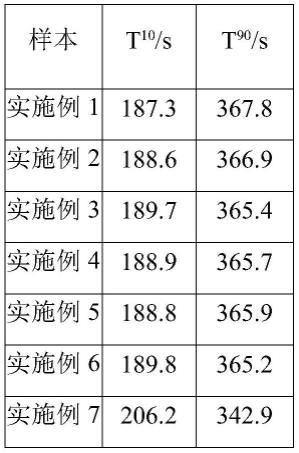
1.本技术涉及硅橡胶生产技术领域,更具体地说,它涉及一种硅橡胶延迟剂、含延迟剂的硅橡胶合成革以及硅橡胶合成革的低耗能制造工艺。
背景技术:2.硅橡胶是一种性能优异的合成橡胶,是近几十年橡胶领域的研究热点之一。加成型液体硅橡胶就是在这种背景下发展出的新型硅橡胶,加成型液体硅橡胶除了具有耐老化、无毒无味、绝缘性能好等优点外,还有硫化过程收缩率小、工艺简单、深层硫化操作简便等相对于其他合成橡胶的优点。在合成加成型液体硅橡胶时,通常使用铂金催化剂进行吸附催化,由于铂金催化剂的催化活性极高,因此通常需要在硅橡胶的原料中添加延迟剂,以适当降低铂金催化剂的催化活性,为硫化加工留出时间。
3.相关技术中有一种硅橡胶延迟剂,选用甲基丁炔醇为主要成分。甲基丁炔醇是一种不饱和醇,甲基丁炔醇中的炔基、羟基均可与铂金催化剂、铁等金属发生吸附,当向硅橡胶原料中添加甲基丁炔醇之后,甲基丁炔醇吸附在铂金催化剂表面,并在铂金催化剂表面形成络合物吸附层,从而阻碍了铂金催化剂与硅橡胶单体之间的吸附,延缓了硫化反应的发生。
4.针对上述中的相关技术,发明人认为,相关技术中的甲基丁炔醇虽然能对硫化反应的发生起到一定的延缓效果,但是甲基丁炔醇在硫化初期容易挥发,因此铂金催化剂对甲基丁炔醇的吸附难以长时间保持,导致甲基丁炔醇延后硫化反应发生的效果不佳。
技术实现要素:5.相关技术中,铂金催化剂对甲基丁炔醇的吸附难以长时间保持,导致甲基丁炔醇延后硫化反应发生的效果不佳,为了改善这一缺陷,本技术提供一种硅橡胶延迟剂、含延迟剂的硅橡胶合成革以及硅橡胶合成革的低耗能制造工艺。
6.第一方面,本技术提供一种硅橡胶延迟剂,采用如下的技术方案:一种硅橡胶延迟剂,所述硅橡胶延迟剂包括如下重量份的组分:不饱和醇复合制剂8-12份,脱附剂缓释胶囊4-6份,所述不饱和醇复合制剂由甲基丁炔醇和甲基丁烯醇衍生物混合而成,所述甲基丁烯醇衍生物由甲基丁炔醇与卤化氢的加成产物中的卤素原子与有机链段供体发生亲核取代反应后得到,所述有机链段供体的组分包括碱金属醇盐,所述碱金属醇盐对应的醇为带有羧基的一元醇;所述脱附剂缓释胶囊的组分包括过硫酸盐。
7.通过采用上述技术方案,本技术对甲基丁炔醇进行改性,先通过加成反应得到了甲基丁烯醇的一卤代物,然后通过卤素原子与碱金属醇盐发生亲核取代反应,脱去碱金属卤盐后得到了甲基丁烯醇衍生物。甲基丁烯醇衍生物中的烯基与炔基类似,均可与铂金催化剂形成络合物。同时,由于亲核取代反应还向甲基丁烯醇衍生物中引入了羧基,而新引入的羧基以及继承自甲基丁炔醇的羟基均可与铂金催化剂形成络合物,因此改性甲基丁炔醇
与甲基丁炔醇相比具有更多的配位基团。使用甲基丁烯醇衍生物部分代替甲基丁炔醇之后,得到的延迟剂稳定性更高,有助于延后硅橡胶发生硫化反应的时间。同时,由于引入了羧基的甲基丁烯醇衍生物更容易形成氢键,因此减少了甲基丁炔醇受热脱附的可能,从而进一步延后了硅橡胶发生硫化反应的时间。在硫化开始之后,随着加热的进行,脱附剂缓释胶囊逐渐释放过硫酸盐。到达硫化温度之后,过硫酸盐完全释放,并将铂金催化剂表面发生络合的甲基丁炔醇和甲基丁烯醇衍生物中的不饱和键氧化,使得不饱和键与铂金催化剂之间的配位键断裂,从而实现了延迟剂的快速脱附。此后,铂金催化剂的催化活性恢复,保障了硫化反应的正常进行。
