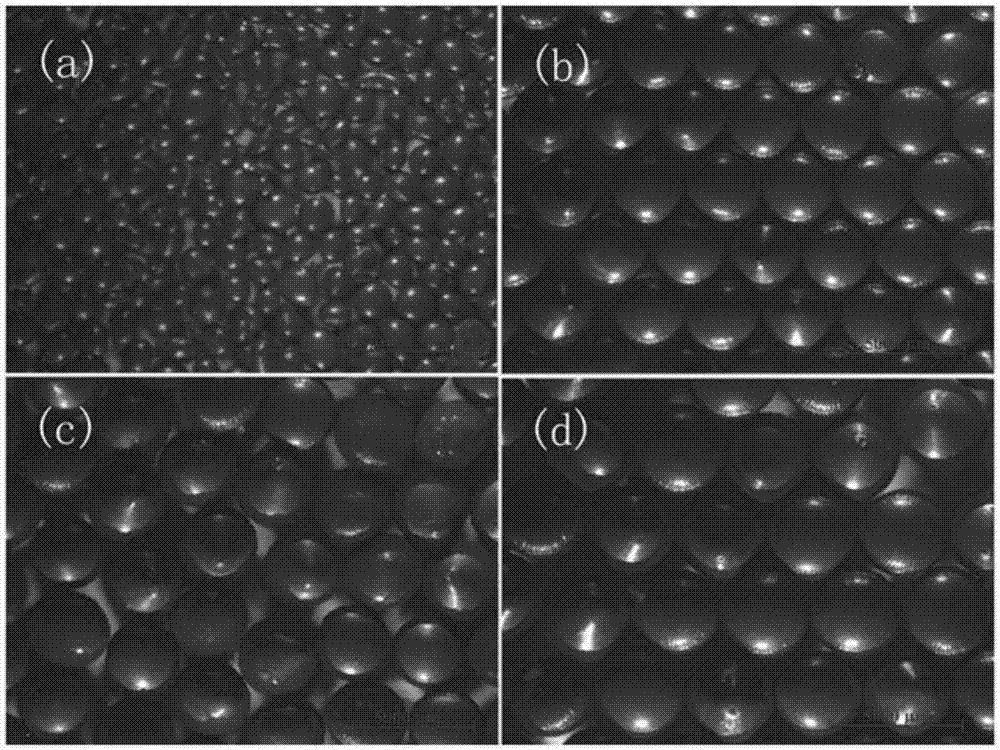
本发明属于化学提取
技术领域:
,特别是涉及一种用于盐湖卤水、海水、地热水、固废浸取液等含锂溶液中颗粒锂吸附剂的制备方法。
背景技术:
:目前,能源短缺、资源匮乏以及环境污染等问题正威胁着人类文明的健康发展。面对环境恶化的严峻形势,大幅减少化石类能源的开采使用,发展新型可再生能源已成为人类共识。锂电池具有高比能量、低自放电、高循环寿命、无记忆效应等特点,是目前最具发展前景的高效二次电池和发展最快的化学储能电源,锂电池的发展和应用对于提高资源利用率、解决能源危机和保护环境都具有重要的战略意义。由于价格高涨,目前锂资源的开发是矿石和卤水工艺并举,未来的产业重心将由含锂矿石提锂转向卤水提锂和退役锂电池回收领域。从卤水中回收锂的技术有沉淀法、膜法、萃取法、吸附法等。沉淀法主要适用于低镁锂比卤水提锂;膜法主要适用锂浓度较高的含锂溶液提锂;萃取法的应用受设备腐蚀和环境污染限制,未能广泛应用。吸附法的关键是性能优良的吸附剂,目前有多种吸附剂对锂具有较高的吸附容量和较高的选择性,常见的锂吸附剂有锰系锂离子筛、钛系锂离子筛、铝盐吸附剂、磷酸铁锂离子筛等。但是由于这些吸附剂合成后均为粉体状态,无法直接应用于固定床等常规设备进行吸附-脱附提锂。因此,研制具有商业应用价值的颗粒锂吸附剂,对未来锂资源的开发具有重要意义。技术实现要素:本发明的目的是提供一种可直接工业化应用于盐湖卤水、海水、地热水、固废浸取液等含锂溶液提锂的颗粒锂吸附剂的制备方法,制备的颗粒锂吸附剂的亲水性好,与锂吸附剂粉体相比吸附容量变化小,操作简单,成本低,易于工业化应用。为了实现上述目的,本发明采用的技术方案如下:本发明的第一个方面提供了一种颗粒锂吸附剂的制备方法,包括以下步骤:将锂吸附剂或其前驱体粉体、多种聚合物、造孔剂和有机溶剂在常压、温度为10-190℃的条件下混合,搅拌1-120min,得到均匀混合物;多种聚合物与有机溶剂的质量比为(0.01-10):1;造孔剂与有机溶剂的质量比为(0~0.2):1;锂吸附剂或其前驱体粉体与有机溶剂的质量比为(0.1~10):1;将上述均匀混合物滴入溶液中,均匀混合物与溶液的质量比为(0.01~0.3):1,或将上述均匀混合物挤出成型破碎,经过洗涤得到颗粒锂吸附剂。所述锂吸附剂或其前驱体粉体是锰系锂离子筛或其前驱体粉末、钛系锂离子筛或其前驱体粉末、铝盐吸附剂粉末、磷酸铁锂前驱体粉末中的至少一种,优选为锰酸锂(limn2o4或li4mn5o12)、铝盐吸附剂(lix·2al(oh)3·nh2o,x代表阴离子,为cl-、so42-中的一种,n的取值范围为0-2)、钛酸锂(li4ti5o12)中的至少一种。