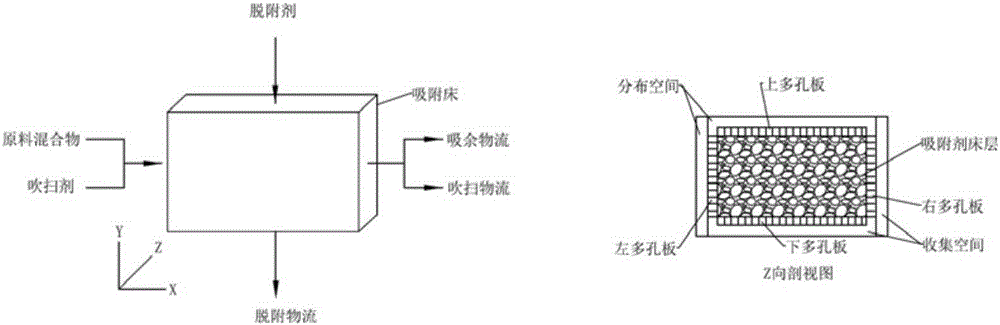
本发明涉及一种新的改进的选择性吸附分离方法,其中利用分子筛作为吸附剂,针对包含待分离的目标组分的原料混合物,在吸附剂床层未完全饱和的吸附步骤之后结合了利用吹扫剂的特定吹扫步骤,和其中还使用了具有特定结构设计的吸附剂床层。
背景技术:
:人类使用吸附剂的历史非常悠久,最常见的如用木炭来吸湿、消除异味。随着科技的进步,酸性白土、硅藻土和活性炭在脱色、脱臭、吸湿、干燥等场合的应用越来越广泛。天然沸石的发现以及后来分子筛的合成,进一步为吸附和催化领域揭开了新的篇章。由于不同吸附剂对不同物质的吸附性能不同,围绕吸附分离已经开展了很多研发工作,使得吸附分离技术迅速发展,并在石油、化工、制药、环保等领域得到了广泛应用。在吸附分离中,选择性吸附分离多用于沸点相近的同分异构体混合物,如从二甲苯混合物中吸附分离对二甲苯、从二氯苯混合物中吸附分离间二氯苯时用的都是选择性吸附分离技术。CN95112773.X中公开了一种从混合二甲苯和乙苯中分离间二甲苯与邻二甲苯的方法,其中混二甲苯和乙苯在吸附条件下以气相状态通过装有MFI型沸石分子筛吸附剂的吸附剂床层以选择性吸附乙苯和对二甲苯,吸余物为间二甲苯和邻二甲苯,之后吸余物经精馏获得间二甲苯和邻二甲苯。CN01812659.6中公开了一种从C8芳烃中变压吸附分离对二甲苯和乙苯的方法,其中采用MFI型对位选择的非酸性中孔分子筛,在高温高压下在等温气相分离C8芳烃中的二甲苯和乙苯。CN99113692.6中公开了一种气相选择吸附分离混合二氯苯的方法,其中混合二氯苯以气相状态通过沸石分子筛吸附剂,吸附剂选择吸附对二氯苯,吸余物为间二氯苯、邻二氯苯和微量对二氯苯,被吸附的对二氯苯在脱附条件下脱附,吸余物经常规精馏获得纯度大于99.7%的间二氯苯。CN1315217A中公开了一种用疏水硅沸石液相选择吸附分离混合二氯苯的方法,其中采用MFI型疏水硅沸石在液相条件下吸附分离至少两种二氯苯异构体混合物,吸附剂选择吸附对二氯苯和/或邻二氯苯,未被吸附的间二氯苯可从吸余物流中直接回收,对二氯苯和/或邻二氯苯可直接通过脱附分离。CN1749226A中公开了一种苯二取代物异构体在疏水硅沸石上复相吸附分离的方法,其中在床层吸附对位取代物达到饱和前或饱和后采用N2进行中吹,目的是吹脱床层死空间中的原料混合物,然后进行脱附,其中中吹得到的中间馏分和脱附得到的抽出物一起收集,与原料混合物相比,所述中间馏分+抽出物中对位异构体只是略有富集,还需要返回吸附过程再次进行吸附处理。另外,在工业水处理过程中,水中含有的微量有机物也可以采用特种分子筛吸附剂进行选择性吸附分离,由此可以脱除并富集所述有机物,所述特种分子筛吸附剂也可以在再生后重复使用。CN101219818A中公开了一种丙酮废水的处理与回收方法,其中利用沸石分子筛吸附分离和回收废水中的丙酮,其特征在于将含丙酮废水通过沸石分子筛吸附柱来吸附废水中的丙酮,然后被吸附的丙酮在高温气体脱附条件下脱附,同时吸附剂得到再生,脱附后的丙酮经冷凝回收。因此,在现有技术中,针对包含待分离的目标组分的原料混合物,选择性吸附分离主要包括吸附步骤和脱附步骤,其中在吸附步骤中原料混合物通过吸附获得主要含非目标组分的吸余物流,和在脱附步骤中基本饱和的吸附剂床层通过脱附获得主要含目标组分的脱附物流,另外,也可在吸附步骤和脱附步骤之间引入中吹操作以脱除床层中残余原料混合物,和然后使吹脱的原料混合物返回吸附步骤进一步进行吸附。技术实现要素:基于现有技术中的选择性吸附分离过程,本发明提出了一种新的改进的选择性吸附分离方法,其中利用分子筛作为吸附剂,针对包含待分离的目标组分的原料混合物,在吸附剂床层未完全饱和的吸附步骤之后结合了利用吹扫剂的特定吹扫步骤,和其中还使用了具有特定结构设计的吸附剂床层。