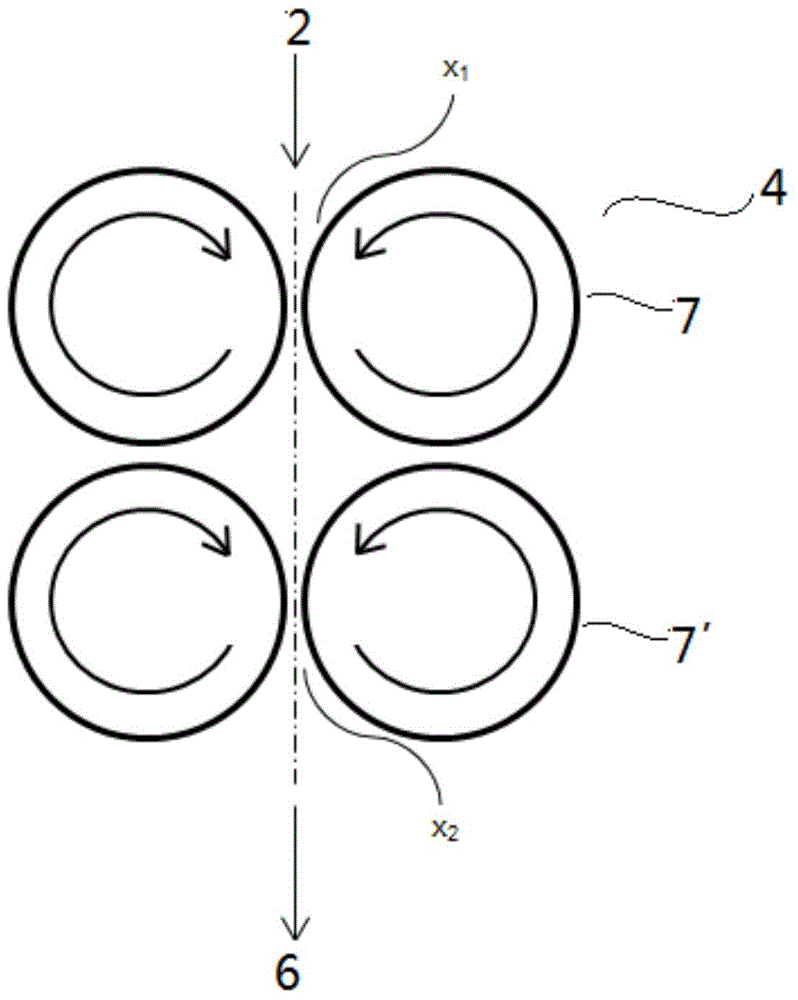
本发明涉及多晶硅制备技术领域,具体涉及一种高球形度籽晶的制备方法以及采用前述籽晶在流化床反应器中连续生产颗粒硅的方法。
背景技术:多晶硅是光伏发电行业和电子信息行业的关键原材料,是实现国家新能源战略的重要产品。自2005年以来,随着光伏行业的兴起与繁荣,中国多晶硅行业也经历了跨越式的发展。但近年来,面对欧洲主要光伏市场的不断萎缩、欧美相继发起“双反”调查的局面,如何实现光伏发电平价上网才是保障行业继续发展的关键举措,这其中基础原料多晶硅的成本下降至关重要。目前,制备多晶硅的方法有改良西门子法、冶金法、流化床法等。流化床法是美国联合碳化学公司早年研发的多晶硅制备工艺技术。该方法是以四氯化硅(SiCl4)、H2、HCl和工业硅为原料,在高温高压流化床内(沸腾床)生成三氯氢硅(SiHCl3或TCS),将SiHCl3再进一步歧化加氢反应生成二氯二氢硅(SiH2Cl2),继而歧化生成硅烷,硅烷或氯硅烷通入加有颗粒硅籽晶(也叫做“硅籽晶”)、500℃~1200℃的反应温度的流化床反应器内进行连续热分解反应,生成粒状多晶硅产品。按照通入流化床反应器内的含硅气体的种类,通常分为硅烷流化床和氯硅烷流化床(例如三氯氢硅流化床)。由于在流化床反应器内参与反应的颗粒硅表面积大,故该方法生产效率高、电耗低、成本低。流化床法的另一优点是:在下游的晶体生长过程中,颗粒硅可以直接装入晶体生长的坩埚中,但传统的改良西门子法生产的棒状多晶硅产品在装入坩埚之前需要进行破碎和分选处理,另外还需要例如用高纯度无机酸刻蚀、用超纯水清洗、干燥以及在干净的环境下处理等一系列的工艺过程。因此,与改良西门子法相比,流化床法生产过程能耗极低、沉积效率高、能够连续运行,同时颗粒硅产品利于下游使用,能够降低硅片制造成本,从而大幅降低现在的光伏电池生产成本。对于流化床而言,维持流化床床层内颗粒的稳态和高球形度对于确保平稳、连续的FBR操作和流态化气体固定的进气速度至关重要。与使用低球形度的颗粒相比,高球形度的流态化颗粒有利于增加流化床的最小流态化速度,同时在需要采用固定流态化气体进气速度和固定Ug/Umf情况下,对于减小反应器直径具有显著效果。其中,Ug是流态化气体的超临界速度,Umf是最小流态化速度。因此,制备出高球形度的籽晶对流化床的性能与长周期稳定运行十分关键。颗粒硅籽晶通常采用筛分、研磨、破碎等方法制备而来。例如通过将流化床制备的颗粒硅按照颗粒尺寸筛选,合格的颗粒硅作为产品包装,不合格的颗粒硅作为籽晶循环进入流化床反应器。利用筛分的方法制备籽晶一般先筛选大尺寸颗粒,再筛选小尺寸颗粒,制备工艺原料利用率低,原料处理量以及籽晶的产量有限。而利用常规的研磨方法则容易产生粉尘,为籽晶的分离和后续使用造成不便。还可参考破碎硅棒的方法制备籽晶,但只能制备出低球形度的籽晶,即制备的籽晶大部分为不规则形状。这种籽晶对于流化床非常不利,因为其不规则的流态化特性和减小的最小流态化速度以及段塞流速度。