8.作为优选,所述硅橡胶延迟剂包括如下重量份的组分:不饱和醇复合制剂9-11份,脱附剂缓释胶囊4-6份。
9.通过采用上述技术方案,优选了不饱和醇复合制剂在延迟剂中的配比,有助于改善对硫化反应的延后效果。
10.作为优选,所述甲基丁烯醇衍生物按照如下方法制备:(1)将甲基丁炔醇、过氧化物引发剂、二甲苯混合均匀,然后向混合所得物中通入卤化氢并水浴加热,加热结束后通过减压蒸馏对混合物进行提纯,得到甲基丁烯醇的卤代物;本步骤中,卤化氢为氯化氢或溴化氢;(2)将甲基丁烯醇卤代物、有机链段供体、二甲苯、氢氧化钠混合后进行加热回流,回流结束后再对回流所得液体进行酸洗和分液,对分液所得有机相进行连续萃取和减压蒸馏,得到甲基丁烯醇衍生物。
11.通过采用上述技术方案,本技术在过氧化物引发剂的引发下使甲基丁炔醇与卤化氢发生自由基加成,得到甲基丁烯醇的卤代物,再通过氢氧化钠的催化使甲基丁烯醇卤代物和碱金属醇盐发生亲核取代反应消去卤原子,得到了甲基丁烯醇衍生物。
12.作为优选,所述有机链段供体按照如下方法制备:(1)将醇、二甲苯、水、氢氧化钠混合均匀,然后对混合所得物进行加热回流;本步骤中所用的醇为带有羧基的一元醇;(2)回流结束后,对回流所得物进行减压蒸发,除去水和二甲苯后再滤去固体杂质,使用无水乙醇溶解剩余物后得到有机链段供体。
13.通过采用上述技术方案,本技术在含水的二甲苯中,通过氢氧化钠与醇共热的方式制备了醇钠和醇的混合物,对于带有羧基的一元醇,醇钠同时也具有羧酸钠的性质。
14.作为优选,制备所述有机链段供体的步骤(1)中,所述带有羧基的一元醇为乙醇酸。
15.通过采用上述技术方案,当选用乙醇酸制备有机链段供体时,有机链段供体为乙醇酸二钠与乙醇酸的混合物,乙醇酸自身具有螯合能力,能够与铂金催化剂形成螯合物,有助于降低铂金催化剂的催化活性,延后了硅橡胶发生硫化反应的时间。此外,乙醇酸在硫化反应的温度条件下时会发生分解,因此乙醇酸能够自动解除与铂金催化剂表面的吸附,保障了硫化反应的正常进行。
16.作为优选,所述脱附剂缓释胶囊按照如下方法制备:(1)将硬脂酸和无水乙醇混合均匀,然后在恒温水浴条件下加热至硬脂酸熔化,得到壁材前体液;
(2)向壁材前体液中加入芯材,搅拌均匀后冷却至室温,再进行减压蒸发除去乙醇,接着对剩余的固体产物进行筛分,得到脱附剂缓释胶囊;本步骤中,芯材的组分包括过硫酸盐和成核剂。
17.通过采用上述技术方案,本技术以硬脂酸作为壁材,先通与无水乙醇混合加热得到了液态硬脂酸与无水乙醇的混合液,然后将芯材加热混合液并进行冷却,经过减压蒸发和筛分之后得到了芯材中含有过硫酸盐的脱附剂缓释胶囊。脱附剂缓释胶囊的壁材为硬脂酸,硬脂酸在硫化反应的加热条件下逐渐熔化,实现了对过硫酸盐的释放。
18.作为优选,所述成核剂为含结晶水的膨润土。
