理液中24h,实现纤维骨架表面化学接枝化学锚定点,然后将纤维骨架连同组合模具一起取出后,用去离子水清洗后,进行干燥备用;(6)将海藻酸钠配制成质量分数为3.5%的海藻酸钠水溶液,将溶液加热至60℃,搅拌均匀,在60khz下超声至溶液澄清后,静置12h,得到海藻酸钠水凝胶;(7)将步骤(6)得到的海藻酸钠水凝胶注入步骤(5)干燥后的组合模具的模具2中,使用刮板沿模具2的上表面反复涂抹后刮平,使得海藻酸钠水凝胶与纤维骨架充分接触,涂抹完成后,静置12h,得到预成型材料;(8)将步骤(7)得到的预成型材料连同组合模具一起浸泡在质量分数为2%的氯化钙水溶液中,固化4h,采用去离子水反复清洗掉材料表面残留的氯化钙后并干燥,按照需要的尺寸裁切组合模具中固化后的材料,并从模具上剥离,即得到高强度医用纤维复合材料。实施例5(1)将尼龙纤维、聚醚醚酮树脂纤维加热软化、拉伸、冷却后,获得长度为100mm的备用纤维,其中,尼龙纤维直径为0.16±0.01mm,聚醚醚酮树脂纤维直径为0.12±0.01mm;(2)使用等离子体清洗机对步骤(1)得到的尼龙纤维和聚醚醚酮树脂纤维进行等离子体刻蚀,刻蚀气体为氧气,尼龙纤维的刻蚀功率为35w,涤纶纤维的刻蚀时间为7min;聚醚醚酮树脂纤维的刻蚀功率为40w,刻蚀时间为10min(3)将等离子体刻蚀后的尼龙纤维和聚醚醚酮树脂纤维立即浸泡在质量浓度为2.5%的kh550水溶液中,进行3h的硅烷化处理后,用去离子水和乙醇清洗尼龙纤维和聚醚醚酮树脂纤维,干燥后备用;(4)将步骤(3)处理后的9根尼龙纤维(直径为0.16±0.01mm)依次穿过模具1上1-1,1-2,1-3,1-4设置的一一对应的圆孔并锁紧,将步骤(3)处理后的36根聚醚醚酮树脂纤维(直径为0.12±0.01mm)依次穿过模具1上2-1,2-2,2-3,2-4设置的一一对应的圆孔并锁紧,即得到尼龙纤维和聚醚醚酮树脂纤维相互正交并复合在一起的纤维骨架;(5)将步骤(4)得到的纤维骨架连同组合模具一起浸泡在表面处理液中24h,实现纤维骨架表面化学接枝化学锚定点,然后将纤维骨架连同组合模具一起取出后,用去离子水清洗后,进行干燥备用;(6)将海藻酸钠配制成质量分数为3.5%的海藻酸钠水溶液,将溶液加热至60℃,搅拌均匀,在60khz下超声至溶液澄清后,静置12h,得到海藻酸钠水凝胶;(7)将步骤(6)得到的海藻酸钠水凝胶注入步骤(5)干燥后的组合模具的模具2中,使用刮板沿模具2的上表面反复涂抹后刮平,使得海藻酸钠水凝胶与纤维骨架充分接触,涂抹完成后,静置12h,得到预成型材料;(8)将步骤(7)得到的预成型材料连同组合模具一起浸泡在质量分数为2%的氯化钙水溶液中,固化4h,采用去离子水反复清洗掉材料表面残留的氯化钙后并干燥,按照需要的尺寸裁切组合模具中固化后的材料,并从模具上剥离,即得到高强度医用纤维复合材料。