这将导致流化床层的喷动颗粒更多,也会增加床层孔隙率。流态化的不稳定和增加的沸腾相将导致含硅原料气体(例如SiHCl3、SiH2Cl2、SiHBr3、SiH2Br2或SiH4)发生自由空间或均相成核机制的气相分解,促使副产的亚微米级硅微粉形成。这些硅微粉如果不被合理地过滤除去,将堵塞下游设备和管道。同时,这些硅微粉由于具有较大的比表面积,容易发生表面污染,在后续的生长过程中容易被长大的硅颗粒吸附包藏,造成颗粒硅产品的纯度降低。此外,在连续操作过程中,与使用多数为球形的颗粒相比,非球形颗粒越多将导致最小流态化速度越低。对于非球形颗粒形成的致密床层,需要提高进气速度来初始流态化。同时,整个床层遭受不规则的高压降直到不规则形貌的颗粒变成“解锁”状态,实现完全流态化。与较多球形颗粒构成的床层相较,一旦达到流态化状态,具有较多非球形颗粒构成床层的孔隙率明显偏大。如前所述,这将导致形成不希望看到的硅微粉。通常,不规则的颗粒因为具有尖锐的边缘,更容易通过磨蚀或摩擦机制形成不想要的粉尘。因此,为避免前述负面因素,仍旧需要一种能够制备出高球形度籽晶的方法,工艺简单,能满足工业化大批量生产,又不产生粉尘,得到的籽晶具有较窄的粒度分布范围。
技术实现要素:本发明的目的是提供一种制备高球形度籽晶的方法,包括将流化床法制备得到的颗粒硅产品作为原料,通过辊式装置对其进行辊式破碎的步骤,根据本发明的制备方法,所制备的籽晶产品球形度高、粒度分布窄。本发明的另一目的是提供一种利用前述制备的高球形度籽晶循环进入流化床反应器制备颗粒硅的方法。为了实现上述目的和技术效果,本发明采用如下的技术方案:一种高球形度籽晶的制备方法,包括将具有一定粒度分布范围的颗粒硅产品作为原料,通过辊式装置对其进行辊式破碎的步骤,其特征在于所述辊式装置包括至少一组对辊,通过调节对辊的辊轮之间的空隙,使得尺寸大于所述辊轮空隙的颗粒硅被破碎,尺寸小于所述辊轮空隙的颗粒硅直接通过空隙,从而制备出高球形度的籽晶。所述颗粒硅产品可以是流化床法制备的颗粒硅产品,无需进行任何筛分等预处理即可作为制备籽晶的原料进料,本领域技术人员可以理解的是,从流化床中采出的颗粒硅具有一定粒度分布范围。当然本发明制备籽晶的原料也可以是其他方法制备的,优选流化床法制备的。在一个优选的实施方案中,所述辊轮空隙尺寸x与原料颗粒硅的中位粒径d50以及目标籽晶的中位粒径D50满足以下关系:100μm<D50<d50<x<2400μm,其中颗粒硅尺寸分布dp的范围为100μm~2400μm。在一个优选的实施方案中,所述辊式装置包括两组对辊,所述两组对辊上下放置,作为原料的颗粒硅产品依次通过上下两组对辊。更为优选地,所述上下两组对辊辊轮的空隙尺寸x1、x2满足关系式x1≥x2,其中x1为位于上方对辊的两个辊轮间的空隙尺寸,x2为位于下方对辊的两个辊轮间的空隙尺寸。