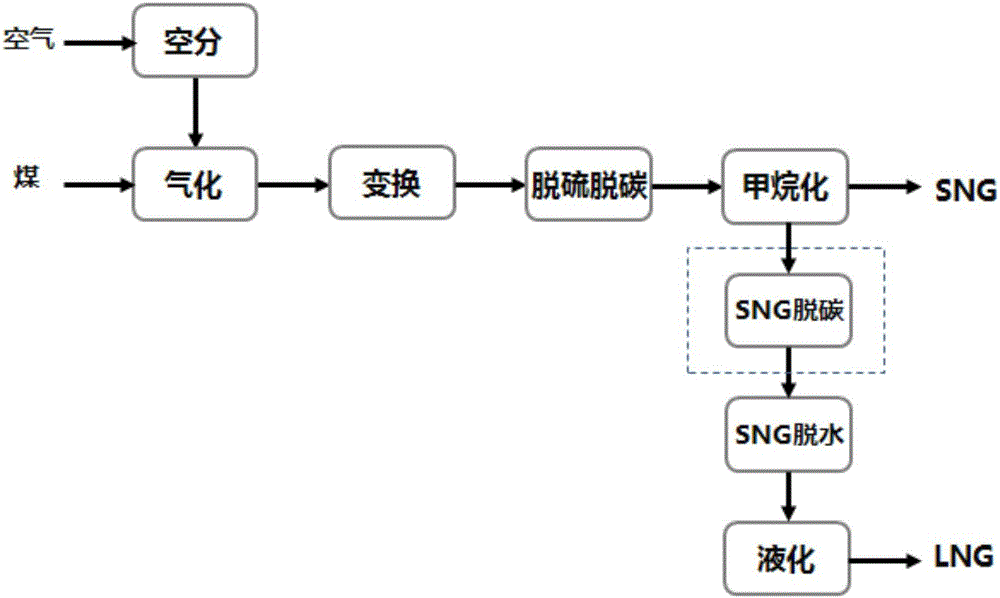
本发明属于天然气制备领域,尤其是涉及一种煤制液化天然气的耦合脱碳工艺。
背景技术:
:天然气是以甲烷为主要成分的气态化石燃料,燃烧后只生成水和CO2,排放清洁,不污染环境,是一种无色无味无毒、热值高、燃烧稳定、洁净环保的优质能源,广泛应用于工业生产和居民生活。由于我国是一个富煤、贫油、少气的国家,在过去的一次能源消费结构占比中,天然气仅占约5.8%,远低于全球平均水平24%。尽管如此,仍有部分天然气需要来自国外进口。2015年天然气进口量高达624亿立方米,对外依存度32.7%。随着近年来雾霾污染的加剧,对洁净的天然气燃料的需求量进一步加大。国务院印发的《能源发展战略行动计划(2014-2020)》明确提出,十三五末期,天然气在一次能源消费中比重将达到10%以上。在保证天然气对外依存度适中、能源安全得到保障的前提下,寻找非常规天然气或替代天然气资源迫在眉睫。煤制天然气是以我国储量较为丰富的煤炭资源为原料,通过煤集中加压气化、变换、脱硫脱碳以及甲烷化等工序合成天然气(SNG),如图1所示。这不仅契合我国富煤、少气的能源结构特点,有助于满足日益增长的天然气需求,降低我国对外依存度,保障我国能源安全,同时,生产过程中产生的硫化氢、有机硫等硫化物,也能通过硫回收工序通过副产硫磺或者硫酸的方式,加以回收,属于典型的煤炭资源清洁高效利用。被认为是比较符合我国能源结构和需求的工艺过程。继十二五期间几个大型煤制天然气项目建成后,2016年初,又有几个大型煤制天然气项目相继通过了环评审批。考虑到天然气使用的季节性差异变化,现代的煤制天然气项目在制备SNG的同时,会选择全部或者部分联产可储存、短距离运输灵活的液化天然气(LNG)产品,以便于项目匹配管网系统的调峰,同时也丰富了产品种类,满足不同用户的需求。由SNG制备LNG时,需要经冷箱在-160℃左右条件下进行精馏处理。由于SNG产品中会含有微量的CO2(约为1mol%),为防止CO2气进入冷箱中结冰,堵塞管道,在进入冷箱系统之前,通常需要设置专门的SNG脱碳工序,对合成的SNG进行深度的脱碳处理,将其中CO2浓度降至50mg/m3以下,如图2所示。该脱碳工序通常采用MDEA(N-甲基二乙醇)等胺法工艺,整个装置包括吸收、再生等系统,需要较大的一次性投资。同时所用的溶剂为特殊配方的MDEA溶液,且溶剂存在不稳定易变质,操作过程中易起泡,对设备腐蚀严重等问题,产生较高的操作费用。技术实现要素:有鉴于此,本发明旨在提出一种煤制液化天然气的耦合脱碳工艺,通过创新性的提出一种耦合的脱碳工艺流程,省去了传统煤制LNG工艺中专门用于SNG脱碳的脱碳装置,节省投资和操作费用。为达到上述目的,本发明的技术方案是这样实现的:一种煤制液化天然气的耦合脱碳工艺,包括如下步骤:(1)将经过甲烷化工序处理的SNG通入换热器中进行冷却;(2)将经过步骤(1)处理的SNG通入气液分离器中脱除其中的溶剂和水,脱除的溶剂和水通入粗煤气脱硫脱碳工序中进行循环利用;(3)将经过步骤(2)处理的SNG通入SNG洗涤塔中脱除CO2至CO2含量低于50mg/Nm3,所述经过步骤(2)处理的SNG由SNG洗涤塔的塔底通入,并与从SNG洗涤塔的塔顶通入的贫溶剂逆流接触,并由塔顶得到的净化的SNG;所述贫溶剂来自于粗煤气脱硫脱碳工序;所述贫溶剂在SNG洗涤塔中吸收CO2后形成富溶剂,将得到的富溶剂通入粗煤气脱硫脱碳工序中进行再生后循环利用。