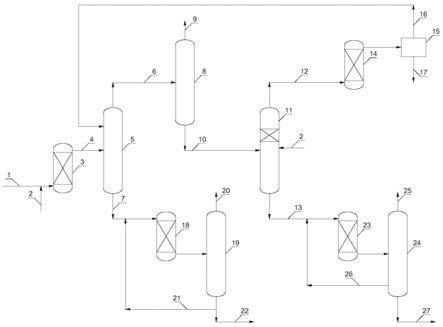
1.本发明涉及一种从碳四烃制备1-丁烯的方法和装置。
背景技术:2.1-丁烯是一种重要的化工原料,高纯度的1-丁烯主要用于生产线性低密度聚乙烯(lldpe)、高密度聚乙烯(hdpe)、聚1-丁烯塑料。此外,1-丁烯还被应用于生产二聚体1-辛烯、三聚体十二碳烯等烯烃产品,除可替代1-丁烯合成更好的lldpe、hdpe外,还可用于生产油品添加剂、表面活性剂以及增塑剂、印染剂、乳化剂等,市场前景非常广阔。1-丁烯的生产路线主要分为两大类:混合碳四分离法和乙烯二聚法。乙烯二聚法是在zegler-netta催化剂作用下,通过乙烯二聚生产高纯度1-丁烯。由于该法需要消耗宝贵的乙烯资源,面临生产成本偏高的巨大压力,已逐步退出市场。目前,1-丁烯的生产以混合碳四分离法为主。
3.无论是蒸汽裂解、催化裂化还是甲醇制烯烃等生产过程中,都会副产一定数量的碳四馏分,其中含有数量不等的异丁烷、异丁烯、1-丁烯、丁二烯、正丁烷、2-丁烯等,这些组分是用途广泛的化工原料,特别是碳四烯烃。随着碳四产量的不断增长,碳四烃的综合利用越来越受到人们的重视,尤其是碳四烯烃的有效利用已成为企业降本增效的有力途径。对于采用混合碳四分离法生产丁烯-1,通常的技术路线为:首先经过丁二烯抽提或氢化除去丁二烯,然后通过mtbe法除去异丁烯后,最后采用精密精馏法分离得到纯度较高的丁烯-1产品,同时得到富含2-丁烯的烃类混合物(主要是2-丁烯及正丁烷)。与1-丁烯、异丁烯和丁二烯相比,2-丁烯的工业应用价值较低,世界上大多数石化公司均把富含2-丁烯的剩余c4烃用作燃料。如果将2-丁烯通过异构化反应转化为1-丁烯,可实现增产1-丁烯的目的,对于提高碳四烃综合利用价值,提升企业经济效益意义重大。由于国家对乙醇汽油的全面推广实施,mtbe面临全面禁用,因此目前已不适合继续采用mtbe法来处理碳四烃中异丁烯和1-丁烯的分离。
4.cn101544532b介绍了一种以催化裂化副产碳四和乙烯裂解副产碳四为原料生产1-丁烯的方法,该法先将混合碳四通入气体分馏塔,塔顶得到含异丁烷、异丁烯和1-丁烯的轻组分物料;然后将该物料通入一分馏塔,塔顶分离出大部分异丁烷,塔釜得到含异丁烯和1-丁烯的重组分物料;接着对该股重组分物料进行深度脱硫及选择性加氢脱除丁二烯的处理;然后再通过mtbe醚化反应除去异丁烯;最后对醚后碳四进行精馏分离得到1-丁烯产品。
5.cn1990438b介绍了一种由碳四烃类的工业混合物制备1-丁烯的方法,该法以至少包含1-丁烯、异丁烯、正丁烷和2-丁烯类的碳四烃类的工业混合物i为原料,首先通过让异丁烯与水、醇或甲醛反应,或通过异丁烯的低聚,使碳四原料i中的部分异丁烯反应,得到标准压力下沸点高于30℃的物料ii;然后通过热分离方法脱除物料ii中未转化的碳四烃类,得到物料iii;接着采用蒸馏分离的方法对物料iii进行处理,分别得到至少包含1-丁烯和异丁烯的物料iv以及至少包含2-丁烯和正丁烷的基本上不含异丁烯的物料v;然后采用醚化方法使物料iv中异丁烯和醇vi发生反应,获得叔丁基醚vii的同时,脱除含1-丁烯物流中未转化的碳四烃并得到物料viii;最后通过蒸馏,从物料viii中分离出1-丁烯。
