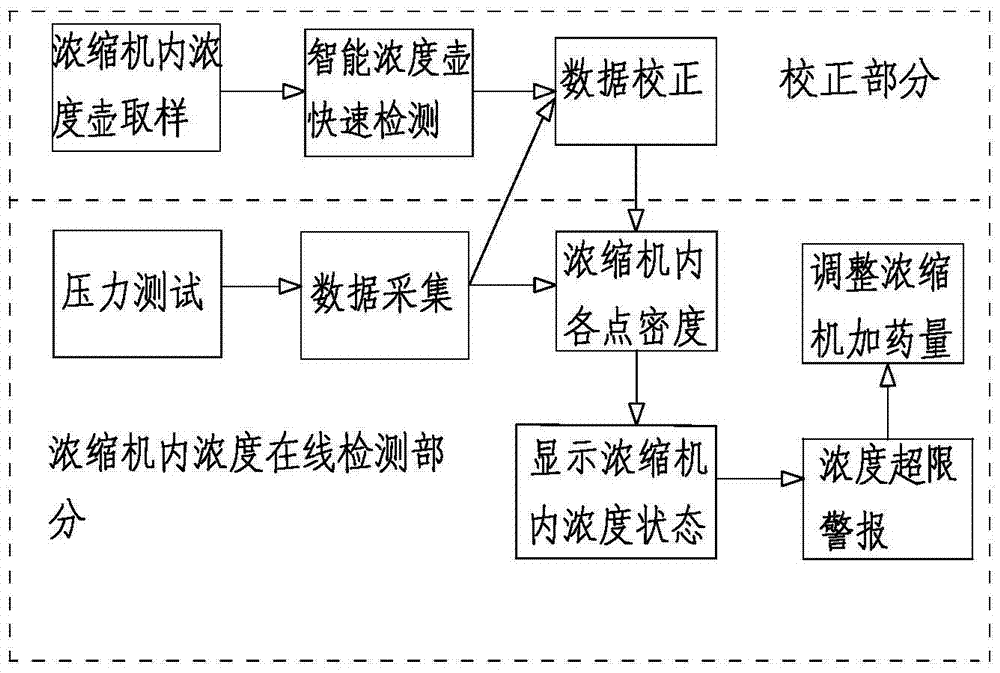
本发明属于选煤技术领域,具体涉及一种用于煤泥水沉降的絮凝剂自动添加系统及其方法。
背景技术:煤泥水处理在除干选以外的所有选煤厂都是最重要的一环之一。煤泥水处理工艺的好坏、完善与否直接影响着选煤厂的生产是否能够顺利进行,是评价一座选煤厂技术和管理水平最重要的因素之一,煤泥水处理效果的好坏影响甚至决定一个矿区的经济效益和社会效益。煤泥水系统担负着回收煤泥、回收水资源的作用,其最终目的是满足环保要求实现洗水闭路循环。在煤泥水处理时,技术人员通常根据浓缩池内物料层的浓度分布,采取在浓缩机前入料管道直接添加凝聚剂和絮凝剂的方法,以达到煤泥水较快净化、沉淀目的;对于絮凝剂加入量的多少直接影响着煤泥水的沉降效果。目前国内外最通常的做法是,先通过人工方法(利用“煤泥探杆”,一种长杆,上有刻度可探浓缩机内床层的厚度)探得浓缩设备内物料层的厚度,根据经验判断添加凝聚剂和絮凝剂量是增大还是减少。现有技术中,国内外比较先进的自动加药方式是中国专利文献CN1958116A公开的“絮凝剂自动添加系统及其方法”,其根据浓度计和流量计检测煤泥水的浓度和流量,由工控机控制泵加入絮凝剂,传感器检测溢流水的浓度,再由工控机判断溢流水浓度,决定是否启动泵向浓缩池内加药;该系统及方法节约了絮凝剂用量、提高了精煤产率,但存在以下问题,导致其未在选煤厂推广运用:(1)系统不完善,只提供一种自动加药方法,没有交代如何添加药剂和采取何种手段分散药剂,以达到深度澄清煤泥水和节省药剂的目的;(2)该系统采用的是开环模式,无法对所添加的药剂量实施监控、反馈及修正,在使用过程中经常出现实际添加药剂量与设定添加量有偏差,造成药剂的浪费;(3)以浓缩机溢流浓度作为唯一考核指标,与实际情况不符,在煤泥水深度澄清中,工程技术人员通常会关心两个问题,首先是浓缩机内床层的浓度分布情况,其次是溢流水浓度,如果只关心溢流水浓度而忽略浓缩机内床层变化,一味添加药剂,将会造成浓缩机“压耙”现象(也即由于浓缩机内床层太厚,浓度太大,导致圆周运动的耙子停止运动,而造成物料无法从浓缩机底流口排出的现象),将严重影响选煤厂的正常生产。因此,本领域技术人员亟需提供一种更节约药剂量、更加完善的用于煤泥水沉降的絮凝剂自动添加系统及其方法。
技术实现要素:针对上述不足,本发明提供了一种更节约药剂量、更加完善的用于煤泥水沉降的絮凝剂自动添加系统及其方法。为实现上述目的之一提供一种用于煤泥水沉降的絮凝剂自动添加系统,本发明采用了以下技术方案:一种用于煤泥水沉降的絮凝剂自动添加系统,包括浓缩机,还包括如下组成部分:煤泥水自动加药系统,该自动加药系统包括依次顺连的煤泥水入料检测单元、监控操作单元、药剂添加单元;所述煤泥水入料检测单元的数据信号输出端均与监控操作单元相连,且监控操作单元的指令传输端与药剂添加单元相连;药剂分散系统,该系统包括连通药剂添加单元的双叶轮发热高效制备桶和药剂添加缓冲桶,药剂添加缓冲桶底部设有两个出料口,其中一个去向螺杆泵与药剂缓冲桶、电动闸阀、恒流药剂流量计、多个射流喷嘴构成恒量加药通道,另一个去向隔膜式计量泵与变量药剂流量计、射流喷嘴构成变量加药通道;恒量加药通道与变量加药通道的药剂均汇入至煤泥水入料管中,且射流喷嘴的朝向均与煤泥水入料管中入料方向一致;由PLC构成的控制系统,煤泥水自动加药系统、药剂分散系统均与控制系统电连接。