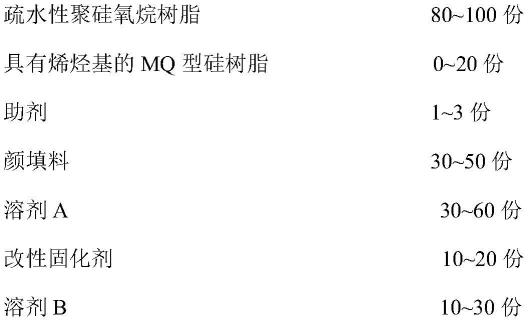
1.本发明属于海洋防污涂料、水下涂料技术领域,特别涉及一种改性有机硅海洋防污涂料及其制备方法。
背景技术:2.海洋生物污损是指海洋生物对浸没于海水环境中的基材进行非选择性黏附的过程。一方面,海洋生物污损会导致金属基材的腐蚀和非金属基材的降解,诱发设备损坏,带来结构危害;另一方面,海洋生物污损会显著增加船舶等设施的自重,从而导致额外燃油消耗以及温室气体的排放。目前,最有效的防治手段是涂刷海洋防污涂料。
3.基于科学技术的发展和环保意识的提升,传统的海洋防污涂料(例如有机锡类海洋防污涂料)尽管具备高效的防污表现,但其同期会向海洋环境释放大量有毒物质,从而威胁海洋生态环境以及人类的生产、生存活动。目前,环保型海洋防污涂料的研发日益受到各国的重视,并相继开辟了污损抑制型、污损释放型和污损降解型环保海洋防污涂料。
4.有机硅海洋防污涂料隶属于污损释放型大类,基于较低的表面自由能(≤30mj/m2),污损生物难以黏附在涂层表面。同时,此类涂料固化后具有较低的弹性模量,少量黏附的污损生物可以通过低能量的剥离方式重新释放到海水环境中,从而实现高效防污、脱污表现。然而,有机硅类海洋防污涂料,基于聚硅氧烷高分子的结构特性,其与极性基材的黏附性较差,即在基材上附着不牢固,很容易从船舶基材等表面脱落,这严重限制了相关涂料在海洋防污领域的应用。
技术实现要素:5.为了克服上述现有技术的不足,本发明的目的在于提供一种改性有机硅海洋防污涂料,经过交联固化反应后涂层与各类极性基材或环氧中间漆能够牢固粘结,即具有优异的附着力,同时固化涂层依然具有较低的表面自由能和较低的弹性模量,从而确保涂层具有优异的防污表现。
6.本发明是通过以下技术方案实现的:
7.本发明所述的一种改性有机硅海洋防污涂料,以重量份数计,其包括:
8.[0009][0010]
作为优选方案,所述疏水性聚硅氧烷树脂选自黏度2800~10000pa
·
s的具有羟基基团的聚硅氧烷树脂。
[0011]
具体的,所述具有羟基基团的聚硅氧烷树脂选自
ɑ
,ω
–
二羟基聚二甲基硅氧烷,
ɑ
,ω
–
二羟基聚硅氧烷,
ɑ
,ω
–
二羟基聚甲基聚硅氧烷树脂中的一种。
[0012]
作为优选方案,所述具有烯烃基的mq型硅树脂选自甲基乙烯基mq型硅树脂,其m:q值(即(a+b):c)≥1.3:1,或在25℃下为液体的甲基乙烯基mq型硅树脂。
[0013]
作为优选方案,助剂选自流平剂、消泡剂、润湿分散剂中的一种或几种。
[0014]
具体的,所述流平剂选自德国毕克byk-306,byk-307,byk-330,byk-333中的一种。
[0015]
具体的,所述消泡剂选自德国毕克by066n,byk-141,byk-071,byk-060n中的一种。
[0016]
具体的,所述润湿分散剂选自德国毕克byk-161,byk-163,byk-167中的一种。
[0017]
作为优选方案,所述颜填料选自滑石粉,重钙粉,金红石型二氧化钛,氧化锌,高岭土,三氧化二铁中的一种。
[0018]
作为优选方案,所述溶剂a选自异丙醇,乙醇,甲醇中的一种。
[0019]
作为优选方案,所述改性固化剂为具有(甲基)丙烯酰氧基的硅烷单体与丙烯酰基多巴胺单体以及不带羟基的丙烯酸酯硬单体在偶氮二异丁腈引发剂条件下反应合成的改性硅氧烷共聚物。