19.通过采用上述技术方案,膨润土一方面能够作为脱附剂缓释胶囊固化成型时的核心,另一方面,膨润土中的结晶水在受热时会恢复流动性,恢复流动性的结晶水能够增加膨润土颗粒表面的湿度,从而促进了膨润土颗粒与过硫酸盐的结合,有利于实现硬脂酸对过硫酸盐的包覆。
20.作为优选,所述芯材的组分还包括醋酸钙。
21.通过采用上述技术方案,醋酸钙能够使一部分乙醇发生凝固,通过醋酸钙在还能够在膨润土颗粒表面与硬脂酸反应产生硬脂酸钙,从而促进了壁材的固化,增大了胶囊壁的致密度,有助于减少过硫酸盐的流失,加强了脱附剂缓释胶囊对过硫酸盐的储存效果。
22.第二方面,本技术提供一种含延迟剂的硅橡胶合成革,采用如下技术方案:一种含延迟剂的硅橡胶合成革,所述硅橡胶合成革包括基布层和硅橡胶层,制备所述硅橡胶层的原料包括支链乙烯基硅油、白炭黑、硅氮烷、聚丙烯酸酯改性苯基硅树脂、含氢硅油、硅烷偶联剂、铂金催化剂、色膏颜料以及上述的任意一种硅橡胶延迟剂。
23.通过采用上述技术方案,本技术以支链乙烯基硅油、白炭黑、硅氮烷、聚丙烯酸酯改性苯基硅树脂、含氢硅油、硅烷偶联剂、铂金催化剂、色膏颜料以及本技术的硅橡胶延迟剂为原料制备了硅橡胶层,并将硅橡胶层与基布层复合,得到了含延迟剂的硅橡胶合成革。
24.第三方面,本技术提供一种硅橡胶合成革的制造工艺,采用如下的技术方案。
25.一种硅橡胶合成革的制造工艺,包括以下步骤:(1)对支链乙烯基硅油、白炭黑、硅氮烷三者进行混炼,然后将聚丙烯酸酯改性苯基硅树脂、含氢硅油、硅烷偶联剂、铂金催化剂、色膏颜料以及上述的任意一种硅橡胶延迟剂混合均匀,得到硅橡胶混合料;(2)将硅橡胶混合料涂覆在离型纸上,得到混合料涂覆层,然后将基布层与混合料涂覆层贴合,并对基布层、混合料涂覆层以及离型纸三者共同进行加热处理,直到混合料涂覆层完成硫化,得到硅橡胶层;(3)等待硅橡胶层冷却至室温后,将离型纸揭去,得到硅橡胶合成革。
26.通过采用上述技术方案,本技术的方法先将支链乙烯基硅油、白炭黑、硅氮烷三者进行混炼,然后将聚丙烯酸酯改性苯基硅树脂、含氢硅油、硅烷偶联剂、铂金催化剂、色膏颜料以及本技术的硅橡胶延迟剂混合,得到了硅橡胶混合料,接着使硅橡胶混合料在离型纸和基布层之间硫化成型,同时完成了对硅橡胶层和基布层的复合,得到了硅橡胶合成革。
27.本技术的硅橡胶延迟剂在延后硫化反应发生的同时,还通过过硫酸盐的氧化作用实现了延迟剂的自动失效,因此无需通过提高温度和延长加热时间的方式来促进延迟剂从铂金催化剂表面的脱附,从而降低了硫化工艺的能耗,有助于减少化石燃料的使用,实现了
低碳环保的效果。
28.综上所述,本技术具有以下有益效果:1、本技术使用甲基丁炔醇和甲基丁烯醇衍生物作为延迟剂中的主要成分,利用铂金催化剂对炔基、烯基、羟基、羧基等基团的络合作用对铂金催化剂的催化活性进行限制,有助于延后硅橡胶发生硫化反应的时间。同时,本技术的延迟剂中的脱附剂缓释胶囊能够在硫化温度下对脱附剂进行释放,有助于保障硫化反应的正常发生。
