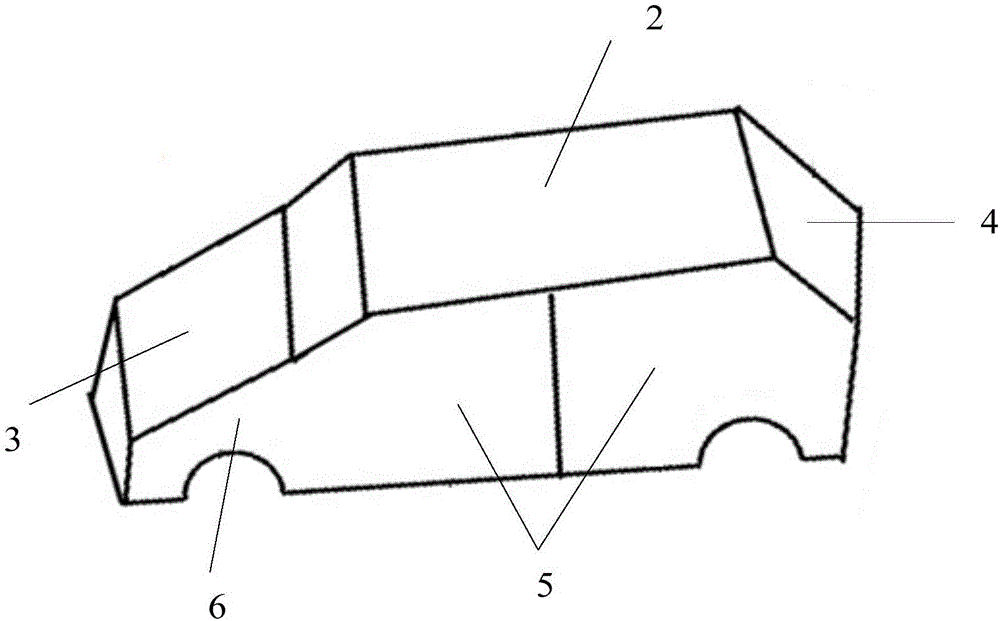
本实用新型涉及汽车
技术领域:
,尤其涉及一种应用夹层板的车身结构及汽车。
背景技术:
:轻量化、高性能、低能耗和安全舒适是汽车工业发展的必然趋势,也是促进车身材料技术进步的主动力。现有技术中的车身材料在满足轻量化的同时车身的强度会降低,无法保证车身刚度的要求。或者车身材料可以满足车身轻量化和车身强度的要求,但所采用的车身材料成本较高,大大提升整车的造价。“三明治”式夹层结构为具有多功能集成特性的轻质结构,且具有结构合理,刚度大,抗冲击性能优良的特性,在汽车行业具有重要的应用前景。技术实现要素:本实用新型提供一种应用夹层板的车身结构及汽车,以提升车身结构的刚度、实现车身结构的轻量化并降低成本,解决现有技术中车身材料不能同时满足刚度和轻量化的需求或者车身材料成本高提升整车造价的问题。本实用新型提供一种应用夹层板的车身结构,所述夹层板包括:第一面板、第二面板以及位于所述第一面板和所述第二面板之间的树脂层,所述树脂层的厚度大于所述第一面板和所述第二面板的厚度,所述第一面板和所述第二面板为金属板;所述车身结构包括:设置于汽车顶部的顶盖、设置于发动机上方的机罩、位于汽车后端的后背门、车门以及翼子板;其中,所述顶盖、后背门外板以及车门外板采用差厚复合、同材质的两面板形成的夹层板制成,或者采用等厚复合、不同材质的两面板形成的夹层板制成;机罩外板采用差厚复合、同材质的两面板形成的夹层板制成,或者采用不同材质、差厚或等厚的两面板形成的夹层板制成;所述翼子板采用差厚或等厚复合、同材质的两面板形成的夹层板制成。优选的,所述顶盖、所述机罩外板、所述后背门外板、所述车门外板以及所述翼子板所采用的夹层板的树脂层的厚度在0.3mm~1.0mm之间,所采用的夹层板的第一面板和第二面板的厚度均在0.2mm~0.3mm之间。优选的,所述顶盖、所述后背门外板、所述车门外板、所述机罩外板以及所述翼子板所采用的夹层板的两面板均为钢板,且位于外层的第一面板的厚度大于位于内层的第二面板的厚度。优选的,所述顶盖和所述车门外板所采用的夹层板的两面板的厚度相同,且位于外层的第一面板为钢板,位于内层的第二面板为铝合金板或镁合金板。优选的,所述后背门外板和所述机罩外板所采用的夹层板的两面板的厚度相同,且位于外层的第一面板为钢板,位于内层的第二面板为铝合金板。优选的,所述机罩外板所采用的夹层板的两面板的厚度不同,位于外层的第一面板为铝合金板,位于内层的第二面板为钢板,且位于外层的第一面板的厚度大于位于内层的第二面板的厚度。优选的,所述机罩外板所采用的夹层板的两面板的厚度不同,位于外层的第一面板为钢板,位于内层的第二面板为铝合金板,且位于外层的第一面板的厚度大于位于内层的第二面板的厚度。优选的,所述翼子板所采用的夹层板的两面板均为钢板,且两面板的厚度相同。优选的,所述车身结构还包括:车身地板和车身隔板,所述车身地板和所述车身隔板均采用夹层板制成,且所述车身地板和所述车身隔板所采用的夹层板的两面板的厚度不同,位于底层的第一面板为钢板,位于上层的第二面板为铝合金板,位于底层的第一面板的厚度大于或者等于位于上层的第二面板的厚度。本实用新型还提供一种汽车,所述汽车包括上述的应用夹层板的车身结构。