[0020]
具体的,所述具有(甲基)丙烯酰氧基的硅烷单体,丙烯酰基多巴胺单体,不带羟基的丙烯酸酯硬单体的重量比为(0.8~1.0):(0.05~0.1):(0.1~0.2)。
[0021]
具体的,所述偶氮二异丁腈引发剂的用量为反应物单体(包括具有(甲基)丙烯酰氧基的硅烷单体、丙烯酰基多巴胺单体、不带羟基的丙烯酸酯硬单体)总重量的1%。
[0022]
.具体的,所述具有(甲基)丙烯酰氧基的硅烷单体选自γ-甲基丙烯酰氧基丙基三异丙氧基硅烷,3-甲基丙烯酰氧丙基三甲基氧基硅烷,γ-甲基丙烯酰氧基丙基甲基二甲氧基硅烷中的一种。
[0023]
具体的,所述丙烯酰基多巴胺单体选自3-甲基丙烯酰胺基多巴胺,香豆酰多巴胺,n-咖啡酰多巴胺,3-丙烯酰胺基多巴胺中的一种。
[0024]
具体的,所述不带羟基的丙烯酸酯硬单体是指玻璃化温度在室温以上的不带羟基的丙烯酸酯,选自甲基丙烯酸甲酯,丙烯酸甲酯,甲基丙烯酸异冰片酯中的一种。
[0025]
具体的,所述改性固化剂通过如下步骤制备:
[0026]
在通有氮气保护条件下的反应釜中,将具有(甲基)丙烯酰氧基的硅烷单体、丙烯酰基多巴胺单体、不带羟基的丙烯酸酯硬单体在室温下混合15-30min,随后加入偶氮二异丁腈在45-60℃下进行反应3~6h;
[0027]
将反应后的产物使用乙醇进行萃取三次,取下层粘稠液体,即为改性固化剂,密封避光保存。
[0028]
作为优选方案,所述溶剂b选自二甲苯,丁酮,甲苯中的一种。
[0029]
作为优选方案,所述催化剂选自常规用于羟基封端聚硅氧烷交联固化反应的催化剂。
[0030]
具体的,所述催化剂选自二月硅酸二丁基锡、辛酸亚锡、有机铋中的一种。
[0031]
作为优选方案,所述溶剂c选自戊二酮,乙酸乙酯,丙酮中的一种。
[0032]
本发明还提供一种改性有机硅海洋防污涂料的制备方法,其包括以下步骤:
[0033]
将疏水性聚硅氧烷树脂,具有烯烃基的mq型硅树脂,助剂,颜填料,溶剂a按其重量份数混合,在300rpm/min下分散1h,所得混合物即为预分散浆料,将预分散浆料密封保存至少24h;
[0034]
将改性固化剂,溶剂b按其重量份数混合,在避光100rpm/min下分散15min,所得混合物即为固化剂组分,将固化剂组分避光密封保存;
[0035]
将催化剂,溶剂c按其重量份数混合,在100rpm/min下分散15min,所得混合物即为催化剂组分,密封保存。
[0036]
本发明还提供一种改性有机硅海洋防污涂层,将预分散浆料,固化剂组分,催化剂组分混合均匀,采用喷涂方式将涂料覆盖在基材或/和环氧中间漆表面,经过至少4h交联反应,即得所述改性有机硅海洋防污涂层。
[0037]
与现有技术相比,本发明具有如下得有益效果:
[0038]
1.本发明改性有机硅海洋防污涂料制备工艺简单,尤其是改性固化剂的制备条件简单。
[0039]
2.本发明改性有机硅海洋防污涂料固化涂层可以与各类极性基材或环氧中间漆牢固粘结,在使用过程中不会因为涂层脱落而失效。
[0040]
3.本发明改性有机硅海洋防污涂料固化涂层依然具有优异的低表面能和较低的弹性模量,确保涂层优异的海洋防污效果。
具体实施方式
[0041]
