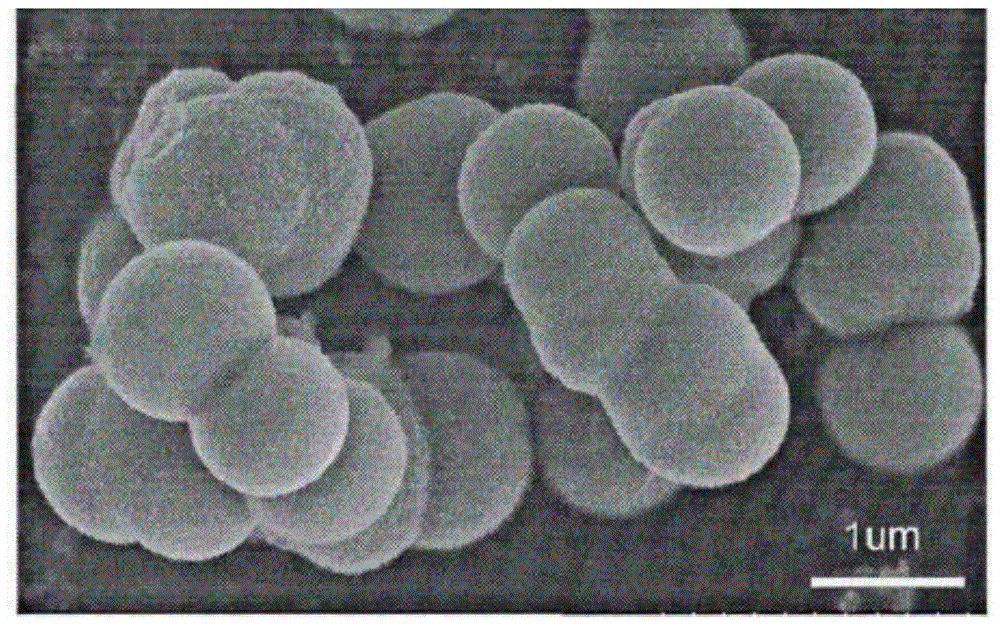
本发明属于超疏水材料
技术领域:
,具体涉及一种自修复微胶囊的制备方法及其在超疏水涂层中的应用。
背景技术:
:超疏水表面(接触角大于150°和滚动角小于10°)性能优异,因此在很多领域,如自清洁、抗腐蚀、防覆冰、减阻、防污等领域具有广泛的应用前景。然而,人造超疏水表面在实际使用过程中耐久性不佳,容易因刮擦、磨损等物理破坏而丧失超疏水性能,大大限制了超疏水材料的应用,此外,涂层在遭受酸碱溶液侵蚀破坏时,也溶液丧失超疏水性能,因此,赋予超疏水材料自修复性能,在材料受损时自发启动修复“程序”、弥补损伤对材料结构和组分造成的不利影响、修复受损的超疏水性能,可有效延长材料的使用寿命,对拓展其应用领域具有十分重要的意义。鉴于以上原因,特提出本发明。技术实现要素:为了解决现有技术存在的以上问题,本发明提供了一种自修复微胶囊的制备方法及其在超疏水涂层中的应用,本发明的自修复微胶囊在遭受酸碱溶液侵蚀破坏时,微胶囊在ph响应范围内及时释放低表面能物质且多孔纳米粒子能够填充裂缝,达到自修复的作用。为了实现上述目的,本发明采用如下技术方案:一种自修复微胶囊的制备方法,包括如下步骤:(1)首先制备多孔纳米粒子;(2)将制备的多孔纳米粒子加入到体积比为2:1的去离子水和乙醇的混合溶液中搅拌溶解,将低表面能物质加入其中搅拌2-3h形成混合溶液a,得到嚢芯;(3)将聚谷氨酸和丙烯酸分别溶于0.1mol/l的磷酸盐缓冲液中,在搅拌的条件下加入引发剂硫酸铵搅拌25-35min,然后加入四甲基乙二胺再搅拌1.8-2.2h形成混合溶液b,将混合溶液a逐滴加入到混合溶液b中并搅拌2-3h,清洗,50-60℃下干燥,研磨,得到所述的自修复微胶囊。进一步的,步骤(1)中所述的多孔纳米粒子为多孔二氧化钛纳米粒子、多孔氧化锌纳米粒子、多孔二氧化硅纳米粒子中的一种或多种。进一步的,所述的多孔二氧化钛纳米粒子按照如下方法制备而成:将乙醇、正钛酸四丁酯、二乙醇胺、冰乙酸按照体积比1:0.5:0.05:0.8依次加入到烧杯搅拌2-3h,形成乳白色悬浮液后陈化12h,倒掉上清液并用丙酮离心清洗3次除去杂质离子,在60℃下干燥12h,研磨得到粉末状二氧化钛,将粉末状二氧化钛在300-400℃下煅烧3-4h,得到多孔二氧化钛纳米粒子;进一步的,所述的多孔氧化锌纳米粒子按照如下方法制备而成:将2.2g乙酸锌溶解于15-25ml乙醇胺中,并加入体积比为1:1-3的去离子水和乙醇的混合溶液,进行搅拌25-35min,然后在170-180℃下恒温反应4-8h,离心清洗至中性,60℃下干燥12h,研磨后在300-400℃下煅烧3-4h,得到多孔氧化锌纳米粒子;进一步的,所述的多孔二氧化硅纳米粒子按照如下方法制备而成:将0.5g聚乙烯吡咯烷酮溶于40ml乙醇和60ml去离子水的混合溶液中,将1g十二胺溶于5ml无水乙醇中加入其中,搅拌50-70min后加入5ml正硅酸乙酯,并在30-50℃下搅拌5-7h形成白色胶体,离心清洗后,在100℃下干燥12h,研磨后,在550-650℃下煅烧3.5-4.5h,得到多孔二氧化硅纳米粒子。进一步的,步骤(2)中按照重量份,多孔纳米粒子15-30重量份,去离子水和乙醇的混合溶液20-30重量份,低表面能物质1-4重量份。