本实用新型技术方案的有益效果至少包括:本实用新型技术方案,根据车身零部件的需求设置不同规格的夹层板,利用不同规格的夹层板制成不同的器件,通过夹层板零件的应用,可以在零件相同重量的条件下显著提升刚度,提升整车舒适性和竞争力;通过夹层板零件的应用,可在零件相同刚度的条件下显著降低零部件重量,提升车身的轻量化水平;在实现轻量化的同时可降低整车重心,提升整车操控性、安全性及舒适性,提高车辆的溢价能力和竞争力。进一步的,夹层板根据应用部位和目的的不同,面板可进行钢板、铝合金、镁合金的定制化组合,有效实现零件性能提升和轻量化的集成优化。附图说明图1表示本实用新型夹层板结构示意图;图2表示本实用新型应用夹层板的车身结构示意图;图3表示本实用新型第一规格的夹层板示意图;图4表示本实用新型第二规格的夹层板示意图;图5表示本实用新型第三规格的夹层板示意图;图6表示本实用新型第四规格的夹层板示意图;图7表示本实用新型第五规格的夹层板示意图;图8a~图8c表示现有技术的机罩断面示意图;图8d表示本实用新型的机罩断面示意图;图9表示本实用新型第六规格的夹层板示意图。其中图中:1、夹层板;11、第一面板;12、第二面板;13、树脂层;2、顶盖;3、机罩;4、后背门;5、车门;6、翼子板。具体实施方式下面将结合本实用新型实施例中的附图,对本实用新型实施例中的技术方案进行清楚、完整地描述,显然,所描述的实施例是本实用新型一部分实施例,而不是全部的实施例。基于本实用新型中的实施例,本领域普通技术人员在没有作出创造性劳动前提下所获得的所有其他实施例,都属于本实用新型保护的范围。本实用新型实施例提供一种应用夹层板的车身结构,如图1所示,夹层板1包括:第一面板11、第二面板12以及位于第一面板11和第二面板12之间的树脂层13,树脂层13的厚度大于第一面板11和第二面板12的厚度,第一面板11和第二面板12为金属板;如图2所示,车身结构包括:设置于汽车顶部的顶盖2、设置于发动机上方的机罩3、位于汽车后端的后背门4、车门5以及翼子板6;其中,顶盖2、后背门外板以及车门外板采用差厚复合、同材质的两面板形成的夹层板制成,或者采用等厚复合、不同材质的两面板形成的夹层板制成;机罩外板采用差厚复合、同材质的两面板形成的夹层板制成,或者采用不同材质、差厚或等厚的两面板形成的夹层板制成;翼子板6采用差厚或等厚复合、同材质的两面板形成的夹层板制成。其中差厚复合是指不同厚度的两面板进行复合,差厚复合的两面板除厚度外其余尺寸都相等,等厚复合的两面板的各个尺寸均相等。具体的,如图1所示,夹层板1的结构为:位于中间的树脂层13,与树脂层13的第一端面连接的第一面板11,与树脂层13的第二端面连接的第二面板12,其中第一端面与第二端面相对,且中间的树脂层13的厚度大于第一面板11和第二面板12的厚度。面板具有密度大、模量高及强度高的特性。“三明治”式的夹层板的力学原理类似于“工”字梁,具有优异的力学性能。当夹层板承受弯曲载荷时,面板相当于翼缘作为主要承力部位承受拉伸或压缩载荷,中间层作为腹板承受弯曲时的剪力和部分弯矩。因面板具有密度大、模量高和强度高等特征,具有提高夹层板整体刚度的作用;厚度较大的树脂层的存在显著增加夹层板的截面惯性矩,使夹层板的抗弯刚度显著提升,“三明治”结构刚度效应原理如表1中所示,其中间层的密度较低,质量忽略不计。两侧面板厚度和夹层板整体厚度三明治结构相对质量相对弯曲刚度1t1112t1714t137表1其中,为了具备简单加工性能的非深冲型复合板,通过前期零部件的计算机辅助工程和同步工程的分析,结合车身相关零件外板结构简单的特点,可实现轻质夹层板零件的开发应用。