具体地,本发明提供了一种利用分子筛作为吸附剂对原料混合物进行选择性吸附分离的方法,所述原料混合物包含待分离的目标组分,该方法包括以下步骤:吸附步骤,其中使原料混合物沿第一方向通过吸附剂床层,在吸附剂床层沿第一方向的出口处收集吸余物流,持续吸附过程,直到吸附剂床层上目标组分的吸附量按动态穿透吸附量计达到65-99.5%为止;吹扫步骤,其中使吹扫剂沿第二方向通过吸附剂床层,在吸附剂床层沿第二方向的出口处收集吹扫物流,持续吹扫过程,以清除吸附剂床层中的非目标组分,其中第二方向与第一方向相同;脱附步骤,其中使脱附剂沿第三方向通过吸附剂床层,在吸附剂床层沿第三方向的出口处收集脱附物流,持续脱附过程,直到脱附物流中目标组分的浓度不变或变化很小为止,其中第三方向与第一方向相同、相逆或相互垂直,优选为相逆或相互垂直,更优选为相互垂直;和任选的循环步骤,其中依次重复上述各操作步骤进行循环。按照本发明,其中在吸附步骤进行到一定程度即在吸附剂床层尚未饱和时,例如一般在吸附剂床层上目标组分吸附量按动态穿透吸附量计至多99.5%、优选至多98%和更优选至多96%时停止吸附步骤和开始吹扫步骤,在吹扫步骤中吹扫剂与原料混合物进料方向相同,使得吹扫路径与吸附路径相同,由此驱扫吸附剂床层内的残余原料混合物重新经过吸附路径,使得其中的目标组分可以被不饱和吸附剂床层上的剩余吸附位点进一步吸附,即所述残余原料混合物在被吹扫迁移的过程中进行补充吸附,这样在吹扫结束后吸附剂床层几乎不含或只含有少量非目标组分,并且得到的吹扫物流本身或与吹扫剂分离如通过相分离如水油相分离或气液相分离后的吹扫物流的组成也非常接近吸余物流,它们甚至可以与吸余物流合并收集和然后进一步处理,而在对吹扫后的吸附剂床层进行脱附后,所获得的脱附物流也几乎不含或只含有少量非目标组分。因此,按照本发明,通过组合应用吸附步骤中的不饱和吸附过程与吹扫步骤中吹扫路径与吸附路径相同的同向吹扫过程(即吹扫和补充吸附),可以尽最大可能保证吸附剂床层中主要存在被吸附的目标组分,使得后续脱附步骤中获得的脱附物流的目标组分纯度更高,由此提高了吸附和脱附的效率,从而可以实现目标组分与非目标组分的高效分离,使整个吸附分离过程更加有效,这也是本发明技术方案的优点所在。按照本发明,在吸附步骤中,吸附剂床层上目标组分的吸附量按照动态穿透吸附量来计量。在本领域中,动态穿透吸附量是吸附剂本身特有的性能参数,通常是在一定温度和压力下吸附剂达到动态穿透点时所能吸附的目标组分量,以单位重量或单位体积吸附剂的平均值计。在本领域中,在测量吸附剂的动态穿透吸附量时,一般将一定量的吸附剂填充于吸附剂床层中,使具有确定目标组分浓度的液体或气体在所述温度和压力下以确定流量通过吸附剂床层,测量出口液体或气体中目标组分浓度,当出口液体或气体中目标组分浓度达到相应的临界值时即认为吸附剂床层被目标组分穿透,此时单位重量或体积吸附剂的吸附容量就对应所述吸附剂针对目标组分的动态穿透吸附量。按照本发明,其中作为吸附剂的分子筛可以为本领域中通常使用的各种合适类型的分子筛,通常可以选自MFI型沸石如ZSM-5、FER型沸石如镁碱沸石、BEA型沸石如β沸石和高硅FAU型沸石如Y沸石和超稳Y沸石,优选为这些沸石的钠型沸石或无粘结剂钠型沸石、无粘结剂疏水型沸石或亲水型沸石,更优选为MFI型无粘结剂疏水硅沸石或无粘结剂Silicalite-1沸石,该分子筛吸附剂通常可以为任何合适的尺寸和形状,例如,其平均粒度一般为1-5mm,优选为2-3mm,和形状一般为球形或圆柱体等。