本发明的另一方面,一种流化床颗粒硅的制备方法,包括以下步骤:1)含硅原料气体和流态化气体在加有籽晶的流化床反应器内,于500℃~1200℃的反应温度下进行连续的热分解反应,并在籽晶表面沉积硅制备颗粒硅产品;2)所述制备的颗粒硅产品采出后一部分包装作为最终产品;3)所述采出的颗粒硅产品采出后一部分经权利要求1-5任一项所述的高球形度籽晶的制备方法制备得到高球形度的颗粒硅籽晶,并循环进入流化床反应器内部,维持流化床床层籽晶数量稳定。其中,所述含硅原料气体选自SiHaXb,其中,X=F、Cl、Br、I,a、b各自独立选自a=0~4、b=0~4,且a+b=4。在一个优选的实施方案中,所述含硅原料气体为硅烷。在另一个优选的实施方案中,所述含硅原料气体为氯硅烷。优选地,所述含硅原料气体为三氯氢硅。根据本发明的高球形度籽晶的制备方法,以具有一定粒度分布的颗粒硅产品作为原料,通过辊式装置进行辊磨、破碎,通过调节所述辊式装置对辊的辊轮之间的空隙尺寸满足100μm<D50<d50<x<2400μm,使得尺寸大于所述辊轮空隙的颗粒硅被破碎,而绝大部分尺寸小于所述辊轮空隙的颗粒硅直接通过并保持原有的球形形貌,从而使得大多数籽晶均为球形,得到高球形度的籽晶。本发明还可以根据作为原料的颗粒硅产品的粒度分布来调节辊式装置对辊辊轮的孔隙尺寸,以得到一定尺寸和较窄粒度分布范围的高球形度的籽晶。根据本发明的高球形度籽晶的制备方法,通过辊式装置一次处理即可得到高球形度的籽晶,与筛分的方法相比,工艺较为简单,无需分级筛选,节约时间,一次性辊磨即可将大颗粒破碎,而小颗粒直接筛分通过,该方法处理量大,原料全部转化为籽晶,原料利用率高。与研磨的方法相比,不产生细硅粉,制备的籽晶球形度高、粒度分布窄。根据本发明的高球形度籽晶和流化床颗粒硅的制备方法,制备的高球形度、粒度分布窄的籽晶,循环进入流化床反应器中,这种籽晶有利于维持流化床平稳操作,延长了流化床的运行周期。同时,床层的孔隙率较小,避免了自由空间或均相成核形成硅微粉带来的堵塞下游管道或污染产品等问题。附图说明图1是本发明的高球形度籽晶的制备装置示意图。图2是本发明的高球形度籽晶的另一制备装置示意图。图3是本发明的流化床颗粒硅及籽晶的制备方法流程示意图。图4是球形度与最小流态化速度的关系曲线。图5是实施例1的原料颗粒硅的粒度分布示意图。图6是实施例1辊磨前后原料颗粒硅与籽晶的粒度分布柱形示意图。图7是实施例1辊磨前后原料颗粒硅与籽晶的粒度分布曲线示意图。图8是实施例1原料颗粒硅的实物图。图9是实施例1原料颗粒硅经辊式破碎后的籽晶实物图。图10是对比例1辊磨前后原料颗粒硅与籽晶的粒度分布柱形示意图。图11是对比例1辊磨前后原料颗粒硅与籽晶的粒度分布曲线示意图。图12是对比例1原料颗粒硅的实物图。图13是对比例1原料颗粒硅经辊式破碎后的籽晶实物图。图14是实施例1与对比例1制备籽晶的粒度分布示意图。其中,1为流化床反应器、2颗粒硅产品、3包装、4辊式装置、5颗粒硅成品、6籽晶、7、7’对辊。具体实施方式:下面结合附图对本发明的具体实施方式进行详细说明,但是,必需说明的是,本发明的保护范围并不受这些具体实施方式的限制,具体实施方式中所涉及的具体装置装配及参数设置是为说明本发明而列举在本具体实施方式中,并不是对本发明的任何限制。