6.zl00129353.2介绍了一种利用含硫碳四馏分生产高纯度1-丁烯的方法,该法以脱除了异丁烯后的醚后碳四为原料,首先将原料通入第一个蒸馏塔,在塔顶分离出异丁烷、碳三馏分及部分含硫化合物轻组分,塔釜含1-丁烯、2-丁烯、正丁烷的重组分进入第二个蒸馏塔;在第二个蒸馏塔内丁二烯被选择性加氢,含硫化物进从塔釜采出,塔顶或侧线得到1-丁烯产品,必要时通过2-丁烯异构化为1-丁烯的催化蒸馏来生产1-丁烯产品。
7.cn104876785a介绍了一种由剩余碳四生产mtbe/1-丁烯的工艺及装置,该法以抽余碳四为原料,采用mtbe法脱除碳四原料中的异丁烯组分,其中mtbe的反应设备包括醚化反应器和催化蒸馏塔,脱除了异丁烯的碳四物料通过隔壁精馏分离出其中的1-丁烯产品。
8.以上各方法中,对于异丁烯和1-丁烯的分离均采用mtbe法,或直接以醚后碳四为原料生产1-丁烯,已不适合当前对异丁烯和1-丁烯体系的处理。
9.cn101514135b介绍了一种碳四混合物催化异构制1-丁烯的方法,该法将碳四物料加热到300~350℃后送入反应器,在固体酸催化剂作用下将2-丁烯异构化为1-丁烯,反应产物通入提浓塔,塔顶得到富含1-丁烯的混合物,塔釜重组分部分循环返回至反应器。该法对碳四原料的进料要求高,只能处理富含2-丁烯的碳四原料。
10.zl200410030737.4介绍了一种分离1-丁烯的方法,该法首先将碳四烯烃原料通入吸收塔,并在吸收塔内采用含可溶性银盐的吸收液选择性吸收碳四烯烃中1-丁烯和顺-2-丁烯;然后将吸收塔釜富含1-丁烯和顺-2-丁烯的吸收液通入萃取塔(或解析釜),将萃取塔顶富含1-丁烯和顺-2-丁烯的萃取液(或解析釜解析的含1-丁烯和顺-2-丁烯的气体)通入至精馏塔;最后在精馏塔塔顶得到1-丁烯产品。该法不涉及含异丁烯的碳四原料的处理,而如何对碳四烃中的异丁烯和1-丁烯组分进行有效处理是碳四烃高效利用的关键。
技术实现要素:11.本发明所要解决的技术问题是现有技术中碳四烃利用率不高、1-丁烯生产须转型升级的问题。针对该问题,本发明提供了一种新的从碳四烃制备1-丁烯的方法,该方法具有碳四综合利用率高、1-丁烯收率高的特点,特别适用于处理至少含有异丁烯及1-丁烯组分的碳四物流。
12.本发明的第一方面提供了一种从碳四烃制备1-丁烯的方法,包括以下步骤:
13.s1:将碳四原料和氢气混合进行选择性加氢反应,得到物料i;
14.s2:将所述物料i进行第一精馏分离,得到含异丁烯、1-丁烯和任选的异丁烷的物料ii和含2-丁烯和任选的正丁烷的物料iii;
15.s3:将所述物料ii进行第二精馏分离,得到含1-丁烯、异丁烯的物料iv;
16.s4:将所述物料iv进行反应精馏,得到含异丁烯的物料v和含2-丁烯的物料vi;
17.s5:将所述物料vi进行第二双键异构化反应,得到含1-丁烯的物料a。
18.根据本发明的一些实施方式,所述方法还包括步骤s6:将所述物料iii进行第一双键异构化反应,得到含1-丁烯的物料b。
19.根据本发明的一些实施方式,将所述物料b进行第三精馏分离,得到1-丁烯和循环碳四物料viii。
20.根据本发明的一些实施方式,所述物料viii返回s6中进行进行第一双键异构化反应。
21.根据本发明的一些实施方式,所述方法还包括步骤s7:将所述物料v进行骨架异构化反应得到含正丁烯的物料vii,所述物料vii返回返回s2中进行第一精馏分离。
22.根据本发明的一些实施方式,将所述物料a进行第四精馏分离,得到1-丁烯和循环2-丁烯物料。
23.根据本发明的一些实施方式,所述循环2-丁烯物料返回返回s5中第二双键异构化反应。
24.根据本发明的一些实施方式,所述碳四原料来自于fcc装置、乙烯蒸汽裂解装置或mto装置。