所述多种聚合物是聚偏氟乙烯、聚乙烯、聚丙烯、聚氯乙烯、氯化聚氯乙烯、聚苯乙烯、聚偏二氟乙烯、聚偏二氯乙烯、abs树脂、聚酰胺、聚甲醛、聚碳酸酯、聚醚酮、聚醚砜、聚苯醚、聚氨酯、聚乙烯醇缩丁醛、聚乙烯吡咯烷酮、聚丙烯酸、聚甲基丙烯酸甲酯、聚乙二醇、聚乙烯醇、聚对苯二甲酸乙二醇酯中的至少一种。所述造孔剂为氯化钠、氯化钾、硫酸钠、硫酸钾、碳酸钠、碳酸钾、硝酸钠、硝酸钾中的至少一种。所述有机溶剂为苯、甲苯、四氢呋喃、三氯甲烷、四氯化碳、二氯亚砜、n,n-二甲基甲酰胺、n,n-二甲基乙酰胺、全氯乙烯、三氯乙烯、芳烃、乙酸乙酯、丙酮、n-甲基吡咯烷酮中的至少一种。所述将上述均匀混合物滴入溶液中,滴加采用方法为滴管滴加、注射器滴加、泵抽取滴加中的至少一种。所述将上述均匀混合物滴入溶液中,均匀混合物与溶液的距离为0.1-1m。所述将上述均匀混合物滴入溶液中,溶液为水、乙醇、丙醇、乙二醇、丙酮中的至少一种。所述将上述均匀混合物挤出成型破碎,挤出成型的温度为0-200℃,挤出压力为0-15mpa。所述洗涤采用水、乙醇、丙醇、乙二醇、丙酮中的至少一种。所述经过洗涤得到颗粒锂吸附剂,在洗涤前还包括脱锂步骤,所述脱锂采用的脱锂剂是:盐酸、硫酸、硝酸、过硫酸铵溶液、氯化锂溶液或去离子水,脱锂的温度为0-100℃。本发明的第二个方面提供了一种所述方法制备的颗粒锂吸附剂。所述颗粒锂吸附剂的粒径为0.3-4mm。由于采用上述技术方案,本发明具有以下优点和有益效果:本发明提供的颗粒锂吸附剂的制备方法制备的颗粒锂吸附剂,颗粒强度高、韧性好,装入固定床或吸附塔中不易破碎、粉化,亲水性好,成型后与粉体吸附量差异小;工艺简单,且使用的溶剂在精馏后回用,成本低,对环境污染小,适用于工业化应用。本发明提供的颗粒锂吸附剂的制备方法制备的颗粒锂吸附剂,适用于吸附盐湖卤水、海水、地热水、固废浸取液等含锂溶液中的锂,以多种聚合物为粘结剂,对锂吸附剂粉末进行成型造粒,获得颗粒状锂吸附剂,颗粒吸附剂平均粒径可控制在0.3-4.0mm范围内。附图说明图1为不同粒径的实施例1制备的颗粒锰系锂离子筛体视显微镜图像。a为平均粒径0.840mm的颗粒;b为平均粒径2.735mm的颗粒;c为平均粒径2.923mm的颗粒;d为平均粒径3.346mm的颗粒。图2为颗粒锰系锂离子筛的xrd谱图。图3为颗粒铝盐吸附剂的xrd谱图。图4为颗粒钛系锂离子筛的xrd谱图。图5为颗粒锰系锂离子筛前驱体热重曲线。图6为li4mn5o12粉末与实施例1制备的颗粒锰系锂离子筛的吸附动力学曲线。图7为固定床填充实施例1制备的颗粒锂吸附剂的吸附穿透曲线。图8为固定床填充实施例1制备的颗粒锂吸附剂的洗脱曲线。具体实施方式为了更清楚地说明本发明,下面结合优选实施例对本发明做进一步的说明。本领域技术人员应当理解,下面所具体描述的内容是说明性的而非限制性的,不应以此限制本发明的保护范围。