实施例6(1)将涤纶纤维加热软化、拉伸、冷却后,获得长度为100mm的备用纤维,其中9根直径为0.16±0.01mm,36根直径为0.12±0.01mm;(2)使用等离子体清洗机对步骤(1)得到的涤纶纤维和聚醚醚酮树脂纤维进行等离子体刻蚀,刻蚀气体为氧气,涤纶纤维的刻蚀功率为30w,涤纶纤维的刻蚀时间为5min;(3)将等离子体刻蚀后的涤纶纤维立即浸泡在质量浓度为2.5%的kh550水溶液中,进行3h的硅烷化处理后,用去离子水和乙醇清洗涤纶纤维,干燥后备用;(4)将步骤(3)处理后的9根涤纶纤维(直径为0.16±0.01mm)依次穿过模具1上1-1,1-2,1-3,1-4设置的一一对应的圆孔并锁紧,将步骤(3)处理后的36根涤纶纤维(直径为0.12±0.01mm)依次穿过模具1上2-1,2-2,2-3,2-4设置的一一对应的圆孔并锁紧,即得到涤纶纤维相互正交并复合在一起的纤维骨架;(5)将步骤(4)得到的纤维骨架连同组合模具一起浸泡在表面处理液中24h,实现纤维骨架表面化学接枝化学锚定点,然后将纤维骨架连同组合模具一起取出后,用去离子水清洗后,进行干燥备用;(6)将海藻酸钠配制成质量分数为3.5%的海藻酸钠水溶液,将溶液加热至60℃,搅拌均匀,在60khz下超声至溶液澄清后,静置12h,得到海藻酸钠水凝胶;(7)将步骤(6)得到的海藻酸钠水凝胶注入步骤(5)干燥后的组合模具的模具2中,使用刮板沿模具2的上表面反复涂抹后刮平,使得海藻酸钠水凝胶与纤维骨架充分接触,涂抹完成后,静置12h,得到预成型材料;(8)将步骤(7)得到的预成型材料连同组合模具一起浸泡在质量分数为2%的氯化钙水溶液中,固化4h,采用去离子水反复清洗掉材料表面残留的氯化钙后并干燥,按照需要的尺寸裁切组合模具中固化后的材料,并从模具上剥离,即得到高强度医用纤维复合材料。实施例7(1)将涤纶纤维和尼龙纤维加热软化、拉伸、冷却后,获得长度为100mm的备用纤维,其中涤纶纤维直径为0.16±0.01mm,尼龙纤维直径为0.12±0.01mm;(2)使用等离子体清洗机对步骤(1)得到的涤纶纤维和尼龙纤维进行等离子体刻蚀,刻蚀气体为氧气,涤纶纤维的刻蚀功率为30w,涤纶纤维的刻蚀时间为5min;(3)将等离子体刻蚀后的涤纶纤维和尼龙纤维立即浸泡在质量浓度为2.5%的kh550水溶液中,进行3h的硅烷化处理后,用去离子水和乙醇清洗涤纶纤维和尼龙纤维,干燥后备用;(4)将步骤(3)处理后的17根涤纶纤维(直径为0.16±0.01mm)依次穿过模具1上1-1,1-2,1-3,1-4设置的一一对应的圆孔并锁紧,将步骤(3)处理后的36根尼龙纤维(直径为0.12±0.01mm)依次穿过模具1上2-1,2-2,2-3,2-4设置的一一对应的圆孔并锁紧,即得到涤纶纤维相互正交并复合在一起的纤维骨架;(5)将步骤(4)得到的纤维骨架连同组合模具一起浸泡在表面处理液中24h,实现纤维骨架表面化学接枝化学锚定点,然后将纤维骨架连同组合模具一起取出后,用去离子水清洗后,进行干燥备用;(6)将海藻酸钠配制成质量分数为3.5%的海藻酸钠水溶液,将溶液加热至60℃,搅拌均匀,在60khz下超声至溶液澄清后,静置12h,得到海藻酸钠水凝胶;(7)将步骤(6)得到的海藻酸钠水凝胶注入步骤(5)干燥后的组合模具的模具2中,使用刮板沿模具2的上表面反复涂抹后刮平,使得海藻酸钠水凝胶与纤维骨架充分接触,涂抹完成后,静置12h,得到预成型材料;(8)将步骤(7)得到的预成型材料连同组合模具一起浸泡在质量分数为2%的氯化钙水溶液中,固化4h,采用去离子水反复清洗掉材料表面残留的氯化钙后并干燥,按照需要的尺寸裁切组合模具中固化后的材料,并从模具上剥离,即得到高强度医用纤维复合材料。