29.2、本技术中优选制备有机链段供体选用的醇类物质为乙醇酸,乙醇酸一方面能够和铂金催化剂发生络合,从而实现了对铂金催化剂催化活性的限制。另一方面,乙醇酸能够在硫化反应的温度条件下自动发生分解,从而保障了硫化反应的正常发生。
30.3、本技术的方法,在硫化成型的同时实现了硅橡胶层与基布层的贴合,最终得到了硅橡胶层与基布层的复合,完成了对硅橡胶合成革的制备。本技术的硅橡胶延迟剂无需通过提高温度和延长加热时间的方式来促进延迟剂从铂金催化剂表面的脱附,从而降低了硫化工艺的能耗,有助于减少化石燃料的使用,实现了低碳环保的效果。
具体实施方式
31.以下结合实施例、制备例和对比例对本技术作进一步详细说明,本技术涉及的原料均可通过市售获得。
32.甲基丁烯醇衍生物的制备例以下以制备例1为例说明。
33.制备例1本制备例提供一种有机链段供体和一种甲基丁烯醇衍生物,其中甲基丁烯醇衍生物的结构如式(1)所示:本制备例中,有机链段供体按照如下方法制备:(1)将10kg乙醇酸、25kg二甲苯、8kg水、12kg氢氧化钠混合均匀,然后在75℃下对混合所得物加热回流4h;(2)回流结束后,对回流所得物进行减压蒸发,除去水和二甲苯后再过滤除去固体杂质,使用10kg无水乙醇溶解剩余物,得到有机链段供体。
34.本制备例中,甲基丁烯醇衍生物按照以下方法制备:(1)将10kg甲基丁炔醇、0.1kg过氧化物引发剂、18kg二甲苯混合均匀,然后向混合所得物中以2l/min的速率通入卤化氢气体并在85℃进行水浴加热,加热1h后通过减压蒸馏分离出反应体系中剩余的卤化氢、二甲苯和甲基丁炔醇,得到甲基丁烯醇的卤代物;本步骤中,卤化氢为氯化氢,过氧化物引发剂为过氧化二苯甲酰;(2)将5kg甲基丁烯醇卤代物、10kg有机链段供体、20kg二甲苯、8kg氢氧化钠混合
后在80℃加热回流3h,回流结束后再对回流所得液体进行酸洗和分液,然后对分液所得有机相进行连续萃取和减压蒸馏,得到甲基丁烯醇衍生物;本步骤中,酸洗时选用的试剂为质量分数10%的盐酸,萃取剂为石油醚。
35.制备例2本制备例与制备例1的不同之处在于,将制备甲基丁烯醇衍生物的步骤(1)中的氯化氢气体替换为溴化氢气体。
36.脱附剂缓释胶囊的制备例制备例3本制备例提供一种脱附剂缓释胶囊,脱附剂缓释胶囊按照如下方法制备:(1)将5kg硬脂酸和10kg无水乙醇混合均匀,然后在恒温水浴条件下加热至75℃,保温直至硬脂酸熔化,得到壁材前体液;(2)向壁材前体液中加入4.5kg芯材,搅拌均匀后以10℃/h的速率逐渐冷却至室温,再减压蒸发除去乙醇,接着对剩余的固体产物进行筛分,筛选粒径在200μm-350μm之间的部分得到脱附剂缓释胶囊;本步骤中,芯材的组分包括2kg过硫酸盐;本步骤中,芯材包括 3kg过硫酸盐和1.5kg成核剂,成核剂为经过煅烧脱水的膨润土。
37.制备例4本制备例与制备例3的不同之处在于,成核剂为含结晶水的膨润土,膨润土的中结晶水的质量分数为18%。
38.制备例5本制备例与制备例4的不同之处在于,芯材的组分还包括0.5kg醋酸钙。实施例
39.实施例1-5以下以实施例1为例进行说明。