25.根据本发明的一些实施方式,所述碳四原料包括异丁烯和1-丁烯。
26.根据本发明的一些实施方式,所述碳四原料包括丁二烯、异丁烯和1-丁烯。
27.根据本发明的一些实施方式,所述碳四原料包括丁二烯、异丁烯、1-丁烯和2-丁烯。
28.根据本发明的一些实施方式,所述碳四原料包括异丁烷、异丁烯、1-丁烯、丁二烯、2-丁烯和正丁烷。
29.根据本发明的一些实施方式,以质量百分比计,所述碳四原料中至少含有3%的异丁烯,优选至少含有6%的异丁烯,更优选至少含有9%的异丁烯,进一步优选至少含有12%的异丁烯。
30.根据本发明的一些实施方式,所述物料iii中,异丁烯的质量流量/2-丁烯的质量流量的比值《1/200。
31.根据本发明的一些实施方式,所述物料iii中,正丁烷的质量流量/所述物料ii中正丁烷的质量流量的比值》20/1。
32.根据本发明的一些实施方式,所述物料vi中,异丁烯的质量流量/2-丁烯的质量流量的比值《1/100。
33.根据本发明的一些实施方式,所述物料vi中,2-丁烯质量流量/1-丁烯的质量流量的比值不小于85%,优选不小于90%,更优选不小于95%。
34.根据本发明的一些实施方式,所述物料viii的质量流量与所述物料iii的质量流量的比值(循环比)大于0.5,优选大于1,更优选大于1.5,进一步优选大于2。
35.根据本发明的一些实施方式,所述选择性加氢反应的条件包括:反应温度为30-100℃,反应压力为1.0-4.0mpag,反应空速为1-15hr-1
,氢气与丁二烯摩尔比为1.1-3.0。
36.根据本发明的一些实施方式,所述反应精馏在反应精馏塔中进行。
37.根据本发明的一些实施方式,所述反应精馏塔的塔顶操作压力为0.4-0.9mpag,氢烯摩尔比(氢气/正丁烯)为0.01-0.06。
38.根据本发明的一些实施方式,所述反应精馏塔内从上到下依次为精馏段、反应段和提馏段。
39.根据本发明的优选实施方式,所述精馏段理论板数为5-20,所述提馏段理论板数为60-120。
40.根据本发明的一些实施方式,所述第一双键异构化反应的条件包括:反应温度为280-400℃,反应压力为0.3-1.0mpag,反应空速为2-10hr-1
。
41.根据本发明的一些实施方式,所述第二双键异构化反应的条件包括:反应温度为
280-400℃,反应压力为0.3-1.0mpag,反应空速为2-10hr-1
。
42.根据本发明的一些实施方式,所述骨架异构化反应的条件包括:反应温度为350-600℃,反应压力为0.2-1.0mpag,反应空速为1-10hr-1
。
43.根据本发明的一些实施方式,所述选择性加氢反应采用的催化剂为负载在氧化铝载体上的包含选自镍、锌或钯中的至少一种的催化剂。
44.根据本发明的一些实施方式,所述反应精馏包括异构反应和精馏分离。
45.根据本发明的一些实施方式,所述异构反应的催化剂包括氧化铝载体负载包含选自镍、锌和钯中的至少一种的催化剂。
46.根据本发明的一些实施方式,所述催化剂装填量与所述物料iv每小时进料量的比值为0.1-0.8。
47.根据本发明的一些实施方式,所述第一双键异构化反应采用的催化剂为固体酸催化剂。
48.根据本发明的一些实施方式,所述第二双键异构化反应采用的催化剂为固体酸催化剂。
49.根据本发明的一些实施方式,所述骨架异构化反应采用的催化剂为负载在氧化铝载体上的钛基催化剂。
