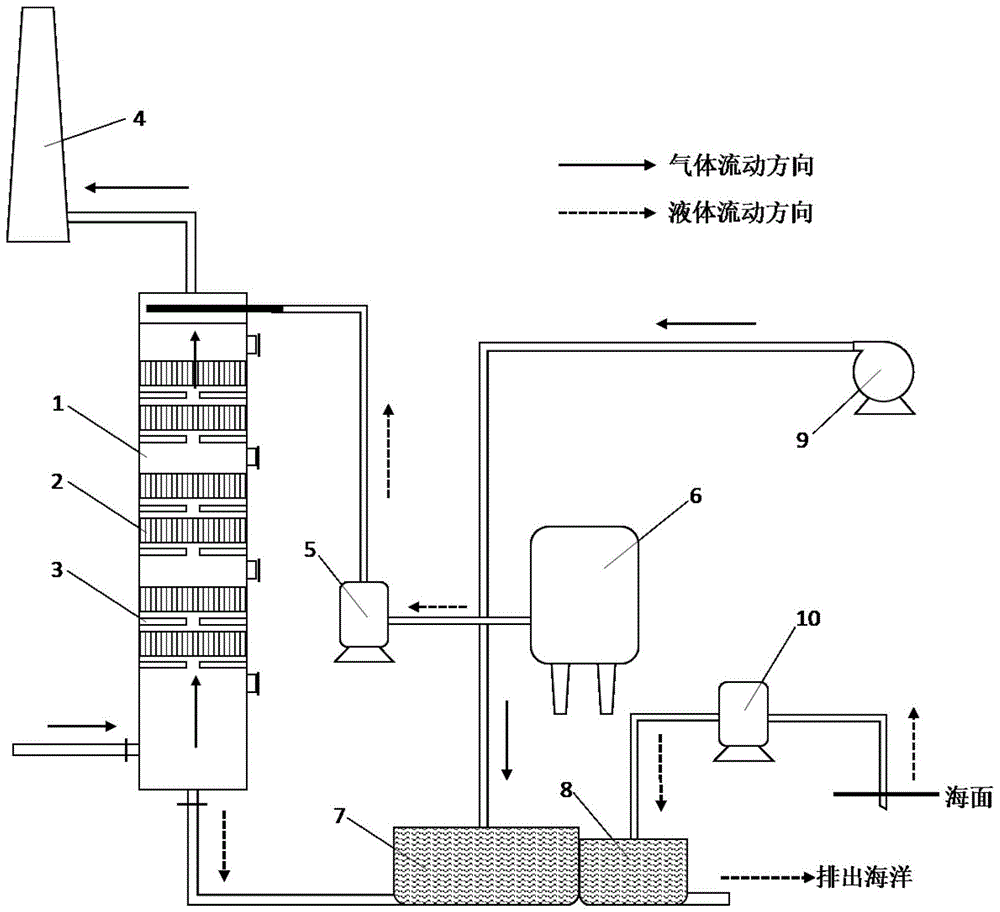
本发明涉及一种烟气脱硫脱硝工艺,特别涉及一种船舶烟气光催化氧化脱硫和还原脱硝工艺,属于环境保护/废气处理
技术领域:
。
背景技术:
:现代社会经济发展迅速,各国之间的贸易联系日益密切,海上运输方便高效的优点使其成为国际交通中的主要方式。与机动车烟气相比,船舶的燃料主要是重柴油,所以船舶烟气中含有较高浓度的nox和so2,如不经任何处理,烟气经大气循环和水循环的迁移、转化、沉积,将导致海洋酸化和陆地生态系统衰退,对全球气候变化造成严重影响。船舶燃用低品质重油所释放的烟气污染物成分复杂,主要有nox、so2、co、co2、hc(碳氢化合物)、pm(颗粒物)等,其中nox和so2所占的比例很高,是主要污染物。2018年中国船舶排放的so2和nox分别是58.8万吨、151.1万吨,其中nox占非道路移动源排放的29.2%。2019年船舶排放nox为139.1万吨,占非道路移动源排放的28.2%。而nox和so2的排放严重威胁着海洋生态环境和沿海居民的健康。国际海事组织(imo)将nox和so2列为首要控制的船舶烟气污染物。烟气中的nox主要包括no、no2、n2o、n2o5等,其中no占90%以上。no在空气中容易氧化为no2,会对人体的肺和心脏产生毒害作用,也会形成光化学烟雾,对人的眼睛和呼吸道有毒害作用,甚至致癌。nox还会对臭氧层产生破坏作用,nox与o3反应,从而使o3变成o2,使之失去对紫外光辐射的屏蔽作用。同时也是形成酸雨的主要污染物。sox中95%为so2,so3仅占5%。so2对人体健康有直接的损害,造成呼吸道疾病;高浓度时,还侵害中枢神经系统和心脏等,使人和动物昏迷,直至死亡。sox还是酸雨的主要成因,严重破坏生态环境。所以,控制船舶烟气中的nox、sox排放的关键是对no和so2进行脱除。国内对船舶废气脱硫脱硝、脱硫脱硝后的废水、冷却水和清洗废水的ph、硝酸盐、pahs、温度等都规定了执行标准,并且划定了船舶排放控制区范围,明确了燃油硫含量、颗粒物和氮氧化物排放控制要求,船舶靠港使用岸电要求等。由于no3-不是海洋固有离子,imo规定,洗涤水系统应防止硝酸盐的排放超过清除废气中12%的nox所对应的硝酸盐量或60mg/l。因此针对船舶动力废气净化研究,必须脱除船舶烟气中的主要污染物so2和nox,并且产生的废水中no3-、ph等也要符合排放要求。中国专利申请cn107456856a公开了一种基于海水法船舶尾气脱硫脱硝一体化去除装置及方法。其利用海水中的氯离子和碳酸根离子对氧化性试剂过硫酸钠进行活化,并利用尾气余热强化海水过硫酸钠溶液的活化,活化后的过硫酸钠溶液与尿素溶液混合,在气旋式洗涤塔内与烟气进行混合接触,利用湿法氧化技术和还原技术相结合方式达到同时脱硫脱硝的目的。最终的脱除产物为硫酸盐和氮气。