本发明实施例中所用的聚偏氟乙烯的平均分子量为534000,购自上海麦克林生化科技有限公司;聚乙烯醇的分子量为31000-500000,购自赛默飞世尔科技(中国)有限公司;abs树脂型号为500p,购自美国杜邦公司;聚乙烯吡咯烷酮的分子量为50000-60000,购自上海泰坦科技股份有限公司;氯化聚氯乙烯型号为mc250,购自美国普立万公司;聚甲醛的型号bs090,购自上海蓝星聚甲醛有限公司;li4mn5o12、铝盐吸附剂、li4ti5o12粉末均为自制。li4mn5o12粉末的制备方法包括以下步骤:将碳酸锂和碳酸锰粉末按摩尔比为1:2.5的比例充分研磨后,在温度为400℃的条件下煅烧24h以上,获得li4mn5o12粉末。铝盐吸附剂粉末(licl·2al(oh)3·nh2o,n的取值范围为0-2)的制备方法包括以下步骤:将浓度为2.28mol·l-1的氯化锂与浓度为3.8mol·l-1的氯化铝混合溶液175ml,与浓度为6mol·l-1、100ml的氢氧化钠溶液搅拌反应,在80℃条件下,使用去离子水,以50ml/g粉末的比例脱锂1h后获得铝盐吸附剂粉末。li4ti5o12粉末的制备方法包括以下步骤:将碳酸锂和二氧化钛粉末按质量比为1.05:2.5的比例充分研磨后,在温度为900℃的条件下煅烧24h以上,获得li4ti5o12粉末。实施例1常压,温度为80℃条件下,将5.00g聚偏氟乙烯与1.00g聚乙烯醇溶解于20ml丙酮中,加入10gli4mn5o12超细粉体与2.0g氯化钠粉末,用高速匀浆机搅拌8min得到均匀混合物;多种聚合物聚偏氟乙烯与有机溶剂的质量比为0.38:1;造孔剂氯化钠与有机溶剂的质量比为0.13:1;锂吸附剂或其前驱体粉体与有机溶剂的质量比为0.63:1。使用不同口径的滴管将上述均匀混合物分别滴加到体积比为1:1的水和乙醇的混合溶液100ml中,均匀混合物与溶液的质量比为0.02:1,均匀混合物与溶液的距离为0.5m,获得粒径为0.8-3.3mm的颗粒锰系锂离子筛前驱体,将获得的颗粒锰系锂离子筛前驱体分别置于0.5mol·l-1的盐酸200ml中,25℃浸泡24小时,用100ml去离子水分三次洗涤,得到不同粒径的颗粒锰系锂离子筛即颗粒锂吸附剂,粒径为0.8-3.3mm,其体视显微镜图像见图1,图1为不同粒径的实施例1制备的颗粒锰系锂离子筛体视显微镜图像。a为平均粒径0.840mm的颗粒;b为平均粒径2.735mm的颗粒;c为平均粒径2.923mm的颗粒;d为平均粒径3.346mm的颗粒,从图中可以看出,所得颗粒锰系锂离子筛粒度均匀,且均为球形。所得颗粒锰系锂离子筛的xrd谱图见图2,图2为颗粒锰系锂离子筛的xrd谱图。从图中可以看出,成型后的颗粒锰系锂离子筛仍为尖晶石结构。