进一步的,所述步骤(1)中SNG在换热器中与冷媒或与步骤(3)得到的净化的SNG换热冷却。进一步的,所述步骤(3)的贫溶剂经过增压泵增压后通入SNG洗涤塔的塔顶。进一步的,所述步骤(1)中的经过甲烷化工序处理的SNG与贫溶剂混合后再通入换热器中进行换热冷却。进一步的,所述粗煤气脱硫脱碳工序为低温甲醇洗脱硫脱碳工序或MDEA法脱硫脱碳工序。进一步的,所述步骤(1)中甲烷化工序处理的SNG经过压缩后再通入换热器中进行换热冷却。进一步的,所述溶剂为甲醇。进一步的,所述换热器为绕管式换热器或管壳式换热器。相对于现有技术,本发明所述的煤制液化天然气的耦合脱碳工艺具有以下优势:(1)本发明所述的煤制液化天然气的耦合脱碳工艺对SNG的进行脱碳处理,仅需在粗煤气脱硫脱碳系统内耦合几台设备即可实现,省去了原工艺流程中专设的SNG脱碳装置,大大节省了一次性投资费用;(2)本发明通过粗煤气脱硫脱碳工序与SNG脱碳系统地耦合,缩短了流程,减少了溶剂损失量;对于粗煤气脱硫脱碳工序采用低温甲醇洗工艺的煤制LNG项目中采用本发明后,在溶剂消耗方面减少的更为明显,可有效避免传统SNG脱碳装置采用的MDEA等特殊配方的溶剂以及伴生的溶剂价格昂贵、循环量大、对设备腐蚀等问题,节约了操作费用;(3)采用本发明对于粗煤气脱硫脱碳工序采用低温甲醇洗工艺的煤制LNG,低温甲醇对CO2溶解度较大,通过调节吸收甲醇的使用量,可便利地控制SNG中CO2浓度,保证下游液化装置的稳定。附图说明构成本发明的一部分的附图用来提供对本发明的进一步理解,本发明的示意性实施例及其说明用于解释本发明,并不构成对本发明的不当限定。在附图中:图1为现有技术中的煤制天然气的流程示意图;图2为现有技术中的煤制LNG的流程示意图;图3为本发明耦合脱碳工艺的煤制LNG的流程示意图;图4为本发明的实施例所述的一种耦合脱碳工艺的示意图;图5为本发明的实施例所述的另一种耦合脱碳工艺示意图。附图标记说明:1-换热器;2-气液分离器;3-SNG洗涤塔;4-增压泵。具体实施方式需要说明的是,在不冲突的情况下,本发明中的实施例及实施例中的特征可以相互组合。在本发明的描述中,需要说明的是,除非另有明确的规定和限定,术语“安装”、“相连”、“连接”应做广义理解,例如,可以是固定连接,也可以是可拆卸连接,或一体地连接;可以是机械连接,也可以是电连接;可以是直接相连,也可以通过中间媒介间接相连,可以是两个元件内部的连通。对于本领域的普通技术人员而言,可以通过具体情况理解上述术语在本发明中的具体含义。下面将参考附图并结合实施例来详细说明本发明。本发明所述的一种煤制液化天然气的耦合脱碳工艺,具体工艺流程如图3所示,包括如下步骤:(1)将来自甲烷化工序的SNG通入换热器1,进行冷却。在该换热器1内,该SNG既可以与完成脱碳后净化的SNG换热冷却,也可以与换热器1内的冷媒换热冷却。若脱硫脱碳工序采用低温工艺,如低温甲醇洗脱硫脱碳工序,由于此时SNG内含有饱和的水蒸气,极易在管道和换热器内结冰影响工艺的进行,此时则需要喷入贫溶剂来降低SNG的冰点,分别如图4和图5所示。经换热器1回收冷量直接送往下游液化工序,制备LNG。