下面结合具体实施例对本发明进行详细说明。以下实施例将有助于本领域的技术人员进一步理解本发明,但不以任何形式限制本发明。应当指出的是,对本领域的普通技术人员来说,在不脱离本发明构思的前提下,开可以做出若干变形和改进。这些都属于本发明的保护范围。
[0042]
本发明的涂料,按照常规交联固化反应后能够形成三维有机硅网络结构。利用改性固化剂作为黏附增强组分,在不影响主要成膜物疏水性聚硅氧烷树脂特性的前提下,利用改性固化剂具有的高粘结基团,例如丙烯酰氧基团、多巴胺基团等实现与各类极性基材或环氧中间漆的牢固粘结。而固化后的三维有机硅网络结构,主要成膜物具有的特性会赋予涂层低表面能和低弹性模量,从而满足海洋防污的要求。
[0043]
实施例1-6中涉及的改性固化剂分别通过以下合成例1-3制备得到。其中,合成例1-3所使用原材料见表1,实际应用时并不局限于改厂家的产品。
[0044]
表1
[0045][0046]
合成例1
[0047]
(1)具有(甲基)丙烯酰氧基的硅烷单体a-1,丙烯酰基多巴胺单体b-1,不带羟基的丙烯酸酯硬单体c-1按重量比为1.0:0.05:0.1配料;
[0048]
(2)在通有氮气保护条件下的反应釜中,将具有(甲基)丙烯酰氧基的硅烷单体a-1、丙烯酰基多巴胺单体b-1、不带羟基的丙烯酸酯硬单体c-1在室温下混合15min,随后加入偶氮二异丁腈(用量为反应物总重量的1%)在55℃下进行反应5h;
[0049]
(3)将反应后的产物使用乙醇进行萃取三次,取下层粘稠液体,即为改性固化剂,密封避光保存。
[0050]
合成例2
[0051]
(1)具有(甲基)丙烯酰氧基的硅烷单体a-2,丙烯酰基多巴胺单体b-3,不带羟基的丙烯酸酯硬单体c-1按重量比为0.9:0.1:0.2配料;
[0052]
(2)在通有氮气保护条件下的反应釜中,将具有(甲基)丙烯酰氧基的硅烷单体a-2、丙烯酰基多巴胺单体b-3、不带羟基的丙烯酸酯硬单体c-1在室温下混合20min,随后加入偶氮二异丁腈(用量为反应物总重量的1%)在45℃下进行反应6h;
[0053]
(3)将反应后的产物使用乙醇进行萃取三次,取下层粘稠液体,即为改性固化剂,密封避光保存。
[0054]
合成例3
[0055]
(1)具有(甲基)丙烯酰氧基的硅烷单体a-2,丙烯酰基多巴胺单体b-2,不带羟基的丙烯酸酯硬单体c-2按重量比为0.8:0.08:0.15配料。
[0056]
(2)在通有氮气保护条件下的反应釜中,将具有(甲基)丙烯酰氧基的硅烷单体a-2、丙烯酰基多巴胺单体b-2、不带羟基的丙烯酸酯硬单体c-2在室温下混合30min,随后加入偶氮二异丁腈(用量为反应物总重量的1%)在60℃下进行反应3h;
[0057]
(3)将反应后的产物使用乙醇进行萃取三次,取下层粘稠液体,即为改性固化剂,密封避光保存。
[0058]
实施例1-6所使用的原材料见表2。
[0059][0060][0061]
实施例1-6的改性有机硅海洋防污涂料及其固化涂层的制备方法如下所示。实际应用时按照海洋防污涂料的常规方法制备,并不局限于该制备方法。
[0062]
(1)将疏水性聚硅氧烷树脂,具有烯烃基的mq型硅树脂,助剂,颜填料,溶剂a按其重量份数混合,在300rpm/min下分散1h,所得混合物即为预分散浆料,将预分散浆料密封保存至少24h;