在本发明的选择性吸附分离方法中,吹扫剂和脱附剂的选择可以按本领域中的通常标准进行,一般来说,原料混合物中含有的目标组分可能被吸附剂强吸附,而吹扫剂和脱附剂也可能被吸附剂吸附,但吸附程度相对于目标组分而言要弱一些,即不会与目标组分竞争占据床层吸附位点,并且它们在体系中通常是惰性的,即不能与被吹扫或被脱附的物质等相互作用,另外,还要求它们要尽可能容易地与被吹扫或被脱附的物质相互分离,如可以很容易地通过相分离如气液相分离或水油相分离或者精馏等来实现彼此分离,这些对于本领域技术人员来说都是熟知的,即本领域技术人员可以基于本领域的这些通常标准来相应地选择和使用吹扫剂和脱附剂。按照本发明,其中优选进一步按照分离系数比来选择吹扫剂和脱附剂,其中使脱附剂的分离系数比β目标组分/脱附剂>1,优选为1-10,和使吹扫剂的分离系数比β目标组分/吹扫剂≥β目标组分/脱附剂,优选为2-100,更优选为3-50。具体地,按照本发明,其中脱附剂的分离系数比为目标组分的分离系数与脱附剂的分离系数之比,吹扫剂的分离系数比为目标组分的分离系数与吹扫剂的分离系数之比,分离系数则为各物质在分子筛吸附相中的量与其在非分子筛吸附相中的量之比,其中,脱附剂和吹扫剂的分离系数比分别定义如下:和按照本发明,由以上吹扫剂和脱附剂的进一步选择可知,所述吹扫剂和脱附剂可以相同或不同,且吹扫剂的分离系数比大于或等于脱附剂的分离系数比,也就是说,吹扫剂的分离系数要小于或等于脱附剂的分离系数,即吹扫剂的被吸附强度一般不能强于脱附剂,而脱附剂的分离系数比β目标组分/脱附剂>1和优选为1-10,即要求脱附剂的分离系数在一定程度上低于目标组分,从而可以在一定程度上被吸附剂床层吸附。这样,按照本发明,吹扫剂主要起到吹扫和清除床层空间内残余原料混合物的作用,而不会与目标组分竞争占据吸附剂床层上的吸附位点,并且,由于在本发明中在吸附剂床层不饱和时开始吹扫步骤且吹扫路径与吸附路径相同,可以使床层内被吹扫剂吹扫迁移的残余原料混合物中的目标组分被床层内剩余的吸附位点进一步吸附,使得离开床层的吹扫物流中目标组分的含量相当低,即最后吹扫和清除的主要是非目标组分,从而所得吹扫物流可能不需要返回吸附步骤再次进行吸附分离,甚至可以在任选与吹扫剂分离如通过相分离如水油相分离或气液相分离之后与吸余物流合并收集和然后进一步处理,而之后脱附剂则主要从吸附剂床层上排挤掉目标组分,但又不会在快速通过吸附剂床层的过程中被过于牢固地吸附到吸附剂床层上,进而很好地实现目标组分的脱附,使吸附剂床层得到“再生”,由此可以进入下一个吸附、吹扫和脱附循环。按照本发明,其中使原料混合物沿第一方向通过吸附剂床层,使吹扫剂沿第二方向通过吸附剂床层,和使脱附剂沿第三方向通过吸附剂床层,其中第二方向与第一方向相同,第三方向与第一方向相同、相逆或相互垂直,优选为相逆或相互垂直,更优选为相互垂直,和其中吸附剂床层沿第一方向的长径比大于或等于吸附剂床层沿第二方向和第三方向的长径比。因此,按照本发明,原料混合物通常沿长径比较高的路线通过吸附剂床层,从而可以在较长行程内相对充分地进行吸附过程,吹扫剂通常与原料混合物在吸附剂床层内的流向相同,即吹扫路径通常与吸附路径相同,从而在吹扫过程中使被吹扫剂驱扫迁移的残余原料混合物重新经过吸附路径,使其中的目标组分进一步被吸附,由此使吹扫物流中目标组分含量很低,最后,脱附剂与原料混合物在吸附剂床层内的流向相同、相逆或相互垂直,优选为相逆或相互垂直,更优选为相互垂直,从而可以有效地实现目标组分的脱附。按照本发明,吸附剂床层可以为圆柱状吸附剂床层,其中圆柱体内部填充有吸附剂,圆柱体顶部和下部分别设有分布和收集空间以及分布和收集多孔板,此时第三方向优选与第一和第二方向相逆,因此可以更有效地进行脱附。按照本发明,吸附剂床层也可以为箱体状吸附剂床层,其中箱体内部填充有吸附剂,箱体在水平横向和垂直纵向的两端均分别设有分布和收集空间以及分布和收集多孔板,此时第三方向优选与第一和第二方向相互垂直,因此脱附距离可能较短,脱附时间也相应较短,从而进一步提高脱附效率。