50.本发明的第二方面提供了一种从碳四烃制备1-丁烯的装置,包括选择性加氢反应器、第一精馏塔、第二精馏塔、反应精馏塔、第一双键异构化反应器和第二双键异构化反应器,其中,所述选择性加氢反应器和第一精馏塔相连,所述第二精馏塔与所述第一精馏塔的塔顶相连,所述反应精馏塔与所述第二精馏塔的塔釜相连,所述第一双键异构化反应器的入口与所述第一精馏塔的塔釜相连,所述第二双键异构化反应器的入口与所述反应精馏塔的塔釜相连。
51.根据本发明的一些实施方式,所述装置还包括第三精馏塔、第四精馏塔和任选的骨架异构化反应器,其中,所述第三精馏塔与所述第一双键异构化反应器的出口相连;所述第四精馏塔与所述第二双键异构化反应器的出口相连;所述骨架异构化反应器与所述反应精馏塔的塔顶相连;所述骨架异构化反应器通过骨架异构化反应产物分离单元与第一精馏塔相连。
52.根据本发明的一些实施方式,所述选择性加氢反应器用于将碳四原料和氢气混合进行选择性加氢反应,得到物料i。
53.根据本发明的一些实施方式,所述第一精馏塔用于将所述物料i进行第一精馏分离,塔顶得到含任选的异丁烷、异丁烯和1-丁烯的物料ii,塔釜得到含2-丁烯和任选的正丁烷的物料iii。
54.根据本发明的一些实施方式,所述第二精馏塔用于将所述物料ii进行第二精馏分离,塔釜得到含1-丁烯、异丁烯的物料iv。
55.根据本发明的一些实施方式,所述反应精馏塔用于将所述物料iv进行反应精馏,塔顶得到含异丁烯的物料v,塔釜得到含2-丁烯的物料vi。
56.根据本发明的一些实施方式,所述第一双键异构化反应器用于将所述物料iii进行第一双键异构化反应,得到含1-丁烯的物料a。
57.根据本发明的一些实施方式,所述第二双键异构化反应器用于将所述物料vi进行
第二双键异构化反应,得到含1-丁烯的物料b。
58.根据本发明的一些实施方式,所述第三精馏塔将所述物料a进行第三精馏分离,塔顶得到1-丁烯,塔釜得到循环碳四物料viii。
59.根据本发明的一些实施方式,所述物料viii返回至第一双键异构化反应器中进行第一双键异构化反应。
60.根据本发明的一些实施方式,所述第四精馏塔用于将所述物料b进行第四精馏分离,塔顶得到1-丁烯,塔釜得到循环2-丁烯物料。
61.根据本发明的一些实施方式,所述循环2-丁烯物料返回至第二双键异构化反应器中进行第二双键异构化反应。
62.根据本发明的一些实施方式,所述骨架异构化反应器用于将所述物料v进行骨架异构化反应得到含正丁烯的物料vii,所述物料vii返回至第一精馏分离塔中进行第一精馏分离。
63.本发明通过优化工艺流程及原料处理方式,采用选择性加氢技术、反应精馏技术、骨架异构技术以及双键异构技术等,在避免采用传统mtbe处理异丁烯/1-丁烯体系的同时,充分利用了碳四原料中包括异丁烯、1-丁烯、丁二烯、2-丁烯在内的所有烯烃资源生产1-丁烯。本发明的方法特别是针对经选择性加氢、反应精馏、骨架异构处理后得到的不同规格的2-丁烯物料,采用两台双键异构化反应器增产1-丁烯的配合运行模式,相较于采用单台双键异构化反应器处理所有2-丁烯物料的运行方式,在保证1-丁烯产量相同的条件下,可大大降低双键异构反应单元的循环量和装置规模,显著提升装置经济效益。本发明大幅提升了碳四烃的综合利用率和附加值,为传统mtbe/1-丁烯装置的升级转型提供了较好的技术路线,取得了较好的技术效果。
附图说明
64.图1为根据本发明的从碳四烃制备1-丁烯的工艺流程示意图。
