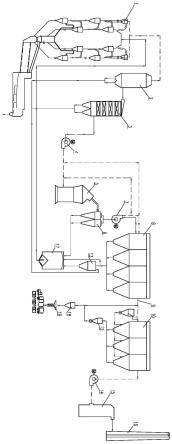
1.本发明涉及一种净化系统及方法,尤其涉及一种水泥窑窑尾烟气脱汞与其它重金属的净化系统及方法。
背景技术:2.水泥窑协同处置垃圾焚烧飞灰及一般固体废弃物、危险废弃物,是指在水泥生产的同时将满足或经过预处理后满足入窑要求的飞灰及固危废进行无害化处理,并将其作为替代原料或燃料,从而实现物料和能源的最大化利用的处置过程。
3.由于垃圾焚烧飞灰、一般固废及危废中含有大量重金属元素(如hg、tl、cd、as、pb等),以及燃煤电厂的粉煤灰作为辅料应用和水泥煅烧过程中的使用的燃煤都会带入金属汞,在水泥窑协同处置过程中,这些重金属容易成为气态或附着在颗粒物表面从而进入烟气中,而现有的窑尾烟气处理工艺,难以处理这些重金属,难以做到按国家标准限值排放。
4.目前水泥行业鲜有烟气脱hg及重金属的应用案例,偶有个别项目是在脱硝脱硫过程中附带对汞做一些处理,对其他重金属基本没有针对性净化处理。
5.关于水泥行业窑尾烟气脱汞,现有技术中在理论上存在两种技术路线,一种是催化剂氧化法,一种是窑尾收尘器吸附法。以上两种技术路线都没有将hg从烧成系统中脱除出来,hg在烧成系统、生料制备系统及窑尾烟气处理系统中的循环富集问题始终无法得到解决,hg的富集压力会成为排放的堰塞湖,为事故排放埋下隐患。另外,hg其实也是一种资源,由于《关于汞的水俣公约》规定不允许开采矿石初次制汞,上述两种路线也同样无法实现固废中汞的资源化处置。
6.除此之外,其他半挥发性质的重金属,比如tl、cd、as、pb等在现有技术中都缺乏必要的处理措施和手段,这些半挥发性质的重金属逃逸到大气中,会对环境造成极大危害。
技术实现要素:7.发明目的:本发明旨在提供一种能实现重金属超低排放的水泥窑窑尾烟气脱汞与其它重金属的净化系统;本发明的另一目的在于提供一种所述净化系统进行窑尾烟气脱汞及其它重金属的方法。
8.技术方案:本发明所述的水泥窑窑尾烟气脱汞与其它重金属净化系统,包括按顺序依次相连的窑尾预热器(1)、余热锅炉(2)、scr脱硝装置(3)、高温风机(4)、原料磨系统(5)、旋风收尘器(6)、原料磨风机(7)、窑尾收尘器、窑尾排风机(14)、湿法脱硫塔(15)和窑尾烟囱(16),所述窑尾收尘器包括窑尾一级收尘器(8)和窑尾二级收尘器(10),所述窑尾一级收尘器(8)依次与窑灰仓(13)、生料均化库(17)相连,所述窑尾二级收尘器(10)的底部烟道上设有与吸附剂喷射装置(11)相连的吸附剂喷射点,并且窑尾二级收尘器(10)的灰斗出料口与吸附剂收集小仓(12)相连。
9.进一步地,所述窑尾一级收尘器(8)与窑尾二级收尘器(10)之间的连接管道上还设有吸附剂喷射点,用于吸附剂收集小仓(12)内的吸附剂复喷至连接管道内,吸附剂循环
使用。
