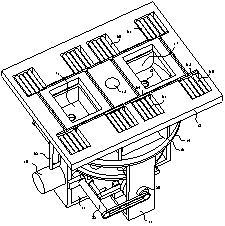
1.本发明涉及新能源汽车电能自动补给技术领域,具体为基于车联网技术的新能源汽车电能自动补给装置。
背景技术:2.电动汽车为一种清洁、环保型的绿色车辆,采用动力蓄电池作为主要电源,电动汽车的充电方式一般为:依靠地面充电站或车载充电系统在车辆停驶的情况下对电池进行充电;电动汽车电池更换站是为电动汽车快速更换电池箱并对电池箱进行充电、管理的场所,整个系统的运作过程对电动汽车电池充电情况至关重。
3.现有换电站对电池进行更换过程中,先将没有电或旧的电池进行拆卸,再将换出电池拿出操作区,进一步将换入电池装载到操作平台,再拖入操作区进行装载;更换过程极其复杂,即使使用专业的更换工具,也需要付出工人很大的体力劳动,而且由于动作复杂,电池较重,更换过程中不得不使用一些复杂的工具,这就会导致工具的动力源为多个,且配合容易出现不稳定,进一步的不但会导致了换电效率低下的问题出现,而且容易导致安全事故。
4.基于此,本发明设计了基于车联网技术的新能源汽车电能自动补给装置,以解决上述问题。
技术实现要素:5.本发明的目的在于提供基于车联网技术的新能源汽车电能自动补给装置,以解决上述背景技术中提出的问题。
6.为实现上述目的,本发明提供如下技术方案:基于车联网技术的新能源汽车电能自动补给装置,包括底板、电池承载板、拆装驱动总成、转运驱动总成;所述底板上开设有操作口;所述电池承载板顶部设置有若干数量的电池限位区, 所述电池限位区上设置两个阶梯通孔,所述阶梯通孔均滑动连接有套筒;所述拆装驱动总成用于驱动套筒先上升后旋转;所述转运驱动总成用于驱动电池承载板间歇转动;所述拆装驱动总成驱动套筒动作时,电池承载板不转动。
7.作为本发明的进一步方案,所述拆装驱动总成包括转动杆,所述转动杆上固定连接有非全齿轮,所述非全齿轮上方设有环形齿条,所述非全齿轮转动时与环形齿条间歇啮合,所述环形齿条顶面固定连接有筒形凸轮,所述筒形凸轮凸起端均固定连接有弧形齿条,所述筒形凸轮上方设置有限位板,所述限位板滑动连接有两个顶推杆,所述顶推杆上方正对套筒,两个所述顶推杆底部连接有u型杆,所述u型杆与两个所述顶推杆均转动连接,所述顶推杆与套筒花键连接,所述顶推杆均固定连接有驱动齿轮,所述筒形凸轮将u型杆顶至最高处时,驱动齿轮与弧形齿条啮合;
作为本发明的进一步方案,所述转运驱动总成包括包括间歇半球、驱动轴,所述驱动轴竖直布置且顶端与底板中部转动连接,所述间歇半球同轴固定设置在驱动轴外壁,所述转动杆靠近间歇半球的侧壁关于间歇半球竖向轴线对称固定设置有两组凸轮机构,所述间歇半球侧壁开设有用于配合凸轮机构的间歇槽;作为本发明的进一步方案,所述凸轮机构包括凸轮盘,所述凸轮盘侧壁固定设置有凸轮抓扣,所述凸轮抓扣套设在间歇半球四周环绕其竖向轴线等角度开设的长圆槽内,所述间歇半球侧壁还开设有用于配合凸轮盘的锁止半圆;作为本发明的进一步方案,所述转动杆外壁同轴套设有对准凸轮,所述对准凸轮下端接触有两块对称的桥板,所述桥板远离对准凸轮的一端通过支架转动设置在安装底架上端面,远离对准凸轮的所述桥板一端侧壁的转动轴外壁套设有对准顶杆,所述对准顶杆上端通过铰链转动设置有顶块,所述顶块转动设置在顶升盘底端的槽内;所述安装底架上端内壁靠近环形齿条上端面固定设置有用于锁止环形齿条转动的防转齿板;作为本发明的进一步方案,所述底板上端转动设置有多组自动复位组,所述自动复位组内包括多个轴线排列成圆弧凸面向下的复位辊,所述复位辊两端转动设置在底板侧壁开设的轮胎槽内,所述复位辊末端同轴固定设置有齿牙,所述齿牙上端啮合有锁止齿条,每个所述锁止齿条固定设置有同一个解锁框,所述解锁框竖向滑动设置在底板开设的避让槽内,所述顶块侧壁固定设置有l解锁杆,所述l解锁杆穿过底板侧壁的避让孔固定设置在解锁框底端;作为本发明的进一步方案,所述套筒下端侧壁开设有补偿环槽,所述补偿环槽外端套设有施力板,所述施力板竖向滑动在补偿环槽内,所述施力板外壁滑动设置在电池限位区之间内壁。