但该方法采用海水和烟气余热活化过硫酸钠,活化效率不高,会影响脱硝效果。活化后产生的氧化性自由基氧化能力很强,不仅能将nox氧化生成亚硝酸根,也能进一步氧化生成硝酸根,而尿素无法还原硝酸根,可能不能满足硝酸根的排放要求。同时采用氧化剂过硫酸钠和还原剂尿素,不仅流程复杂,成本较高,且活化后的过硫酸钠溶液会与尿素溶液混合后反应,造成极大的浪费。中国专利申请cn105536486a公开了一种船舶尾气脱硝工艺及系统、脱硫脱硝一体化工艺及系统。当船舶使用低硫油时,采用船舶尾气脱硝工艺,降温后的船舶尾气进入吸附塔,使nox吸附在吸附剂上,而后升温脱附nox进入脉冲等离子体反应器处理,nox部分分解成n2,部分被氧化为no2;最后通过na2so3溶液喷淋吸收还原。而当船舶使用硫含量较高时,采用船舶尾气脱硫脱硝一体化工艺,尾气降温后先经过洗涤水洗涤和钠碱吸收so2后,产生的na2so3溶液用于后续脱硝。但采用低温等离子法nox的脱除率较低,设备需要使用高压高频电源来产生活性物质,能耗较高,危险性高,且设备周围会产生强电磁场,对船舶上的电器设备产生干扰,严重影响船舶安全运行。中国专利申请cn107551813a公开了一种船舶脱硫脱硝一体化工艺及其装置。在脱硫吸收塔内喷淋氢氧化钠溶液除去焦油并吸收烟气中的so2,生成亚硫酸钠溶液储存;而后烟气进入脱硝干燥氧化塔,经过干燥氧化后,no在脱硝催化剂的作用下发生氧化反应生成no2;最后进入脱硝吸收塔,no、no2被氢氧化钠和脱硫生成的亚硫酸钠还原吸收,生成n2及硝酸盐。但需要利用脱硫生成的亚硫酸钠脱硝,不仅工艺流程复杂,而且在烟气硫含量较低时亚硫酸钠浓度低还原效果不好,使硝酸盐不能满足排放要求。氮氧化物含量较高时催化剂氧化脱除效果差,不能达到烟气排放标准。技术实现要素:针对以上问题,本发明的目的是提供一种高效协同、一体化的舰船烟气光催化氧化脱硫和还原脱硝工艺,能够在同一塔中高效地氧化脱硫和还原脱硝,具有操作简单,设备占地面积小,投资少,操作弹性大,运行成本低,无二次污染,产生的na2so4和n2能直接排放到海洋和大气中的优点。本发明的原理如下:在规整陶瓷光催化剂填料和真空紫外(vuv)灯的作用下,船舶烟气中的部分so2和no被氧化成so3和no2;同时,利用高级还原技术vuv/nahso3体系产生的还原自由基,将nox还原为n2,而nahso3溶液被氧化成无污染的na2so4溶液;部分so2被海水吸收也能补充溶液中的hso3-,保持较高的还原脱硝效果;洗涤废海水通过曝气将少量未反应完的hso3-氧化成so42-。本发明实现了在同一塔中氧化脱硫和还原脱硝,并且由于na+离子和so42-离子都是海洋可接纳的离子,极大简化船舶脱硫脱硝装置以及洗涤废水的处理难度,在不同船舶烟气净化中具有可推广性。同时,nahso3还是陆地碱法脱硫的副产物,能起到“以废治废”的效果。