10.进一步地,所述吸附剂收集小仓(12)下方还连接有吸附剂储仓(18)和吸附剂散装系统(19)。
11.利用所述净化系统进行窑尾烟气脱汞及其它重金属的方法,包括以下步骤:
12.①
来自窑尾预热器(1)的烟气先进入余热锅炉(2)进行余热回收,然后进入scr脱硝装置(3)进行脱硝,脱硝后经高温风机(4)送入原料粉磨系统(5),后经旋风收尘器(6)及原料磨风机(7)进入窑尾一级收尘器(8),或直接由高温风机(4)直接送入窑尾一级收尘器(8);
13.②
在窑尾一级收尘器(8)内,将窑灰捕集下来,送入窑灰仓(13),然后送入生料均化库(17),进而将窑灰送回窑尾预热器(1)的喂料点,净化后的烟气进入窑尾二级收尘器(10),吸附剂喷射装置(11)将吸附剂喷洒入窑尾二级收尘器(10)的底部烟道内,进行hg及其它重金属吸附,窑尾二级收尘器(10)将新鲜吸附剂及复喷吸附剂收集下来,送入吸附剂收集小仓(12),然后再被喷入窑尾一级收尘器(8)与窑尾二级收尘器(10)之间的连接管道中,吸附剂循环利用,直至达到富集要求后,外排送去资源化处置;
14.③
窑尾二级收尘器(10)净化后的烟气经窑尾排风机(14)送入湿法脱硫塔(15)中进行湿法脱硫,脱硫后送入窑尾烟囱(16)外排。
15.步骤(2)中所述高效吸附剂为改性活性炭或是改性三聚氰胺类高分子材料,其元素为c、h、n。
16.进一步地,步骤(2)中所述富集要求为吸附剂内hg的质量浓度≥2.5%。
17.进一步地,所述其它重金属为tl、cd、as或pb。
18.有益效果:与现有技术相比,本发明具有如下显著优点:(1)本发明操作简单,真正实现将hg等重金属从烧成系统及窑尾烟气处置系统中分离出来,实现资源化处置,并杜绝hg等重金属脱除过程中的二次污染,并且节约了吸附剂用量,降低了烟气处置成本,是实现水泥窑烟气no
x
、so2,hg及其它重金属tl、cd、as、pb,二噁英和粉尘的超低排放的有效手段;(2)水泥窑协同处置垃圾焚烧飞灰及固体废弃物、危险废弃物时窑尾废气中hg等重金属超低排放;(3)脱除出来的重金属hg资源化处置,达到富集标准后可再生利用;(4)减少烧成系统中hg等重金属循环富集;(5)减轻熟料中重金属含量消纳负担;(6)减少烧成系统中重金属催化合成二噁英,减少二噁英排放控制负担;(7)提高吸附剂的吸附率,减少吸附剂用量;(8)杜绝重金属净化过程中衍生的二次污染。
附图说明
19.图1是本发明实施例所述实施方案的工艺系统流程图;
20.图2是本发明对比例1所述实施方案的工艺系统流程图;
21.图3是本发明对比例2所述实施方案的工艺系统流程图。
具体实施方式
22.下面结合附图对本发明的技术方案作进一步说明。
23.如图1所示,本发明所述系统包括如下部件:1.窑尾预热器、2.余热锅炉、3.scr脱硝装置、4.高温风机、5.原料磨系统、6.旋风收尘器、7.原料磨风机、8.窑尾一级收尘器、9.
