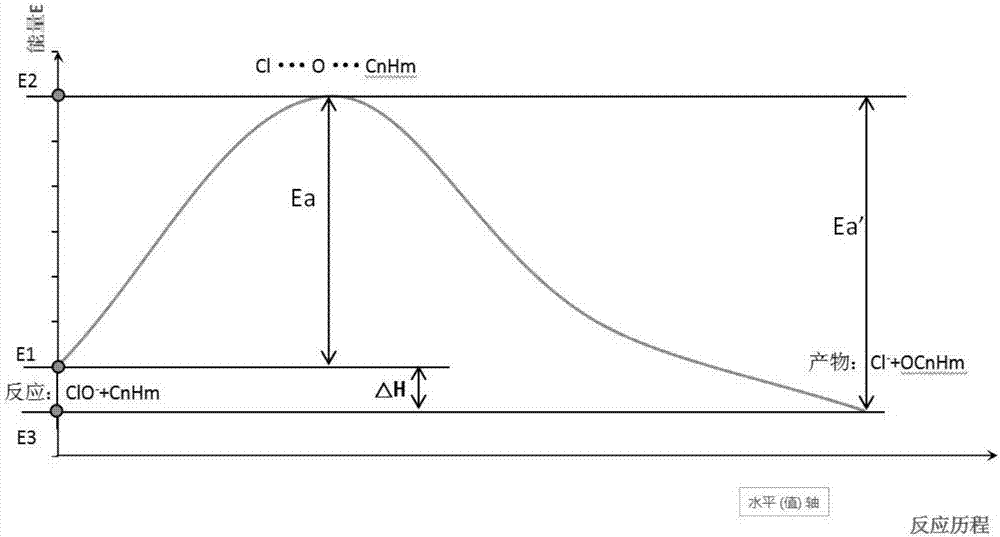
本发明涉及工业废水处理
技术领域:
,采用混凝和漂白粉催化氧化联合处理方法,特别适合印染等一类难降解的工业废水。
背景技术:
:印染废水是我国水量最大的工业废水之一,其特点是水量大、污染重,含有偶氮类、苯胺类、蒽醌类、苯酚类、苯乙烯、双酚a和二氯苯氨等大量有毒有色物质,难降解,对自然水体的危害尤为明显。印染废水以采用生物降解法为主,因为可以实现废水资源化,使污水的处理和利用一体化。但是却存在着设施占地面积大,处理周期长,易受季节、气温、光照等自然因素的影响使效果不稳定等不足之处,尤其是难降解的印染废水的处理效果不理想。所以难降解的印染废水处理研究大多采用两种甚至多种方法联合,其中混凝法是最常用的联合步骤。因为印染废水中高色度、高毒性的染料如分散染料、直接染料、还原染料和硫化染料等多为疏水性的,混凝去除率较高。但活性染料、酸性染料、阳离子染料和中性染料等多为亲水性的,混凝去除率较低。所以混凝法也常与深度氧化联用,常见的氧化剂有过氧化氢、臭氧、高锰酸钾、氯气、次氯酸盐和二氧化氯等。其中,过氧化氢、臭氧、二氧化氯等氧化性强,可以有效去除废水中的色、臭、味,杀菌效果也很好,但是它们除了成本较高以外,由于药剂稳定性差,增大了储存、运输和使用的难度,高锰酸钾则会增大出水和污泥中锰的残留。这些氧化剂的催化氧化中使用的催化剂研究,如fenton试剂等较少是均相的,而以多相催化最常见,存在催化剂制备成本高,用量大,需回收和再生等缺陷,难以推广使用。选用漂白粉对印染废水进行氧化脱色、去除cod,具有价廉,固体药剂易于储存、运输和使用的优点,但有效氯较低,且氧化反应速率和处理效果均有待提高。因此需要筛选高效率、低成本、无需回收和再生的绿色环保型催化剂,才便于推广使用。同时,印染废水大多色度和cod高,仅用氧化处理的漂白粉用量大,除了成本被提高以外,常常引起出水ph过高,难以达到排放标准。所以提出与混凝联合的处理方法,此方法也适用于类似的难降解工业废水的处理。技术实现要素:有鉴于此,本发明的目的是提出一种难降解工业废水的混凝和漂白粉催化氧化联合处理方法,该方法在混凝沉降去除部分cod和色度之后,再采用镁盐催化剂进一步催化漂白粉氧化去除剩余的污染物,能够有效提高反应速率和氧化指数,增强氧化效果。本发明采用以下方案实现:一种难降解工业废水的混凝和漂白粉催化氧化联合处理方法,包括以下步骤:步骤s1:将取自印染厂的工业废水和絮凝剂、助凝剂加入反应器中,控制反应液的ph为5-10,室温下搅拌15-60min,静置20-60min,分离出上层清液;步骤s2:在分离出的清液中加入漂白粉与镁盐催化剂,控制反应液的ph为5-9,室温下搅拌10-60min,完成工业废水的混凝与催化氧化处理过程。进一步地,所述的工业废水与絮凝剂的质量比为1000:0.1-3,絮凝剂与助凝剂聚丙烯酰胺的质量比为1000:1-50。进一步地,所述的工业废水混凝后分离出的清液与漂白粉的质量比为1000:0.2-5,漂白粉与镁盐催化剂的质量比为1000:10-200。进一步地,所述的工业废水为印染废水,也可以为类似的难降解的工业废水。