进一步的,步骤(2)中所述的低表面能物质为十三氟锌基三乙氧基硅烷、1h,1h,2h,2h-全氟辛基三甲氧基硅烷、十二烷基三甲氧基硅烷、十六烷基三甲氧基硅烷和十八烷基三甲氧基硅烷中的一种或多种。进一步的,步骤(3)中聚谷氨酸、丙烯酸、硫酸铵、四甲基乙二胺的质量比为3:7:0.55:0.043,聚谷氨酸与磷酸盐缓冲液的质量体积比为0.03g:5ml。一种所述的方法制备的自修复微胶囊在超疏水涂层中的应用。进一步的,所述的超疏水涂层ph的敏感范围5-9。也就是在ph为5-9之间,本发明制备的超疏水涂层具有较好的自修复效果,疏水性能和耐久性能持久稳定。进一步的,所述的超疏水涂层按照重量份,包括如下原料:丙烯酸树脂15-20重量份、溶剂15-30重量份、微胶囊5-20重量份、表面活性剂1-3重量份、疏水性物质10-20重量份、消泡剂1-5重量份、流平剂1-5重量份和固化剂2-8重量份。进一步的,所述的溶剂为甲苯、二甲苯、丙酮、聚酰胺、四氢呋喃中的一种或多种,所述的表面活性剂为聚乙烯吡咯烷酮或十六烷基三甲基溴化铵,所述的疏水性物质为石蜡、滑石粉、膨润土、十三氟锌基三乙氧基硅烷、1h,1h,2h,2h-全氟辛基三甲氧基硅烷、十二烷基三甲氧基硅烷、十六烷基三甲氧基硅烷、十八烷基三甲氧基硅烷中的一种或多种,所述的消泡剂为聚二甲基硅氧烷或聚丙乙二醇-环氧烷聚合物,所述的流平剂为聚醚改性聚硅氧烷,所述的固化剂为过氧化苯甲酰、过氧化氢异丙苯、叔丁基过氧化氢、过氧化苯甲酰、过氧化环己酮中的一种或多种。进一步的,超疏水涂层的制备方法包括如下步骤:(a)基材预处理:选择二氧化硅玻璃作为基体,将基体浸在乙醇中超声清洗15-20min,超纯水清洗三次,烘干,用保鲜膜包住备用;(b)超疏水涂层按照如下方法制备而成:按照各原料的重量,将丙烯酸树脂溶于溶剂中,依次加入微胶囊、表面活性剂、疏水性物质、消泡剂、流平剂和固化剂,超声搅拌均匀后涂覆在备用的基材上,在100-110℃下固化。本发明的制备的超疏水性涂层可以用于户外建筑、玻璃、金属及纺织品等领域。与现有技术相比,本发明的有益效果为:(1)本发明提供的自修复微胶囊采用包裹低表面能的多孔纳米粒子为嚢芯,纳米级的多孔粒子结构可以使微胶囊在遭受酸碱破坏时纳米粒子填充裂缝,起到自修复的作用,多孔结构可以使得嚢芯的比表面积增加,表面能增加,进而表面吸附能力更强,可以将低表面能物质更容易的吸附在嚢芯表面,微胶囊在ph为5-9时,具有较好的自修复效果;微胶囊的囊壁选择高分子聚合物,高分子聚合物含有弱酸或弱碱的ph响应特性的基团,如羧基、氨基等,随着ph值,离子强度的变化,弱酸或弱碱基团会发生电离,氢键解离,造成聚合溶胀,通过嚢芯和囊壁的协同作用,当囊壁的结构遭到破坏时,嚢芯的表面仍然具有较高的粗糙度,通过囊壁和嚢芯的协同作用,可以自动修复受损的超疏水表面;(2)本发明的制备的超疏水涂层在ph敏感范围内能够及时的释放低表面能物质以及多孔纳米粒子能够填充裂缝,达到自修复的效果,使得该超疏水性涂层的疏水性能和耐久性能持久稳定,本发明的涂层可以应用在户外建筑、玻璃、金属及纺织品等领域。附图说明为了更清楚地说明本发明实施例或现有技术中的技术方案,下面将对实施例或现有技术描述中所需要使用的附图作简单地介绍,显而易见地,下面描述中的附图仅仅是本发明的一些实施例,对于本领域普通技术人员来讲,在不付出创造性劳动的前提下,还可以根据这些附图获得其他的附图。