一种舰船烟气光催化氧化脱硫和还原脱硝工艺,其特征在于,包括以下步骤:(1)船舶烟气经过除尘控温后,从底部进入内装真空紫外灯和规整陶瓷光催化剂填料的光催化脱硫脱硝塔,自下而上通过负载有光催化剂的填料床层;(2)光催化剂被高能紫外线激发,通过光催化氧化和真空紫外辐射产生的大量o3和活性自由基,将烟气中的大部分so2氧化成so3,部分no氧化成no2;(3)从塔顶喷淋配制好的nahso3海水喷淋液,与经步骤(2)处理后的烟气逆向接触,通过光催化剂/vuv/nahso3体系,将nox还原成n2和nh4+,nahso3溶液被氧化成na2so4溶液;同时,通过海水吸收脱除烟气中的so2、so3,补充溶液中的hso3-;(4)经光催化脱硫脱硝塔完成氧化脱硫和还原脱硝一体化处理后的洁净烟气由塔顶烟气出口经烟囱排放;(5)反应后的海水溶液从塔底排放进入曝气池,在曝气条件下将少量未反应完的hso3-氧化成so42-,然后与大量新鲜海水混合后,使ph值大于等于6.8,no3-小于等于60mg/l,达到排放标准,直接排入大海。其进一步的特征在于,所述步骤(1)的光催化剂的活性组分是ag/tio2-x,通过在n2氛围下煅烧tio2前驱体制备tio2-x,然后采用光还原agno3法在tio2-x表面负载银制备ag/tio2-x,所用溶剂为异丙醇溶液,光催化剂中ag的含量是0.5-3.5%。进一步的,所述步骤(1)的光催化剂通过硅溶胶和硅烷偶联剂负载于规整陶瓷上。进一步的,所述步骤(1)光催化脱硫脱硝塔内的规整陶瓷光催化剂填料与真空紫外灯通过筛板交替放置。进一步的,所述步骤(1)的真空紫外灯,其功率为100~500w,波长为λ≤200nm,真空紫外线有利于激发光催化剂产生氧化活性自由基,催化氧化烟气中的so2和nox,且真空紫外线能活化hso3-产生还原性自由基还原烟气中的nox。进一步的,所述步骤(2)和(3)的光催化的反应温度为50~80℃,烟气空速范围为1500~6500h-1,烟气中氧气体积分数为2~8%,所述nahso3海水喷淋液的浓度为0.01~0.04mol/l,液气比为2~8l/m3。所述的反应过程如下:(1)光催化技术ag/tio2-x+hv→h++e-h2o→oh-+h+oh-+h+→·ohso2+2·oh→so3+h2ono+2·oh→no2+h2oh++e-→h·2no+4h·→n2+2h2ono+5h·+h+→nh4++h2o(2)真空紫外辐照:o2+hv(λ≤200nm)→2o·o·+o2→o32so2+o3→2so3+o22no+o3→2no2+o2(3)高级还原技术:hso3-+hv→h·+so3·-2no+4h·→n2+2h2ono+5h·+h+→nh4++h2o4so3·-+o2+h2o→4hso4-no+no2+3nahso3→3nahso4+2n22no2+4nahso3→4nahso4+n2(4)其他(吸收、曝气氧化)so2+h2o→h2so3→h++hso3-so3+h2o→h2so4→2h++so42-2nahso3+o2→2nahso42nahso4→na2so4+h2so4。