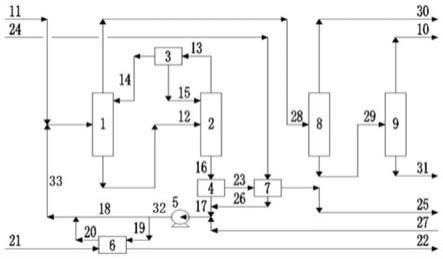
chppo双塔精馏分离系统及分离方法
技术领域
1.本发明涉及一种环氧化反应产物分离系统及分离方法,尤其涉及一种生产能力为5~80万吨/年的chppo环氧化反应产物双塔精馏分离系统及分离方法。
背景技术:2.环氧丙烷po是除聚丙烯和丙烯腈外的第三大丙烯衍生物,是一种重要的基本有机化工合成原料。在全球石油化工市场范围内,环氧丙烷最大工业用途是制备聚醚多元醇,还可用于丙二醇、第四代洗涤剂、非离子表面活性剂、油田破乳剂、农药乳化剂及润湿剂等。环氧丙烷的衍生物广泛用于汽车、船舶、建筑、食品、烟草、医药及化妆品等行业,能够进一步生产的下游产品有近百种,是精细化工产品的重要原料之一。
3.异丙苯氧化制备环氧丙烷chppo法是在绝热固定床反应器中,采用超疏水性含钛二氧化硅多孔材料作催化剂,在全液相条件下,过氧化氢异丙苯chp把丙烯选择氧化为环氧丙烷po产品,同时过氧化氢异丙苯还有一部分转化为α,α
‑
二甲基苄醇dmba副产品。环氧化反应产物经回收丙烯、分离副产物后得到的粗环氧丙烷,但是仍含有有机酸类、醇类缩合物、并异丙苯等杂质。这些杂质产物除了增加原料消耗外,还会引起设备腐蚀,因此在环氧丙烷分离、提纯及精制过程中,这些杂质产物均需加以脱除。
4.专利申请号201510510737.2公开了环氧丙烷溶液进入环氧丙烷分离塔进行分离,分离后含有少量环氧丙烷的水溶液进入环氧丙烷再分离塔进行再分离。该发明仅仅将环氧化反应产物进行分离得到粗环氧丙烷产品,工业化实施性差。
技术实现要素:5.发明目的:本发明的第一目的是提供一种能够降低环氧丙烷分离塔塔釜温度及异丙苯损耗率的chppo双塔精馏分离系统,本发明的第二目的是提供利用该系统进行chppo环氧化反应产物双塔精馏分离的方法。
6.技术方案:本发明的chppo双塔精馏分离系统,包括精馏塔、回收塔、油水分层罐、油水分离罐、回流泵、水洗器、脱轻塔和脱重塔;其中,精馏塔分别与回收塔、回流泵和萃取器相连;油水分层罐分别与精馏塔和回收塔相连;脱轻塔分别与精馏塔和脱重塔相连;油水分离罐分别与回收塔、水洗器和回流泵相连;萃取器与回流泵相连。
7.本发明的chppo双塔精馏分离方法,包括以下步骤:
8.a、环氧化反应产物进入精馏塔,分离得到精馏塔釜料和精馏塔顶料;精馏塔顶料进入脱轻塔,分离得到轻组分和脱轻塔釜料,脱轻塔釜料进入脱重塔,分离得到粗po产品和重组分分别送出系统外;
9.b、精馏塔釜料进入回收塔,分离得到回收塔顶料和回收塔釜料;回收塔顶料进入油水分层罐,分离得到分层罐油相和分层罐水相;分层罐油相进入精馏塔,分层罐水相返回回收塔;
10.c、回收塔釜料进入油水分离罐,分离得到分离罐油相和分离罐水相;分离罐油相
进入水洗器,用水水洗得到含水苄醇和水洗水,含水苄醇送出系统外;
11.d、分离罐水相、水洗水和碱液混合后进入回流泵,得到混合水相;混合水相中一部分平衡水进入萃取器,用异丙苯萃取得到萃取相和废水,废水送出系统外;
12.e、萃取相与混合水相中另一部分混合液混合为混合返回液;混合返回液与环氧化反应产物混合进入精馏塔。
13.优选的,所述分离方法工艺操作参数如下:精馏塔的操作压力0.12~0.24mpaa,塔顶操作温度45~75℃,塔釜操作温度80~110℃;回收塔的操作压力0.08~0.20mpaa,塔顶操作温度45~75℃,塔釜操作温度80~110℃;脱轻塔的操作压力0.26~0.39mpaa,塔顶操作温度39~79℃,塔釜操作温度51~91℃;脱重塔的操作压力0.14~0.27mpaa,塔顶操作温度35~75℃,塔釜操作温度63~103℃。
14.更优选的,所述分离方法工艺操作参数如下:精馏塔的操作压力0.14~0.22mpaa,塔顶操作温度50~70℃,塔釜操作温度85~105℃;回收塔的操作压力0.10~0.18mpaa,塔顶操作温度50~70℃,塔釜操作温度85~105℃;脱轻塔的操作压力0.28~0.37mpaa,塔顶操作温度44~74℃,塔釜操作温度56~86℃;脱重塔的操作压力0.16~0.25mpaa,塔顶操作温度40~70℃,塔釜操作温度68~98℃。