优选的,所述煤泥水入料检测单元设为电磁流量计与压差式浓度计,分别用于检测出浓缩机入料管的矿浆流量与矿浆浓度,所述监控操作单元包括PLC以及与PLC电连接的触摸屏,所述药剂添加单元包括计量泵。进一步的,所述双叶轮发热高效制备桶包括固定在桶体中轴线上端的双叶轮搅拌器,双叶轮搅拌器的外围固设有套筒,套筒的中轴线与搅拌桶的中轴线重合;所述套筒上设有第一循环孔,所述双叶轮搅拌器在上叶轮上设有第二循环孔,第一循环孔、第二循环孔与下叶轮配合,形成在搅拌桶内部循环的紊流流场。进一步的,在双叶轮发热高效制备桶的内壁上还均匀设有多个电阻发热线圈;在双叶轮发热高效制备桶内还安装有多个均布在桶内的黏度检测探头,所述黏度检测探头与监控操作单元电连接。进一步的,所述双叶轮发热高效制备桶中通过电阻发热线圈控制药剂溶液的温度在40至50℃。进一步的,所述棒条叶轮搅拌缓冲桶内安装有液位传感器Ⅰ、多棒条叶轮搅拌器,液位传感器Ⅰ与PLC电连接。进一步的,所述药剂缓冲桶中设计有与PLC电连接的液位传感器Ⅱ,通过恒流药剂流量计的数据、相应地控制电动闸阀的开启度来调节药剂的流量,进而控制液位处于设定区间。进一步的,多个射流喷嘴朝向相同的安装在浓缩机入料管的中轴线上;且在射流喷嘴的下游处、浓缩机入料管的管道上还安装有充分混合药剂与煤泥水的管道混合器。进一步的,所述射流喷嘴内设有一组配合浓缩机入料管中煤泥水形成旋流的导流叶片;所述管道混合器设为在管道中安装的多组液体混合单元,每一混合单元由多个固定叶片按规定角度交叉组成。本发明的目的之二是提供一种上述絮凝剂自动添加系统的添加方法,具体包括以下工序:S1、浓缩机内的浓度实时传送至煤泥水自动加药系统后,煤泥水入料检测单元首先通过电磁流量计与压差式浓度计检测出浓缩机入料管的矿浆流量与矿浆浓度,数据信号传输至PLC,流量与浓度相乘计算出总干煤泥量,各种数据均显示在触摸屏上;由调度人员根据显示数据在触摸屏上设定控制参数,再由PLC根据设定参数和采集的数据信号计算药剂添加量;S2、设定好药剂添加量后,药剂添加到药剂分散系统的双叶轮发热高效制备桶中,形成循环紊流流场,在40至50℃下药剂快速搅拌溶解,如多个黏度检测探头数据均符合设定值,即开启入料泵将溶液输出至棒条叶轮搅拌缓冲桶,液位传感器Ⅰ检测桶内物料液位,直至液位符合要求;多棒条叶轮搅拌器低速转动,维持已制备好絮凝剂的状态;S3、药剂缓冲桶底部两个出料口的泵开启,其中一个出料口溶液去恒量加药通道,经电动闸阀的开启度来调节药剂的流量,另一个出料口溶液去变量加药通道,两个加药通道的药剂均经射流喷嘴喷出,再与自浓缩机入料管流入的煤泥水经管道混合器充分混合后最后流入浓缩机。