图1是实施例1制备的多孔二氧化钛纳米粒子的透射电镜图;图2是实施例4制备的超疏水涂层的接触角;图3是实施例4制备的超疏水涂层用ph为5的酸溶液处理后的接触角;图4是实施例4制备的超疏水涂层用ph为9的碱溶液处理后的接触角。具体实施方式为使本发明的目的、技术方案和优点更加清楚,下面将对本发明的技术方案进行详细的描述。显然,所描述的实施例仅仅是本发明一部分实施例,而不是全部的实施例。基于本发明中的实施例,本领域普通技术人员在没有做出创造性劳动的前提下所得到的所有其它实施方式,都属于本发明所保护的范围。实施例1本实施例的一种自修复微胶囊的制备方法,包括如下步骤:(1)首先制备多孔二氧化钛纳米粒子:多孔二氧化钛纳米粒子按照如下方法制备而成:将乙醇、正钛酸四丁酯、二乙醇胺、冰乙酸按照体积比1:0.5:0.05:0.8依次加入到烧杯搅拌2h,形成乳白色悬浮液后陈化12h,倒掉上清液并用丙酮离心清洗3次除去杂质离子,在60℃下干燥12h,研磨得到粉末状二氧化钛,将粉末状二氧化钛在300℃下煅烧3h,得到多孔二氧化钛纳米粒子;(2)将制备的多孔二氧化钛纳米粒子加入到体积比为2:1的去离子水和乙醇的混合溶液中搅拌溶解,将低表面能物质加入其中搅拌2.5h形成混合溶液a,得到嚢芯,其中,多孔二氧化钛纳米粒子15g,去离子水和乙醇的混合溶液20g,低表面能物质1g,低表面能物质为十三氟锌基三乙氧基硅烷;(3)将聚谷氨酸3g和丙烯酸7g分别溶于500ml的0.1mol/l的磷酸盐缓冲液中,在搅拌的条件下加入引发剂硫酸铵0.55g搅拌30min,然后加入四甲基乙二胺0.043g再搅拌2h形成混合溶液b,将混合溶液a逐滴加入到混合溶液b中并搅拌2.5h,用去离子水清洗,55℃下干燥,研磨,得到所述的自修复微胶囊。本实施例制备的多孔二氧化钛纳米粒子的透射电镜图如图1所示。多孔二氧化钛纳米粒子的微孔的孔径随着煅烧温度的升高会减小、比表面积减少、晶粒的结晶度增加,纳米颗粒的平均粒径增大,如图1所示,本实施例制备的多孔二氧化钛纳米粒子,煅烧温度在300℃时形成的微孔孔径较小,孔径在1-2nm,颗粒粒径在10-12nm,孔径变化不明显。本申请人经过大量试验发现当煅烧温度增加到400℃时,形成锐钛矿型的二氧化钛。但是煅烧温度过高时,多孔结构会收缩或坍塌,比表面积极大减小,比表面能下降,进而影响低表面物质的吸附量,涂层的疏水效果变差。实施例2本实施例的一种自修复微胶囊的制备方法,包括如下步骤:(1)首先制备多孔氧化锌纳米粒子:多孔氧化锌纳米粒子按照如下方法制备而成:将2.2g乙酸锌溶解于20ml乙醇胺中,并加入体积比为1:2的去离子水和乙醇的混合溶液10ml,进行搅拌30min,然后在175℃下恒温反应6h,离心清洗至中性,60℃下干燥12h,研磨后在350℃下煅烧3.5h,得到多孔氧化锌纳米粒子;(2)将制备的多孔氧化锌纳米粒子加入到体积比为2:1的去离子水和乙醇的混合溶液中搅拌溶解,将低表面能物质加入其中搅拌2h形成混合溶液a,得到嚢芯,其中,多孔氧化锌纳米粒子22g,去离子水和乙醇的混合溶液25g,低表面能物质2.5g,低表面能物质为十二烷基三甲氧基硅烷;(3)将聚谷氨酸3g和丙烯酸7g分别溶于500ml的0.1mol/l的磷酸盐缓冲液中,在搅拌的条件下加入引发剂硫酸铵0.55g搅拌30min,然后加入四甲基乙二胺0.043g再搅拌1.8h形成混合溶液b,将混合溶液a逐滴加入到混合溶液b中并搅拌2h,用去离子水清洗,50℃下干燥,研磨,得到所述的自修复微胶囊。