65.图1中1为碳四原料,2为氢气,3为选择性加氢反应器,4为选择性加氢产物,5为第一精馏塔,6为第一精馏塔塔顶物料,7为第一精馏塔塔釜物料,8为第二精馏塔,9为第二精馏塔塔顶物料,10为第二精馏塔塔釜物料,11为反应精馏塔,12为反应精馏塔塔顶物料,13为反应精馏塔塔釜物料,14为骨架异构化反应器,15为骨架异构化反应产物分离单元,16为丁烯混合物,17为骨架异构化产物重组分,18为第一双键异构化反应器,19为第三精馏塔,20为第三精馏塔塔顶物料,21为第三精馏塔塔釜循环碳四,22为第三精馏塔塔釜外排碳四,23为第二双键异构化反应器,24为第四精馏塔,25为第四精馏塔塔顶物料,26为第四精馏塔侧线物料,27为第四精馏塔塔釜重组分。
具体实施方式
66.本发明提供了一种从碳四烃制备1-丁烯的方法,其采用图1所示的流程工艺,具体地,碳四原料1和氢气2进入选择性加氢反应器3,经选择性加氢反应后,碳四原料中的丁二烯被加氢为单烯烃。选择性加氢产物4进入第一精馏塔5,第一精馏塔塔顶得到含异丁烷、异丁烯、1-丁烯的物料6,塔釜得到含2-丁烯、正丁烷的物料7。第一精馏塔塔顶物料6进入第二精馏塔8,第二精馏塔塔顶排出含异丁烷的物料9,塔釜得到含1-丁烯、异丁烯的物料10。第
二精馏塔塔釜物料10与氢气2进入反应精馏塔11,在临氢条件下,塔内发生1-丁烯异构为2-丁烯的反应,同时也进行精馏分离,反应精馏塔塔顶得到含异丁烯的物料12,塔釜得到含2-丁烯的物料13。反应精馏塔塔顶物料12进入骨架异构化反应器14,反应器内异丁烯骨架异构为正丁烯,骨架异构化产物通过分离单元15进行分离,顶部丁烯混合物16循环返回至第一精馏塔5,底部排出重组分17。第一精馏塔塔釜物料7进入第一双键异构化反应器18,反应器内2-丁烯异构为1-丁烯。第一双键异构化产物进入第三精馏塔19,第三精馏塔塔顶得到1-丁烯物料20,塔釜得到含2-丁烯、正丁烷的馏出物,其中部分作为循环碳四21返回至第一双键异构化反应器18,部分作为外排碳四22排出。反应精馏塔塔釜物料13进入第二双键异构化反应器23,反应器内2-丁烯异构为1-丁烯。第二双键异构化产物进入第四精馏塔24,第四精馏塔塔顶得到1-丁烯物料25,侧线未反应的2-丁烯物料26循环返回至第二双键异构化反应器23,塔釜排出重组分27。
67.为使本发明容易理解,下面将结合实施例来详细说明本发明,这些实施例仅起说明性作用,并不局限于本发明的应用范围。
68.本发明中所使用的原料或组分若无特殊说明均可以通过商业途径或常规方法制得。
69.以下实施例采用图1所示的流程工艺,具体地,碳四原料1和氢气2进入选择性加氢反应器3,经选择性加氢反应后,碳四原料中的丁二烯被加氢为单烯烃。选择性加氢产物4进入第一精馏塔5,第一精馏塔塔顶得到含异丁烷、异丁烯、1-丁烯的物料6,塔釜得到含2-丁烯、正丁烷的物料7。第一精馏塔塔顶物料6进入第二精馏塔8,第二精馏塔塔顶排出含异丁烷的物料9,塔釜得到含1-丁烯、异丁烯的物料10。第二精馏塔塔釜物料10与氢气2进入反应精馏塔11,在临氢条件下,塔内发生1-丁烯异构为2-丁烯的反应,同时也进行精馏分离,反应精馏塔塔顶得到含异丁烯的物料12,塔釜得到含2-丁烯的物料13。反应精馏塔塔顶物料12进入骨架异构化反应器14,反应器内异丁烯骨架异构为正丁烯,骨架异构化产物通过分离单元15进行分离,顶部丁烯混合物16循环返回至第一精馏塔5,底部排出重组分17。第一精馏塔塔釜物料7进入第一双键异构化反应器18,反应器内2-丁烯异构为1-丁烯。第一双键异构化产物进入第三精馏塔19,第三精馏塔塔顶得到1-丁烯物料20,塔釜得到含2-丁烯、正丁烷的馏出物,其中部分作为循环碳四21返回至双键异构化反应器18,部分作为外排碳四22排出。反应精馏塔塔釜物料13进入第二双键异构化反应器23,反应器内2-丁烯异构为1-丁烯。第二双键异构化产物进入第四精馏塔24,第四精馏塔塔顶得到1-丁烯物料25,侧线未反应的2-丁烯物料26循环返回至第二双键异构化反应器23,塔釜排出重组分27。