按照本发明,其中吸附步骤和吹扫步骤可以分别在常压或加压下在气相或液相状态下进行,而脱附步骤可以在常压、加压或真空下在气相或液相状态下进行,即吸附和吹扫通常在常压或加压下以气相或液相进行,而脱附则可以在常压、加压或真空下以气相或液相进行,这一点与现有技术中基本一致。按照本发明,其中原料混合物可以为苯系二取代物或苯系三取代物的同分异构体混合物,其中苯系二取代物可以包括二甲苯、二乙苯、甲基乙基苯、二氯苯、氯甲苯、氯乙苯等,此时对位取代物通常为目标组分,和其中苯系三取代物可以包括二氯甲苯、二氯乙苯等,此时1,2,5-三取代物或1,2,4-三取代物通常为目标组分,而吹扫剂则可以选自水蒸汽、CO2、C1-C4烃、空气、氮气和氩气。按照本发明,当苯系二取代物或苯系三取代物的同分异构体混合物作为原料混合物时,其中原料混合物中目标组分的含量可能相对较高,但一般不高于80wt%,优选不高于70wt%,更优选不高于60wt%,和不低于1wt%,优选不低于3wt%,其中在目标组分的吸附量按动态穿透吸附量计达到68-96%、优选70-95%时停止吸附步骤,其中与吸附步骤的持续时间τ相比,吹扫步骤的持续时间一般为0.01-5τ,优选为0.05-1τ,和当脱附物流中目标组分的含量低于0.5wt%、优选低于0.3wt%时停止脱附步骤。进一步,按照本发明,当苯系二取代物或苯系三取代物的同分异构体混合物作为原料混合物时,其中原料混合物、吹扫剂和脱附剂可以按照本领域常规的重时空速进料,例如,原料混合物和脱附剂的重时空速一般分别为0.1-5h-1、优选0.3-2.5h-1、更优选0.5-1.5h-1,和吹扫剂的重时空速一般为0.1-10h-1、优选0.2-5h-1、更优选0.3-3h-1。按照本发明,当苯系二取代物如二甲苯混合物为原料混合物时,此时吹扫剂优选为水蒸汽或C1-C4烃,脱附剂优选为甲苯,其中作为原料混合物的二甲苯混合物、作为吹扫剂的水蒸汽或C1-C4烃和作为脱附剂的甲苯通常在常压下预热至140-170℃后进料至吸附剂床层以在气相状态下进行吸附、吹扫和脱附。按照本发明,当苯系二取代物如二氯苯混合物为原料混合物时,此时吹扫剂优选为空气、氮气或C1-C4烃,脱附剂优选为氯苯,其中作为原料混合物的二氯苯混合物、作为吹扫剂的空气、氮气或C1-C4烃和作为脱附剂的氯苯通常在常压下预热至180-200℃后进料至吸附剂床层以在气相状态下进行吸附、吹扫和脱附。按照本发明,当苯系三取代物如二氯甲苯混合物作为原料混合物时,此时可以首先由五种二氯甲苯异构体的二氯甲苯混合物精馏获得可用作选择性吸附分离的原料混合物的主要含三种二氯甲苯异构体的二氯甲苯混合物,例如所述原料混合物可以为主要含1,2,4-二氯甲苯、1,2,5-二氯甲苯、1,2,6-二氯甲苯的二氯甲苯三异构体混合物,其中1,2,5-二氯甲苯为目标组分,此时吹扫剂优选为氮气,脱附剂优选为氯苯,其中作为原料混合物的二氯甲苯混合物和作为吹扫剂的氮气通常在0.1-0.5MPa的表压下预热至200-260℃后进料至吸附剂床层以在气相状态下进行吸附和吹扫,和其中作为脱附剂的氯苯通常在常压下预热至200-260℃后进料至吸附剂床层以在气相状态下进行脱附,在此所应用的说法“主要含”指的是所述主要包含的各组分的总含量至少为50wt%,优选为至少70wt%,更优选为至少90wt%,而其它非主要包含的各组分的总含量则很少,例如不超过50wt%,优选不超过30wt%,和更优选不超过10wt%。按照本发明,其中原料混合物也可以为含少量有机物的废水或者含少量水的有机物液体,其中含少量有机物的废水中有机物为目标组分,含少量水的有机物液体中水为目标组分,所述有机物可以选自己烷、庚烷、苯、甲苯、乙苯、苯乙烯、对二甲苯、丙酮、乙酸、乙醇、乙酸乙酯、1-丙醇、1,3-丙二醇、正丁醇、甲胺、乙胺、丙胺、正丁胺、甲酰胺、乙酰胺、N,N-二甲基甲酰胺、N,N-二甲基乙酰胺、氯仿、环己酮肟以及小分子药物中间体如医药中间体和农药中间体等,其中吹扫剂和脱附剂可以各自独立地选自水蒸汽、CO2、C1-C4烃、空气、氮气和氩气。