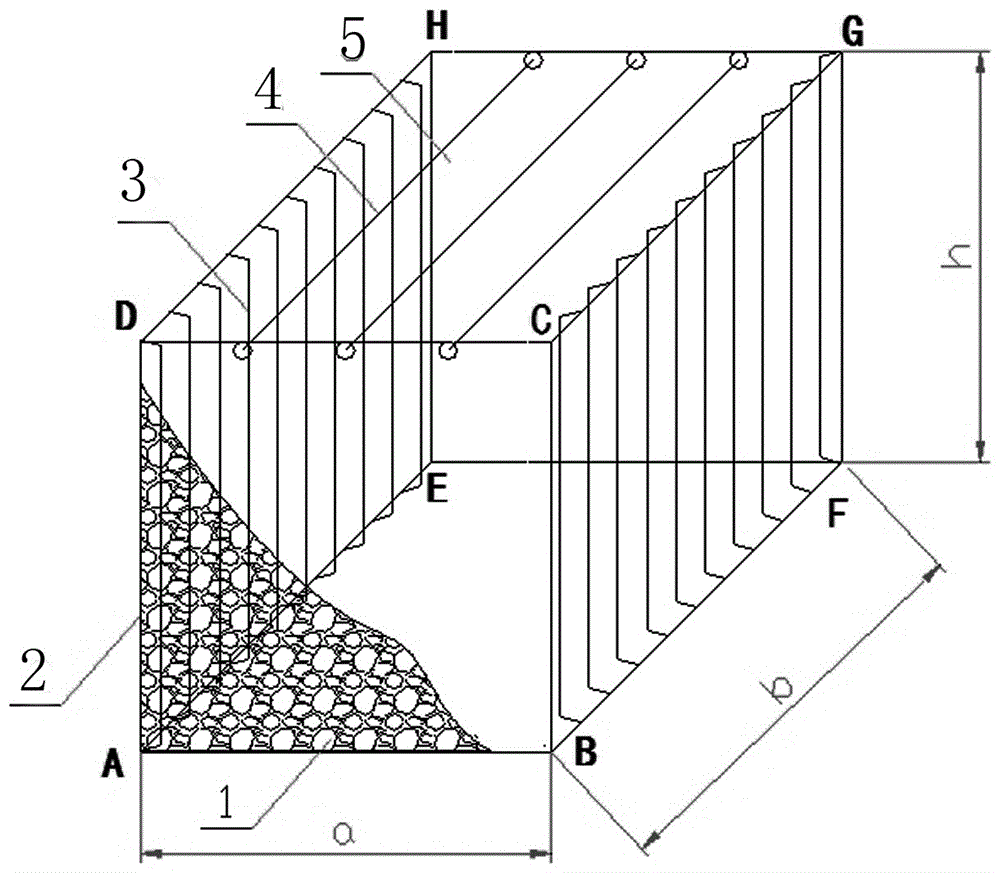
本发明属于微连续流体器件领域,公开了一种用于微通道反应器内构件及其装填方法。
背景技术:
:微通道反应器是一种借助于特殊微加工技术的新型反应器,具有返混小、传质传热效率高、反应时间与反应温度便于控制、易于放大等特征。但微通道加工难度大,制作成本高,因此开发简单的微通道构件加工方法,降低微通道反应器的成本是急需要解决的难题。CN105396528A公开了一种具有防腐性能的微通道反应器,该反应器结构紧凑、密封简单、加工难度小、换热和反应效率高、可移动、可实现成套设备微型化。CN105126721A公开一种带有冷却系统的非叠层结构微反应器,可进行拆卸清洗和系统冷却,有效防止微反应器微通道的堵塞和微反应器装置的局部过热。CN102421515A公开了一种送液量小、混合性能高的微反应器,通过至少一次的流体分割混合来实现流体的均匀混合与快速反应。已经公开的专利致力于增加防腐性能、提高传热传质速率及强化流体的混合与分布,未能有效的降低微通道反应器的加工成本。技术实现要素:针对微通道反应器制作成本高的缺陷,本发明公开了一种用于液体酸烷基化反应的微通道反应器内构件模块及其装填方法,可精准控制反应温度,提高传质速率与宏观反应速率。微通道构件具有耐酸,耐腐蚀性能,可实现高效、节能、安全、低碳和环保的连续化生产。为解决上述技术问题,本发明是这样实现的。一种用于液体酸烷基化反应的微通道反应器内构件模块,它包括纤维布、框架、支撑筋、穿钉及纤维捻;所述支撑筋与框架活动相接;所述纤维布通过框架立柱及支撑筋实现多层折叠;所述纤维布始端及终端通过纤维捻与框架固定相接;所述穿钉穿过纤维布。作为一种优选方案,本发明所述框架为圆钢构成的长方体,长度为200~1000mm,宽度为200~1000mm,高度为200~1000mm,圆钢直径为3~30mm。进一步地,本发明在所述框架顶部两根平行的横梁下方设置若干圆环,圆环内径为3~20mm,圆环间距为100~500mm;所述穿钉端部与圆环固定相接。进一步地,本发明所述支撑筋为圆钢或钢丝,两端做成弯钩,搭载在框架非设置圆环的上下两根横梁之上;支撑筋直径为2~10mm,长度与框架高度相同。进一步地,本发明所述穿钉为圆钢或钢丝制成,直径略小于所述圆环内径,差值为2~5mm,长度与框架宽度相同;穿钉两端设置螺纹,螺纹长度为5~20mm。进一步地,本发明所述纤维布由膨化纤维编织而成,具有致密孔隙状结构;骨架密度为0.1~3.0g/mL,平均直径为10~240μm,比表面积为0.1~30m2/g。上述用于液体酸烷基化反应的微通道反应器内构件模块的装填方法,可按如下步骤进行。A、称取膨化纤维,加工制成宽度与框架高度相同的纤维布。B、利用纤维捻将纤维布始端缝制在框架中的一根立柱上,将纤维布依次绕过框架对面立柱与各个支撑筋实现多层折叠后,使用纤维捻将纤维布终端缝制固定。C、每折叠一次,将穿钉穿过该层纤维布,折叠完成之后,将穿钉两端锁死在框架顶部横梁下方的圆环之上,并均匀分布横梁之上的支撑筋。本发明上述纤维布厚度优选0.5~20mm。通过改变纤维模块的填充率,可灵活的调控反应过程的压降与物料停留时间。