实施例3本实施例的一种自修复微胶囊的制备方法,包括如下步骤:(1)首先制备多孔二氧化硅纳米粒子:多孔二氧化硅纳米粒子按照如下方法制备而成:将0.5g聚乙烯吡咯烷酮溶于40ml乙醇和60ml去离子水的混合溶液中,将1g十二胺溶于5ml无水乙醇中加入其中,搅拌60min后加入5ml正硅酸乙酯,并在40℃下搅拌6h形成白色胶体,离心清洗后,在100℃下干燥12h,研磨后,在600℃下煅烧4h,得到多孔二氧化硅纳米粒子;(2)将制备的多孔二氧化硅纳米粒子加入到体积比为2:1的去离子水和乙醇的混合溶液中搅拌溶解,将低表面能物质加入其中搅拌2h形成混合溶液a,得到嚢芯,其中,多孔二氧化硅纳米粒子30g,去离子水和乙醇的混合溶液30g,低表面能物质4g,低表面能物质为1h,1h,2h,2h-全氟辛基三甲氧基硅烷;(3)将聚谷氨酸1.5g和丙烯酸3.5g分别溶于250ml的0.1mol/l的磷酸盐缓冲液中,在搅拌的条件下加入引发剂硫酸铵0.275g搅拌30min,然后加入四甲基乙二胺0.0215g再搅拌2.2h形成混合溶液b,将混合溶液a逐滴加入到混合溶液b中并搅拌3h,用去离子水清洗,60℃下干燥,研磨,得到所述的自修复微胶囊。实施例4本实施例为实施例1制备的自修复微胶囊在超疏水涂层中的应用,制备超疏水涂层的原料包括如下:丙烯酸树脂15g、溶剂15g、实施例1制备的微胶囊5g、表面活性剂1g、疏水性物质10g、消泡剂1g、流平剂1g和固化剂2g;其中,溶剂为甲苯,表面活性剂为聚乙烯吡咯烷酮,疏水性物质为十三氟锌基三乙氧基硅烷,消泡剂为聚二甲基硅氧烷,流平剂为聚醚改性聚硅氧烷(生产厂家湖北新四海化工股份有限公司),固化剂为过氧化苯甲酰;超疏水涂层的制备方法包括如下步骤:(a)基材预处理:选择二氧化硅玻璃作为基体,将基体浸在乙醇中超声清洗15min,超纯水清洗三次,烘干,用保鲜膜包住备用;(b)超疏水涂层按照如下方法制备而成:将丙烯酸树脂溶于溶剂中,依次加入微胶囊、表面活性剂、疏水性物质、消泡剂、流平剂和固化剂,超声搅拌均匀后涂覆在备用的基材上,在100℃下固化。实施例5本实施例为实施例2制备的自修复微胶囊在超疏水涂层中的应用,制备超疏水涂层的原料包括如下:丙烯酸树脂17.5g、溶剂22.5g、实施例2制备的微胶囊12.5g、表面活性剂2g、疏水性物质15g、消泡剂3g、流平剂3g和固化剂5g;其中,溶剂为四氢呋喃,表面活性剂为十六烷基三甲基溴化铵,疏水性物质为十二烷基三甲氧基硅烷,消泡剂为聚丙乙二醇-环氧烷聚合物,流平剂为聚醚改性聚硅氧烷(生产厂家湖北新四海化工股份有限公司),固化剂为过氧化氢异丙苯;超疏水涂层的制备方法包括如下步骤:(a)基材预处理:选择二氧化硅玻璃作为基体,将基体浸在乙醇中超声清洗17.5min,超纯水清洗三次,烘干,用保鲜膜包住备用;(b)超疏水涂层按照如下方法制备而成:将丙烯酸树脂溶于溶剂中,依次加入微胶囊、表面活性剂、疏水性物质、消泡剂、流平剂和固化剂,超声搅拌均匀后涂覆在备用的基材上,在105℃下固化。