按照本发明,当含少量有机物的废水或者含少量水的有机物液体作为原料混合物时,其中原料混合物中目标组分的含量可能相对较低,例如,一般不高于20wt%,优选不高于15wt%,更优选不高于10wt%,和不低于0.01wt%,优选不低于0.03wt%,其中在目标组分的吸附量按动态穿透吸附量计达到90-99.5%、优选95-98%时停止吸附步骤,其中与吸附步骤的持续时间τ相比,吹扫步骤的持续时间一般为0.001-0.5τ,优选为0.002-0.2τ,和脱附步骤的持续时间一般为0.01-0.5τ,优选为0.02-0.2τ。按照本发明,当含少量有机物的废水或者含少量水的有机物液体作为原料混合物时,其中原料混合物、吹扫剂和脱附剂可以按照本领域常规的重时空速进料,例如,原料混合物和脱附剂的重时空速一般分别为0.1-10h-1、优选0.2-5h-1、更优选0.25-2.5h-1,和吹扫剂的重时空速一般为0.1-50h-1、优选0.2-30h-1、更优选0.25-10h-1。按照本发明,当含少量有机物的废水如含丙酮废水为原料混合物时,此时吹扫剂和脱附剂可以各自独立地选自水蒸汽、CO2、C1-C4烃、空气、氮气和氩气,其中吸附步骤通常在常压下进行,吹扫步骤和脱附步骤通常在0.1-1.0MPa表压下进行。按照本发明,当含少量有机物的废水如含二甲基乙酰胺废水为原料混合物时,此时吹扫剂和脱附剂可以各自独立地选自水蒸汽、CO2、C1-C4烃、空气、氮气和氩气,其中吸附步骤和脱附步骤通常在常压下进行,吹扫步骤通常在0.02-0.15MPa表压下进行。附图说明下面结合附图来更详细地描述本发明的方法,其中:图1是本发明一种实施方式的示意图;和图2是本发明又一种实施方式的示意图。图1给出了本发明方法的一种实施方式,其中吸附剂床层为圆柱状吸附剂床层,其中在圆柱体内部填充有吸附剂,在圆柱体的顶部和下部分别设有分布空间和收集空间以及分布和收集多孔板;原料混合物从吸附剂床层下部通入,吸余物流在吸附剂床层上部采出;吹扫剂从吸附剂床层下部通入,吹扫物流在吸附剂床层上部采出;脱附剂从吸附剂床层上部通入,脱附物流在吸附剂床层下部采出;其中吹扫剂与原料混合物在吸附剂床层内的流向相同,和脱附剂与原料混合物在吸附剂床层内的流向相逆。图2给出了本发明方法的又一种实施方式,其中吸附剂床层为箱体状吸附剂床层,其中在箱体内部填充有吸附剂,箱体在水平横向和垂直纵向的两端均分别设有分布和收集空间以及分布和收集多孔板如图中所示的左、右多孔板及上、下多孔板;原料混合物在吸附剂床层左侧入口处进料和沿X轴正向通过吸附剂床层,吸余物流在吸附剂床层右侧出口处采出;吹扫剂由吸附剂床层左侧入口处进料和沿X轴正向通过吸附剂床层,吹扫物流在吸附剂床层右侧出口处采出;脱附剂由吸附剂床层上部进料和沿Y轴负向通过吸附剂床层,脱附物流从吸附剂床层下部采出,其中吹扫剂与原料混合物在吸附剂床层内的流向相同,和脱附剂与原料混合物在吸附剂床层内的流向相互垂直。具体实施方式下面通过实施例进一步描述本发明,但所述实施例不以任何方式限制本发明的范围。在下列实施例中,所采用的吸附剂为按照专利CN1105906A(该专利在此全文引入作为参考)中所述方法生产的MFI型无粘结剂疏水硅沸石,即ZSM-5型无粘结剂疏水硅沸石或无粘结剂Silicalite-1沸石,这类无粘结剂疏水硅沸石为可商购的工业产品,具有强的水热稳定性以及强的耐酸和耐弱碱性,且由于分子筛骨架中基本不含铝,疏水性很强,吸水量很小,而且在中毒失活后也可以通过简单焙烧恢复活性,具体在300-800℃下焙烧1-5小时即可恢复活性而实现再生。