与现有技术相比,本发明具有以下优点:(1)本发明结合光催化技术、真空紫外辐射和vuv/nahso3高级还原技术,高效协同,实现同时高效脱除烟气中的so2和nox。so2经光催化氧化、真空紫外辐射氧化为so3,被海水吸收形成用于还原脱硝的nahso3;nox经光催化还原、高级还原技术还原为n2和nh4+去除,n2还原率60~75%。so2脱除率最高达100%,nox脱除率最高达99.8%,脱硫脱硝的产物主要为so42-和n2,ph值和no3-浓度达到排放标准。(2)本发明可简化现有的船舶脱硫脱硝装置。目前,舰船烟气的脱硫脱硝处理需要scr脱硝装置和脱硫塔串联工作,存在工艺复杂,初始投资成本高、装置尺寸大、反应中间产物排放超标和scr催化剂容易中毒失效等问题。本发明能避免上述缺点,实现在同一塔中高效地氧化脱硫还原脱硝,操作简单,设备占地面积小,投资少,操作弹性大,运行成本低,无二次污染,产生的na2so4和n2能直接排放到海洋和大气中。附图说明图1是本发明的工艺流程图。图中,1.光催化脱硫脱硝塔;2.光催化填料床层;3.真空紫外灯;4.烟囱;5.进料泵;6.nahso3海水储液罐;7.曝气池;8.混合池;9.曝气鼓风机;10.混合池海水稀释泵。图2是实施例1中制备的光催化剂的sem图。图3是实施例1中制备的光催化剂和光催化剂/规整陶瓷的xrd图。具体实施方式下面结合附图并通过具体实施例来详细说明本发明。实施例1:本实施例的流程图如图1所示,首先烟气在除尘控温后从光催化脱硫脱硝塔1的塔底进入塔内,烟气自下而上通过负载有光催化剂的光催化填料床层2;光催化剂被真空紫外灯3释放的高能紫外线激发,通过光催化氧化和真空紫外辐射产生的大量o3和活性自由基,将烟气中的大部分so2氧化成so3,部分no氧化成no2;同时进料泵5从nahso3海水储液罐6中抽取配制好的nahso3海水溶液,从塔顶喷淋,与氧化处理后的烟气逆向接触,通过光催化剂/vuv/nahso3体系,将nox还原成n2和nh4+,nahso3溶液被氧化成na2so4溶液;同时,通过海水吸收脱除烟气中的so2、so3,补充溶液中的hso3-;经光催化脱硫脱硝塔1完成氧化脱硫和还原脱硝一体化处理后的洁净烟气由塔顶烟气出口经烟囱4排放;反应后的海水溶液从塔底排放进入曝气池7,通过曝气鼓风机9在曝气条件下将少量未反应完的hso3-氧化成so42-,然后进入混合池8,与通过海水稀释泵10吸取的大量新鲜海水混合后,使ph值大于等于6.8,no3-小于等于60mg/l,达到排放标准,直接排入大海。本实施例选用的光催化剂是ag/tio2-x复合二元光催化剂,以钛酸四正丁酯为原料,通过溶胶凝胶法制备凝胶,干燥研磨,在n2氛围下煅烧得到tio2-x。