实施例6本实施例为实施例3制备的自修复微胶囊在超疏水涂层中的应用,制备超疏水涂层的原料包括如下:丙烯酸树脂20g、溶剂30g、实施例3制备的微胶囊20g、表面活性剂3g、疏水性物质20g、消泡剂5g、流平剂5g和固化剂8g;其中,溶剂为丙酮,表面活性剂为十六烷基三甲基溴化铵,疏水性物质为1h,1h,2h,2h-全氟辛基三甲氧基硅烷,消泡剂为聚丙乙二醇-环氧烷聚合物,流平剂为聚醚改性聚硅氧烷(生产厂家湖北新四海化工股份有限公司),固化剂为过氧化苯甲酰;超疏水涂层的制备方法包括如下步骤:(a)基材预处理:选择二氧化硅玻璃作为基体,将基体浸在乙醇中超声清洗20min,超纯水清洗三次,烘干,用保鲜膜包住备用;(b)超疏水涂层按照如下方法制备而成:将丙烯酸树脂溶于溶剂中,依次加入微胶囊、表面活性剂、疏水性物质、消泡剂、流平剂和固化剂,超声搅拌均匀后涂覆在备用的基材上,在110℃下固化。对比例1本对比例制备的超疏水涂层与实施例4相同,不同之处在于,多孔二氧化钛纳米粒子在制备过程中不采用煅烧处理,直接研磨粉碎即可。试验例1测试实施例4的方法制备的超疏水性涂层在酸碱条件下的自修复性能。疏水性测试方法:用接触角测试仪测量水滴在膜层表面接触角,接触角值由5个随机位置测量取平均值后得到,静态接触角采用躺滴法(sessiledrop)测量,超疏水表面(即静态接触角大于150°的表面)测量时,测量时统一使用5μl水滴。1、按照上述疏水性测试方法,测试实施例4制备的超疏水涂层的接触角为159.12°,接触角如图2所示。2、用盐酸分别配置ph为4、5和6的酸溶液,用氢氧化钠配置ph为8、9和10的碱溶液。按照实施例4的方法分别制备6组试样涂层进行测试不同酸碱性下超疏水性涂层的自修复性能,测试方法如下:分别将试样涂层浸入不同ph的溶液中24h,然后将涂层移出并除去表面的酸碱溶液,测定接触角,然后将涂层置于80℃环境修复2h,测定涂层的接触角,结果见表1。表1处理的溶液ph酸或碱溶液处理后接触角(°)修复后的接触角(°)4132.14138.955153.26158.166154.49158.878153.62158.719154.03158.8310134.62139.82从表1可以看出,在ph为5-9时,涂层的修复性能较好,ph小于5或大于9时,修复效果较差,说明本发明的超疏水涂层在ph为5-9时具有较好的自修复效果,当本发明的超疏水涂层遭受到ph为5-9的溶液破坏时,可以保持稳定的疏水性能。其中,ph为5的酸溶液处理后超疏水涂层的接触角如图3所示,ph为9的碱溶液处理后的超疏水涂层的接触角如图4所示。本发明人也对其他实施例制备的超疏水涂层做了上述试验,结果基本一致,由于篇幅有限,不再一一列举。试验例2本试验例对对比例1制备的超疏水涂层测试在酸碱条件下的自修复性能,测试方法与试验例1相同,测定结果见表2。1、对比例1制备的超疏水涂层的接触角为153.12°。表2处理的溶液ph酸或碱溶液处理后接触角(°)修复后的接触角(°)4123.45127.565146.32148.286147.56147.988145.85146.139146.38148.2310114.62123.87从表1和2中可以看出,不采用煅烧处理的纳米二氧化钛的疏水涂层自修复性能比采用煅烧处理的疏水涂层的自修复效果差,且接触角小,即疏水性也降低,这是由于煅烧处理增加了多孔纳米粒子表面的孔洞增加了表面积,低表面能物质的吸附性能更强,自修复效果更好,疏水性能更好。以上所述,仅为本发明的具体实施方式,但本发明的保护范围并不局限于此,任何熟悉本
技术领域:
的技术人员在本发明揭露的技术范围内,可轻易想到变化或替换,都应涵盖在本发明的保护范围之内。因此,本发明的保护范围应以所述权利要求的保护范围为准。当前第1页12