70.【实施例1】
71.按图1所示,碳四原料组成(质量%,下同)为:异丁烷36.2%,异丁烯14.4%,丁二烯1.3%,1-丁烯:11.8%,2-丁烯:23.4%,正丁烷12.9%。采用本发明工艺流程,选择性加氢反应器入口温度40℃,反应压力1.4mpag,反应空速13hr-1
,氢气与丁二烯摩尔比2.8,反应器内催化剂为氧化铝负载金属钯;反应精馏塔内精馏段理论板数12,提馏段理论板数68,反应段内催化剂为氧化铝负载金属钯,催化剂装填量与反应精馏塔每小时进料量的比值0.8,塔顶操作压力0.5mpag,回流比46,氢烯摩尔比0.01;骨架异构化反应器入口温度460℃,反应压力0.4mpag,反应空速5hr-1
,反应器内催化剂为氧化铝负载金属钛;第一双键异构化反应器入口温度300℃,反应压力0.4mpag,反应空速3hr-1
;第二双键异构化反应器入口温度
300℃,反应压力0.4mpag,反应空速3hr-1
;两个双键异构反应器内催化剂都为氧化铝-氧化硅固体酸催化剂;第一双键异构化反应器进料循环比4.7。1-丁烯的收率为72.3%(质量,针对原料碳四1中的所有烯烃,下同)。
72.【实施例2】
73.按图1所示,碳四原料组成为:异丁烷36.2%,异丁烯14.4%,丁二烯1.3%,1-丁烯:11.8%,2-丁烯:23.4%,正丁烷12.9%。采用本发明工艺流程,选择性加氢反应器入口温度60℃,反应压力2.5mpag,反应空速10hr-1
,氢气与丁二烯摩尔比2.5,反应器内催化剂为氧化铝负载金属镍;反应精馏塔内精馏段理论板数10,提馏段理论板数85,反应段内催化剂为氧化铝负载金属钯,催化剂装填量与反应精馏塔每小时进料量的比值0.7,塔顶操作压力0.4mpag,回流比38,氢烯摩尔比0.02;骨架异构化反应器入口温度500℃,反应压力0.6mpag,反应空速6hr-1
,反应器内催化剂为氧化铝负载金属钛;第一双键双键异构化反应器入口温度320℃,反应压力0.6mpag,反应空速6hr-1
;第二双键异构化反应器入口温度300℃,反应压力0.4mpag,反应空速3hr-1
;两个双键异构反应器内催化剂都为氧化铝-氧化硅固体酸催化剂;第一双键异构化反应器进料循环比2.6。1-丁烯的收率为60.6%。
74.【实施例3】
75.按图1所示,碳四原料组成为:异丁烷4.6%,异丁烯38.7%,丁二烯3.9%,1-丁烯:25.1%,2-丁烯:18.5%,正丁烷9.2%。采用本发明工艺流程,选择性加氢反应器入口温度70℃,反应压力1.9mpag,反应空速5hr-1
,氢气与丁二烯摩尔比1.5,反应器内催化剂为氧化铝负载金属镍;反应精馏塔内精馏段理论板数7,提馏段理论板数112,反应段内催化剂为氧化铝负载金属镍,催化剂装填量与反应精馏塔每小时进料量的比值0.3,塔顶操作压力0.8mpag,回流比10,氢烯摩尔比0.02;骨架异构化反应器入口温度580℃,反应压力0.8mpag,反应空速2hr-1
,反应器内催化剂为氧化铝负载金属钛;第一双键异构化反应器入口温度330℃,反应压力0.8mpag,反应空速4hr-1