15.最优选的,所述分离方法工艺操作参数如下:精馏塔的操作压力0.16~0.20mpaa,塔顶操作温度55~65℃,塔釜操作温度90~100℃;回收塔的操作压力0.12~0.16mpaa,塔顶操作温度55~65℃,塔釜操作温度90~100℃;脱轻塔的操作压力0.30~0.35mpaa,塔顶操作温度49~69℃,塔釜操作温度61~81℃;脱重塔的操作压力0.18~0.23mpaa,塔顶操作温度45~65℃,塔釜操作温度73~93℃。
16.分离方法步骤a中,所述精馏塔顶料不含水,以强化精馏塔的分离效率,提高粗po回收率,使粗po回收率提高到99.95wt%以上。
17.分离方法步骤b中,所述回收塔釜料含水,以降低回收塔塔釜温度,使回收塔塔釜温度降低到110℃以下。
18.分离方法步骤c中,所述水为一级脱盐水、二级脱盐水、蒸馏水、精制水、净化水、纯水中的一种。
19.分离方法步骤d中,所述碱液为naoh、koh、ca(oh)2、nahco3、na2co3、khco3、k2co3水溶液中的一种或一种以上混合水溶液。
20.分离方法步骤d中,所述碱液的浓度为15~35wt%。
21.发明人研究发现,现有技术中chppo装置在环氧丙烷分离、提纯及精制过程中,虽然环氧丙烷化学稳定性相对比较好,粗环氧丙烷分离塔塔釜温度、物料在塔釜的停留时间等因素对环氧丙烷含量基本没有影响,但是异丙苯具有化学热敏性,当粗环氧丙烷分离塔塔釜温度升高到150~210℃时,塔釜物料中的并异丙苯含量随着粗环氧丙烷分离塔塔釜温度升高而大幅度增加,表明异丙苯在粗环氧丙烷分离塔物料分离过程中发生化学热敏反应生成并异丙苯,从而造成异丙苯大量损失。同时为了保证粗环氧丙烷分离塔有足够的上升气流,需要高能位的蒸汽加热粗环氧丙烷分离塔塔釜,存在粗环氧丙烷分离塔塔釜温度高、异丙苯损失大、粗环氧丙烷回收率低、运行能耗高的问题。因此,本发明拟对chppo环氧化反应产物分离系统及工艺流程进行优化,解决现有技术存在的问题。
22.有益效果:与现有技术相比,本发明具有如下显著优点:将粗po分离塔分为精馏塔
和回收塔双塔进行精馏分离,在精馏塔与回收塔之间设置油水分层罐,将分层罐油相送入精馏塔,分层罐水相作为回流液返回回收塔,并控制精馏塔顶物料不含水,强化精馏塔的分离效率,提高粗po回收率,使粗po回收率提高到99.95wt%以上;通过水洗器加入水,控制回收塔釜料含水,以降低回收塔塔釜温度,使回收塔塔釜温度从现有技术150~210℃降低到110℃以下,回收塔塔釜异丙苯损耗率从现有技术0.2006~1.0177wt%减少到0.0019~0.0024wt%,而且可使用低能位蒸汽加热回收塔塔釜以降低运行的能耗。
附图说明
23.图1为本发明的工艺流程图。
具体实施方式
24.下面结合附图对本发明的技术方案作进一步说明。
25.实施例1
26.以公称能力为5万吨/年chppo商业化工业生产装置为例,采用本发明所述chppo双塔精馏分离系统及分离方法,在粗po精馏分离工艺流程中,通过引入水24,降低回收塔2塔釜的操作温度以防止发生异丙苯生成并异丙苯的不利反应,从而减少异丙苯的损耗率。其中,水24选用二级脱盐水,精馏塔1选用粗po精馏塔,回收塔2采用粗po回收塔。所述水24也可为一级脱盐水、蒸馏水、精制水、净化水、纯水中的任意一种。
27.如图1所示,本实施例的工艺流程如下:来自系统外已经脱除丙烯含异丙苯、po和α,α
‑
二甲基苄醇的环氧化反应产物11进入粗po精馏塔进行精馏分离,塔釜含异丙苯、含水的α,α
‑