实施例2常压,温度为50℃条件下,将4.50gabs树脂与2.00g聚乙烯吡咯烷酮溶解于20ml三氯甲烷中,加入9g铝盐吸附剂粉末licl·2al(oh)3与0.5g氯化钠粉末,用高速匀浆机搅拌8min得到均匀混合物;多种聚合物与有机溶剂的质量比为0.22:1;造孔剂氯化钠与有机溶剂的质量比为0.017:1;锂吸附剂或其前驱体粉体与有机溶剂的质量比为0.3:1。使用注射器将上述均匀混合物滴加到体积比为1:1的水和乙醇的混合溶液100ml中,均匀混合物与溶液的质量比为0.02:1,均匀混合物与溶液的距离为0.3m,获得粒径为1.0mm的铝盐吸附剂前驱体,用100ml去离子水分三次洗涤,获得颗粒铝盐吸附剂即颗粒锂吸附剂,粒径为1.0mm。颗粒铝盐吸附剂xrd谱图见图3,图3为颗粒铝盐吸附剂的xrd谱图。从图中可以看出,成型后的颗粒铝盐吸附剂仍为氢氧化铝的八面体结构。实施例3常压,温度为25℃条件下,将4.5g氯化聚氯乙烯与1.0g聚甲醛溶解于15ml四氢呋喃中,加入10gli4ti5o12粉末,用高速匀浆机搅拌80min得到均匀混合物;多种聚合物与有机溶剂的质量比为0.41:1;锂吸附剂或其前驱体粉体与有机溶剂的质量比为0.75:1;将上述均匀混合物使用挤出成型机挤出成型,挤出成型的温度为25℃,挤出压力为10mpa,置于60℃鼓风干燥箱内烘干后破碎,获得粒径为1-2mm的颗粒钛系锂离子筛前驱体,颗粒钛系锂离子筛前驱体置于0.5mol·l-1的盐酸中25℃浸泡120小时,用100ml去离子水分三次洗涤,得到颗粒钛系锂离子筛即颗粒锂吸附剂,粒径为1-2mm。颗粒钛系锂离子筛xrd谱图见图4,图4为颗粒钛系锂离子筛的xrd谱图。从图中可以看出,成型后的颗粒钛系锂离子筛仍为尖晶石结构。实施例4将实施例1制备的颗粒锰系锂离子筛在50℃下烘干,取少量使用热重分析其热稳定性,见图5,图5为颗粒锰系锂离子筛热重曲线,从图中可以看出,其在125℃内基本无失重,说明其热稳定性好,可以应用于各种温度下的水溶液。采用智能颗粒强度试验机来测试单个直径约2.5mm的颗粒锰系锂离子筛的机械强度,即使压力增大到50n,颗粒仍不破损,只是变形。实施例5用滤纸将实施例1制备的颗粒锰系锂离子筛表面吸干,称取一定质量的颗粒m1(单位g),同时在量筒加入一定量的去离子水(读取水体积v1(单位ml)),将称取的颗粒加入量筒中,待颗粒完全浸入水中后,读取总体积v2(单位ml),随后放入已知质量的离心管中,最后在50℃的鼓风干燥箱中干燥后称重(干燥颗粒质量m2(单位g)),以式1和式2计算样品颗粒的湿密度和孔隙率,测量5次,结果见表1。从表1中可以看出制备样品的孔隙率达到了79.83%,有利于li+的吸附和脱附。ρ=m1/(v2-v1)式1p=(m1-m2)/[ρh2o·(v2-v1)]式2式中:ρ为颗粒的湿密度,g·ml-1;ρh2o为去离子水的密度,g·ml-1;p为颗粒孔隙率。