进一步地,所述的絮凝剂为al2(so4)3·18h2o和alcl3中的一种或者两种按照任意比例的混合。进一步地,所述的助凝剂为聚丙烯酰胺。进一步地,所述镁盐催化剂为硫酸镁或氯化镁中的一种或者两种按照任意比例混合。进一步地,所述步骤s1与步骤s2中的搅拌方式为机械搅拌和曝气搅拌中的一种或两种方式交替进行。在本发明中,所述的工业废水为印染废水时,难生物降解的印染废水采用混凝-漂白粉催化氧化法的原理如下:印染废水大多色度和cod高,毒性大,影响生物降解效果,如果仅用漂白粉氧化处理,漂白粉的用量大,除了提高成本以外,常常引起出水ph过高,难以达到排放标准,因此采用混凝联合的处理方法。在所述步骤s1中,若在混凝去除印染废水的污染物中应用絮凝剂al2(so4)3·18h2o和助凝剂聚丙烯酰胺进行处理,能够实现印刷废水的固液分离。根据混凝机理,印刷废水中高色度、高毒性的染料如分散染料、直接染料、还原染料和硫化染料等多为疏水性的,混凝去除率较高,但活性染料、酸性染料、阳离子染料和中性染料等多为亲水性的,混凝去除率较低。因为这些胶粒的表面和水溶性有机污染物大多带有电荷,由于同性电荷之间的相互排斥而使得胶粒分散开来,不易凝聚成大颗粒沉淀下来。向水样中投加带高异性电荷的无机絮凝剂,起到压缩胶粒双电层,降低其电动电位作用,搅拌使胶粒和水溶性污染物相互接触、碰撞,聚集成拥有一定粒径的聚集体,此时高分子有机助凝剂能把这些聚集体通过吸附、架桥、裹挟等作用,进一步凝聚成絮状体,它在寻转、沉降过程中又吸附、卷扫了更多的悬浮和水溶性有机污染物,最终在重力的作用下而沉淀,达到固液分离的目的。在所述步骤s2中,在混凝后的印染废水澄清液的漂白粉氧化过程中,将含镁离子的镁盐作为催化剂添加到反应物中并进行搅拌,能有效促进其在常温常压下产生新生态氧原子,与水作用生成羟自由基,利用羟自由基的强氧化性深度氧化难以生物降解的有色有毒污染物,能够提高氧化反应速率和氧化指数,提高还原性污染物的氧化去除效率。与现有技术相比,本发明有以下有益效果:(1)与生物降解法比较,本发明采用混凝-催化氧化法,在经过混凝处理后的难降解工业废水中投入漂白粉和镁盐催化剂,并进行搅拌,在常温常压下产生新生态氧原子,与水作用生成羟自由基,利用羟自由基的强氧化性深度氧化难以生物降解的有色有毒污染物,反应过程快速直接,使出水达到国家二级排放标准;(2)本发明采用镁盐催化剂,其用量小,催化效率高,能够将氧化指数提高到接近2,在室温下能成倍提高漂白粉的氧化脱色速率,出水codcr比不加催化剂降低三分之一,同时该镁盐催化剂绿色无毒,无需回收和再生,成本低廉,小于0.1元/t废水;(3)本发明的废水处理设施占地少,投资省,处理周期短,设施利用率高,且药剂总费用小于2元/t废水;(4)本发明尤其适用于难生物降解的高毒性印染等工业废水。附图说明图1为本发明中催化氧化联合处理方法的流程示意图。图2为本发明实施例中未加入催化剂的氧化反应历程图。图3为本发明实施例中加入催化剂的催化氧化反应历程图。具体实施方式下面结合附图及实施例对本发明做进一步说明。