若异丁烷或注入反应器的惰性制冷剂的饱和蒸汽压接近反应器的平均压力,此时反应器压降的变化,可用于调整异丁烷或惰性取热介质的汽化量,精准调控反应温度。与现有技术相比,本发明具有的优点和积极效果是:使用模块化的纤维填料作为微通道构件,降低了微通道反应器的制作成本;反应物料与催化剂实现膜接触,提高传质速率与宏观反应速率;通过改变纤维模块的填充率,可灵活的调控反应过程的压降与物料停留时间,并精准控制反应温度。本发明的微通道构件模块具有耐酸,耐腐蚀性能,可实现高效、节能、安全、低碳和环保的连续化生产。附图说明下面结合附图和具体实施方式对本发明作进一步说明。本发明的保护范围不仅局限于下列内容的表述。图1为本发明用于液体酸烷基化反应的微通道反应器内构件模块结构示意图。图2为本发明用于液体酸烷基化反应的微通道反应器内构件模块装填方法示意图。图中:1、纤维布;2、框架;3、支撑筋;4、穿钉;5、纤维捻;6、反应区;7、死区。具体实施方式如图所示,用于液体酸烷基化反应的微通道反应器内构件模块,包括纤维布1、框架2、支撑筋3、穿钉4及纤维捻5;所述支撑筋3与框架2活动相接;所述纤维布1通过框架2立柱及支撑筋3实现多层折叠;所述纤维布1始端及终端通过纤维捻5与框架2固定相接;所述穿钉4穿过纤维布1。本发明所述框架2为圆钢构成的长方体,长度为200~1000mm,宽度为200~1000mm,高度为200~1000mm,圆钢直径为3~30mm。本发明在所述框架2顶部两根平行的横梁下方设置若干圆环,圆环内径为3~20mm,圆环间距为100~500mm;所述穿钉4端部与圆环固定相接。本发明所述支撑筋3为圆钢或钢丝,两端做成弯钩,搭载在框架2非设置圆环的上下两根横梁之上;支撑筋3直径为2~10mm,长度与框架高度相同。本发明所述穿钉4为圆钢或钢丝制成,直径略小于所述圆环内径,差值为2~5mm,长度与框架宽度相同;穿钉两端设置螺纹,螺纹长度为5~20mm。本发明所述纤维布1由膨化纤维编织而成,具有致密孔隙状结构;骨架密度为0.1~3.0g/mL,平均直径为10~240μm,比表面积为0.1~30m2/g。上述用于液体酸烷基化反应的微通道反应器内构件模块的装填方法,可按如下步骤进行。A、称取膨化纤维,加工制成宽度与框架高度相同的纤维布1;纤维布厚度为0.5~20mm。B、利用纤维捻5将纤维布1始端缝制在框架2中的一根立柱上,将纤维布1依次绕过框架对面立柱与各个支撑筋3实现多层折叠后,使用纤维捻5将纤维布1终端缝制固定。C、每折叠一次,将穿钉4穿过该层纤维布1,折叠完成之后,将穿钉4两端锁死在框架2顶部横梁下方的圆环之上,并均匀分布横梁之上的支撑筋3。本发明纤维布由膨化纤维编织而成,纤维可以是玻璃纤维、聚乙烯纤维、聚丙烯纤维、丙纶纤维、芳纶纤维、聚苯硫醚纤维或耐酸聚酰亚胺纤维中的一种或几种。纤维骨架密度为0.1~3.0g/mL,平均直径为10~240μm,比表面积为0.1~30m2/g。编织而成的纤维布具有致密孔隙状结构,耐腐蚀,适用于有强酸参与的化学反应。纤维布具有亲酸疏烃性能,可在外表面形成酸膜,反应物在酸膜外流动,酸粘度相对较大,而反应物粘度相对较小,反应物与酸之间存在速度差,液液两相之间形成内摩擦力将酸膜变薄实现膜接触,增大传质面积,提高传质效率。使用纤维模块替代微加工技术,保留微通道反应器诸多优点的同时降低制造成本。