对比例1同实施例4,不同之处在于:(1)将聚醚醚酮树脂纤维加热软化、拉伸、冷却后,获得长度为100mm的备用纤维,其中,17根直径为0.16±0.01mm,36根直径为0.12±0.01mm;(2)将聚醚醚酮树脂纤维浸泡在质量浓度为2.5%的kh550水溶液中,进行3h的硅烷化处理后,用去离子水和乙醇清洗聚醚醚酮树脂纤维,干燥后备用;(3)将步骤(2)处理后的17根聚醚醚酮树脂纤维(直径为0.16±0.01mm)依次穿过模具1上1-1,1-2,1-3,1-4设置的一一对应的圆孔并锁紧,将36根聚醚醚酮树脂纤维(直径为0.12±0.01mm)依次穿过模具1上2-1,2-2,2-3,2-4设置的一一对应的圆孔并锁紧,即得到聚醚醚酮树脂纤维相互正交并复合在一起的纤维骨架;(4)将步骤(3)得到的纤维骨架连同组合模具一起浸泡在表面处理液中24h,实现纤维骨架表面化学接枝化学锚定点,然后将纤维骨架连同组合模具一起取出后,用去离子水清洗后,进行干燥备用;(5)将海藻酸钠配制成质量分数为3.5%的海藻酸钠水溶液,将溶液加热至60℃,搅拌均匀,在60khz下超声至溶液澄清后,静置12h,得到海藻酸钠水凝胶;(6)将步骤(5)得到的海藻酸钠水凝胶注入步骤(4)干燥后的组合模具的模具2中,使用刮板沿模具2的上表面反复涂抹后刮平,使得海藻酸钠水凝胶与纤维骨架充分接触,涂抹完成后,静置12h,得到预成型材料;(7)将步骤(6)得到的预成型材料连同组合模具一起浸泡在质量分数为2%的氯化钙水溶液中,固化4h,采用去离子水反复清洗掉材料表面残留的氯化钙后并干燥,按照需要的尺寸裁切组合模具中固化后的材料,并从模具上剥离,即得到高强度医用纤维复合材料。对比例2同实施例4,不同之处在于:(1)将聚醚醚酮树脂纤维加热软化、拉伸、冷却后,获得长度为100mm的备用纤维,其中17根直径为0.16±0.01mm,36根直径为0.12±0.01mm;(2)使用等离子体清洗机对步骤(1)得到的聚醚醚酮树脂纤维进行等离子体刻蚀,刻蚀气体为氧气,刻蚀功率为40w,刻蚀时间为10min;(3)将步骤(2)处理后的17根聚醚醚酮树脂纤维(直径为0.16±0.01mm)依次穿过模具1上1-1,1-2,1-3,1-4设置的一一对应的圆孔并锁紧,将36根聚醚醚酮树脂纤维(直径为0.12±0.01mm)依次穿过模具1上2-1,2-2,2-3,2-4设置的一一对应的圆孔并锁紧,即得到聚醚醚酮树脂纤维相互正交并复合在一起的纤维骨架;(4)将步骤(3)得到的纤维骨架连同组合模具一起浸泡在表面处理液中24h,实现纤维骨架表面化学接枝化学锚定点,然后将纤维骨架连同组合模具一起取出后,用去离子水清洗后,进行干燥备用;(5)将海藻酸钠配制成质量分数为3.5%的海藻酸钠水溶液,将溶液加热至60℃,搅拌均匀,在60khz下超声至溶液澄清后,静置12h,得到海藻酸钠水凝胶;(6)将步骤(5)得到的海藻酸钠水凝胶注入步骤(4)干燥后的组合模具的模具2中,使用刮板沿模具2的上表面反复涂抹后刮平,使得海藻酸钠水凝胶与纤维骨架充分接触,涂抹完成后,静置12h,得到预成型材料;(7)将步骤(6)得到的预成型材料连同组合模具一起浸泡在质量分数为2%的氯化钙水溶液中,固化4h,采用去离子水反复清洗掉材料表面残留的氯化钙后并干燥,按照需要的尺寸裁切组合模具中固化后的材料,并从模具上剥离,即得到高强度医用纤维复合材料。