8.作为本发明的进一步方案,所述底板下方设有安装底架,两个所述转动杆穿过安装底架的一端均传动连接有两个通过支架转动设置在安装底架侧壁的锥齿轮轴组,两个所述锥齿轮轴组与电机传动连接。
9.与现有技术相比,本发明的有益效果是:1、本发明通过电机间接驱动非全齿轮转动驱动筒形凸轮转动,驱动u型杆上升同时,再通过筒形凸轮上端的齿条对顶推杆外壁的驱动齿轮作用使得套筒上升到顶端后转动,将汽车的旧电池进行拆卸且向下托出到底板下端,同时在拆卸过程中已经将新电池装载到相邻的电池限位区内,在非全齿轮脱离与环形齿条啮合,使得凸轮盘侧壁的凸轮抓扣驱动间歇半球转动,从而驱动驱动轴转动使得上端的限位板转动并且将新电池转动到操作口下端,同时再通过转动筒形凸轮同时使得上端相反的齿条驱动驱动齿轮反转,将新电池送入汽车电池仓同时进行固定,从而解决了现有换电站需要多次对新旧电池通过同一载台进行上下的操作,使得换电时间长,造成换电效率低下的问题出现。
10.2、本发明运行时,转动杆驱动对准凸轮转动再通过下端的桥板转动将对准顶杆顶起,再将上端的顶块顶起,将顶升盘下端的环形齿条顶升与防转齿板啮合,从而保持了顶升盘静止,从而有效解决了驱动轴转动对新旧电池换位过程中,造成顶升盘转动从而造成顶推杆上移,造成设备卡死的问题出现。
11.3、本发明通过顶块上升带动锁止齿条上移,从而对的自动复位组内的复位辊进行解锁,使得轮胎滑动到中间最低复位辊上端,使得汽车电池仓与操作口进行对准,从而保证
接下来的换电工作正常进行,有效避免了汽车多次调整方位,使得电池仓与操作口进行对准,从而浪费了大量时间,使得换电效率低下的问题出现。
附图说明
12.为了更清楚地说明本发明实施例的技术方案,下面将对实施例描述所需要使用的附图作简单地介绍,显而易见地,下面描述中的附图仅仅是本发明的一些实施例,对于本领域普通技术人员来讲,在不付出创造性劳动的前提下,还可以根据这些附图获得其他的附图。
13.图1为本发明总体结构示意图;图2为本发明底板隐藏后总体结构示意图;图3为本发明左前俯视角轴剖结构示意图;图4为本发明图3中a处放大结构示意图;图5为本发明图3中b处放大结构示意图;图6为本发明图3中c处放大结构示意图;图7为本发明图3中d处放大结构示意图;图8为本发明仰视角结构示意图图9为本发明右后俯视角u型杆和筒形凸轮配合结构示意图;图10为本发明配合结构示意图。
14.附图中,各标号所代表的部件列表如下:电机10,安装底架11,底板12,驱动轴13,限位板14,操作口15,电池承载板16,电池限位区17,阶梯通孔18,套筒19,顶推杆20,u型杆21,驱动齿轮22,间歇半球23,转动杆24,锥齿轮轴组25,凸轮机构4,凸轮盘41,凸轮抓扣42,锁止半圆43,顶升盘51,筒形凸轮52,对准凸轮53,桥板54,对准顶杆55,顶块56,环形齿条57,非全齿轮58,弧形齿条59,自动复位组60,复位辊61,齿牙62,锁止齿条63,解锁框64,l解锁杆65,防转齿板66,补偿环槽70,施力板71。
具体实施方式