烟道、10.窑尾二级收尘器、11.吸附剂喷射装置、12.吸附剂收集小仓、13.窑灰仓、14.窑尾排风机、15.湿法脱硫塔、16.窑尾烟囱、17.生料均化库、18.吸附剂储仓、19.吸附剂散装系统。
24.实施例1
25.本发明所述水泥窑窑尾烟气脱汞与其它重金属净化系统包括按顺序依次相连的窑尾预热器1、余热锅炉2、scr脱硝装置3、高温风机4、原料磨系统5、旋风收尘器6、原料磨风机7、窑尾收尘器、窑尾排风机14、湿法脱硫塔15和窑尾烟囱16,所述窑尾收尘器包括窑尾一级收尘器8和窑尾二级收尘器10,所述窑尾一级收尘器8依次与窑灰仓13和生料均化库17相连,所述窑尾二级收尘器10的底部烟道上设有与吸附剂喷射装置11相连的吸附剂喷射点,并且窑尾二级收尘器10的灰斗出料口与吸附剂收集小仓12相连。所述窑尾一级收尘器8与窑尾二级收尘器10之间的烟道9上还设有吸附剂喷射点,用于吸附剂收集小仓12内的吸附剂复喷至连接管道内,吸附剂循环使用。所述吸附剂收集小仓12下方还连接有吸附剂储仓18和吸附剂散装系统19。基于上述系统的窑尾烟气脱汞及其它重金属方法,包括以下步骤:
26.步骤一:来自窑尾预热器1的烟气先进入余热锅炉2进行余热回收,同时在余热锅炉2内有部分降尘作用,然后进入中温scr脱硝装置3进行脱硝,脱硝后经高温风机4送入原料粉磨系统5,然后经旋风收尘器6及原料磨风机7进入窑尾一级收尘器8,或直接由高温风机4直接送入窑尾一级收尘器8。
27.步骤二:在窑尾一级收尘8内,将窑灰捕集下来,送入窑灰仓13,然后送入生料均化库17,进而将窑灰送回烧成系统,净化后的烟气进入窑尾二级收尘器10,吸附剂喷射装置11将新鲜吸附剂喷洒入窑尾二级收尘器10的底部烟道内,进行hg及其它重金属吸附,窑尾二级收尘器10灰斗将新鲜吸附剂及复喷吸附剂收集下来,送入吸附剂收集小仓12,然后再被喷入窑尾一级收尘器8与窑尾二级收尘器10之间的烟道9中,吸附剂循环利用,直至达到富集要求(吸附剂内hg的质量浓度≥2.5%)后,外排至达到富集标准的吸附剂储仓18内,然后送入吸附剂散装系统(19),这种达到富集标准的灰粉,可以委外实现hg等重金属的资源化处置。
28.步骤三:窑尾二级收尘器10净化后的烟气经窑尾排风机14送入湿法脱硫塔15中进行湿法脱硫,脱硫后送入窑尾烟囱16外排。
29.高效吸附剂为一种改性活性炭或是一种三聚氰胺改性高分子材料(其元素为c、h、n)或其混合物。
30.窑尾预热器1出口风温为260~350℃,粉尘浓度低于60g/nm3,nox浓度低于120mg/nm3;so2浓度低于100mg/nm3;hg浓度低于150μg/nm3,(tl、cd、as、pb)低于3.0mg/nm3。
31.经过窑尾余热锅炉2余热利用,以及经过scr脱硝装置3后,烟气温度范围200~240℃,粉尘浓度低于30g/nm3,nox浓度低于30~50mg/nm3,so2浓度低于100mg/nm3,hg浓度低于120μg/nm3,(tl、cd、as、pb)低于2.5mg/nm3。
32.经过窑尾一级收尘器后,烟气温度范围100~180℃,粉尘浓度低于5~10mg/nm3,nox浓度低于30~50mg/nm3,so2浓度低于80mg/nm3,hg浓度低于90μg/nm3,(tl、cd、as、pb)低于2.0mg/nm3。
33.窑尾二级收尘器10出口处烟气中hg含量小于25μg/nm3,(tl、cd、as、pb)低于0.8mg/nm3。
34.窑尾二级收尘器10出口烟气经窑尾排风机14送入湿法脱硫塔15,脱硫后,烟气温度范围30~50℃,粉尘浓度低于5mg/nm3,nox浓度低于30~50mg/nm3,so2浓度低于20mg/nm3,烟气中hg含量小于25μg/nm3,(tl、cd、as、pb)低于0.8mg/nm3,so2对于二噁英的低温合成有抑制作用,本系统湿法脱硫放置到流程最后,有利于减少二噁英的低温合成。