;第二双键异构化反应器入口温度350℃,反应压力0.6mpag,反应空速7hr-1
;两个双键异构反应器内催化剂都为氧化铝-氧化硅固体酸催化剂;第一双键异构化反应器进料循环比0.8。1-丁烯的收率为53.0%。
76.【实施例4】
77.按图1所示,碳四原料组成为:异丁烷4.6%,异丁烯38.7%,丁二烯3.9%,1-丁烯:25.1%,2-丁烯:18.5%,正丁烷9.2%。采用本发明工艺流程,选择性加氢反应器入口温度90℃,反应压力3.2mpag,反应空速8hr-1
,氢气与丁二烯摩尔比1.9,反应器内催化剂为氧化铝负载金属锌;反应精馏塔内精馏段理论板数13,提馏段理论板数95,反应段内催化剂为氧化铝负载金属锌,催化剂装填量与反应精馏塔每小时进料量的比值0.5,塔顶操作压力0.7mpag,回流比22,氢烯摩尔比0.04;骨架异构化反应器入口温度560℃,反应压力0.6mpag,反应空速3hr-1
,反应器内催化剂为氧化铝负载金属钛;第一双键异构化反应器入口温度330℃,反应压力0.9mpag,反应空速5hr-1
;第二双键异构化反应器入口温度390℃,反应压力0.3mpag,反应空速9hr-1
;两个双键异构反应器内催化剂都为氧化铝-氧化硅固体酸催化剂;第一双键异构化反应器进料循环比1.4。1-丁烯的收率为57.7%。
78.【实施例5】
79.按图1所示,碳四原料组成为:异丁烷2.7%,异丁烯5.5%,丁二烯2.1%,1-丁烯:20.6%,2-丁烯:64.8%,正丁烷4.3%。采用本发明工艺流程,选择性加氢反应器入口温度
80℃,反应压力2.7mpag,反应空速9hr-1
,氢气与丁二烯摩尔比2.2,反应器内催化剂为氧化铝负载金属锌;反应精馏塔内精馏段理论板数6,提馏段理论板数105,反应段内催化剂为氧化铝负载金属锌,催化剂装填量与反应精馏塔每小时进料量的比值0.4,塔顶操作压力0.5mpag,回流比17,氢烯摩尔比0.05;骨架异构化反应器入口温度380℃,反应压力0.9mpag,反应空速7hr-1
,反应器内催化剂为氧化铝负载金属钛;第一双键异构化反应器入口温度380℃,反应压力0.7mpag,反应空速8hr-1
;第二双键异构化反应器入口温度340℃,反应压力0.5mpag,反应空速6hr-1
;两个双键异构反应器内催化剂都为氧化铝-氧化硅固体酸催化剂;第一双键异构化反应器进料循环比4.8。1-丁烯的收率为83.2%。
80.【实施例6】
81.按图1所示,碳四原料组成为:异丁烷2.7%,异丁烯5.5%,丁二烯2.1%,1-丁烯:20.6%,2-丁烯:64.8%,正丁烷4.3%。采用本发明工艺流程,选择性加氢反应器入口温度50℃,反应压力3.0mpag,反应空速6hr-1
,氢气与丁二烯摩尔比2.4,反应器内催化剂为氧化铝负载金属钯;反应精馏塔内精馏段理论板数16,提馏段理论板数77,反应段内催化剂为氧化铝负载金属镍,催化剂装填量与反应精馏塔每小时进料量的比值0.6,塔顶操作压力0.5mpag,回流比40,氢烯摩尔比0.03;骨架异构化反应器入口温度420℃,反应压力0.4mpag,反应空速9hr-1
,反应器内催化剂为氧化铝负载金属钛;第一双键异构化反应器入口温度360℃,反应压力0.5mpag,反应空速5hr-1
;第二双键异构化反应器入口温度320℃,反应压力0.5mpag,反应空速4hr-1