二甲基苄醇和少量po的精馏塔釜料12进入回收塔2中。塔顶不含水、含轻组分和重组分的精馏塔顶料28进入脱轻塔8中进行精馏分离,脱轻塔8塔顶流出轻组分30送出系统外,塔釜流出的脱轻塔釜料29进入脱重塔9中进行精馏分离。脱重塔9塔釜流出重组分31送出系统外,脱重塔9塔顶流出粗po产品10送去系统外的精制单元。精馏塔釜料12进入回收塔2进行精馏分离,回收塔顶料13进入油水分层罐3进行油水分离,得到分层罐油相14送入粗po精馏塔作为回流液继续精馏分离,分层罐水相15返回回收塔2。回收塔釜料16进入油水分离罐4进行油水分离,得到分离罐油相23进入水洗器7中,通过系统外加入二级脱盐水进行水洗处理,水洗后的含水苄醇25送去系统外的氢解单元。油水分离罐4分离得到分离罐水相17、水洗器7水洗后的水洗水26和来自系统外的碱液27混合进行碱洗处理,然后经回流泵5加压成为混合水相32。混合水相32中的一部分作为平衡水19进入萃取器6,用系统外加入的异丙苯21萃取,含少量α,α
‑
二甲基苄醇和po的萃取相20与混合水相32中另一部分混合液18混合成为混合返回液33,返回液33与环氧化反应产物11混合进入粗po精馏塔。萃取器6流出的萃余相作为废水22送出系统外进行后续的环保处理。
28.本实施例工艺操作参数如下:粗po精馏塔的操作压力0.15mpaa,塔顶操作温度53℃,塔釜操作温度87℃;粗po回收塔的操作压力0.11mpaa,塔顶操作温度54℃,塔釜操作温度109℃;脱轻塔8的操作压力0.29mpaa,塔顶操作温度47℃,塔釜操作温度58℃;脱重塔9的操作压力0.17mpaa,塔顶操作温度43℃,塔釜操作温度70℃;碱液27为20wt%的naoh水溶液。由此粗po回收塔塔釜操作温度从现有技术182℃降低到本实施例109℃,粗po回收塔2塔釜异丙苯损耗率从现有技术0.2968wt%减少到本实施例0.0023wt%,粗po回收率从现有技
术99.92wt%提高到本实施例99.96wt%,具有粗po塔塔釜温度低、异丙苯损失小、粗po回收率高、工业化实施性强的特点,取得了较好的技术效果。
29.实施例2
30.同实施例1,仅仅公称能力和工艺操作参数改变,公称能力改为10万吨/年chppo商业化工业生产装置,本实施例的工艺参数修改如下:粗po精馏塔的操作压力0.21mpaa,塔顶操作温度63℃,塔釜操作温度98℃;粗po回收塔的操作压力0.17mpaa,塔顶操作温度64℃,塔釜操作温度109℃;脱轻塔8的操作压力0.35mpaa,塔顶操作温度57℃,塔釜操作温度69℃;脱重塔9的操作压力0.23mpaa,塔顶操作温度53℃,塔釜操作温度81℃;碱液27为20wt%的koh水溶液。由此粗po回收塔塔釜操作温度从现有技术198℃降低到本实施例109℃,粗po回收塔塔釜异丙苯损耗率从现有技术0.6360wt%减少到本实施例0.0023wt%,粗po回收率从现有技术99.90wt%提高到本实施例99.96wt%,具有粗po塔塔釜温度低、异丙苯损失小、粗po回收率高、工业化实施性强的特点,取得了较好的技术效果。
31.实施例3
32.同实施例1,仅仅公称能力和工艺操作参数改变,公称能力改为30万吨/年chppo商业化工业生产装置,本实施例的工艺参数修改如下:粗po精馏塔的操作压力0.12mpaa,塔顶操作温度45℃,塔釜操作温度80℃;粗po回收塔的操作压力0.08mpaa,塔顶操作温度45℃,塔釜操作温度80℃;脱轻塔8的操作压力0.26mpaa,塔顶操作温度39℃,塔釜操作温度51℃;脱重塔9的操作压力0.14mpaa,塔顶操作温度35℃,塔釜操作温度63℃;碱液27为15wt%的naoh水溶液。由此粗po回收塔塔釜操作温度从现有技术150℃降低到本实施例100℃,粗po回收塔2塔釜异丙苯损耗率从现有技术0.2006wt%减少到本实施例0.0019wt%,粗po回收率从现有技术99.94wt%提高到本实施例99.97wt%,具有粗po塔塔釜温度低、异丙苯损失小、粗po回收率高、工业化实施性强的特点,取得了较好的技术效果。
33.实施例4