如图2所示,应用夹层板的车身结构包括:设置于汽车顶部的顶盖2、设置于发动机上方的机罩3、位于汽车后端的后背门4、车门5以及翼子板6。其中顶盖2、机罩3、后背门4、车门5以及翼子板6均属于汽车上的开闭件。其中顶盖2采用差厚复合、同材质的两面板形成的夹层板制成,也可以采用等厚复合、不同材质的两面板形成的夹层板制成。在采用差厚复合时,位于外层的面板的厚度大于位于内层的面板的厚度;在采用等厚复合时,位于外层的面板的强度大于内层的面板的强度。后背门外板采用差厚复合、同材质的两面板形成的夹层板制成,其中位于外层的面板的厚度大于位于内层的面板的厚度;后背门外板也可以采用等厚复合、不同材质的两面板形成的夹层板制成,其中位于外层的面板的强度大于内层的面板的强度。车门外板采用差厚复合、同材质的两面板形成的夹层板制成,车门外板也可以采用等厚复合、不同材质的两面板形成的夹层板制成。其中,在差厚复合时,位于外层的面板的厚度大于位于内层的面板的厚度,在等厚复合时,位于外层的面板的强度大于内层的面板的强度。机罩外板采用差厚复合、同材质的两面板形成的夹层板制成,此时外层面板的厚度大于内层面板的厚度;还可以采用不同材质、等厚度的两面板形成的夹层板制成,此时外层面板的刚度大于内层面板的刚度;也可以采用不同材质、不同厚度的两面板形成的夹层板制成,此时外层面板的厚度大于内层面板的厚度。翼子板6采用差厚复合、同材质的两面板形成的夹层板制成,此时外层面板的厚度大于内层面板的厚度;翼子板6也可以采用等厚复合、同材质的两面板形成的夹层板制成。本实用新型根据轻质夹层板的结构特点和性能优势,进行车身开闭件外板零件的开发应用,可以在保证制造工艺可行性及成本合理的前提下,有效的实现外板零件刚度的提升和整车的轻量化,对整车性能提升及节能减排具有重要的现实价值。在本实用新型实施例中,如图1和图2所示,顶盖2、机罩外板、后背门外板、车门外板以及翼子板6所采用的夹层板1的树脂层13的厚度在0.3mm~1.0mm之间,所采用的夹层板1的第一面板11和第二面板12的厚度均在0.2mm~0.3mm之间,可以在实现零部件轻量化的同时保证零部件的刚度。本实用新型将夹层板在实现制备工艺可行的前提下应用于汽车车身开闭件外板,可显著提升零部件及车身刚度,且轻量化效果显著,具有重要的应用价值。在本实用新型实施例中,如图2和图3所示,顶盖2、后背门外板、车门外板、机罩外板以及翼子板6所采用的夹层板1的两面板均为钢板,且位于外层的第一面板11的厚度大于位于内层的第二面板12的厚度。具体的,顶盖2采用第一规格的夹层板1制成,第一规格的夹层板1的第一面板11、第二面板12均为钢板,且位于外层的第一面板11的厚度大于内层的第二面板12的厚度,此种规格的顶盖2对应的连接工艺包括:点焊、激光焊、胶接。同时后背门外板、车门外板、机罩外板以及翼子板6均可采用第一规格的夹层板1制成,则此种规格的后背门外板对应的连接工艺包括:点焊、铆接、螺接、激光焊、胶接;此种规格的车门外板对应的连接工艺包括:点焊、铆接、螺接、激光焊、弧焊、胶接;此种规格的机罩外板对应的连接工艺包括:点焊、激光焊、铆接、胶接;此种规格的翼子板6对应的连接工艺包括:点焊、激光焊、铆接、胶接。需要说明的是,顶盖2、后背门外板、车门外板、机罩外板以及翼子板6使用第一规格的夹层板1制成,但根据零件的使用需求,各个零件所采用的夹层板1的厚度有所区别,即树脂层13的厚度、第一面板11和第二面板12的厚度有所不同。