在下列实施例中,所使用的分子筛吸附剂是平均直径为2-3mm的小球,所采用的原料混合物及收集得到的吸余物流、吹扫物流和脱附物流最终均以液相形式存在,这些液相物流的组成通过气相色谱进行分析。实施例实施例1二甲苯混合物的选择性吸附分离使用如图1所示的圆柱状吸附剂床层,床层内径为0.1m,高度为0.2m,所述床层配有夹套,床层中装填有800g吸附剂小球,其中原料混合物为组成如下表1所示的二甲苯混合物,采用水蒸汽作为吹扫剂,其分离系数比β对二甲苯/水蒸汽约为20,和采用甲苯作为脱附剂,其分离系数比β对二甲苯/甲苯约为7.5,其中吸附步骤、吹扫步骤和脱附步骤均在常压下进行。操作步骤如下:吸附步骤,其中使二甲苯混合物预热至155℃和以重时空速1h-1从吸附剂床层下部进料,吸余物流从吸附剂床层上部采出,经冷却获得液相吸余物流,保持吸附剂床层温度为155℃,持续进料,直到对二甲苯吸附量达到其动态穿透吸附量的95%时停止进料,此时吸附步骤的持续时间为30min;吹扫步骤,其中使作为吹扫剂的水蒸汽加热至160℃和以重时空速1h-1从吸附剂床层下部进料,吹扫物流从吸附剂床层上部采出,吹扫过程持续2min,经冷却和水油相分离获得吹扫物流油相,所述吹扫物流油相与吸余物流合并收集;脱附步骤,其中使作为脱附剂的甲苯预热至155℃和以重时空速1h-1从吸附剂床层上部进料,脱附物流从吸附剂床层下部采出,经冷却获得液相脱附物流,以脱附物流中对二甲苯含量小于0.2wt%为脱附终点,此时脱附步骤的持续时间为60min;和依次重复上述各操作步骤进入下一个循环。操作完成后获得的各物流组成如下表1所示。表1实施例1的原料混合物及获得的各物流的组成由实施例1的结果可知,采用本发明的方法,所获得的吸余物流+吹扫物流油相的混合物流中对二甲苯含量很低,该混合物流经后续分离即可获得高纯度的间二甲苯和邻二甲苯,和所获得的脱附物流经后续分离后即可获得高纯度的对二甲苯和乙苯,从而可以实现四种C8组分的高效分离。实施例2二氯苯混合物的选择性吸附分离使用图1所示的圆柱状吸附剂床层,床层内径为0.1m,高度为0.2m,所述床层配有夹套,床层中装填有800g吸附剂小球,其中原料混合物为组成如下表2所示的二氯苯混合物,采用氮气作为吹扫剂,其分离系数比β对二氯苯/氮气约为25,和采用氯苯作为脱附剂,其分离系数比β对二氯苯/氯苯约为1.5,其中吸附步骤、吹扫步骤和脱附步骤均在常压下进行。操作步骤如下:吸附步骤,其中使二氯苯混合物预热至193℃和以重时空速1h-1从吸附剂床层下部进料,吸余物流从吸附剂床层上部采出,经冷却获得液相吸余物流,保持吸附剂床层温度为193℃,持续进料,直到对二氯苯吸附量达到其动态穿透吸附量的70%时停止进料,此时吸附步骤的持续时间为6min;吹扫步骤,其中使作为吹扫剂的氮气加热到200℃和以重时空速1h-1从吸附剂床层下部进料,吹扫物流从吸附剂床层上部采出,吹扫过程持续1min,经冷却和气液相分离获得吹扫物流液相,所述吹扫物流液相与吸余物流合并收集;脱附步骤,其中使作为脱附剂的氯苯预热至190℃和以重时空速1h-1从吸附剂床层上部进料,脱附物流从吸附剂床层下部采出,经冷却获得液相脱附物流,以脱附物流中对二氯苯含量小于0.2wt%为脱附终点,此时脱附步骤的持续时间为15min;和依次重复上述各操作步骤进入下一个循环。操作完成后获得的各物流组成如下表2所示。表2实施例2的原料混合物及获得的各物流的组成由实施例2的结果可知,采用本发明的方法,所获得的吸余物流+吹扫物流液相的混合物流中对二氯苯含量很低,该混合物流经后续分离即可获得高纯度的间二氯苯和邻二氯苯,所获得的脱附物流经简单精馏即可获得高纯度的对二氯苯,从而可以实现三种二氯苯异构体混合物的高效分离。