本发明所保护的范围,由权利要求书确定。一种高球形度籽晶的制备方法,将具有一定粒度分布范围的颗粒硅产品2作为原料,通过辊式装置4进行辊磨破碎,所述辊式装置包括至少一组对辊,如图1所示,所述辊式装置包括一组对辊7,每组对辊7包括两个相向转动的辊轮。通过调节所述辊轮之间的空隙尺寸x,使得尺寸大于所述辊轮空隙x的颗粒硅被磨碎,而大部分尺寸小于所述辊轮空隙的颗粒硅则直接通过,由于制备的籽晶是直接通过而未被破碎的颗粒与破碎后颗粒的混合物,其中,未被破碎的颗粒占大部分,从而制备出的籽晶具有较高的球形度。通常,流化床中采出的颗粒硅产品的颗粒尺寸范围dp从100μm~2400μm不等,但不限于此,具有较宽的粒度分布范围。而通过调节所述辊轮空隙x,就可以实现籽晶具有比较窄的粒度分布范围。在本发明中,球形度即所制备籽晶中形貌为球形的籽晶数量占总籽晶数量的比例,球形籽晶数量占比越多,球形度越大。所述辊式装置可参考现有技术,例如瓦克公司专利US20090114748A1中公开的辊式装置,由相向转动的至少一组对辊构成,所述对辊表面具有硬质金属涂层,例如碳化钨等,但不限于此。不同的是该专利的辊式装置用于将硅棒全部破碎,得到大小差不多的小硅块。但本发明用于制备高球形度的籽晶,需要根据原料的粒度分布范围调节对辊辊轮的空隙尺寸,所述原料颗粒硅通过辊式装置,被辊式破碎。在具体的实施方式中,所述辊式装置的原料颗粒硅粒度分布范围为100μm~2400μm,可根据颗粒尺寸分布调节对辊的两个辊轮间的空隙尺寸。当大颗粒包括但不限于大于1500μm时,可通过调节辊轮空隙x为1500μm或更小,此时100μm~1500μm或更小的颗粒直接通过空隙,不被破碎,保持原有的球形度。当大颗粒包括但不限于大于1250μm时,可通过调节辊轮空隙x为1250μm或更小,此时100μm~1250μm或更小的颗粒不被破碎,保持原有的球形度。当大颗粒包括但不限于大于1000μm时,可通过调节辊轮空隙x为1000μm或更小,此时100μm~1000μm或更小的颗粒不被破碎,保持原有的球形度。当大颗粒包括但不限于大于750μm时,可通过调节辊轮空隙x为750μm或更小,此时100μm~750μm或更小的颗粒不被破碎,保持原有的球形度。当大颗粒包括但不限于大于1750μm时,可通过调节辊轮空隙x为1750μm或更小,此时100μm~1750μm或更小的颗粒不被破碎,保持原有的球形度。当大颗粒包括但不限于大于2000μm时,可通过调节辊轮空隙x为2000μm或更小,此时100μm~2000μm或更小的颗粒不被破碎,保持原有的球形度。当大颗粒包括但不限于大于2250μm时,可通过调节辊轮空隙x为2250μm或更小,此时100μm~2250μm或更小的颗粒不被破碎,保持原有的球形度。当大颗粒包括但不限于大于2400μm时,可通过调节辊轮空隙x为2400μm或更小,此时100μm~2400μm或更小的颗粒不被破碎,保持原有的球形度。