本发明的有益效果在于:1)、本发明煤泥水自动加药系统,药剂分散系统,控制系统共同配合构成絮凝剂自动添加系统,与该系统适配的添加方法自动化程度大大提高,极大地减少了人力物力的投入,煤泥水自动加药系统计算药剂添加量、通过PLC驱动药剂添加单元自动加药,自药剂添加单元定量的药剂流入药剂分散系统充分溶解分散后,经两个加药通道中的多个射流喷嘴与煤泥水流入向同向喷出,药剂与煤泥水的混合更加均匀,进而更节约药剂量。2)、本发明可应用在煤泥水深度澄清系统中,其中,药剂添加单元是煤泥水自动加药系统的最终执行环节,系统根据总干煤泥量计算出在此浓度下的最佳凝聚剂与絮凝剂药量,通过计量泵和电动阀门进行加药。同时不断根据实际煤泥水浓度与流量以及煤泥水深度澄清系统中浓缩机内浓度检测系统所反馈的数据信息,计算药剂添加量与恒量加药量的差值,通过控制变量加药通道的隔膜计量泵来完成,有利于药剂添加量迅速到位,消除药剂添加的滞后性。药剂落入药剂分散系统后,在恒量加药通道中的电动闸阀一般不随意改变开度,除非煤质发生重大变化,有利于加药系统的稳定与准确。变量加药通道上隔膜式计量泵出料管处安装有流量计,由于计量泵是转动设备,其自身运动部件的磨损,随着时间的推移可能造成计量泵输出量与计量存在误差,在此环节设计闭路系统,有利于计量泵计量准确与校正。3)、本发明中搅拌桶设为双叶轮发热高效制备桶,与传统搅拌桶相比,其优点在于:①叶轮外有套筒,套筒上有循环孔,可以促进药剂的溶解;②所使用的叶轮是双叶轮,上叶轮上也有循环孔,与下叶轮配合,形成恰到好处的紊流流场;③搅拌桶内壁设置有2组电阻发热线圈,药剂溶液的温度控制在40至50℃,有利于药剂的快速溶解,保证了药剂在冬季的快速溶解。④桶内安装有多个溶液黏度检测探头,黏度检测探头与监控操作单元电连接,如多个黏度检测探头数据均符合设定值,说明溶液制备完成,实现溶液制备状态的自动监控。4)、本发明多个射流喷嘴朝向相同的安装在浓缩机入料管的中轴线上,使药剂溶液在有限空间内射流,形成流核区、基本流动区、回流区、管流区,在下游较远区域呈现出完全管流的流动特性,促进了药剂与煤泥水的均匀混合,为药剂量的节约提供保证。5)、本发明在射流喷嘴的下游处、浓缩机入料管的管道上还安装有管道混合器,是在管道中安装有若干组液体混合单元,每一混合单元由一定数量的固定叶片按规定角度交叉组成;射流喷嘴内设有一组配合浓缩机入料管中煤泥水形成旋流的导流叶片,有利于药剂与煤泥水的进一步混合均匀,提高药剂的使用效率。附图说明图1为本发明应用于煤泥水深度澄清系统中的流程图。图2为煤泥水深度澄清系统中浓缩机内浓度在线监测系统的流程图。图3为本发明煤泥水自动加药系统的流程图。图4为煤泥水深度澄清系统中对浓缩机内密度检测仪所采集数据的运算流程图。图5为本发明应用在煤泥水深度澄清系统的设备连接简示图。图6为煤泥水深度澄清系统中智能浓度壶的结构简示图。图7为煤泥水深度澄清系统中浓缩机内密度检测仪的结构简示图。图8为本发明双叶轮发热高效制备桶及棒条叶轮搅拌缓冲桶的结构示图。图9为本发明中射流喷嘴的主视结构简示图。图10为本发明中射流喷嘴的俯视图。