在本实用新型实施例中,如图2、图4和图5所示,顶盖2和车门外板所采用的夹层板1的两面板的厚度相同,且位于外层的第一面板11为钢板,位于内层的第二面板12为铝合金板或镁合金板。如图2和图4所示,具体的,顶盖2采用第二规格的夹层板1制成,第二规格的夹层板1的第一面板11、第二面板12的材质不同,位于外层的第一面板11为钢板,位于内层的第二面板12为铝合金板,且第一面板11和第二面板12的厚度相同。此种规格的顶盖2对应的连接工艺包括:铆接、激光焊、胶接。同时车门外板也可采用第二规格的夹层板1制成,则此种规格的车门外板对应的连接工艺包括:铆接、激光焊、胶接。如图2和图5所示,顶盖2也可采用第三规格的夹层板1制成,第三规格的夹层板1的第一面板11、第二面板12的材质不同,位于外层的第一面板11为钢板,位于内层的第二面板12为镁合金板,且第一面板11和第二面板12的厚度相同。此种规格的顶盖2对应的连接工艺包括:铆接、激光焊、胶接。同时车门外板也可采用第三规格的夹层板1制成,则此种规格的车门外板对应的连接工艺包括:铆接、激光焊、胶接。顶盖2、车门外板使用第三规格的夹层板1制成,但根据零件的使用需求,各个零件所采用的夹层板1的厚度有所区别,即树脂层13的厚度、第一面板11和第二面板12的厚度有所不同。在本实用新型实施例中,如图2和图4所示,后背门外板和机罩外板所采用的夹层板1的两面板的厚度相同,且位于外层的第一面板11为钢板,位于内层的第二面板12为铝合金板。具体的,后背门外板、机罩外板采用第二规格的夹层板1制成,第二规格的夹层板1的第一面板11、第二面板12的材质不同,位于外层的第一面板11为钢板,位于内层的第二面板12为铝合金板,且第一面板11和第二面板12的厚度相同。此种规格的后背门外板对应的连接工艺包括:铆接、激光焊、胶接;此种规格的机罩外板对应的连接工艺包括:铆接、激光焊、胶接。需要说明的是,顶盖2、车门外板、后背门外板、机罩外板使用第二规格的夹层板1制成,但根据零件的使用需求,各个零件所采用的夹层板1的厚度有所区别,即树脂层13的厚度、第一面板11和第二面板12的厚度有所不同。在本实用新型实施例中,如图2和图6所示,机罩外板所采用的夹层板1的两面板的厚度不同,位于外层的第一面板11为铝合金板,位于内层的第二面板12为钢板,且位于外层的第一面板11的厚度大于位于内层的第二面板12的厚度。具体的,机罩外板采用第四规格的夹层板1制成,第四规格的夹层板1的第一面板11、第二面板12的材质不同,且第一面板11和第二面板12的厚度不同,其中第一面板11为铝合金板,第二面板12为钢板,且铝合金板的厚度大于钢板的厚度;此种规格的机罩外板对应的连接工艺包括铆接、激光焊、胶接。在本实用新型实施例中,如图2和图7所示,机罩外板所采用的夹层板1的两面板的厚度不同,位于外层的第一面板11为钢板,位于内层的第二面板12为铝合金板,且位于外层的第一面板11的厚度大于位于内层的第二面板12的厚度。具体的,机罩外板采用第五规格的夹层板1制成,第五规格的夹层板1的第一面板11、第二面板12的材质不同,且第一面板11和第二面板12的厚度不同,其中第一面板11为钢板,第二面板12为铝合金板,位于外层的第一面板11的厚度大于位于内层的第二面板12的厚度;此种规格的机罩外板对应的连接工艺包括铆接、激光焊、胶接。其中采用第四规格的夹层板1形成的零件与采用第五规格的夹层板1形成的零件相比,具有更优的轻量化。