35.利用实施例1所述系统对某水泥生产企业窑尾废气进行重金属脱除处理,其中烟气在窑尾一级收尘器出口测得hg含量为100μg/nm3,(tl、cd、as、pb)含量为1.5mg/nm3,经过二级除尘器并喷射吸附剂处理后,在二级收尘器出口测得hg含量为20μg/nm3,(tl、cd、as、pb)含量为0.6mg/nm3,去除率达80%以上,烟气排放浓度达到超低排放标准,并且经过吸附剂循环利用后,吸附剂内富集的hg含量大于2.5%,达到资源化处置标准。
36.对比例1
37.本对比例采用催化剂氧化法进行,装置图如图2所示,整个系统包括:窑尾预热器1、余热锅炉2、scr脱硝装置3、高温风机4、原料磨系统5、旋风收尘器6、原料磨风机7、窑尾袋收尘器、窑尾排风机14、湿法脱硫塔15、窑灰仓13、生料均化库17及窑尾烟囱16。
38.使用催化剂氧化法,利用窑尾烟气脱硝装置,在脱硝的同时,通过增加氧化性催化剂把单质hg0氧化为hg
2+
,二价hg
2+
的化合物饱和蒸气压低,易吸附在颗粒表面并团聚,容易被窑尾袋收尘器捕集下来,同时,二价hg
2+
的化合物易溶于水,未被窑尾收尘器捕集的二价hg
2+
结合后续湿法烟气脱硫装置实现hg的有效脱除(也有未考虑湿法脱硫工艺的,剩余的二价hg
2+
及hg0,排入大气)。
39.该种处理方法,催化剂将hg0氧化为hg
2+
,协同处置工艺烟气中含有大量cl-,容易与hg
2+
结合生产hgcl2,hgcl2是共价化合物,溶于水,微电离,有剧毒,湿法脱硫过程中,hgcl2会大量进入废水中,一部分进入到脱硫石膏中。通常情况下脱硫废水会回喷至窑头篦冷机内,高温下hgcl2及其他汞的化合物会随水蒸汽挥发,部分经窑头收尘器排入大气,造成窑头烟囱hg排放超标,排出的hg
2+
,容易在污染源周围沉积,造成环境二次污染。另外,催化氧化法,窑尾袋收尘捕集的hg会随着窑灰重新进入烧成系统,在烧成系统内不断循环富集,这种循环富集的倍数是系统hg输入的数十倍,当原料磨停磨时,窑尾袋收尘器粉尘浓度急剧下降,窑尾袋收尘的捕集作用大大下降,没有湿法脱硫装置的生产线会有大量的活性hg
2+
在短时间排入大气,由于缺乏行之有效的在线监测手段,往往这种排放难以被觉察;有湿法脱硫的生产线,脱硫水中会大量溶入hg
2+
,脱硫水回喷到窑头篦冷机后,对窑头烟囱汞排放限值造成直接冲击。而单独窑尾收尘器捕集二价hg
2+
及颗粒汞hg
p
的效率偏低,容易造成窑尾hg排放超标。综上,可以看出这种方法难以从根本上对hg进行脱除。
40.对比例2
41.本对比例采用吸附法,装置图如图3所示,整个系统包括:窑尾预热器1、窑尾余热锅炉2、高温风机3、scr脱硝装置4、原料磨系统5、旋风收尘器6、原料磨风机7、吸附剂收集小仓及吸附剂喷射装置11、窑尾袋收尘器、窑尾排风机14、窑灰仓13、生料均化库17及窑尾烟囱16。
42.吸附法是通过窑尾收尘器入口喷射活性炭吸附(或是干法脱硫技术,脱硫剂兼作吸附剂),hg及重金属被吸附后经窑尾收尘器捕集,由于跟窑灰混在一起,窑灰是资源而且量大,吸附灰无法从系统中拿出而不得不随窑灰一起进入生料均化库17,将再次进入烧成系统,在烧成系统中高温转变为汞蒸气,再次进入窑尾烟气中,使hg及重金属在烧成系统、
窑尾废气处理及生料粉磨系统中循环富集,富集压力增大后易在事故中一次性排放,造成环境污染问题。此外,此种技术路线会在生料中带入炭,生料入窑时,在窑尾c1筒,260~350摄氏度的低温区,加上窑灰中的重金属催化,以及烟气中的cl-离子,更易重新合成二噁英,又对二噁英排放造成压力。