实施例3二氯甲苯三异构体混合物的选择性吸附分离使用如图1所示的圆柱状吸附剂床层,床层内径为0.1m,高度为0.2m,所述床层配有夹套,床层中装填有800g吸附剂小球,其中原料混合物为组成如下表3所示的主要含有1,2,4-二氯甲苯、1,2,5-二氯甲苯、1,2,6-二氯甲苯的二氯甲苯三异构体混合物,其中1,2,5-二氯甲苯为目标组分,采用氮气作为吹扫剂,其分离系数比β1,2,5-二氯甲苯/氩气约为28,和采用氯苯作为脱附剂,其分离系数比β1,2,5-二氯甲苯/氯苯约为2.1,其中吸附步骤和吹扫步骤在加压下进行,和脱附步骤在常压下进行。操作步骤如下:吸附步骤,其中使二氯甲苯三异构体混合物在表压为0.3MPa下预热至250℃和以重时空速3h-1从吸附剂床层下部进料,吸余物流从吸附剂床层上部采出,经冷却获得液相吸余物流,保持吸附剂床层温度为255℃,持续进料,直到1,2,5-二氯甲苯吸附量达到其动态穿透吸附量的80%时停止进料,此时吸附步骤的持续时间为4min;吹扫步骤,其中使作为吹扫剂的氮气在表压为0.3MPa下加热到250℃和以重时空速0.1h-1从吸附剂床层下部进料,吹扫物流从吸附剂床层上部采出,吹扫过程持续3min,经冷却和气液相分离获得吹扫物流液相,所述吹扫物流液相与吸余物流合并收集;脱附步骤,其中使作为脱附剂的氯苯在常压下预热至210℃和以重时空速1.5h-1从吸附剂床层上部进料,脱附物流从吸附剂床层下部采出,经冷却获得液相脱附物流,以脱附物流中1,2,5-二氯甲苯含量小于0.2wt%为脱附终点,此时脱附步骤的持续时间为12min;和依次重复上述各操作步骤进入下一个吸附分离循环。操作完成后获得的各物流组成如下表3所示。表3实施例3的原料混合物及获得的各物流的组成*备注:表3所示的作为原料混合物的二氯甲苯三异构体混合物由二氯甲苯五异构体混合物精馏获得,其中该二氯甲苯三异构体混合物作为塔顶产物获得由实施例3的结果可知,采用本发明的方法,所获得的吸余物流+吹扫物流液相的混合物流中1,2,5-二氯甲苯含量很低,该混合物流经精馏可作为塔底产物获得纯度达99.85wt%的1,2,6-二氯甲苯,所获得的脱附物流经简单精馏可作为塔底产物获得1,2,4-二氯甲苯和1,2,5-二氯甲苯的混合物,该混合物经进一步结晶或精馏后可获得高纯度的1,2,4-二氯甲苯和1,2,5-二氯甲苯,从而可以实现二氯甲苯三异构体混合物的高效分离。由此可知,本发明的选择性吸附分离方法可以与精馏和结晶相结合实现对二氯甲苯五异构体混合物的高效分离。因此,按照本发明,在吸附床层未饱和如床层吸附量以动态穿透吸附量计达到一定值时停止吸附和开始吹扫,且其中吹扫剂的吹扫路径与原料混合物的吸附路径相同,使得在吹扫过程中床层内残余原料混合物内的目标组分再次经过吸附路径时可以被不饱和床层中剩余的吸附位点继续吸附,由此收集得到的吹扫物流可以无需再次经历吸附分离,而是可以在与吹扫剂相分离(水油相分离或气液相分离)后与吸余物流一起收集,且如此获得混合物流中目标组分含量很低,所获得的脱附物流中目标组分含量也很高,从而可以实现各组分的高效分离,实施例1-3已经很好地证实了这一点。实施例4废水中丙酮的选择性吸附分离使用如图2所示的箱体状吸附剂床层,床层沿X、Y、Z轴的内部尺寸分别为0.28m、0.2m和0.05m,所述床层配有夹套,床层中装填有800g吸附剂小球,其中原料混合物为组成如下表4所示的含丙酮废水,采用空气作为吹扫剂,其分离系数比β丙酮/空气约为15,和采用水蒸汽作为脱附剂,其分离系数比β丙酮/水蒸汽约为8,其中吸附步骤在常压下进行,吹扫步骤和脱附步骤在加压下进行操作步骤如下:吸附步骤,其中使含丙酮废水在常温常压下以重时空速1h-1由吸附剂床层左侧入口处进料和沿X轴正向通过