为进一步提高所制籽晶的球形度,还可以根据原料颗粒硅和目标籽晶的中位粒径D50来调节对辊空隙尺寸x。通常,D50是指一个样品的累计粒度分布百分数达到50%时所对应的粒径。它的物理意义是粒径大于它的颗粒占50%,小于它的颗粒也占50%,因此一般D50也叫中位径或中值粒径。而在本发明中,为便于区分,作为原料的具有一定颗粒尺寸分布的颗粒硅的中位粒径记为d50,而通过辊磨破碎制备的目标籽晶的中位粒径记为D50。当制备籽晶的原料确定时,该颗粒硅原料的粒度分布范围及中位粒径即可通过检测计算确定。在本发明中,优选地,所述辊轮空隙x与作为原料的颗粒硅的颗粒尺寸分布dp、中位粒径d50以及制备的目标籽晶中位粒径D50满足以下关系:100μm<D50<d50<x<2400μm,其中颗粒尺寸分布dp的范围为100μm~2400μm,但不限于此,例如还可以为50μm~3000μm。本领域技术人员熟知的是,可通过在线的粒度分析仪分析计算出流化床反应器中采出的颗粒硅产品的粒度分布范围,并计算出中位粒径,如此可以有目的地调节对辊空隙尺寸x。在具体的实施方式中,粒度分布范围为100μm~2400μm的原料颗粒硅的中位粒径为1500μm时,调节辊轮空隙x大于1500μm,则尺寸大于1500μm的颗粒全被破碎,且被破碎的硅颗粒占比小于50%。此时大部分硅颗粒直接通过辊式装置未被破碎且保持原有的球形度。此时制备的籽晶为未被破碎的颗粒与破碎颗粒的混合物,但未被破碎的颗粒占大多数,因此所制备的籽晶具有较高的球形度。以此类推,当所述颗粒硅的中位粒径还可以为1250μm、750μm、1750μm、2000μm、2250μm等,但不限于此,调节辊轮空隙x大于相应的中位粒径,则大部分颗粒硅直接通过辊式装置而未被破碎,从而提高所制籽晶的球形度。在一个优选的实施方案中,如图2所示,所述辊式装置包括两组对辊7和7’,所述两组对辊上下放置,作为原料的颗粒硅依次通过上下两组对辊。更为优选地,所述上下两组对辊的辊轮空隙x1、x2满足关系式x1≥x2,其中x1为位于上方的对辊两个辊轮空隙,x2为位于下方的对辊的两个辊轮空隙。位于下方的对辊可用于精细调节目标籽晶的粒度范围和球形度。例如可以根据需要制备的籽晶目标直径进一步细调所述对辊尺寸x2,优选为D50<x2<x1,但不限于此。例如当作为制备籽晶的原料硅颗粒的中位粒径d50为1500μm,所需制备籽晶的目标中位粒径D50为800μm时,按照上述描述首先x1需调节至1500μm<x1<2400μm,进一步细调x2,则x2需调节至800μm<x2<1500μm,则可以通过下方的对辊辊轮空隙精细化调节,得到更窄粒度分布范围且具有高球形度的籽晶颗粒。可以理解的是,在籽晶制备过程中,所述辊式装置还可以包括更多的对辊,比如三组、四组、五组或六组,但不限于此。这可根据目标籽晶的要求进行设置和调节相应的辊轮空隙。还可以几组辊式装置串联或并列使用,提高籽晶的制备效率。