15.下面将结合本发明实施例中的附图,对本发明实施例中的技术方案进行清楚、完整地描述,显然,所描述的实施例仅仅是本发明一部分实施例,而不是全部的实施例。基于本发明中的实施例,本领域普通技术人员在没有作出创造性劳动前提下所获得的所有其它实施例,都属于本发明保护的范围。
16.请参阅图1
‑
10,基于车联网技术的新能源汽车电能自动补给装置,包括底板12、电池承载板16、拆装驱动总成、转运驱动总成;底板12上开设有操作口15;电池承载板16顶部设置有若干数量的电池限位区17, 电池限位区17上设置两个阶梯通孔18,所述阶梯通孔18均滑动连接有套筒19;拆装驱动总成用于驱动套筒19先上升后旋转;转运驱动总成用于驱动电池承载板16间歇转动;拆装驱动总成驱动套筒19动作时,电池承载板16不转动;
本技术方案投入使用时,电池承载板16上若干数量的电池限位区17间隔摆放好能源充盈的新能源汽车电池,当待补给的电动汽车驾驶至底板12上合适区域时,识别系统识别汽车后(现有技术相对成熟未做赘述),启动动力驱动拆装驱动总成动作,使拆装驱动总成驱动套筒19完成两次先上升后旋转的动作,在拆装驱动总成动作的过程中转运驱动总成一直在驱动电池承载板16间歇转动,并且在拆装驱动总成驱动套筒19动作时,电池承载板16不转动,当拆装驱动总成驱动套筒19完成第一次先上升后旋转后完成对新能源汽车上电池的拆卸,随后电池承载板16在转运驱动总成的作用下将电池限位区17上能源充盈的新能源汽车电池转动至操作口15正下方,当拆装驱动总成驱动套筒19完成第二次先上升后旋转后完成对新能源汽车上电池的安装。
17.进一步的,拆装驱动总成包括转动杆24,转动杆24上固定连接有非全齿轮58,非全齿轮58上方设有环形齿条57,非全齿轮58转动时与环形齿条57间歇啮合,环形齿条57顶面固定连接有筒形凸轮52,筒形凸轮52凸起端均固定连接有弧形齿条59,筒形凸轮52上方设置有限位板14,限位板14滑动连接有两个顶推杆20,顶推杆20上方正对套筒19,两个顶推杆20底部连接有u型杆21,u型杆21与两个顶推杆20均转动连接,顶推杆20与套筒19花键连接,顶推杆20均固定连接有驱动齿轮22,筒形凸轮52将u型杆20顶至最高处时,驱动齿轮22与弧形齿条59啮合。
18.进一步,转运驱动总成包括包括间歇半球23、驱动轴13,驱动轴13竖直布置且顶端与底板12中部转动连接,间歇半球23同轴固定设置在驱动轴13外壁,转动杆24靠近间歇半球23的侧壁关于间歇半球23竖向轴线对称固定设置有两组凸轮机构4,间歇半球23侧壁开设有用于配合凸轮机构4的间歇槽。
19.进一步,凸轮机构4包括凸轮盘41,凸轮盘41侧壁固定设置有凸轮抓扣42,凸轮抓扣42套设在间歇半球23四周环绕其竖向轴线等角度开设的长圆槽内,间歇半球23侧壁还开设有用于配合凸轮盘41的锁止半圆43。
20.进一步的,底板12下方设有安装底架11,两个转动杆24穿过安装底架11的一端均传动连接有两个通过支架转动设置在安装底架11侧壁的锥齿轮轴组25,两个锥齿轮轴组25与电机10传动连接。
21.本发明使用时,先将换电设备组装完毕,保持底板12与地面持平,使得整个设备主体沉浸在地面以下(如图1所示,保持电池一直在地面以下进行操作,节约地面的空间,其次电池充电过程中电池自身会发出一定热量,通过地下的冬暖夏凉,保持电池充电过程中一直保持适宜的温度,其中图1左下为设备的前方,图1中上端为设备的上端,为叙述清楚本发明的技术方案,均采用图1视角进行叙述),先将换电汽车开到底板12载台上端,保持汽车电池安装仓与底板12上的操作口15对准,启动设备电机10,完成电池的更换。