(2)冷却后的SNG进入气液分离器2,脱除SNG中的溶剂和水,脱除的溶剂和水通入粗煤气脱硫脱碳工序中进行循环利用。(3)将经过步骤(2)处理的SNG由底部进入SNG洗涤塔3,由下往上流动,来自脱硫脱碳系统的贫溶剂经增压泵4加压后或直接由SNG洗涤塔3塔顶进入塔内,由上往下喷淋。在SNG洗涤塔3内,SNG与贫溶剂逆流接触,SNG中的CO2被贫溶剂吸收,由塔顶得到的CO2浓度小于50mg/m3的净化的SNG。上述工艺中,粗煤气脱硫脱碳工序可以是低温甲醇洗脱硫脱碳工序,也可以是MDEA法脱硫脱碳工序等常用脱硫脱碳工序。上述工艺中,进入粗煤气脱硫脱碳工序的SNG可以直接来自甲烷化装置,也可是经压缩后的。经压缩后,压力稍高于脱硫脱碳系统操作压力,更利于系统的耦合。上述工艺中,由于CO2在贫溶剂中的溶解度较大,通过简单调节塔顶贫溶剂的量,即可以便利的控制SNG中的CO2浓度,保证了下游液化装置的稳定运行。上述工艺中,由于SNG中的CO2含量很低,洗涤SNG后的富溶剂,吸收能力仍较强,可作为半贫液,进入粗煤气脱硫脱碳系统的脱碳段,用于洗涤粗煤气。同时,该富溶液中可能溶解的甲烷,经粗煤气气提后,又解析进入合成气系统,避免了甲烷的浪费。上述工艺中,换热器1可以采用绕管式换热器,也可用常规的管壳式换热器。实施例本实施例的煤制天然气联产4亿Nm3/年的LNG,甲烷化规模为19.4亿Nm3/年,SNG产品为15.4亿Nm3/年。本实施例的工艺流程图如图3所示,粗煤气脱硫脱碳工序采用低温甲醇洗工序,其他工序均采用常规操作,经甲烷化工序的SNG依次通入换热器1、气液分离器2、SNG洗涤塔3进行脱碳处理得到净化的SNG,净化的SNG经过液化得到LNG。本实施例中所用的换热器为绕管式换热器,SNG洗涤塔的型号为ID1600,材质为09MnNiDR,气液分离器ID1000,材质为09MnNiDR,贫甲醇增压泵为H为150m,流量为136.1m3/h。上述设备基于原系统需增加的投资费用约为215万元。本实施例中SNG脱碳处理的气量如见表1:表1本实施例中SNG脱碳处理的气量本实施例中原料的消耗量见表2:表2本实施例原料的消耗量名称单位消耗量甲醇消耗kg/hr75循环冷却水(30-40℃)t/hr14470.5MPa(G)蒸汽t/hr29.81.1MPa(G)蒸汽t/hr15.1轴功率kW4435对比例本对比例采用的是图2所示的工艺流程图,即用低温甲醇洗工序对粗煤气进行脱硫脱碳,用MDEA法脱碳工序对SNG的脱碳,两工序所要处理的气量见表3:表3低温甲醇洗工序和MDEA法脱碳工序的气量本对比例中原料的消耗量见表4:表4低温甲醇洗工序和MDEA法脱碳工序中原料的消耗量本对比例中MDEA法脱碳工序所需的设备的一次性投资费用为1100万元。实施例与对比例的投资费用和原料消耗量的对比见下表由上表可以看出,采用本发明的工艺,一次性投资费用可节省约885万元。同时,若循环水取0.25元/t,电取0.45元/kwh,MDEA溶液取30000元/m3,0.5MPaG蒸汽取110元/t,1.1MPaG蒸汽取120元/t,年原料的费用可节省约350万元。由此可见,采用本发明的工艺整体经济效益比较明显。以上所述仅为本发明的较佳实施例而已,并不用以限制本发明,凡在本发明的精神和原则之内,所作的任何修改、等同替换、改进等,均应包含在本发明的保护范围之内。当前第1页1 2 3