如图1所示,本实施例提供了一种难降解工业废水的混凝和漂白粉催化氧化联合处理方法,包括以下步骤:步骤s1:将取自印染厂的工业废水和絮凝剂、助凝剂加入反应器中,控制反应液的ph为5-10,室温下搅拌15-60min,静置20-60min,分离出上层清液;步骤s2:在分离出的清液中加入漂白粉与镁盐催化剂,控制反应液的ph为5-9,室温下搅拌10-60min,完成工业废水的混凝与催化氧化处理过程。在本实施例中,所述的工业废水与絮凝剂的质量比为1000:0.1-3,絮凝剂与助凝剂聚丙烯酰胺的质量比为1000:1-50。在本实施例中,所述的工业废水混凝后分离出的清液与漂白粉的质量比为1000:0.2-5,漂白粉与镁盐催化剂的质量比为1000:10-200。在本实施例中,所述的工业废水为印染废水,也可以为类似的难降解的工业废水。在本实施例中,所述的絮凝剂为al2(so4)3·18h2o和alcl3中的一种或者两种按照任意比例的混合。在本实施例中,所述的助凝剂为聚丙烯酰胺。在本实施例中,所述镁盐催化剂为硫酸镁或氯化镁中的一种或者两种按照任意比例混合。在本实施例中,所述步骤s1与步骤s2中的搅拌方式为机械搅拌和曝气搅拌中的一种或两种方式交替进行。在本实施例中,所述的工业废水为印染废水时,难生物降解的印染废水采用混凝-漂白粉催化氧化法的原理如下:印染废水大多色度和cod高,毒性大,影响生物降解效果,如果仅用漂白粉氧化处理,漂白粉的用量大,除了提高成本以外,常常引起出水ph过高,难以达到排放标准,因此采用混凝联合的处理方法。在所述步骤s1中,若在混凝去除印染废水的污染物中应用絮凝剂al2(so4)3·18h2o和助凝剂聚丙烯酰胺进行处理,能够实现印染废水的固液分离。根据混凝机理,印染废水中高色度、高毒性的染料如分散染料、直接染料、还原染料和硫化染料等多为疏水性的,混凝去除率较高。但活性染料、酸性染料、阳离子染料和中性染料等多为亲水性的,混凝去除率较低。因为这些胶粒的表面和水溶性有机污染物大多带有电荷,由于同性电荷之间的相互排斥而使得胶粒分散开来,不易凝聚成大颗粒沉淀下来。向水样中投加带高异性电荷的无机絮凝剂,起到压缩胶粒双电层,降低其电动电位作用,搅拌使胶粒和水溶性污染物相互接触、碰撞,吸附、聚集成拥有一定粒径的聚集体,此时高分子有机助凝剂能把这些聚集体通过吸附、架桥、裹挟等作用,进一步凝聚成絮状体,它在寻转、沉降过程中又吸附、卷扫了更多的悬浮和水溶性有机污染物,最终在重力的作用下而沉淀,达到固液分离的目的。在所述步骤s2中,在混凝后的印染废水澄清液的漂白粉氧化过程中将含镁离子的镁盐作为催化剂添加到反应物中并进行搅拌,能有效促进其在常温常压下产生新生态氧原子,与水作用生成羟自由基,利用羟自由基的强氧化性深度氧化难以生物降解的有色有毒污染物,能够提高氧化反应速率和氧化指数,增强还原性污染物的氧化去除效率。其中,镁盐催化剂的催化机理具体如下:镁离子催化漂白粉氧化的机理较复杂,既有根据过渡态理论的活化络合物中间体形成(如图2和图3所示),又有游离基的参与。将图2和图3进行对比,加催化剂后,如图3所示,各活化络合物能量均有所增加,同时反应物和产物的总能量也有增加;其中,e1为反应物能量,e催为加入催化剂使体系增加的能量,ea为未加催化剂的活化能,ea’为未加催化剂的逆反应活化能,ea催为加入催化剂后的活化能,a为催化剂,cnhm为有机污染物,cl…o…cnhm为clo-与cnhm的活化络合物(以此类推)。