22.其中,更换的具体过程分为三个部分:拆卸旧电池、电池限位区17的换位过程和安装新电池。当电机10持续单向转动时,拆卸旧电池和安装新电池两个部分组成的整体与电池限位区17的换位过程交替进行,切换过程以非全齿轮58与环形齿条57的啮合与否为区分或切换,其中,非全齿轮58与环形齿条57啮合时为拆卸旧电池或安装新电池部分,否则为电池限位区17的换位过程。其中:拆卸旧电池和安装新电池两个部分在他们组成的整体中交替出现。
23.拆卸旧电池过程如下:如图10所示:电机10驱动锥齿轮轴组25转动,锥齿轮轴组25
转动驱动转动杆24转动,转动杆24转动驱动非全齿轮58转动,非全齿轮58转动驱动上端的环形齿条57绕着其轴线转动(结合图3和图9所示,由于凸轮机构4中的凸轮抓扣42还未与间歇半球23侧的间歇槽接触,所以这时的凸轮抓扣42虽然转动但是转运驱动总成处于空载状态,无法驱动设备中的驱动轴13转动),环形齿条57转动驱动上端的顶升盘51转动,顶升盘51转动从而驱动其边缘的筒形凸轮52产生绕驱动轴转动;当筒形凸轮52外轮廓较高的部分转向挤压u型杆21时,配合限位板14的避让孔对顶推杆20的限位作用,会使得u型杆21及顶推杆20竖直上升,顶推杆20的上升一端距离后与套筒19下端进行啮合,从而带动上端的套筒19同时在阶梯通孔18内上升(如图3、4和5所示,本设备对方向不做完全的限定,只是保证设备动力传递方向,其中方向可有换向变速器进行操作,换向变速器的设置属于现有技术,在此不做赘述),直到套筒19伸入汽车的电池螺栓位置,随着电机10继续转动,如图9所示:u型杆21运行到筒形凸轮52远休止段,随着筒形凸轮52继续转动,从而使得筒形凸轮52远休止段的齿条59与顶推杆20下端的驱动齿轮22啮合,从而驱动顶推杆20发生转动,将汽车的电池固定螺栓进行拆卸,同时随着电机10继续转动,筒形凸轮52继续转动,使u型杆21进入筒形凸轮52的回程段;对应的:这时套筒19在阶梯通孔18内下降,将没有电的电池和螺栓同时拆卸托住并且向下移动直到完全将电池完全收缩到限位板14上端面(该种手段简单的实现了自动拆卸的功能,且极大程度上降低了人工劳动强度,而且整个拆卸过程中,不存在冲击,从而达到了安全且稳定的技术效果),使没有电的电池收纳到限位板14上的电池限位区17内,即所有的拆卸过程完成;需要注意的是:在进行拆卸电池过程中,即可在相邻的电池限位区17内装载新的准备安装的电池(可以减少旧电池转运过程中的时间消耗,提高更换速率);旧电池落到限位板14上端面后,非全齿轮58转动到齿牙尽头,此时非全齿轮58不再驱动环形齿条57转动。这时的筒形凸轮52保持静止,不再驱动u型杆21进行动作。
24.电池限位区17的换位过程具体如下:紧接拆卸旧电池过程,随着电机10继续转动,由于凸轮机构4中的凸轮抓扣42与间歇半球23侧的间歇槽接触,所以间歇半球23开始转动(如图2和8所示,其中凸轮抓扣42关于凸轮盘41轴线倾斜设置,配合间歇半球23的曲面,避免在转动过程中与间歇半球23侧壁的竖向滑孔卡死的现象出现;其次凸轮盘41侧壁的半圆槽又与间歇半球23侧壁的锁止半圆43进行啮合,在凸轮抓扣42驱动间歇半球23转动时凸轮盘41侧壁的半圆槽与间歇半球23侧壁的锁止半圆43解锁,在凸轮抓扣42不对间歇半球23驱动时,使得凸轮盘41与锁止半圆43啮合,从而避免了设备中驱动轴13产生不必要的动力位移差,从而导致