;两个双键异构反应器内催化剂都为氧化铝-氧化硅固体酸催化剂;第一双键异构化反应器进料循环比5.7。1-丁烯的收率为87.6%。
82.【实施例7】
83.按图1所示,碳四原料组成为:异丁烷16.8%,异丁烯18.3%,丁二烯8.5%,1-丁烯:9.7%,2-丁烯:34.9%,正丁烷11.8%。采用本发明工艺流程,选择性加氢反应器入口温度60℃,反应压力3.5mpag,反应空速2hr-1
,氢气与丁二烯摩尔比1.6,反应器内催化剂为氧化铝负载金属镍;反应精馏塔内精馏段理论板数14,提馏段理论板数88,反应段内催化剂为氧化铝负载金属钯,催化剂装填量与反应精馏塔每小时进料量的比值0.2,塔顶操作压力0.6mpag,回流比33,氢烯摩尔比0.01;骨架异构化反应器入口温度550℃,反应压力0.3mpag,反应空速8hr-1
,反应器内催化剂为氧化铝负载金属钛;第一双键异构化反应器入口温度370℃,反应压力0.5mpag,反应空速3hr-1
;第二双键异构化反应器入口温度330℃,反应压力0.8mpag,反应空速5hr-1
;两个双键异构反应器内催化剂都为氧化铝-氧化硅固体酸催化剂;第一双键异构化反应器进料循环比2.9。1-丁烯的收率为61.5%。
84.【实施例8】
85.按图1所示,碳四原料组成为:异丁烷16.8%,异丁烯18.3%,丁二烯8.5%,1-丁烯:9.7%,2-丁烯:34.9%,正丁烷11.8%。采用本发明工艺流程,选择性加氢反应器入口温度70℃,反应压力3.8mpag,反应空速5hr-1
,氢气与丁二烯摩尔比1.4,反应器内催化剂为氧化铝负载金属钯;反应精馏塔内精馏段理论板数9,提馏段理论板数94,反应段内催化剂为氧化铝负载金属镍,催化剂装填量与反应精馏塔每小时进料量的比值0.3,塔顶操作压力0.4mpag,回流比27,氢烯摩尔比0.02;骨架异构化反应器入口温度520℃,反应压力0.7mpag,反应空速4hr-1
,反应器内催化剂为氧化铝负载金属钛;第一双键异构化反应器入口温度350℃,反应压力0.6mpag,反应空速7hr-1
;第二双键异构化反应器入口温度360℃,反
应压力0.7mpag,反应空速5hr-1
;两个双键异构反应器内催化剂都为氧化铝-氧化硅固体酸催化剂;双键异构化反应器进料循环比4.0。1-丁烯的收率为69.3%。
86.【对比例1】
87.在不采用传统mtbe法利用异丁烯和1-丁烯的条件下,按照采用传统的双键异构反应器技术从碳四烃制备1-丁烯的工艺方法,按实施例1的原料条件及步骤,并保持与第一双键异构单元的操作条件不变,此时与实施例1相比,1-丁烯的收率为28.3%。
88.【对比例2】
89.按实施例1的条件及步骤,保持其他操作条件不变,不设置第二双键异构化反应器和第四精馏塔,反应精馏塔塔釜物料同第一精馏塔塔釜物料都进入第一双键异构化反应器,在取得相同的1-丁烯收率时,第一双键异构化反应器所需处理的进料量比实施例1中第一、第二双键异构化反应器所需处理的进料量的总和增加19.2%。
90.应当注意的是,以上所述的实施例仅用于解释本发明,并不构成对本发明的任何限制。通过参照典型实施例对本发明进行了描述,但应当理解为其中所用的词语为描述性和解释性词汇,而不是限定性词汇。可以按规定在本发明权利要求的范围内对本发明作出修改,以及在不背离本发明的范围和精神内对本发明进行修订。尽管其中描述的本发明涉及特定的方法、材料和实施例,但是并不意味着本发明限于其中公开的特定例,相反,本发明可扩展至其他所有具有相同功能的方法和应用。