对比例3同实施例4,不同之处在于:(1)将聚醚醚酮树脂纤维加热软化、拉伸、冷却后,获得长度为100mm的备用纤维,其中17根直径为0.16±0.01mm,36根直径为0.12±0.01mm;(2)使用等离子体清洗机对步骤(1)得到的聚醚醚酮树脂纤维进行等离子体刻蚀,刻蚀气体为氧气,刻蚀功率为40w,刻蚀时间为10min;(3)将等离子体刻蚀后的聚醚醚酮树脂纤维立即浸泡在质量浓度为2.5%的kh550水溶液中,进行3h的硅烷化处理后,用去离子水和乙醇清洗聚醚醚酮树脂纤维,干燥后备用;(4)将步骤(3)处理后的17根聚醚醚酮树脂纤维(直径为0.16±0.01mm)依次穿过模具1上1-1,1-2,1-3,1-4设置的一一对应的圆孔并锁紧,将36根聚醚醚酮树脂纤维(直径为0.12±0.01mm)依次穿过模具1上2-1,2-2,2-3,2-4设置的一一对应的圆孔并锁紧,即得到聚醚醚酮树脂纤维相互正交并复合在一起的纤维骨架;(5)将海藻酸钠配制成质量分数为3.5%的海藻酸钠水溶液,将溶液加热至60℃,搅拌均匀,在60khz下超声至溶液澄清后,静置12h,得到海藻酸钠水凝胶;(6)将步骤(5)得到的海藻酸钠水凝胶注入干燥后的组合模具的模具2中,使用刮板沿模具2的上表面反复涂抹后刮平,使得海藻酸钠水凝胶与纤维骨架充分接触,涂抹完成后,静置12h,得到预成型材料;(7)将步骤(6)得到的预成型材料连同组合模具一起浸泡在质量分数为2%的氯化钙水溶液中,固化4h,采用去离子水反复清洗掉材料表面残留的氯化钙后并干燥,按照需要的尺寸裁切组合模具中固化后的材料,并从模具上剥离,即得到高强度医用纤维复合材料。对比例4同实施例5,不同之处在于:(1)将尼龙纤维、聚醚醚酮树脂纤维加热软化、拉伸、冷却后,获得长度为100mm的备用纤维,其中,尼龙纤维直径为0.08±0.01mm,聚醚醚酮树脂纤维直径为0.12±0.01mm;(2)使用等离子体清洗机对步骤(1)得到的尼龙纤维和聚醚醚酮树脂纤维进行等离子体刻蚀,刻蚀气体为氧气,尼龙纤维的刻蚀功率为35w,涤纶纤维的刻蚀时间为7min;聚醚醚酮树脂纤维的刻蚀功率为40w,刻蚀时间为10min(3)将等离子体刻蚀后的尼龙纤维和聚醚醚酮树脂纤维立即浸泡在质量浓度为2.5%的kh550水溶液中,进行3h的硅烷化处理后,用去离子水和乙醇清洗尼龙纤维和聚醚醚酮树脂纤维,干燥后备用;(4)将步骤(3)处理后的9根尼龙纤维(直径为0.08±0.01mm)依次穿过模具1上1-1,1-2,1-3,1-4设置的一一对应的圆孔并锁紧,将步骤(3)处理后的36根聚醚醚酮树脂纤维(直径为0.12±0.01mm)依次穿过模具1上2-1,2-2,2-3,2-4设置的一一对应的圆孔并锁紧,