图中标注符号的含义如下:A-浓缩机内浓度在线监测系统A1-智能浓度壶A11-外壳体A111-卡槽A112-提手固定装置A113-内胆支架A114-显示器A12-内胆A13-传感器A131-上支撑板A132-下支撑板A133-上支撑板挡板A134-下支撑板挡板A2-浓缩机内密度检测仪A21-压力变送器B-煤泥水自动加药系统B1-电磁流量计B2-压差式浓度计C-药剂分散系统C1-双叶轮发热高效制备桶C2-螺杆泵C11-双叶轮搅拌器C12-套筒C120-第一循环孔C13-上叶轮C130-第二循环孔C14-下叶轮C15-电阻发热线圈C16-黏度检测探头C3-药剂缓冲桶C30-液位传感器ⅡC4-电动闸阀C5-恒流药剂流量计C6-射流喷嘴C60-导流叶片C7-管道混合器C8-隔膜式计量泵C9-变量药剂流量计C10-棒条叶轮搅拌缓冲桶C100-液位传感器ⅠC101-多棒条叶轮搅拌器D-浓缩机具体实施方式下面将结合本发明实施例中的附图,对本发明中的技术方案进行清楚、完整地描述。基于本发明中的实施例,本领域普通技术人员在没有做出创造性劳动前提下所获得的所有其他实施例,都属于本发明保护的范围。实施例1.本发明应用在煤泥水深度澄清系统中如图1~5所示,一种煤泥水深度澄清系统,包括浓缩机D,还包括如下组成部分:①浓缩机内浓度在线监测系统A,该系统包括校正部分及浓缩机内浓度在线检测部分,校正部分对浓缩机内浓度在线检测部分的数据进行校正;②絮凝剂自动添加系统,本发明絮凝剂自动添加系统包括:煤泥水自动加药系统B,该自动加药系统包括依次顺连的煤泥水入料检测单元、监控操作单元、药剂添加单元;所述浓缩机内浓度在线检测部分、煤泥水入料检测单元的数据信号输出端均与监控操作单元相连,且监控操作单元的指令传输端与药剂添加单元相连;药剂分散系统C,该系统包括连通药剂添加单元、接收药剂的双叶轮发热高效制备桶C1,储备药剂的棒条叶轮搅拌缓冲桶C10底部设有两个出料口,其中一个去向螺杆泵C2与药剂缓冲桶C3、电动闸阀C4、恒流药剂流量计C5、多个射流喷嘴C6构成恒量加药通道,另一个去向隔膜式计量泵C8与变量药剂流量计C9、射流喷嘴C6构成变量加药通道;恒量加药通道与变量加药通道的药剂均汇入至煤泥水入料管中,且射流喷嘴C6的朝向均与煤泥水入料管中入料方向一致;由PLC构成的控制系统,浓缩机内浓度在线监测系统、煤泥水自动加药系统、药剂分散系统均与控制系统电连接。其中,所述校正部分设为对浓缩机内物料进行取样及快速检测浓度的智能浓度壶A1;所述浓缩机内浓度在线检测部分设为浓缩机内密度检测仪A2。如图6所示,所述智能浓度壶A1包括立方体型外壳体A11以及布置于外壳内作为收集煤泥水的筒状内胆A12;所述外壳体A11上段设有卡槽A111、中段设有提手固定装置A112及内胆支架A113,卡槽A111与内胆支架A113均用于固定内胆A12,下段固设有显示器A114,外壳体A11与内胆A12围成的密封空间底部还固设有传感器A13,传感器A13上、下两侧分别设有上、下支撑板A131、A132,且上、下支撑板A131、A132的左右两侧分别设有上、下支撑板挡板A133、A134;所述传感器A13与显示器A114相连,在工作状态下传感器A13将采集来的重量信号转换为煤泥水浓度并显示在显示器A114上;如图7所示,所述浓缩机内密度检测仪A2设为将多个压力变送器A21沿竖向均匀分布固定在密封容器内的测试装置;压力变送器A21的电压输出信号采用数据采集卡采集。