另一方面,如图3所示,采用辊磨的方法制备用于流化床法的颗粒硅籽晶,在流化床反应器1中通过含硅原料气体分解、并在硅籽晶上不断沉积硅得到高纯颗粒硅产品2。一部分颗粒硅产品2通过包装3得到最终颗粒硅成品5。为了制备籽晶,流化床反应器得到的颗粒硅产品2被具有一组圆柱形辊的辊式装置4破碎,得到籽晶6,减小了颗粒尺寸分布(PSD)。籽晶6颗粒作为循环物料进入硅沉积流化床1(FBR),其通过连续或半连续操作采出颗粒硅产品。这一籽晶循环过程对于维持床层内部颗粒数量和PSD恒定非常重要,进而可延长连续或半连续操作的运行周期。因为当反应器内的颗粒硅表面发生硅沉积不断长大时,颗粒的直径和球形度不断增加。而循环率(循环进入流化床的籽晶占被辊磨成籽晶的产品百分比)、PSD和循环籽晶的球形度,初始床层的PSD和球形度和沉积速率是决定稳态PSD和流化床床层颗粒球形度的主要因素。因此,制备得到窄粒度分布且高球形度的籽晶并以平稳的数量循环进入流化床对于维持流化床性能和平稳操作极为重要。相比较而言,现有的分选、研磨等方法均无法满足该要求。只有通过本发明辊磨的方法,控制上述循环率、制备得到窄粒度分布、高球形度的籽晶,即可实现上述技术效果,从而实现流化床反应器的长周期稳定运行。此外,籽晶的球形度越高,则流化床反应器的最小流态化速度越大。图4是籽晶粒度分布d50为850μm时颗粒球形度与最小流态化速度的关系曲线。其中,最小流态化速度Umf通过下面的方程计算而来:从图4可以看出,随着籽晶颗粒球形度的增大,其作为流化床床层的最小流态化速度Umf也逐渐增大。在需要采用固定流态化气体进气速度和固定Ug/Umf情况下,对于减小流化床反应器直径具有显著效果。本发明中,所述含硅原料气体选自SiHaXb,其中,X=F、Cl、Br、I,a、b各自独立选自a=0~4、b=0~4,且a+b=4。优选为,所述含硅原料气体为硅烷或氯硅烷,更优选为三氯氢硅,但不限于此。例如可以为硅烷(SiH4)、二氯硅烷(SiH2Cl2)、三氯硅烷(SiHCl3)、四氯化硅(SiCl4)、二溴硅烷(SiH2Br2)、三溴硅烷(SiHBr3)、四溴化硅(SiBr4)、二碘硅烷(SiH2I2)、三碘硅烷(SiHI3)、四碘化硅(SiI4)及其混合物。本领域技术人员可以理解的是,所述含硅原料气体还可以是乙硅烷(Si2H6)、高级硅烷(SinH2n+2)等等。所述含硅原料气体也可以与一种或多种流态化气体混合,所述流态化气体包括氢气或选自如下气体中的一种或多种惰性气体,如氮(N2)、氦(He)、氩(Ar)、以及氖(Ne)等,可用于使床层流态化。在本发明中没有特别述及之处均可参考现有技术,这也是本领域技术人员所熟知的。例如籽晶循环进入流化床的操作、流化床采出颗粒硅产品、产品分选包装等,这都不是本发明的创新所在。此外,所述流化床反应器的流态化速度一般略大于最小流态化速度Umf,优选流化床的流态化速为1.1Umf~3.0Umf,优选1.2Umf~2.0Umf。