[0063]
(2)将改性固化剂,溶剂b按其重量份数混合,在避光100rpm/min下分散15min,所得混合物即为固化剂组分,将固化剂组分避光密封保存;
[0064]
(3)将催化剂,溶剂c按其重量份数混合,在100rpm/min下分散15min,所得混合物即为催化剂组分,将催化剂组分密封保存;
[0065]
(4)将预分散浆料,固化剂组分,催化剂组分混合均匀,采用喷涂方式将涂料依次覆盖在基材和环氧中间漆表面,经过至少4h交联反应,即得对应得改性有机硅海洋防污涂层。
[0066]
对比例1
[0067]
与实施例1相比,对比例1的固化剂选自γ-甲基丙烯酰氧基丙基三异丙氧基硅烷,其余组分及重量份相同,其制备工艺也与实施例1相同。
[0068]
对比例2
[0069]
与实施例2相比,对比例2的固化剂选自3-甲基丙烯酰氧丙基三甲基氧基硅烷,其余组分及重量份相同,其制备工艺也与是实施例1相同。
[0070]
《具体测试实验和条件》
[0071]
测试1:表面自由能
[0072]
使用上海轩准仪器有限公司生产的xg-camc3型全自动接触角测量仪测定固化涂层表面的去离子水和二碘甲烷接触角。测量前需要用无水乙醇清洗涂层表面并干燥,随后根据owens二液法计算涂层的表面自由能。
[0073]
测试2:弹性模量
[0074]
使用聚四氟乙烯模具注模,并按照国标gb/t 528-1998的要求制备拉伸试样,使用济南兰光机电厂生产的xlm型电子拉力实验机测定拉伸试样的拉伸曲线,拉伸速率为10mm/min。记录拉伸试样的拉伸实验数均,并对变形率不超过0.5%的拉伸实验数据进行线形拟合,所得拟合曲线即为拉伸试样的弹性模量。每个涂层测3次,取平均值。
[0075]
测试3:拉拔法测附着力(钢板,环氧中间漆)
[0076]
使用广州标格达精密仪器有限公司生产的bgd500数显半自动附着力测试仪测量涂刷在相应基材或环氧中间漆的涂层的附着力。钢板使用前需要用800目砂纸打磨,使用的环氧中间漆为上海金丝帝生产的环氧云铁中间漆。
[0077]
测试4:防污性能
[0078]
将一种至少含有108单位唾液链球菌分散在20毫升胰蛋白酶大豆肉汤中,并在38℃,5%co2中培养2小时。随后进一步稀释悬浮液,并将其接种在补充有5%羊血的琼脂中,并在38℃,5%co2中培养48小时,然后将含有六个菌落形成的单位分散在10ml胰蛋白酶大豆肉汤中。随后在10
×
5cm范围的涂层上覆盖20ml上述细菌悬浮液,并在38℃,5%co2中培养24小时。培养结束后,每个样品需要在45ml蒸馏水中旋转冲刷30秒,然后再用50ml蒸馏水漂洗,以除去不粘物质,使用德国卡尔蔡司公司生产的simga300型扫描电镜观察表面黏附的细菌。
[0079]
实施例1-6和对比例1-2的具体测试实验结果如表3所示。
[0080][0081][0082]
通过上述测试可以证实,实施例与对比例涂层均具有较低的表面自由能和较低的弹性模量,因此呈现出优异的防污性能。本发明的优势在于,实施例在各类极性基材上均具有优异的附着力,远强于对比例,展现出优异的粘结效果。
[0083]
以上对本发明的具体实施例进行了说明。需要理解的是,本发明并不局限于上述特定实施方式,本领域技术人员可以在权利要求范围内做出各种变形或修改,这并不影响本发明的实质内容。