以agno3为前驱体,通过氙灯光还原合成ag/tio2-x光催化剂。其sem图如图2,从图中可以看出ag纳米颗粒已成功沉积到tio2-x表面。本实施例选用的载体为规整陶瓷,将制备的光催化剂通过硅溶胶和硅烷偶联剂负载于规整陶瓷上,制备成光催化填料床层2。所制备光催化剂和光催化剂/规整陶瓷的xrd如图3所示,从图中可以看出ag/tio2-x已成功负载到规整陶瓷表面。本实施例以n2为载气,烟气中so2初始浓度为2056mg/m3,no初始浓度为1023mg/m3,o2含量为4%,所用光源是波长λ≤200nm的真空紫外灯,功率是100w,烟气光催化空速是4500h-1,所用喷淋液为浓度0.02mol/l的nahso3海水溶液。烟气通过烟气分析仪进行检测,废液中的no3-、no2-和nh4+浓度通过三氮检测仪进行检测。考察不同温度和液气比下的脱硫脱硝效果,结果如表1。表1不同温度和液气比下的脱硫脱硝效果序号温度/℃液气比/(l/m3)脱硫率/%脱硝率/%no3-/(mg/l)n2还原率/%160397.396.826.8574.9260499.696.923.3565.9360610094.819.5363.8450498.294.930.1061.0570410098.526.5767.8680499.299.320.6569.6由表1可知,在不同温度和液气比下本工艺能实现高效脱硫脱硝,no3-浓度达到排放标准,n2还原率61~75%。同一温度下,液气比越大,脱硫率越高;液气比为4l/m3时脱硝率最高,达到96.9%。同一液气比下,温度越高,脱硝率越高,温度70℃时脱硫率最高,达到100%,低于70℃或高于70℃时脱硫率均有所下降。实施例2:本实施例选用的烟气光催化脱硫脱硝一体化工艺与实施例1一致,选用的光催化剂与实施例1一致。本实施例以n2为载气,烟气中so2初始浓度为2459mg/m3,no初始浓度为1003mg/m3,所用光源是波长λ≤200nm的真空紫外灯,功率是100w,反应温度60℃,液气比4l/m3。烟气通过烟气分析仪进行检测,废液中的no3-、no2-和nh4+浓度通过三氮检测仪进行检测。考察不同o2含量、空速和nahso3浓度下的脱硫脱硝效果,结果如表2。表2不同o2含量、空速和nahso3浓度下的脱硫脱硝效果由表2可知,在不同o2含量、空速和nahso3浓度下本工艺能实现高效脱硫脱硝,no3-浓度达到排放标准,n2还原率68~74%。同一o2含量和nahso3浓度下,空速越小,脱硫脱硝率越高。空速为3000h-1时脱硫脱硝率最大,脱硫率100%,脱硝率99.8%。同一空速和nahso3浓度下,o2含量越高,脱硫率越高,脱硝率越低。同一o2含量和空速下,nahso3浓度越大,脱硫率越低,脱硝率越高。当前第1页12