浓缩机内密度检测仪A2采集所得的数据可通过计算软件绘制浓缩机内浓度或密度等值线及云图,为加药量、入料给入及底流排放提供技术指导,具体的,计算软件对数据的处理流程如图4所示。压力变送器A21的电压输出信号采用数据采集卡采集。其中,压力变送器A21采用扩散硅型压力变送器;数据采集卡采用MPS-010602多功能USB信号采集卡。如图1、5所示,所述煤泥水入料检测单元设为电磁流量计B1与压差式浓度计B2,分别用于检测出浓缩机入料管的矿浆流量与矿浆浓度,所述监控操作单元包括PLC以及与PLC电连接的触摸屏,所述药剂添加单元包括计量泵。如图8所示,所述双叶轮发热高效制备桶C1包括固定在桶体中轴线上端的双叶轮搅拌器C11,双叶轮搅拌器C11的外围固设有套筒C12,套筒C12的中轴线与搅拌桶的中轴线重合;所述套筒C12上设有第一循环孔C120,所述双叶轮搅拌器在上叶轮C13上设有第二循环孔C130,第一循环孔C120、第二循环孔C130与下叶轮C14配合,形成在搅拌桶内部循环的紊流流场;在双叶轮发热高效制备桶C1的内壁上还均匀设有多个电阻发热线圈C15。在双叶轮发热高效制备桶C1内安装有若干黏度检测探头C16,黏度检测探头C16是等距离布置在桶内,黏度检测探头C16将检测数据通过信号传输单元传输至监控操作单元。如多个黏度检测探头C16数据均符合设定值,说明絮凝药剂制备完成,即开启入料泵将溶液输出至棒条叶轮搅拌缓冲桶C10。棒条叶轮搅拌缓冲桶C10内安装有液位传感器ⅠC100、多棒条叶轮搅拌器C101。液位传感器ⅠC100用于检测桶内物料液位;多棒条叶轮搅拌器C101低速转动,维持已制备好絮凝剂的状态。如图5所示,所述药剂缓冲桶C3中设计有与PLC电连接的液位传感器ⅡC30,通过恒流药剂流量计C5的数据、相应地控制电动闸阀C4的开启度来调节药剂的流量,进而控制液位处于设定区间。多个射流喷嘴C6朝向相同的安装在浓缩机入料管的中轴线上;且在射流喷嘴C6的下游处、浓缩机D入料管的管道上还安装有充分混合药剂与煤泥水的管道混合器C7。如图9、10所示,所述射流喷嘴C6内设有一组配合浓缩机入料管中煤泥水形成旋流的导流叶片C60,导流叶片C60设为4个。所述管道混合器C7设为在管道中安装的多组液体混合单元,每一混合单元由多个固定叶片按规定角度交叉组成。所述双叶轮发热高效制备桶C1中通过电阻发热线圈C15控制药剂溶液的温度在40至50℃。实施例2.