表1颗粒锰系锂离子筛的颗粒的湿密度和孔隙率序号颗粒的湿密度(g·ml-1)颗粒孔隙率(%)11.21380.9421.22978.9031.20681.0341.25480.0751.21878.22实施例6取0.3g实施例1制备的颗粒锰系锂离子筛加入100ml的氯化锂的氨缓溶液(licl浓度为0.01mol·l-1,氨水和氯化铵浓度均为0.1mol·l-1)中,测定其吸附动力学曲线,并与相同条件下li4mn5o12离子筛粉末(0.1gli4mn5o12粉末加入到100ml相同的氯化锂的氨缓溶液中的吸附动力学曲线比较,见图6,图6为li4mn5o12粉末与实施例1制备的颗粒锰系锂离子筛的吸附动力学曲线;在15小时后,本发明实施例1制备的颗粒锰系锂离子筛吸附量与li4mn5o12粉末吸附量相差不大。实施例7采用固定床对实施例1制备的颗粒锰系锂离子筛进行动态吸附-脱附评价,评价分为四个过程:1.吸附过程为将某盐湖老卤以一定流速自下而上通入固定床中,吸附过程中在出口取样,测样品中的各种阳离子浓度;2.吸附后将去离子水以一定流速自下而上通入固定床中,直至出口溶液电导率与去离子水电导率在一个数量级上;3.脱附过程为将0.5mol·l-1的盐酸以一定流速自下而上通入固定床中,脱附过程中在出口取样,测样品中的各种阳离子浓度;4.脱附后将去离子水以一定流速自下而上通入固定床中,直至出口溶液ph值大于5。固定床规格为φ25mm×50cm,吸附液为某盐湖老卤,各种阳离子浓度见表2,吸附流速为8ml·min-1时,吸附过程锂回收率为83%,锂吸附量为1.2mmol·g-1,对杂质离子基本不吸附;采用0.5mol·l-1的盐酸,洗脱流速为5ml·min-1时,洗脱量与吸附量基本相同,洗脱液中li+浓度最高浓缩7倍,杂质离子浓度显著降低,其吸附穿透曲线和洗脱曲线分别见图7和图8,图7为固定床填充实施例1制备的颗粒锂吸附剂的吸附穿透曲线,图8为固定床填充实施例1制备的颗粒锂吸附剂的洗脱曲线。从图7中可以看出,吸附剂对li+的选择性很好,基本上不吸附其他离子,从图8中可以看出,脱附液中的li+最大浓度超过300mmol·l-1,而mg2+的最大浓度降低到50mmol·l-1以下,达到了镁锂分离的目的。表2盐湖老卤中各种阳离子浓度li+na+k+ca2+mg2+concentration(mmol/l)50.2146.774.93.94700以上显示和描述了本发明的基本原理和主要特征和本发明的优点。本行业的技术人员应该了解,本发明不受上述实施例的限制,上述实施例和说明书中描述的只是说明本发明的原理,在不脱离本发明精神和范围的前提下,本发明还会有各种变化和改进,这些变化和改进都落入要求保护的本发明范围内。本发明要求保护范围由所附的权利要求书及其等效物界定。当前第1页12