吸附剂床层,吸余物流在吸附剂床层右侧出口处收集,持续进料,直到丙酮吸附量达到其动态穿透吸附量的98%时停止进料,此时吸附步骤的持续时间为5h;吹扫步骤,其中使作为吹扫剂的空气加压至0.3MPa表压后以重时空速0.3h-1由吸附剂床层左侧入口处进料和沿X轴正向通过吸附剂床层,吹扫过程持续5min,在床层右侧出口处收集得到的吹扫物流经气液相分离后得到吹扫物流液相,该吹扫物流液相和吸余物流合并收集后可作为达标废水排放;脱附步骤,首先采用夹套加热使吸附剂床层温度达140℃,然后使预热至120℃的水蒸汽以重时空速0.5h-1由吸附剂床层顶部进料和沿Y轴负向通过吸附剂床层,脱附物流从吸附剂床层下部采出,经冷却获得液相脱附物流,以液相脱附物流中丙酮含量小于0.2wt%为脱附终点,此时脱附步骤的持续时间2h;和依次重复上述各操作步骤进入下一个循环。操作完成后获得的各物流组成如下表4所示。表4实施例4的原料混合物及获得的各物流的丙酮含量物流含丙酮废水吸余物流+吹扫物流液相脱附物流丙酮含量1.2wt%45ppmw13.9wt%由实施例4的结果可知,采用本发明的方法,可以将含丙酮废水中的丙酮浓度降低至45ppmw,从而达到废水排放标准,另外还能得到含量高达13.9wt%的丙酮溶液,该丙酮溶液可经进一步提纯得到丙酮溶剂。实施例5废水中二甲基乙酰胺的选择性吸附分离使用如图2所示的箱体状吸附剂床层,床层沿X、Y、Z轴的内部尺寸分别为0.28m、0.2m和0.05m,所述床层配有夹套,床层中装填有1500g吸附剂小球,其中原料混合物为组成如下表5所示的含二甲基乙酰胺废水,采用氮气作为吹扫剂和脱附剂,其分离系数比β二甲基乙酰胺/氮气约为4.5,其中吸附步骤和脱附步骤在常压下进行,和吹扫步骤在加压下进行。操作步骤如下:吸附步骤,其中使含二甲基乙酰胺废水在常温常压下以重时空速0.5h-1由吸附剂床层左侧入口处进料和沿X轴正向通过吸附剂床层,吸余物流在吸附剂床层右侧出口处收集,持续进料,直到二甲基乙酰胺吸附量达到其动态穿透吸附量的98%时停止进料,此时吸附步骤的持续时间为12h;吹扫步骤,其中使作为吹扫剂的氮气加压至0.05MPa表压后以重时空速0.2h-1由吸附剂床层左侧入口处进料和沿X轴正向通过吸附剂床层,吹扫过程持续2min,在床层右侧出口处收集得到的吹扫物流经气液相分离后得到吹扫物流液相,该吹扫物流液相和吸余物流合并收集后可作为达标废水排放;脱附步骤,首先采用夹套加热使吸附剂床层温度达250℃,其间在温度达到100℃时将预热至200℃的氮气以重时空速4.0h-1由吸附剂床层顶部进料和沿Y轴负向通过吸附剂床层,脱附物流从吸附剂床层下部采出,经冷却和气液相分离获得脱附物流液相,以不再获得脱附物流液相或脱附物液相流量很少为脱附终点,此时脱附步骤的持续时间为0.5h;和依次重复上述各操作步骤进入下一个循环。操作完成后获得的各物流组成如下表5所示。表5实施例5的原料混合物及获得的各物流的二甲基乙酰胺含量由实施例5的结果可知,采用本发明的方法,可以将含二甲基乙酰胺废水中的二甲基乙酰胺浓度降低至30ppmw,从而达到废水排放标准,另外还能得到含量高达30wt%的二甲基乙酰胺溶液,该二甲基乙酰胺溶液可经进一步提纯得到二甲基乙酰胺溶剂。也就是说,按照本发明,在进行废水处理时,不仅可以实现废水的达标排放,还可以回收废水中的有机物质如丙酮和二甲基乙酰胺,从而提高了废水处理的附加值。而且,如实施例4和5所证实的,当脱附方向与吸附方向垂直时,可使脱附时间缩短,进而提高吸附床的使用效率。另外,按照本发明,在进行废水处理时,由于吹扫步骤已经将床层中的大部分非目标组分即水吹出床层,因此,在脱附步骤时,这部分水不再耗费能量被脱附,由此可以节约很大一部分的过程能耗,这也是本发明的优点所在。当前第1页1 2 3