因为漂白粉的有效成分是次氯酸钙,其游离基漂白理论认为,次氯酸钙与酸反应产生有漂白性次氯酸,而次氯酸在光照或催化剂作用下能分解产生氧自由基[o],进而与水反应形成同样活泼性很强的羟自由基[ho],反应式如下:ca(clo)2+2h+=ca2++2hclohclo→h++cl-+[o][o]+h2o→[ho]当有带正电荷的催化剂mg2+存在时,根据正离子对酸根的反极化理论,所筛选的mg2+催化剂极化能力比漂白粉中的ca2+强,可在常温常压下促使次氯酸根的cl-o键被松动的程度加大,形成稳定性更差的活化络合物,加快其分解,既降低了催化氧化反应的活化能(图3中由于反应历程的改变,决定催化氧化正反应速率的最大活化能是ea2催,比图2中决定无催化的氧化正反应速率的最大活化能ea小),又可以促进氧自由基[o]和氧化电位高达2.80v羟自由基[ho]的生成,在羟自由基[ho]的强氧化作用及随之产生的各种活性自由基的链式反应中,使废水中的有机物得以氧化,从而加快了氧化速率,同时还打破了氧化剂与还原剂间的电荷平衡,使用cod降低值与氧化剂的耗氧量比值来表示的氧化指数提高到接近2,即少量漂白粉就能降解超量的cod,表现出氧化速率的加快和氧化效率的提高。根据以上步骤给出如下几个实施例进行具体说明:实施例1一、将取自印染厂的印染废水和絮凝剂、助凝剂加入反应器中,控制反应液的ph为9,室温下搅拌30min,静置30min,分离出上层清液;其中,印染废水与絮凝剂al2(so4)3·18h2o的质量比为1000:0.4、絮凝剂al2(so4)3·18h2o与助凝剂聚丙烯酰胺(pam)的质量比为400:1;二、取步骤一的上层清液测定色度去除率,结果列入表1。实施例2实施例2与实施例1的不同之处为:絮凝剂al2(so4)3·18h2o与助凝剂聚丙烯酰胺(pam)按质量比400:2加入反应器中。实施例3实施例3与实施例1的不同之处为:絮凝剂al2(so4)3·18h2o与助凝剂聚丙烯酰胺(pam)按质量比400:3加入反应器中。实施例4实施例4与实施例1的不同之处为:印染废水和絮凝剂al2(so4)3·18h2o按质量比1000:0.5,絮凝剂al2(so4)3·18h2o与助凝剂聚丙烯酰胺(pam)按质量比500:1加入反应器中。实施例5实施例5与实施例1的不同之处为:印染废水和絮凝剂al2(so4)3·18h2o按质量比1000:0.5,絮凝剂al2(so4)3·18h2o与助凝剂聚丙烯酰胺(pam)按质量比500:2加入反应器中4。实施例6实施例6与实施例1的不同之处为:印染废水和絮凝剂al2(so4)3·18h2o按质量比1000:0.5,絮凝剂al2(so4)3·18h2o与助凝剂聚丙烯酰胺(pam)按质量比500:3加入反应器中。实施例7实施例7与实施例1的不同之处为:印染废水与絮凝剂alcl3按质量比1000:0.2,絮凝剂alcl3与助凝剂聚丙烯酰胺(pam)按质量比100:1加入反应器中。