即得到尼龙纤维和聚醚醚酮树脂纤维相互正交并复合在一起的纤维骨架;(5)将步骤(4)得到的纤维骨架连同组合模具一起浸泡在表面处理液中24h,实现纤维骨架表面化学接枝化学锚定点,然后将纤维骨架连同组合模具一起取出后,用去离子水清洗后,进行干燥备用;(6)将海藻酸钠配制成质量分数为3.5%的海藻酸钠水溶液,将溶液加热至60℃,搅拌均匀,在60khz下超声至溶液澄清后,静置12h,得到海藻酸钠水凝胶;(7)将步骤(6)得到的海藻酸钠水凝胶注入步骤(5)干燥后的组合模具的模具2中,使用刮板沿模具2的上表面反复涂抹后刮平,使得海藻酸钠水凝胶与纤维骨架充分接触,涂抹完成后,静置12h,得到预成型材料;(8)将步骤(7)得到的预成型材料连同组合模具一起浸泡在质量分数为2%的氯化钙水溶液中,固化4h,采用去离子水反复清洗掉材料表面残留的氯化钙后并干燥,按照需要的尺寸裁切组合模具中固化后的材料,并从模具上剥离,即得到高强度医用纤维复合材料。力学性能测试:取8g质量分数为3.5%的海藻酸钠水溶液,平铺于板框式有机玻璃模型板上,浸泡在2%的氯化钙溶液中,完全固化后,得到平均厚度为0.3mm的膜,并裁切成长60mm、宽9.8mm的空白试样。按照实施例1-7以及对比例1-4的方法,制备尺寸分别为(厚0.3mm、长60mm、宽9.8mm)的试样,并保证试样表面平整,无气泡、裂纹、分层、机械损伤等缺陷。在instronmodel5544万能材料试验机上进行拉伸试验,测定样品的拉伸弹性模量和拉伸强度,夹具标距为40mm,拉伸速度为0.5mm/s,每个样品做3个平行试验,取平均值,测试结果如下表1:表1测试项拉伸弹性模量(mpa)拉伸强度(mpa)空白试样0.0720.016实施例176.392.06实施例281.262.18实施例3326.4311.58实施例4443.5714.16实施例592.432.59实施例686.392.23实施例7306.439.78对比例1431.525.64对比例2435.416.79对比例3433.626.62对比例436.481.14由表1所示试验结果可知,应用本发明提出的制备方法制成的医用纤维增强复合材料的机械性能与海藻酸钠水凝胶单体相比有了显著的提升,其中拉伸弹性模量提高了3-4个数量级,断裂强度提高了2-3个数量级。细胞毒性测试:采用mtt比色法测定实施例1-7中的医用纤维增强复合材料的细胞毒性,所选用的细胞为小鼠成纤维细胞(l929),测试结果见表2:表2实施例相对生长率rgr(%)评级1101.302103.203105.604102.405101.106103.307104.20从表2中可以看出,实施例1-7制备得到的医用纤维增强复合材料对小鼠成纤维细胞(l929)的细胞毒性较低,细胞的相对生长率达100%以上,评级为0级(最优级),说明应用本发明制成的医用纤维增强复合材料可用作生物医用材料。以上述依据本发明的理想实施例为启示,通过上述的说明内容,相关工作人员完全可以在不偏离本项发明技术思想的范围内,进行多样的变更以及修改。本项发明的技术性范围并不局限于说明书上的内容,必须要根据权利要求范围来确定其技术性范围。当前第1页12