40.实施例1本实施例提供一种硅橡胶延迟剂,由8kg不饱和醇复合制剂和4kg制备例3的脱附剂缓释胶囊混合而成,不饱和醇复合剂为4kg甲基丁炔醇和4kg制备例1的甲基丁烯醇衍生物混合后得到。
41.本实施例还提供一种含延迟剂的硅橡胶合成革,包括基布层和硅橡胶层,硅橡胶层由如下原料制备:支链乙烯基硅油6kg、白炭黑1.5kg、硅氮烷0.25kg、聚丙烯酸酯改性苯基硅树脂1.5kg、含氢硅油2kg、硅烷偶联剂0.15kg、铂金催化剂30g、色膏颜料1kg、本实施例配制的硅橡胶延迟剂8g,硅烷偶联剂为kh560。
42.本实施例中,硅橡胶合成革按照以下步骤制备:(1)在60℃下对支链乙烯基硅油、白炭黑、硅氮烷三者的混合物混炼3h,再升温至150℃混炼2h,等待混炼产物冷却至室温之后,再将混炼产物聚丙烯酸酯改性苯基硅树脂、含氢硅油、硅烷偶联剂、铂金催化剂、色膏颜料以及硅橡胶延迟剂在行星式搅拌机中混合搅拌 10min,得到硅橡胶混合料;(2)将硅橡胶混合料涂覆在离型纸上,得到混合料涂覆层,然后将基布层与混合料涂覆层贴合,并对基布层、混合料涂覆层以及离型纸三者放置于隧道炉中,在130℃下加热硫化 15min,得到硅橡胶层;
(3)等待硅橡胶层冷却至室温后,将离型纸揭去,得到硅橡胶合成革。
43.如表1,实施例1-5的不同之处主要在于,硅橡胶延迟剂由不同重量的不饱和醇复合制剂和脱附剂缓释胶囊混合而成。
44.表1 样本不饱和醇复合制剂/kg脱附剂缓释胶囊/kg实施例184实施例294.5实施例3105实施例4115.5实施例5126实施例6本实施例与实施例3的不同之处在于,不饱和醇复合制剂中的甲基丁烯醇衍生物为制备例2 的甲基丁烯醇衍生物。
45.实施例7本实施例与实施例3的不同之处在于,脱附剂缓释胶囊为制备例4的脱附剂缓释胶囊。
46.实施例8本实施例与实施例7的不同之处在于,脱附剂缓释胶囊为制备例5的脱附剂缓释胶囊。
47.对比例对比例1一种含延迟剂的硅橡胶合成革,包括基布层和硅橡胶层,硅橡胶层由如下原料制备:支链乙烯基硅油6kg、白炭黑1.5kg、硅氮烷0.25kg、聚丙烯酸酯改性苯基硅树脂1.5kg、含氢硅油2kg、硅烷偶联剂0.15kg、铂金催化剂30g、色膏颜料1kg、硅橡胶延迟剂8g,硅橡胶延迟剂为甲基丁炔醇,硅烷偶联剂为kh560。
48.硅橡胶合成革按照以下步骤制备:(1)在60℃下对支链乙烯基硅油、白炭黑、硅氮烷三者的混合物混炼3h,再升温至150℃混炼2h,等待混炼产物冷却至室温之后,再将混炼产物聚丙烯酸酯改性苯基硅树脂、含氢硅油、硅烷偶联剂、铂金催化剂、色膏颜料以及甲基丁炔醇在行星式搅拌机中混合搅拌 10min,得到硅橡胶混合料;(2)将硅橡胶混合料涂覆在离型纸上,得到混合料涂覆层,然后将基布层与混合料涂覆层贴合,并对基布层、混合料涂覆层以及离型纸三者放置于隧道炉中,在130℃下加热硫化 15min,得到硅橡胶层;(3)等待硅橡胶层冷却至室温后,将离型纸揭去,得到硅橡胶合成革。
49.对比例2本对比例与实施例3的不同之处在于,硅橡胶延迟剂的组分中不包括脱附剂缓释胶囊,硅橡胶合成革中的硅橡胶延迟剂仅包括8g不饱和醇复合剂。