表1印染废水混凝结果实施例8一、印染废水和絮凝剂al2(so4)3·18h2o按质量比1000:0.4,絮凝剂al2(so4)3·18h2o与助凝剂聚丙烯酰胺(pam)按质量比400:2加入反应器中,控制ph为9,室温下搅拌30min,静置30min,分离出上层清液;二、按混凝后清液与漂白粉质量比为1000:0.4加入漂白粉,按漂白粉与硫酸镁质量比为10:1加入硫酸镁,控制反应液的ph为6,室温下搅拌30min;三、取步骤二的溶液测定色度去除率,结果列入表2。实施例9实施例9与实施例8的不同之处为:漂白粉与硫酸镁质量比为10:2,控制反应液的ph为7。实施例10实施例10与实施例8的不同之处为:漂白粉与硫酸镁质量比为10:4,控制反应液的ph为8。实施例11实施例11与实施例8的不同之处为:清液与漂白粉质量比为1000:1,漂白粉与硫酸镁质量比为100:4,控制反应液的ph为7。实施例12实施例12与实施例8的不同之处为:清液与漂白粉质量比为1000:1,漂白粉与硫酸镁质量比为100:8,控制反应液的ph为8。实施例13实施例13与实施例8的不同之处为:清液与漂白粉质量比为1000:1,漂白粉与硫酸镁质量比为100:16,控制反应液的ph为6。实施例14实施例14与实施例8的不同之处为:清液与漂白粉质量比为1000:1.6,漂白粉与硫酸镁质量比为40:1,控制反应液的ph为8。实施例15实施例15与实施例8的不同之处为:清液与漂白粉质量比为1000:1.6,漂白粉与硫酸镁质量比为40:2,控制反应液的ph为6。实施例16实施例16与实施例8的不同之处为:清液与漂白粉质量比为1000:1.6,控制反应液的ph为7。实施例17实施例17与实施例8的不同之处为:按漂白粉与氯化镁质量比为10:0.8。实施例18(对照实施例1)对比实施例1的不同之处为:不加硫酸镁催化剂,控制反应液的ph为6。表2混凝后清液催化氧化结果测定codcr:选取下列四组水样测定codcr,结果列入表3:(1)未经处理的印染废水;(2)絮凝后的印染废水清液;(3)不加催化剂只加100mg/l漂白粉处理的印染废水混凝后清液;(4)最佳条件即加入80mg/l硫酸镁,100mg/l漂白粉处理的ph为6的印染废水混凝后清液。表3四组水样的codcr测定结果实验号1(原印染废水)2(絮凝后)3(不加催化剂)4(加催化剂)codcr(mg/l)5923339370脱色速率测定:实施例18(对照实施例1),控制反应液的ph为6,室温下搅拌反应,每5min取反应液一份,4000r/min离心2min,取上层清液测定色度去除率,结果列入表4。按实施例12加漂白粉与硫酸镁,控制反应液的ph为6,每5min取反应液一份,4000r/min离心2min,取上层清液测定色度去除率,结果列入表4。表4ph=6时的催化氧化脱色速率由表4可以看出,ph=6时加了催化剂a后,5min的脱色率已超过不加催化剂的30min效果,且加了催化剂a在15min脱色率即达到最高,而不加催化剂的脱色率需25min以上才达到最高,可见催化剂的催化氧化脱色全程速率提高了近一倍,前期(5min)催化氧化脱色速率提高5倍以上。以上所述仅为本发明的较佳实施例,凡依本发明申请专利范围所做的均等变化与修饰,皆应属本发明的涵盖范围。当前第1页12