34.同实施例1,仅仅公称能力和工艺操作参数改变,公称能力改为30万吨/年chppo商业化工业生产装置,本实施例的工艺参数修改如下:粗po精馏塔的操作压力0.21mpaa,塔顶操作温度63℃,塔釜操作温度98℃;粗po回收塔的操作压力0.18mpaa,塔顶操作温度67℃,塔釜操作温度108℃;脱轻塔8的操作压力0.35mpaa,塔顶操作温度57℃,塔釜操作温度69℃;脱重塔9的操作压力0.23mpaa,塔顶操作温度53℃,塔釜操作温度81℃;碱液27为10wt%的naoh与15wt%的na2co3的混合水溶液。由此粗po回收塔塔釜操作温度从现有技术202℃降低到本实施例108℃,粗po回收塔塔釜异丙苯损耗率从现有技术0.7511wt%减少到本实施例的0.0022wt%,粗po回收率从现有技术为99.87wt%提高到本实施例99.96wt%,具有粗po塔塔釜温度低、异丙苯损失小、粗po回收率高、工业化实施性强的特点,取得了较好的技术效果。
35.实施例5
36.同实施例1,仅仅公称能力和工艺操作参数改变,公称能力改为30万吨/年chppo商业化工业生产装置,本实施例的工艺参数修改如下:粗po精馏塔的操作压力0.24mpaa,塔顶操作温度75℃,塔釜操作温度110℃;粗po回收塔的操作压力0.20mpaa,塔顶操作温度75℃,塔釜操作温度110℃;脱轻塔8的操作压力0.39mpaa,塔顶操作温度79℃,塔釜操作温度91℃;脱重塔9的操作压力0.27mpaa,塔顶操作温度75℃,塔釜操作温度103℃;碱液27为
35wt%的naoh水溶液。由此粗po回收塔塔釜操作温度从现有技术210℃降低到本实施例110℃,粗po回收塔塔釜异丙苯损耗率从现有技术1.0177wt%减少到本实施例0.0024wt%,粗po回收率从现有技术99.74wt%提高到本实施例99.95wt%,具有粗po塔塔釜温度低、异丙苯损失小、粗po回收率高、工业化实施性强的特点,取得了较好的技术效果。
37.实施例6
38.同实施例1,仅仅公称能力和工艺操作参数改变,公称能力改为30万吨/年chppo商业化工业生产装置,本实施例的工艺参数修改如下:粗po精馏塔的操作压力0.21mpaa,塔顶操作温度63℃,塔釜操作温度98℃;粗po回收塔的操作压力0.19mpaa,塔顶操作温度71℃,塔釜操作温度106℃;脱轻塔8的操作压力0.35mpaa,塔顶操作温度57℃,塔釜操作温度69℃;脱重塔9的操作压力0.23mpaa,塔顶操作温度53℃,塔釜操作温度81℃;碱液27为10wt%的naoh与15wt%的k2co3混合水溶液。由此粗po回收塔塔釜操作温度从现有技术206℃降低到本实施例106℃,粗po回收塔塔釜异丙苯损耗率从现有技术0.8783wt%减少到本实施例0.0021wt%,粗po回收率从现有技术99.82wt%提高到本实施例99.96wt%,具有粗po塔塔釜温度低、异丙苯损失小、粗po回收率高、工业化实施性强的特点,取得了较好的技术效果。
39.表1实施例1~6chppo装置详细数据汇总表
[0040][0041][0042]
对比例1~6
[0043]
设置对比例1~6,公称能力30万吨/年chppo商业化工业生产装置,粗po塔塔釜操作温度为150~210℃,工艺步骤和其它工艺参数同实施例3,由此粗po塔塔釜异丙苯损耗率为0.2006~1.0177wt%,粗po回收率为99.74~99.94wt%,见表2。
[0044]
表2改变粗po塔釜温度的异丙苯损耗率和粗po回收率表
[0045][0046]
对比例7~12
[0047]
设置对比例7~12,公称能力为30万吨/年chppo商业化工业生产装置,粗po塔操作压力为0.08~0.20mpaa,工艺步骤和其它工艺参数同实施例3,由此粗po塔塔釜异丙苯损耗率为0.2006~1.0177wt%,粗po回收率为99.74~99.94wt%,见表3。
[0048]
表3改变粗po塔压力的异丙苯损耗率和粗po回收率表
[0049][0050]
对比例13~18
[0051]
设置对比例13~18,在公称能力为5~80万吨/年chppo商业化工业生产装置中,粗po塔塔釜操作温度为206℃,工艺步骤和其他工艺参数同实施例3,由此粗po塔塔釜异丙苯损耗率为0.8778~0.8784wt%,粗po回收率为99.76~99.83wt%,见表4。
[0052]
表4改变chppo工业生产装置公称能力的异丙苯损耗率和粗po回收率表
[0053]