50.对比例3本对比例与对比例1的不同之处在于,硅橡胶延迟剂由甲基丁炔醇和本技术制备
例3的脱附剂缓释胶囊按照2:1的重量比复配而成,且甲基丁炔醇的总重量不变。
51.性能检测试验方法使用《gb/t 16584》规定的硫化仪测试本技术各实施例、对比例的硅橡胶的硫化特性,结果见表2。
52.表2表2结合实施例1-5和对比例1并结合表2可以看出,实施例1-5测得的t
10
均大于对比例1,说明本技术通过亲核取代反应还向甲基丁烯醇衍生物中引入了羧基后,由于新引入的羧基以及继承自甲基丁炔醇的羟基均可与铂金催化剂形成络合物,因此改性甲基丁炔醇与甲基丁炔醇相比具有更多的配位基团,因此使用甲基丁炔醇和甲基丁烯醇衍生物复配得到的硅橡胶延迟剂对硅橡胶的硫化具有更好的延后效果。实施例1-5测得的t
90
均小于对比例1,说明本技术的硅橡胶延迟剂通过不饱和醇复合制剂与脱附剂缓释胶囊的复配,借助过硫酸盐的氧化效果实现了对铂金催化剂的脱附处理,加快了硅橡胶的硫化速率。
53.结合实施例3和对比例2并结合表2可以看出,实施例3测得的t
10
与对比例2接近,而t
90
小于对比例2,说明在未添加脱附剂缓释胶囊的情况下,由于本技术的硅橡胶延迟剂中的甲基丁烯醇衍生物对铂金催化剂的催化活性具有较好的抑制效果,而甲基丁烯醇衍生物难以自发从铂金催化剂表面脱离,因此在延后硫化反应的同时也减缓了硅橡胶的硫化速率。
54.结合实施例3和对比例3并结合表2可以看出,对比例3测得的t
10
与对比例1接近,而t
90
小于对比例1,说明在应用了本技术的脱附剂缓释胶囊之后,随着脱附剂中过硫酸盐成分的逐渐释放,过硫酸盐逐渐将甲基丁炔醇氧化,从而使甲基丁炔醇脱离了铂金催化剂的表面,恢复了铂金催化剂的催化活性,从而加快了硫化速率。
55.结合实施例3和实施例6并结合表2可以看出,实施例6测得的t
90
以及t
10
均与实施例3接近,说明改变卤化氢种类得到的甲基丁烯醇衍生物的性能无明显变化。
56.结合实施例3、实施例7并结合表2可以看出,实施例7测得的t
10
大于实施例3,而t
90
小于实施例3,说明膨润土在受热时释放的结晶水促进了膨润土与过硫酸盐的结合,改善了硬脂酸对过硫酸盐的包覆效果,从而减少了被脱附剂缓释胶囊提前释放的过硫酸盐的总量,有助于保持延迟剂对硅橡胶硫化的延后效果。同时,由于过硫酸盐被提前释放的总量减少,因此过硫酸盐对铂金催化剂的脱附效果更好,从而加快了硅橡胶的硫化速率。
57.结合实施例8、实施例7并结合表2可以看出,实施例8测得的t
10
大于实施例7,而 t
90
小于实施例7,说明实施例8通过在芯材中添加醋酸钙,在膨润土释放结晶水的前提下,利用醋酸钙与硬脂酸结合形成硬脂酸钙颗粒,从而促进了脱附剂缓释胶囊的胶囊壁的固化,改善了脱附剂缓释胶囊对过硫酸盐的包覆效果,有助于保持延迟剂对硅橡胶硫化的延后效果以及加快了硅橡胶的硫化速率。
58.本具体实施例仅仅是对本技术的解释,其并不是对本技术的限制,本领域技术人员在阅读完本说明书后可以根据需要对本实施例做出没有创造性贡献的修改,但只要在本技术的权利要求范围内都受到专利法的保护。