电池限位区17无法与操作口15对准,从而导致电池更换失败的现象出现)其中转动杆24继续转动,这时的非全齿轮58和环形齿条57处于非啮合状态,间歇半球23转动九十度从而驱动驱动轴13转动九十度(当电池限位区17不是图中展示的四个时,转动角度应当做相适应的调整),驱动轴13转动驱动限位板14转动九十度,从而将相邻的电池限位区17内的限位板14上的新的电池转动到刚刚拆卸的电动汽车下端,这时凸轮盘41侧壁的凸轮抓扣42不再对间歇半球23作用,同时凸轮盘41与锁止半圆43处于锁止状态,如此:完成新旧电池在限位板14上的位置之间的更换。需要注意的是:这时非全齿轮58又一次与环形齿条57啮合从而进入到更换新的电池的过程中,进一步的,也完成了电池限位区17的换位过程。
25.安装新电池过程如下:非全齿轮58驱动环形齿条57转动,环形齿条57转动驱动顶升盘51绕着驱动轴13转动,顶升盘51转动驱动筒形凸轮52转动,筒形凸轮52转动通过另外一侧的上止面驱动u型杆21上升,u型杆21上升间接将套筒19在阶梯通孔18内向上顶起,阶
梯通孔18和套筒19上移从而将新电池和固定螺栓同时向上顶起(其中套筒19内竖向长度用于补偿电池顶升到位过程中,螺栓为打入固定螺栓内的长度,从而避免了将固定说栓顶断的现象出现),将电池顶升到汽车电池固定位置,这时筒形凸轮52继续转动使得上端齿条59与驱动齿轮22啮合(如图10所示,其中筒形凸轮52上端的两个齿条22一个设置在驱动齿轮22内侧,一个设置在驱动齿轮22外侧),从而使得驱动齿轮22这时发生反转,从而将螺栓打入汽车电池固定螺栓上,从而完成换电过程(如图1和3和10所示,其中底板12上端开设又两个操作口15,可同时为两台车进行同步换电,从而进一步加快设备的换电效率,其次,本设备中的驱动设备本体采用关于驱动轴13轴线的对称方式,从而保持设备运动部件的受力均衡,从而避免设备出现卡死现象出现);本发明通过电机10间接驱动非全齿轮58转动驱动筒形凸轮52转动,驱动u型杆21上升同时,再通过筒形凸轮52上端的齿条59对顶推杆20外壁的驱动齿轮22作用使得套筒19上升到顶端后转动,将汽车的旧电池进行拆卸且向下托出到底板12下端,同时在拆卸过程中已经将新电池装载到相邻的电池限位区17内,在非全齿轮58脱离与环形齿条57啮合,使得凸轮盘41侧壁的凸轮抓扣42驱动间歇半球23转动,从而驱动驱动轴13转动使得上端的限位板14转动九十度将新电池转动到操作口15下端,同时再通过转动筒形凸轮52同时使得上端相反的齿条59驱动驱动齿轮22反转,将新电池送入汽车电池仓同时进行固定,从而解决了现有换电站需要多次对新旧电池通过同一载台进行上下的操作,使得换电时间长,造成换电效率低下的问题出现。
26.本发明在使用时,由于驱动轴13的转动对新旧电池进行转运的同时,可能会驱动上端的顶升盘51转动,从而造成顶升盘51的位置出现偏移,导致u型杆21出现不规则上升的问题出现,从而造成套筒19的上升造成设备卡死的现象出现,现希望设置一套防转装置以解决上述问题;作为本发明的进一步方案,转动杆24外壁同轴套设有对准凸轮53,对准凸轮53下端接触有两块对称的桥板54,桥板54远离对准凸轮53的一端通过支架转动设置在安装底架11上端面,远离对准凸轮53的桥板54一端侧壁的转动轴外壁套设有对准顶杆55,对准顶杆55上端通过铰链转动设置有顶块56,顶块56转动设置在顶升盘51底端的槽内;安装底架11上端内壁靠近环形齿条57上端面固定设置有用于锁止环形齿条57转动的防转齿板66