需要说明的是,机罩外板可以采用第一规格、第二规格、第四规格或者第五规格的夹层板制成,下面以机罩为例进行轻质夹层板结构优化分析,如图8a~8c所示为采用普通金属板材的机罩3的断面示意图,为保证零件性能设计要求(刚度、行人保护),使零件断面结构复杂、材料成形性要求高,导致设计、材料及工艺成本的增加;如图8d所示,机罩3采用轻质夹层板后断面形状简单化,同时因材料刚度提升和低密度特性使零部件性能提升,且降低了零件对工艺及材料的要求,提高了零件设计自由度。在本实用新型实施例中,如图2和图9所示,翼子板6所采用的夹层板1的两面板均为钢板,且两面板的厚度相同。其中翼子板6采用第六规格的夹层板1制成,第六规格的夹层板1的第一面板11、第二面板12的材质相同,均为钢板,且第一面板11和第二面板12的厚度相同。此种规格的翼子板6对应的连接工艺包括点焊、激光焊、铆接、胶接。在本实用新型实施例中,通过轻质夹层板材料及结构设计,其零件可通过铆接、螺接、电阻点焊、弧焊、激光焊、胶接等工艺实现连接,在合适的参数和辅助工装的条件下激光钎焊也可实现有效连接。本实用新型基于“三明治”结构刚度效应原理,研究识别轻质夹层板车身开闭件外板结构(包括机罩外板、翼子板、车门外板、顶盖及后背门外板等),在保证制造工艺可行性及成本合理的前提下,与刚度相同的普通钢质零件相比可实现减重30%~40%,而且降低整车重心,满足整车轻量化发展需求;同时也具有提高整车行人保护及NVH(Noise、Vibration、Harshness噪声、振动与声振粗糙度)性能的优点。根据应用部位和目的的不同,通过开展目标优化,高强度面板可进行钢板、铝合金板材、镁合金板材的定制化组合,实现性能、重量及成本的集成优化。进一步的,应用夹层板的车身结构还可以包括:车身地板和车身隔板,车身地板和车身隔板均采用夹层板制成,且车身地板和车身隔板所采用的夹层板的两面板的厚度不同,位于底层的第一面板为钢板,位于上层的第二面板为铝合金板,位于底层的第一面板的厚度大于或者等于位于上层的第二面板的厚度。具体的,如图7所示,车身地板和车身隔板采用第五规格的夹层板1制成,第五规格的夹层板1的第一面板11、第二面板12的材质不同,且第一面板11和第二面板12的厚度不同,其中第一面板11为钢板,第二面板12为铝合金板,且钢板的厚度大于铝合金的厚度,可以进一步保证整车的刚度。具体的,如图4所示,车身地板和车身隔板采用第二规格的夹层板1制成,第二规格的夹层板1的第一面板11、第二面板12的材质不同,第一面板11和第二面板12的厚度相同,其中第一面板11为钢板,第二面板12为铝合金板,同样可以保证整车的刚度。需要说明的是,车身地板和车身隔板可以采用第二规格的夹层板1或第五规格的夹层板1制成,但车身地板和车身隔板采用的第二规格的夹层板1的厚度与其他器件所采用的第二规格的夹层板1的厚度有所区别;相应的车身地板和车身隔板采用的第五规格的夹层板1的厚度与其他器件所采用的第五规格的夹层板1的厚度也有所区别。综上,不同的零件虽然可以采用同一规格的夹层板制成,但各个零件由于用途和安装位置的差异,其夹层板的厚度有所区别。本实用新型实施例还提供一种汽车,包括上述的应用夹层板的车身结构。以上所述的是本实用新型的优选实施方式,应当指出对于本
技术领域:
的普通人员来说,在不脱离本实用新型所述的原理前提下还可以作出若干改进和润饰,这些改进和润饰也在本实用新型的保护范围内。当前第1页1 2 3