本发明框架为圆钢构成的长方体,为内构件模块提供固定的外形结构与尺寸。框架长度a为200~1000mm,宽度b为200~1000mm,高度h为200~1000mm,构成框架的圆钢直径为3~30mm。在框架顶部横梁CD与横梁GH下方设置若干圆环,用悬挂穿钉,圆环内径为3~20mm,圆环间距为100~500mm。支撑筋为圆钢或钢丝制成,为纤维布在框架内折叠过程提供支撑。支撑筋两端做成弯钩,左侧搭载在横梁DH与横梁AE之上,右侧搭载在横梁CG与横梁BF之上,支撑筋在横梁上可沿着框架宽度的方向自由滑动。支撑筋直径为2~10mm,长度与框架2高度h相同。穿钉为圆钢或钢丝制成,穿透纤维布,防止纤维布塌陷。穿钉直径略小于框架顶部横梁CD与横梁GH下方圆环内径,差值为2~5mm,长度与框架宽度b相同。穿钉两端设置螺纹,螺纹长度为5~20mm,一端螺纹连接钉头,用于穿透纤维布,另一端螺纹连接螺母,用于将穿钉锁死在横梁CD与横梁GH下方的圆环上。纤维捻材质与纤维布相同,用于缝制纤维布,即将纤维布两端固定在框架的立柱上。将反应器划分为反应区与死区两部分,以反应区最大化为原则,对反应器横截面进行规划,确定用于液体酸烷基化反应的微通道反应器内构件模块尺寸,并使用隔板将反应区与死区之间隔开。按照微通道构件模块填充容重的要求,称取一定重量的膨化纤维,加工制成宽度与框架高度h相同的纤维布,纤维布厚度为0.5~20mm,利用纤维捻将纤维布始端缝制在框架中的一根立柱AD上,将纤维布绕过对面立柱BC,并在横梁DH与横梁AE之上搭载一根支撑筋,继续将纤维布绕过该支撑筋之后,在对面的横梁CG与横梁BF之上搭载另一根支撑筋,按照相同的方法将纤维布依次绕过各个支撑筋实现多层折叠。通过螺纹,在穿钉4的一端加装钉头,纤维布每折叠一次,推进穿钉,将全部穿钉4穿过该层纤维布,同时将支撑筋紧靠一起,全部纤维布折叠完成之后,卸下钉头,使用螺母将穿钉两端锁死在框架顶部横梁CD与横梁GH下方的圆环之上,同时使用纤维捻将纤维布终端进行缝制固定,并均匀分布横梁之上的支撑筋。不同内构件模块的高度必须一致,但长度与宽度可以存在差异。在反应器底部设置支撑板,按照预期的规划方案,将内构件模块以整砌的方式装入反应器支撑板之上的反应区,完成装填,进一步加装顶部封头与底部封头之后即构成微通道反应器。在本发明微通道内构件的反应器内,以硫酸为催化剂,以异丁烷或丙烷作为冷剂进行烷基化反应。具体反应条件见表1,反应结果见表2。比较例1~2。比较例1采用常规的内部设置制冷管束的卧式机械搅拌反应器,比较例2采用常规微通道反应器(微通道构件同实施例1),反应条件参见表1,反应结果参见表2。表1实施例与比较例烷基化反应主要条件。实施例1比较例1比较例2烷烯摩尔比9:19:19:1酸烃体积比1:11:11:1反应温度,℃0℃4℃4℃反应压力,MPa0.30.30.3停留时间,min102020表2实施例与比较例烷基化反应结果。实施例1比较例1比较例2丁烯转化率,mol%100100100酸耗,kg酸/t烷基化油436574烷基化油辛烷值(马达法)95.492.793.1以上所述仅为本发明较佳的实施例而已,并不用以限制本发明,凡在发明的精神和原则之内所做的任何修改,等同替换和改进等,均应包含在本发明保护范围之内。当前第1页1 2 3