;本发明使用时,当凸轮盘41侧壁的凸轮抓扣42驱动间歇半球23转动之前,在转动杆24驱动环形齿条57转动将套筒19向下释放过程中(使得在间歇半球23转动之前,顶升盘51已经处于锁死状态),转动杆24外壁的对准凸轮53驱动桥板54其中间转动点转动,从而将对准顶杆55顶起,对准顶杆55上升从而驱动上端的顶块56上移,顶块56上移从而将顶升盘51向上顶起一小段距离,(如图3和9所示,其中套筒19和顶推杆20之间的间隙从而补偿了顶升盘51向上一小段的位移,从而避免造成套筒19上移,使得设备出现卡死的现象出现),顶升盘51上移同时将环形齿条57向上带动,环形齿条57上移与安装底架11内侧壁的防转齿板66啮合,从而使得环形齿条57保持静止,同时的保持顶升盘51静止,从而使得整个限位板14转位过程中,顶升盘51不再转动;本发明通过2运行时,转动杆24驱动对准凸轮53转动再通过下端的桥板54转动将对准顶杆55顶起,再将上端的顶块56顶起,将顶升盘51下端的环形齿条57顶升与防转齿板66啮合,从而保持了顶升盘51静止,从而有效解决了驱动轴13转动对新旧电池换位过程中,
造成顶升盘51转动从而造成顶推杆20上移,造成设备卡死的问题出现。
27.本发明在使用时,由于车辆停车过程中的位移差问题,从而可能会出现汽车电池仓不好对准操作口15的现象出现,从而浪费了大量的时间,使得换电效率低下的问题出现,现希望设置一套自动对准装置,从而解决上述问题;作为本发明的进一步方案,底板12上端转动设置有多组自动复位组60,自动复位组60内包括多个轴线排列成圆弧凸面向下的复位辊61,复位辊61两端转动设置在底板12侧壁开设的轮胎槽内,复位辊61末端同轴固定设置有齿牙62,齿牙62上端啮合有锁止齿条63,每个锁止齿条63固定设置有同一个解锁框64,解锁框64竖向滑动设置在底板12开设的避让槽内,顶块56侧壁固定设置有l解锁杆65,l解锁杆65穿过底板12侧壁的避让孔固定设置在解锁框64底端;本发明使用时,当上一辆车换电完成后,新的换电车辆进入换电设备上端的底板12上端时,使得四个轮胎分别处于自动复位组60内的复位辊61上,当卸载电池限位区17仓对准操作口15时(卸载旧电池的电池限位区17和新电池的电池限位区17不同,避免了电池限位区17需要兼容多样性,从而造成设备的成本过高问题出现),这时的顶升盘51处于上升锁死过程,这时的顶块56带动其外侧l解锁杆65上升,l解锁杆65上升带动解锁框64上升,解锁框64上升带动锁止齿条63上升,锁止齿条63上升从而对复位辊61端头转轴上的的齿牙62进行解锁,复位辊61自由转动,从而将复位辊61上端的轮胎自动滑落到中间最低的复位辊61上端,从而保持汽车电池仓与操作口15进行对准,从而保证接下来的换电工作正常进行。
28.本发明通过顶块56上升带动锁止齿条63上移,从而对的自动复位组60内的复位辊61进行解锁,使得轮胎滑动到中间最低复位辊61上端,使得汽车电池仓与操作口15进行对准,从而保证接下来的换电工作正常进行,有效避免了汽车多次调整方位,使得电池仓与操作口15进行对准,从而浪费了大量时间,使得换电效率低下的问题出现。
29.作为本发明的进一步方案,套筒19下端侧壁开设有补偿环槽70,补偿环槽70外端套设有施力板71,施力板71竖向滑动在补偿环槽70内,施力板71外壁滑动设置在电池限位区17之间内壁;从而使得套筒19在举升电池时能带动施力板71上移,从而使得施力板71对电池进行举升和卸载工作,避免了电池应力集中,从而导致变形的问题出现。