本发明应用在煤泥水深度澄清系统中的处理工艺该处理工艺具体包括以下工序:S1、浓缩机内浓度在线监测系统A中通过浓缩机内密度检测仪A2实时检测浓缩机D内物料层变化,完成数据采集,通过计算软件绘制浓缩机D内浓度或密度等值线及云图,显示浓缩机D内浓度状态,当浓度超限时发出警报,进而调整浓缩机加药量;同时,在该在线监测过程中通过浓缩机智能浓度壶A1取样监测后,对浓缩机内浓度在线检测系统A进行定期维护及数据校正,具体的如图1、2所示;S2、如图1、3所示,浓缩机D内的浓度实时传送至煤泥水自动加药系统B后,煤泥水入料检测单元首先通过电磁流量计B1与压差式浓度计B2检测出浓缩机D入料管的矿浆流量与矿浆浓度,数据信号传输至PLC,流量与浓度相乘计算出总干煤泥量,各种数据均显示在触摸屏上;由调度人员根据显示数据在触摸屏上设定控制参数,再由PLC根据设定参数和采集的数据信号计算最佳药剂添加量;同时不断根据实际煤泥水浓度与流量以及浓缩机内在线监测系统A所反馈的数据信息,计算加药量,通过控制计量泵对药剂添加量进行实时调整;对于特定的选煤厂,煤泥水性质在一段时间波动值有限,药剂添加主要由恒量加药通道完成;计算药剂添加量与恒量加药量的差值由变量药剂通道完成,有利于药剂添加量迅速到位,消除药剂添加的滞后性;在变量加药通道的管道上还设有流量计,用于检测隔膜式计量泵的输出量,检测值与计量泵本身计量值对比,实现数据的反馈和计量泵工作状态的监控;其中,煤泥水自动加药系统B设有全自动模式和半自动模式:全自动模式下,PLC根据检测到的煤泥水浓度、流量等数据自动计算所需添加的凝聚剂和絮凝剂,并进行添加;手动模式下,岗位司机根据系统采集到显示于触摸屏上的数据,手动设置凝聚剂和絮凝剂的添加量,PLC根据给定的控制参数计算药剂的添加量;接着,岗位司机再输出控制信号驱动计量泵和电动阀门进行自动加药;同时不断根据实际煤泥水浓度与流量以及浓缩机内浓度在线监测系统A所反馈的数据信息,计算加药量,通过控制计量泵对药剂添加量进行实时调节;并且PLC预留有通讯接口,可以将系统数据传输至调度所,进行监控;S3、如图5、7所示,设定好药剂添加量后,药剂添加到药剂分散系统C的双叶轮发热高效制备桶C1中,形成循环紊流流场,在40至50℃下药剂快速搅拌溶解,如多个黏度检测探头C16数据均符合设定值,即开启入料泵将溶液泵送至棒条叶轮搅拌缓冲桶C10,棒条叶轮搅拌缓冲桶C10内安装有液位传感器ⅠC100、多棒条叶轮搅拌器C101。液位传感器ⅠC100用于检测桶内物料液位,根据药剂缓冲桶内物料液位检测数据,计算消耗的药剂量;多棒条叶轮搅拌器C101低速转动,维持已制备好絮凝剂的状态;溶解后的药剂溶液输出至多棒条叶轮搅拌缓冲桶C10,该桶底部两个出料口,其中一个出料口溶液去恒量加药通道,恒量加药通道上药剂缓冲桶C3中设计有液位传感器ⅡC30,使液位处于设定区间,为药剂在恒量加药通道内的稳定、恒量流入提供保证,其中,恒量药剂流量计C5为电动闸阀C4的调节提供数据支持,再经电动闸阀的开启度来调节药剂的恒定流量;另一个出料口溶液去变量加药通道,两个加药通道的药剂均经射流喷嘴C6喷出;由于射流喷嘴C6均安装在浓缩机D入料管的中轴线上,且朝向均与煤泥水入料管中入料方向一致,保证了在有限空间内的射流,从而与自浓缩机D入料管流入的煤泥水经管道混合器C7充分均匀混合后,最终流入浓缩机D。