所述颗粒硅籽晶的粒径通常在50~1000μm,优选100~500μm;而生产出的粒状多晶硅产品的尺寸通常100~3000μm,优选800~2000μm。下面通过几个具体的实施例进一步说明本发明的技术效果,但对本发明并不构成任何限制,仅仅用于解释本发明。实施例1采用流化床反应器制备的颗粒硅产品通过辊式装置制备籽晶,其参数设置如下表1所示。通过采用上下两组对辊,其中上方对辊的辊轮空隙为2000μm,下方对辊的辊轮空隙为1500μm,将粒度分布范围为100–2400μm、中位粒径为1135μm的颗粒硅产品通过辊磨破碎制备出中位粒径为857μm的籽晶。表1实施例1实验数据图5为该实施例原料颗粒硅的粒度分布示意图。从图中可以看出,78%的颗粒硅直接通过了辊式装置辊轮的空隙而未被破碎,只有22%的硅颗粒被辊磨破碎。图6示出了辊磨前后硅颗粒及籽晶的粒度分布。从中可以看出,大尺寸的硅颗粒被破碎变成小尺寸的颗粒硅,且籽晶的粒度分布范围变窄。从图7计算的百分比曲线中更能直观的反应看出颗粒尺寸变小,同一尺寸颗粒比例增加。图8和图9分别给出了辊磨前后放大13.4倍的颗粒硅及籽晶的实物照片。从图8中可以看出辊磨之前的原料球形度较好,但颗粒硅大小不一,粒度分布较宽。但经过辊磨破碎后,得到的籽晶包括大部分未被破碎的颗粒硅和小部分经破碎的颗粒硅,总体球形度较高,颗粒尺寸比较均一,如图9所示。对比例1为比较研究,通过交替研磨的方法将硅颗粒全部破碎得到与实施例1类似粒度分布范围的籽晶,如表2所示。表2对比例1实验数据图10示出了研磨前后颗粒硅及籽晶的粒度分布柱状图。可以看出,大颗粒全部被磨碎变成小颗粒。图11给出了相应的计算曲线,更加直观地看出2400μm以上的颗粒全部被磨碎至2000μm以下。图12和13给出了破碎前后颗粒硅及籽晶放大13.4倍的实物照片。原料颗粒硅球形度高、尺寸均一,通过研磨后颗粒硅全部被破碎,球形度较低。图14给出了实施例1和对比例1的比较图,从中可以看出两种方法制备的籽晶粒度分布类似,但两种方法制备的籽晶形貌差异极大,本发明的方法制备的籽晶球形度远远高于对比例1的方法。本发明进一步研究了所制备的籽晶在流化床反应器中的孔隙率。表3给出了流化床反应器制备的颗粒硅产品、实施例1制备的籽晶、对比例1制备的籽晶在致密床层和最小流态化速度两种状况下的流化床层孔隙率(即床层中颗粒硅之间的空隙体积占总体积的比例)。可以看出,实施例与对比例两种方法制备的籽晶形成床层的孔隙率均比流化床颗粒硅产品要高。在最小流态化速度情况下,对比例1的孔隙率比实施例1制备的籽晶要高19.4%,但实施例1制备的籽晶与颗粒硅产品相比差异较小,其孔隙率仅比颗粒硅产品作为籽晶时高10.4%。因此,与常规的研磨方法相比,本发明制备的籽晶孔隙率更低,更易于避免硅微粉的形成而造成的负面影响。表3几种不同籽晶形成床层孔隙率比较尽管上文对本发明的具体实施方式给予了详细描述和说明,但是应该指明的是,本领域技术人员可以依据本发明的构想对上述实施方式进行各种等效改变和修改,其所产生的功能作用仍未超出说明书所涵盖的精神时,均应在本发明的保护范围之内。